Figures & data
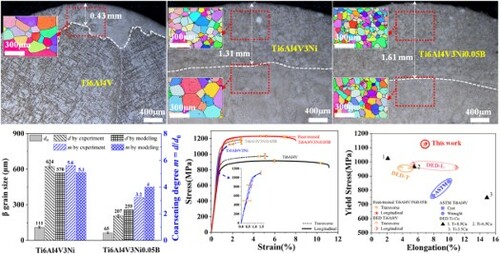
Table 1. Processing parameters for DED.
Figure 1. The β-grains at the top of Ti6Al4VxNiyB and the initial solidification mechanism of the last layer. (a), (d) Ti6Al4V; (b), (e) Ti6Al4V3Ni; (c), (f) Ti6Al4V3Ni0.05B; (g) grain size d0 plotted against the inverse Q. (The dashed white lines in a-c separate the equiaxed grains obtained only by solidification from the ones subjected to subsequent thermal-cycling. TE is the equilibrium liquidus temperature and ΔTn is the critical undercooling for nucleation).
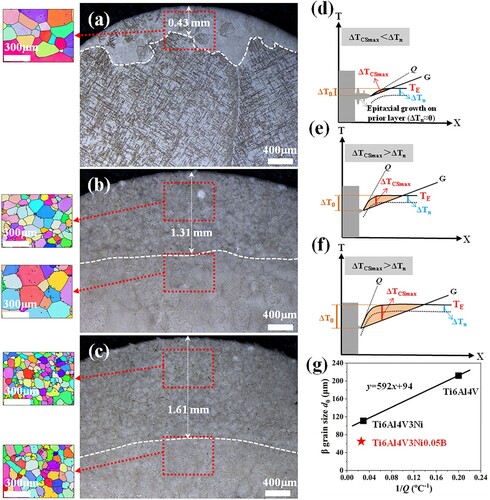
Table 2. The Q, ΔT0, ml, k and Qi.
Figure 2. The β-grains at the middle of the Ti6Al4V3NiyB deposits. (a) Ti6Al4V3Ni, (b) Ti6Al4V3Ni0.05B; (c) β-grain size and coarsening degree m; (d) the function of the simulated m with regard to d0, and the symbols represent the experimental value; the simulated δdi, d = d0+Σδdi, δMi and M = ΣδMi with regard to the thermal-cycling number (Tβ˂Tp˂Ts) in (e) Ti6Al4V3Ni and (f) Ti6Al4V3Ni0.05B. (Ts and Tβ are calculated using Thermo-Calc.).
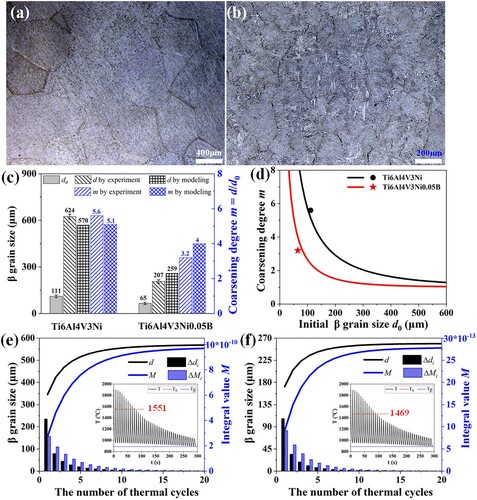
Figure 3. The microstructures at the middle of the Ti6Al4VxNiyB deposits. As-built: (a) Ti6Al4V, (b) Ti6Al4V3Ni, and (c) Ti6Al4V3Ni0.05B, (d) heat-treated Ti6Al4V3Ni0.05B.
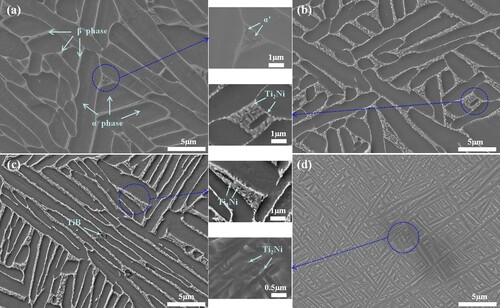
Figure 4. Mechanical properties of Ti6Al4VxNiyB alloys. (a) Representative engineering stress–strain curves; the error bars (UTS and EL) represent one standard deviation. (b) Tensile properties for heat-treated Ti6Al4V3Ni0.05B are comparable with Ti-Cu [Citation6] and Ti6Al4V [Citation10] by DED and the ASTM standard for Ti6Al4V [Citation32]. (c) Anisotropy (the calculation method is shown in [Citation21]).
![Figure 4. Mechanical properties of Ti6Al4VxNiyB alloys. (a) Representative engineering stress–strain curves; the error bars (UTS and EL) represent one standard deviation. (b) Tensile properties for heat-treated Ti6Al4V3Ni0.05B are comparable with Ti-Cu [Citation6] and Ti6Al4V [Citation10] by DED and the ASTM standard for Ti6Al4V [Citation32]. (c) Anisotropy (the calculation method is shown in [Citation21]).](/cms/asset/b268df6f-33c5-4ab3-8988-f4c7f0a1fe5c/tmrl_a_2115323_f0004_oc.jpg)
Figure 5. Fracture surfaces of longitudinal specimens: (a) (c) as-built Ti6Al4V, (b) (d) as-built Ti6Al4V3Ni, Ti6Al4V3Ni0.05B (e) (f) as-built and (g) (h) heat-treated.
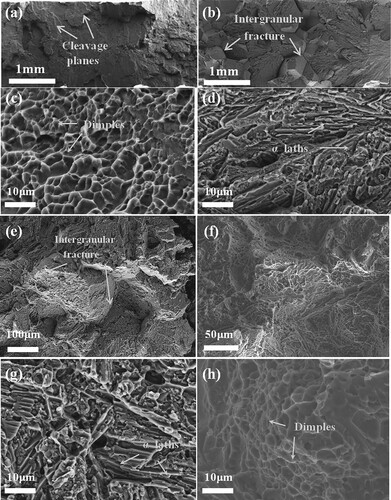