Figures & data
Figure 1. Schematic of uniform sand-grain roughness model (Adams et al., Citation2012; ANSYS, Citation2019).
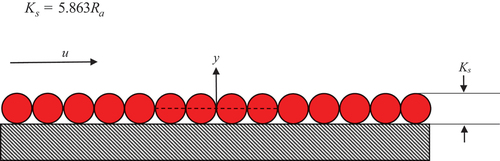
Table 1. Surface roughness level (JIS, Citation2013)
Table 2. Journal bearing parameter
Figure 6. Comparison between the result of the present investigation and the references (Gertzos et al., Citation2008; Wada et al., Citation1974).
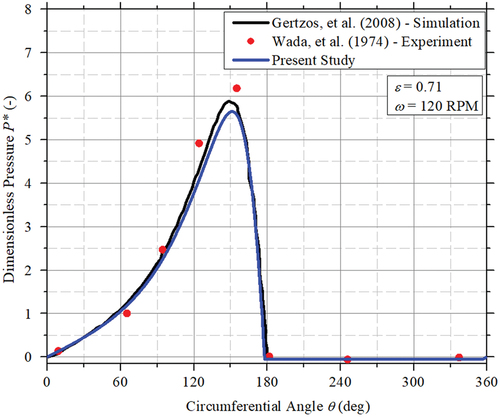
Figure 7. Effect of surface roughness level on (a) load-carrying capacity, (b) friction force, and (c) average acoustic power level.
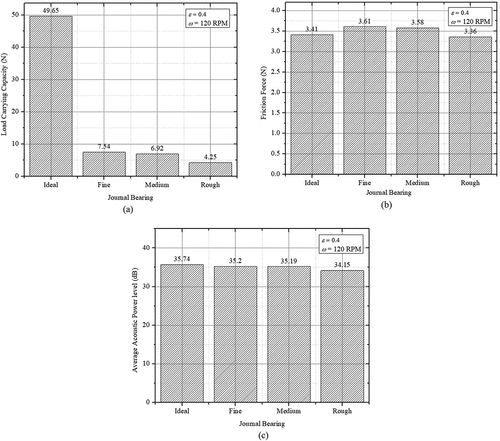
Figure 9. Comparison of pressure contour of the bearing for several roughness levels: (a) Ra = 0 μm (Smooth), (b) Ra = 0.4 μm (Fine), (c) Ra = 1.6 μm (Medium), Ra = 12.5 μm (Rough).
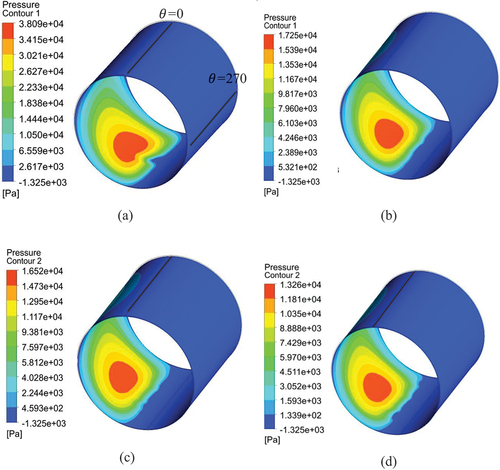
Figure 10. Distribution of hydrodynamic pressure and vapor volume fraction varying surface roughness levels.
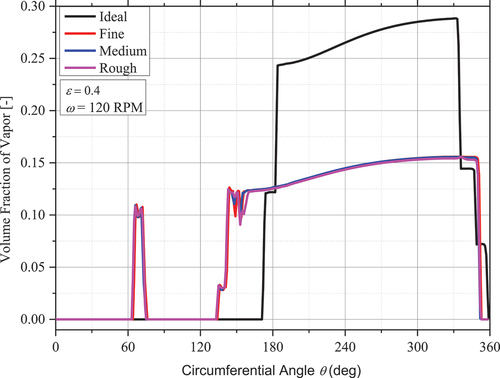
Figure 11. Effect of eccentricity ratio on (a) load-carrying capacity, (b) friction force, and (c) average acoustic power level of the roughed journal bearing.
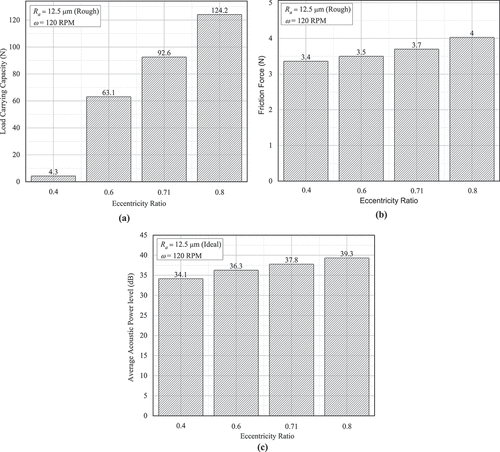
Figure 12. Distribution of acoustic power level of roughed journal bearing varying eccentricity ratios.
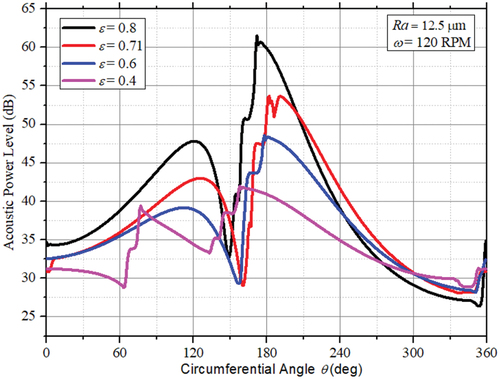