Figures & data
Figure 3. Time histories of the target input signals of AQA earthquake: accelerations, velocities, and displacements.
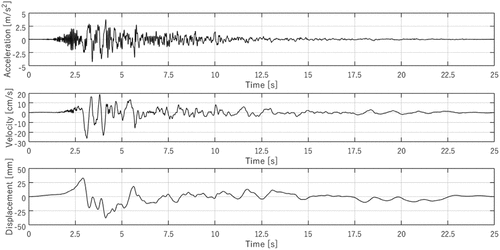
Table 1. List of tests carried out on the unstrengthened test specimen: dynamic identification tests (DIT) and shaking table tests (ST).
Table 2. List of tests carried out on the strengthened test specimen: dynamic identification tests (DIT) and shaking table tests (ST).
Figure 4. FEM‒UNS macro-model of the full-scale vault in DIANA environment: (a) geometry, (b) mesh of the model.
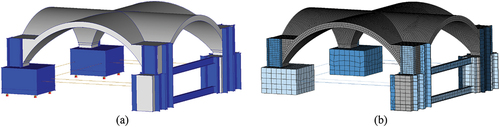
Table 3. Element types of the numerical FEM‒UNS and FEM – SM models built in DIANA 10.5 (Citation2022).
Figure 5. Constitutive laws used in the FEM–UNS and FEM–SM models: (a) non-linear hysteretic behaviour of masonry elements, (c) Mohr–coulomb criterion for sliding interface.

Figure 6. Strengthened FEM‒SM macro-model of the full-scale vault in DIANA 10.5 (Citation2022) environment: (a) shell element (CQ40S) for the Geocalce F, (b) embedded grid to simulate geosteel grid 200.
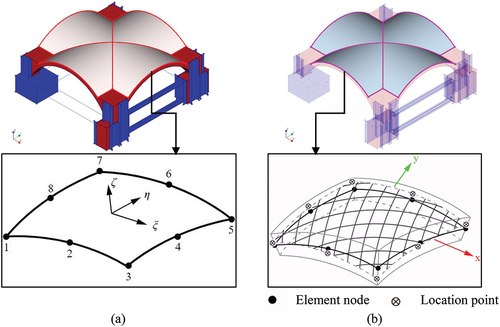
Figure 7. Grout injections modelled in the strengthened FEM‒SM model in DIANA 10.5 (Citation2022): (a) damaged intrados at the end of the ST–UNS–75%, (b) solid elements to simulate injections (intrados and north elevation).

Table 4. Mechanical properties for the TRM system adopted in the numerical FEM‒SM (DIANA 10.5 Citation2022.).
Figure 10. Contacts behaviour in the DEM model: (a) elastic joint model between brick-steel, shaking table-brick, shaking table-steel and steel-steel, (b) Mohr–coulomb criterion between brick-brick in the normal direction, (c) Mohr–coulomb criterion between brick-brick in the tangential direction.
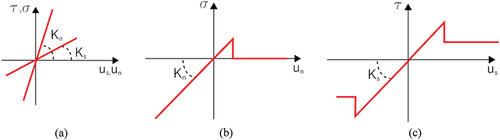
Figure 11. Failure surface implemented for Mohr–coulomb (MC) and combined material behaviour of Mohr–coulomb (MC‒CM). Adapted by Pulatsu (Citation2023).
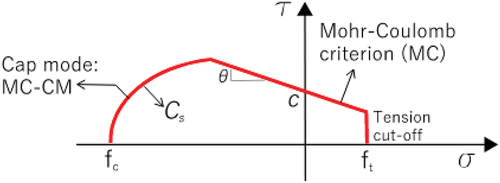
Figure 12. Mode shapes of the first modes of the specimens (UNS and SM) and numerical models: (a) DIT‒0–UNS–Y test, (b) first mode obtained from eigenvalue analysis for FEM‒UNS model, (c) DIT‒0–SM–Y test; (d) first mode obtained from eigenvalue analysis for FEM‒SM model.
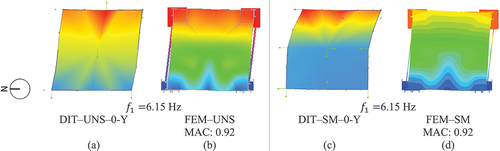
Table 5. Final properties after the calibration for FEM‒UNS and FEM‒SM models. Calibrated properties.
Figure 13. Comparison of frequency response functions obtained from the numerical modelling and the dynamic identification tests. (DIT‒0–UNS–Y, red dashed line) and the numerical model (DEM‒UNS, black solid line).
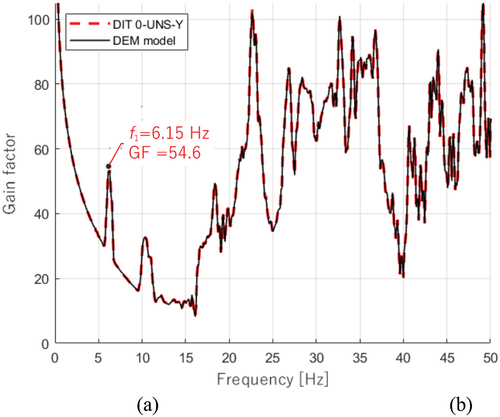
Table 6. Final properties of joints after the calibration for classic Mohr–Coulomb criterion in DEM‒UNS model. Calibrated properties.
Figure 14. DEM calibration: (a) MAC matrix, (b) first mode shape between DIT (red) and DEM‒UNS (blue) model performing vibration analysis.
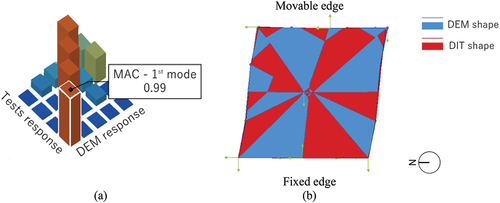
Table 7. List of analyses carried out on the unstrengthened and strengthened numerical models.
Figure 16. Evolution of cracks at the extrados: (a) ST–UNS–75, (b) deformed shapes of DEM‒UNS model (deformation factor: 100), (c) strains distribution in FEM‒UNS model.

Table 8. Peak values and root mean square of displacements (RMSD) and average errors between the results measured by for each seismic test of the unstrengthened specimen and obtained by DEM‒UNS and FEM‒UNS models.
Figure 20. In-plane deformation profiles of the strengthened configuration for the ST–SM–150% when all the optical cameras measure the maximum displacements. Deformation factor: 10.
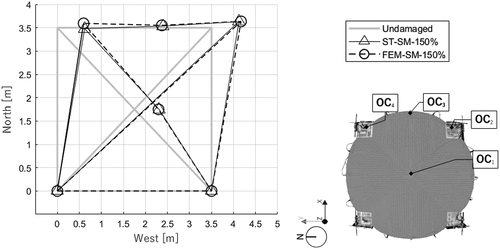
Table 9. Peak values and root mean square (RMSD) of displacements and average errors obtained from of the ST — SM–150% and the FEM‒SM model.