Abstract
Unmanned aerial vehicles are expected to complete their missions even in adverse weather conditions. Overheating in the engine area may occur, particularly at high speeds due to using the full engine throttle. Another design factor that affects endurance duration and maximum take-off weight is the weight of the unmanned aerial vehicle heat exchanger. In this paper, a new type of air-cooled fuel cooler heat exchanger is proposed to reduce the total weight of the heat exchanger by increasing cooling performance through the design flexibility offered by additive manufacturing. The printed circuit heat exchanger has a circular cross-section to prevent dead bends in the heat transfer surfaces and feed coolant air directly onto the fins and circulation pipes. Twisted fins and piping structure were adjusted so they could be produced without any support, generate turbulence, and reduce total weight. The fluid flow and heat transfer characteristics of novel and conventional heat exchangers were simulated in 3D. The flow physics of both exchangers were studied to determine how the new design enhances heat transfer. Numerical results showed that the new heat exchanger has 55.6% more cooling capacity than the conventional one. The heat exchanger weight was decreased from 774 to 263 g.
Acknowledgments
We would like to thank Turkish Aerospace Industries Ltd. for their great support of problem identification in the field of aviation. Last but not least, we would like to thank the technical team at additive manufacturing labs in ALUTEAM (Aluminium Test Training and Research Centre) for their immense effort in designing and manufacturing necessary parts.
Disclosure statement
No potential conflict of interest was reported by the author(s).
Additional information
Funding
Notes on contributors
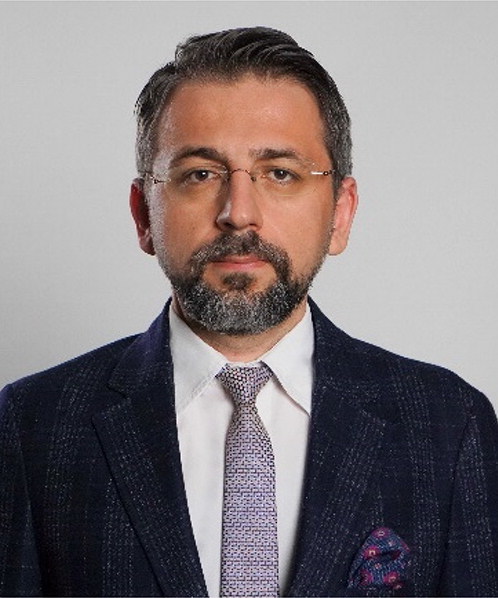
Aliihsan Koca
Aliihsan Koca is an Associate Professor at the Department of Mechanical Engineering, Istanbul Technical University. He received his B.Sc. and Ph.D. degrees from Yıldız Technical University, Department of Mechanical Engineering, Thermodynamics and Heat Technics program in 2009 and 2015 respectively. He received his M.Sc. degree from Istanbul Technical University, Mechanical Engineering Department thermo-fluid program in 2011. He worked at Michigan Technological University (USA) as a postdoctoral researcher, where he worked on next-generation thermal systems. He has 13 years of professional experience in the energy field and mechanical engineering. He has taken part in many national/international research and demonstration projects in the industry as project manager/researcher, and has carried out several projects funded by the European Commission, National Science Foundation USA and The Scientific and Technological Research Council of Turkey. He has more than 40 academic research papers and 5 patent applications. Heat transfer, thermodynamics, fluid mechanics, modern thermal systems, computational fluid dynamics and project management are among his fields of basic research.
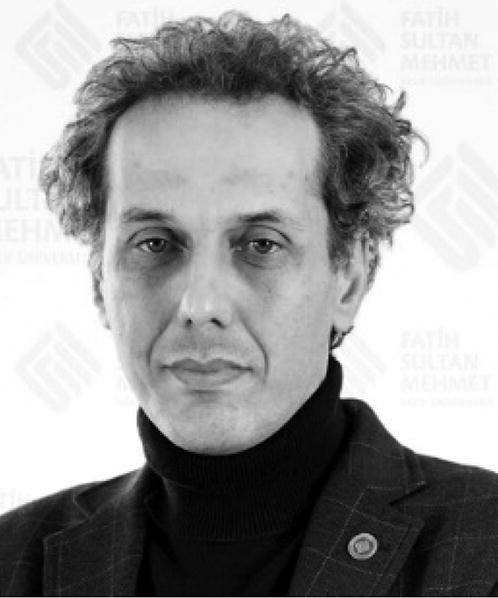
Cemal İrfan Çalışkan
Cemal İrfan Çalışkan is an Assistant Professor at Fatih Sultan Mehmet Vakif University and works at FSMVU Aluteam research center as design and additive manufacturing production coordinator. In 2005, he earned his master’s degree in Industrial Design. He finished his Ph.D. studies in Building Physics and Materials at MSGSU on additive manufacturing. His research interests include conformal cooling channels and, design for additive manufacturing.
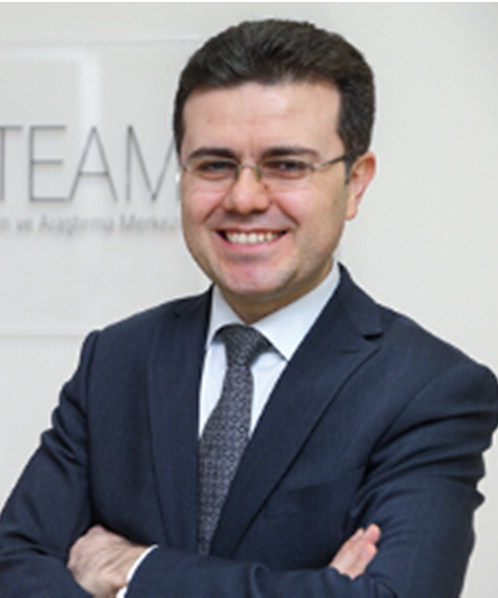
Ebubekir Koç
Ebubekir Koç is a Founder and Director of ALUTEAM (Aluminum Test, Training and Research Center) at Fatih Sultan Mehmet Vakif University in Istanbul, Turkey. He has completed his Ph.D. in Manufacturing Engineering Center at Cardiff University in the field of Industrial Engineering. He worked on developing intelligent algorithms for advanced manufacturing systems. He is on the board of the Aviation and Space Association of Istanbul (SAHA Istanbul), the founding member of the Turkish Additive Manufacturing Association (TAMA), and one of the founders and co-chairs of the Additive Manufacturing Conference Turkey (AMC TURKEY). He and his team have many completed and ongoing research projects under industry contracts. His main research interests focus on intelligent optimization, intelligent design and advanced manufacturing technologies and materials.
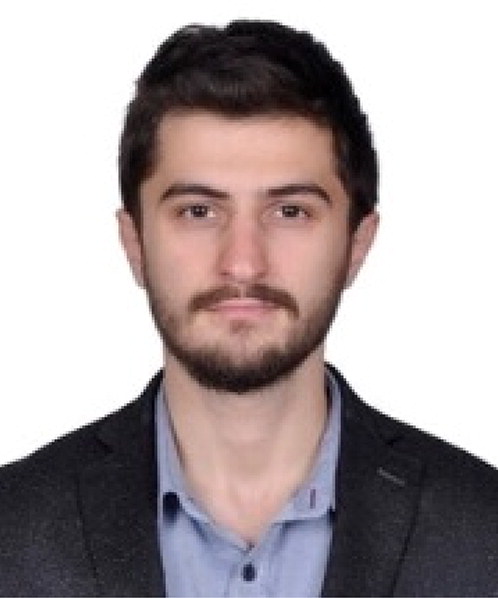
Ömer Akbal
Omer Akbal currently works in the design and analysis of aircraft systems including thermal management, environmental control system, aerodynamics, and aircraft icing at Turkish Aerospace. He received his master’s degree from Istanbul Technical University in 2019. Doctoral studies in the field of aerothermal and icing technologies continue at Istanbul Technical University, Department of Aerospace and Aeronautical. His main research interests focus on aircraft icing technologies, thermal management, computational fluid dynamics, aerodynamics, and heat transfer.