Figures & data
Figure 3. Schematic of the existing manufacturing process chain (top) and the proposed NNS manufacturing process chain (bottom).
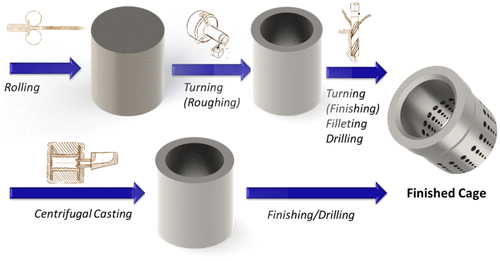
Figure 4. True centrifugal casting and semi-centrifugal casting (Swift & Booker, Citation2013).
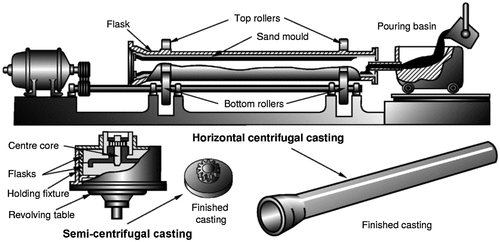
Figure 5. Schematic of the two process chains and the associated differential cost analysis (i.e. cost models comparison).
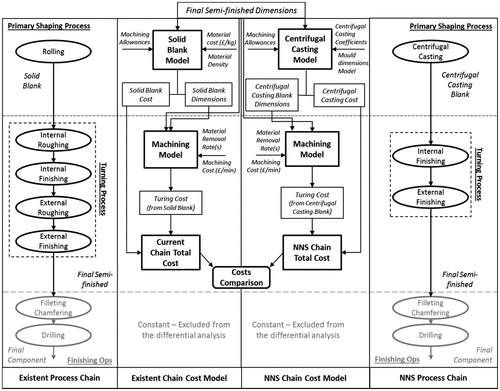
Figure 8. Cost comparison of the NNS process chain (a) and existing chain (b). Cost details for different cages sizes: 100 mm (c), 250 mm (d) and 400 (e). Component cost comparison of component evaluated costs for the NNS process chain (i.e. centrifugal casting and finish machining) and the existing process chain (i.e. machining from solid blank) (f).
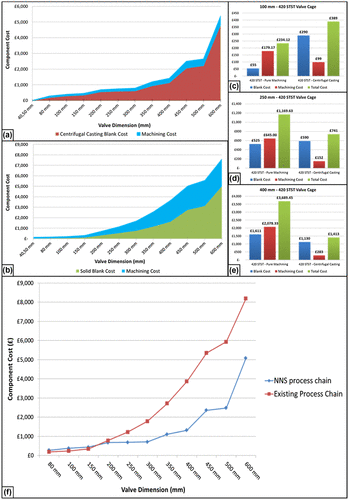
Figure 9. Step diagram for selecting the outer diameter of centrifugal casting’s mould given the outer diameter of the final component.
Table