Figures & data
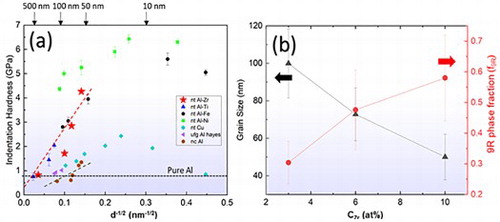
Figure 1. (a) XRD θ-2θ scans of sputtered Al-Zr on Si(111) substrates identifying strong (111) texture. (b-d) XRD (111) pole figure analysis revealing clear six-fold symmetry after introducing Zr, indicating twin variant formation.
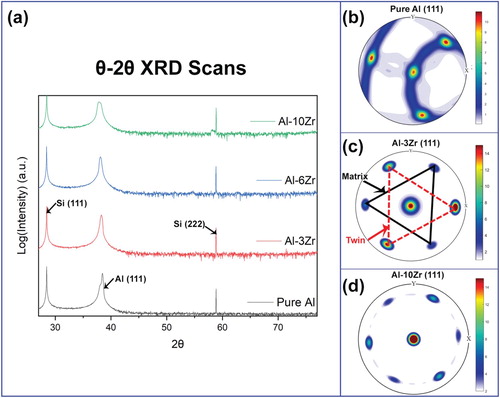
Figure 2. (a–c) Plan-view TEM micrographs with corresponding selected area diffraction (SAD) patterns with increasing Zr content. The microstructure transitions from single-crystal-like (Al-3Zr) to nanocrystalline (Al-6Zr, Al-10Zr). (d–f) In-plane inverse pole figures (IPF) along the <101> direction, confirming the single-crystal-like structure in Al-3Zr with consistent in-plane <101> texture across the entire sample, and the formation of polycrystalline nanograins and grain refinement upon further Zr additions. (g) Plot depicting grain size (d) and hardness evolution with increasing Zr content.
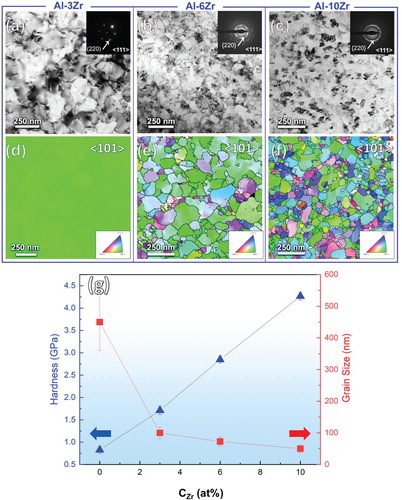
Figure 3. Cross-section TEM (XTEM) micrographs of NT Al-Zr alloy films. (a,d,g) Bright-field (BF) XTEM image with inserted SAD pattern showing columnar grains bounded by ITBs. Columnar refinement occurs at higher Zr content. (b,e,h) EDS maps showing complete solid solution at all compositions. (c,f,h) High-resolution TEM (HRTEM) images of (c) narrow ITB, (f) extended ITB, forming 9R phase, and (i) broad 9R phase, spanning ∼40 nm.
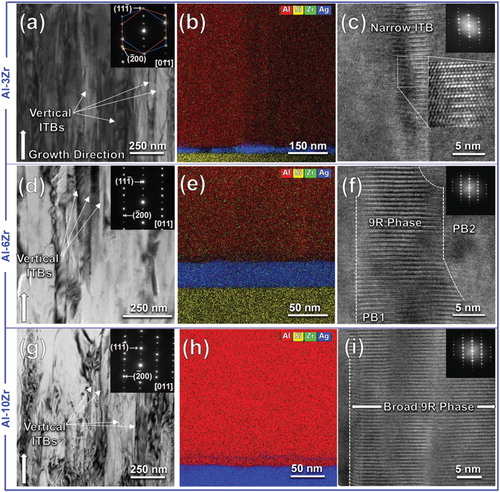
Figure 4. (a) Hall-Petch plot comparing hardness of NT Al-Zr with Al and other NT Al-X systems and NT Cu [Citation9,Citation13,Citation30–32,Citation39] (b) Fraction of columns containing 9R phase and grain size evolution with at% Zr. (c) DFT calculation comparing energy required for stacking fault formation in pure Al and Al-Zr. Zr reduces the stable stacking fault energy of Al. (d–e) DFT calculation showing excess energy per surface atom for (d) trimer and (e) heptamer clusters to move from an FCC stacking position to a faulted position. Zr increases the energy barrier for surface migration.
![Figure 4. (a) Hall-Petch plot comparing hardness of NT Al-Zr with Al and other NT Al-X systems and NT Cu [Citation9,Citation13,Citation30–32,Citation39] (b) Fraction of columns containing 9R phase and grain size evolution with at% Zr. (c) DFT calculation comparing energy required for stacking fault formation in pure Al and Al-Zr. Zr reduces the stable stacking fault energy of Al. (d–e) DFT calculation showing excess energy per surface atom for (d) trimer and (e) heptamer clusters to move from an FCC stacking position to a faulted position. Zr increases the energy barrier for surface migration.](/cms/asset/866adaee-6a5d-47bb-bc56-3be208a1846f/tmrl_a_1840451_f0004_oc.jpg)