Figures & data
Figure 5. Structure redesign for AM via combined design for AM methods: a. TO combines with generative design; b. TO combines with lattice configuration.
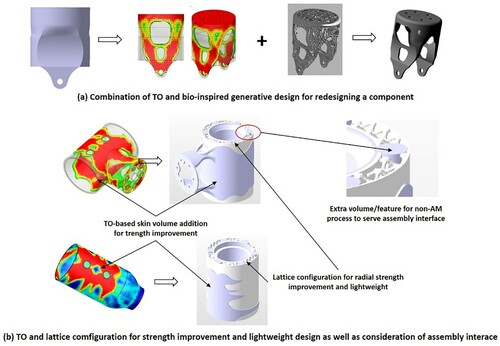
Figure 6. Redesigned components of the AM component group of the actuator system (left) and the full actuator system (right).
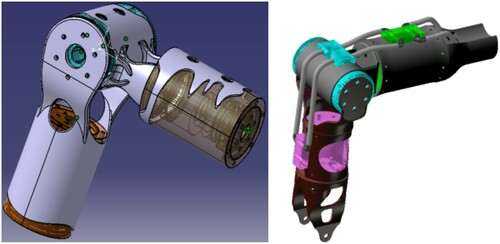
Figure 8. (a) Ti200 double-laser machine; (b) scanning electron microscopy image of Ti6Al4 V powder.
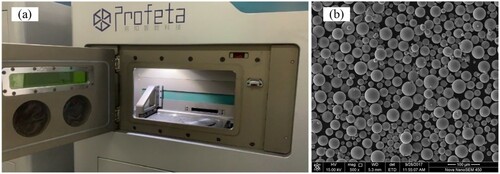
Table 1. Main printing parameter settings.
Figure 13. Simulation curves of the position relationship between the TCP in space and the driving joint.
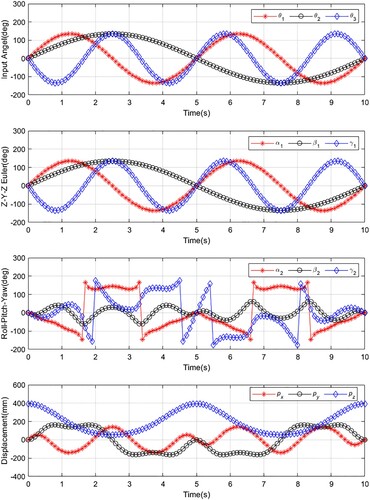
Table 2. Parameter values of the 3-DOF robot actuator.