Figures & data
Table 1. Overview of diagnostic load tests reviewed in this study.
Table 2. Overview of proof load tests reviewed for this study.
Figure 19. Application of FBG sensors. Left: glued to steel rebar, and right: attached to a concrete surface.
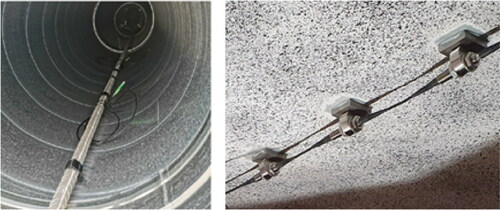
Figure 24. Installation of SA sensors. Left: before casting, and right: inside a drilled hole in an existing structure.
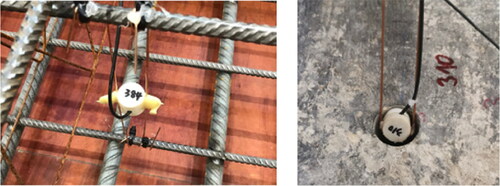
Table 3. Summary of techniques and sensors.
Table 4. Goal of the diagnostic load test of a reinforced concrete bridge and measurements.
Table 5. Stop criteria and measurements during a proof load test of a reinforced concrete bridge.