Figures & data
Figure 1. ESEM images of CRM processed by (a) ambient grinding (b) cryogenic grinding, adapted from (Shen & Amirkhanian, Citation2007).
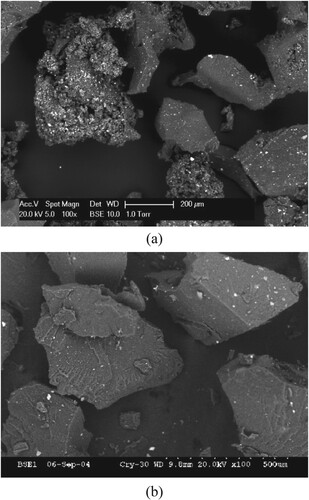
Table 1. Basic properties of CRM.
Figure 2. ESEM sample preparation process (a) heat and casting (b) flattening and transferring (c) storing.
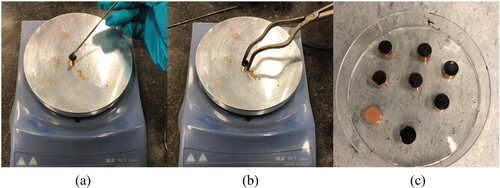
Figure 9. MSCR test results as a function of interaction temperature and time: (a) Nonrecoverable creep compliance and (b) percentage of recovery.
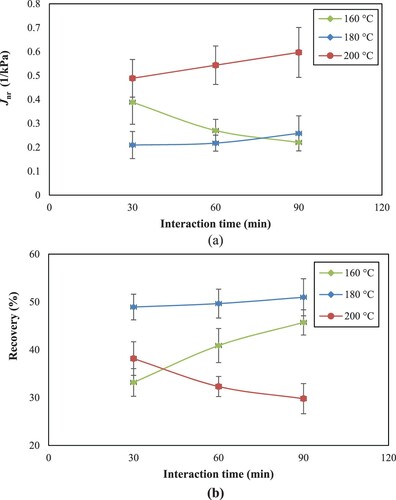
Table 2. MSCR test results of different asphalt binders.
Figure 12. LAS material integrity versus damage intensity curves of (a) base asphalt with and without WMA additives, (b) CRMA binder with and without WMA additives, (c) comparison between experimental data and model fitting of CRMA binder.
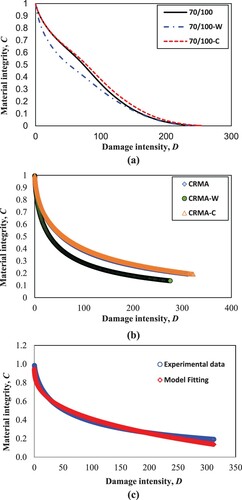
Table 3. Analysis of LAS results.
Figure 14. Master curve of shear stress relaxation modulus G(t) at a reference temperature of −10°C.
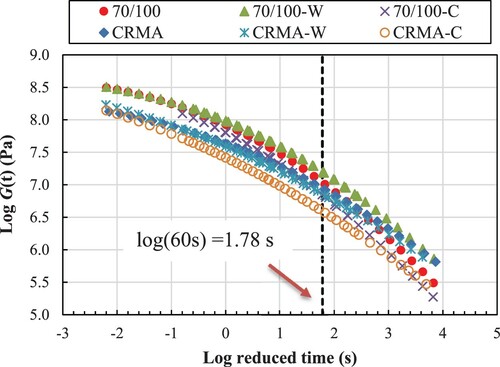