Figures & data
Figure 1. Force acting on the tight (FT) and slack (FS) ends of a rope winding around a rotating cylinder.
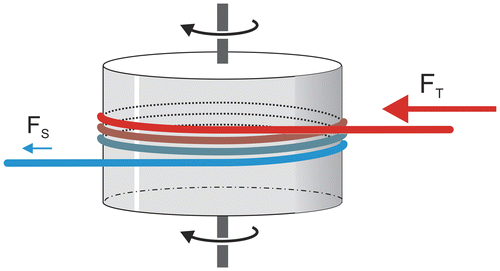
Figure 2. Braking mechanism of the first friction-loaded ergometers; braking force acting on the flywheel (FFW) is equal to the difference between tight (FT) and slack (FS) forces which were displayed by means of scale.
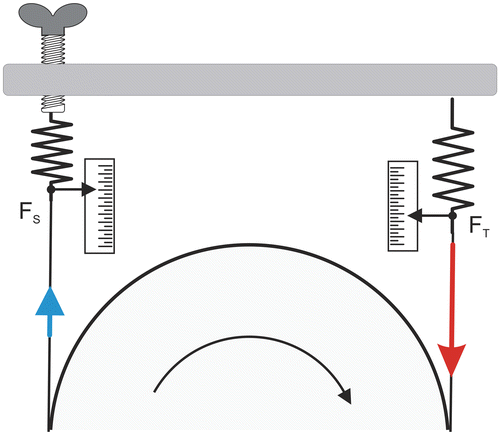
Figure 3. Amar’s cycle ergometer; D, P, and R correspond to the dynamometer, platform for weight, and steel ribbon, respectively.
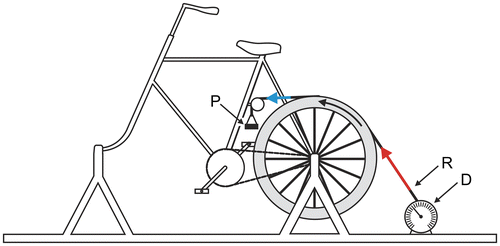
Figure 4. Thomson brake (drawing adapted from Beaumont, Citation1889, p. 33; Jervis-Smith, Citation1915, p. 82).
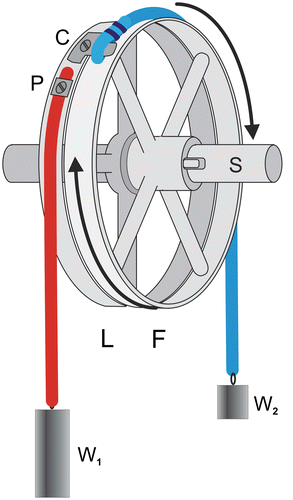
Figure 5. Fleisch ergometer; F et L fast et loose wheels, C connection between pulley L and belt B that is attached to weight W2 at the other end.
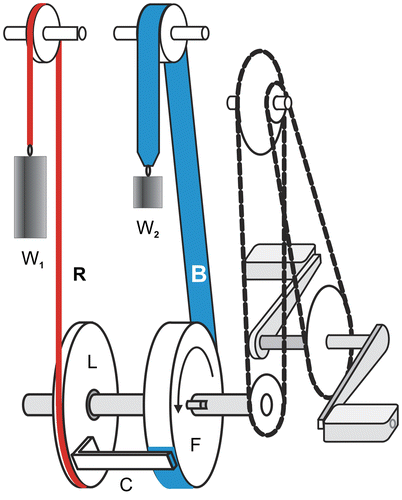
Figure 6. A, LB et LP arms of forces FB and P; FT and FS, tensions of the tight and slack ends of the belt; O1, O2, and O3, axles of the flywheel, cam, and pulley, respectively; O4 pivot of the roman steelyard; B, h1, and h2 lever-arms of FS1 and FS2, respectively; Wc and hc weight of the cam and its lever arm.
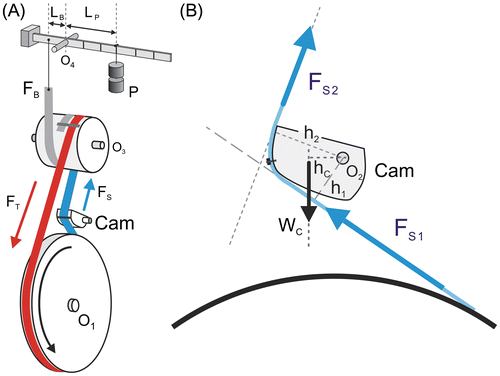
Figure 7. Von Döbeln ergometer.
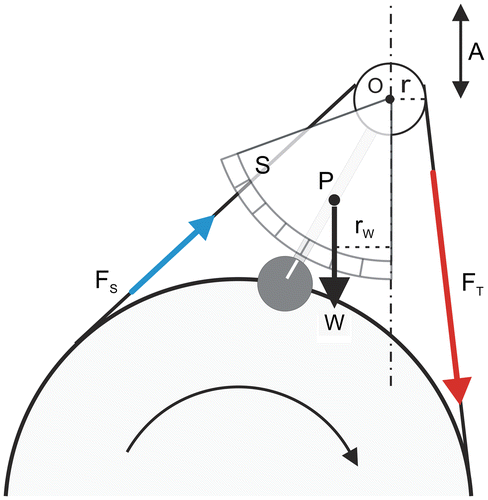
Figure 8. Monark sinus-balance cycle ergometer.
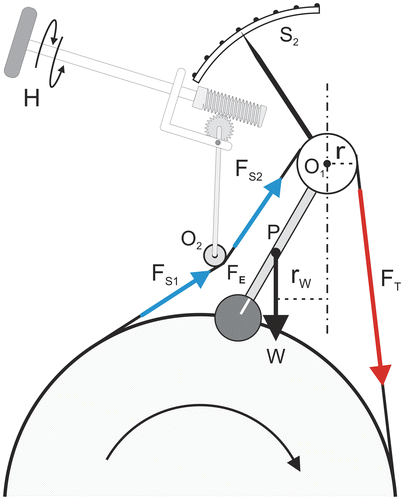
Figure 9. Weight-basket loaded cycle ergometer.
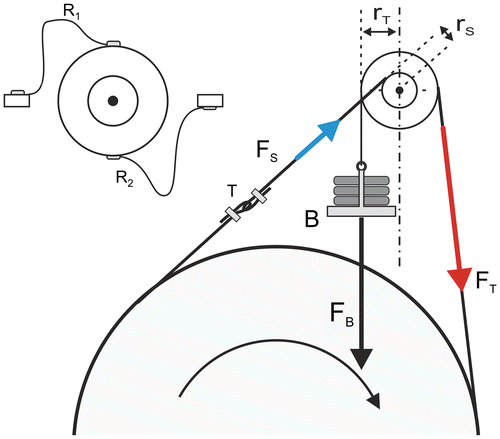
Figure 10. A, belt in the sinus-balance model; B, belt and rope in the basket-loaded ergometers; C, digging of small grooves in the circumference of aluminum flywheel; D, 3-turn rope.
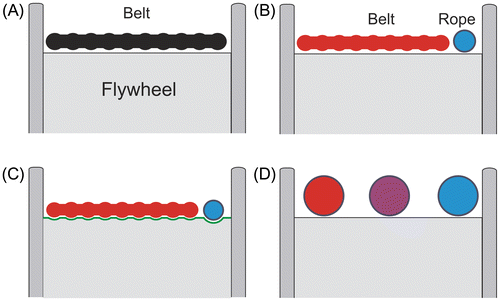
Figure 11. Relationships between μ, FT, FS, and error in FFW expressed as fractions of FB.
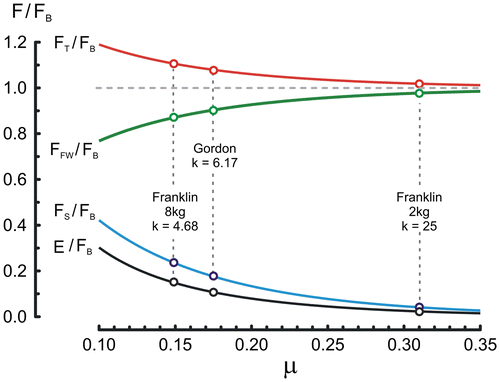
Figure 12. In A, time–frequency curves during all-out sprints against different loads on a Monark 864 cycle ergometer; in B, relationship between load and peak frequency (Vpeak).
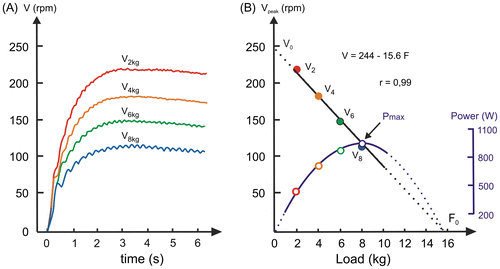
Figure 13. Time–power output curves computed during all-out sprints on basket-loaded cycle ergometer against loads equal to 19 N (red curve) and 76 N (blue curve).
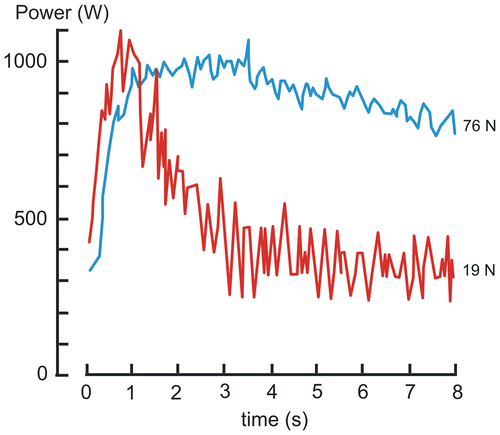
Figure 14. Relationship between the computed torque exerted on the crankwheel and crank angular speed (or pedal rate) during all-out sprints against two loads (19 N red points and 76 N blue points) in the same subject.
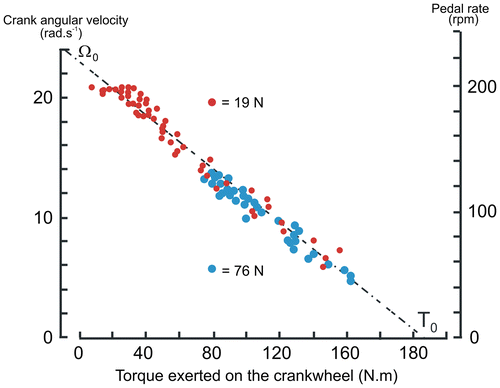
Figure 15. In A, adjustment of the zero; in B, force calibration with a calibrated weight.
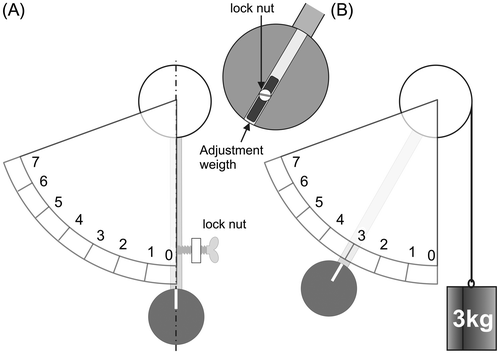
Figure 17. In A decomposition of the force F1 exerted on the pedal into a force F2 exerted on the crank shaft and a couple C; in B comparison of the mean torque (red line) and the torques exerted on the left (blue dashed line, L) and right crank (blue continuous line, R) during a pedal revolution.
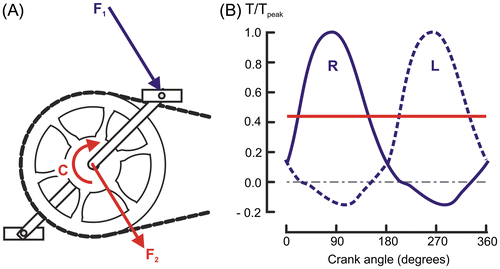
Figure 18. Schematic diagram of the method used in the study by Jones & Passfield (Citation1998) for the comparison of a basket-loaded MonarkTM ergometer (in blue), model 814 (ME) and data of different SRMTM transducers.
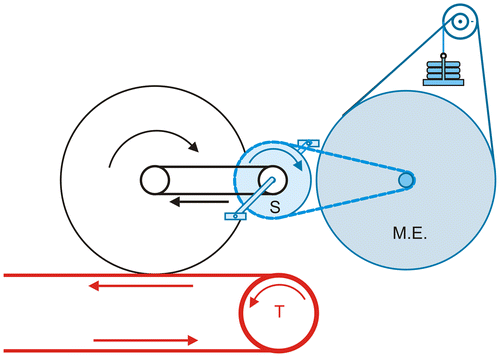
Figure 19. Results of dynamic calibrations of friction-loaded ergometers.
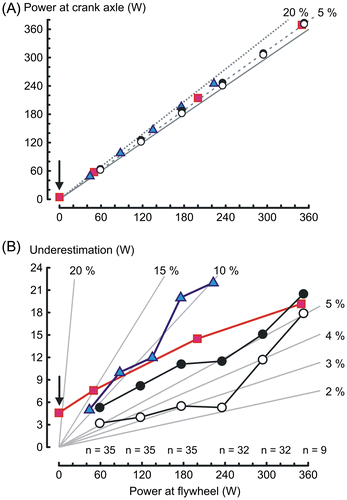
Figure 20. Parts of a cycle ergometer that must be maintained (explanations in text); 7, chain adjuster bolt, lateral view.
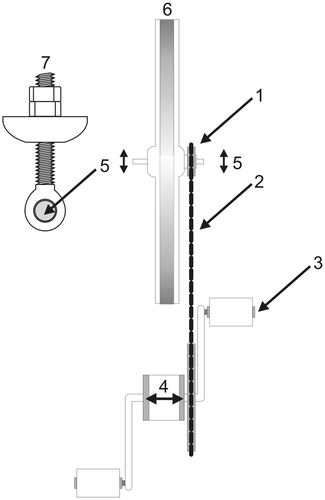
Figure 21. Example of a mechanism enabling the adjustment of the belt tension by a change in distance between the axes of the pulley (O1) and the flywheel; O2, axle of the mechanism; H, handle; N, locking nut.
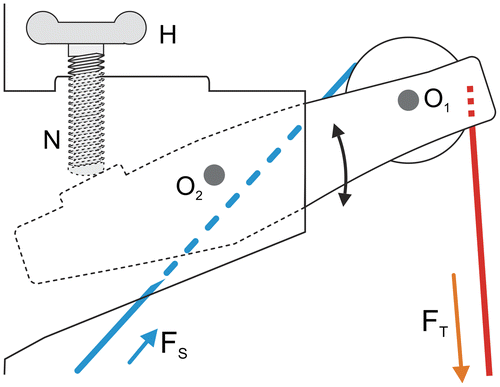
Figure 22. Braking mechanism consisting of a friction belt made of two belts in series; in red, belt with low friction coefficient (μ1); in blue, belt with high friction-coefficient (μ2).
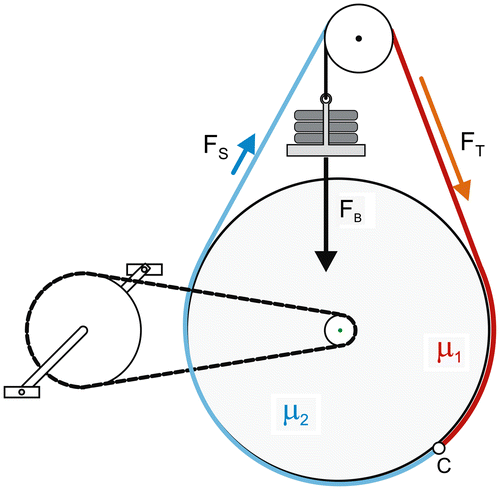
Figure 23. Variation of the location of the center of mass during half a revolution of the flywheel.
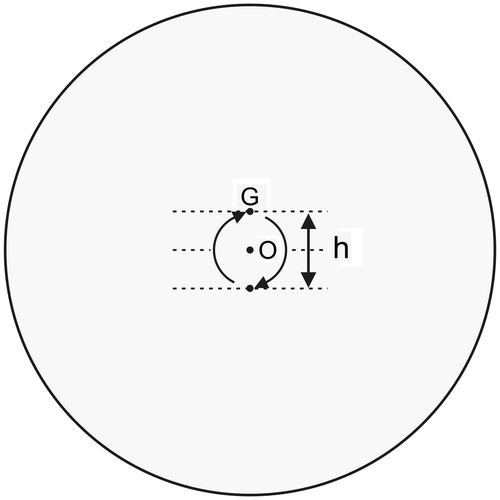
Figure 24. Relationship between ratio μ1/μ2 and descent (D) of the basket from a basket weight equal to 2 kg to a weight equal to 8 kg.
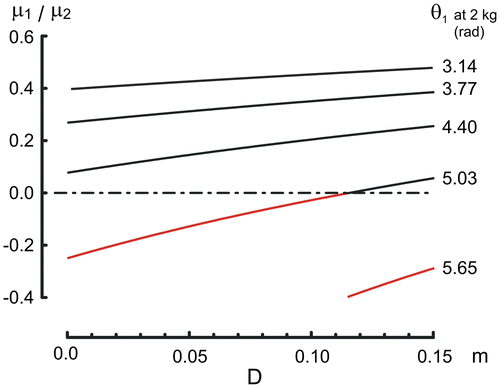