Figures & data
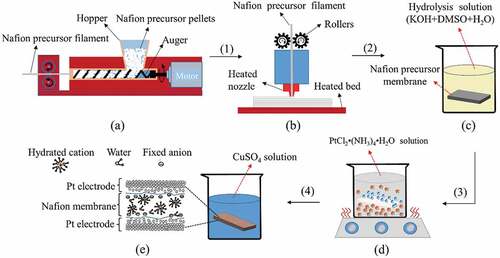
Figure 1. Schematic diagram of IPMC specimen fabrication by FDM technology: (a) Fabrication process of Nafion precursor filament. (b) Nafion precursor membrane printed by a 3D printer. (c) The hydrolysis process exchanges the sulfonyl fluoride group to a sulfonate end group. (d) Prepare Pt electrodes by an electroless plating process. (e) Ion exchange process
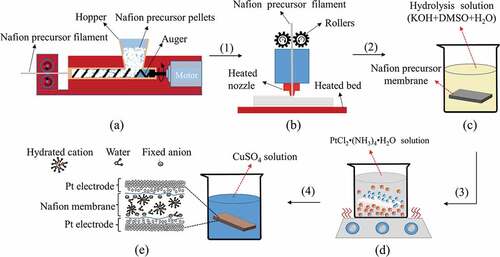
Figure 2. (a) The relationship between the thickness of precursor specimen and hydrolysis time; (b) the comparison of the IEC between the printed Nafion membrane and commercial membrane
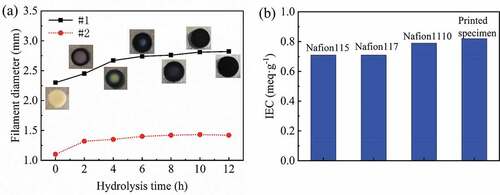
Figure 4. Currents vs. time under AC voltage with a frequency of 0.1 Hz. The actual current changes of the IPMC under square wave input (a) and sinusoidal input (b); the maximum currents of IPMCs under square wave input (c) and sinusoidal input (d)
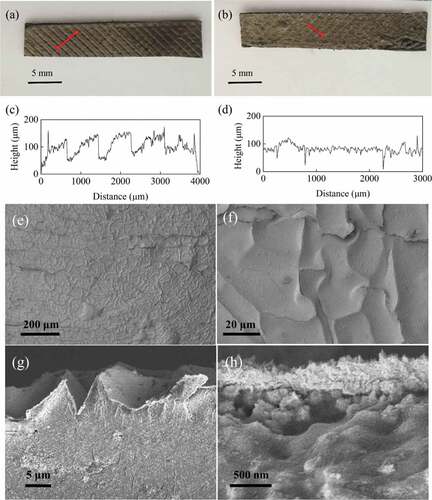
Figure 5. Currents vs. time under AC voltage with a frequency of 0.1 Hz. The actual current changes of the IPMC under square wave input (a) and sinusoidal input (b); the maximum currents of IPMCs under square wave input (c) and sinusoidal input (d)
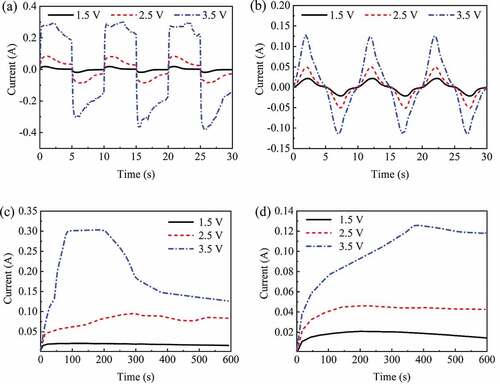
Figure 6. Displacement vs. time under AC voltage with a frequency of 0.1 Hz. The actual displacement changes of the IPMC under square wave input (a) and sinusoidal input (b); Maximum displacement of IPMC under square wave input (c) and sinusoidal input (d)
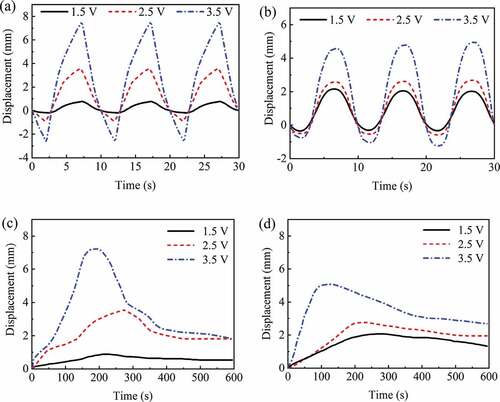