Figures & data
Figure 2. The stress–strain curves of pure nylon 6 at different temperatures for strain rate of (a) 0.33 × 10−3; (b) 1.67 × 10−3; (c) 3.33 × 10−3; (d) 1.67 × 10−2.
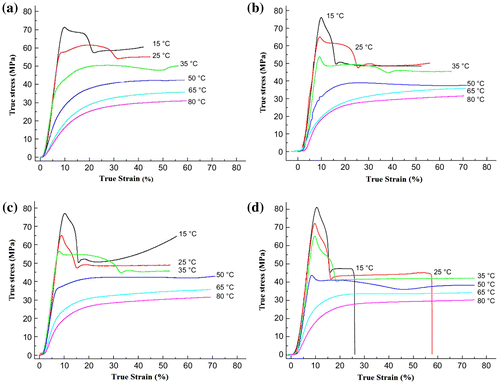
Table 1. Thermal properties of the work-piece and FSP tool, and back-plate
Table 2. The FSP parameters used in the simulation procedure and actual FSP experiment
Figure 3. The macro-surface appearance of the specimen fabricated by the optimum combination of 2,000 rpm for rotational speed and 100 mm/min for traverse speed.
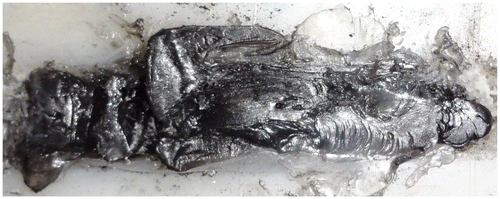
Figure 4. XRD patterns of pure nylon 6 and the specimen fabricated with the optimum combination of FSP parameters.
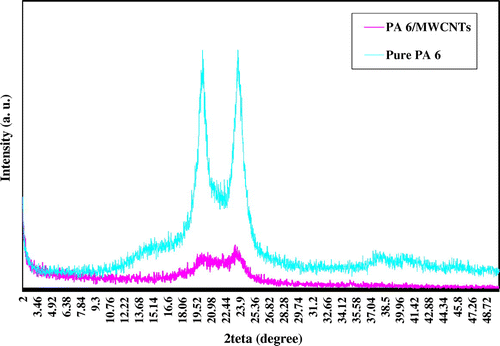
Figure 7. The homogenous dispersion of MWCNTs in matrix of nylon 6 fabricated in 2,000 rpm of rotational speed and 100 mm/min of traverse speed.
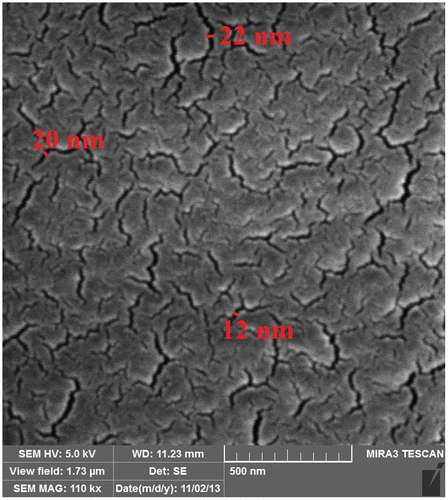
Figure 9. The temperature contours along the tool path after 18 mm tool feed (a) at surface; (b) in midline cross section; (c) in bulk.
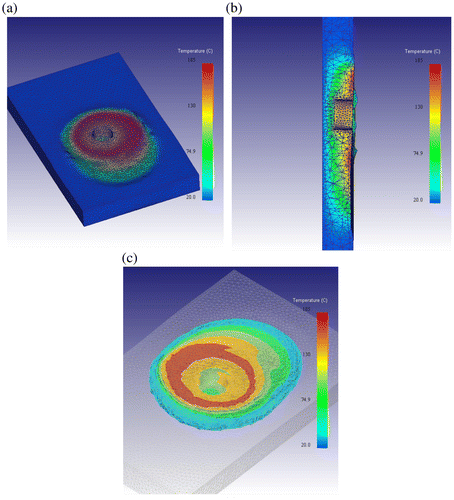
Figure 11. The temperature history of selected points located at advancing and retreating side of work-piece.
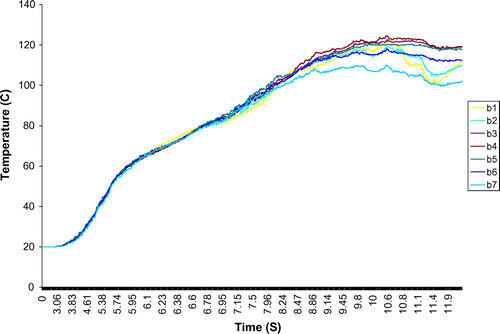