Figures & data
Figure 1. Correlation between cold rolling deformation, aging time, solution temperature, and the properties for pure components ((a)–(c)), and Cu-Ti alloys ((d)–(f), (g)–(i), and (j)–(l)).
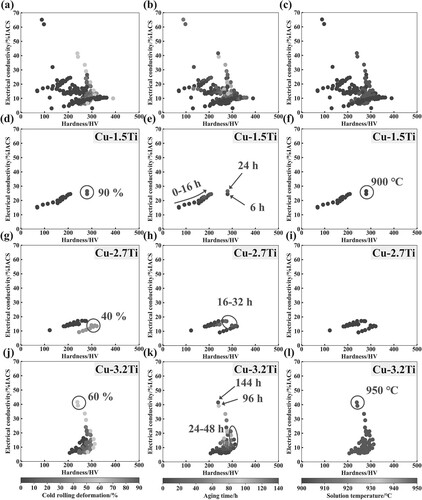
Figure 2. (a) Three newly expected data (five-pointed stars) designed by the Pareto front technique; (b) a comparison between the experimental properties of the designed alloys and those from the literature reports [Citation8,Citation20–24]; (c) and (d) represent the experimental hardness and electrical conductivity at different stages for the three designed alloys; (e) Cu-Ti Phase diagram (Ti < 10wt.%) [Citation29]; (f) Simulated mean radius of precipitates, compared with the experimental data.
![Figure 2. (a) Three newly expected data (five-pointed stars) designed by the Pareto front technique; (b) a comparison between the experimental properties of the designed alloys and those from the literature reports [Citation8,Citation20–24]; (c) and (d) represent the experimental hardness and electrical conductivity at different stages for the three designed alloys; (e) Cu-Ti Phase diagram (Ti < 10wt.%) [Citation29]; (f) Simulated mean radius of precipitates, compared with the experimental data.](/cms/asset/10303a9b-02d3-40ee-b84a-3d3acd732f86/tmrl_a_2358964_f0002_ob.jpg)
Table 1. List of compositions and process parameters of three selected alloys.
Figure 3. Measured microstructures of designed alloys: (a) STEM-HAADF image of the precipitates in Alloy 2# aged at 380°C for 48 h. (b) and (c) depict the elemental mappings for Cu and Ti, respectively, from the area shown in (a). Figures (e) and (f) respectively depict the magnified micrograph and FFT image of Area 1 in (d), while (g) and (h) correspond to Area 2;(i) the positions of β’-Cu4Ti tetragonal lattice diffraction spots along the [001]Cu axis [Citation34]; (j) shows the morphologies and average sizes of precipitates in Alloy 2# aged for 24 h; (k) for Alloy 1# aged for 48 h; (l) for Alloy 2# aged for 48 h; (m) for Alloy 3# aged for 48 h.
![Figure 3. Measured microstructures of designed alloys: (a) STEM-HAADF image of the precipitates in Alloy 2# aged at 380°C for 48 h. (b) and (c) depict the elemental mappings for Cu and Ti, respectively, from the area shown in (a). Figures (e) and (f) respectively depict the magnified micrograph and FFT image of Area 1 in (d), while (g) and (h) correspond to Area 2;(i) the positions of β’-Cu4Ti tetragonal lattice diffraction spots along the [001]Cu axis [Citation34]; (j) shows the morphologies and average sizes of precipitates in Alloy 2# aged for 24 h; (k) for Alloy 1# aged for 48 h; (l) for Alloy 2# aged for 48 h; (m) for Alloy 3# aged for 48 h.](/cms/asset/1cd3edb7-e382-4ab3-af0e-65430c26a22e/tmrl_a_2358964_f0003_ob.jpg)
Figure 4. Influence of each input variable on model predictions (SHAP value). The blue signifies contribution to electrical conductivity, while the red indicates contribution to hardness. The length of the bar corresponds to the strength of the effect.
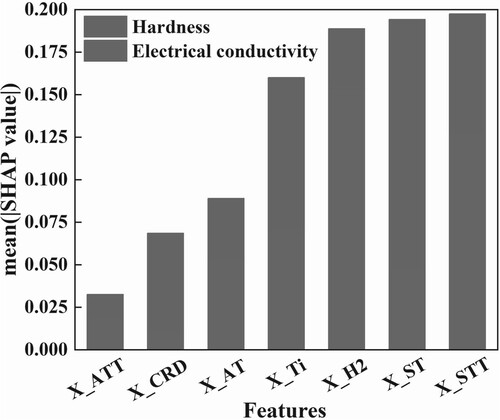