Figures & data
Table 1 Nozzle geometry, calculated pressure drop rate, experimentally determined bubble density, and expansion ratio for SCFX extrudates
Figure 1 Schematic of nozzle geometry. Three nozzle radii, R = 3.00, 2.25, and 1.50 mm, were used to vary pressure drop rates and final bubble density of the starch-based SCFX foam.
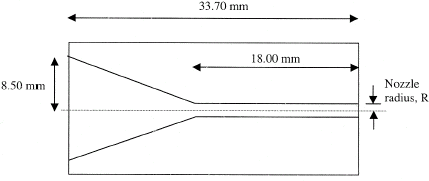
Figure 2 Theoretical pressure profiles in extruder nozzle for three different nozzle radii, R—(i) 3.00 mm, (ii) 2.25 mm, and (iii) 1.50 mm. In the flow restrictor valve and spacer element prior to the nozzle, P drops from 10 MPa to a value determined by R. ΔP/Δt refers to the calculated pressure drop rates in the straight section of the nozzles. The inset shows the nozzle profile with tapered (AB) and straight (BC) sections.
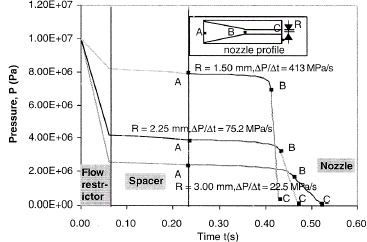
Figure 3 Average bubble diameter (D bubble) and nucleation density (N bubble) vs. nozzle radius for SCFX extrudates.
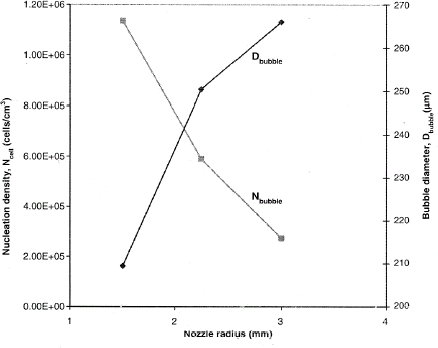