Figures & data
Figure 2. Illustration of (a) wetting and (b) non-wetting effects of the solid surface by melted liquids.
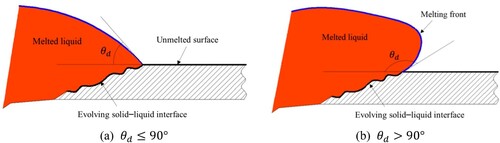
Figure 3. Particle distribution within the support domain of the smoothing function W for particle i. The support domain () and its boundary S is circular with the radius of
. The figure is cited from the book by Liu & Liu, Citation2003.
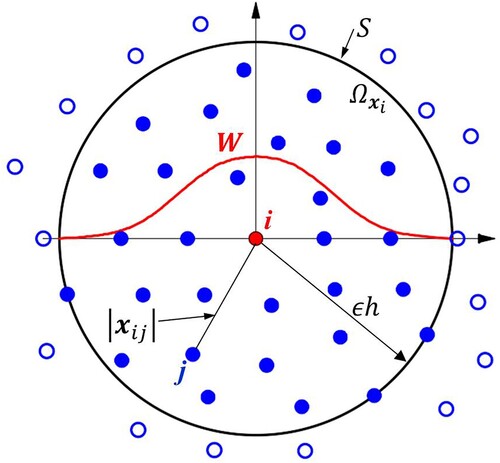
Table 1. Pseudo-code of implementing the established SPH model.
Figure 13. (a) The initial particle distribution for the test of square droplet deformation, and (b) the particle distribution at t = 6.0s.
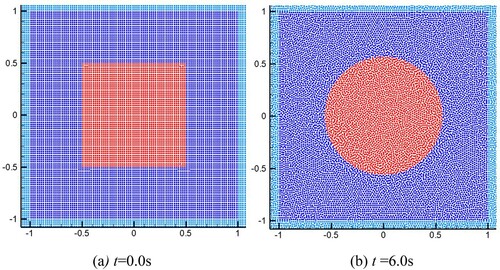
Figure 14. Time history of pressure difference. (a) Density ratio (DR) = 1.0, showing effect of smoothing length. (b) DR = 100.0, showing effect of interface sharpness force ().
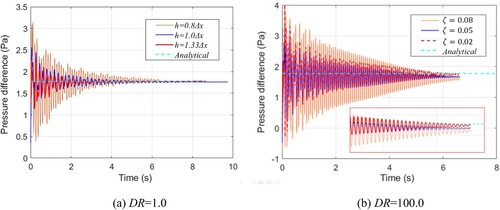
Figure 17. (a) Model parameters of single bubble rising, and SPH results of stable bubble based on different particle spacing: (b) ; (c)
; (d) Bubble profiles at different time instants.
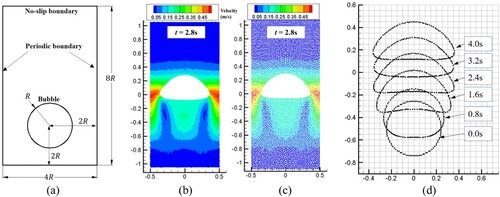
Table 2. Parameters for single bubble rising (model validation).
Figure 18. (a) Time history of velocity of ascending bubble, and (b) terminal bubble morphologies using different particle spacings (t = 2.8s).
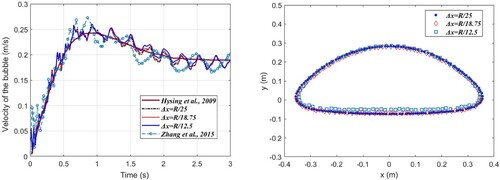
Table 3. Physical parameters for two rising bubbles.
Figure 22. Comparison of bubble morphologies between present SPH results (blue line) and level-set results (dotted red line, Grenier et al., Citation2013) (Bo = 80.0).
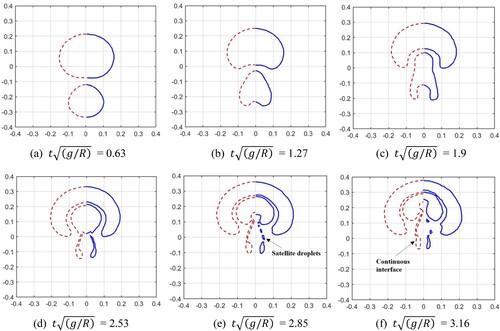
Figure 24. The time history of melted liquid volume with three particle resolutions. The volume is obtained by multiplying the area of molten liquid by the reference length (1.0m).
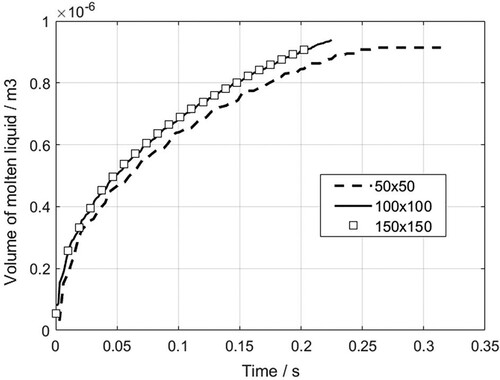
Figure 27. The particle distribution and normal vector of the interface at the initial moment of melting (t = 0.0025s).
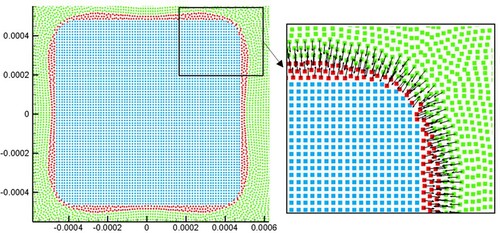
Figure 29. (a) Comparison of droplet morphologies between two particle resolutions (t = 0.18 s), (b) trends of melted liquid volume are obtained using three particle resolutions. The volume is obtained by multiplying the area of molten liquid by the reference length (1.0m).
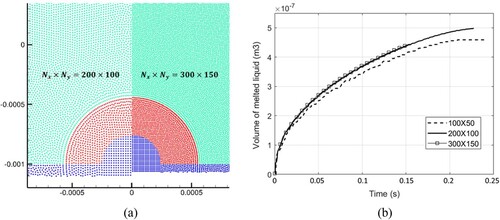
Figure 30. Simulation results of the melting process of a square solid on an adiabatic wall (case 2).
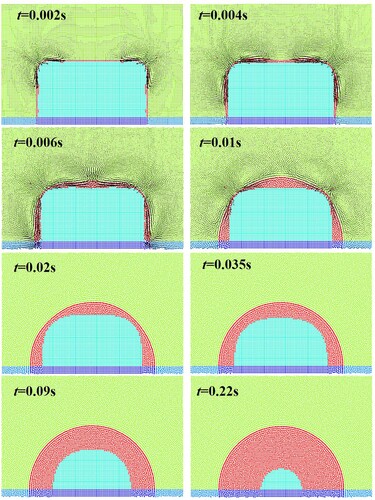
Figure 32. Model parameters and initial conditions of sinking and melting of a square solid (case 3).
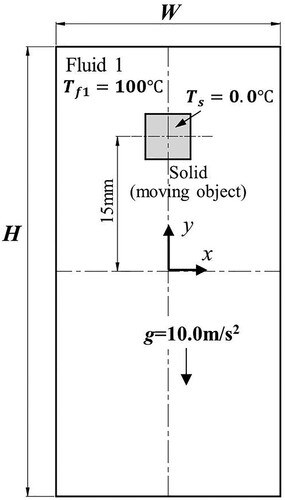
Figure 33. Time history of melted liquid volume using three different particle resolutions (case 3). The volume is obtained by multiplying the area of molten liquid by the reference length (1.0m).
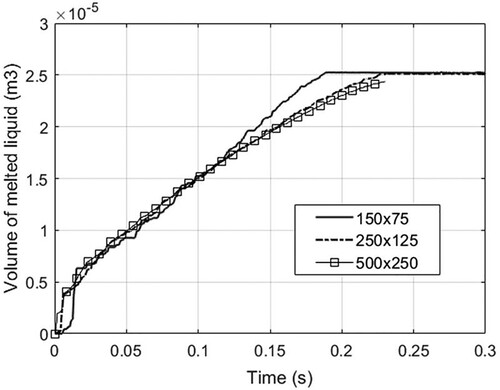
Figure 36. Temperature distribution inside the droplet during sinking of the solid. The morphology of the (unmelted) solid is shown in white (case 3).
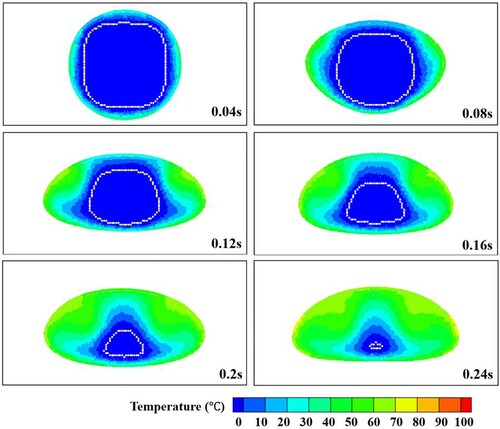
Figure 38. (a) Time evolution of melted liquid volume with four different particle resolutions, (b) comparison of the droplet profile between two particle resolutions at time 0.22 s (the convergence study for case 4). The volume is obtained by multiplying the area of molten liquid by the reference length (1.0m).
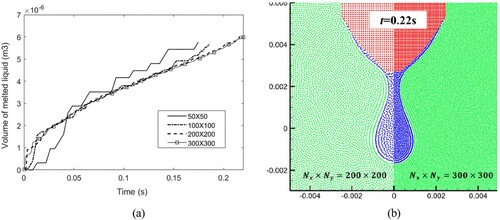
Figure 42. Results of molten droplet formation and dripping process for the three different Bond numbers.
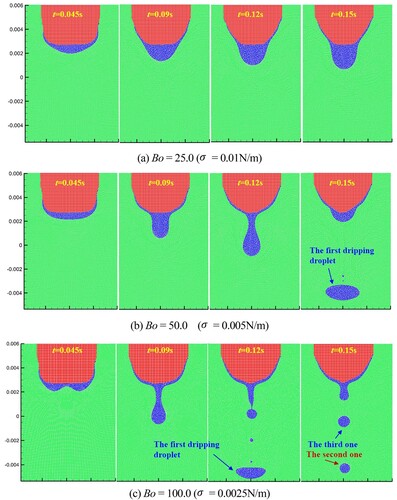
Figure 43. The time curve of melted liquid (a) volume and (b) melt kinetic energy with respect to different Bond numbers. The volume is obtained by multiplying the area of molten liquid by the reference length (1.0m).
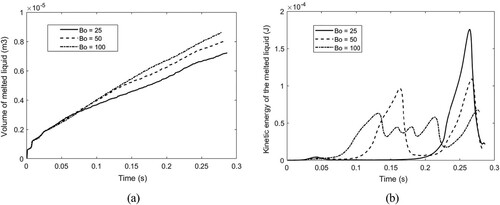