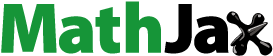
Abstract
Wood drying is a key operation of wood processing to ensure that the wood retains its physical integrity and stability in remanufacturing and in use. However, in industrial drying various drying defects still occur, which include uneven moisture content between and within boards, board distortion, residual drying stresses that may induce internal and external checking, and wood collapse. This paper presents a review on advances in wood drying research and development, which lay foundation for better understanding of the drying process, mechanisms of drying defect occurrence and affecting factors. In particular, recent progresses in understanding drying stress development and wood collapse formation during drying are presented in more details. Based on these advances, inter-linkage and interactions are analyzed among wood physical and microstructural properties, moisture movement in wood during drying, stress development and reversal, and wood collapse formation. Following this, drying schedule improvements and novel drying technologies are presented with targets to mitigate the drying defects, reduce energy consumption and increase the productivity. Application of artificial intelligence for modeling and control of the timber drying is also briefly described. Finally, recommendations are made for future studies and practical implementation.
1. Introduction
Wood as a biological and renewable material has been historically used for buildings, furniture and decorations. In order to retain its physical integrity and mechanical stability in remanufacturing and in use, the wood moisture content before use is commonly manipulated to a level close to the value which wood will attain at the given surrounding conditions (temperature and relative humidity). As the green wood moisture content is normally much higher than the target value, wood drying is required which is nowadays conducted in industrial kilns. In short, the timber is stacked layer by layer between which stickers are placed to provide gaps for hot air (drying medium) to flow through as shown in .
Wood originates from tree stems and thus has certain intrinsic characteristics, which can affect the drying process and dry wood quality. If the wood is dried inappropriately, one or more drying defects may occur, and these will either require longer drying time (thus consume more energy) or degrade the dry wood quality.
The most common issue in industrial timber drying is uneven moisture content distribution among boards in a stack, although a certain level of variation is acceptable. Boards with too high moisture content after drying will lose moisture in storage or in use, and in these cases shrinkage and/or distortion occurs. On the other hand, if the boards are over-dried and the final moisture content is too low, the dried wood will gain moisture in storage or in use, which induces swelling and/or distortion.
shows an example of drying a stack of mixed sapwood and heartwood radiata pine boards at dry-bulb/wet-bulb temperatures of 90/60 °C and 5 m/s air velocity.[Citation1] The board dimensions were 100 mm (width) by 40 mm (thickness). The initial moisture content of the sapwood boards was 140% while that of the heartwood boards was 40%. After 22 h of drying, the average moisture content of the boards was 22%, but the moisture contents of individual boards varied from 7% to 45%. With further 8 h of drying, the average moisture content was reduced to 11% and the moisture content variation was still significant, from 6% to 16%.
Figure 2. Moisture content distribution among boards toward the end of drying.[Citation1]
![Figure 2. Moisture content distribution among boards toward the end of drying.[Citation1]](/cms/asset/782b2f30-c2fb-4ec7-8ec4-66f212fbf917/ldrt_a_2205530_f0002_c.jpg)
For a single board, the moisture content gradient within wood is either directly or indirectly the driving force for moisture movement.[Citation2] shows an example from a published study[Citation3] on the drying of single boards at dry-bulb/wet-bulb temperatures of 120/70 °C and 5 m/s velocity. The board dimensions were 100 mm (width) by 50 mm (thickness). The moisture content gradients along the board thickness at different drying times are shown in for a sapwood board and in for a heartwood board. The moisture content gradient is inevitable; however, if the moisture content gradient is too high and not reduced in post-drying treatment, moisture movement within wood in storage or in use may induce distortion or checking.
Figure 3. Moisture content gradients along board thickness for sapwood (a) and heartwood (b) at different drying times.[Citation3]
![Figure 3. Moisture content gradients along board thickness for sapwood (a) and heartwood (b) at different drying times.[Citation3]](/cms/asset/3c492b6e-033b-4f6f-82ee-345898e5a276/ldrt_a_2205530_f0003_b.jpg)
Other common drying defects are illustrated in . Distortion can be the consequence of a number of factors, including variable shrinkage of wood in different directions or at different angles and excessive internal stress. Internal stress is commonly observed in all types of wood[Citation7,Citation8] which can be caused by uneven shrinkage and moisture content gradient. Wood collapse is observed in monocots including palms,[Citation9] bamboo[Citation10] and in some hardwoods species.[Citation11,Citation12]
Table 1. Common defects in wood drying.[Citation4–6]
To understand the causes and related factors of the drying defects, extensive studies have been conducted over the past 50 years. The early reviews were published in the Drying Technology journal by an earnest expert in wood drying, William Simpson, of USDA Forest Products Laboratory at Madison.[Citation13,Citation14] In the first review,[Citation13] the needs for wood drying and causes for drying defects were described. Then wood fundamental properties related to drying were proposed which include how the water is held in the wet wood, wood-water relationships, wood shrinkage, and equilibrium moisture content of wood as a function of temperature and relative humidity. Following this, the moisture movement process, driven by diffusion, and the stress development, driven by uneven shrinkage, were discussed. In the second part of Simpson’s review,[Citation14] drying technologies and drying schedules were introduced.
In the past 40 years since these two reviews were published, the drying process has been understood much better and the drying operation has been improved for reducing drying time and achieving even moisture content distribution both between and within boards. However, the other drying defects are still occurring, although the causes of these defects are better known.
The objectives of this review are to present and assess the advances in the following areas:
Fundamental understanding of the wood properties and moisture movements in wood during drying.
Fundamental understanding of drying stress development and reduction of wood distortion.
Fundamental understanding of wood collapse during drying.
Drying schedule improvement and development of novel technologies for wood drying.
From this review, areas will be identified for future research and development.
2. Moisture movement and modelling approaches on wood drying
Wood drying, similarly to the drying of other wet materials, is an integrated heat and mass transfer process between the drying medium (hot air or superheated steam) and the wood material. The mass transfer is an interconnected process of moisture vapor transfer from the wood surface and moisture movement within the wood toward the surfaces.[Citation15] The heat transfer is also an integrated process of heat convection from the main gas stream to the wood surface and the heat conduction/convection within the wood for material heat-up and moisture vaporization. This review will focus on the moisture movement within the wood during drying.
Water in wood plays an important role in tree growth that it acts as nutrient carrier and moves from roots to leaves for photosynthesis. Knowing these functions of the water can help understanding how the water is held in wood and how it moves within wood during drying. In a growing tree, water transport in the tree stem is driven by capillary forces through numerous cell lumens and tracheid cells, which form a channel network. However, if part of the tree stem is cut or damaged where the water flow channel is interrupted with exposure to ambient air, the bordered pits on the two adjacent cell walls aspirate and the affected water channel is then closed. The pit aspiration is irreversible. In this way, the remaining undamaged stem is protected and the water flow within the unaffected wood can be maintained. The water movement can vary for different types of wood (hardwood or softwood) and different tree species. An illustration is presented in adapted from Chen et al.[Citation15] Penvern et al.[Citation16] and Cocusse et al.[Citation17]
Figure 4. Various possible modes of water transport in different types of wood adapted from Chen et al.[Citation15] Penvern et al.[Citation16] and Cocusse et al.[Citation17]
![Figure 4. Various possible modes of water transport in different types of wood adapted from Chen et al.[Citation15] Penvern et al.[Citation16] and Cocusse et al.[Citation17]](/cms/asset/8acf5abe-b499-4cd4-a92f-96a1bd3667de/ldrt_a_2205530_f0004_c.jpg)
When a board is cut in a sawmill, the bordered pits on and near the board surfaces become closed. This means that liquid water cannot flow right to the board surface during drying. This led to the concept of a thin dry layer around the board surfaces proposed by Pang et al.[Citation18] This concept has been confirmed and accepted in later studies, which can explain the observations that the surface temperature of the board during drying is always higher than the wet-bulb temperature as theoretically predicted.[Citation19–21]
Fresh softwood can have moisture content of up to 200% in fully saturated sapwood, which is located in the outer part of the stem. On the other hand, the heartwood, which is in the core part of a stem, may have moisture contents from 40 to 50%.[Citation22] However, moisture loss occurs during log transport and storage before sawing, and timber sawing and storage before drying. The moisture in wood during drying can exist in three forms: liquid water above the fiber saturation point, which acts as free water, bound water, which is attached to the cell wall material through hydroxyl (OH) bound, and water vapor in the cavities of wood.
The maximum bound water content is termed the fiber saturation point (FSP) at which all of the water is chemically bound within wood cell and no liquid water exists.[Citation22,Citation23] The FSP is about 30% at room temperature, but decreases with increasing temperatures.
The FSP is an important property of wood drying due to the following facts:
More energy is needed to remove the bound water than liquid water. The extra energy is termed as the heat of wetting or heat of adsorption.[Citation24]
Wood starts to shrink with moisture content reduction below the fiber saturation point, and vice versa.[Citation25]
Wood mechanical properties (strength, modulus) increase with the decrease in moisture content below the FSP.[Citation26,Citation27]
The liquid water can move within wood through the cell lumens and tracheid cells. However, there are different suggestions for the driving force including gradient of water concentration or gradient of moisture content (by diffusion), and gradient of liquid pressure (Darcy’s law). Pang[Citation28] assessed the two types of models and identified the suitability of each in different situations. Comprehensive models also consider gas/vapor transport driven by pressure gradient.[Citation2,Citation18,Citation29–31] In the drying models, bound water diffusion is dominant when the moisture content is below the FSP, driven by gradient of moisture concentration or chemical potential. The vapor diffuses through the wood cavities with partial pressure gradient as the driving force. The dominant mechanisms of moisture movement are dependent on moisture content, drying intensity (temperature), drying medium and wood species.
In the modeling of wood drying, the liquid water movement is related to the liquid pressure gradient generated by the local capillary pressure.[Citation2,Citation16,Citation29–31] The capillary pressure is also related to the saturation, which is, in turn, related to moisture content. The liquid movement is only possible when the liquid flow channel maintains continuity at moisture contents close to but above the FSP.[Citation18]
Previous studies have been conducted to experimentally verify the liquid flow mechanism. Dumyang et al.[Citation32] studied liquid flow on oil palm wood which contains roughly spherical parenchyma cells with a cell diameter of 70 ± 10 µm and cell wall thickness of 1.3 ± 0.5 µm. This gives a ratio of the cell wall thickness to the cell cavity diameter of just about 0.02 at the equator. The cell wall comprises only the primary wall layer. The parenchyma cells connect through the small channel of plasmodesmata (rp = 41 ± 6 nm). The very small pit opening induces a relatively large capillary pressure of up to 2.5 MPa.[Citation32] Capillary transport is, therefore, dominant in this type of structure and the existence of cell collapse confirms the main role of capillary pressure in water transport. To the extreme end, the water transport in a similar porous structure with micrometer-sized voids connected by nanometer-sized channels with a radius of less than 5 nm has been demonstrated in the laboratory to occur by the process of cavitation.[Citation33] The heterogeneous nucleation of the gas bubbles is reported to take place at a capillary pressure of more than 20 MPa. However, this type of water transport has not yet been observed in wood during drying.
In drying of some hardwood and softwood species at slow drying rate, liquid water diffusion may be the dominant mechanism. Penvern et al.[Citation16] and Cocusse et al.[Citation17] studied water extraction during convective drying in poplar (hardwood) and Douglas fir (softwood) wood and found that bound water diffusion in cell walls is the main process right from the beginning even when the local moisture content is well above the FSP. For sufficiently slow drying, free water is extracted from vessels and fibers toward the cell walls and then diffuses toward the surface. The distribution of bound water within the cell walls remains uniform until the free water is completely removed. Once the cell cavities are empty, the gradient of bound water starts to develop. At a higher drying rate, the bound water gradient in the cell walls can develop before the complete extraction of free water from the cell cavities. Therefore, for the entire drying process, only bound water diffusion is the control mechanism, with no (or small) contribution from the capillary flow in these types of wood species. For most species of wood, the liquid movement occurs through combined bulk flow and diffusion.
Local equilibrium may be assumed between water and vapor within wood during drying, and this can be described by an isothermal relationship. In this way, the relative humidity can be estimated at a given moisture content and temperature from which the vapor partial pressure at a specific location can be calculated to determine the vapor partial pressure gradient. This is used to quantify the vapor diffusion.
Early models for wood drying were based on Fick’s law of diffusion as outlined in the review of Simpson.[Citation13] However, there are two issues in the diffusion-based drying model:
The smooth moisture content distribution is in most cases unrealistic for average moisture content above the FSP.
The boundary conditions at the board surface are arbitrary. The external mass transfer is based on the difference of gas phase concentrations between the main stream of drying medium and the board surface. However, the moisture movement within wood is based on moisture concentration gradient. In order to overcome this issue, a surface emission factor was introduced to correlate the surface moisture content and the vapor concentration, although the use of a mass-transfer coefficient and a sorption relationship between wood moisture content and the vapor pressure immediately above is a more conventional and established engineering approach.
With rapid advances in computer technologies and software development, more sophisticated models were developed in the past 30 years, which are based on transport phenomena and coupled heat and mass transfer processes. However, the wood intrinsic properties and behavior are important and should be taken into account in any modeling approach.
The results from experimental and mathematical modeling studies[Citation1,Citation20] have shown that, after the wood stack is loaded into a commercial kiln and the drying starts, the wood initially picks up some moisture due to the low temperature of the wood. However, this lasts a very short time, and fast drying commences once the wood surface is heated to above a certain temperature. During fast drying period, the surface temperature is always higher than the wet-bulb temperature, which is due to the thin dry layer formed around the board surfaces even before drying. The fast drying lasts as long as the liquid flow toward the surface can compensate for the moisture loss from the surface into the drying medium. Following this stage, the drying rate is reduced as free water is removed and bound water diffusion becomes dominant.
3. Stress development in wood during drying
The internal stresses in wood during drying are resulted from constraints between layers to meet the force balance condition for all layers. These constraints are results from different shrinkages among layers, which are in turn induced by moisture content gradient during drying as shown in . The constraints may be relieved to a certain extent toward the end of drying when the moisture content gradient is reduced. If the wood behaves as an ideal rigid material and the final moisture content is uniform through the material, the stresses are completely relieved. However, the wood behaves more like a flexible material showing elastic and plastic characteristics. Wood mechanical properties also vary with moisture content and temperature. In addition, wood as a biomaterial shows mechano-sorptive behavior, where additional strain is generated in the wood due to combined effect of moisture content change and stresses. Therefore, in order to understand and model the stress development and thus to reduce the residual stresses in the dried wood, determinations of the related wood physical and mechanical properties are needed.
3.1. Shrinkage in radial, tangential and longitudinal directions
It is well known that below the fiber saturation point, wood shrinks with a decrease in the moisture content, however, at the same moisture content the shrinkage is higher in the tangential direction and lower in the longitudinal direction, as shown in .[Citation25] The shrinkage in radial direction is slightly less than that in the tangential direction. Shrinkage may also vary with early wood and latewood, and wood species.[Citation25,Citation34] It is also reported that the wood shrinkage varies with temperature as shown in .[Citation35]
Figure 5. Wood shrinkage as a function of moisture content in tangential direction (a) and longitudinal direction (b), adapted from Pang and Herritsch.[Citation25]
![Figure 5. Wood shrinkage as a function of moisture content in tangential direction (a) and longitudinal direction (b), adapted from Pang and Herritsch.[Citation25]](/cms/asset/c9d8c2d8-0588-4e19-8972-d1be1ee12e4f/ldrt_a_2205530_f0005_c.jpg)
Figure 6. Stress-free shrinkage in tangential direction (solid lines) and in radial direction (dotted lines) as a function of moisture content and temperature, adapted from Lazarescu et al.[Citation35]
![Figure 6. Stress-free shrinkage in tangential direction (solid lines) and in radial direction (dotted lines) as a function of moisture content and temperature, adapted from Lazarescu et al.[Citation35]](/cms/asset/e380869a-8bed-46a1-8d97-ad76298c089f/ldrt_a_2205530_f0006_b.jpg)
3.2. Stress development and relief in wood drying
The development of internal stress during drying is a very complicated process. Here a brief description is presented, but more details can be found in a number of studies.[Citation5,Citation6,Citation36,Citation37] During drying, the moisture content gradient forms as shown in , and the moisture contents at the surface or in the near-surface layers are lower than those in the inner layers. When the local moisture contents in the surface layers decrease to below the fiber saturation point, these layers start to shrink whereas the inner layers of wood have higher moisture contents and have not yet started shrinking. As the wood holds together as one piece, the surfaces layers are stretched by the inner layers while the inner layers are compressed by the surface layers. As the overall thickness of the surface layers is much thinner than the inner layers, the tensile stress in the surface layers may be greater than the maximum elastic limit in which case permanent strain is formed. This can be further increased by mechano-sorptive strain and increase in wood temperature. Once the permanent strain is formed, the wood cannot be recovered to its original state even if the stress is relieved.
As drying proceeds, the moisture contents in the inner layers also decrease to below the fiber saturation point and start to shrink. However, the surface layers have already been in state of permanent strain from the early stage of stretching, therefore, the surface layers resist the full recovery and generate constraints for the shrinkage of the inner layers. In this way, the stress profile is reversed with surface layers in compression and the inner layers in tension. The above stress development pattern has been simulated by integrated drying and stress models as well as experimentally investigated.[Citation5,Citation6,Citation36,Citation37]
Surface checking may form in the early stages of drying when the tensile stress reaches the maximum strength of the wood at local moisture content and temperature while internal checking may be created in the late stages of drying when the tensile stress in the inner layers reaches the maximum strength. In most cases, the internal stress cannot be seen until the wood is cut and the constraint is relieved. However, by better understanding and quantifying the stress development during drying, the stress can be reduced or relieved with an improved drying schedule or post-drying steaming treatment.[Citation20,Citation38]
The drying stress reversal behavior, central to the stress development during wood drying, has been modeled using the concept of the mechano-sorptive creep at varying moisture contents in addition to the classical viscoelastic creep at a constant moisture content.[Citation7,Citation20,Citation39–41] Moutee et al.[Citation40] in particular, proved that the viscoelastic creep model is not sufficient to fully describe the stress reversal behavior and the mechano-sorptive effect must be included. Ranta-Maunus[Citation42] first proposed an empirical expression to correlate the extra “memory” strain rate to be proportional to the product of the applied stress and the rate of moisture change below the fiber saturation point. Later, some modifications have been made to the equation in an attempt to capture the complex mechano-sorptive creep phenomena.[Citation43,Citation44]
Despite success in quantitatively describing several material behaviors during drying, the physical mechanism of mechano-sorptive creep has not been fully understood and is still a matter of debate.[Citation45] Without good understanding of the underlying mechanisms, the empirical model of mechano-sorptive creep requires a significant amount of experimental data to deduce the model parameters for each test condition. In addition, the model is only limited within the data range obtained and has no predictive power outside it.
Understanding the underlying mechanisms of mechano-sorptive creep is therefore crucial for scientific and technological development in the field of wood drying. Although not yet fully understood with many views on physical mechanisms proposed, there have been some definite facts discovered by many authors since it was first observed in wood by Armstrong and Kingston,[Citation46] and Armstrong and Christensen[Citation47] as follows:
Not only in solid wood, but many porous materials including cellulose-based materials such as wood fibers,[Citation48] wool[Citation49] and paper,[Citation50] synthetic fibers such as Kevlar[Citation51] and concrete[Citation52] also exhibit mechano-sorptive creep. These materials have the common characteristic that they contain hydrogen bonds.
A single wood fiber, when exposed to cyclic moisture change, exhibits mechano-sorptive creep suggesting that the phenomena take place at the microscopic level within the cell wall[Citation48] where the contribution from lignin is not significant.[Citation53]
The modulus of elasticity of wood is reduced by mechano-sorptive creep.[Citation54]
A steady state migration of moisture through the wood without a change of local moisture content under a constant moisture gradient does not produce mechano-sorptive creep.[Citation55]
Moreover, specifically for wood drying, a recent measurement by Tomad et al.[Citation36] revealed that the stress reversal takes place at a certain point of time as the dry zone, where moisture content is below FSP, moves inwards to the wet zone where moisture content is still above FSP. Therefore, the existence of the wet zone and the role of the dry front are also likely to be responsible for the stress reversal during wood drying and should be given more attention. Cocusse et al.[Citation17] also suggested from experimental observations that bound water transport through the wood cell wall where free water coexists (i.e. the wet zone) is analogous to the flow of liquid through a saturated porous structure under the action of a pressure gradient. All the above facts and views should pave the way to the understanding of mechano-sorptive creep and should serve as platforms in the design of future experiments and modeling.
4. Better understanding of collapse in wood drying
According to a recent literature review by Yang and Liu,[Citation56] Tiemann is believed to be the first person who used the term “wood collapse” in the literature to distinguish excessive deformation from the shrinkage that is normally expected in wood drying. There was a very interesting historical note where he concluded in 1913[Citation57] based on his experience on planting Eucalyptus globulus in California with less than twenty years of tree growth, that the wood “shrinks and warps so excessively that it cannot be regarded as lumber in any true sense”.
At that time Eucalyptus lumber was obtained from old native trees in Australia, but Tiemann found it almost impossible to dry trees younger than 40 to 50 years without an unacceptable level of downgrade. He described collapse as uneven shrinkage, alternating between early and late wood to produce corrugated surface patterns. He also tried pretreatments, such as boiling and steaming, to reduce internal stresses but the results were equal or worse.
More than a century later, we are still unable to dry the wood from young trees of many Eucalyptus species without an unacceptable level of downgrade, which raises the question of whether it is even possible to solve this problem in practice. To answer that question, this section reviews the classical theory of wood collapse, explains most current interpretations of the phenomenon, and summarize methods that have been investigated in practice to dry prone-to-collapse wood species.
4.1. Classical theory of wood collapse during drying
The most popular explanation for wood collapse during drying is capillary pressure. This was visually described in the early literature[Citation58] with, for example, the drawing reproduced in . The theory assumes that water tension develops inside cell lumens when air-water interfaces (meniscus) reach a capillary pore in cell walls. Cell containing air bubbles in the cavities can dry because bubbles expand under tension, but fully saturated cells will need to stand the maximum capillary pressure associated to the capillary radius before air can enter the lumens to produce bubbles that expand.
Figure 7. Drawing adapted from Hawley[Citation58] from early wood-water-relationships explaining the phenomenon of capillary pressure inside wood cells during drying.
![Figure 7. Drawing adapted from Hawley[Citation58] from early wood-water-relationships explaining the phenomenon of capillary pressure inside wood cells during drying.](/cms/asset/eb62870d-96bf-481c-a7ee-cb0d6210d856/ldrt_a_2205530_f0007_b.jpg)
The mathematical formula of capillary tension was based on the Young-Laplace law[Citation23,Citation59,Citation60] which states that a curved gas-liquid interface creates a pressure difference between gas and liquid (ΔP) which can be estimated by EquationEq. (1)(1)
(1) .[Citation61] In the equation, σ is the surface tension, and R1 and R2 are two orthogonal radii defining the surface curvature.
(1)
(1)
The curved liquid-gas interface attaches to the capillary walls at a certain angle determined by the properties of gas, liquid and solid at the contact point. In the case of wood, the receding contact angle of individual fibers in aqueous solutions can be assumed to be zero, regardless of the type of wood and chemicals in the solution.[Citation62] Consequently, capillary pressure in wood can be calculated by EquationEq. (2)(2)
(2) , in which R is the equivalent radius of the capillary pore.
(2)
(2)
Water surface tension is a function of temperature and may be expressed in EquationEq. (3)(3)
(3) where σ (N/m) represents the surface tension of water and vapor in equilibrium for the entire temperature range T (K) from the triple to the critical points.[Citation63]
(3)
(3)
The bordered pits on the wood cell walls are not actually capillaries in the sense that they have a morphological structure comprising aperture, chamber, and membrane.[Citation64] The membrane is a porous remnant of the primary cell wall,[Citation64] which fills the cross-section area of the pit cavity. This makes the equivalent pit radius much smaller than the pit aperture radius observed under a microscope. For example, pit radii measured with a scanning electron microscope (SEM) in radiata pine were between 1.5 and 3 µm.[Citation65] In comparison, equivalent pit radii estimated from capillary pressure measurements showed values between 0.1 and 0.55 µm in green sapwood, and between 0.014 and 0.05 µm in green heartwood for selected softwood species.[Citation66]
shows examples of capillary pressure calculated with EquationEqs. (1)(1)
(1) and Equation(2)
(2)
(2) at 20 °C using equivalent pit radii reported in the literature.[Citation66] The capillary pressures are compared with the tensile strength perpendicular to the grain in green conditions for similar species reported in the literature.[Citation67] Although the negative pressure and tensile strength are not directly comparable, the tensile strength perpendicular to the grain provides a reference to assess if negative pressure is relatively high or low for a certain species. Based on analysis of the stresses in the cell walls and boundary layers among cells, in the cases where wood yields or is fractured at the middle lamella, then the stress at this layer is equivalent to the capillary-induced negative pressure and can be directly compared. The comparison shows that the capillary pressure is relatively low in sapwood, but relatively higher than tensile strength in heartwood. Fortunately, heartwood is not expected to be saturated with water, thus most softwood timber is not particularly prone to collapse during drying.
Table 2. Equivalent pit radius and maximum capillary pressure for selected softwood species[Citation66] in comparison with the transverse tensile strength in green condition[Citation67].
Hardwood species, on the other hand, are much more prone to collapse, arguably because some cells in the heartwood are no longer for water transport. The hardwood cells can be classified in three main groups: tracheary, parenchymatous and libriform.[Citation68] Tracheary elements specialize in water transport, parenchymatous cells specialize in storage, and libriform fibers specialize in mechanical strength.[Citation68] Fiber pits are distinctly smaller, scarce and irregularly arranged, which contrasts with the numerous, larger and distinctly bordered pits of the tracheary elements.[Citation69] Their function is almost exclusively mechanical support, thus pits are generally inconspicuous.[Citation64]
If the non-tracheary elements do not to contain large pits, they could develop extremely high capillary pressures, which in turn may cause massive collapse and internal checking in hardwood timber where fiber cells contribute between 30 to 75% of the tissue volume.[Citation70] This phenomenon was clearly visualized by using an optical microscope and digital image analysis by Dickson.[Citation71] The microscope had a digital camera and motorized XY scanning stage that allowed reconstruction of large surface areas by adjoining adjacent images. Collapsed cells were identified by automatic thresholding as zones with no lumens.[Citation71]
shows an example of Eucalyptus nitens, where color from green to magenta represents deformation levels, and white represents full cell collapse.[Citation71] The images clearly show that collapse occurs around the vessels where non-tracheary elements reside. They also show that collapse increases with the severity of the drying regime (air drying < kiln drying at mild temperatures < oven drying at 103 °C), and that the counter effect of collapse is internal checking.
Figure 8. The top two rows are, from left to right, microscope images of air dried, kiln dried and oven-dried (103 °C) Eucalyptus nitens samples adapted from Dickson.[Citation71] Colors in the bottom two rows show deformation visualization in which color change from green to magenta represents deformation levels, and white represents full cell collapse.
![Figure 8. The top two rows are, from left to right, microscope images of air dried, kiln dried and oven-dried (103 °C) Eucalyptus nitens samples adapted from Dickson.[Citation71] Colors in the bottom two rows show deformation visualization in which color change from green to magenta represents deformation levels, and white represents full cell collapse.](/cms/asset/2f13479c-f744-4e53-81af-297e2315def2/ldrt_a_2205530_f0008_c.jpg)
Internal checking, which is the counter effect of collapse in the timber core, has also been visualized at a macroscopic scale by taking cross sectional images of Eucalyptus nitens sample with a medical CT-scanner at different stages of drying. shows an unpublished example of four Eucalyptus nitens boards dried from initial moisture contents (MC) between 123% and 144% to final MC between 65% and 78%. The drying conditions were 25 °C/24 °C dry-bulb/wet-bulb temperatures and 1 m/s air velocity. The grayscale from black to white represents density, meaning that brighter zones are areas of higher MC. Regardless of how slow and mild the drying schedule was, numerous internal checks and corrugated surface patterns developed as water was removed from the timber.
4.2. Wood collapse in the light of new drying theories
In wood drying theories proposed recently, capillary pressure is not only determined as a function of capillary radius, but also as a function of saturation level which is related to the MC above FSP.[Citation30,Citation72,Citation73] A notable exception is the percolation model of Salin[Citation74] in which the wood cells are represented by a network of squares connected by openings with random radiuses. When a square is dry, it creates meniscuses with adjacent squares full of water, and the meniscus with the largest radius will break first continuing drying in that direction. shows an example of MC profiles simulated with the percolation model for drying of 180 mm wide x 100 mm thick timber.[Citation75] The figure shows saturated (blue) and dried (red) cells distributions at four different instances during drying, where some cells dry faster than others depending on their opening random radii.
Figure 10. Example of MC profiles simulated with the percolation model.[Citation75] Drying proceeds from top-left to bottom-right. Blue areas represent free water, red areas represent dried cells, and black histograms represent average MC profiles.
![Figure 10. Example of MC profiles simulated with the percolation model.[Citation75] Drying proceeds from top-left to bottom-right. Blue areas represent free water, red areas represent dried cells, and black histograms represent average MC profiles.](/cms/asset/3f81b77d-38ad-403c-899b-4a2ac799905b/ldrt_a_2205530_f0010_c.jpg)
However, one advantage of simulating capillary pressure as a function of saturation (MC) is that capillary pressure can be measured experimentally at a macroscopic level.[Citation76] Another advantage is that the theoretical relationships are well founded in the theory of thermodynamics equilibrium. In short, thermodynamics equilibrium is reached when a component has the same chemical potential in all phases.[Citation29,Citation77] If there are differences in water potential, then molecules will be spontaneously exchanged to equalize those differences.
Water chemical potential depends on pressure, temperature, concentrations, its interactions with solid surfaces, gravity and any other factors affecting the potential energy of a component. For a simpler analysis, however, EquationEqs. (4)(4)
(4) and Equation(5)
(5)
(5) are used, respectively, for a vapor phase under ideal gas conditions and incompressible liquids at constant chemical composition.[Citation77]
(4)
(4)
(5)
(5)
Where µi is chemical potential, Vi is molar volume, P is pressure, Peq is equilibrium vapor pressure, T is absolute temperature, R is the ideal gas constant, and superscript 0 represents the reference state.
In EquationEq. (4)(4)
(4) , Peq/P0eq is the same as relative humidity (RH) in fractional units for humid air, which in turn determines wood equilibrium moisture content (EMC) through sorption isotherms at known temperatures. shows numerical examples calculated at 20 °C using EquationEqs. (2)–Equation(5)
(5)
(5) in which R = 8.3145 J/mol.K, V = 1.807 × 10−5 m3/mol, and the Hailwood and Horrobin sorption isotherm[Citation78] was used to estimate the EMC. also shows the associated water potentials, equivalent capillary radiuses, and wet-bulb temperatures.
Table 3. Calculated RH, EMC and capillary pressure in equilibrium at 20 °C, with corresponding water potential, equivalent capillary R, and wet-bulb temperature.
indicates that ΔP at equilibrium with a moisture content less than 26.9% (or RH < 98.2%) is already very high in comparison with the tensile strength perpendicular to grain as given in . However, if cell walls have large pit radii, then the meniscus will recede at lower ΔP and water in cell lumens will be replaced by air. On the contrary, if effective pit radii are smaller than 0.06 µm, the bordered pits are aspirated, inexistent or plugged with extractives for example, then water tension will build up inside water saturated cells until reaching thermodynamic equilibrium with the surrounding EMC and RH, or more likely, until cells collapse.
The theory of water potential has been used in the past for modeling timber drying,[Citation79,Citation80] but not in the context of predicting water tension. More recently, a timber drying study by Riley et al.[Citation81] showed evidence that moisture does not necessarily move from zones of higher MC to lower MC, but rather from higher to lower water potential. An example is reproduced in for a 25 mm thick radiata pine sample dried at 90 °C dry-bulb and 60 °C wet-bulb temperature for 5 h.
Figure 11. CT-scanner cross section image of 25 mm thick radiata pine sample dried at 90/60 °C for 5 h.[Citation81] The CT-scanner image was treated digitally to show MC > FSP (blue) and MC < FSP (red) in a scale from 200% to 0%.
![Figure 11. CT-scanner cross section image of 25 mm thick radiata pine sample dried at 90/60 °C for 5 h.[Citation81] The CT-scanner image was treated digitally to show MC > FSP (blue) and MC < FSP (red) in a scale from 200% to 0%.](/cms/asset/f82b0ff2-0bb4-479f-9df5-1975bf294c4f/ldrt_a_2205530_f0011_c.jpg)
demonstrates that areas with MC < FSP can be surrounded by areas with MC > FSP, which contradicts the theory that water flows in the direction of moisture gradients. On the other hand, if liquid water is temporarily under metastable tension due to capillary pressure for example, then water potential could decrease further in the water than in adjacent dried fibers, thus allowing moisture to flow in theory from areas with MC < FSP to areas with MC > FSP.
Separated studies also investigated the water transport in some collapse-prone wood species such as red cedar[Citation12] in which both bound water diffusion and capillary flow should be operative simultaneously. The tracheid has the cell diameter of about 30 µm and the cell wall thickness of about 4 µm as measured by Flibotte et al.[Citation82] which gives a ratio of the cell wall thickness to the cell cavity diameter of 0.13 which is much larger than that of the oil palm wood. The contribution of bound water diffusion is therefore higher than the oil palm wood. The pit system with heavily deposited extractives should also induce significant capillary pressure. A similar approach used by Penvern et al.[Citation16] and Cocusse et al.[Citation17] should be employed to elucidate the water migration mechanisms in the collapse-prone wood species in the future. A clearer picture of the mode of water transport in the different wood structures during drying could then be obtained.
4.3. Methods to reduce wood collapse during drying
It is acknowledged in this review that the theory of wood collapse is still controversial, and there is not a single method that can completely solve this problem in practice. Different researchers have provided solutions and explanations that fit the purpose of their experimental work, but it is still not clear whether they are generically valid. The list below summarizes some of the most common solutions proposed for reducing collapse in timber drying and explains them briefly based on the previous theoretical foundations.
Supercritical CO2 dewatering: The most recent technology published in the literature for removing water from wood without collapse is known as supercritical CO2 dewatering.[Citation83–85] In this method, the wood is placed in a chamber which is pressurized with CO2 at around 50 °C and pressures between 10 to 30 MPa. In supercritical state, the CO2 can easily penetrate the wood and dissolve in the water. When pressure is released, the CO2 expands into gas bubbles that push water out of the wood. This technology has proven to reduce collapse in Euclayptus nitens by 75% compared to kiln drying.[Citation83] One explanation could be that CO2 bubbles break water tension inside the lumens (see ). It has also been shown that CO2 dewatering removes extractives and opens bordered pits in Eucalyptus urophydis, which in turn enlarge capillary openings.[Citation84]
Reducing surface tension and inducing bubbles: Reducing surface tension and inducing bubbles have been proven feasible to reduce wood collapse in laboratory.[Citation86] Different treatments have been reported in the literature to reduce water tension by impregnating wood with surfactants or replacing water with solvents that reduce surface tension.[Citation87] Treatments to induce bubble nucleation have also been reported in the literature, such as impregnation with sodium bicarbonate,[Citation88] supercritical CO2, and application of ultrasonic fields.[Citation87] However, methods that rely on diffusion through green timber are very slow and often ineffective in getting active components into the core. They have been mainly successful for treating small pieces of wood, such as in alcohol drying of wood strips before X-ray analysis.[Citation86] It is also used for drying submerged archaeological wood.
Freeze drying: Freeze drying is a common laboratory technique to remove water from soft materials that collapse during drying. It consists of drying the material at pressures and temperatures below the triple point of water (0.612 kPa and 0.01 °C), so that ice sublimates directly into vapor without passing through liquid state. It is commonly used for drying of archaeological wood.[Citation89] However, archaeological wood is generally impregnated with water-based polymers, such as polyethylene glycol (PEG), to add structural support after drying.[Citation90] It does not appear at first glance that freeze drying is economically viable for commercial timber drying, except for a Canadian study where winter temperatures are well below freezing point. In a study naturally frozen timber was covered with polyethylene sheet to allow sun to heat the timber surfaces while simultaneously protecting from snow and rain.[Citation91] It was found that about 50% of the water could be removed during the winter months.[Citation92]
Superheated steam: Drying with superheated steam consists of exposing a substance to water vapor at temperatures above the boiling point of water, thus water could theoretically boil inside the material and produce bubbles.[Citation93] Bubble formation could break water tension inside the cell lumens, but vapor pressures at typical timber drying temperatures would seldom be enough to cancel the capillary pressure values reported in . For example, vapor pressure at 120 °C is 203 kPa, only a fraction of the ΔP = −2435 kPa calculated for 98.2% RH. The main benefit of superheated steam drying, according to the literature, is that timber can be dried faster and is more energy efficient than in convective kiln drying with equivalent product quality.[Citation94–96] The superheated steam drying will be discussed in more details in Section 6.4 of this paper.
Vacuum drying: Vacuum drying is a generic term referring to the drying of timber inside vacuum chambers, which vary depending on the heat source.[Citation97] Superheated steam vacuum drying is one variety. An important sub-set in these technologies is that heat is not transferred by convection from the surrounding vapor, but by other means directly into the wood. Such methods can potentially reduce collapse if the surrounding vapor remains at saturated conditions, so that equilibrium water potential is equivalent to 100% RH. For example, it is claimed that conductive heating vacuum drying (where heat is transferred by contact with a hot surface) reduces surface and internal checking.[Citation97] Furthermore, it has been demonstrated experimentally that radiofrequency vacuum drying (where energy is supplied by an electromagnetic field) reduced collapse by 60% in Eucalyptus nitens.[Citation98]
Slow drying: It is well known in industry that difficult to dry hardwood species must be dried slowly to minimize downgrade. Non-published commercial research, performed by the authors on Eucalyptus nitens in Chile, showed that water above FSP should be dried at low temperature (i.e. 40 °C), low wet-bulb depression (i.e. 1 °C) and low air velocity (i.e. 1 m/s). A recent technical bulleting with recommendations for drying oak confirms the same principles.[Citation99] For drying moisture above FSP, the study recommended that temperature should not exceed 30 to 40 °C, RH should be maintained as high as possible, and air velocity should be lower than 2 m/s. Since the glass transition temperature for wood is between 65 to 70 °C,[Citation100] it has been argued that low temperatures are safer because cell walls are stronger.[Citation86] From a thermodynamics perspective, however, slow drying should also reduce collapse if RH is maintained as high as possible. In addition, slow drying would help to maintain higher MC at the surfaces, so that equilibrium water potential will remain closer to the equivalent of FSP.
Cyclic drying: Cyclic drying has been proposed as a method to release stresses during drying.[Citation101–104] The method consists of alternating drying (higher temperature and lower relative humidity) and equalization cycles (lower temperature and higher relative humidity), so that surfaces are reconditioned with moisture after intermittent periods of drying. The difficulty of characterizing cyclic drying resides in the larger number of set-point parameters that are required to control the process (i.e the duration of each cycle and associated temperature, RH, air velocity). Consequently, anecdotical results from cyclic drying of timber studies vary considerably depending on how the processes were implemented and controlled.
5. Drying schedule optimisation for the batch drying of timber
A drying schedule is a set of dry and wet-bulb temperatures, essentially air temperatures and humidities, that vary with either elapsed time or moisture content as the drying process continues. Evaluation of drying schedules produced by repeated trials are reported in works by Korkut et al.[Citation105] and Rahimi et al.[Citation106] while Cronin et al.[Citation107] have used a simple drying model to predict final moisture contents, with optimization being done to reduce the variation.
Some drying schedules are based on maximizing the productivity while keeping the stresses in the timber within the acceptable failure boundaries, which is a non-linear optimization problem.[Citation108,Citation109] Improvements included addressing the issue of biological variability when optimizing the drying schedules as proposed by Pordage and Langrish.[Citation110]
While not optimizing the drying schedule mathematically, Pang[Citation1] showed how a full rheological model, coupled with a distributed parameter drying model, could be used to improve drying schedules for radiata pine timber. In one aspect of his work, the coupled model was used to explain how to improve intermittent drying schedules, which are drying schedules where temperatures and/or humidities are cycled or alternate between different levels, emulating the daily cycling of temperatures and humidities in solar drying.
His approach was to cycle the humidity between small and large values, but to reduce the difference progressively as drying proceeds, so that both humidity levels approach a condition that achieves the equilibrium moisture content that is required. He did this because he found that intermittent drying between two fixed humidity levels may increase surface tension:[Citation1] “When the humidity was cycled to the high value the wood surface picked up moisture and the compression stress at the surface increased (but increased to a lesser extent because the mechano-sorptive strain helped to relax the constraint between the surface layer and the interior zone). However, when the humidity was cycled to a low level, the surface lost moisture and the surface stress then became tensile as it attempted to shrink. In this way, the previous mechano-sorptive compressive strain increased the surface tension in the subsequent lower humidity environment.”
In most cases, internal drying stress is inevitable; therefore, post-drying treatment is necessary in industrial drying to relieve the residual stress. The post-drying treatment is normally done by injection of saturated steam, termed as steaming,[Citation38] or by using high humidity air which is called conditioning or equalization.[Citation5,Citation111] These post-drying treatments can reduce the moisture content variation between and within boards. More importantly, the post-drying treatment can reduce the internal stress within wood which is believed to be due to two key factors: the mechano-sorptive effect and the material yield.[Citation6] At the end of drying, the wood surface has low moisture content, and it is in compression. At the start of steaming or conditioning, the wood surface picks up significant amount of moisture which further increases the compressive stress to a yield point, generating permanent compressive strain. As the post-treatment proceeds, the moisture moves from the surface inwards and the wood surface starts to shrink. In this way the constraint is relaxed and stress is relieved. In addition, the mechano-sorptive strain helps with stress relief when local moisture content changes. The reduction of moisture content distribution and mechanism of stress relief during the post-drying steaming have been verified both from experimental results[Citation38] and mathematical modeling.[Citation6] An important observation is that the kiln stack should be cooled down to a certain level to make the steaming more effective. This involves a complex process for moisture pick-up by the wood surface as the wood surface temperature can increase above 100 °C at the start of steaming due to the release of latent heat of vapourisation and heat of sorption when the steam changes phase.
6. Novel timber drying technologies
Novel drying technologies for wood drying have been developed with targets to increase drying rate or productivity, improve energy efficiency, reduce operation costs and minimize environmental impact, and at the same time achieve the required dry wood quality. A type of novel drying technology that has many potential applications for high-value lumber board drying is dielectric drying, including the use of radiofrequencies and microwave.[Citation112] Considerations when implementing the technology include the point of application for these techniques, with the technique sometimes being applied toward at the end of drying in order to make the moisture content distribution more uniform, requiring decreased energy input due to the rising surface temperatures at lower drying rates and moisture contents.[Citation113]
6.1. Radio frequency assisted drying
Active innovations in the field of radiofrequency drying for western red cedar and western hemlock timber were reported by Avramidis and Liu,[Citation114] reporting exceptional final timber quality in terms of low internal drying stresses, little to no internal and external checking and no surface discoloration. Good control of the dying rates was achieved by adjusting the electrode plate voltages as functions of time and moisture level, in view of the changing dielectric properties of wood at different moisture contents. Continuing innovations in this field have been reported by Fu et al.[Citation115] investigating the mechanisms for the greatly increased (doubled) drying rates and lower gradients in the moisture contents. Radiofrequency drying was found to have larger effects around and below the fiber saturation point than above it. In combination with some conventional drying inputs, this type of innovative drying technology reduced residual stresses near the timber surface and resulted in lower drying stresses.
In terms of implementing this technology, Elustondo and Avramidis[Citation116] analyzed different sorting strategies for radiofrequency drying, finding that there were benefits in terms of average timber moisture content by batch dry/sort/re-drying (b-DSRD) and continuous or retro-feed dry/sort/re-dry (c-DSRD) compared with moisture content-based pre-sorting (MCPS). However, the drying strategy was not found to affect the effective drying time. Following this innovation through to the commercial scale, Elustondo et al.[Citation117] discussed the first commercial scale dry/sort/re-dry (Q-Sift(R)) strategy for the drying of Pacific Coast hemlock timber using the combination of radio frequency vacuum drying and conventional drying techniques. A techno-economic analysis showed that the method was industrially viable, with short payback times of under 1.5 years.
6.2. Drying with heat recovery
Another area of innovation in timber and lumber drying is energy recovery, with self-heat recuperation technology being discussed by Chen et al.[Citation118] This approach was also used by Aziz et al.[Citation119] as shown in , who used a compressor-expander in a closed-loop fluidized-bed drying system to recover energy from the outlet gas and return it to the fluidized-bed dryer through heating coils that were immersed in the bed of solids. They did not use the energy in the warmed cooling fluid from the condenser to reheat the inlet gas to the dryer. Both systems use a compressor and expander (turbine) after the dryer, to increase the dew-point temperature of the compressed air for subsequent reheating of the dryer. The compression increases the exergy of the air by increasing its pressure. The system of Aziz et al.[Citation119] includes a desuperheater after the dryer before the compressor and expander, then returning the air to the dryer.
Figure 12. Schematic diagram of closed-loop heat recovery system, adapted from Aziz et al.[Citation119]
![Figure 12. Schematic diagram of closed-loop heat recovery system, adapted from Aziz et al.[Citation119]](/cms/asset/029c1222-a933-4d2a-af3b-2f7ac34eb47b/ldrt_a_2205530_f0012_b.jpg)
6.3. Multistage progressive and continuous drying kilns
The widespread implementation of progressive kilns in the lumber manufacturing industry is a relatively recent advancement. Just a couple of decades ago, progressive kilns were not commonly used for drying high quality dimension timber. Previous generation of progressive kilns consisted in a tunnel with capacity for 10 to 25 packages placed perpendicular to the tunnel length so that air flowed along the tunnel perpendicularly to wood packages in a counter-current fashion.[Citation31] Most advanced progressive kilns comprised two successive zones, one for warming-up the timber and another for drying. The drying process consists of opening the kiln doors every 2 to 6 h, and pushing one green wood package through the entry door while removing one dried wood package from the exit door.[Citation31] shows an example of a two-stage progressive kiln commonly used one decade ago in the wood drying industry.
Figure 13. Example of a two-stage progressive kiln commonly used one decade ago in the lumber drying industry.[Citation31]
![Figure 13. Example of a two-stage progressive kiln commonly used one decade ago in the lumber drying industry.[Citation31]](/cms/asset/cdbc2d83-535c-4cc3-9065-22196167c9ab/ldrt_a_2205530_f0013_c.jpg)
However, around one decade ago it became evident in the wood processing industry that a new generation of progressive kilns was going to transform the drying process as we knew it.[Citation120] These changes were not related to scientific research (thus academic literature is lacking), but rather to practical modifications that made the technology equivalent to batch kilns in terms of drying quality and control, and equivalent to progressive kilns in term of energy efficiency and productivity.
In new progressive kilns, wood packages move in the direction of the timber length parallel to the tunnel, while air flows perpendicularly to the timber length like in batch kilns. New progressive kilns have typically three zones, a central zone in which the wood is dried, and two input/output zones in which wood warms-up and cools-down as it gets into and out of the kiln. Depending on the case, wood packages could move through parallel tracks in counter-flow direction so that the cool-down energy of outgoing packages becomes the warm-up energy of incoming ones. shows an example of a progressive kiln offered commercially by a local manufacturer in New Zealand, but there are many other kiln designs offered by kiln manufacturers around the world.
Figure 14. Example of progressive kiln offered commercially by a local kiln manufacturer in New Zealand (www.windsorengineering.co.nz/drying/kilns/).
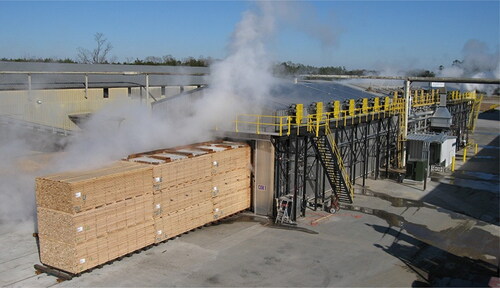
An example of the progressive kiln is described here based on unpublished data measured in eight progressive kilns used to dry 25 to 50 mm thick softwood lumber in undisclosed locations in North America. The kilns had 16 to 50 m long drying zones and 10 to 43 m long input/output zones. The dry-bulb and wet-bulb temperatures varied from respectively 95 to 132 °C, and 60 to 88 °C, and airflow velocities varied from 5 to 8 m/s. For lumber initial MC from 50 to 200% and final MC from 10 to 17%, the residence times through the drying zones were between 10 and 22 hr and the energy consumption was between 0.4 and 2.0 GJ/m3. Although these numbers are not substantially different than those for traditional batch kiln, the counter-flow version of continuous kiln is expected to be more energy efficient as warm-up energy is re-used inside the kiln.
The main advantage of progressive kilns, however, is the increased productivity. This is because the kilns can be operated in a continuous mode without having to stop and restart after each run like in traditional batch kilns. There are many logistics and technical questions to be considered as companies adapt their drying operations from batch to a continuous process, and we expect that some of these questions will create opportunities for research and development in both industry and academia.
6.4. Superheated drying
Mujumdar[Citation121] is one of the first to raise the attention to superheated steam drying (SSD) in the 1990s. At that time SSD had been known for more than 100 years, but the commercial application was limited with less than 10 manufacturers worldwide.[Citation121] SSD is a convective drying technique comparable to conventional kiln drying, but with the main difference that only steam is used as the drying medium. At a given pressure, when the steam temperature is higher than the saturation temperature, the steam is superheated which possesses capability to provide heat and absorb vapor as long as the steam temperature remains above the saturation temperature (superheated). When the superheated steam is in contact with wet materials, the material is heated to above the saturation temperature thus water evaporates and the vapor diffuses into the superheated steam stream. For temperatures below 100 °C, the saturation pressure of steam is below atmospheric pressure thus the dryer needs to be operated in vacuum, so that it is usually referred as superheated steam vacuum drying (SSVD).
A main characteristic of SSD is the absence of air in the drying medium. This has potential advantages: it can reduce energy consumption because there is no need for fresh air ventilation and humid air exiting; it can increase drying rate because the resistance to vapor transfer from the material to the steam stream is very low; and it prevents oxidation reactions because there is not oxygen in the system. SSVD has also the potential to reduce thermal degradation and preserve timber mechanical properties due to the possibility of using low temperatures.
Faster drying rates in SSD has been confirmed with higher extent of superheating. It was reported that SSD of 25 to 50 mm thick parawood timber at 110 °C and 1 bar reduced the drying time with respect to kiln drying from 7 to 10 days in low temperature drying (40 °C and 70%RH) to merely 35 h.[Citation95] In a separate study, it was reported that SSVD of 25.4 mm thick rubberwood at temperatures between 60 and 80 °C and pressures between 0.12 and 0.15 bar reduced the drying time to 20 h from 168 h in conventional kiln drying.[Citation122]
Pang and Pearson[Citation123] investigated SSD of 40 mm thick radiata pine at 160 °C and 3 bar and reported 5 to 10 times shorter drying times than high-temperature and accelerated kiln drying schedules. The same drying time reduction was also found for SSD at 170 °C and 1 bar, but SSVD at 90 °C and 0.2 bar increased drying time from 31 to 48 h with respect to kiln drying.[Citation123] Longer drying times in SSVD could be explained by the low external heat transfer coefficient and the lower heat capacity of the steam under vacuum.
It is believed that SSD is generally faster because water can potentially evaporate at boiling point with very low resistance to vapor diffusion. Based on this assumption the principle of the dry layer was used to develop semi empirical models for SSVD by Elustondo et al.[Citation94] The dry layer model assumes that during early stages of drying there is a receding waterfront under the surfaces that is controlled mainly by external heat transfer. Pang[Citation124] modeled timber drying mathematically and confirmed that vapor diffusion is much higher in SSD than in conventional drying, while external heat transfer coefficients are on the same order of magnitude.
Effects of SSD and SSVD on timber quality have also been reported in the previous studies. Yamsaengsung and Sattho[Citation122] reported that SSVD of 25.4 mm thick rubberwood showed increases in hardness, compression and sharing strengths parallel to the grain. In this study, superheated steam at 110 °C was intermittently injected during the process to relieve stress and reduce cracking. Bovornsethanan and Wongwises[Citation95] found that SSD of 25 to 50 mm thick parawood timber retained a color similar to fresh wood, and there was almost not residual stress as determined by prong tests. It was found, however, that the quality of parawood dried with superheated steam was lower in thinner timber in comparison with the conventional lower temperature kiln drying, thus the study concluded that SSD of parawood was not recommended for thicknesses below 30 mm.[Citation95] For 100 mm thick larch timber a study concerning the possibility of continuous SSD reported that surface checks was not observed even though the moisture content difference between surface and core was high.[Citation125] However, some internal checks occurred in juvenile and core wood.
Overall, SSD has the potential to reduce energy consumption and drying time, as well as increase wood quality specially for thick timber that it is already difficult to dry with conventional kiln drying. Several timber drying operations using SSD have been reported in the Netherlands.[Citation126] This study claimed that SSD of beach and oak timber at 1 bar reduced drying time and energy consumption by 50% and 20%, respectively, in comparison with conventional kiln drying. The timber quality remained similar although the SSD was found to have a positive effect in the color, being generally darker depending on wood species.[Citation126]
6.5. Application of Artificial intelligence
Artificial intelligence (AI) has been applied in drying R&D with artificial neural network modeling and neuro-fuzzy drying control.[Citation127–130] The AI applications require a wide range of database on material properties, drying performance at different conditions and variability both with the materials and the drying kiln. For timber drying, a neural network was developed to automatically classify crack severity in image processing from timber cross sections,[Citation131] and machine learning was tried to predict moisture content during the timber drying.[Citation132] A robust process controller has also been developed using a neural network for timber drying.[Citation133] However, due to the complexity and variability of the wood materials, artificial intelligence (AI) has been used in a limited way for timber drying. In the future, the AI will have even greater promise, by integrating different aspects of the timber drying process together, such as process control, timber drying rates and cracking. AI may do this by enabling learning from very large databases of timber properties to minimize carbon dioxide emissions during timber drying, in addition to maximizing productivity, minimizing wastage and predicting timber failure.
7. Conclusion and future research
With advances in research and development in wood drying, the fundamentals of the drying process and mechanisms of drying defects occurrence are much better understood, which helps to improve drying operations and develop new drying technologies.
In wood drying understanding and controlling moisture movement in wood is critically important. Too fast drying would generate large moisture content gradient, which is likely to induce high drying stresses and occurrence of wood collapse for many species of wood. On the other hand, too slow drying would lengthen the drying time, increase energy consumption and reduce productivity. In drying of most softwoods and some hardwoods, free water movement is driven by liquid pressure gradient due to capillary actions whereas bound water movement is by diffusion. However, for drying of some difficult-to-dry hardwoods, diffusion is the dominant mechanism for moisture movement. The driving force for the moisture diffusion can be moisture content gradient or water potential gradient. The exact regime of moisture movement is closely related to wood species and level of moisture content, therefore future research should be conducted to determine how the anatomical and structural properties in wood species affect the moisture movement, particularly above the fiber saturation point.
The development of internal stress during drying is a very complicated process, however, it can be summarized as interaction of shrinkage difference due to the moisture content gradient, permanent strain formation and mechano-sorptive behavior of wood. As a result, in early stages of drying the surface layers are in tension and core is in compression. As the drying proceeds, the stresses are reversed at certain stage which requires appropriate post-drying treatment. In order to predict the stress development and relief accurately, databases for common wood species should be created for wood stress-strain relationships and mechano-sorptive creep properties at different temperatures and moisture contents.
Wood collapse is most likely induced by capillary pressure (negative) which is related to saturation level, and dimensions and structures of the wood cells, tracheid and vessels. However, collapse occurrence is also dependent on strength of the cell wall and strength of the lamella layers of the wood. The exact mechanisms for wood collapse are still debatable even this issue has been recognized for over 100 years. Future research should be conducted on stress development in wood cells and failure mechanism under negative pressures.
Drying schedule improvement and novel drying technology development are an on-going practice in wood drying industry which can be made effective with good understanding of the wood properties, drying process and drying defects occurrence. Artificial intelligence (AI) is potentially a powerful tool for wood drying modeling and control, however, limited applications have been found due to the complexity and variability of the wood as a bio-origin material. Establishing databases for different wood species and drying behavior is critical for AI applications in the future.
Disclosure statement
No potential conflict of interest was reported by the authors.
Additional information
Funding
References
- Pang, S. Investigation of Effects of Wood Variability and Rheological Properties on Lumber Drying: Application of Mathematical Models. Chem. Eng. J. 2002, 86, 103–110. DOI: 10.1016/S1385-8947(01)00278-9.
- Moya, R.; Tovar, D. A.; Tenorio, C.; Bond, B. Moisture Content Variation in Kiln-Dried Lumber from Plantations of Vochysia Guatemalensis. Wood Fiber Sci. 2011, 43, 121–129.
- Pang, S. Moisture Content Gradient in a Softwood Board during Drying: Simulation from a 2-D Model and Measurement. Wood Sci. Technol. 1996, 30, 165–178. DOI: 10.1007/BF00231631.
- Sandberg, D. Distortion and Visible Crack Formation in Green and Seasoned Timber: Influence of Annual Ring Orientation in the Cross Section. Holz Roh Werkst. 2005, 63, 11–18. DOI: 10.1007/s00107-004-0546-2.
- Yin, Q.; Liu, H.-H. Drying Stress and Strain of Wood: A Review. Appl. Sci. 2021, 11, 5023. DOI: 10.3390/app11115023.
- Pang, S. Modelling of Stress Development during Drying and Relief during Steaming in Pinus Radiata Lumber. Drying Technol. 2000, 18, 1677–1696. DOI: 10.1080/07373930008917806.
- McMillen, J. M. Stresses in Wood during Drying. Report 1652. Department of Agriculture, Forest Service, Forest Products Laboratory, Madison, 1958.
- Perré, P.; Passard, J. Stress Development. In Fundamental of Wood Drying: Perré, P. Ed.; European COST E15; A.R.BO.LOR: Nancy, France, 2007; pp 243–271.
- Haslett, A. N. Suitability of Oil Palm Trunk for Timber Uses. J. Trop. For. Sci. 1990, 2, 243–251.
- Vetter, R. E.; Sá Ribeiro, R. A.; Sá Ribeiro, M. G.; Ires, P. A. Miranda Studies on Drying of Imperial Bamboo. Eur. J. Wood Prod. 2015, 73, 411–414. DOI: 10.1007/s00107-015-0900-6.
- Yuniarti, K.; Ozarska, B.; Brodie, G.; Harris, G.; Waugh, G. Collapse Development of Eucalyptus Saligna under Different Drying Temperature. J. Trop. For. Sci. 2015, 27, 462–471.
- Meyer, R. W.; Barton, G. M. A. Relationship between Collapse and Extractives in Western Red Cedar. For. Prod. J. 1971, 21, 58–60.
- Simpson, W. T. Drying Wood: A Review – Part I. Drying Technol. 1983a, 2, 235–264. DOI: 10.1080/07373938308959827.
- Simpson, W. T. Drying Wood: A Review – Part II. Drying Technol. 1983b, 2, 353–368. DOI: 10.1080/07373938308959836.
- Chen, C.; Kuang, Y.; Zhu, S.; Burgert, I.; Keplinger, T.; Gong, A.; Li, T.; Berglund, L.; Eichhorn, S. J.; Hu, L. Structure–Property–Function Relationships of Natural and Engineered Wood. Nat. Rev. Mater. 2020, 5, 642–666. DOI: 10.1038/s41578-020-0195-z.
- Penvern, H.; Zhou, M.; Maillet, B.; Courtier-Murias, D.; Scheel, M.; Perrin, J.; Weitkamp, T.; Bardet, S.; Caré, S.; Coussot, P. How Bound Water Regulates Wood Drying. Phys. Rev. Appl. 2020, 14, 054051. DOI: 10.1103/PhysRevApplied.14.054051.
- Cocusse, M.; Rosales, M.; Maillet, B.; Sidi-Boulenouar, R.; Julien, E.; Caré, S.; Coussot, P. Two-Step Diffusion in Cellular Hygroscopic (Vascular Plant-like) Materials. Sci. Adv. 2022, 8, eabm7830. Published online DOI: 10.1126/sciadv.abm7830.
- Pang, S.; Langrish, T. A. G.; Keey, R. B. Moisture Movement in Softwood Timber at Elevated-Temperatures. Drying Technol. 1994, 12, 1897–1914.
- Rémond, R.; Perré, P.; Mougel, E. Using the Concept of Thin Dry Layer to Explain the Evolution of Thickness, Temperature, and Moisture Content during Convective Drying of Norway Spruce Boards. Drying Technol. 2005, 23, 249–271. DOI: 10.1081/DRT-200047918.
- Pang, S. Mathematical Modelling of Kiln Drying of Softwood Timber: Model Development, Validation, and Practical Application. Drying Technol. 2007, 25, 421–431. DOI: 10.1080/07373930601183751.
- McCurdy, M. C.; Pang, S.; Keey, R. B. Surface Colour Change in Wood during Drying above and below Fibre Saturation Point. Maderas, Cienc. Tecnol. 2006, 8, 31–40. DOI: 10.4067/S0718-221X2006000100004.
- Walker, J. C. F. 2006. Water in Wood. In Primary Wood Processing: Principles and Practice; Walker, J. C. F., Ed.; Springer: Dordrecht, The Netherlands; pp 69–94.
- Siau, J. F. 1984. Transport Processes in Wood; Springer-Verlag: Syracuse, NY.
- Pang, S.; Langrish, T. A. G.; Keey, R. B. The Heat of Sorption of Timber. Drying Technol. 1993, 11, 1071–1080. DOI: 10.1080/07373939308916883.
- Pang, S.; Herritsch, A. Physical Properties of Earlywood and Latewood of Pinus Radiata D. Don: Anisotropic Shrinkage, Equilibrium Moisture Content and Fibre Saturation Point. Walter de Gruyter 2005, 59, 654–661. DOI: 10.1515/HF.2005.105.
- Gerhards, C. C. Effect of Moisture Content and Temperature on the Mechanical Properties of Wood: An Analysis of Immediate Effects. Wood Fiber 1982, 14, 4–36.
- Báder, M.; Németh, R. Moisture-Dependent Mechanical Properties of Longitudinally Compressed Wood. Eur. J. Wood Prod. 2019, 77, 1009–1019. DOI: 10.1007/s00107-019-01448-1.
- Pang, S. Relationship between a Diffusion Model and a Transport Model for Softwood Drying. Wood Fiber Sci. 1997, 29, 58–67.
- Stanish, M. A.; Schajer, G. S.; Kayihan, F. A Mathematical Model of Drying for Hygroscopic Porous Media. AIChE J. 1986, 32, 1301–1311. DOI: 10.1002/aic.690320808.
- Perré, P.; Turner, I. Determination of the Material Property Variations across the Growth Ring of Softwood for Use in a Heterogeneous Drying Model. Part 1. Capillary Pressure, Tracheid Model and Absolute Permeability. Holzforschung 2001, 55, 318–323. DOI: 10.1515/HF.2001.052.
- Salin, J.-G.; Wamming, T. Drying of Timber in Progressive Kilns: Simulation, Quality, Energy Consumption and Drying Cost Considerations. Wood Mater. Sci. Eng. 2008, 3, 12–20. DOI: 10.1080/17480270802561003.
- Dumyang, K.; Settapong, P.; Rittiphet, C.; Khongthong, S.; Matan, N. Initiation and Termination of Liquid Flow Controlled Drying Collapse of Interconnected Parenchyma Cells in Palm Wood. Drying Technol. 2023 (published online 24 Jan. 2023). DOI: 10.1080/07373937.2023.2166949.
- Vincent, O.; Sessoms, D. A.; Huber, E. J.; Guioth, J.; Stroock, A. D. Drying by Cavitation and Poroelastic Relaxations in Porous Media with Macroscopic Pores Connected by Nanoscale Throats. Phys. Rev. Lett. 2014, 113, 134501. DOI: 10.1103/PhysRevLett.113.134501.
- US Forest Products Laboratory, Wood Shrinkage Table. http://woodbin.com/ref/wood-shrinkage-table/ (accessed November 24, 2022).
- Lazarescu, C.; Avramidis, S.; Oliveira, L. Modeling Shrinkage Response to Tensile Stresses in Wood Drying: I. Shrinkage-Mmoisture Interaction in Stress-Free Specimens. Drying Technol. 2009, 27, 1183–1191. DOI: 10.1080/07373930903263111.
- Tomad, J.; Leelatanon, S.; Jantawee, S.; Srisuchart, K.; Matan, N. Internal Stress Development within Wood during Drying: Regime and Kinetics. Drying Technol. 2023, 41, 77–88. DOI: 10.1080/07373937.2022.2084750.
- Xiang, Z.; Peralta, P.; Peszlen, I. Lumber Drying Stresses and Mitigation of Cross-Sectional Deformation. Wood Fiber Sci. 2012, 44, 94–102.
- Pang, S.; Simpson, I.; Haslett, T. Cooling and Steam Conditioning after High-Temperature Drying of Pinus Radiata Board: Experimental Investigation and Mathematical Modelling. Wood Sci. Technol. 2001, 35, 487–502. DOI: 10.1007/s00226-001-0124-2.
- Ormarsson, S.; Dahlblom, O.; Petersson, H. A Numerical Study of the Shape Stability of Sawn Timber Subjected to Moisture Part 2: Simulation of Drying Board. Wood Sci. Technol. 1999, 33, 407–423. DOI: 10.1007/s002260050126.
- Moutee, M.; Fortin, Y.; Fafard, M. A. Global Rheological Model of Wood Cantilever as Applied to Wood Drying. Wood Sci. Technol. 2007, 41, 209–234. DOI: 10.1007/s00226-006-0106-5.
- Salinas, C.; Chavez, C.; Ananias, R. A.; Elustondo, D. Unidimensional Simulation of Drying Stress in Radiata Pine Wood. Drying Technol. 2015, 33, 996–1005. DOI: 10.1080/07373937.2015.1012767.
- Ranta-Maunus, A. The Viscoelasticity of Wood at Varying Moisture Content. Wood Sci. Technol. 1975, 9, 189–205. DOI: 10.1007/BF00364637.
- Salin, J. G. Numerical Prediction of Checking during Timber Drying and a New Mechano-Sorptive Creep Model. Holz Als Roh-Und Werkstoff 1992, 50, 195–200. DOI: 10.1007/BF02663286.
- Mårtensson, A. Mechano-Sorptive Effects in Wooden Material. Wood Sci. Technol. 1994, 28, 437–449.
- Navi, P.; Stanzl-Tschegg, S. Micromechanics of Creep and Relaxation of Wood. A Review. Holzforschung 2009, 63, 186–195. DOI: 10.1515/HF.2009.013.
- Armstrong, L. D.; Kingston, R. S. T. Effect of Moisture Changes on Creep in Wood. Nature 1960, 185, 862–863. DOI: 10.1038/185862c0.
- Armstrong, L. D.; Christensen, G. N. Influence of Moisture Changes on Deformation of Wood under Stress. Nature 1961, 191, 869–870. DOI: 10.1038/191869a0.
- Olsson, A.-M.; Salmén, L.; Eder, M.; Burgert, I. Mechano-Sorptive Creep in Wood Fibres. Wood Sci. Technol. 2007, 41, 59–67. DOI: 10.1007/s00226-006-0086-5.
- Mackay, B. H.; Downes, J. G. The Effect of the Sorption Process on the Dynamic Rigidity Modulus of the Wool Fiber. J. Appl. Polym. Sci. 1959, 2, 32–38. DOI: 10.1002/app.1959.070020405.
- Byrd, V. L. Effect of Relative Humidity Changes during Creep on Handsheet Paper Properties. Tappi 1972, 55, 247–252.
- Wang, J. Z.; Dillard, D. A.; Wolcott, M. P.; Kamke, F. A.; Wilkes, G. L. Transient Moisture Effect in Fibers and Composite Materials. J. Compos. Mater. 1990, 24, 994–1009. DOI: 10.1177/002199839002400906.
- Pickett, G. The Effect of Change in Moisture-Content of the Creep of Concrete under a Sustained Load. J. Am. Concr. Inst. 1942, 13, 333–355.
- Peng, H.; Salmén, L.; Jiang, J.; Lu, J. Creep Properties of Compression Wood Fibers. Wood Sci. Technol. 2020, 54, 1497–1510. DOI: 10.1007/s00226-020-01221-1.
- Bethe, E. Strength Properties of Construction Wood Stored under Changing Climates and Mechanical Load. Holz Als Roh-Und Werkstoff 1969, 27, 291–303. DOI: 10.1007/BF02612703.
- Armstrong, L. D. Deformation of Wood in Compression during Moisture Movement. Wood Sci. 1972, 5, 81–86.
- Yang, L.; Liu, H. A Review of Eucalyptus Wood Collapse and Its Control during Drying. BioResources 2018, 13, 2171–2181. DOI: 10.15376/biores.13.1.Yang.
- Tiemann, H. D. 1913. Eucalyptus Lumber. Forest Products Laboratory, Deparatment of Agriculture: Madison, WI; p 20
- Hawley, L. F. 1931. Wood-Liquid Relations; US Department of Agriculture: Madison, WI.
- Zimmermann, M. H.; Tyree, M. T. 1983. Xylem Structure and the Ascent of Sap; Springer: Syracuse, NY.
- Skaar, C. 1988. Wood-Water Relations; Springer-Verlag: Syracuse, NY.
- Elustondo, D. Semi-Empirical Linear Correlation between Surface Tension and Thermodynamics Properties of Liquids and Vapours. Chem. Phys. 2021, 545, 111145. DOI: 10.1016/j.chemphys.2021.111145.
- Deng, Y.; Abazeri, M. Contact Angle Measurement of Wood Fibers in Surfactant and Polymer Solutions. Wood Fiber Sci. 1998, 30, 155–164.
- Kestin, J.; Sengers, J. V.; Kamgar‐Parsi, B.; Sengers, J. M. H. L. Thermophysical Properties of Fluid H2O. J. Phys. Chem. Ref. Data 1984, 13, 175–183. DOI: 10.1063/1.555707.
- Wiedenhoeft, A. 2010. Structure and Function of Wood. In Wood Handbook: Wood as an Engineering Material; Centennial, Ed.; General Technical Report FPL; GTR-190; US Department of Agriculture, Forest Service, Forest Products Laboratory: Madison, WI, 2010; Vol. 190; p 3.1–3.18. Chapter 3.
- Jinxing, L. Distribution, Size and Effective Aperture Area of the Inter-Tracheid Pits in the Radial Wall of Pinus Radiata Tracheids. Iawa J. 1989, 10, 53–58. DOI: 10.1163/22941932-90001111.
- Stamm, A. J. Maximum Effective Pit Pore Radii of the Heartwood and Sapwood of Six Softwoods as Affected by Drying and Resoaking. Wood Fiber Sci. 1970, 1, 263–269.
- Green, D. W. 1999. Mechanical Properties of Wood. In Green, D. W., Winandy, J. E., Kretschmann, D. E., Eds.; Wood Handbook; US Department of Agrieculture, Forest Service, Products Laboratory: Madison, WI; 4–1
- Magendans, J. 1999. Morphology of Pits in Hardwood Fibres; Wageningen Agricultural University: Wageningen, The Netherlands.
- Magendans, J.; van Veenendaal, W. Bordered Pits and Funnel Pits: Further Evidence of Convergent Evolution. Wageningen Agric. Univ. Pap. 1999, 99, 31–97.
- Ek, M.; Gellerstedt, G.; Henriksson, G. 2009. Wood Chemistry and Biotechnology; Walter de Gruyter: Berlin, Germany.
- Dickson, A. Mosaic, Block-Face Microscopy for Measuring Cell Dimensions, Cell Collapse, and Spatial Relationships in Wood. Iawa J. 2021, 43, 197–212. DOI: 10.1163/22941932-bja10072.
- Perré, P.; Turner, I. W. A 3-D Version of TransPore: A Comprehensive Heat and Mass Transfer Computational Model for Simulating the Drying of Porous Media. Int. J. Heat Mass Transf. 1999, 42, 4501–4521. DOI: 10.1016/S0017-9310(99)00098-8.
- Perré, P.; Keey, R. B. Drying of Wood: Principles and Practices. In Handbook of Industrial Drying; Mujumdar, A, Ed.; CRC Press: Boca Raton, FL; 2014; pp 822–872.
- Salin, J.-G. Modelling of the Behaviour of Free Water in Sapwood during Drying: Part I. A New Percolation Approach. Wood Mater. Sci. Eng. 2006, 1, 4–11. DOI: 10.1080/17480270600630927.
- Salin, J.-G. Fibre Level Modelling of Free Water Behaviour during Wood Drying and Wetting. Maderas, Cienc. Tecnol. 2011, 13, 153–162. DOI: 10.4067/S0718-221X2011000200003.
- Omoregie, Z. S. Factors Affecting the Equivalency of Different Capillary Pressure Measurement Techniques. SPE Form. Eval. 1988, 3, 147–155. DOI: 10.2118/15384-PA.
- Lewis, G. N.; Randall, M. 1961. Thermodynamics: By Gilbert Newton Lewis and Merle Randall. Rev. by Kenneth S. Pitzer and Leo Brewer, McGraw-Hill: New York, USA.
- Simpson, W. T. Predicting Equilibrium Moisture Content of Wood by Mathematical Models. Wood Fiber Sci. 1973, 5, 41–49.
- Cloutier, A.; Fortin, Y. A Model of Moisture Movement in Wood Based on Water Potential and the Determination of the Effective Water Conductivity. Wood Sci. Technol. 1993, 27, 95–114. DOI: 10.1007/BF00206228.
- Cloutier, A.; Fortin, Y. Wood Drying Modelling Based on the Water Potential Concept: Hysteresis Effects. Drying Technol. 1994, 12, 1793–1814. DOI: 10.1080/07373939408962207.
- Riley, S.; Harrington, J.; Elustondo, D. A Theoretical Analysis of the Potential Effect of Negative Pressure in Wood Drying Based on a CT-Scanner Study. Drying Technol. 2022, 40, 2975–2989. DOI: 10.1080/07373937.2021.1986062.
- Flibotte, S.; Menon, R. S.; MacKay, A. L.; Hailey, J. R. T. Proton Magnetic Resonance of Western Red Cedar. Wood Fiber Sci. 1990, 22, 362–376.
- Dawson, B. S. W.; Pearson, H.; Kimberley, M. O.; Davy, B.; Dickson, A. R. Effect of Supercritical CO2 Treatment and Kiln Drying on Collapse in Eucalyptus Nitens Wood. Eur. J. Wood Prod. 2020, 78, 209–217. DOI: 10.1007/s00107-020-01500-5.
- Yang, L.; Liu, H. Effect of Supercritical CO2 Drying on Moisture Transfer and Wood Property of Eucalyptus Urophydis. Forests 2020, 11, 1115. DOI: 10.3390/f11101115.
- Pearson, H.; Donaldson, L.; Kimberley, M. Mitigation of Cellular Collapse during Drying of Eucalyptus Nitens Wood Using Supercritical CO2 Dewatering. Iawa J. 2022, 44, 1–20. DOI: 10.1163/22941932-bja10101.
- Blakemore, P.; Northway, R. 2009. Review of, and Recommendations for, Research into Preventing or Ameliorating Drying Related Internal and Surface Checking in Commercially Important Hardwood Species in South-Eastern Australia. Final report received by FWPA in November, 2009.
- Kauman, W. Cell Collapse in Wood. CSIRO Div. For. Prod. Reprint No. 566. CSIRO Transl. Holz Als Roh-Und Werkstoff 1964, 22, 183–196. DOI: 10.1007/BF02613024.
- Karl, L. W.; Dedrick, E. L. 1950. Method Involving the Use of Chemicals for Increasing the Drying Rate of Wood, Google Patents.
- Shaozhi, Z.; Yu, P.; Dongpo, L.; Youming, Z.; Guangming, C.; Heng, L. A Thermophysical Study on the Freeze Drying of Wooden Archaeological Artifacts. J. Cult. Heritage 2016, 17, 95–101. DOI: 10.1016/j.culher.2015.07.003.
- Jones, S. P.; Slater, N. K.; Jones, M.; Ward, K.; Smith, A. D. Investigating the Processes Necessary for Satisfactory Freeze-Drying of Waterlogged Archaeological Wood. J. Archaeol. Sci. 2009, 36, 2177–2183. DOI: 10.1016/j.jas.2009.05.028.
- Grattan, D. W.; McCawley, J. C. The Potential of the Canadian Winter Climate for the Freeze-Drying of Degraded Waterlogged Wood. Stud. Conserv. 1978, 23, 157–167. DOI: 10.2307/1505844.
- Grattan, D. W.; McCawley, J. C.; Cook, C. The Potential of the Canadian Winter Climate for the Freeze-Drying of Degraded Waterlogged Wood: Part II. Stud. Conserv. 1980, 25, 118–136. DOI: 10.2307/1505808.
- Elustondo, D.; Ahmed, S.; Oliveira, L. Drying Western Red Cedar with Superheated Steam. Drying Technol. 2014, 32, 550–556. DOI: 10.1080/07373937.2013.843190.
- Elustondo, D.; Oliveira, L.; Avramidis, S. Evaluation of Three Semi-Empirical Models for Superheated Steam Vacuum Drying of Timbers. Drying Technol. 2003, 21, 875–893. DOI: 10.1081/DRT-120021690.
- Bovornset, S.; Wongwises, S. Drying Parawood with Superheated Steam. Am. J. Appl. Sci. 2007, 4, 215–219. DOI: 10.3844/ajassp.2007.215.219.
- Gard, W. F.; Riepen, M. Super Heated Steam Drying of European Hardwoods. In ISCHP 07 2007; p 143.
- Espinoza, O.; Bond, B. Vacuum Drying of Wood—State of the Art. Curr. For. Rep. 2016, 2, 223–235. DOI: 10.1007/s40725-016-0045-9.
- Ananías, R. A.; Sepúlveda-Villarroel, V.; Pérez-Peña, N.; Torres-Mella, J.; Salvo-Sepúlveda, L.; Castillo-Ulloa, D.; Salinas-Lira, C. Radio Frequency Vacuum Drying of Eucalyptus Nitens Juvenile Wood. BioRes 2020, 15, 4886–4897. DOI: 10.15376/biores.15.3.4886-4897.
- Câmpean, M.; Lazarescu, C. Considerations upon the Drying of Oak Lumber. Bull. Transilvania Univ. Brasov. For. Wood Ind. Agric. Food Eng. Ser. II 2016, 9, 37.
- Antoniow, J. S.; Maigret, J.-E.; Jensen, C.; Trannoy, N.; Chirtoc, M.; Beaugrand, J. Glass-Transition Temperature Profile Measured in a Wood Cell Wall Using Scanning Thermal Expansion Microscope (SThEM). Int. J. Thermophys. 2012, 33, 2167–2172. DOI: 10.1007/s10765-012-1313-y.
- Toba, K.; Nakai, T.; Kanbayashi, T.; Saito, H. Effects of Cyclic Drying and Moistening on the Mechanical and Physical Properties of Wood. Eur. J. Wood Prod. 2022, 80, 1333–1341. DOI: 10.1007/s00107-022-01847-x.
- Wu, Y. Q.; Hayashi, K.; Cai, Y. C. Study on Collapse-Shrinkage Characteristics in Plantation-Grown Eucalyptus Wood under Continuous and Intermittent Drying Regimes. In Defect and Diffusion Forum; 2010; Vol. 297–301; pp 1022–1026. DOI: 10.4028/www.scientific.net/DDF.297-301.1022.
- Yang, L.; Liu, H.; Cai, Y.; Hayashi, K.; Wu, Z. Effect of Drying Conditions on the Collapse-Prone Wood of Eucalyptus Urophylla. BioResources 2014, 9, 7288–7298. DOI: 10.15376/biores.9.4.7288-7298.
- Yuniarti, K.; Ozarska, B.; Brodie, G.; Harris, G.; Waugh, G. The Drying Performance and Post-Drying Qualities of Eucalyptus Saligna Exposed to Intermittent and Continuous Drying. Indones. J. For. Res. 2020, 7, 43–57. DOI: 10.20886/ijfr.2020.7.1.43-57.
- Korkut, S.; Unsal, O.; Kocaefe, D.; Aytin, A.; Gokyar, A. Evaluation of Kiln-Drying Schedules for Wild Cherry Wood (Cerasus Avium). Maderas, Cienc. Tecnol. 2013, 15, 0–0. DOI: 10.4067/S0718-221X2013005000022.
- Rahimi, S.; Faezipour, M.; Tarmian, A. Drying of Internal-Check Prone Poplar Lumber Using Three Different Conventional Kiln Drying Schedules. J. Indian Acad. Wood Sci. 2011, 8, 6–10. DOI: 10.1007/s13196-011-0016-5.
- Cronin, K.; Baucour, P.; Abodayeh, K.; Da Silva, A. B. Probabilistic Analysis of Timber Drying Schedules. Drying Technol. 2003, 21, 1433–1456. DOI: 10.1081/DRT-120024487.
- Langrish, T. A. G.; Brooke, A. S.; Davis, C. L.; Musch, H. E.; Barton, G. W. An Improved Drying Schedule for Australian Ironbark Timber: Optimisation and Experimental Validation. Drying Technol. 1997, 15, 47–70. DOI: 10.1080/07373939708917218.
- Musch, H. E.; Barton, G. W.; Langrish, T. A. G.; Brooke, A. S. Non-Linear Model Predictive Control of Timber Drying. Comput. Chem. Eng. 1998, 22, 415–425. DOI: 10.1016/S0098-1354(97)00235-4.
- Pordage, L. J.; Langrish, T. A. G. Optimisation of Hardwood Drying Schedules Allowing for Biological Variability. Drying Technol. 2000, 18, 1797–1815. DOI: 10.1080/07373930008917811.
- Rohrbach, K.; Oliveira, L.; Avramidis, S. Drying Schedule Structure and Subsequent Post-Drying Equalisation Effect on Hemlock Timber Quality. Int. Wood Prod. J. 2014, 5, 55–64. DOI: 10.1179/2042645313Y.0000000052.
- Tran, N.; Rozsa, A. N. 2000. Development of a Novel Radio Frequency Heating System for Drying Wood. In Proceedings of the 6th International IUFRO Wood Drying Conference; Vermaas, H., Steinmann, D., Eds, University of Stellenbosch, Stellenbosch, South Africa, Jan. 25–28, 1999; pp 42–44.
- Leiker, M.; Adamska, M. A. Energy Efficiency and Drying Rates during Vacuum Drying of Wood. Holz Als Roh- Und Werkstoff 2004, 62, 203–208. DOI: 10.1007/s00107-004-0479-9.
- Avramidis, S.; Liu, F. Drying Characteristics of Thick Lumber in a Laboratory Radiofrequency Vacuum Dryer. Drying Technol. 1994, 12, 1963–1981. DOI: 10.1080/07373939408962215.
- Fu, Z. Y.; Avramidis, S.; Weng, X.; Cai, Y. C.; Zhou, Y. D. Influence Mechanism of Radio Frequency Heating on Moisture Transfer and Drying Stress in Larch Boxed-Heart Square Timber. Drying Technol. 2019, 37, 1625–1632. DOI: 10.1080/07373937.2018.1526191.
- Elustondo, D.; Avramidis, S. Simulated Comparative Analysis of Sorting Strategies for RFV Drying. Wood Fiber Sci. 2003, 35, 49–55.
- Elustondo, D.; Avramidis, S.; Zwick, R. The Demonstration of Increased Lumber Value Using Optimized Lumber Sorting and Radio Frequency Vacuum Drying. For. Prod. J. 2005, 55, 76–83.
- Chen, J. J.; Han, D.; Bai, G. P.; Zheng, M. R.; Si, Z. T.; Song, Y.; Gu, J. M. Thermodynamic Analysis of a Novel Wood Drying System Based on Self-Heat Recuperation Technology. Energy Sources Part A – Recovery Util. Environ. Effects 2022, 44, 2385–2401. DOI: 10.1080/15567036.2019.1649752.
- Aziz, M.; Fushimi, C.; Kansha, Y.; Mochidzuki, K.; Kaneko, S.; Tsutsumi, A.; Matsumoto, K.; Hashimoto, T.; Kawamoto, N.; Oura, K.; et al. Innovative Energy-Efficient Biomass Drying Based on Self-Heat Recuperation Technology. Chem. Eng. Technol. 2011, 34, 1095–1103. DOI: 10.1002/ceat.201100065.
- Elustondo, D. Guest Editorial: R&D Needs in Wood Drying Technology. Drying Technol. 2014, 32, 629–630. DOI: 10.1080/07373937.2014.895141.
- Mujumdar, A. S. Superheated Steam Drying. In Handbook of Industrial Drying. Mujumdar, A. S., Ed.; CRC Press, Boca Raton, FL; 1995; Vol. 2; pp 1071–1086.
- Yamsaengsung, R.; Sattho, T. Superheated Steam Vacuum Drying of Rubberwood. Drying Technol. 2008, 26, 798–805. DOI: 10.1080/07373930802046518.
- Pang, S.; Pearson, H. Experimental Investigation and Practical Application of Superheated Steam Drying Technology for Softwood Timber. Drying Technol. 2004, 22, 2079–2094. DOI: 10.1081/DRT-200034252.
- Pang, S. Some Considerations in Simulation of Superheated Steam Drying of Softwood Lumber. Drying Technol. 1997, 15, 651–670. DOI: 10.1080/07373939708917252.
- Park, Y.; Chung, H.; Kim, H.; Yeo, H. Applicability of Continuous Process Using Saturated and Superheated Steam for Boxed Heart Square Timber Drying. J. Korean Wood Sci. Technol. 2020, 48, 121–135. DOI: 10.5658/WOOD.2020.48.2.121.
- Gard, W.; Riepen, M. 2008. Super-Heated Steam Drying in Dutch Operations. In COST E53, Delft, The Netherlands; pp 293–302.
- Jumah, R.; Mujumdar, A. Modeling Intermittent Drying Using Adaptive Neuro-Fuzzy Inference System. Drying Technol. 2005, 23, 1075–1092. DOI: 10.1081/DRT-200059138.
- Farkas, I. Use of Artificial Intelligence for the Modelling of Drying Processes. Drying Technol. 2013, 31, 848–855. DOI: 10.1080/07373937.2013.769002.
- Aghbashlo, M.; Hosseinpour, S.; Mujumdar, A. S. Application of Artificial Neural Networks (ANNs) in Drying Technology: A Comprehensive Review. Drying Technol. 2015, 33, 1397–1462. DOI: 10.1080/07373937.2015.1036288.
- Martynenko, A. Artificial Intelligence: Is It a Good Fit for Drying? Drying Technol. 2018, 36, 891–892. DOI: 10.1080/07373937.2017.1362153.
- Kato, S.; Wada, N.; Shiogai, K.; Tamaki, T.; Kagawa, T.; Toyosaki, R.; Nobuhara, H. Automatic Classification of Crack Severity from Cross-Section Image of Timber Using Simple Convolutional Neural Network. Appl. Sci. 2022, 12, 8250. DOI: 10.3390/app12168250.
- Rahimi, S.; Avramidis, S. Predicting Moisture Content in Kiln Dried Timbers Using Machine Learning. Eur. J. Wood Prod. 2022, 80, 681–692. DOI: 10.1007/s00107-022-01794-7.
- Cao, J.; Zhu, L.; Hu, Q. 2010. Decentralized Neural Network Variable Structure Controller Design for Wood Drying Process. In 22nd Chinese Control and Decision Conference, May 26–28, Xuzhou, P.R. China; pp 506–511.