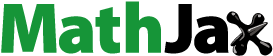
Abstract
Blended textile fabrics with dyed cotton and polyester (PET) fibres intimately mixed are extensively used in the textile industry. Separating and recycling these blends cannot be performed by conventional mechanical or chemical recycling processes, and this is contributing significantly to the global textile waste problem. Here we demonstrate an approach to separate coloured cotton and polyester blends, and the dye is retained in the separated polyester and cotton components. The separation was achieved via chemical dissolution of cotton using a co-solvent system of ionic liquid and dimethyl sulfoxide, from which regenerated cellulose fibres could be directly wet spun. The polyester component was left intact and recovered via filtration. The recovered products were characterised for thermal, chemical, mechanical, colour strength, and morphological properties.
Introduction
A major roadblock to the textile recycling effort is the use of blended fabrics. Fabrics with cotton and polyester (PET) fibres intimately mixed (polycotton blends) are one of the most common blended textiles (Subramanian et al., Citation2022). Cotton and polyester are blended to impart fabrics with the desirable properties of each fibre type. The cotton gives fabric a soft feel with high water absorbency while the polyester lends its great mechanical properties to the fabric (Palme et al., Citation2017). In terms of sustainability, combining cotton and polyester has an initial positive impact, with the strength of the polyester allowing the fabric to be more durable and thus have a theoretical longer serviceable life cycle. However, in the current linear model, garments are readily discarded to landfill after minimal uses. Efforts to recycle textiles is increasing worldwide and recycling of single component garments has matured for both mechanical and chemical recycling approaches with international brands such as Hennes & Mauritz AB (H&M), Patagonia, Inc., and Levi Strauss & Co. (Levi’s) incorporating recycled fibres in their products (Keh, Citation2021; Patagonia, Citation2021; Levi Strauss & Co, Citation2021). Harmsen et al. (Harmsen et al., Citation2021) provide a detailed account of the current organisations and technologies available to recycle single stream materials for polyester and cotton. Many organisations require the recycled product to be blended with virgin material to achieve industrial quality fabrics, however brands such as Ambercycle, Inc. and Evrnu SPC have claimed to create products using 100% recycled polyester (Ambercycle, Citation2021) and cellulosic material (Evrnu, Citation2020). Due to the chemical differences between polyester and cotton, efficient separation of blended fabrics without degradation to one or both components remains a challenge with many approaches remaining at the research level (Subramanian et al., Citation2022). A partnership between the Hong Kong Research Institute of Textiles and Apparel (HKRITA) and the H&M Foundation has resulted in a promising technology for commercial separation of polyester-cotton blends termed ‘The Green Machine’ (Ellen MacArthur Foundation, Citation2021).This technology employs a hydrothermal method to separate blends using heat, pressure, and a small concentration of ‘green chemicals’ (Keh, Citation2021). The polyester is recovered in the form of fibres which can be blended with virgin material for yarns through a typical mechanical recycling process. The cotton component is degraded and powdered, and it has been stated that the cellulosic material retained is ‘too short and powdery to be turned into fiber’ (Keh, Citation2021). Therefore, the challenges remain for retaining both blended materials as high-value textile products.
Recent studies have proposed various methods to separate intimately blended polycotton textiles. Techniques used have involved either dissolution or depolymerisation of polyester whilst attempting to retain the cotton (Palme et al., Citation2017; Ling et al., Citation2019; Motte & Palme, Citation2019) or cotton dissolution/degradation whilst attempting to retain the polyester (Ouchi et al., Citation2010; De Silva et al., Citation2014; Haslinger et al., Citation2019). Ling et al. focused on depolymerisation of the polyester using phosphotungstic acid aqueous solution and filtered to obtain residues of polyester, blended fibres, and Microcrystalline Cellulose (MCC) (Ling et al., Citation2019) whilst Motte & Palme successfully demonstrated the recycling of polycotton blends into PET monomers and regenerated cellulose fibres (RCFs) with the use of sodium hydroxide solution (Motte & Palme, Citation2019). Ouchi et al. used high concentrations of sulfuric acid to completely degrade the cellulose in the blend whilst leaving the polyester unharmed (Ouchi et al., Citation2010) whilst studies by De Silva et al. and Haslinger et al. both used ionic liquids to dissolve the cotton whilst retaining the polyester (De Silva et al., Citation2014; Haslinger et al., Citation2019). Sun et al. (Sun et al., Citation2021) succeeded in separating polyester-cotton and polyester-wool blended fabrics using ionic liquid to dissolve the natural fibres. Interestingly, these researchers were able to create recycled cellulosic fibres via wet spinning and recycled PET fibres via melt spinning using the recovered materials (Sun et al., Citation2021). Many of these techniques involve the use of chemicals known to bleach cotton or polyester fabrics, leading to the need for further dyeing or colouring of any new products made from the recovered materials. Recycling polyester and cotton can significantly reduce the impact of textiles on the environment, however if re-dyeing of recycled products is required the environmental benefits will be significantly impaired.
Whilst the awareness surrounding textile recycling is increasing, many aspects of the textile industry are still environmentally unsustainable. The textile industry is a major consumer of fresh water and one of the worst polluters of water globally (Yuan et al., Citation2013; Chen et al., Citation2021). A significant contributor to this water consumption and subsequent pollution is the colouration of textiles - the dyeing process (Chen et al., Citation2021; Esteve-Turrillas & de la Guardia, Citation2017). The dyeing of polycotton blends is a time- and energy-intensive process, as the two fibre types require different dyeing agents and process parameters (Wakelyn et al., Citation2006). The polycotton dyeing process is traditionally a two-bath process that requires multiple rinses with fresh water (Zhou et al., Citation2022). Cotton is typically dyed using reactive dyes; this process requires large amounts of salt to improve the affinity of the dye to the cotton, hence resulting in effluents containing reactive dyes, salt complexes, and other auxiliary chemicals (Wakelyn et al., Citation2006; Kim et al., Citation2017). Polyester is typically dyed using dispersive dyes, again significant amounts of water and chemicals are used in the process (Wakelyn et al., Citation2006; Xu et al., Citation2016). Due to the quantity and variety of chemicals used in the dyeing process, the effluent produced from a dye house is complex and this has created tremendous environmental issues for local rivers and water ways near the dye houses, with pollution having adverse impacts on the entire community (Better Thinking Ltd, Citation2006).
Here we report a chemical technique for the separation and recycling of pre-consumer polycotton waste fabric. The original colour of the waste textile is maintained in the separated fibres, eliminating or reducing the need to redye the recycled fibres whilst retaining the value of both the polyester and the cotton. The current work utilizes a binary solvent containing an ionic liquid (IL), namely 1-butyl-3-methylimidazolium acetate ([Bmim]OAc), and dimethyl sulfoxide (DMSO). The polyester is recovered without any obvious degradation and the cotton is processed into a regenerated cellulose fibre (RCF) with similar tenacity (strength) to the most common commercial RCF—viscose (Michud et al., Citation2016). Importantly, both fibre types retain the colour of the original fabric indicating that re-dyeing of the recycled fibres can be reduced or avoided. The approach here is to use the IL/DMSO solvent system to preferentially dissolve the cotton whilst leaving the polyester intact. The choice of ionic liquid as a ‘green’ solvent here stems from the number of different ways ionic liquids can be recovered (Mai et al., Citation2014) and the ability for ionic liquids to dissolve cellulose over multiple recycling cycles (Elsayed et al., Citation2020). shows the starting waste 80% polyester/20% cotton polycotton fabric as well as the separated, recovered polyester and RCF. The polyester remains unchanged by the process, whilst the cotton fibres have been entirely removed from the fabric and recycled via regeneration into new, coloured fibres.
Experimental methodology
Materials
The following fabrics were obtained from a local retailer (Spotlight, Australia) to act as pre-consumer waste textiles; 100% polyester fabric (blue), polycotton fabric (80% polyester, 20% cotton) (blue), 100% cotton fabric (orange). Two types of blends were assessed here: a purchased 80/20 polyester/cotton blend and a manually mixed 50/50 polyester/cotton blend. The dye history of the fabrics was not certain, however the common dye processes for these fabrics mentioned in the introduction were assumed to apply here. That is, the dyes used were assumed to be reactive dyes for the cotton and disperse dyes for the polyester. The polycotton fabric samples were put through the process in both a fabric form and a chopped snippet form. The 100% polyester and 100% cotton were prepared in the chopped snippet form to enable mixing. The solvents used were dimethyl sulfoxide (Sigma Aldrich) and 1-butyl-3-methylimidazolium acetate ([Bmim]OAc) ≥95% (IoLiTec), both of which were used as received. The sulfuric acid used was 98% purity and diluted to 0.5 wt% before use.
Separation process
The chopped snippets and fabric samples were treated in aqueous solution containing 0.5 wt% sulfuric acid to lower the degree of polymerisation (DP) of the cotton component. The fabric concentration in the sulfuric acid aqueous solution was 5 wt% for the 80/20 polycotton blend and 2 wt% for the 50/50 mixed polyester and cotton. This ensured the percentage weight of cotton in each pre-treatment remained consistent at 1 wt% with a sulfuric acid to cotton ratio of 1:2. The solution was heated to 75 °C before the fabrics were added, after which the solution was kept at constant temperature for 1 h under magnetic stirring at 250 RPM. The pre-treated fabrics were filtered, rinsed with deionised water, and oven dried. The methodology used to dissolve and regenerate the cotton portion of the samples closely followed the process used in a previous study where 100% cotton fabric was dissolved and regenerated into cellulose fibres exhibiting good mechanical and morphological properties whilst retaining the colour (Ma et al., Citation2020). The samples were then treated with the binary solvent system of 80% DMSO and 20% ionic liquid. The cotton concentration in the solvent system was 6 wt% leading to a fabric concentration of 30 wt% for the 80/20 polycotton blend and 12 wt% for the 50/50 mixed polyester and cotton. The dissolution involved addition of DMSO under manual stirring before addition of ionic liquid and subsequent stirring. The solution was then processed in a conditioning mixer (THINKY ARE-250 Mixing and Degassing Machine) with speeds ranging from 500 to 2000 RPM for a period of approximately 30 min. After a 24-hour period, the solution was filtered using a syringe filter containing a metal mesh with a 15 µm pore size. The cellulose dope filtrate was collected for spinning whilst the solid polyester material was collected, washed, and dried. The recovered polyester was subject to a rinsing step using DMSO to remove residual cellulose solution before being air-dried.
Spinning parameters
Wet-spinning was employed to create the regenerated cellulose fibres using a pilot wet-spinning line (Dissol, South Korea). The cellulose dope was loaded into the barrel of the spinning gear-pump and heated to 70 °C. The dope was extruded through a 100-hole spinneret at a rate of 1 m/min into a coagulation bath containing water at approximately 20 °C before being washed in a water bath at 60 °C. The fibres were automatically wound onto rollers. The wind-up speed of the rollers was varied starting at 1 m/min and increasing to 6 m/min to achieve fibres with draw ratios (wind-up speed divided by extrusion speed) from 1 to 6, respectively. The spun fibres were then washed in ambient-temperature deionised water before being air dried for 48 h.
Characterisation
Thermal analysis
Thermogravimetric analysis (TGA) was used to measure the thermal decomposition of the samples and confirm the separation of the blended materials. Measurements were obtained using a TA Q50 TGA (TA Instruments). Approximately 5–10 mg of material was loaded into a platinum pan and heated under inert conditions (N2). The samples were heated from 30 to 500 °C at a rate of 10 °C/minute. Differential scanning calorimetry (DSC) was used to further assess the thermal properties of the polyester samples. Approximately 2.5 mg of material was loaded and crimped into the sample pan and the reference pan was left empty. Samples were kept at 10 °C for 2 min before being heated to 310 °C and kept at this temperature for 2 min, after which the samples were cooled back to 10 °C. The heating and cooling rate was 20 °C/min. The temperature cycle was completed once to eliminate the thermal history of the samples before being repeated. The repeat cycle contained the data for analysis.
Scanning electron microscopy (SEM)
The morphologies of the fabrics and recovered materials were observed using a Zeiss Supra 55VP scanning electron microscope. This allowed for both detection of any changes in fibre morphology before and after separation and confirmation that cotton had been removed from the polycotton blend. The electron high-tension was 5.0 kV at a working distance of 9.7 mm. All samples were fixed to a carbon tape and coated in 5 nm of gold (Au) before imaging.
Fourier transform infrared spectroscopy (FTIR)
Attenuated Total Reflectance-Fourier Transform Infrared Spectroscopy (ATR-FTIR) was used to identify changes and similarities in molecular bonds of the samples and therefore detect signs of degradation in recovered polyester samples. A Bruker Vertex 70 FTIR was used. A scan resolution of 4 cm−1 was used, and scans were taken in the range of 600–4000 cm−1. The sample scan time was 32 scans, and the data was normalised.
Reflection spectrophotometry
A Datacolor600 spectrophotometer was used to measure the colour strength and colour difference in the different samples. An aperture size of 9 mm was used, and all samples were contained in transparent LDPE bags. Samples were folded multiple times to ensure no light could pass through to the sample holder. Three scans per sample were completed and the mean was taken, using the standard deviation to show the range. The spectrophotometer software automatically calculated the colour strength (K/S) from the reflectance percentage (R) according to EquationEquation 1(1)
(1) (Whetzel, Citation2008) below.
(1)
(1)
where R is the reflectance, K is the absorption coefficient, and S is the scattering coefficient.
To measure the similarity of colour between materials the colour difference, ΔE, between the original materials and the recovered materials was calculated. This was done using EquationEquation 2(2)
(2) below. The data from the spectrophotometry measurements contains values for CEILab coordinates L*, a*, and b*, which were used in the equation (Haslinger et al., Citation2019).
(2)
(2)
Where ΔE is the difference in colour between two measurements, ΔL* is the difference in lightness and darkness, Δa* is the difference in red and green, and Δb* is the difference in yellow and blue. shows the description related to certain values of colour difference as described by Haslinger et al. (Haslinger et al., Citation2019).
Table 1. Descriptions for different values for the colour difference.
Mechanical properties of regenerated cellulose fibres
The mechanical properties of the recycled cellulose fibres were tested using a Favimat tensile testing device (Textechno, Germany). The tests were performed under ambient temperature and humidity, using a gauge length of 20 mm, a pre-tension of 1.1 cN/tex and a testing rate of 2 mm/min. The samples mass density was estimated to be 1.5 g/cm3. For each sample, 25 individual fibres were tested. The outliers were removed to obtain an average (mean) and standard deviation for the properties. The properties measured were linear density, elongation at break, elastic modulus, and tensile strength (tenacity).
Results and discussion
Thermal decomposition and melt characteristics of recovered polyester
shows the thermal decomposition for 100% polyester fabric, 80/20 polycotton (80% polyester, 20% cotton) fabric, and the recovered polyester which was separated and retained from the 80/20 polycotton blend. The onset of thermal decomposition (Td) for the recovered polyester was 414 °C, which was slightly higher than the 100% polyester fabric, found to have a Td of 402 °C. The thermal degradation profile for the 80/20 polycotton blend clearly shows a two-step decomposition profile, the initial step corresponds to the decomposition of the cotton component with a Td of approximately 293 °C and an approximate 20% loss of mass. The second step corresponds to the decomposition of the polyester at approximately 405 °C accounting for the remaining 80% weight loss. The small difference in decomposition onset temperature observed for the recovered polyester and the 100% polyester may be attributed to different finishes applied to the two different fabrics, or slightly different production parameters for each material (Jaffe & East, Citation2006). To further assess the impact of the separation process here on the thermal decomposition of polyester, a 100% polyester sample was treated with an identical separation process as the polycotton blend. The thermal decomposition data for the treated and untreated 100% polyester are found in . The treated and untreated 100% polyester samples proved to have very similar decomposition behaviour before and after treatment indicating this separation process does not influence the thermal decomposition onset temperature of polyester.
Figure 2. (a) Thermal gravimetric analysis (TGA) data displaying the thermal decomposition of 100% polyester fabric, recovered polyester, and the 80/20 polycotton blend, (b) thermal decomposition of treated and untreated 100% polyester, and (c) Differential Scanning Calorimetry (DSC) data showing the melt characteristics of 100% polyester and recovered polyester from the 80/20 blend.
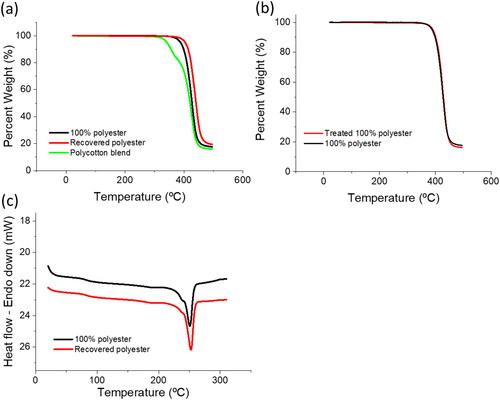
The thermal behaviour of the recovered and 100% polyester is shown in and the thermal transition temperatures are provided in . Both samples had a similar glass transition temperature of 84 ± 1.7 °C. The mean glass transition temperature for the recovered polyester was 0.5 °C lower than for the 100% polyester. The melting temperature of both samples was in the range of 250.3 ± 2.1 °C, with the recovered polyester having a mean melting temperature 1.8 °C higher. The enthalpy of melting for the recovered polyester was 49.9 J/g and 51.2 J/g for the 100% polyester. provides the comprehensive thermal behaviour results. As was the case for the thermal decomposition behaviour, the slight differences seen here may have arisen from slight differences in production and finishing processes for the polyester materials. The similarities in the melting behaviour of the recovered polyester and the 100% polyester are evidence that the separation and recovery process used here does not hinder the ability of the recovered polyester to be melted and processed in the same way as 100% polyester fabric. Unfortunately, polyester fibres and fabric already have low intrinsic viscosity and molecular weight compared to the PET beverage containers which are a popular raw material for recycled polyester (Awaja & Pavel, Citation2005). Due to the known degradation of intrinsic viscosity caused by thermal processing (Awaja & Pavel, Citation2005) polyester fibres and fabric may not be suitable for melt processing into new fibres. However, a recent study by Sun et al demonstrated that low strength recycled polyester fibres are achievable via melt recycling (Sun et al., Citation2021).
Table 2. DSC results including the onset and midpoint of the glass transition, the onset and peak for melting temperature, and the enthalpy for 100% polyester and recovered polyester from the 80/20 polycotton blend.
Chemical changes in recovered polyester
To further assess the suitability of the recovered polyester for recycling the sample was analysed for changes in chemical bond structure using Attenuated Total Reflectance-Fourier Transform Infrared Spectroscopy (ATR-FTIR). The FTIR spectra in revealed the chemical similarities of the recovered polyester and the 100% polyester fabric. For reference, displays spectra for 100% cotton, 100% polyester, and the 80/20 polycotton samples. Analysis into regions where degradation products of polyester would likely occur revealed no signs of chemical degradation caused by thermal, mechanical, hydrolytic, or chemical processing. Thermomechanical degradation of polyester leads to the absorption band at 2962 cm−1 becoming larger due to symmetric and asymmetric stretch vibrations of CH2, and increased absorption intensity at 3548 cm−1 is brought about by the promotion of –OH terminated products (Badia et al., Citation2012). An increase in intensity of C-H rocking and C-H bending at the 899 and 846 cm−1, as well as 1471 and 1446 cm−1 can be caused by increased crystallinity through thermomechanical processing (Badia et al., Citation2012). None of these thermomechanical changes were observed in the recovered polyester sample. Hydrolysis of polyester can result in the emergence of two peaks between 2800 and 3000 cm−1 and a reduced intensity of the carbonyl group around 1710–1720 cm−1 (Lindström, Citation2018). The recovered polyester here shows no such changes at those wavenumbers. Degradation of polyester by sulfuric acid results in the products terephthalic acid (TPA) and ethylene glycol (EG) (Yoshioka et al., Citation1994), however new peaks in the FTIR spectra in the regions for these products were not seen in the recovered polyester. A study that degraded PET using DMSO showed products of dimethyl terephthalate (DMT) and EG with the DMT being characterised by a peak at 3421 cm−1 (Sharma et al., Citation2013). No such peak was observed in the recovered polyester here. The use of ionic liquid has also been studied for PET degradation, with the main degradation product representing a shift in the carbonyl peak from 1720 to 1688 cm−1 (Wang et al., Citation2009), however a strong carbonyl peak can be seen in both the 100% polyester sample and the recovered polyester sample here at approximately 1718 cm−1. The ionic liquid degradation product also showed a strong peak at 1285 cm−1 that was designated to breaks in the ester group during the degradation process (Wang et al., Citation2009), but this peak was not seen here.
Figure 3. FTIR spectra for (a) 100% polyester and recovered polyester from 80/20 polycotton and (b) 100% polyester, 100% cotton, and 80/20 polycotton fabric.
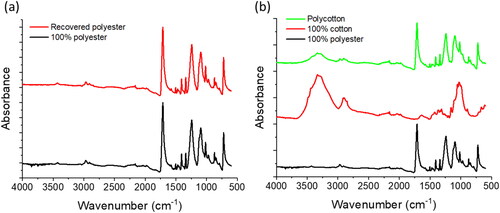
The approach used here is mild and likely accounts for the lack of structural changes in the recovered polyester. The pre-treatment step uses a very low concentration of sulfuric acid at moderate temperatures and very short time durations. Whilst sulfuric acid is capable of degrading polyester at high concentrations and temperatures (Yoshioka et al., Citation1994), the dilute acid, low processing temperature, and short duration here are likely responsible for the retention of polyester characteristics. The main constituent in the solvent system used here, DMSO, can discolour and dissolve polyester (Wu et al., Citation2014; Wu et al., Citation2019), however very high processing temperatures are required. The secondary solvent constituent used here, ionic liquid, is aprotic in nature and therefore does not directly interact with the polyester like a protic IL might. The lack of any degradation to the recovered polyester here demonstrates the recovery of high value polyester similar to pre-consumer 100% polyester fabric.
Mechanical properties of regenerated cellulose fibres from recovered cotton
To assess the suitability of the recovered regenerated cellulose fibres for use as textile fibres the mechanical properties were analysed. In a previous study it was shown that the chemical recycling of 100% cotton fabric using DMSO and ionic liquid could achieve good mechanical properties with tenacity similar to that of commercial viscose fibres (Ma et al., Citation2020). As seen in , the mechanical properties of the fibres produced from the recovered cellulose solution here were similar to those produced in our previous study. Two factors were expected to affect the mechanical properties of these fibres compared to fibres prepared from chemical recycling of 100% cotton. The first was the effectiveness of the acid pre-treatment in lowering the DP of the cellulose contained in the blended fabric. For 100% cotton waste, the acid pre-treatment acts to reduce the DP of cellulose in pre-consumer waste cotton to the level required for dissolution and wet spinning. As the polyester and cotton fibres in the blend here were intimately mixed until cotton dissolution, the DP of the pre-treated cotton in the blend could not be directly measured. The DP is known to have significant influence over the mechanical properties of regenerated cellulose fibres (De Silva & Byrne, Citation2017). The second factor was the concentration of cotton in the cellulose solution. A cellulose concentration of 6 wt% was targeted, however due to the residual cellulose remaining on the polyester directly after filtration, the concentration in the cellulose spinning solution was likely lower. The cellulose concentration also impacts the mechanical properties of the regenerated fibres (Sixta et al., Citation2015). The strength (tenacity) of the recovered fibres was very similar to fibres made from 100% waste cotton whilst the elongation was higher for the recovered cellulose fibres and the stiffness was lower. This may be due to a lower DP of the fibres produced from polycotton or the slightly lower cellulose concentration in the spinning solution.
Table 3. Draw ratio, linear density, tenacity, elongation, and elastic modulus of fibres produced form 100% cotton and from polycotton, compared to viscose fibres.
Colour properties of recovered materials
The recovered polyester and the regenerated cellulose fibres both visually retained the blue colour of the original blend material as was demonstrated in . Spectrophotometry measurements provided further insight into the colour retention of the recovered materials and from this colour strength and colour difference values were calculated. The colour strength is a measurement of colour concentration in a material (Whetzel, Citation2008) whilst the colour difference, ΔE, assesses the similarity of colours using parameters known as CEILab coordinates (Haslinger et al., Citation2019). The CEILab coordinates, colour strength, and colour difference data for recovered polyester, regenerated cellulose fibres, and the 80/20 polycotton blend are found in . The colour strength of all three materials was similar with the recovered polyester having a colour strength slightly higher than the original polycotton fabric and the regenerated cellulose fibres having a colour strength slightly lower than the polycotton fabric. Given that dyes have different affinities for cotton and polyester, and that the dyeing process would have been different for each material in the blend, it was expected that these different materials had different colour strengths. Compared to the original 80/20 polycotton fabric the recovered polyester fabric had a colour difference of 3.7, indicating a perceivable difference in colour, whilst the regenerated cellulose fibres had a colour difference of 8.3, meaning they were an entirely different colour. The small colour difference between the original fabric and the recovered polyester fabric was expected due to the same reasons for the difference in colour strength. The colour difference between the original fabric and the regenerated cellulose fibres was large; however this value was still lower than colour differences seen in other fibre-dye recycling work in which brightly coloured recycled fibres were produced with potential applications in the textile industry (Haslinger et al., Citation2019). Considering the retention of colour strength in the regenerated cellulose fibres here, the colour difference is not likely a result of dye loss, but instead due to the change in morphology of fibres when the cotton is dissolved and regenerated (Haslinger et al., Citation2019; Nasri-Nasrabadi et al., Citation2020).
Table 4. CEILab space coordinates, colour strength values and colour difference values for polycotton 80:20 blend, 100% polyester and recovered materials.
Due to the practice of using different processes with different dye types for each fibre type, it was important to determine if the dye on the individual fibre would be retained without any potential mixing of dyes. To assess this, an orange coloured 100% cotton waste fabric and a blue coloured 100% polyester waste fabric were manually mixed. These materials were chosen due to their difference in colour (orange and blue). Both these waste fabrics were chopped into snippets 0.2 mm in length, which were combined at a percentage ratio of 50/50. Once mixed, the polyester-cotton snippets were pre-treated, dissolved, and separated as described previously and illustrated in . It can be seen in that the separated cellulose, in the form of RCFs, retains the original orange colour while the separated polyester retains the original blue colour. The CEILab coordinates, colour strength, and colour difference data for the 100% polyester fabric, 100% polyester milled, and the recovered polyester from the 50/50 mixture are found in . The change in colour strength between the 100% polyester and the recovered polyester is acceptable as it may have arisen from differences in light reflection due to the form of the material (rough, chopped snippets), this is demonstrated in the moderate difference of colour strength between the polyester fabric and polyester snippets before the recycling process. The colour difference, ΔE, between the 100% polyester fabric and the recovered polyester was 5.4. This is a significant colour difference; however the colour difference between the 100% polyester in fabric form and snippet form was 4.4. The comparable colour difference of the 100% polyester snippets and the recovered snippets suggests that the difference comes not from loss of dye and instead is caused by the change in form of the material.
Figure 4. Schematic showing that the discrete dye colour specific to fibre type is retained on the recovered materials. Note the dark colour of the sample labelled ‘mixed and pre-treated’ and the solution-dispersion labelled ‘dissolved’ indicating a homogenous mixture of dissolved orange cotton and undissolved blue polyester snippets.
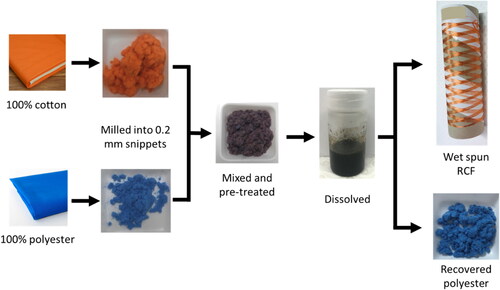
Utilising this separation process to retain the colour on similar and dissimilar coloured polyester and cotton has demonstrated that the dye remains on each material throughout the separation and recovery process. The mechanisms of dye retention likely depend on several factors. The pre-treatment here was mildly acidic, of moderate temperature and short duration. Cotton fabrics are commonly bleached in alkali conditions (Brooks & Moore, Citation2000), and the mechanisms of acid and alkali treatment of cotton vary significantly (Philipp, Citation1984), thus the low pH of the pre-treatment likely had a negligible effect on the dye. The co-solvent system of DMSO and [Bmim]OAc used here works to dissolve the cellulose by interrupting the intermolecular hydrogen bonds of the cellulose chains. The anion of the ionic liquid interacts with the hydroxyl groups on the cellulose chains whilst the bulky cation enhances repulsion between cellulose chains (El Seoud et al., Citation2021). The DMSO helps to increase the mobility by decreasing the viscosity of the solution (Shamsuri et al., Citation2021). As mentioned in the introduction, reactive dyes are common for cotton and cellulosic fibres, and these dyes form strong covalent bonds with the cellulose molecules (Shang et al., Citation2013). As the ionic liquid targets the hydrogen bonds between cellulose molecules, there is no significant interaction between IL and the covalently bonded dye molecules. Further, acid pre-treatment, ionic liquid and DMSO caused no degradation or change to the recovered polyester properties, indicating there is little interaction between these chemicals and polyester molecules for the processing parameters used here.
Morphology of recovered materials
During the separation process scanning electron microscopy (SEM) was used to confirm the separation of the two blended materials. The different morphologies of cotton and polyester allows easy distinction between the two materials in SEM images. shows the SEM image of the 100% polyester from the above process in the snippet form prior to being mixed with the cotton and recovered, and displays the polyester snippets after separation. The morphology of the polyester snippets did not appear to change as result of the separation process. The irregular morphologies of the snippets seen in the figure are likely a result of the cutting process, where the fabrics were sheared with a blade, and the increased temperature and shear forces caused the fibres to deform from the usual cylindrical morphology. Importantly, no residual cellulose was observed on the recovered polyester snippets, indicating effective separation in the chopped snippet form. shows the 80/20 polycotton in fabric form before separation, and shows the recovered polyester in fabric form. show a single bundle of the 80/20 polycotton fabric before separation and a single bundle of the recovered polyester, respectively. In the fabric and bundle form, cotton fibres with the ‘twisted ribbon’ morphology (Yue, Citation2011) could be seen in the samples before separation (), whilst only cylindrical-shaped polyester fibres were observed after separation (). These micrographs clearly show the absence of any cotton fibres in the recovered polyester. The presence of residual regenerated cellulose on the recovered polyester has been reported previously (Lv et al., Citation2015) and this problem was initially observed here. SEM images of recovered polyester with residual cellulose are displayed in . This setback was overcome by introducing a ‘rinse’ step directly after separation using the co-solvent DMSO. The complete removal of cotton is essential as contaminants are a major factor affecting the recyclability of polyester (Awaja & Pavel, Citation2005). The removal of residual cellulose on the recovered polyester confirms the suitability of this polyester for recycling.
Conclusions
A facile route to separating polyester-cotton blends has been demonstrated using a binary solvent system. The separation process could retain the original colour of the starting fabric and produced regenerated cellulose fibres with mechanical properties suitable for application as textiles. The recovered polyester fabric and chopped snippets showed no signs of cellulose after separation; demonstrating effective cotton removal and indicating the polyester may be suitable for subsequent mechanical or chemical recycling. Thermal analysis and characterisation of the melting properties of the polyester before and after separation revealed similar characteristics, suggesting the recovered polyester can be re-processed. The chemical structure of the recovered polyester was not altered from the original polyester and an extensive analysis showed no signs of any degradation products. The colour retention of each fibre component indicated the separation process here has no significant effect on the dyes used for both the cotton and polyester materials, and vibrant colours were achieved in the recycled fibres. Utilising the dye of the original fabric in recycled fibres has the potential to offset the need for redyeing, which could lead to large reductions in the environmental impact of the textile industry.
Acknowledgements
The authors acknowledge the Australian Government for their support through an Australian Government Research Training Program Scholarship and acknowledge that this work was performed in part at the Deakin Hub in the Victorian Node of the Australian National Fabrication Facility (ANFF).
Disclosure statement
No potential conflict of interest was reported by the authors.
References
- Ambercycle, I. (2021). Cycora. Available from https://cycora.com/about/.
- Awaja, F., & Pavel, D. (2005). Recycling of PET. European Polymer Journal, 41(7), 1453–1477.
- Badia, J. D., Strömberg, E., Karlsson, S., & Ribes-Greus, A. (2012). The role of crystalline, mobile amorphous and rigid amorphous fractions in the performance of recycled poly (ethylene terephthalate) (PET). Polymer Degradation and Stability, 97(1), 98–107. https://doi.org/10.1016/j.polymdegradstab.2011.10.008
- Better Thinking Ltd. (2006). Dyeing for a change: Current conventions and new futures in the textile colour industry/rrent c Thinking Ltd. In Better thinking’s perfect t-shirt.
- Brooks, R. E., & Moore, S. B. (2000). Alkaline hydrogen peroxide bleaching of cellulose. Cellulose, 7(3), 263–286. https://doi.org/10.1023/A:1009273701191
- Chen, X., Memon, H. A., Wang, Y., Marriam, I., & Tebyetekerwa, M. (2021). Circular economy and sustainability of the clothing and textile industry. Materials Circular Economy, 3(1), 12. https://doi.org/10.1007/s42824-021-00026-2
- De Silva, R., & Byrne, N. (2017). Utilization of cotton waste for regenerated cellulose fibres: Influence of degree of polymerization on mechanical properties. Carbohydrate Polymers, 174, 89–94. https://doi.org/10.1016/j.carbpol.2017.06.042
- De Silva, R., Wang, X., & Byrne, N. (2014). Recycling textiles: The use of ionic liquids in the separation of cotton polyester blends. RSC Adv, 4(55), 29094–29098. https://doi.org/10.1039/C4RA04306E
- El Seoud, O. A., Bioni, T. A., & Dignani, M. T. (2021). Understanding cellulose dissolution in ionic liquid-dimethyl sulfoxide binary mixtures: Quantification of the relative importance of hydrogen bonding and hydrophobic interactions. Journal of Molecular Liquids, 322, 114848. https://doi.org/10.1016/j.molliq.2020.114848
- Ellen MacArthur Foundation. (2021). Textile-to-textile recycling to reduce virgin material demand: The green machine. Available from: https://ellenmacarthurfoundation.org/circular-examples/textile-to-textile-recycling-to-reduce-virgin-material-demand-the-green.
- Elsayed, S., Hellsten, S., Guizani, C., Witos, J., Rissanen, M., Rantamäki, A. H., Varis, P., Wiedmer, S. K., & Sixta, H. (2020). Recycling of superbase-based ionic liquid solvents for the production of textile-grade regenerated cellulose fibers in the lyocell process. ACS Sustainable Chemistry & Engineering, 8(37), 14217–14227. https://doi.org/10.1021/acssuschemeng.0c05330
- Esteve-Turrillas, F. A., & de la Guardia, M. (2017). Environmental impact of recover cotton in textile industry. Resources, Conservation and Recycling, 116, 107–115. https://doi.org/10.1016/j.resconrec.2016.09.034
- Evrnu, S. P. C. (2020). Now, single-life textiles are a multi-life resource. Available from: https://www.evrnu.com/nucycl.
- Harmsen, P., Scheffer, M., & Bos, H. (2021). Textiles for circular fashion: The Logic behind recycling options. Sustainability, 13(17), 9714. https://doi.org/10.3390/su13179714
- Haslinger, S., Hummel, M., Anghelescu-Hakala, A., Määttänen, M., & Sixta, H. (2019). Upcycling of cotton polyester blended textile waste to new man-made cellulose fibers. Waste Management (New York, N.Y.), 97, 88–96. https://doi.org/10.1016/j.wasman.2019.07.040
- Haslinger, S., Wang, Y., Rissanen, M., Lossa, M. B., Tanttu, M., Ilen, E., Määttänen, M., Harlin, A., Hummel, M., & Sixta, H. (2019). Recycling of vat and reactive dyed textile waste to new colored man-made cellulose fibers. Green Chemistry, 21(20), 5598–5610. https://doi.org/10.1039/C9GC02776A
- Jaffe, M., & East, A. J. (2006). Polyester fibers. In M. Lewin, (Ed.), Handbook of fiber chemistry (pp. 1–29). Taylor & Francis Group.
- Keh, E. (2021). New paradigm for R&D and business model of textile circularity. In L. Liu & S. Ramakrishna (Ed.), An introduction to circular economy (pp. 325–347). Singapore.
- Kim, Y., McCoy, L. T., Lee, E., Lee, H., Saremi, R., Feit, C., Hardin, I. R., Sharma, S., Mani, S., & Minko, S. (2017). Environmentally sound textile dyeing technology with nanofibrillated cellulose. Green Chemistry, 19(17), 4031–4035. https://doi.org/10.1039/C7GC01662J
- Levi Strauss & Co. (2021). Bringing innovation to an icon. Available from: https://www.levistrauss.com/2021/12/13/bringing-innovation-to-an-icon/.
- Lindström, F. (2018). Chemical and physical changes in PET fibres due to exhaust dyeing. In The Swedish school of textiles. University of Borås.
- Ling, C., Shi, S., Hou, W., & Yan, Z. (2019). Separation of waste polyester/cotton blended fabrics by phosphotungstic acid and preparation of terephthalic acid. Polymer Degradation and Stability, 161, 157–165. https://doi.org/10.1016/j.polymdegradstab.2019.01.022
- Lv, F., Wang, C., Zhu, P., & Zhang, C. (2015). Isolation and recovery of cellulose from waste nylon/cotton blended fabrics by 1-allyl-3-methylimidazolium chloride. Carbohydrate Polymers, 123, 424–431. https://doi.org/10.1016/j.carbpol.2015.01.043
- Ma, Y., Rosson, L., Wang, X., & Byrne, N. (2020). Upcycling of waste textiles into regenerated cellulose fibres: Impact of pretreatments. The Journal of the Textile Institute, 111(5), 630–638. https://doi.org/10.1080/00405000.2019.1656355
- Mai, N. L., Ahn, K., & Koo, Y.-M. (2014). Methods for recovery of ionic liquids: A review. Process Biochemistry, 49(5), 872–881. https://doi.org/10.1016/j.procbio.2014.01.016
- Michud, A., Tanttu, M., Asaadi, S., Ma, Y., Netti, E., Kääriainen, P., Persson, A., Berntsson, A., Hummel, M., & Sixta, H. (2016). Ioncell-F: Ionic liquid-based cellulosic textile fibers as an alternative to viscose and Lyocell. Textile Research Journal, 86(5), 543–552. https://doi.org/10.1177/0040517515591774
- Motte, H., Palme, A. (2019). The development of the Blend Re: Wind process. Available from: http://mistrafuturefashion.com/wp-content/uploads/2018/06/Mistra-Future-Fashion-2018-5-H.-dl.-Motte.-Blend-Re-wind.pdf.
- Nasri-Nasrabadi, B., Wang, X., & Byrne, N. (2020). Perpetual colour: Accessing the colourfastness of regenerated cellulose fibres from coloured cotton waste. The Journal of the Textile Institute, 111(12), 1745–1754. https://doi.org/10.1080/00405000.2020.1728182
- Ouchi, A., Toida, T., Kumaresan, S., Ando, W., & Kato, J. (2010). A new methodology to recycle polyester from fabric blends with cellulose. Cellulose, 17(1), 215–222. https://doi.org/10.1007/s10570-009-9358-1
- Palme, A., Peterson, A., de la Motte, H., Theliander, H., & Brelid, H. (2017). Development of an efficient route for combined recycling of PET and cotton from mixed fabrics. Textiles and Clothing Sustainability, 3(1), 4. https://doi.org/10.1186/s40689-017-0026-9
- Patagonia, I. (2021). Recycled materials. Available from https://www.patagonia.com.au/pages/recycled.
- Philipp, B. (1984). Degradation of cellulose—mechanisms and applications. Pure and Applied Chemistry, 56(3), 391–402. https://doi.org/10.1351/pac198456030391
- Shamsuri, A. A., Abdan, K., & Jamil, S. (2021). Properties and applications of cellulose regenerated from cellulose/imidazolium-based ionic liquid/co-solvent solutions: A short review. e-Polymers, 21(1), 869–880. https://doi.org/10.1515/epoly-2021-0086
- Shang, S. M., et al. (2013). 13 - Process control in dyeing of textiles. In A. Majumdar (Ed.), Process control in textile manufacturing (pp. 300–338). Woodhead Publishing.
- Sharma, V., Parashar, P., Srivastava, P., Kumar, S., Agarwal, D. D., & Richharia, N. (2013). Recycling of waste PET-bottles using dimethyl sulfoxide and hydrotalcite catalyst. Journal of Applied Polymer Science, 129(3), 1513–1519. https://doi.org/10.1002/app.38829
- Sixta, H., Michud, A., Hauru, L., Asaadi, S., Ma, Y., King, A. W., Kilpeläinen, I., & Hummel, M. (2015). Ioncell-F: A high-strength regenerated cellulose fibre. Nordic Pulp & Paper Research Journal, 30(1), 43–57. https://doi.org/10.3183/npprj-2015-30-01-p043-057
- Subramanian, K., Sarkar, M. K., Wang, H., Qin, Z.-H., Chopra, S. S., Jin, M., Kumar, V., Chen, C., Tsang, C.-W., & Lin, C. S. K. (2022). An overview of cotton and polyester, and their blended waste textile valorisation to value-added products: A circular economy approach—research trends, opportunities and challenges. Critical Reviews in Environmental Science and Technology, 52(21), 3921–3942. https://doi.org/10.1080/10643389.2021.1966254
- Sun, X., Wang, X., Sun, F., Tian, M., Qu, L., Perry, P., Owens, H., & Liu, X. (2021). Textile waste fiber regeneration via a green chemistry approach: A molecular strategy for sustainable fashion. Advanced Materials, 33(48), 2105174. https://doi.org/10.1002/adma.202105174
- Wakelyn, P. J., et al. (2006). Cotton fibers. In M. Lewin (Ed.), Handbook of fiber chemistry (pp 521–666). Taylor & Francis Group.
- Wang, H., Li, Z., Liu, Y., Zhang, X., & Zhang, S. (2009). Degradation of poly(ethylene terephthalate) using ionic liquids. Green Chemistry, 11(10), 1568–1575. https://doi.org/10.1039/b906831g
- Whetzel, N. (2008). The Kubelka-Monk Theory and K/S.
- Wu, B., et al. (2014). Recycled waste polyester textiles decoloration by DMSO. Journal of Textile Research, 35(4), 80–84.
- Wu, H., Lv, S., He, Y., & Qu, J.-P. (2019). The study of the thermomechanical degradation and mechanical properties of PET recycled by industrial-scale elongational processing. Polymer Testing, 77, 105882. https://doi.org/10.1016/j.polymertesting.2019.04.029
- Xu, S., Chen, J., Wang, B., & Yang, Y. (2016). An environmentally responsible polyester dyeing technology using liquid paraffin. Journal of Cleaner Production, 112, 987–994. https://doi.org/10.1016/j.jclepro.2015.08.114
- Yoshioka, T., Sato, T., & Okuwaki, A. (1994). Hydrolysis of waste PET by sulfuric acid at 150 °C for a chemical recycling. Journal of Applied Polymer Science, 52(9), 1353–1355. https://doi.org/10.1002/app.1994.070520919
- Yuan, Z.-W., Zhu, Y.-N., Shi, J.-K., Liu, X., & Huang, L. (2013). Life-cycle assessment of continuous pad-dyeing technology for cotton fabrics. The International Journal of Life Cycle Assessment, 18(3), 659–672. https://doi.org/10.1007/s11367-012-0470-3
- Yue, Y. (2011). A comparative study of cellulose I and II and fibers and nanocrystals. In The school of renewable natural resources. Louisiana State University and Agricultural and Mechanical College.
- Zhou, T., Wang, Y., Zheng, H., Du, B., & Zheng, L. (2022). Sustainable and eco-friendly strategies for polyester-cotton blends dyeing in supercritical CO2. Journal of CO2 Utilization, 55, 101816. https://doi.org/10.1016/j.jcou.2021.101816