Abstract
This paper describes the thermal design of a compact vapor compression refrigeration system for high heat flux removal. The system operates with R-134a as the working fluid and consists of a miniature compressor, a compact condenser, and a spray-based heat sink device that combines the expansion device (an array of micro-orifices) and the evaporator into a single unit. The SPHINX (Spray Heat Sink Integrated with the Expansion Device) unit has been designed based on a phenomenological model for the critical two-phase flow in the micro-orifices and phase-change heat transfer resulting from the spray atomization/jet impingement on the heated surface. The SPHINX model was solved together with mathematical models for the other system components (compressor and condenser) in order to obtain the heater surface temperature behavior as a function of the system variables. A parametric study was performed to evaluate the effect of several design variables on the system performance. Correlations available in the literature for spray cooling and two-phase jet impingement heat transfer were analyzed and critically compared. The results indicate that a cooling unit with two compressors in parallel is capable of removing thermal loads of up to 560 W (140 W/cm2) while maintaining the heater surface temperature below 85°C.
NOMENCLATURE
Aheater | = | heat transfer area, m2 |
Bo | = | Boiling number, dimensionless |
Cf | = | Blasius friction factor, dimensionless |
COP | = | coefficient of performance, dimensionless |
cp | = | specific heat capacity at constant pressure, J kg−1 K−1 |
d32 | = | Sauter mean diameter (SMD), m |
G* | = | dimensionless mass flow rate, dimensionless |
H | = | orifice-to-surface distance, m |
h | = | specific enthalpy, J kg−1 |
= | two-phase specific enthalpy, J kg−1 | |
ℏ | = | local heat transfer coefficient, W m−2 K−1 |
= | average heat transfer coefficient, W m−2 K−1 | |
Ja | = | Jakob number, dimensionless |
k | = | thermal conductivity, W m−1 K−1 |
kheater | = | thermal conductivity of the heater material, W m−1 K −1 |
Lo | = | micro-orifice length, m |
Lheater | = | heater side length, m |
= | system mass flow rate, kg s−1 | |
= | critical mass flow rate, kg s−1 | |
No | = | number of micro-orifices, dimensionless |
NTU | = | number of transfer units, dimensionless |
P | = | pressure, kPa |
Pr | = | Prandtl number, dimensionless |
= | spray volumetric flow rate, m3 s−1 | |
= | condenser heat transfer rate, W | |
= | evaporator heat transfer rate, W | |
= | compressor thermal losses power, W | |
= | spray mean volumetric flux, m s−1 | |
q′′ | = | surface heat flux, W m−2 |
q′′heater | = | imposed heat flux, W m−2 |
R2 | = | correlation coefficient, dimensionless |
Reo | = | two-phase flow Reynolds number, dimensionless |
= | Reynolds number based on orifice diameter, dimensionless | |
RTIM | = | thermal interface material thermal resistivity, m2 K W−1 |
s | = | specific entropy, J kg−1 K−1 |
so | = | spacing between micro-orifices, m |
Sf | = | nucleate boiling suppression factor, dimensionless |
T | = | temperature, °C |
UA | = | condenser global thermal conductance, W K−1 |
Vo | = | two-phase flow velocity, m s−1 |
= | electric power consumption, W | |
= | Weber number based on orifice flow conditions, dimensionless | |
= | Weber number based on Sauter mean diameter, dimensionless | |
x | = | vapor quality, dimensionless |
Greek Symbols
β | = | factor defined in EquationEq. (29) |
δheater | = | heater plate thickness, m |
Δhf | = | friction-based energy loss, J kg−1 |
ΔTsat | = | wall superheating degree, °C |
ΔTsup | = | superheating degree at the compressor inlet, °C |
ΔTsub | = | subcooling degree, °C |
γA | = | surface area enhancement ratio, dimensionless |
μ | = | dynamic viscosity, kg m−1 s−1 |
= | two-phase dynamic viscosity, kg m−1 s−1 | |
ρ | = | density, kg m−3 |
= | two-phase density, kg m−3 |
Subscripts
1 | = | compressor inlet |
2 | = | compressor outlet |
3 | = | condenser outlet |
4 | = | evaporator outlet |
cond | = | condensation |
cv | = | convection |
evap | = | evaporation |
film | = | film conditions |
l | = | liquid at saturation conditions |
l, o | = | liquid at orifice exit conditions |
lv | = | heat of evaporation |
mo | = | multiple orifice |
nb | = | nucleate boiling |
s | = | surface |
so | = | single orifice |
v | = | vapor at saturation conditions |
v, o | = | vapor at orifice exit conditions |
Superscripts
* | = | modified dimensionless groups used in Eqs. (25), (27), and (30) |
Additional information
Notes on contributors
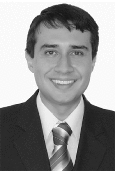
Pablo A. de Oliveira
Pablo A. de Oliveira is a mechanical engineering Ph.D. candidate at Polo Research Laboratories for Emerging Technologies in Cooling and Thermophysics, Federal University of Santa Catarina (UFSC), Florianópolis, Brazil. He completed in 2005 his B.Sc. degree in mechanical production engineering from Federal University of Paraíba (UFPB), João Pessoa, Brazil. In 2006, he joined Polo Laboratories (UFSC), where he worked with the modeling and numerical simulation of thermal regenerators for magnetic refrigeration, obtaining, in 2008, his M.Sc. degree in mechanical engineering. He is currently working on spray and jet cooling technologies for compact refrigeration systems applied to electronics cooling.
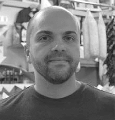
Jader R. Barbosa
Jader R. Barbosa, Jr., holds B.Sc. (1995) and M.Sc. (1997) degrees in mechanical engineering from the Federal University of Rio de Janeiro, Brazil, and a Ph.D. in chemical engineering from Imperial College, UK (2001). He is an associate professor at the Department of Mechanical Engineering of the Federal University of Santa Catarina, Brazil. In 2004, he received the Young Scientist Award from the European Committee for the Advancement of Thermal Sciences (EUROTHERM). He also received the Dudley Newitt Award (2001) of Imperial College for a doctoral thesis of exceptional merit, and the HTFS Award (Heat Transfer and Fluid Flow Service) for the best paper at the UK National Heat Transfer Conference (Edinburgh, UK, 1999). He has published more than 150 scientific papers in indexed journals and international peer-reviewed conferences. He carries out research on fluids engineering and thermal sciences, with a focus on thermodynamics of mixtures, phase change, multiphase flows, heat exchangers, and emerging cooling technologies.