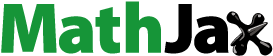
ABSTRACT
This research compared the production processes for mixed rare earth oxide (Nd/Pr oxide) powders from a leach solution obtained from acid baking with nitric acid followed by water leaching. Furthermore, the precipitation behaviour of the constituent elements in the leach liquor was examined. Development of economically feasible processes is significant on an industrial scale. In this regard, Nd/Pr oxide powders were recovered from the leach solution by using oxalic acid, ammonium oxalic acid (C2H2O4), sodium hydroxide (NaOH), and ammonium hydrogen carbonate (NH4HCO3) in a comparative manner. Experimental investigations showed behavioural similarities between C2H2O4 and NH4HCO3 precipitation agents; they precipitate rare earth elements (REEs), selectively. However, NaOH was different from them as it precipitates constituent elements in the leach liquor. The cost of C2H2O4 and NH4HCO3 on the industrial scale is higher than NaOH. The resulting flow diagrams of the preparation of Nd/Pr oxide powders were comprehensively compared and optimised to propose more environmentally friendly, economical, and sustainable process.
Cette recherche a comparé les procédés de production de poudres d’oxydes mixtes de terres rares (oxydes Nd/Pr) à partir d’une solution de lixiviation obtenue de la cuisson acide avec de l’acide nitrique suivie d’une lixiviation à l’eau. En outre, on a examiné le comportement de précipitation des éléments constituants de la liqueur de lixiviation. Le développement de procédés économiquement réalisables est important à l’échelle industrielle. À cet égard, on a récupéré les poudres d’oxyde Nd/Pr de la solution de lixiviation en utilisant de l’acide oxalique, de l’acide oxalique d’ammonium (C2H2O4), de l’hydroxyde de sodium (NaOH) et de l’hydrogénocarbonate d’ammonium (NH4HCO3) d’une manière comparative. Les études expérimentales ont montré des similitudes comportementales entre les agents de précipitation C2H2O4 et NH4HCO3; ils précipitent de manière sélective les éléments de terres rares (ETR). Cependant, NaOH était différent d’eux puisqu’il précipite les éléments constituants dans la liqueur de lixiviation. Le coût du C2H2O4 et du NH4HCO3 à l’échelle industrielle est supérieur à celui du NaOH. On a comparé globalement et optimisé les schémas de procédé résultants de la préparation des poudres d’oxyde Nd/Pr pour proposer un procédé plus écologique, économique et durable.
Introduction
In the twenty-first century, products based on new technologies such as electronic devices, renewable energy systems, and magnetic imaging devices have become the primary source of economic development on a global scale. Rare earth elements (REEs) and permanent magnets are widely employed in technological products and applications and form the basis for the new generation technology. REEs are the list of critical metals owing to their increased demand and the associated supply risk [Citation1–6]. According to the report first published by the European Union Commission in 2011 and most recently in 2023, REEs are the ones with the highest supply risk among critical elements [Citation7]. One of the most common uses of REEs is NdFeB magnets, which are used in a wide variety of high-tech products. Therefore, the recycling of NdFeB magnets is critical for their long-term use [Citation8–10].
Numerous studies have been carried out to recover of REEs from waste NdFeB magnets. Pyrometallurgical and hydrometallurgical methods have been reported [Citation11–13]. To obtain high purity REEs, hydrometallurgical methods, such as precipitation, solvent extraction, or ion exchange methods were employed. Different precipitation methods, such as oxalate precipitation, carbonate precipitation and hydroxide precipitation are mainly employed for the separation. However, the separation of individual REEs from a mixture is complicated owing to the similar physical and chemical properties; hence, separation of REEs generally is carried out by solvent extraction [Citation14]. Apart from solvent extraction, REEs are separated from other metals in acidic medium at pH < 4 by precipitation as oxalate form using oxalic acid. Moreover, REEs are precipitated in the form of REEs and sodium double sulphate salts like NaREEs(SO4)2-xH2O [Citation15,Citation16].
Most procedures recommended in the literature on separation and producing metals after the leaching has been obtained by employing traditional precipitation agents. Han et al. investigated the precipitation behaviour of REEs with various agents, such as phosphate, oxalate, fluoride, carbonate, and sulphate using thermodynamic principle [Citation17]. Silva et al. investigated rare earth oxides precipitation in a purified rare earth solution with sodium carbonate and oxalic acid. While they recovered rare earth oxide with a purity of 94.2% using sodium carbonate, rare earth oxide with a purity of 99.2% were recovered by oxalic acid [Citation18].
In another study, the precipitation of Fe with lime water is one of the methods to remove the Fe from the aqueous solutions at the acidic pH ranges. In the study of Parhi et al. [Citation19], the iron content of the leach liquor was removed by precipitation using lime water-calcium hydroxide (Ca(OH)2). They reported that the initial pH of the leach liquor was 1.52 and the leach liquor was taken in a beaker and stoichiometric amount of H2O2 was added to oxidise the Fe (II) content to Fe (III) followed by addition of Ca(OH)2 until the pH was attained at 4. Their results revealed that the precipitation of Fe increased to 99.9% with increase of pH from 2.0 to 4.01. Moreover, the co-precipitation of other metal ions such as Nd, Pr and B was not observed in that pH range.
In another study, (H2C2O4) was used to precipitate Nd, Dy and B from leach solution after the Fe removal process. For their experiments, oxalic acid was added dropwise into the leached solution containing Nd, Dy and B over a period of 15 min under constant stirring using a magnetic stirrer. The quick formation of precipitates was observed soon after the addition of oxalic acid. The precipitation by oxalic acid showed that 91–92% of Nd and 81–82% of Dy in the solution were recovered in the formation of the precipitate. However, B dissolved in the solution was not recovered by oxalic acid precipitation. Both XRD pattern and chemical analysis data confirmed that Fe was completely removed during Fe precipitation [Citation20]. Although there have been studies on investigation of the precipitation of REEs by various precipitation agents, there has been lack of systematic investigation on precipitation of REEs in the recycling of NdFeB magnets.
In this study, to further optimises the precipitation of REEs from a leach liquor obtained from acid baking followed by water leaching, various precipitation agents for the precipitation of REEs are studied to develop a more economical, efficient recovery of REEs and environmentally friendly process. Furthermore, this research investigates the effect of precipitation agents on the morphology and purity of Nd/Pr oxide powders and the thermal decomposition behaviour of the precipitates.
Material and method
1. | Characterisation of NdFeB magnet powders |
The chemical composition of the NdFeB magnet powders was investigated by X-ray fluorescence (XRF) spectroscopy (Panalytical WDXRF spectrometer, Malvern Panalytical B.V.). Subsequently, NdFeB magnet powders were dissolved in a 3 mol/L of nitric acid solution to define the detailed chemical composition of the NdFeB magnet powders. After the solid and liquid separation by vacuum filtration setup, the solution was analyzed by inductively coupled plasma optical emission spectroscopy (ICP-OES) (Spectro Arcos, Spectro Analytical Instruments). Morphological investigation of NdFeB and elemental mapping of the powders were conducted by scanning electron microscopy (Thermo Fisher Quattro S, FESEM).
2. | Acid Baking of NdFeB magnet powders |
3. | Production of Nd/Pr oxide powders by precipitation agents |
Result and discussion
1. | Chemical analysis of NdFeB magnet powders |
After crushing the EoL demagnetised NdFeB magnets into fine powders, the XRF analysis was conducted to determine their chemical composition. presents the XRF analysis of the magnet powders.
Table 1. Chemical composition of NdFeB magnet powder determined by XRF analysis.
As reported elsewhere [Citation23], high amounts of Fe, Nd and Pr are observed, with the addition of small amounts of Dy, Si, Al, Co, Mn and Pd. For the detailed chemical analysis of the magnet powders, ICP analysis was conducted. The result of ICP-OES analysis of NdFeB magnet’ powders is shown in .
Table 2. Chemical analysis of NdFeB magnet powder determined by ICP analysis.
Elemental mapping of NdFeB magnet powder was conducted by EDX analysis. shows the elemental mapping of the magnet powders.
In addition to XRD and ICP analyses, Fe, Nd, Pr, Dy, and Co were also detected by the elemental mapping technique. The homogenous distribution of constituent elements can be observed in the elemental mapping.
2. | Characterisation of acid baking product and water leaching |
Two reactions can take place during the acid baking depending on the nitric acid concentration, temperature and metal type, these reactions are given in Equations (1) and (2).
(1)
(1)
(2)
(2) Gibbs free energy calculations for both reactions were conducted by HSC Chemistry 9.
shows the reaction Gibbs free energy calculation for acid baking process.
The Gibbs free energy calculations for Nd, Fe and Dy are based on Equations (1) and (2). Both of equations are possible for all metals, but Equation (1) is more thermodynamically favourable.
The morphology and elemental distribution of the selectively oxidised powder were revealed by FE-SEM and EDX, respectively. illustrates the FE-SEM analysis and the EDX analysis of the powders.
Figure 3. (a) elemental mapping of the acid baking product, (b) FE-SEM micrograph of the acid baking product and (c) EDX analysis of the acid baking product (percentage composition).
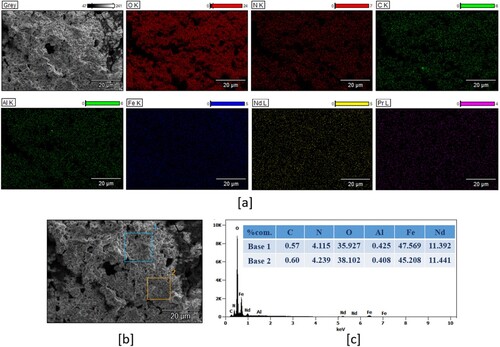
The presence of O, Fe, Nd, and Pr was confirmed by EDX analysis and N was observed owing to rare earth elements being in the nitrate form and Al tub was used for SEM and EDX analysis; therefore, the small amount of Al was observed.
The selectively oxidised powders were leached by water for 2 h. presents the extraction amount of B, Co, Dy, Fe, Pr, and Nd during the water leaching.
Figure 4. Extraction of B, Co, Dy, Fe, Pr, and Nd at water leaching` duration of 30, 60, 90 and 120 min.
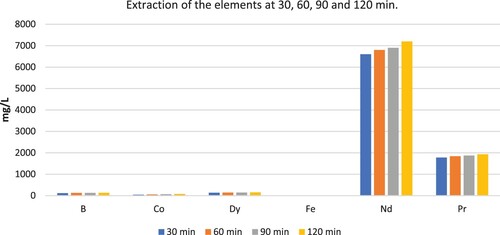
The pH value of the leachate is between 3 and 4. The increase in the leaching time results in a gradual increase in the extraction of Nd, as expected. Along with Nd, small amounts of B, Co, and Dy were extracted during water leaching; moreover, the small amount of Fe extraction was observed. After the selective oxidation, Fe2O3 and REEs(NO3)3 were obtained, while Fe2O3 is not soluble in water, REEs(NO3)3 is soluble in water which allows us to perform the selective leaching of REEs. The expected reaction for REEs during the water leaching is shown in Equation (3).
(3)
(3)
3. | Precipitation behaviours of REEs with different agents |
presents the precipitation behaviours of REEs, B, Co, and Fe at different pH values by NaOH.
REEs were precipitated by NaOH at pH 7–8 and pH 12–13. A higher amount of REEs was precipitated at a pH value of between 12 and 13. Moreover, Fe, Co, and B were precipitated between pH 12 and 13. Unfortunately, REEs, Co, and Fe were co-precipitated by NaOH.
illustrates the precipitation behaviours of REEs, B, Co, and Fe by oxalic acid at different pH values.
REEs were precipitated at pH 2–3 and 3–4. Higher amounts of REEs were precipitated between pH 3 and pH 4 values. When compared to NaOH, a small amount of B and Co were precipitated by oxalic acid. illustrates the precipitation behaviour of the elements at different pH values by NH4HCO3.
At pH between 4 and 5, All REEs in the solution were precipitated and REEs can be precipitated selectively at pH values of 3–4 and 4–5 by oxalic acid. Consequently, high-purity Nd/Pr oxide powders can be achieved by NH4HCO3 and C2H2O4.
4. | Thermal decomposition behaviours of the precipitates |
Figure 8. DTA-TG analysis of the precipitate obtained by C2H2O4 precipitation under air at a heating rate of 10°C min−1.
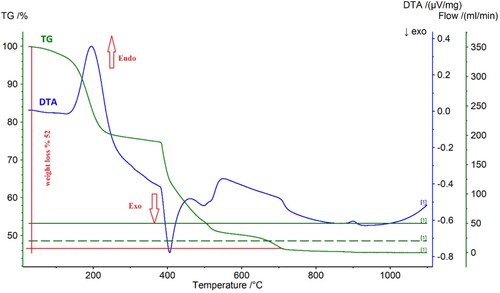
Based on the TG analysis of the precipitate obtained by C2H2O4, the loss of weight of the precipitate has continued until approximately 700°C. An endothermic transition was observed at 200°C owing to the desorption of the physisorbed and chemisorbed water. An exothermic peak was observed at about 400°C and this peak can be attributed to the thermal decomposition of the rare earth oxalate product. The main reaction for obtaining Nd/Pr oxide powders from rare earth oxalate was described in Equation (4).
(4)
(4) DTA TG analysis was performed to investigate the thermal behaviour of the (REE(OH)3) obtained by NaOH. exhibits DTA-TG analysis of the (REE(OH)3).
Figure 9. DTA-TG analysis of the precipitate obtained by NaOH precipitation under air at a heating rate of 10°C min−1.
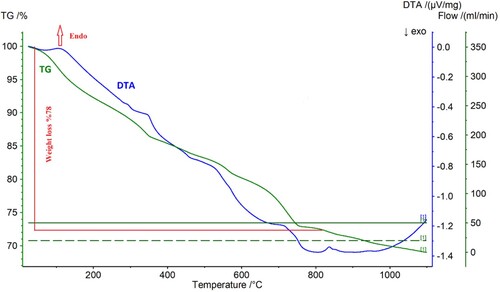
As can be seen , the thermal decomposition of REE(OH)3 occurs in two major stages. The desorption of the adsorbed water can be attributed the wide peak in the range of 30°C and 220 °C. The decomposition of rare earth elements hydroxide into Nd/Pr oxide powders can be observed in the range of 220 and 700 °C. After approximately 770°C, the weight loss continued; however, gradually slowed. The main equation for the formation of Nd/Pr oxide powders by NaOH can be described as follows.
(5)
(5) illustrates DTA-TG analysis of the precipitate obtained by NH4HCO3. The analysis was conducted in the temperature range of 30–1100°C.
Figure 10. DTA-TG analysis of the precipitate obtained by NH4HCO3 precipitation under air at a heating rate of 10°C min−1.
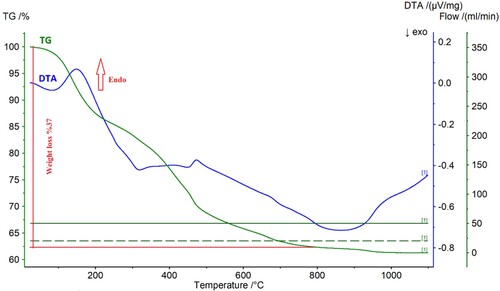
At approximately between 100°C and 210°C, an endothermic peak was observed, which was ascribed to the loss of physical and crystal water. The phase transformation of the REEs carbonate to Nd/Pr oxide powders can be observed in the range of 300°C and 700°C. The straight line on the TG curve between 700°C and 1100°C shows the formation of Nd/Pr oxide powders with no further significant weight loss. The reaction of the preparation for Nd/Pr oxide powders by NH4HCO3 is given as follows
(6)
(6) presents the FTIR analyses of the precipitates, Nd/Pr oxide powders calcined at various temperatures.
Figure 11. FTIR spectrum of REEs powders before and after calcination at 600, 700 and 800°C; (a) REEs-oxalate, (b) REEs-hydroxide, and (c) REEs-carbonate.
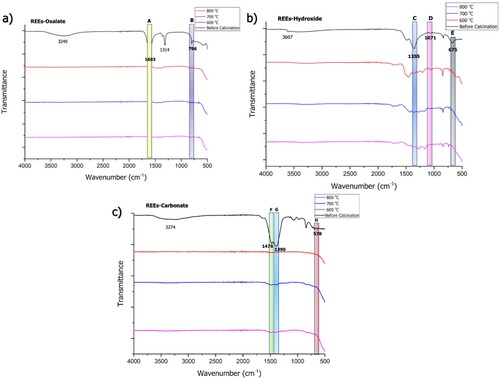
As can be seen in (a) REEs-oxalate gives peaks related to OH bonds at 3240 cm−1, C–O bond vibration at 1603 cm−1 (A), and the O-M-O bond vibration peak at 796 cm−1 (B) in the FTIR spectrum [Citation24]. In the REEs-hydroxide FTIR spectrum, OH bond vibration at 3607 cm−1, the vibration of NO3- bond remaining from water leaching at 1355 cm−1 (C), and REEs-OH bond vibration at 1071 (D) and 675 cm−1 (E) were observed [Citation25]. In the REEs-carbonate FTIR spectrum, peaks related to the stretching of O–H bonds originating from water remaining in the structure were observed at 3274 cm−1, as well as peaks for the characteristic REEs-carboxyl groups at 1476 (F) and 1398 cm−1 (G), the vibration of carboxyl groups at 840 cm−1, and the REEs-O vibration at 578 cm−1 (H) (see [a]) [Citation26]. The characteristic A and B peaks of the REEs-oxalate structure disappear with the calcination process. Similarly, the D and E peaks, belonging to the characteristic REEs-OH bond of the REEs-hydroxide structure, as well as the C peak of the nitrate group, also disappear with increasing temperature. The characteristic carboxyl group peaks in the REEs-carbonate structure (F and G), as well as the REEs-O peak (H), were observed to disappear with high temperature.
5. | Characterisation of Nd/Pr oxide powders |
Figure 12. SEM micrographs of the dried powders precipitated by (a) NH4HCO3, (b) NaOH, and (c) C2H2O4.
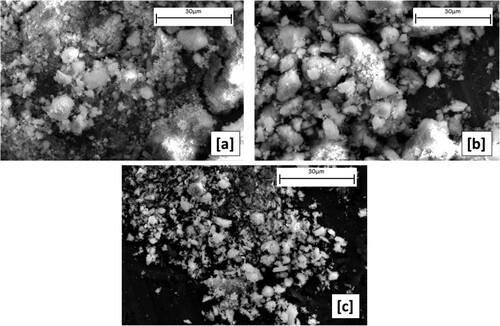
The precipitated Nd/Pr oxide powders by using NH4HCO3 and drying at 65°C have an irregular shape. The particle agglomeration was observed, as can be seen in (a). The produced particles by using NaOH as a precipitating agent have dense morphology and irregular shape. These particles show wide particle size distribution. Moreover, as it can be observed in (c), the particles precipitated by C2H2O4 had an irregular shape and smaller particle size, when compared to the particles precipitated by NaOH and NH4HCO3.
presents the SEM micrographs of Nd/Pr oxide powders calcined at 800°C and precipitated by NH4HCO3 [a], NaOH [b], and C2H2O4 [c].
Figure 13. SEM micrographs of Nd/Pr oxide powders calcined at 800°C and precipitated by NH4HCO3 (a), NaOH (b), and C2H2O4 (c).
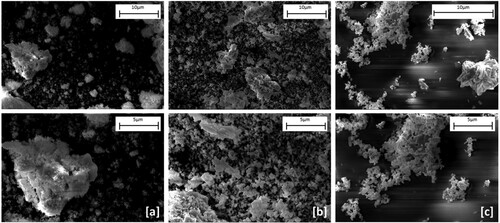
The produced Nd/Pr oxide powders by using NH4HCO3 as a precipitation agent and calcining at 800oC tend to agglomerate, as can be seen in (a). As illustrated in (b) and (c), the produced Nd/Pr oxide powders had a nearly spherical shape. Moreover, the rodlike morphology can be observed in (c). When sintering or pelleting the powders which are produced by NaOH and C2H2O4, the spherical morphology would be advantageous for those processes. In addition, the particle morphology influences on particle performance. Depending on the application, spherical morphology would present high performance owing to the high surface area of them.
When comparing all precipitation agents for REEs, NH4HCO3 and C2H2O4 show better performance on the separation of REEs from other elements, including Fe, Co, and B in the leach solution. Therefore, Nd/Pr oxide powders produced with oxalic acid were selected for an elemental mapping. The elemental mapping and EDX analysis of Nd/Pr oxide powders were given in .
Figure 14. (a) elemental mapping of the Nd/Pr oxide powders, (b) FE-SEM micrograph of Nd/Pr oxide powders, and (c) EDX analysis of the Nd/Pr oxide powders (percentage composition).
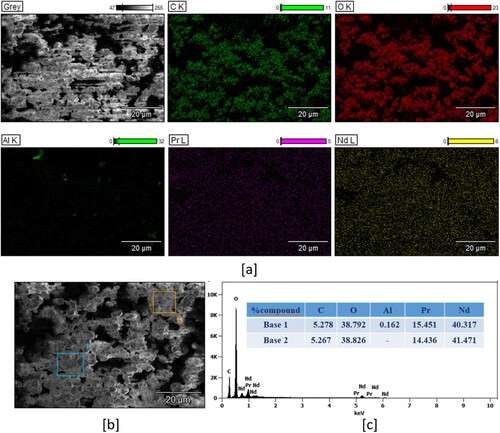
The presence and uniform distribution of Nd, Pr, and O are evident from the elemental mapping of Nd/Pr oxide powders and well-defined EDX peaks in (c). The presence of Al is coming from the SEM stub.
exhibits the XRD analysis of Nd/Pr oxide powders precipitated by C2H2O4 and calcined at different temperatures.
Figure 15. XRD analyses of the Nd/Pr oxide powders precipitated by C2H2O4 and calcined at 600°C, 700°C and 800°C.
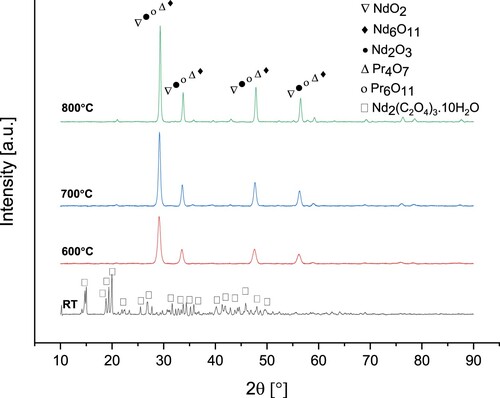
The diffraction peaks of the precipitate powders by C2H2O4 show the crystal structure of Nd2(C2O4)3·10H2O (JCPDS data card No. 20-0764). The XRD patterns of Nd/Pr oxide powders calcined at varying calcination temperatures from 600°C to 800°C are NdO2, Nd6O11, Nd2O3, Pr4O7, and Pr6O11. The XRD patterns of Nd/Pr oxide powders were consistent with standards JCPDF 46-1074, JCPDF 45-0087, JCPDF 21-0579, JCPDF 03-065-6027, and JCPDF 42-1121, respectively. Whereas XRD patterns of the sample calcined at 600 °C had lower intensity peaks, the powders calcined at 800°C exhibited higher peaks intensity, indicating higher crystallinity of the powders.
XRD analyses Nd/Pr oxide powders precipitated by NaOH were shown in .
Figure 16. XRD analyses of Nd/Pr oxide powders precipitated by NaOH and calcined at 600°C, 700°C and 800°C.

The diffraction peaks of the precipitate powders at room temperature reveal the presence of Nd(OH)3 phase compatible with JCPDS card no 06-0601. NdO2, Nd6O11, Nd2O3, Pr4O7, and Pr6O11 phases were observed in the calcined powders at different temperatures. presents the XRD analyses of Nd/Pr oxide powders precipitated by NH4HCO3 and calcined at various temperatures.
Figure 17. XRD analyses of Nd/Pr oxide powders precipitated by NH4HCO3 and calcined at 600°C, 700°C and 800°C.
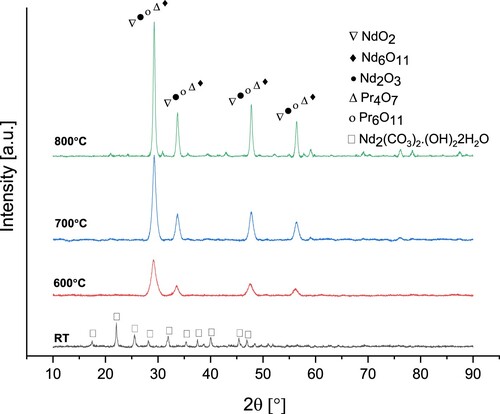
The XRD pattern of the powders precipitated at room temperature shows the characteristic peaks of the Nd2(CO3)2(OH)2·2H2O (JCPDS card 46-0371). Nd/Pr oxide powders produced with NH4HCO3 have the same crystalline structure as Nd/Pr oxide powders synthesised with C2H2O4 and NaOH. According to XRD and FTIR analyses, calcination temperatures of 700°C and 800°C are suitable for producing highly crystalline Nd/Pr oxide powders.
Conclusion
In this study, acid baking followed by precipitation route is proposed to produce Nd/Pr oxide powders from waste NdFeB magnet. Consequently, highly crystalline Nd/Pr oxide powders were produced by all precipitation agents NH4HCO3, C2H2O4, and NaOH after the calcination process at 700°C and 800°C under air atmosphere. The recovery efficiency of REEs with all precipitation agents are more than approximately 99.5%. The purities of the Nd/Pr oxide powders precipitated by NH4HCO3 and C2H2O4 are higher than the powders produced by NaOH. Oxalic acid precipitation method produces a large amount of wastewater but has advantages of easy filtration and good crystallisation even at 600°C. In addition, NH4HCO3 precipitation method also produces a large amount of wastewater, including ammonia nitrogen and various elements. In consideration of environmental responsibilities and economic concern, NaOH might be potential precipitation agent for industrial application. Moreover, the impurities, such as B and Co in the produced Nd/Pr oxide powders by NaOH can be acceptable in case of the powders are used in the production of NdFeB magnets.
Disclosure statement
The authors declare that they have no known competing financial interests or personal relationships that could have appeared to influence to this work.
References
- Bide T, Brown TJ, Gunn AG, et al. Utilisation of multiple current and legacy datasets to create a national minerals inventory: a UK case study. Resources Policy. 2020;66:101654. doi:10.1016/j.resourpol.2020.101654
- Blagoeva D, Pavel C, Wittmer D, et al. (2019). Materials dependences for dual-use technologies relevant to Europe's defence sector.
- Glöser S, Espinoza LT, Gandenberger C, et al. Raw material criticality in the context of classical risk assessment. Resour Policy. 2015;44:35–46. doi:10.1016/j.resourpol.2014.12.003
- Lewicka E, Guzik K, Galos K. On the possibilities of critical raw materials production from the EU’s primary sources. Resources. 2021;10(5):50), doi:10.3390/resources10050050
- Mudali UK, Patil M, Saravanabhavan R, et al. Review on E-waste recycling: part II—technologies for recovery of rare earth metals. Trans Indian Natl Acad Eng. 2021;6(3):1–19. doi:10.1007/s41403-021-00231-0
- Silvestri L, Forcina A, Silvestri C, et al. Circularity potential of rare earths for sustainable mobility: recent developments, challenges and future prospects. J Clean Prod. 2021;292:126089. doi:10.1016/j.jclepro.2021.126089
- Blengini GA, El Latunussa C, Eynard U, et al. Study on the EU's list of critical raw materials. Brussels: Publications Office of the European Union; 2020.
- Lucas J, Lucas P, Le Mercier T, et al. Rare earths: science, technology, production and use. Amsterdam: Elsevier; 2014.
- Charalampides G, Vatalis KI, Apostoplos B, et al. Rare earth elements: industrial applications and economic dependence of Europe. Procedia Econ Finance. 2015;24:126–135. doi:10.1016/S2212-5671(15)00630-9
- Biesiekierski A, Li Y, Wen C. The application of the rare earths to magnesium and titanium metallurgy in Australia. Adv Mater. 2020;32(18):1901715. doi:10.1002/adma.201901715
- Bian Y, Guo S, Tang K, et al. Recovery of rare earth elements from NdFeB magnet scraps by pyrometallurgical processes. Rare Met Technol. 2016;2015:239–248. doi:10.1007/978-3-319-48188-3_27
- Uysal E, Al S, Emil-Kaya E, et al. Hydrometallurgical recycling of waste NdFeB magnets: design of experiment, optimisation of low concentrations of sulphuric acid leaching and process analysis. Can Metall Q. 2023;62(1):107–118. doi:10.1080/00084433.2022.2058152
- Kumari A, Sahu SK. A comprehensive review on recycling of critical raw materials from spent neodymium iron boron (NdFeB) magnet. Sep Purif Technol. 2023;317:123527. doi:10.1016/j.seppur.2023.123527
- Akcil A, Ibrahim YA, Meshram P, et al. Hydrometallurgical recycling strategies for recovery of rare earth elements from consumer electronic scraps: a review. J Chem Technol Biotechnol. 2021;96(7):1785–1797. doi:10.1002/jctb.6739
- Han KN. Characteristics of precipitation of rare earth elements with various precipitants. Minerals. 2020;10(2):178. doi:10.3390/min10020178
- Chi RA, Xu ZG. A solution chemistry approach to the study of rare earth element precipitation by oxalic acid. Metall Mater Trans B. 1999;30:189–195. doi:10.1007/s11663-999-0047-0
- Han KN. Characteristics of precipitation of rare earth elements with various precipitants. Minerals. 2020;10(2):178. doi:10.3390/min10020178
- Silva RG, Morais CA, Teixeira LV, et al. Selective precipitation of high-quality rare earth oxalates or carbonates from a purified sulphuric liquor containing soluble impurities. Min Metall Explor. 2019;36:967–977. doi:10.1007/s42461-019-0090-6
- Parhi PK, Sethy TR, Rout PC, et al. Separation and recovery of neodymium and praseodymium from permanent magnet scrap through the hydrometallurgical route. Sep Sci Technol. 2016;51(13):2232–2241. doi:10.1080/01496395.2016.1200087
- Rabatho JP, Tongamp W, Takasaki Y, et al. Recovery of Nd and Dy from rare earth magnetic waste sludge by hydrometallurgical process. J Mater Cycles Waste Manage. 2013;15:171–178. doi:10.1007/s10163-012-0105-6
- Önal MAR, Aktan E, Borra CR, et al. Recycling of NdFeB magnets using nitration, calcination and water leaching for REE recovery. Hydrometallurgy. 2017;167:115–123. doi:10.1016/j.hydromet.2016.11.006
- Emil-Kaya E, Stopic S, Gürmen S, et al. Production of rare earth element oxide powders by solution combustion: a new approach for recycling of NdFeB magnets. RSC Adv. 2022;12(48):31478–31488. doi:10.1039/D2RA05876F
- Emil-Kaya E, Polat B, Stopic S, et al. Recycling of NdFeB magnets employing oxidation, selective leaching, and iron precipitation in an autoclave. RSC Adv. 2023;13(2):1320–1332. doi:10.1039/D2RA06883D
- Marins AAL, Banhos SG, Muri EJB, et al. Synthesis by coprecipitation with oxalic acid of rare earth and nickel oxides from the anode of spent Ni–Mh batteries and its electrochemical properties. Mater Chem Phys. 2020;242:122440. doi:10.1016/j.matchemphys.2019.122440
- Wang Y, Liu Y, Guo T, et al. Lanthanum hydroxide: a highly efficient and selective adsorbent for arsenate removal from aqueous solution. Environ Sci Pollut Res. 2020;27:42868–42880. doi:10.1007/s11356-020-10240-1
- Yin, J. Q., Zou, Z. Q., & Tian, J. (2020). Preparation of crystalline rare earth carbonates with large particle size from the lixivium of weathered crust elution-deposited rare earth ores. Int J Miner Metall Mater, 27, 1482–1488. doi:10.1007/s12613-020-2066-4