Figures & data
Figure 1. Contact between two cylindrical surfaces (Chula, Citation2017).
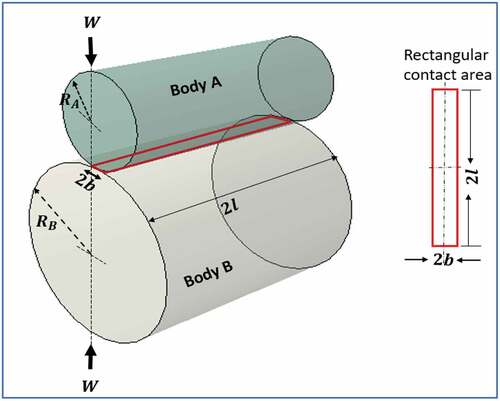
Table 1. Dimensions of cylindrical roller bearing components of an airflow root blower
Table 2. Material properties of cylindrical roller bearing components of an airflow root blower (Salifu et al., Citation2020f, Citation2020e, Citation2020a, Hlebanja et al.)
Table 3. Natural frequency and mode shapes of cylindrical bearing components
Table 4. Comparison of the first eight natural frequencies of cylindrical roller bearing
Figure 11. Temperature distribution profile contour plot and results for the different operating speeds.
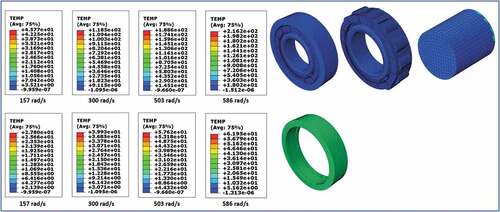
Figure 13. Contour plots and stress distribution profile results for the different operating speeds.
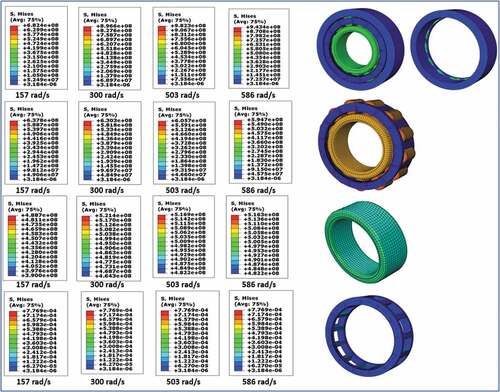
Table 5. Comparison of the FEA and analytically calculated Hertzian stress at 157 rad/s