Figures & data
Table 1. Engine characteristics.
Table 2. Measurement instruments specifications.
Table 3. ECE-R96 standard for testing constant speed engine.
Table 4. Kinetics reactions used in simulations (Turns, Citation2000).
Table 5. Equilibrium reactions used in simulations (Turns, Citation2000).
Table 6. Fuels characteristics (Iranian Research Institute of Petroleum Industry).
Figure 11. Cylinder pressure in full load and different advance timings, diesel mode (a), dual mode with 50% diesel (b), dual mode with 40% diesel (c), and dual mode with 30% diesel (d).
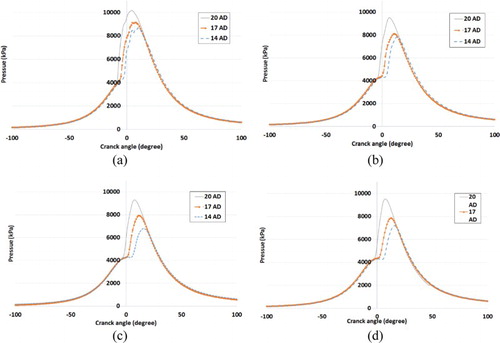
Figure 12. Experimental and simulation results of cylinder pressure in: (a) diesel mode, (b) dual mode with 50% diesel, (c) dual mode with 40% diesel, and (d) dual mode with 30% diesel.
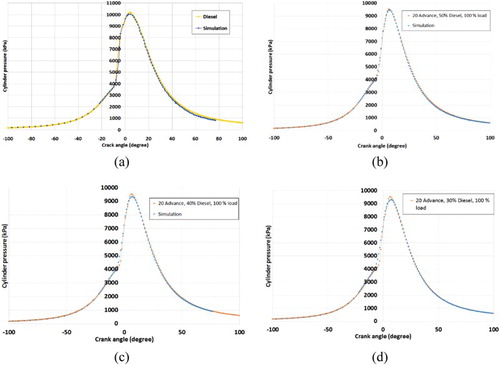
Figure 13. Simulation results for HRR and cumulative temperature in: (a) diesel mode, (b) dual mode with 50% diesel, (c) dual mode with 40% diesel, and (d) dual mode with 30% diesel.
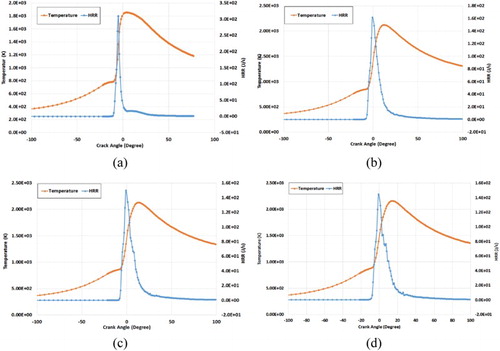
Figure 14. Simulation results for cylinder pressure at TDC for 20 degree advance timing in: (a) diesel mode, (b) dual mode with 50% diesel, (c) dual mode with 40% diesel, and (d) dual mode with 30% diesel.
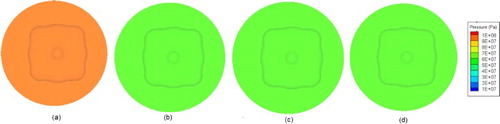
Figure 15. Simulation results for cylinder temperature at TDC for 20 degree advance timing in: (a) diesel mode, (b) dual mode with 50% diesel, (c) dual mode with 40% diesel, and (d) dual mode with 30% diesel.
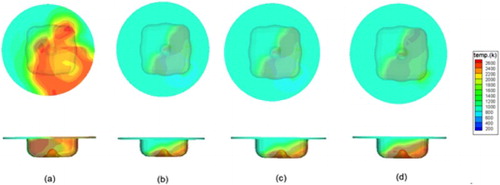