Figures & data
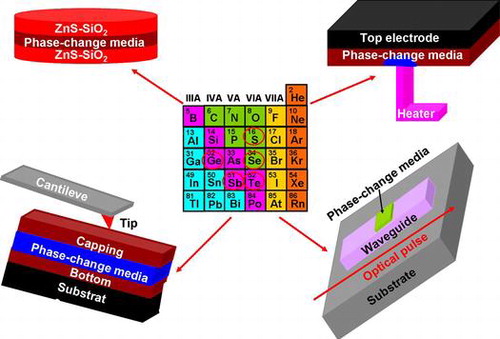
Figure 6. Crystallization and amorphization processes along with the temporal evolution of temperature.
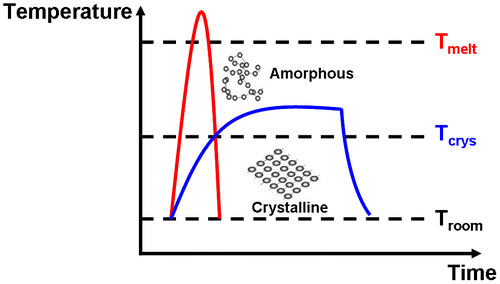
Figure 8. Measured resistance as a function of time for different annealing temperatures TA, under conditions TR = TA (a) and TR = 30°C (b). Note the different temperature behaviour of the curve slope, indicating the power-law exponent ν of resistance drift. Reprinted with permission from [Citation64].
![Figure 8. Measured resistance as a function of time for different annealing temperatures TA, under conditions TR = TA (a) and TR = 30°C (b). Note the different temperature behaviour of the curve slope, indicating the power-law exponent ν of resistance drift. Reprinted with permission from [Citation64].](/cms/asset/fe266729-68b1-45ef-a847-08f142b00920/tsta_a_1332455_f0008_oc.gif)
Figure 10. The ‘Millipede’ system when operated in its write and readout modes. Upgraded and reprinted with permission from [Citation106].
![Figure 10. The ‘Millipede’ system when operated in its write and readout modes. Upgraded and reprinted with permission from [Citation106].](/cms/asset/263d6abf-caea-49a4-9c59-f3d9f0b45c9d/tsta_a_1332455_f0010_oc.gif)
Figure 11. Phase-change probe memory when operated in (a) write mode, and (b) read mode. Reprinted with permission from [Citation17].
![Figure 11. Phase-change probe memory when operated in (a) write mode, and (b) read mode. Reprinted with permission from [Citation17].](/cms/asset/dfa0f04d-501d-4004-8e3a-1e57a7d345ef/tsta_a_1332455_f0011_oc.gif)
Figure 14. (a) Schematic of the ‘encapsulated’ tip concept, and (b) the experimentally fabricated encapsulated tip. Upgraded and reprinted with permission from [Citation124].
![Figure 14. (a) Schematic of the ‘encapsulated’ tip concept, and (b) the experimentally fabricated encapsulated tip. Upgraded and reprinted with permission from [Citation124].](/cms/asset/85eade69-bec0-47e7-8187-19f088af526e/tsta_a_1332455_f0014_oc.gif)
Figure 15. The resulting crystalline bit from the designed optimal electrical probe memory. The written bit exhibits a radius of approximately 5 nm, corresponding to 10 Tbit/in2. Reprinted with permission from [Citation130].
![Figure 15. The resulting crystalline bit from the designed optimal electrical probe memory. The written bit exhibits a radius of approximately 5 nm, corresponding to 10 Tbit/in2. Reprinted with permission from [Citation130].](/cms/asset/82cf354f-472c-4cf2-87ab-cb9b76d49e0c/tsta_a_1332455_f0015_oc.gif)
Figure 16. Schematic (top) of conventional mark-position recording, as used in probe memories to date; schematic (middle) of a new mark-length recording strategy; and (bottom) a current image of mark-length recorded bits in a phase-change medium (image is 580 nm × 140 nm and recorded bit sequence is 11001110111101110001111000111 with a bit cell length of 20 nm). Reprinted with permission from [Citation131].
![Figure 16. Schematic (top) of conventional mark-position recording, as used in probe memories to date; schematic (middle) of a new mark-length recording strategy; and (bottom) a current image of mark-length recorded bits in a phase-change medium (image is 580 nm × 140 nm and recorded bit sequence is 11001110111101110001111000111 with a bit cell length of 20 nm). Reprinted with permission from [Citation131].](/cms/asset/19300522-4129-4524-ad94-67e4d04bf828/tsta_a_1332455_f0016_oc.gif)
Figure 19. Various PRAM devices for threshold voltage scaling using: (a) additional electrode, reprinted with permission from [Citation154]; (b) phase-change nanowire, reprinted with permission from [Citation155]; (c) phase-change bridge, reprinted with permission from [Citation44]; and (d) carbon nanotube (CNT) electrode, reprinted with permission from [Citation160].
![Figure 19. Various PRAM devices for threshold voltage scaling using: (a) additional electrode, reprinted with permission from [Citation154]; (b) phase-change nanowire, reprinted with permission from [Citation155]; (c) phase-change bridge, reprinted with permission from [Citation44]; and (d) carbon nanotube (CNT) electrode, reprinted with permission from [Citation160].](/cms/asset/ff9bfb25-a12f-428e-9233-07fec3db4c1e/tsta_a_1332455_f0019_oc.gif)
Figure 20. Threshold field as a function of the length of the active phase-change region in a phase-change bridge memory for four different PCMs. Reprinted with permission from [Citation159]. ‘AIST’ refers to ‘Ag4In3Sb66Te27’.
![Figure 20. Threshold field as a function of the length of the active phase-change region in a phase-change bridge memory for four different PCMs. Reprinted with permission from [Citation159]. ‘AIST’ refers to ‘Ag4In3Sb66Te27’.](/cms/asset/f755c17c-539b-4463-b4df-ce81d635b443/tsta_a_1332455_f0020_oc.gif)
Figure 21. Various PRAM devices for ‘RESET’ current scaling using: (a) edge-contact type; (b) μTrench type; (c) ring-shaped type; (d) pillar type; (e) pore type; (f) cross-spacer type; and (g) dash type. Reprinted with permission from [Citation162].
![Figure 21. Various PRAM devices for ‘RESET’ current scaling using: (a) edge-contact type; (b) μTrench type; (c) ring-shaped type; (d) pillar type; (e) pore type; (f) cross-spacer type; and (g) dash type. Reprinted with permission from [Citation162].](/cms/asset/7e3e3ad3-6f14-403c-8b1a-0f08978ea8fe/tsta_a_1332455_f0021_oc.gif)
Figure 22. ‘RESET’ current as a function of equivalent contact diameter, showing a linear scaling trend with the effective contact area as the device feature size goes down. A constant ~40 MA/cm2 current density is required to program the PRAM cell. Reprinted with permission from [Citation14].
![Figure 22. ‘RESET’ current as a function of equivalent contact diameter, showing a linear scaling trend with the effective contact area as the device feature size goes down. A constant ~40 MA/cm2 current density is required to program the PRAM cell. Reprinted with permission from [Citation14].](/cms/asset/303995f1-7abe-4319-83d1-fb1df37fc0bf/tsta_a_1332455_f0022_oc.gif)
Figure 23. High-angle annular dark field (HAADF)-scanning transmission electron microscope (STEM) image of GeTe/Sb2Te3 superlatttice. Reprinted with permission from [Citation170].
![Figure 23. High-angle annular dark field (HAADF)-scanning transmission electron microscope (STEM) image of GeTe/Sb2Te3 superlatttice. Reprinted with permission from [Citation170].](/cms/asset/cb8ac507-1ef2-4696-ac23-7ef670f64845/tsta_a_1332455_f0023_oc.gif)
Figure 25. (a) Typical Rcell-Ipulse curve obtained by varying the current pulse amplitude for a mushroom phase-change memory cell. Reprinted with permission from [Citation174]. (b) Schematic illustrating the basic iterative programming concept using a sequence of adaptive write and verify steps. Reprinted with permission from [Citation179].
![Figure 25. (a) Typical Rcell-Ipulse curve obtained by varying the current pulse amplitude for a mushroom phase-change memory cell. Reprinted with permission from [Citation174]. (b) Schematic illustrating the basic iterative programming concept using a sequence of adaptive write and verify steps. Reprinted with permission from [Citation179].](/cms/asset/9bc744af-34f1-4fda-b1bb-7427372dabee/tsta_a_1332455_f0025_oc.gif)
Figure 26. Structure of the cross-point PRAM cell. Reprinted with permission from [Citation162].
![Figure 26. Structure of the cross-point PRAM cell. Reprinted with permission from [Citation162].](/cms/asset/5fc12d80-9392-4c26-88c0-770634a8434a/tsta_a_1332455_f0026_oc.gif)
Figure 27. Device structure and operation of VCCPCM. Reprinted with permission from [Citation190].
![Figure 27. Device structure and operation of VCCPCM. Reprinted with permission from [Citation190].](/cms/asset/5afd8320-b3ed-4ed3-805c-0c8a1c292295/tsta_a_1332455_f0027_oc.gif)
Figure 28. Schematics of the nanophotonic device using PCMs. Reprinted with permission from [Citation11].
![Figure 28. Schematics of the nanophotonic device using PCMs. Reprinted with permission from [Citation11].](/cms/asset/8965ea1f-64bd-4c4f-b54b-68d007a93bb9/tsta_a_1332455_f0028_oc.gif)
Figure 29. Eight clearly distinguishable levels are reached using this nanophotonic device by gradually changing the device transmission. Reprinted with permission from [Citation11].
![Figure 29. Eight clearly distinguishable levels are reached using this nanophotonic device by gradually changing the device transmission. Reprinted with permission from [Citation11].](/cms/asset/eab49213-6f76-4e1a-9b19-536f4222e0e2/tsta_a_1332455_f0029_oc.gif)