Figures & data
Figure 1. (a) SE images of AlSi10Mg powder (inset shows cross-sectioned powders), and (b) particle size distribution.
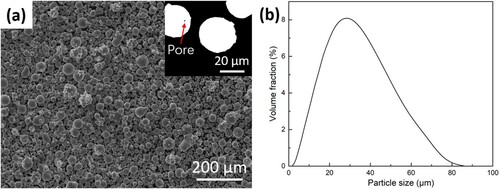
Figure 2. OM images showing typical surface morphologies of SLM specimens fabricated in two melting modes: (a) CM, and (b) KM.
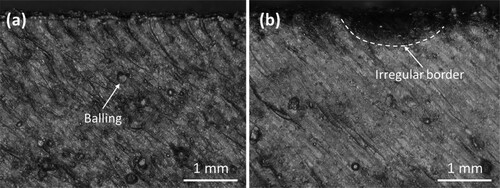
Figure 3. OM images of SLM AlSi10Mg specimens fabricated in two melting modes: (a) and (c) CM, and (b) and (d) KM.
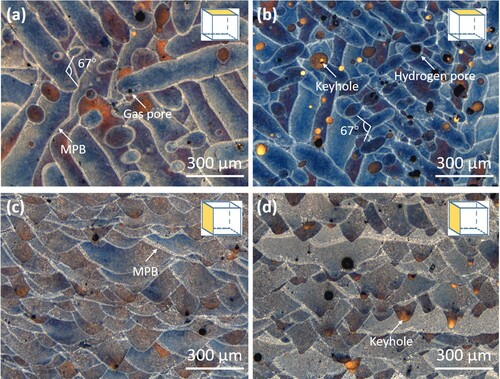
Figure 5. SE and inset BF TEM images of SLM AlSi10Mg specimens for the two melting modes: (a) and (c) CM, and (b) and (d) KM.
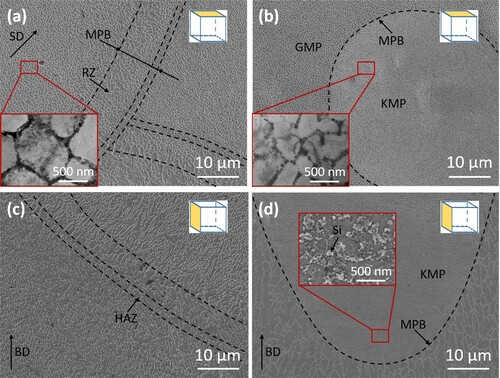
Figure 6. (a) Inverse pole figure (IPF) map and (b) image quality (IQ) map on the top view of the KM specimen.
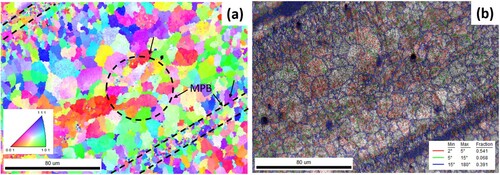
Figure 7. HAADF-STEM image of the cells in KMP and corresponding EDS mapping of the main elements (Al, Si, Mg and Fe).
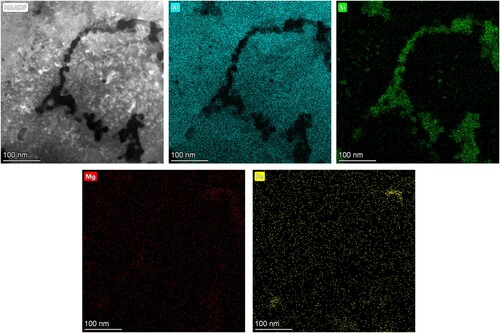
Figure 9. (a) Friction coefficients versus sliding time and (b) wear rates for the SLM and as-cast specimens.
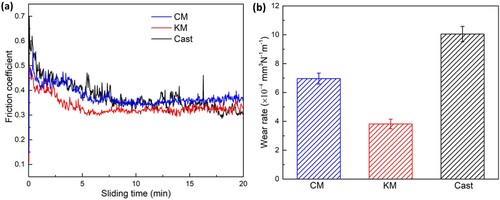