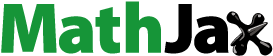
Abstract
In recent decades, wood drying has emerged as an important method to ensure wood quality and improve wood utilization. However, the addition of modifiers to wood can hinder the transfer of moisture, making the drying process difficult. Therefore, the drying of modified wood is challenging. This study focuses on poplar wood and reports the preparation of modified wood capable of releasing health-beneficial negative oxygen ions. In particular, this study examined the effect of hexacyclite on the transfer of internal moisture and heat in wood. Hexacyclite was dispersed using sodium hexametaphosphate as a dispersing agent, and the modified poplar wood was prepared via vacuum pressure impregnation. The process involved six cycles of the following treatments: a vacuum treatment (−0.08 MPa, 20 min), followed by a pressure treatment (1 MPa, 120 min), and a final atmospheric treatment (5 min). The modified wood was dried via kiln drying, during which the overall wood temperature rapidly increased, with the total drying rate also increasing by 1.05%/h. The introduction of hexacyclite potentially altered the way modified wood bound with moisture, leading to permanent changes in the porosity of cell walls and the structure of polymers and thus altering the movement of water molecules. The modified wood continuously emitted far-infrared rays with a wavelength of 8–15 μm. In some large water clusters, after the far-infrared energy was absorbed, the movement of water molecules accelerated, thereby increasing the drying rate in the wood below the fiber saturation point. Ultimately, this resulted in the modified wood drying faster and thus exhibiting a better quality.
1. Introduction
Wood, due to its high specific strength and hardness, is the most widely used biomass material.[Citation1,Citation2] Furthermore, as a renewable resource, it is commonly used in the construction, furniture, and packaging industries.[Citation3,Citation4] Therefore, research into the preparation of new materials from wood is of great significance.[Citation5] However, as natural forests are being depleted globally, access to them for logging and utilization purposes is decreasing, and they have thus been replaced by artificial fast-growing forests. Poplar wood has become an important raw material in the wood industry, with advantages such as high yield and low price.[Citation6,Citation7] However, poplar wood is soft and has poor dimensional stability, resulting in low material value.[Citation8–10] Therefore, one effective approach to enhance its usage is to modify it. Currently, the main methods adopted for this purpose include thermal modification,[Citation11] surface modification,[Citation12] and impregnation.[Citation13] Impregnation involves filling the wood with chemical substances to confer health-enhancing, flame-retardant,[Citation14] and hydrophobic[Citation15,Citation16] properties to it. Negative oxygen ions (NOI) are negatively charged individual gas molecules with redox properties and are widely used for indoor air purification.[Citation17] In modification techniques aiming to achieve health benefits, integrating the characteristics of NOI released by natural minerals into the wood allows to obtain health-promoting effects.[Citation18] Wood modification has become an effective technique for improving the value of this material.
The presence of moisture in wood affects its performance. Therefore, drying is essential to ensure wood quality and improve wood utilization.[Citation19–21] However, due to the addition of modifiers, some pores in the wood may be blocked, thereby hindering the transfer of moisture and making the drying process difficult. Therefore, while preparing modified wood, it is necessary to consider not only the drying quality and final moisture content but also the internal state of the wood. The drying of modified wood has always been a challenge in terms of ensuring the efficient application of the obtained product; therefore, it is necessary to study the drying characteristics of modified wood. For example, Cai et al.[Citation22] used the vacuum pressure impregnation method to modify poplar wood by applying 1,3-dimethylol-4,5-dihydroxyethyleneurea (DM) and maltodextrin (MA) as modifiers and explored the drying characteristics of the impregnated wood with different initial moisture contents during the drying process. Their experimental results showed that the poplar wood impregnated with a lower initial moisture content showed better drying.
Currently, nuclear magnetic resonance (NMR) spectroscopy is an efficient and nondestructive tool for determining the distribution and levels of moisture in wood as well as the distribution of pore sizes in it.[Citation23] By adopting the resin impregnation method, it is possible to obtain modified wood with excellent hardness, density, and mechanical strength. However, one of the main challenges is to determine the moisture transfer pathways during the drying process. Xu et al.[Citation24] employed the impregnation method to modify poplar wood using a water-soluble melamine urea formaldehyde (MUF) resin solution. They used low field NMR technology to study the drying of wood treated with water-soluble resin oligomers and measured the spin–spin relaxation time (T2) distribution, confirming that although the resin treatment did not increase the number of peaks in the T2 distribution, it did affect the T2 value. After the addition of resin, the drying process includes three phases, that is, moisture migration, evaporation, and resin curing. Compared with untreated wood, modified wood needs to meet the standards not only in terms of drying quality and final moisture content but also in terms of the internal state of the modifier inside the wood.[Citation22. Citation24] To explore these aspects, another study examined the drying of wood impregnated with MUF resin at different temperatures and the influence of the drying temperature on its physical and mechanical properties.[Citation25] Compared with high-temperature drying and air drying, conventional drying can achieve modified wood with a higher quality.[Citation26] The drying speed reflects the movement of moisture within the wood and is an important indicator of difficulties in drying.
In the present study, we used the vacuum pressure impregnation method to prepare modified wood capable of releasing NOI by integrating hexacyclite into it. Then, we explored the drying characteristics of the modified wood and studied the influence of hexacyclite on its internal moisture and heat transfer. The performance of the modified wood was evaluated using indicators such as density and NOI release. The micromorphology of hexacyclite within the wood was also analyzed. By comparing the drying speed and changes in moisture content between untreated wood and modified wood, we determined the variation in moisture content in the wood layers during the drying process. We used weighing, NMR imaging, and thermocouples to explore the changes in moisture content during drying, elucidating the mechanism through which hexacyclite enhances the drying of modified wood.
2. Materials and methods
2.1. Materials
Samples of Populus bolleana Lauche were purchased from the Timber Factory in Hohhot City, Inner Mongolia, China. The samples were obtained from the sapwood and shaped into dimensions of 200 mm × 100 mm × 20 mm (longitudinal × tangential × radial). Hexacyclite (8000 meshs, with an average particle size of 17.85 μm) was purchased from Shijiazhuang Zhuzhong Technology Co., Ltd, China. All purchased chemicals were used as soon as they were received. Deionized water prepared in the laboratory was used throughout the experiment.
2.2. Preparation of poplar wood modified using hexacyclite
2.2.1. Preparation of hexacyclite dispersions
Three dispersants were tested: sodium hexametaphosphate, polyethylene glycol 400, and polysorbate-20. First, 20 g of hexacyclite and various amounts of the dispersants (0.5, 1, 1.5, and 2 g, respectively) were dissolved in 100 mL of deionized water. Then, each solution was placed on a magnetic stirrer (MS-H-Pro+, Dragon Lab) and agitated at 1000 rpm until a uniform mixture was obtained. The mixed dispersive liquid was then transferred into an ultrasonic cell disruptor (SM-1800D, Nanjing Shunma Instrument Equipment, China) and subjected to ultrasonic treatment for 60 min. Finally, a series of hexacyclite dispersions were obtained.
2.2.2. Preparation of poplar wood modified by hexacyclite
Before impregnation, the wood was first dried in a forced-air oven (101 A-3B, Tianjin Hongnuo Instrument, China) at 103 °C ± 2 °C until absolute dryness was achieved, and then its weight was recorded. The poplar wood was then immersed in the hexacyclite dispersive liquid and subjected to vacuum pressure impregnation–drying–vacuum pressure impregnation cycles. First, a vacuum was drawn (−0.08 MPa, 10 min), then pressure was applied (1 MPa, 120 min). Subsequently, the wood was dried in a forced-air oven to obtained the modified wood. This process was cyclically repeated until the variation in weight was <0.02 g, which indicated that the hexacyclite had sufficiently penetrated into the wood.
2.3. Characterization of modified wood
Morphological analysis of hexacyclite and the modified wood was conducted using a scanning electron microscope (S-3400N, Hitachi, Japan), with appropriate magnification for imaging purposes. The structure and molecular bonding of the prepared samples were determined by analyzing the fourier transform infrared (FT-IR) spectra recorded using a FT-IR spectrometer (Nicolet Magna-IR 750, Thermo Nicolet Corp., USA). The obtained spectra were scanned within a spectral range of 400–4000 cm−1. The crystal structure of the samples was analyzed using an ESCA-14 (Bruker AXS GmbH, Germany) X-ray diffractometer (XRD) under Cu Kα radiation at 45 kV between 5° and 90° throughout the process.
A particle size analyzer (BT-1700, Dandong Bait Instrument, China) was used to measure the particle size of hexacyclite and the modified powder. The instrument detected particle sizes ranging from 1 to 10,000 μm, and the scanning diameter was 55 mm. The weight percentage gain (WPG) and liquid absorption rate (LAR) of the samples after impregnation with the dispersive liquid were calculated to quantify the impregnation effect. EquationEquations (1)(1)
(1) and Equation(2)
(2)
(2) were used for the calculations as follows:
(1)
(1)
(2)
(2)
where m0 is the mass of the sample in the dry state (g), ma is the dry wood mass after the impregnation treatment (g), and mb is the wet mass of the absorbed impregnation liquid after the treatment (g). To measure the air-dry density and oven-dry density of the specimens, their initial weight as well as the tangential, radial, and longitudinal dimensions were recorded. The specimens were dried in a forced-air oven and reweighed every 120 min until the weight difference between two consecutive measurements was <5% of the specimen’s weight. Then, the weight and dimensions were measured again. The air-dry density and oven-dry density of the specimens were calculated using EquationEquations (3)
(3)
(3) and Equation(4)
(4)
(4) , respectively, as follows:
(3)
(3)
(4)
(4)
where ρW is the air-dry density (g/cm3) when the wood moisture content is W, mW is the mass (g) when the moisture content is W, and VW is the volume (cm3) when the moisture content is W. In EquationEquation (4)
(4)
(4) , ρ0 is the oven-dry density of the sample (g/cm3), m0 is the oven-dry wood mass (g), and V0 is the oven-dry wood volume (cm3).
An XDB-6400 negative oxygen ion detector (Shenzhen New Landmark Environmental Protection Technology Development Co., Ltd, China) was used to monitor the amount of released ions based on the national standard GB/T28628-2012. The sample was placed in a box (400 mm × 300 mm × 400 mm) at a constant temperature and humidity. Untreated wood was used for comparison.
2.4. Drying characteristics of modified wood
The modified and untreated wood samples exhibiting similar moisture levels were placed in a high/low temperature test chamber (ZQ-GDW-500H, Instrument National Science and Technology Co., Ltd, China). Their initial moisture content before the drying treatment was 70%. During the drying process, the wood samples were removed from the chamber and weighed every 120 min until samples were oven-dry. Their drying rates were compared by examining the drying curves. The variation in wood was measured the temperatures using a TR230X temperature recorder (Dongguan NAPUI Electronic Technology Co., Ltd, China). The temperatures of each layer were recorded at different moisture contents (i.e. 40%, 30%, 20%, and 10%).
During the drying of the modified and untreated wood samples, NMR imaging (using a Bruker minispc mq20 spectrometer, Bruker, Germany) was employed to measure the spin–spin relaxation time (T2) immediately after the materials were removed from the drying oven at the abovementioned moisture contents. The settings used to obtain the T2 measurements included a Carr–Purcell–Meiboom–Gill pulse sequence with 16 scans, a recycle delay time of 2 s, and 600 echoes. In addition, the variation in moisture content in the thickness direction through the wood layers during the drying process was investigated. EquationEquation (5)(5)
(5) was used for the calculations as follows:
(5)
(5)
where ΔMCh is the deviation in moisture content in the thickness direction (%), MCS is the moisture content of the core layer (%), and MCb is the moisture content of the surface layer (%).
3. Results and discussion
3.1. Analysis of hexacyclite dispersion
As shown in , the surface layer of hexacyclite was flaky and chunky, with many villus-like protrusions capable of absorbing dust and moisture from the air. To achieve a more uniform distribution of hexacyclite within the wood, the dispersion abilities of different dispersants (i.e. sodium hexametaphosphate, polyethylene glycol 400, and polysorbate-20) were compared, and the micromorphology of the dispersed powders was analyzed. The results showed that dispersion with sodium hexametaphosphate did not damage the original hexacyclite structure (). No agglomeration was detected within the powder, and a large number of evenly distributed small particles were observed, indicating an excellent dispersion performance.
Figure 1. SEM micrographs of untreated hexacyclite (a) and hexacyclite dispersed with sodium hexametaphosphate (b). (c) Average distribution of hexacyclite particle size.
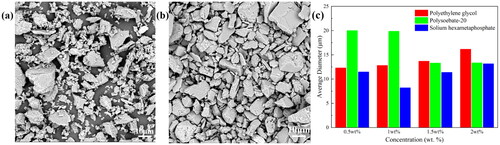
When sodium hexametaphosphate comes into contact with water, hydrolysis occurs. The hydrolysis-derived products react with certain functional groups on the surface of the powder to form hydrogen bonds, which then transform into covalent bonds,[Citation27] creating a new interface region where hexacyclite is effectively dispersed. Here, dispersibility was analyzed based on the average particle size of the powder, that is, the smaller the average particle size, the better the dispersion. The average particle size after dispersion is shown in . The graph clearly indicates that with the increase of the dispersant concentration, the average particle size decreased first and then increased, reaching its minimum when the dispersant concentration was 1%. By comparing the average particle sizes of the powders obtained using the three abovementioned dispersants, it was shown that the smallest (8.2 μm) was achieved when they were applied at a concentration of 1%. Moreover, compared with polyethylene glycol 400 and polysorbate-20, sodium hexametaphosphate showed a better performance. Therefore, the 1% sodium hexametaphosphate solution was selected as the dispersion liquid to be used for wood modification.
3.2. Analysis of poplar wood modified using hexacyclite
The radial and transverse sections of the untreated wood shown in exhibited a smooth surface, with the internal pore structure of the vessels providing space for the penetration of hexacyclite. The radial section of the modified wood () revealed the presence of a significant amount of irregularly distributed hexacyclite particles on the vessel surface within the wood’s pore structure. In addition, comparison of the microscopic morphology of the transverse sections of the untreated and modified woods revealed that the vessel walls in the modified wood were thicker than those in the untreated wood (). Therefore, it was inferred that the impregnation treatment had effectively facilitated the penetration of hexacyclite into the wood.
Figure 2. SEM micrographs of the radial (a) and transverse (c) sections of poplar wood. SEM micrographs of the radial (b) and transverse (d) sections of modified wood.

FT-IR spectroscopy () revealed that the untreated wood exhibited a broad and strong –OH stretching vibration peak at 3331.5 cm−1, whereas the modified wood showed a peak at 3344.4 cm−1 with a shifted position. This shift may be due to the penetration of the dispersant causing hydrogen bonding between the modified groups and the wood –OH. Both the untreated and modified woods showed prominent peaks indicative of cellulose at 1041.37 cm−1 and 876.48 cm−1, respectively. A characteristic absorption peak of the C = O bond in hemicellulose was observed at 1739 cm−1, and peaks indicative of the C = O stretching vibration and aromatic ring skeleton vibration appeared at 1444.90 cm−1, indicating that the lignin structure remained unchanged after modification.[Citation28] The vibration peaks became narrower and weaker after modification using hexacyclite, possibly because the –OH groups on the wood surface were replaced by hydrophobic groups inside the wood.
Figure 3. (a) FT-IR spectra of the modified wood samples. (b) and (c) XRD spectra of hexacyclite and modified wood, respectively. (d) WPG and LAR of modified wood. (e) Density of the untreated and modified wood samples. (f) Release of negative oxygen ions from the modified wood.
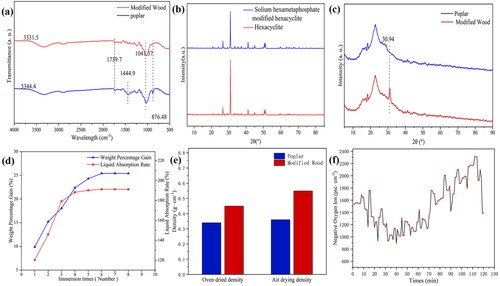
The XRD pattern of hexacyclite exhibited distinct and sharp characteristic diffraction peaks at 2θ = 27.45°, 30.74°, 37.64°, 41.24°, 44.96°, 50.53°, 51.06°, and 59.82° (). Elemental analysis revealed that hexacyclite mainly consisted of Ca, Mg, Si, Fe, and other metal oxides. The XRD spectrum () of hexacyclite dispersed with sodium hexametaphosphate showed no significant change. Both the modified and untreated woods were also subjected to XRD analysis (). The modified wood distinctly showed the characteristic diffraction peaks of hexacyclite near 30.94° and those of the wood cellulose (101) and (002) crystal planes near 18° and 22°, respectively. The position of these diffraction peaks on the crystal planes was the same as that in the untreated wood, indicating that wood modification did not damage the crystalline structure of cellulose.
The impregnation effect of hexacyclite can be estimated based on the WPG and LAR. The WPG values calculated for each immersion are shown in . After the impregnation treatment, the average WPG and LAR of the modified wood were 18.47% and 155.25%, respectively (). As the number of immersions increased, the wood’s WPG and LAR increased proportionally, but the rate of increase slowed down and approached saturation. Due to the filling of the internal voids in the wood, the WPG and LAR reached equilibrium after the sixth immersion. The air-dry and oven-dry densities of the untreated samples were 0.36 g/cm3 and 0.34 g/cm3, respectively, whereas those of the wood modified through powder impregnation were 0.47 g/cm3 and 0.43 g/cm3, respectively (). The modified wood showed a 30.55% and 26.47% increase in air-dry density and oven-dry density, respectively, compared with the untreated wood, indicating that hexacyclite had penetrated into it and that the impregnation treatment increased its density.
Table 1. Weight percentage gain and liquid absorption rate of the modified wood samples.
When the NOI concentration exceeds 1000 pcs/cm3, the air is fresh and comfortable.[Citation29] The modified wood was tested in terms of the amount of released NOI after placing in a box for 7 days and 49 days. The average NOI release of the untreated wood was around 85 pcs/cm3, which can be considered as the natural NOI amount present in the air. In the modified wood, the amount fluctuated (), with the highest and lowest levels reaching 2314 pcs/cm3 and 893 pcs/cm3, respectively, for an average of 1506.95 pcs/cm3.
3.3. Effect of hexacyclite on the temperature of modified wood
To compare the drying temperature of the untreated and modified woods. As illustrated in , the variation in surface, subsurface, and core layers temperature of wood over time was examined the temperatures. Compared with the temperature stratification observed during the drying of untreated wood (), the overall temperature of the modified wood increased rapidly during the drying process, with the values in each layer () being relatively uniform and close to the temperature of the drying medium. The average temperature gradient between layers was 0.85 °C when the wood was below the fiber saturation point, and it increased to 2.32 °C when the wood reached saturation. The overall average temperature gradient was 1.67 °C. The average temperature gradient between layers was 1.58 °C when the wood was below the fiber saturation point, and it increased to 4.04 °C when the wood exceeded the saturation point. The overall average temperature gradient was 2.89 °C. When the wood moisture content was high, the corresponding gradient was large, and the temperature variation in each layer was relatively intense. With the variation in drying time, the temperatures of each layer tended to be consistent.
Figure 4. Detection of temperature in various wood layers (a), changes in internal temperature during the drying of untreated wood (b) and modified wood (c). Changes in moisture content in the layers of untreated wood (d) and modified wood (e) at different moisture levels.
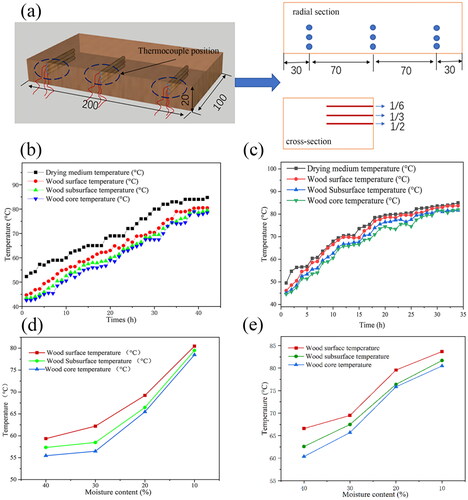
shows that as temperature increased during the drying process, the core was always lower than the surface, forming an overall temperature gradient with values decreasing from the outside to the inside. This also confirmed the higher moisture content in the modified wood layers than in the external layers. During the drying process, a temperature gradient formed, moving from the outside to the inside of the wood. The surface temperature of the modified wood gradually increased, causing the rapid evaporation of surface moisture and accelerating the internal movement of moisture. As a result, moisture evaporated from the inside to the outside, which accelerated the drying process. The internal temperature gradient of both wood types tended to increase with the decreasing moisture content, but the gradient of the modified wood increased at an obviously faster rate. The drying rate of the modified wood decreased from 30% to 20% moisture content, because the wood reached the fiber saturation point, and the internal moisture in the wood consisted of bound water.
Moisture can be present in wood in two forms, that is, free water and bound water.[Citation30] Typically, this is believed to be due to the capillary tension within the wood (lumen) moving free water during the drying process when the moisture content is above the fiber saturation point. As the moisture content decreases below this point, the form of the transferred moisture within the wood changes from free water to bound water, with the latter being removed through the pits and capillaries driven by diffusion inside the cell walls and by the moisture content gradient.[Citation31,Citation32] The average rates of temperature increase in the modified wood surface, subsurface, and core were 2.37, 2.32, and 2.27 °C/h, respectively (). The same rates in the untreated wood layers were 1.87, 1.79, and 1.74 °C/h, respectively. The surface, subsurface, and core temperatures in the modified wood increased by 0.5, 0.53, and 0.53 °C/h, respectively, compared with those in the untreated wood. Compared with the untreated wood, the internal temperature gradient of the hexacyclite-modified wood was smaller and more uniform, and moisture moved more rapidly in it.
3.4. Effect of hexacyclite on the moisture content of modified wood
As a tool for determining the distribution and content of moisture in wood, NMR can be used to invert the T2 signal and obtain the T2 distribution curve. The intensity of the NMR signal is directly proportional to the moisture content of the wood.[Citation33] In the graph shown in , the relaxation times ranging from 0.1 to 10 ms represent the bound water signals, those from 10 to 100 ms represent the free water signals, and those below 0.1 ms represent chemically bound water between cellulose, hemicellulose, and lignin. Therefore, the T2 distribution can be used to differentiate and quantify bound water in the cell walls and free water in the large voids of wood.[Citation34,Citation35] Different peaks in the inversion spectrum represent different water states, and the peak area reflects the moisture content.
Figure 5. Distribution of T2 values in the untreated wood (a) and modified wood (b) samples. (c) Hexacyclite infrared emissivity spectrum for poplar wood. Moisture content gradient in the untreated wood (d) and modified wood (e). (f) Modified wood drying rate.
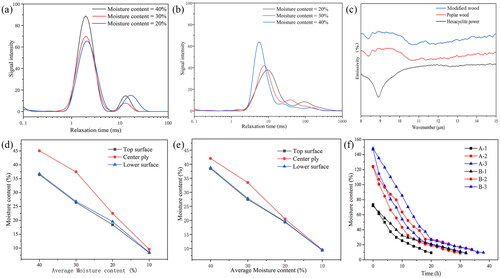
shows that in modified wood with a moisture content of 40%, peaks were present in both the 1–10 ms and 10–100 ms ranges, with the highest signal intensity corresponding to bound water, indicating that this was present in large amounts. At a moisture content of 30%, peaks were still present in the two abovementioned ranges, but the peak intensity of free water was lower than that observed at the 40% moisture content. The relaxation times of the modified wood were generally shorter than those of the untreated wood (). At a moisture content of 20%, the peak intensities of both free water and bound water in the modified wood were reduced, indicating a relatively low content of both water types. Similarly, in the untreated wood at various moisture contents, the peak intensity of bound water was higher than that of free water, indicating that the former was predominant in the internal structure of wood. The modified wood, compared with untreated wood, possibly because the introduction of hexacyclite changed the way modified wood bound with water, permanently altering the porosity and polymer structure of the cell walls and reducing the negative impact of water.[Citation36] The weakened bond between water and modified wood eventually resulted in faster drying.
During the drying process, moisture content gradients are inevitable, but if they are too high, the movement of moisture within the wood during use can cause deformation.[Citation37] In the early stages of drying, sufficient moisture on the surface is easily removed by heating. However, as drying continues, the surface moisture content gradually decreases below the fiber saturation point, and the moisture content gradient between the wood interior and the surface becomes larger. In this study, untreated wood () with moisture contents of 40%, 30%, 20%, and 10% exhibited deviations of 8.59%, 11.01%, 4.1%, and 1.21% in this parameter, respectively. The untreated wood samples showed a high moisture content gradient across the surface, subsurface, and core layers, resulting in a large deviation in moisture content and potential drying-related defects.
As shown in , the introduction of hexacyclite epistilbite promoted the movement of moisture within the wood. This led to a lower deviation in moisture content and a more uniform drying process, reducing the likelihood of drying-related defects. As the moisture content of modified wood decreased from the fiber saturation point to 10% (30%, 20%, and 10%), the drying rate slowed down and the moisture content of the core, surface, and subsurface layers gradually became more consistent. The moisture content deviations were observed 1.1%, 6.01%, and 0.21%. shows that the far-infrared emissivity of hexacyclite stabilized at 9–15 μm, and the emissivity of the modified wood was reduced compared with that of the original powder, allowing the continuous release of far-infrared radiation with wavelengths ranging between 8 and 15 μm. When large water clusters in the modified wood absorbed far-infrared energy (8–14 μm), these disintegrated into smaller water molecules, whose movement was consequently accelerated, thus speeding up the drying rate below the fiber saturation point. We believe that the addition of hexacyclite enhanced the drying performance of wood.
By measuring the variations in weight during the drying process, it was possible to determine the moisture content at different stages. The drying process can be divided into two stages based on the moisture content of the wood sample. In the first stage, this parameter is above the fiber saturation point, and moisture is transferred within the wood mainly in the form of free water. After the first stage, the moisture content decreases below the fiber saturation point. In this study, each control group consisted with a similar initial moisture content modified wood and untreated wood samples (Group I: A-1, B-1. Group II: A-2, B-2. Group III: A-3, B-3), as shown in . shows that the wood modified with sodium hexametaphosphate dried in a shorter amount of time compared with the untreated wood, indicating a faster drying rate. From the initial to the final moisture content during the drying process, the average drying rate of the untreated wood was 3.05%/h, the modified wood had an average drying rate of 4.19%/h. The overall average drying rate increased by 1.14%/h.
Table 2. Moisture content of wood samples at each drying stage.
4. Conclusion
A process to modify wood with sodium hexametaphosphate was developed, and the drying characteristics of the modified wood were investigated. Sodium hexametaphosphate exhibited good dispersion when added to the powder, with the optimal concentration being 1%. Hexacyclite was evenly distributed in the wood vessels and was shown not to alter the wood structure. The WPG and LAR of the modified wood were 18.47% and 155.25%, respectively. The average NOI released from the modified wood was 1506.95 psc/cm3.
The average rate of increase in surface temperature in the modified wood was 0.5 °C/h and that in core temperature was 0.53 °C/h. As moisture content in the modified wood decreased from the fiber saturation point to 10%, the deviation in moisture content decreased from 6.01% to 0.21%. The modified wood dried at an average drying rate of 4.19%/h, an increase of 1.14%/h.
Acknowledgments
The authors gratefully acknowledge the Inner Mongolia Autonomous Region Science and Technology Research Project (Project Approval NJZZ21016), Inner Mongolia Autonomous Region Natural Science Foundation Project (Project approval number 2021MS03087) and Fundamental Research Funds for Inner Mongolia Agricultural University (No. BR22-12-01) for their financial support and useful discussions with teachers and classmates from the School of Materials Science and Art Design at Inner Mongolia Agricultural University.
Disclosure statement
No potential conflict of interest was reported by the authors.
Additional information
Funding
References
- Goldhahn, C.; Cabane, E.; Chanana, M. Sustainability in Wood Materials Science: An Opinion about Current Material Development Techniques and the End of Lifetime Perspectives. Philos. Trans. A Math. Phys. Eng. Sci. 2021, 379, 20200339. DOI: 10.1098/rsta.2020.0339.
- Xiao, S. L.; Chen, C. J.; Xia, Q. Q.; Liu, Y.; Yao, Y.; Chen, Q. Y.; Hartsfield, M.; Brozena, A.; Tu, K. K.; Eichhorn, S. J.; et al. Lightweight, Strong, Moldable Wood via Cell Wall Engineering as a Sustainable Structural Material. Science 2021, 374, 465–471. DOI: 10.1126/science.abg9556.
- Lozhechnikova, A.; Vahtikari, K.; Hughes, M.; Österberg, M. Toward Energy Efficiency through an Optimized Use of Wood: The Development of Natural Hydrophobic Coatings That Retain Moisture-Buffering Ability. Energy Build. 2015, 105, 37–42. DOI: 10.1016/j.enbuild.2015.07.052.
- F.; Jiang, T.; Li, Y. J.; Li, Y.; Zhang, A.; Gong, J. Q.; Dai, E.; Hitz, W.; Luo; L. B. Hu. Wood-Based Nanotechnologies toward Sustainability. Adv. Mater. 2018, 30, 39. DOI: 10.1002/adma.201703453.
- Zhu, H. L.; Luo, W.; Ciesielski, P. N.; Fang, Z. Q.; Zhu, J. Y.; Henriksson, G.; Himmel, M. E.; Hu, L. B. Wood-Derived Materials for Green Electronics, Biological Devices, and Energy Applications. Chem. Rev. 2016, 116, 9305–9374. DOI: 10.1021/acs.chemrev.6b00225.
- Wang, H. W.; Yao, Q. F.; Wang, C.; Fan, B. T.; Xiong, Y.; Chen, Y. P.; Sun, Q. F.; Jin, C. D.; Ma, Z. Q. New Insight on Promoted Thermostability of Poplar Wood Modified by MnFe2O4 Nanoparticles through the Pyrolysis Behaviors and Kinetic Study. Sci. Rep. 2017, 7, 1418. DOI: 10.1038/s41598-017-01597-4.
- Kong, L. Z.; Guan, H.; Wang, X. Q. In Situ Polymerization of Furfuryl Alcohol with Ammonium Dihydrogen Phosphate in Poplar Wood for Improved Dimensional Stability and Flame Retardancy. ACS Sustainable Chem. Eng. 2018, 6, 3349–3357. DOI: 10.1021/acssuschemeng.7b03518.
- Schneider, M.; Witt, A. E. History of Wood Polymer Composite Commercialization. For. Prod. J 2004, 54, 19–24.
- He, B. J.; Zhu, J. Constructing Community Gardens? Residents’ Attitude and Behaviour towards Edible Landscapes in Emerging Urban Communities of China. Urban Urban Green 2018, 34, 154–165. DOI: 10.1016/j.ufug.2018.06.015.
- Pecenka, R.; Lenz, H.; Idler, C. Influence of the Chip Format on the Development of Mass Loss, Moisture Content and Chemical Composition of Poplar Chips during Storage and Drying in Open-Air Piles. Biomass Bioenerg. 2018, 116, 140–150. DOI: 10.1016/j.biombioe.2018.06.005.
- Korkut, S.; Budakçı, M. Effect of High-Temperature Treatment on the Mechanical Properties of Rowan (Sorbus aucuparia L.) Wood. Drying Technol. 2009, 27, 1240–1247. DOI: 10.1080/07373930903267161.
- Leslaw, K. Reinforcing Wood by Surface Modification. Compos. Struct. 2016, 158, 64–71. DOI: 10.1016/j.compstruct.2016.06.055.
- He, Z. B.; Qian; L, J.; Qu, J.; Yan, N.; Yi, S. L. Effects of Tung Oil Treatment on Wood Hygroscopicity, Dimensional Stability and Thermostability. Ind. Crop. Prod. 2019, 140, 111647. DOI: 10.1016/j.indcrop.2019.111647.
- Zhang; W, L. L.; Zhang, L.; Peng, Y.; Wang, W.; Cao, J. Z. Thermal Behavior and Flame Retardancy of Poplar Wood Impregnated with Furfuryl Alcohol Catalyzed by Boron/Phosphorus Compound System. Ind. Crop. Prod. 2022, 176, 114361. DOI: 10.1016/j.indcrop.2021.114361.
- Liu; W, S. Q.; Wan; X, C.; Zhang; A. De Crema, T.; Seeger, S. All-Organic Fluorine-Free Superhydrophobic Bulk Material with Mechanochemical Robustness and Photocatalytic Functionality. Chem. Eng. J. 2020, 385, 9. DOI: 10.1016/j.cej.2019.123969.
- Huang, W.; Li, H. Q.; Zheng, L. Z.; Lai, X. J.; Guan, H.; Wei, Y.; Feng, H. Y.; Zeng, X. R. Superhydrophobic and High-Performance Wood-Based Piezoresistive Pressure Sensors for Detecting Human Motions. Chem. Eng. J. 2021, 426, 130837. DOI: 10.1016/j.cej.2021.130837.
- Ortiz-Grisales, P.; Patiño-Murillo, J.; Duque-Grisales, E. Comparative Study of Computational Models for Reducing Air Pollution through the Generation of Negative Ions. Sustainability 2021, 13, 7197. DOI: 10.3390/su13137197.
- Sun, X. H.; Yu, Q. Q.; Yang, Z. L.; Hu, S. W.; Yang, H. Y.; Wang, X.; Zhou, J. Z.; Yu, Y.; Wang, C. Y.; Wooden, Y. D. L. "Air Purifiers" with Fire-Retardancy and Smoke-Suppression Properties. Adv. Sustain. Syst. 2022, 6, 11. DOI: 10.1002/adsu.202200346.
- Ananias, R. A.; Ulloa, J.; Elustondo, D. M.; Salinas, C.; Rebolledo, P.; Fuentes, C. Energy Consumption in Industrial Drying of Radiata Pine. Drying Technol. 2012, 30, 774–779. DOI: 10.1080/07373930903267161.
- Haque, M. N. Analysis of Heat and Mass Transfer during High-Temperature Drying of Pinus Radiata. Drying Technol. 2007, 25, 379–389. DOI: 10.1080/07373930601184551.
- Pang, S. S. Emissions from Kiln Drying of Pinus Radiata Timber: Analysis, Recovery, and Treatment. Drying Technol. 2012, 30, 1099–1104. DOI: 10.1080/07373937.2012.685673.
- Cai, M. Z.; Fu, Z. Y.; Cai, Y. C.; Zhang, Y.; Cai, J.; Xu, C. Effect of Impregnation with Maltodextrin and 1,3-Dimethylol-4,5-Dihydroxyethyleneurea on the Conventional Drying Characteristics of Poplar Wood. Appl. Sci.-Basel 2019, 9, 473. DOI: 10.3390/app9030473.
- Kekkonen, P. M.; Ylisassi, A.; Telkki, V. V. Absorption of Water in Thermally Modified Pine Wood as Studied by Nuclear Magnetic Resonance. J. Phys. Chem. C 2014, 118, 2146–2153. DOI: 10.1021/jp411199r.
- Xu, K.; Yuan, S. F.; Gao, Y. L.; Wu, Y. Q.; Zhang, J.; Li, X. J.; Lu, J. X. Characterization of Moisture States and Transport in MUF Resin-Impregnated Poplar Wood Using Low Field Nuclear Magnetic Resonance. Drying Technol. 2021, 39, 791–802. DOI: 10.1080/07373937.2020.1719503.
- Xu, K.; Gao, Y. L.; Zhang, X. M.; Li, Z. H.; Song, S. S.; Wu, Y. Q.; Li, X. J.; Lu, J. X. Effects of Drying Temperature on Hygroscopicity and Mechanical Performance of Resin-Impregnated Wood. Drying Technol. 2022, 40, 2414–2426. DOI: 10.1080/07373937.2021.1949341.
- Zhou, Y.; Jiang, X.; Liu, J. 2007 Study on Drying Characteristics of Impregnated Plantation Poplar Lumber. In Proceedings of the 5th Asia-Pacific Drying Conference, Hong Kong, China, 889–895. DOI: 10.1142/9789812771957_0130.
- Chen, L.; Li, J.; Lu, M.; Guo, X.; Zhang, H.; Han, L. Integrated Chemical and Multiscale Structural Analyses for the Processes of Acid Pretreatment and Enzymatic Hydrolysis of Corn Stover. Carbohydr. Polym. 2016, 141, 1–9. DOI: 10.1016/j.carbpol.2015.12.079.
- Labb, N.; Rials, T. G.; Kelley, S. S.; Cheng, Z.-M.; Kim, J.-Y.; Li, Y. FT-IR Imaging and Pyrolysis-Molecular Beam Mass Spectrometry: New Tools to Investigate Wood Tissues. Wood Sci. Technol. 2005, 39, 61–76. DOI: 10.1007/s00226-004-0274-0.
- Jiang, S. Y.; Ma, A.; Ramachandran, S. Negative Air Ions and Their Effects on Human Health and Air Quality Improvement. Int. J. Mol. Sci. 2018, 19, 19. DOI: 10.3390/ijms19102966.
- Eriksson, J.; Johansson, H.; Danvind, J. A. Mass Transport Model for Drying Wood under Isothermal Conditions. Dry. Technol. 2007, 25, 433–439. DOI: 10.1080/07373930601183785.
- Liu, H. H.; Ke, M. Q.; Zhou, T.; Sun, X. L. Effect of Samples Length on the Characteristics of Moisture Transfer and Shrinkage of Eucalyptus urophylla Wood during Conventional Drying. Forests 2023, 14, 1218. DOI: 10.3390/f14061218.
- Hoadley, R. B. Understanding Wood: A Craftsman’s Guide to Wood Technology, Taunton Press, 2000.
- Brownstein, K. R.; Tarr, C. E. Importance of Classical Diffusion in NMR Studies of Water in Biological Cells. Phys. Rev. A 1979, 19, 2446–2453. DOI: 10.1103/PhysRevA.19.2446.
- Riggin, M. T.; Sharp, A. R.; Kaiser, R.; Schneider, M. H. Transverse NMR Relaxation of Water in Wood. J. Appl. Polym. Sci. 1979, 23, 3147–3154. DOI: 10.1002/app.1979.070231101.
- Gao, Y. L.; Zhao, L. Y.; Jiang, J. H.; Li, Z.; Lyu, J. X. Water Absorption Properties in Transverse Direction of Heat-Treated Chinese Fir Wood Determined Using TD-NMR. Forests 2021, 12, 1545. DOI: 10.3390/f12111545.
- Beck, G.; Thybring, E. E.; Thygesen, L. G.; Hill, C. Characterization of Moisture in Acetylated and Propionylated Radiata Pine Using Low-Field Nuclear Magnetic Resonance (LFNMR) Relaxometry. Holzforschung 2018, 72, 225–233. DOI: 10.1515/hf-2017-0072.
- Elustondo, D.; Matan, N.; Langrish, T.; Pang, S. S. Advances in Wood Drying Research and Development. Drying Technol. 2023, 41, 890–914. DOI: 10.1080/07373937.2023.2205530.