Abstract
Sawn-timber drying is the wood industry’s most time- and energy-consuming process. This process can be more efficient than the conventional method by elevating the dry-bulb temperature to above 100 °C in a high-temperature drying (HTD) process, which for some species shortens the drying process by up to 50% without deteriorating the quality. Comprehending the complex correlation between the wood drying physics at high temperatures and the anatomical features of the specific species, along with its mechanical and physical properties, is crucial, as it limited its application from being broadly implemented in industry and the necessity of generalizing this method for wood species. The present study has been conducted to comprehensively review and tackle the challenges of applying this method on various species and the consequences, such as high moisture content gradients resulting in stress residual, unevenness, and color changes. Energy, environment, and economic (3E) assessments of HTD were evaluated. The accelerated drying process in HTD reduces heat losses and air leaks, resulting in higher energy efficiency than the conventional methods. Furthermore, it was proved to be 20% economically in the long term. Confliction in reported studies, such as HTD's effect on permeability and volatile organic compound (VOC) emissions, was raised, highlighting the importance of further studies for generalizing this method to adapt appropriate drying schedules, focusing on Scandinavian species by referring to previous industrial trials.
1. Background
The sawmill industry produces high-value products with a long-life cycle and ranks high in the material cascade—aspects essential for the sustainable use of resources and a circular bioeconomy. Therefore, sawn timber is one of the cornerstones of a sustainable forest products sector, and sawmills’ operations substantially impact the efficient use of forest resources, especially concerning energy efficiency. Global sawn-timber production in 2018 was 482 million m3, with a yearly ascending trend. Drying is one of the operations in the sawmill process that has the most significant effect on energy consumption and the quality of the sawn timber, thereby, the economy of this industry.
Sawmilling converts round timber of a defined geometry and quality into sawn timber. This conversion is done under given or custom-ordered specifications regarding dimensions and quality. A modern industrial sawmill, a complex, large-scale production unit, can quickly convert a log to green-sawn timber. The capacity can vary from a few thousand cubic meters to nearly one million cubic meters of sawn timber annually. Its operations are strongly influenced by the round timber resource available in the nearby region. Green-sawn timber, with a moisture content (MC) between 35 and 180%, is then dried to the desired MC, graded, and designated to a specific customer. The drying process, an essential step in producing high-quality sawn timber, can be completed within a few days or, at most, a few weeks.[Citation1]
In wood science, the amount of water in wood is measured as dry-weight MC, the ratio of the mass of water to the mass of dry wood, often expressed as a percentage. Wood is a hygroscopic material that strives to reach an equilibrium moisture content (EMC), which depends on the temperature of the surrounding air and relative humidity (RH). Before sawn timber could be used in building structures and other wooden products, significant amounts of water have to be dried to a certain pre-defined level according to the EMC of its final use in a controlled way and as soon as possible to prevent uncontrolled drying that causes distortions and cracks, to reduce the timber’s weight, and to avoid the biological degradation that may occur at MC levels above 18%. Several methods of drying sawn timber have been developed, primarily based on an air circulation process under mass and heat transfer. Most drying kilns operate at temperatures below 100 °C, known as low-temperature or conventional air-circulation drying. However, it is possible to run the drying process at temperatures up to ∼160 °C or even higher, allowing the water to vaporize by boiling off, still at atmospheric pressure. This drying method is often referred to as high-temperature drying (HTD). The common goal of all drying methods is to remove the water from the sawn timber without compromising its quality and at the lowest possible cost.
Timber drying is the primary consumer of energy at a sawmill (80% of the sawmill’s total energy consumption) in the form of electricity for the circulation fans (10–20%) and hot water in the heating batteries (80–90%),[Citation2] while a significant share of the input energy is vented away in the form of hot and moist air.
Historically, industrial drying technology for sawn timber has been developed under the context of a meager energy cost. Most of the log leads to products other than sawn timber, i.e., by-products, such as bark, sawdust, and wood chips, which have very low prices on the market compared to sawn timber prices. In such a context, the heat for drying is commonly generated by burning these by-products in the first-hand bark and sawdust. Energy efficiency has been of minor importance to the industry. As an example, the drying kilns in the Swedish sawmill industry annually evaporate 6–7 million tons of water with a total heat consumption of 6–7 TWh, but theoretically, only 4 TWh is needed (excluding the heating regime which, depending on the ambient temperature, accounts for approximately up to 30%) to release the water from the wood, which means that there is a potential to save 2–3 TWh.[Citation3] At the beginning of the 2020s, energy prices increased dramatically in Europe, creating an urge to optimize such energy-consuming processes to reduce costs and create opportunities for new uses of excess thermal energy that may be generated.[Citation4]
Furthermore, energy consumption must be reduced and optimized following the sustainable development goals (SDG) established by the United Nations member states[Citation5] and rapidly implemented.[Citation6] Timber drying relates to all subsets of SDG7, such as energy accessibility, renewable penetration, and energy intensity.[Citation7] In the process of sawn-timber production, drying is not only where the highest energy consumption lies, but it is also the most time-consuming step of sawmilling, and it has raised the debate in, e.g., Scandinavian countries around the use of HTD after having been neglected for years. Therefore, new knowledge must thus be built up to develop a new industrial drying technology supporting the industrial green transition in forestry.
HTD has been used industrially on a large scale since at least World War II in North America as a pioneering nation for species, such as Douglas fir (Pseudotsuga menziesii), red cedar (Thuja plicata) and western hemlock (Tsuga heterophylla), but the first patent related to HTD of sawn timber dates back to 1867.[Citation8] In Australia and New Zealand, HDT has also successfully been used to dry radiata pine (Pinus radiata) sawn timber within ∼30% of the number of kilns.[Citation9] The common experience is that HTD results in shorter drying time and greater demands on the kiln construction and machine installations to withstand the high temperature and the vapor pressure. However, in addition to the reduced drying time, which results in lower heat waste and consequently less energy demand, it is believed that HTD is more economical than conventional drying in regions. There have been extensive research and industrial experiments in different countries to evaluate the possibilities of implementing HTD for species other than, e.g., basswood (Tilia americana), Douglas-fir, ponderosa pine (Pinus ponderosa), radiata pine, southern yellow pine, sweet gum (Liquidambar styraciflua), true firs (Abies grandis), and western hemlock in sawmill drying. Although it has been possible to demonstrate that the total drying costs can be lower than with corresponding conventional drying and that the timber quality after drying has not significantly deteriorated, the impact of this drying method has been relatively limited, especially in Europe, without clear reason. To increase knowledge about the economic potential of HTD with a quality outcome that fulfills the market demands on the dried timber of Norway spruce and Scots pine, this knowledge review has been carried out.
The objective was to extensively review the HTD experimental and numerical studies and their implementation challenges on various wood species properties. Compared with conventional methods, this method’s potential as an appropriate alternative to the energy, economy, and environmental (3E) assessment approach was evaluated, and various conflicts in drying physics and the effect of HTD on wood properties and related knowledge gaps in each section for future research were highlighted.
1.1. Sources for the review
The current review article employed comprehensive research methodology by addressing the objectives in review flow. Two resources, including a well-known scientific database to find scientific journal articles and reports focusing on the HTD context, were categorized according to the mentioned approach. Finally, the research gaps and conflicts were evaluated, and further general recommendations were proposed, focusing on Norway spruce and Scots pine.
HTD is an established drying method for drying biomass for use as fuel and its potential integration into power stations. Although the present study does not consider these aspects, several other studies[Citation10,Citation11] have.
2. The high-temperature drying process
2.1. HTD definition and air circulation drying
A timber-drying process performed at a dry-bulb temperature (DBT) higher than or equal to 100 °C during an extensive period is considered an HTD process. Such conditions are achieved with superheated steam or superheated vapor at normal atmospheric pressure if the wet-bulb temperature (WBT) setpoint is 100 °C or lower, respectively.[Citation12] In conventional kiln drying, the DBT is usually below 90 °C.
The setup of the controlled parameters, including temperatures, relative humidity (RH), and air velocity of the climate inside the kiln through time, is known as the drying schedule. The process can be modeled by accounting for more complex phenomena, e.g., by considering the unsteady variations of heat, mass, momentum, or other factors, such as wood species and moisture transport mechanisms. shows a generic conventional drying schedule divided into different regimes, and based on wood species, the temperature level or duration of each drying stage may change.
Figure 2. The general regimes in a generic drying schedule: (1) heating, (2) capillary, (3) transition, (4) diffusion, (5) conditioning, and (6) cooling.
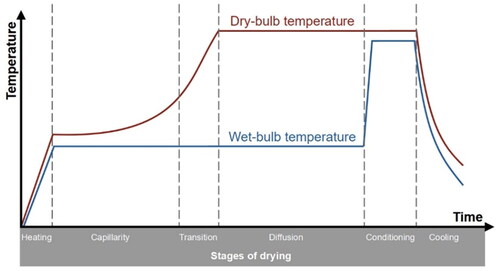
Heating regime: The timber is heated at 100% RH to improve energy transfer and plasticize the material, which restricts stress development.
Capillary regime: Liquid water evaporates as air’s RH decreases, and the gap between DBT and WBT, called wet-bulb depression (WBD), increases.
Transition regime: Most of the liquid water evaporates while part of it is present in isolated regions. Then, bound water in the cell walls also evaporates from the timber. The drying rate decreases due to regulating moisture transport through vapor diffusion.
Diffusion regime: Only bound water is left to be evaporated, and the lowest RH of the process is reached, which is often kept at a low level for the entire duration of the regime.
Conditioning regime: In this stage, RH increases abruptly to eliminate differences in MC gradients in the timber and reduce drying-induced stresses that may cause distortions of the sawn timber in use.
Cooling regime: When timber is removed from a warm kiln, the kiln and timber are cooled in a controlled way to avoid cracks and uncontrolled further drying.
In HTD, the DBT can be raised above 100 °C within the capillary or later within the diffusion regime and will continue until the scheduled targeted MC is reached. Controlled cooling of the timber to below 100 °C is performed before conditioning so that the wood can absorb moisture from the air.
Controlling the HTD process is similar to that in a low-temperature kiln except for the WBT adjustments in capillary and diffusion regime, which is less important due to the fact that the higher the drying temperature, the lower the EMC and consequently lower necessity for setting the RH. Under HTD conditions above a certain level of MC, water boils and creates an internal overpressure in the cell lumen, which creates a radically different driving force to the drying process than during conventional drying. Hence, heat and mass transfer during this process occurred rapidly, raising the importance of precise control and monitoring to adapt the drying parameters properly.
2.2. Physics of the drying process
Water transport in wood happens primarily in liquid and vapor phases. Liquid transport is driven by pressure gradients and capillary forces, which Darcy’s law can describe, and vapor transport is driven by the diffusion of water molecules, which Fick’s first law can describe. However, other mechanisms are also involved under particular drying conditions.
xThe hydrogen bonds that keep water in liquid form are suggested to have lower linkage energy than those keeping bound water connected to the wood-cell material. Thus, as the wood dries, the former type of bonds will break earlier than the latter. The stage at which cell walls are saturated with bound water, but the cell lumen no longer contains liquid water, is defined as the fiber-saturation point (FSP). During drying, the change in mechanical and physical properties of the wood as a function of MC becomes only noticeable below the FSP,[Citation13] which is considered at MC of ∼30% (at 20 °C) and strongly depends on the ambient air conditions. Specific to HTD, it is recommended for most species that once the MC of the wood is below FSP, the DBT could be raised above 100 °C. A consequence of wood drying at elevated temperatures is mild thermal degradation can occur, which in turn may reduce the modulus of elasticity (MOE), modulus of rupture (MOR), and the EMC at a specific temperature and RH combination compared to untreated wood.[Citation14–16]
Wood permeability is a critical factor in drying physics that significantly influences the fluid flow behavior toward the wood surface. Due to the complicated anatomical structure of wood exposed drying medium, specifically at HTD, inconsistency in the correlation between drying temperature and permeability has been observed in the studies. Zhang and Cai[Citation17] evaluated the effect of HTD at 110 °C on Sub-alpine fir (Abies lasiocarpa (Hook)) permeability and found that its improvement is due to opening aspirated pits or breaking the membrane of the bordered pits by vapor forces generated with high temperatures. The same correlation between permeability and HTD was reported in other research for Scots pine[Citation17] and Radiata pine.[Citation18] In contradiction with studies supporting HTD's positive effect on permeability, Leggate et al.[Citation19] showed around a 5% reduction of permeability at 180 °C compared to 40 °C for radiata pine. Comstock and Côte[Citation20] reported that red pine and eastern hemlock have lower permeability at higher temperatures due to the appearance of aspirated pits.
2.3. HTD experimental research
Examples exist where HTD provides benefits in a faster drying process compared to conventional methods. Koch et al.[Citation21] dried southern pine sawn timber (Pinus taeda) with 45 mm thickness in 6 h at 148 °C without drying defects, whereas conventional drying at 82 °C needed 120 h. Cai et al.[Citation22] evaluated applying the HTD method on sub-alpine fir (A. lasiocarpa) sawn timber since this species is prone to so-called wet pockets, and the related drying with conventional kilns is comparatively time-consuming. They reported that drying time decreased substantially, that warping of the sawn timber was reduced, and that the mechanical properties remained unaffected. Cech et al.[Citation23] observed the drying time for Eastern spruce sawn timber was reduced from 60 to 15 h by using HTD. They proposed, however, low temperature drying before HTD because of less quality degradation of the sawn timber. HTD up to 35% more pieces of sawn timber downgraded compared to conventional drying.
Most studies considered a temperature of 115 °C for HTD, although 200 °C has also been reported. McNaught et al.[Citation24] used HTD at 200 °C for splash pine (Pinus elliottii), which decreased the drying process time from 16 to 6 h, but the occurrence of drying defects in such conditions required, in their opinion, further analysis. Elustondo et al.[Citation25] evaluated the drying of 50 mm thick western red cedar (Thuja plicata) in superheated steam by utilizing an external pressure system for controlling the chamber’s pressure. The experiments showed that the sawn timber could be dried in 72 h without compromising quality, as opposed to the 360 h required in conventional drying, which additionally results in wood not meeting the accepted range of MC in the industry. It was reported that by regulating WBD between 2.2 and 3.4 °C, final product degradation was accepted, while it was rejected when it went between 3.5 and 5.7 °C. A drying process at temperatures around 200 °C will considerably change the properties of the sawn timber and should be considered a modification process (thermal modification) rather than a drying process, even though the moisture content is reduced.[Citation26]
summarizes the most significant HTD studies, indicating the correlation between elevating drying temperature, wood species, and accelerated drying time. Generally, the data shows that higher drying temperatures are correlated with shorter drying times, and higher initial MC and thicknesses of the specimens are correlated with longer drying times. In one instance for Norway spruce,[Citation27] the drying temperature was raised from 80 to 170 °C, and the drying time was shortened correspondingly from 24 to 1.2 h.
Table 1. Literature records of implementation of HTD and drying time differences.
2.4. HTD of different wood species
Wood species is one of the dominant factors regarding the applicability of HTD. Some species have been reported to tolerate HTD within constant temperature, mostly with higher permeability; others need to be dried at low temperatures until FSP, and some cannot be dried with HTD without suffering severe checking. The moisture evaporation rate is low for the species with low permeability, which causes pressure build-up, non-uniform MC distribution, internal stress development, and, consequently, various drying defects. In this regard, timber can be classified according to its ease of drying and drying degradation:[Citation52]
Hard-to-dry species: Slow and difficult to dry if the final product is to be free from damage, such as cracks and distortion. They are primarily hardwoods, such as ironbark (Eucalyptus paniculata), blackbutt (Ebenaceae spp.), sal wood (Acacia aulacocarpa), laurel wood (Terminalia elliptica) and poplar (Populus spp.)
Moderately hard-to-dry species: Tendency to crack and split during drying. They can be dried free from defects with moderately rapid drying conditions. They are also mostly exotic hardwoods, such as teak wood (Tectona grandis) and rosewood (Aniba rosaeodora).
Easy-to-dry species: may be rapidly dried without causing defects at high temperatures. They are primarily softwoods, such as chir (Pinus roxburghii), deodar (Himalayan Cedar), Douglas fir (Pseudotsuga menziesii), and radiata pine (Pinus radiata), but also Norway spruce (Picea abies) and Scots pine (Pinus sylvestris) are included in this group.
Boone et al.[Citation35] dried American elm sawn (Ulmus americana) timber from an MC of 45–20 to 7% and compared a combination of conventional drying and HTD with only HTD at airspeeds from 2.5 to 5 m/s. They reported that by starting the HTD from MC of 45 to 20%, the occurrence of end-checks could be reduced by up to 40%, while when it applied from MC of 30 to 20%, end-checks reduced by up to 80%. Therefore, applying HTD at the initial stages on green wood may jeopardize the final product quality. Boone[Citation53] tested HTD at a temperature of 110 °C to a final MC of 6–8%, and they described and addressed the primary defects, such as honeycombing around knots for various hardwood species. Novez et al.[Citation54] investigated the feasibility of HTD for Eucalyptus globulus and Pinus pinaster, and they identified the endpoint determination of the drying as a concern in HTD. Therefore, they proposed the employment of temperature measurements at the core of sawn timber, particularly for softwood, due to resin content creating defects, such as resin fluidification to the surface of the timber, which also created more significant MC gradients. The low permeability of hardwoods is another HDT issue that causes water pockets, collapse, and checking. Some species, such as those belonging to the genus oak (Quercus spp.), show collapse, honeycomb, and discoloration if dried at temperatures above 65 °C, and alternative methods, such as vacuum drying, are recommended.[Citation55]
2.5. HTD numerical modeling
Examples of numerical models for HTD exist in the literature, which often focuses on how heartwood and sapwood content affect drying behavior. The MC of heartwood is only slightly above the FSP, whereas sapwood may be completely saturated with liquid water in its voids. Different models are thus required for the drying process of heartwood and sapwood due to the additional capillary transport phenomena in the latter. To find a drying process, not creating high stresses between shrinking heartwood regions and non-shrinking sapwood regions with an MC above FSP is the critical issue in the modeling of the drying process.
Pang et al.[Citation56] modeled the temperature distribution at the surface and in the center of radiata pine heartwood and sapwood sawn timber during HTD. They accurately predicted the temperature variation from the center to the surface of the timber. However, experimental values for vapor permeability were higher than their predictions. In further studies of the same species, Pang[Citation57] successfully adapted the same model to superheated steam drying and reported that the heat transfer coefficient was much higher than that of moist air. Nijdam et al.[Citation58] adapted Pang’s model for highly permeable softwoods and introduced a moisture transport mechanism during the transition between capillarity and diffusion. Their method could highlight the importance of growth rings associated with drying exposure surface and the effect of density variations on liquid permeability at high core MC. Hukka et al.[Citation59] created highly accurate (error ≤ 2%) one-dimensional analytical models for the HTD process of Norway spruce and Scots pine for temperatures in the range of 110–120 °C. They proposed further improving the model for more significant temperature drops across stacks in the HTD process, similar drying conditions to what can be expected at a large-scale industrial drying condition.
Nevertheless, Haque[Citation60] considered that the information on heat and mass transfer coefficients present in the literature was insufficient for successfully modeling HTD and, therefore, analyzed the process at high temperatures and superheated steam to calculate both heat and mass transfer coefficients for radiata pine. Later, Nabhani et al.[Citation61] used models used for conventional drying for white spruce (Picea glauca) and adapted them to HTD by adding vapor pressure equations. They found good agreement between predicted and experimental results, except sapwood dried at a temperature above 115 °C, where the error was significant. After the advances made up to around 2010 in the field, no major numerical investigation of HTD has been published.
2.6. Energy consumption
Drying of sawn timber exclusively consumes ∼70% of the total energy in the value chain from harvest to the final product.[Citation62] The energy used in the process can be categorized into electric energy for the fans and heat from the combustion of the log fraction not used for sawn timber (∼50% of the log volume). Given this cheap sawmill waste-based heat source and the circumstance that the development of industrial drying of timber in many countries has been adapted to a low electricity cost, the energy efficiency of the drying process has consequently been neglected. Literature on energy-efficient drying is therefore scarce, and sawmills have had low incentives to overcome the inefficiency of their energy management. However, due to the recently increasing energy cost, efficiency regarding the energy generated in sawmills has become more of a focus.
Timber drying, like any other industrial process, is subject to losses and limited to a given efficiency of the equipment, and therefore, HTD could be able to reduce energy consumption by reducing processing time: a shorter drying process reduces the energy losses by air leaks, radiation, and conductive losses through kiln roofs and walls, and also electricity consumption in the fans.[Citation63] Deutschlander et al.[Citation34] showed that HTD could entail a reduction of energy consumption by up to two-thirds compared to conventional drying of grand fir (Abies grandis) and that distortions do not differ significantly between the two methods. Ananías et al.[Citation37] evaluated energy consumption for drying of radiata pine with different HTD schedules and showed that reducing the energy consumption by up to 35% was possible when raising the temperature from 85 to 120 °C and by 14% when raising it from 100 to 130 °C. Furthermore, Theppaya et al.[Citation43] reported a 44% reduction in energy consumption for drying Rubberwood (Hevea brasiliensis) at temperatures of 115 °C compared to 90 °C.
Other methods have been proposed and implemented to reduce energy consumption in conventional kilns. These methods could potentially also be implemented in HTD with even higher efficiency since recovering exhausted latent heat is much easier than in conventional air drying.[Citation64] They include pellet production for a heat and power plant with biomass from the sawmill[Citation65] or recycling the air evacuated from a drying process to a different phase of another drying process.[Citation66] Such implementations have shown the potential to generate up to 12% energy savings.
2.7. Economy
Given a specific production capacity to be maintained, HTD may require fewer or smaller kilns than conventional drying. The design of HTD kilns differs from conventional kilns in that HTD requires more thermal insulation, higher corrosion resistance, especially in the components of the heating systems, and larger fan capacity, resulting in higher initial cost investment. In the long term, however, the running costs of HTD kilns have been estimated to be 20% lower than conventional drying systems,[Citation38] and the drying temperature primarily drives these costs.[Citation67]
2.8. Environmental implications
One of the environmental issues during the drying process is the emission of volatile organic compounds (VOC), dominated by monoterpenes present in wood extractives, which are more common in softwoods than hardwoods. Monoterpenes react with sunlight and nitrogen oxide (NO) and cause the formation of photo oxidants, which have adverse effects on the respiratory system of humans and permitted values of VOC emission mentioned for sawmills certification according to ISO 14001.
The rate of VOC emission during drying depends on the temperature, species, amount of water loss, and presence of knots, which can contain even more than ten times higher VOC than normal wood.[Citation68,Citation69] Most studies reported increased VOC emission with increasing temperature, especially in softwoods, due to the thermal degradation of wood components, which occurs mainly during the initial steps of HTD.[Citation70] At the same time, some other studies reported reduced VOC emission of the HTD compared with conventional drying due to a higher MC gradient, wood surface dried faster, which reduces free water toward the surface, leading to a lower amount of organic compounds carried out to the wood’s surface and also reduction of the kiln’s venting in higher temperature because of its higher inherent energy and lower make up air requirement.[Citation71] The composition of the VOC mix has also been shown to be governed by the process temperature, as the release of different substances occurs at different temperatures.[Citation72] It was suggested that a conventional drying process before HTD or thermal treatment could reduce the VOC emission of softwoods by up to 50%.[Citation73] summarizes literature measuring VOC emission for various species in HTD by unifying values of VOC emission per milligram (mg) per kg of oven-dried wood (odw).
Table 2. VOC emission of HTD.
2.9. Drying quality and wood property changes in HTD
2.9.1. Moisture level and moisture gradients
The drying rate in timber drying, both conventional and HTD, is controlled by the power available for the evaporation of water from the wood, a process that slows down significantly once no liquid water remains to move through the cell cavities and drying regime transitioned into the diffusion regime where there are bounded water fluxes through the cross walls within up to three orders of magnitude slower.[Citation81] During the HTD process, the MC gradient initially increases asymmetrically between the upper and lower surfaces when MC is high and decreases when MC goes below the FSP. The value of FSP is temperature-dependent and must be taken into consideration with great caution since changing the drying temperature to higher levels decreased about 0.1% per 1 °C change.[Citation82] Hence, an inappropriate control of the process may result in sawn timber with a large cross-sectional moisture gradient where the surfaces are dry, and the core is still at a high MC, resulting in distortions and difficulties in further processing the timber. A so-called conditioning regime is necessary to equalize the moisture gradients and internal stress at the end of the drying process. This is usually done by steaming or spraying water and cooling the timber below 100 °C to allow moisture absorption. Another common issue regarding moisture inhomogeneities is the spread of the final average MC of the wood in different sections of the kiln, which may be related to incorrect stacking of the timber piles, malfunctioning of the kiln, or an inappropriate mix of timber with different characteristics.
2.9.2. Color change
Raising the temperature above certain levels causes wood to start degrading, a process starting at about 30 °C but will be of practical importance at temperatures above 100 °C. However, a color change is visible after drying independently of the choice of drying process or temperature level. Wood constituents decompose thermally into aromatic sugars, which give a characteristic color and darkening.[Citation83] This process occurs inevitably during the thermal modification of wood, but it is an undesired defect that also appears during HTD, and the higher the temperature, the higher the color tone. As Boonstra et al.[Citation84] pointed out, thermal degradation starts with the deacetylation of hemicelluloses, which releases acetic acid that acts as a depolymerization catalyst that further increases polysaccharide decomposition. The change in color, at least in the case of some hardwoods, occurs mainly at the beginning of the HTD process, and it correlates clearly with the wood density.[Citation85] For Norway spruce and Scots pine, the darkening of the timber under high temperatures during thermal treatments seems to be more related to the extractive content than to the average density, as it has been reported that Scots pine heartwood darkens on average more than pine sapwood or than Norway spruce.[Citation86]
2.9.3. Stress development and distortion of the sawn-timber
During drying, internal stresses develop in the timber, which in turn can cause deformations and checks. Internal stresses in wood can be due to growing stresses or anatomic features of the wood, such as spiral grain and reaction wood, but stresses can also develop due to the drying process. During HTD, water removal from the wood surface occurs quickly, resulting in severe MC gradients in the cross-section of the sawn timber, which may cause differential shrinkage accompanied by internal stresses. An uneven distribution of MC throughout the kiln may cause part of the batch to reach an MC below the target MC, which in turn causes even more excessive deformations.
The development of stresses during HTD has been studied, and the literature shows that during HTD, there is more stress development than conventional drying caused by a rapid MC reduction at the wood surface in HTD. Such residual stresses are caused by the interaction of growth characteristics, shrinkage anisotropy, temperature, and MC gradients,[Citation87] and can, in the worst case, cause internal cell collapse,[Citation88] even though that does not seem to be the case for Norway spruce and Scots pine. As reported by Zhou et al.,[Citation82] they evaluated drying and residual stress of Chinese fir at HTD, which showed different behavior than conventional drying due to higher effectiveness stress reversal caused by stress relaxation in high temperatures above FSP.[Citation82] Furthermore, since water movement along the fiber direction is up to 15 times faster than across it, checking from the end of the sawn timber is common during timber drying in general, and it can be expected that this phenomenon would become even more severe with HTD.
Various nondestructive testing methods exist for assessing stress development and MC changes during the drying process with high accuracies, such as acoustic emission,[Citation89,Citation90] nuclear magnetic resonance,[Citation91] and X-ray computed tomography.[Citation92]
Internal stress development is not exclusive to HTD, and there have been attempts to minimize the residual stress after conventional drying, e.g., by thermal post-treatment.[Citation93] The experiments performed by Zhan et al.[Citation94] on larch (Larix gmelinii) showed that the residual stress decreases after thermal post-treatment. The high temperature involved in HTD could, therefore, be beneficial in minimizing internal stress.
2.9.4. Creep relaxation
A distinction should be made between creep phenomena in the cross-section of the timber during the drying process and the effects of the process on the creep behavior of the timber once in use. As MC gradients develop during drying, those portions of the wood below FSP tend to shrink but are constrained by the other regions of the wood above FSP, which tend to keep their shape, resulting in stress due to the mutual constraint. If kept over time, these stresses would cause a permanent deformation through creep. HTD may, therefore, cause more severe creep-related deformations due to causing a more significant moisture gradient. However, this does not seem to be the case, and it has been reported that increased temperature even provides more resistance toward creep deformation,[Citation95–98] possibly due to the more significant plastic deformations of the material with increasing temperature.
2.9.5. Durability
When assessed in comparison with conventional kiln drying, HTD does not show significant differences regarding the decay resistance of the wood. Both methods seem to provide significantly lower durability to decay compared to air drying (seasoning) against fungus and termite feeding, while some literature suggested that keeping drying at high temperatures at high MC can inactivate some of the fungicide effects of certain wood extractives and, therefore, deteriorate the decay resistance.[Citation99] Thermal modification at higher temperatures can improve decay resistance due to the reduction of available feed for fungi.[Citation100,Citation101] There is, nevertheless, a considerable knowledge gap regarding the assessment of the durability of HTD timber in the literature.
2.9.6. Dimensional stability
Dimensional stability has been reported to be improved after HTD,[Citation102] specifically in the softwoods, due to the higher susceptibility of hardwoods to thermal degradation and, consequently, a higher tendency for shrinkage and collapse.[Citation103] Elevating the drying temperature can cause morphological changes, affecting the hygroscopicity characteristic of the wood[Citation104] and reducing the share of hemicellulose content.[Citation105] Kininmonth[Citation106] reported the reduction of swelling by elevating the drying temperature from 77 to 115 °C for radiata pine from 2.7 to 2.3%, respectively. Sik et al.[Citation107] conducted an experimental study on the effect of HTD and conventional drying on the adsorption and desorption process on rubberwood at different RH conditions and reported lower EMC values in all RH compared with conventional drying. For instance, The EMC can reach 16% at 120 °C compared to 26% at 60 °C.[Citation15] Frühwald[Citation108] evaluated the effect of HTD on the twist of Norway spruce for temperatures between 80 and 170 °C and reported that the shape stability improved at 120 °C drying temperature and that the value of twist in various moisture cycling was smaller than at lower temperatures. The tangential to radial shrinkage coefficient (T/R) ratio decreased by increasing drying temperature. provides a (T/R) ratio for HTD and conventional methods.
Table 3. Tangential to radial shrinkage ratio of HTD.
3. Aspect on the kiln design for the use in HTD
As previously mentioned, the design of conventional drying kilns and HTD kilns differs mainly in that more insulation and resistance to corrosion are required. Higher temperature and vapor pressure place greater demands regarding the tightness of the construction, fan motors, and buffers. Stainless steel or aluminum is often used for walls, doors, and roofs, and mineral or glass wool that withstands high temperatures is preferred for thermal insulation.
3.1. Temperature and RH sensors
In HTD, the psychrometer can continue to be used as a sensor for process control since the WBT can be below 100 °C in those process regimes when some air is present in the kiln. Water vapor is superheated for a WBT of 100 °C or higher and works as a drying medium. Under such conditions, no inlet venting is needed since the vapor is generated at atmospheric pressure. Since no outdoor air intake is needed in such cases, HTD is a more energy-efficient air-circulating drying method in terms of heat input per kg of evaporated water.
3.2. Fans
As the evaporation capacity during HTD is higher than during conventional kiln drying, often greater air velocity is used in the process. The air velocity should be adapted to maintain uniform drying in various drying conditions.[Citation111] For instance, at initial stages and MC above 40%, higher air velocity can increase the drying rate, and in later phases where diffusion phenomena dominate, the velocity can be reduced, resulting in reduced electrical energy consumption. Higher air velocity can also prevent discoloration during the drying process.[Citation33]
3.3. Drying schedules
The level of sophistication regarding the management of the drying parameters is highly species dependent ranges from simply constant humidity and temperature for long periods to more complex schemes allowing varying climates. Langrish et al.[Citation112] optimized a conventional and HTD schedule of radiata pine sapwood with an initial MC of 140%. They found out that during the first 10 h, the drying rates for different schedules are the same and proposed increasing the drying temperature linearly from 108 to 155 °C. Another idea described in the literature is temperature cycling. Vabsteenkiste et al.[Citation113] conducted HTD experiments with temperature oscillations between 60 and 120 °C on poplar. The oscillations led to more moisture moving from the core to the surface of the sawn timber, resulting in more uniform MC levels and reduced drying defects. Similar principles of temperature oscillations have been tested with conventional drying as well. Milić et al.[Citation114] reported shorter drying times for beech with oscillating climates than with the conventional method, and Lefevre et al.[Citation115] reported that climate oscillations led to mechano-sorptive effects, causing stress relaxation of the wood.
Among the most significant challenges for controlling and managing the HTD process are the drying material being above the water boiling point and boiling water in the wood, which can only be overcome by exact measurements of the drying medium humidity and the wood MC.[Citation14]
3.4. Thermal modification effects
Thermal modification (TM) is proposed immediately after HTD for uniform moisture distribution, relieving stresses, and reducing surface checks. Various efforts have been made to model TM in the HTD process. Pang et al.[Citation116] conducted experimental tests and modeled cooling and steam conditioning of radiata pine sapwood after HTD (120 °C) to achieve 6% MC and evaluated the conditioning effect by the cup and strain test. They recommended immediate cooling between 75 and 90 °C under a prolonged time based on the board thickness and controlled conditioning for up to 4 h. Frühwald[Citation27] evaluated European larch, Norway spruce, and Siberian larch in drying temperatures of 80, 120, and 170 °C and compared the results with thermally modified timber at 190–210 °C (Thermowood® process) and reported that drying time reduced by up to 73%. The mechanical properties of the used wood species were different. At the same time, the MOE and bending strength remained approximately constant after changing temperatures from 120 to 170 °C compared with thermally modified timber. In contrast, the sorption rate for Norway spruce was higher than that of the other species. Lee et al.[Citation117] investigated the effect of high temperature and low humidity pretreatment on the drying rate of Japanese cedar (Cryptomeria japonica) with 150 × 150 mm cross-section. The results indicated that internal and surface cracking was reduced by applying this method.
Rautkari et al.[Citation118] studied Scots pine sapwood and heartwood, which were thermally modified under saturated steam at 120, 150, and 180 °C in a high-pressure reactor, and analyzed the MOE and Brinell hardness. They concluded thermal modification under a saturated steam atmosphere could be done at a lower temperature than the usual 180–210 °C.
4. HTD implementation for Norway spruce and Scots pine
During the 1990s, especially Swedish sawmills showed interest in drying with higher temperatures to shorten drying times and obtain less distorted sawn timber. Attempts were made to raise the drying temperature at Swedish sawmills for Norway spruce and Scots pine, although the focus was kept around 90 °C, the HDT approach was thoroughly evaluated. Kilns at large sawmills were already designed for HTD using aluminum or stainless-steel components, but the peripheral equipment, e.g., boiler and stacking (more sticks were needed), did not allow the kilns to run at higher temperatures. Overall, the trials gave promising results, and balancing short-time drying and achieving an even MC in the batch remained challenging. These industrial trials concluded that conditioning became more critical in limiting MC gradients. Today, it is, however, difficult to find documentation about these trials with HTD since they were industrial, and the documentation has been lost. Some documentation exists in the Swedish language in the form of reports from the Swedish Institute of Wood Technology Research (Trätek).
For drying Norway spruce, Rosenkilde et al.[Citation119] attempted 12 industrial trials in an HTD kiln with a capacity of 6 m3, a thickness of 44–50 mm, a fan speed of 6 m/s, and a maximum DBT of 125 °C with the aim of reduction of color change, MC gradient, and residual stress. They recommended a drying schedule with the following phases: Heating, Gradual DBT increasing, Pre-cooling, Conditioning, Cooling.
They found that condensation on the wood surface occurred, which improved equalization and reached an even MC profile, and final cooling reduced the drying defects. Although unavoidable discoloration, specifically in sapwood, was observed because of higher extractives, no significant defects were reported. The total drying time was 43 h, and they repeated the same setup at 95 °C and reported 73 h while discoloration was reduced.
4.1. Capacity
Increased capacity is the goal of any investment in HTD. In the 1990s, drying at a maximum of 70 °C typically required a drying time of ∼175 h, at a maximum of 90 °C, it required 75 h; and at 115 °C, ∼50 h. Higher temperature correlates strongly negatively with the required drying time; the drying capacity more than doubles when the drying temperature is raised from 70 to 90 °C and almost quadruples when the temperature is raised to 115 °C. This comparison assumes the sufficient capacity to generate the thermal energy required at all temperature levels.
4.2. Quality
Mostly for the Scots pine and Norway spruce in the lab scale, drying schedules were developed for DBT of 70, 90, and 115 °C, and the resulting wood quality was comparable. What differentiates wood that has undergone HTD from regularly dried wood is a particular shade difference in the surface color. At higher temperatures, superficial resin pockets are often emptied, which can be problematic for some applications but advantageous for others because resin liquefaction is avoided during final use. Increased temperature reduced wood distortion by between 20 and 50% immediately after drying. However, the extent to which the wood deforms after re-moistening has not been studied.
Broad industrial applications for evaluating the final quality of HT dried sawn timber have not been implemented and are restricted to a few countries, such as New Zealand, and predominantly for Radiata pine. This specific species dried using HTD is suitable for structural applications due to inherent warp resistance, however, HTD can degrade the machinability due to unexpectedly low MC, which entails high brittleness and therefore makes the material less suitable for applications where reprocessing is required. Furthermore, this method is not recommended in furniture applications with <50 mm thickness due to surface discoloration.[Citation9]
4.3. Maintenance and control
Higher drying temperatures require increased maintenance and control of both equipment and obtained drying quality compared to lower temperatures. Since HTD is faster than conventional drying, a relatively small error in the equipment may have disproportionately large effects on the timber quality. This means the equipment must be maintained and checked in tighter intervals for HTD than for drying at 70 °C. Consequently, the personnel require more training, e.g., knowledge of the drying process, measurement methods, and the technology of the dryer.
4.4. Required investment
The following can be stated based on the conditions applied in the 1990s. Compared with conventional drying, the initial investment required for the drying equipment and kiln construction became more expensive since all interior walls must be coated with foam glass, and concrete blocks must be painted to withstand high temperatures. However, if normalized by the increased capacity, the lower running cost quickly offset that cost increase. Considerable uncertainty was the investment cost for the boiler since it was unclear whether it would need to be replaced or rebuilt to handle higher temperatures and pressure. In addition, the distribution network for the heat to the dryers might consequentially need to be replaced or rebuilt so that the lines, gaskets, and shunt groups can withstand the higher temperatures and pressures. The temperature difference between the drying temperature and the incoming water temperature in the heating batteries was recommended to be in the order of 30 °C, but it was found that also a lower difference may be feasible if the temperatures are higher during the diffusion phase of the drying itself. Another investment deemed necessary in the 1990s was new stick distributors to enable the handling of more sticks. The number of sticks must often be increased to reduce the risk of impact in the wood at the sticks and to constrain the deformations. Today, more sticks are generally used at sawmills compared to the 1990s.
4.5. Drying cost
Drying costs are difficult to assess since they depend on the drying stages to be included. A comparative example from the 1990s, where the temperature was raised from 70 to 115 °C, showed that the savings would be SEK 50/m3 for a medium-sized sawmill if no investment in a new boiler and stick-distributer were required. This example accounted for a possible minor downgrading of the wood due to the higher temperatures.
5. Conclusion
The gathered experience reveals that HTD can be advantageous since it offers the potential to reduce drying time, but the complicated drying mechanisms in elevated temperatures needed be developed, and scientific reports confliction should substantiate any firm to avoid wood defects observed in HTD. The main challenges that still restrict the broad industrial implementation of HTD for various wood species are: (i) providing a suitable drying schedule that matches with abrupt changes in wood during the HTD, specifically for most hardwoods, which are less permeable compared to softwoods, (ii) surface discoloration, (iii) internal stresses caused by high MC gradients, and (iv) high complexity of kilns due to increased demands on sealing and more corrosion-resistant materials. Remarks and proposed future research in HTD based on the revised literature are summarized as follows:
The effect of HTD on wood properties, such as permeability, needs to be clarified to give a reliable estimation in adapting drying schedules.
The potential for reduced energy consumption and VOC emission in HTD should be assessed more thoroughly.
Numerical simulations are required to better understand MC changes during drying under various setups and parameter variations.
The potential for HTD to be integrated with new methods of energy recovery systems should be investigated for a more energy-efficient drying process.
More reliable methods for monitoring stress development during the HTD process are required.
The kiln structure may require further optimization for efficient HTD of Swedish wood species.
Knowledge is required regarding the optimal point of time for starting the conditioning treatment after HTD.
Disclosure statement
The authors report no conflicts of interest. The authors alone are responsible for the content and writing of the paper.
Correction Statement
This article has been corrected with minor changes. These changes do not impact the academic content of the article.
References
- Niemz, P.; Teischinger, A.; Sandberg, D., Eds. Springer Handbook of Wood Science and Technology; Springer: Heidelberg, Germany, 2023.
- Andersson, J.-E.; Lycken, A.; Nordman, R.; Olsson, M.; Räftegård, O.; Wamming, T. State of the Art–Energianvändning I Den Svenska Sågverksindustrin; SP Technical Research Institute of Sweden, 2011.
- Couceiro, J. X-Ray Computed Tomography to Study Moisture Distribution in Wood; Doctoral dissertation, Luleå Tekniska Universite, 2019.
- Hosseini, S. M.; Peer, A. Wood Products Manufacturing Optimization: A Survey. IEEE Access 2022, 10, 121653–121683. DOI: 10.1109/ACCESS.2022.3223053.
- Burke, J.; Goriss-Hunter, A.; Emmett, S. Policy, Discourse and Epistemology in Inclusive Education. In Inclusion, Equity, Diversity, and Social Justice in Education: A Critical Exploration of the Sustainable Development Goals; Springer Nature Singapore: Singapore, 2023; pp 13–27. DOI: 10.1007/978-981-19-5008-7_2.
- Engström, R. E.; Destouni, G.; Howells, M.; Ramaswamy, V.; Rogner, H.; Bazilian, M. Cross-Scale Water and Land Impacts of Local Climate and Energy Policy—A Local Swedish Analysis of Selected SDG Interactions. Sustainability 2019, 11, 1847. DOI: 10.3390/su11071847.
- Dmytrów, K.; Bieszk-Stolorz, B.; Landmesser-Rusek, J. Sustainable Energy in European Countries: Analysis of Sustainable Development Goal 7 Using the Dynamic Time Warping Method. Energies 2022, 15, 7756. DOI: 10.3390/en15207756.
- Smith, J. Apparatus Drying and Sbasoning Lumber; Google Patents-USA, 1867.
- Haslett, A. Drying Radiata Pine in New Zealand; New Zealand Forest Research Institute: Rotorua, 1998.
- Stenström, S. Drying of Biofuels from the Forest—A Review. Drying Technol. 2017, 35, 1167–1181. DOI: 10.1080/07373937.2016.1258571.
- Liu, M.; Xu, C.; Han, X.; Liu, R.; Qin, Y.; Yan, J. Integration of Evaporative Dryers into Lignite-Fired Power Plants: A Review. Drying Technol. 2020, 38, 1996–2014. DOI: 10.1080/07373937.2019.1606824.
- Kollmann, F. F.; Cote, W. A. Principles of Wood Science and Technology. Volume I: Solid Wood; Springer-Verlag: Berlin, 1984.
- Babiak, M.; Kúdela, J. A Contribution to the Definition of the Fiber Saturation Point. Wood Sci. Technol. 1995, 29, 217–226. DOI: 10.1007/BF00204589.
- Konopka, A.; Baranski, J.; Hurakova, T.; Klement, I. The Influence of High Temperature Wood Drying Conditions Using Air-Steam Mixture on Its Properties. Ann. Warsaw Univ. Life Sci. SGGW For. Wood Technol. 2015, 90, 107–114.
- Simpson, W. T.; Rosen, H. N. Equilibrium Moisture Content of Wood at High Temperatures. Wood Fiber Sci. 1981, 13, 150–158.
- Thompson, W. S.; Stevens, R. R. Influence of Thermal Treatments on the Mechanical and Chemical Properties of Wood: A Review of Research at the Mississippi Forest Products Laboratory. Proceedings of Research Conference on High-Temperature Drying Effects on Mechanical Properties of Softwood Lumber; Department of Agriculture, Forest Service, Forest Products Laboratory, 1976; p 9.
- Terziev, N.; Daniel, G. Industrial Kiln Drying and Its Effect on Microstructure, Impregnation and Properties of Scots Pine Timber Impregnated for above Ground Use. Part 2. Effect of Drying on Microstructure and Some Mechanical Properties of Scots Pine Wood. Holzforschung 2002, 56, 434–439.
- Booker, R.; Evans, J. The Effect of Drying Schedule on the Radial Permeability of Pinus radiata D. Holz als Roh- und Werkstoff, 1994, 52, 150-156. DOI: 10.5555/19940607361.
- Leggate, W.; Kumar, C.; McGavin, R. L.; Faircloth, A.; Knackstedt, M. The Effects of Drying Method on the Wood Permeability, Wettability, Treatability, and Gluability of Southern Pine from Australia. BioResources 2020, 16, 698–720. DOI: 10.15376/biores.16.1.698-720.
- Comstock, G.; Côté Jr, W. Factors Affecting Permeability and Pit Aspiration in Coniferous Sapwood. Wood Sci. Technol. 1968, 2, 279–291. DOI: 10.1007/BF00350274.
- Koch, P.; Wellford, W. L. Some Mechanical Properties of Small Specimens Cut from 1.79-Inch-Thick Southern Pine Dried for 6 Hours at 300 F or for 5 Days at 180 Fa Comparison. Wood Fiber Sci. 1977, 8, 235–240.
- Cai, L.; Oliveira, L. C. Experimental Evaluation and Modeling of High Temperature Drying of Sub-Alpine Fir. Wood Sci. Technol. 2010, 44, 243–252. DOI: 10.1007/s00226-009-0280-3.
- Cech, M. Y.; Huffman, D. R. High-Temperature Drying of Mixed Spruce, Jack Pine, and Bals Am Fir. Publ. Dep. Environ. Can. For. Serv. 1974, 1337, 1-15. DOI: 10.5555/19740618752.
- McNaught, A. M.; Gough, D. K. Drying 40-Mm-Thick Slash Pine in 2.5 Hours at 200 °C. For. Prod. J. 1995, 45, 51.
- Elustondo, D.; Ahmed, S.; Oliveira, L. Drying Western Red Cedar with Superheated Steam. Drying Technol. 2014, 32, 550–556. DOI: 10.1080/07373937.2013.843190.
- Sandberg, D.; Kutnar, A.; Karlsson, O.; Jones, D. Wood Modification Technologies: Principles, Sustainability, and the Need for Innovation; CRC Press, 2021.
- Frühwald, E. Effect of High-Temperature Drying on Properties of Norway Spruce and Larch. Holz als Roh-und Werkstoff 2007, 65, 411–418.
- Konopka, A.; Barański, J. The Dying Medium Temperature Impact on the Final Moisture Content of Pine Wood at Constant Drying Time. Ann. Warsaw Univ. Life Sci. SGGW For. Wood Technol. 2016, 95, 91–96.
- Schneider, A. Untersuchungen Uber Den Einfluss Der Feuchttemperatur Auf Den Verlauf Der Hochtemperaturtrocknung Von Schnittholz. Holz als Roh-und Werkstoff 1981, 39, 379–387. DOI: 10.1007/BF02606450.
- Borrega, M.; Kärenlampi, P. P. Three Mechanisms Affecting the Mechanical Properties of Spruce Wood Dried at High Temperatures. J. Wood Sci. 2010, 56, 87–94. DOI: 10.1007/s10086-009-1076-7.
- Hansson, L.; Antti, A. The Effect of Microwave Drying on Norway Spruce Woods Strength: A Comparison with Conventional Drying. J. Mater. Process. Technol. 2003, 141, 41–50. DOI: 10.1016/S0924-0136(02)01102-0.
- Kerr, C. Nz Radiata Pine Users Manual; New Zealand Institute of Forestry: New Zealand, 1996.
- McCurdy, M. C. Efficient Kiln Drying of Quality Softwood Timber; PhD thesis, Chemical and Process Engineering to the University of Canterbury, 2006.
- Deutschlander, H. M.; Wagner, F. G.; Folk, R. L.; Shook, S. R.; Everson, D. O.; Association, W. D. K. Impacts of High-Temperature and Restraint on Kiln-Dried Grand Fir Studs Curve Sawn from Small-Diameter Logs; Moscow, Idaho: Western Dry Kiln Association, 2006.
- Boone, R. S. Kiln Drying 4/4 American Elm and Sweetgum Lumber with a Combination of Conventional-Temperature and High-Temperature Schedules; US Department of Agriculture, Forest Service, Forest Products Laboratory, 1989; Vol. 491.
- Klement, I.; Huráková, T. Determining the Influence of Sample Thickness on the High-Temperature Drying of Beech Wood (Fagus sylvatica L.). BioResources 2016, 11, 5424–5434. DOI: 10.15376/biores.11.2.5424-5434.
- Ananias, R. A.; Ulloa, J.; Elustondo, D. M.; Salinas, C.; Rebolledo, P.; Fuentes, C. Energy Consumption in Industrial Drying of Radiata Pine. Drying Technol. 2012, 30, 774–779. DOI: 10.1080/07373937.2012.663029.
- Garrahan, P.; Lavoie, V.; Elustondo, D. Element 5: Application of Rapid Drying Technologies to Streamline the Lumber Manufacturing Process Applying Rapid Drying Technologies to Canadian Spf Lumber; FPInnovations: Canada, 2011.
- Yamsaengsung, R.; Tabtiang, S. Hybrid Drying of Rubberwood Using Superheated Steam and Hot Air in a Pilot-Scale. Drying Technol. 2011, 29, 1170–1178. DOI: 10.1080/07373937.2011.574805.
- Thiam, M.; Milota, M. R.; Leichti, R. J. Effect of High-Temperature Drying on Bending and Shear Strengths of Western Hemlock Lumber. For. Prod. J. 2002, 52, 64–68.
- Cai, L.; Oliveira, L. C. Impact of High-Temperature Schedules on Drying of Spruce and Pine. Drying Technol. 2008, 26, 1160–1164. DOI: 10.1080/07373930802266280.
- Chanpet, M.; Rakmak, N.; Matan, N.; Siripatana, C. Effect of Air Velocity, Temperature, and Relative Humidity on Drying Kinetics of Rubberwood. Heliyon 2020, 6, e05151. DOI: 10.1016/j.heliyon.2020.e05151.
- Theppaya, T.; Prasertsan, S. Optimization of Rubber Wood Drying by Response Surface Method and Multiple Contour Plots. Drying Technol. 2004, 22, 1637–1660. DOI: 10.1081/DRT-200025622.
- Koch, P. Strength of Southern Pine Lumber Dried at High Temperatures. Proceedings of the Research Conference on High‐Temperature Drying Effects on Mechanical Properties of Softwood Lumber, 1976; pp 38–49.
- Gilmore, R. Summary of Work on High Temperature Drying at North Carolina State University. Proceedings of the Research Conference on High Temperature Drying Effects on Mechanical Properties of Softwood Lumber, 1976.
- Troxell, H. E.; Luza, M. P. High-Temperature Drying Properties of Lodgepole Pine Studs; College of Forestry and Natural Resources Colorado State University: Fort Collins, Colorado, 1972.
- Khamtree, S.; Ratanawilai, T.; Nuntadusit, C. An Approach for Indirect Monitoring of Moisture Content in Rubberwood (Hevea brasiliensis) during Hot Air Drying. Drying Technol. 2019, 37, 2116–2125. DOI: 10.1080/07373937.2018.1563901.
- Baranski, J. Moisture Content during and after High-and Normal-Temperature Drying Processes of Wood. Drying Technol. 2018, 36, 751–761. DOI: 10.1080/07373937.2017.1355319.
- Milota, M. R. Warp and Shrinkage of Hem-Fir Stud Lumber Dried at Conventional and High Temperatures. For. Prod. J. 2000, 50, 79-84.
- Bovornset, S.; Wongwises, S. Drying Parawood with Superheated Steam. Am. J. Appl. Sci. 2007, 4, 215–219. DOI: 10.3844/ajassp.2007.215.219.
- Basilico, C.; Genevaux, J.; Martin, M. High Temperature Drying of Wood Semi-Industrial Kiln Experiments. Drying Technol. 1990, 8, 751–765. DOI: 10.1080/07373939008959913.
- Bootle, K. R. Wood in Australia. Types, Properties and Uses; McGraw-Hill Book Company: Sydney, 1983.
- Boone, R. High-Temperature Kiln-Drying of 4/4 Lumber from 12 Hardwood Species. For. Prod. J. 1984, 34, 10–18.
- Alverez Noves, H.; Fernandez-Golfin Seco, J. I. Practical Evaluation and Operation of Superheated Steam Drying Process with Different Softwoods and Hardwoods. Holz als Roh-und Werkstoff 1994, 52, 135–138. DOI: 10.1007/BF02615209.
- Jomaa, W.; Baixeras, O. Discontinuous Vacuum Drying of Oak Wood: Modelling and Experimental Investigations. Drying Technol. 1997, 15, 2129–2144. DOI: 10.1080/07373939708917355.
- Pang, S.; Haslett, A. The Application of Mathematical Models to the Commercial High-Temperature Drying of Softwood Lumber. Drying Technol. 1995, 13, 1635–1674. DOI: 10.1080/07373939508917045.
- Pang, S. Some Considerations in Simulation of Superheated Steam Drying of Softwood Lumber. Drying Technol. 1997, 15, 651–670. DOI: 10.1080/07373939708917252.
- Nijdam, J.; Langrish, T.; Keey, R. A High-Temperature Drying Model for Softwood Timber. Chem. Eng. Sci. 2000, 55, 3585–3598. DOI: 10.1016/S0009-2509(00)00042-7.
- Hukka, A. Evaluation of Parameter Values for a High-Temperature Drying Simulation Model Using Direct Drying Experiments. Drying Technol. 1997, 15, 1213–1229. DOI: 10.1080/07373939708917288.
- Haque, M. Analysis of Heat and Mass Transfer during High-Temperature Drying of Pinus radiata. Drying Technol. 2007, 25, 379–389. DOI: 10.1080/07373930601184551.
- Nabhani, M.; Laghdir, A.; Fortin, Y. Simulation of High-Temperature Drying of Wood. Drying Technol. 2010, 28, 1142–1147. DOI: 10.1080/07373937.2010.483563.
- Milota, M. Corrim Report: Module B Life Cycle Assessment for the Production of Pacific Northwest Softwood Lumber; Oregon State University: Corvallis, OR, 2015.
- Taylor, F. W. A Comparison of Energy Requirements for Kiln-Drying Southern Pine at Different Drying Temperatures. Wood Fiber Sci. 1982, 14, 246–253.
- Mujumdar, A. S. Handbook of Industrial Drying; CRC Press: Boca Raton, 2006.
- Anderson, J.-O.; Toffolo, A. Improving Energy Efficiency of Sawmill Industrial Sites by Integration with Pellet and CHP Plants. Appl. Energy 2013, 111, 791–800. DOI: 10.1016/j.apenergy.2013.05.066.
- Andersson, J.-O.; Westerlund, L. Mind Based Optimisation and Energy Analysis of a Sawmill Production Line. Conference on Process Integration, Modelling and Optimisation for Energy Saving and Pollution Reduction: 28/08/2010-01/09/2010; 2010; pp 1–5.
- Salin, J.-G. Determination of the Most Economical Drying Schedule and Air Velocity in Softwood Drying; AB Trätek, Swedish Institute for Wood Technology Research: Stockholm, Sweden, 2001.
- Wu, J.; Milota, M. R. Effect of Temperature and Humidity on Total Hydrocarbon Emissions from Douglas-Fir Lumber. For. Prod. J. 1999, 49, 52.
- Ingram, L. L. Jr.; Templeton, M. C.; McGraw, G. W.; Hemingway, R. W. Knot, Heartwood, and Sapwood Extractives Related to VOCs from Drying Southern Pine Lumber. J. Wood Chem. Technol. 2000, 20, 415–439. DOI: 10.1080/02773810009351892.
- McDonald, A.; Gifford, J.; Steward, D.; Dare, P.; Riley, S.; Simpson, I. Air Emission from Timber Drying: High Temperature Drying and Re-Drying of CCA Treated Timber. Eur. J. Wood Wood Prod. 2004, 62, 291–302.
- Milota, M. R.; Wu, J.; Association, W. D. K. Changes in the VOC Emissions from Douglas-Fir Lumber with Temperature and Humidity; Oregon State University Corvallis, Oregon, Western Dry Kiln Association, 1997.
- Otwell, L. P.; Hittmeier, M. E.; Hooda, U.; Yan, H.; Su, W.; Banerjee, S. Haps Release from Wood Drying. Environ. Sci. Technol. 2000, 34, 2280–2283. DOI: 10.1021/es991083q.
- Hyttinen, M.; Masalin-Weijo, M.; Kalliokoski, P.; Pasanen, P. Comparison of VOC Emissions between Air-Dried and Heat-Treated Norway Spruce (Picea abies), Scots Pine (Pinus sylvesteris) and European Aspen (Populus tremula) Wood. Atmos. Environ. 2010, 44, 5028–5033. DOI: 10.1016/j.atmosenv.2010.07.018.
- Ingram, L.; Taylor, F.; Templeton, M. Volatile Organic Compound Emissions from Southern Pine Kilns. Proceedings of the Drying Pacific Northwest Species for Quality Markets, 1996; pp 41–45.
- McDonald, A.; Wastney, S. Analysis of Volatile Emissions from Kiln Drying of Radiata Pine. Proceedings of the 8th International Symposium on Wood and Pulping Chemistry, 1995; pp 434–436.
- Englund, F.; Nussbaum, R. M. Monoterpenes in Scots Pine and Norway Spruce and Their Emission during Kiln Drying; Holzforschung: Germany, 2000.
- Milota, M. R. HAP and VOC Emissions from White Fir Lumber Dried at High and Conventional Temperatures. For. Prod. J. 2003, 53, 60.
- Milota, M. R. Hazardous Air Pollutant Emissions from Lumber Drying. For. Prod. J. 2006, 56, 79.
- Milota, M. R.; Mosher, P. Emissions from Western Hemlock Lumber during Drying. For. Prod. J. 2006, 56, 66.
- Dahlen, J.; Shmulsky, R.; Jones, D. Volatile Organic Compounds Emitted during the Kiln Drying of Southern Pine Utility Poles. For. Prod. J. 2010, 60, 629–631. DOI: 10.13073/0015-7473-60.7.629.
- Skaar, C. Wood-Water Relations; Springer: Berlin, Heidelberg, 2012.
- Zhou, F.; Fu, Z.; Zhou, Y.; Zhao, J.; Gao, X.; Jiang, J. Moisture Transfer and Stress Development during High-Temperature Drying of Chinese Fir. Drying Technol. 2019, 38, 545–554. DOI: 10.1080/07373937.2019.1588900.
- Torniainen, P.; Popescu, C.-M.; Jones, D.; Scharf, A.; Sandberg, D. Correlation of Studies between Colour, Structure and Mechanical Properties of Commercially Produced Thermowood® Treated Norway Spruce and Scots Pine. Forests 2021, 12, 1165. DOI: 10.3390/f12091165.
- Boonstra, M. J.; Tjeerdsma, B. Chemical Analysis of Heat Treated Softwoods. Holz als Roh-und Werkstoff 2006, 64, 204–211.
- Klement, I.; Marko, P. Colour Changes of Beech Wood (Fagus sylvatica L.) during High Temperature Drying Process. Wood Res. 2009, 54, 45–54.
- Dagbro, O.; Torniainen, P.; Karlsson, O.; Morén, T. Colour Responses from Wood, Thermally Modified in Superheated Steam and Pressurized Steam Atmospheres. Wood Mater. Sci. Eng. 2010, 5, 211–219. DOI: 10.1080/17480272.2010.520739.
- Cheng, W.; Morooka, T.; Wu, Q.; Liu, Y. Characterization of Tangential Shrinkage Stresses of Wood during Drying under Superheated Steam above 100 C. For. Prod. J. 2007, 57, 39.
- Shahverdi, M.; Eshaghi, S.; Gholamiyan, H.; Haji Mirza Tayeb, S. Effect of Wood Drying Conditions on Occurrence of Collapse during Drying. Proceedings of 53rd International Convention of Society of Wood Science and Technology, October, 2010; pp 11–14.
- Kowalski, S. J.; Molinski, W.; Musielak, G. The Identification of Fracture in Dried Wood Based on Theoretical Modelling and Acoustic Emission. Wood Sci. Technol. 2004, 38, 35–52. DOI: 10.1007/s00226-003-0211-7.
- Nasir, V.; Ayanleye, S.; Kazemirad, S.; Sassani, F.; Adamopoulos, S. Acoustic Emission Monitoring of Wood Materials and Timber Structures: A Critical Review. Constr. Build. Mater. 2022, 350, 128877. DOI: 10.1016/j.conbuildmat.2022.128877.
- Guo, P.; Yang, C.; Yu, D.; Xu, Z. An Optimized UMR Sensor for Non-destructive Measurements of Moisture in Wood. Appl. Phys. A 2022, 128, 907. DOI: 10.1007/s00339-022-06016-8.
- Hansson, L.; Cherepanova, E. Determination of Wood Moisture Properties Using a CT-Scanner in a Controlled High-Temperature Environment. J. Civ. Eng. Archit. 2012, 6, 372.
- Boonstra, M. J.; Van Acker, J.; Tjeerdsma, B. F.; Kegel, E. V. Strength Properties of Thermally Modified Softwoods and Its Relation to Polymeric Structural Wood Constituents. Ann. For. Sci. 2007, 64, 679–690. DOI: 10.1051/forest:2007048.
- Zhan, J.-F.; Avramidis, S. Impact of Conventional Drying and Thermal Post-Treatment on the Residual Stresses and Shape Deformations of Larch Lumber. Drying Technol. 2017, 35, 15–24. DOI: 10.1080/07373937.2016.1156123.
- Bengtsson, C.; Kliger, R. Bending Creep of High-Temperature Dried Spruce Timber; Holzforschung: Germany, 2003.
- Honfi, D.; Mårtensson, A.; Thelandersson, S.; Kliger, R. Modelling of Bending Creep of Low-and High-Temperature-Dried Spruce Timber. Wood Sci. Technol. 2014, 48, 23–36. DOI: 10.1007/s00226-013-0581-4.
- Hanhijärvi, A. Deformation Properties of Finnish Spruce and Pine Wood in Tangential and Radial Directions in Association to High Temperature Drying Part IV. Modelling. Holz als Roh-und Werkstoff 2000, 58, 211–216.
- Hanhijärvi, A. Deformation Properties of Finnish Spruce and Pine Wood in Tangential and Radial Directions in Association to High Temperature Drying Part II. Experimental Results under Constant Conditions (Viscoelastic Creep). Holz als Roh-und Werkstoff 1999, 57, 365–372.
- Sehlstedt-Persson, M.; Wamming, T. Wood Drying Process: Impact on Scots Pine Lumber Durability. J. Wood Sci. 2010, 56, 25–32. DOI: 10.1007/s10086-009-1066-9.
- Calonego, F. W.; Severo, E. T. D.; Furtado, E. L. Decay Resistance of Thermally-Modified Eucalyptus Grandis Wood at 140, 160, 180, 200 and 220 C. Bioresour. Technol. 2010, 101, 9391–9394. DOI: 10.1016/j.biortech.2010.06.119.
- Vidholdová, Z.; Kačík, F.; Reinprecht, L.; Kučerová, V.; Luptáková, J. Changes in Chemical Structure of Thermally Modified Spruce Wood Due to Decaying Fungi. J. Fungi 2022, 8, 739. DOI: 10.3390/jof8070739.
- Edvardsen, K.; Sandland, K. M. Increased Drying Temperature-Its Influence on the Dimensional Stability of Wood. Holz als Roh-und Werkstoff 1999, 57, 207–209.
- Chang, C.; Keith, C. Properties of Heat-Darkened Wood. II Mechanical Properties and Gluability; Forest Products Laboratory: Canada, 1978.
- Bao, Y.; Zhou, Y. Comparative Study of Moisture Absorption and Dimensional Stability of Chinese Cedar Wood with Conventional Drying and Superheated Steam Drying. Drying Technol. 2017, 35, 860–866. DOI: 10.1080/07373937.2016.1222417.
- Bekhta, P.; Niemz, P. Effect of High Temperature on the Change in Color, Dimensional Stability and Mechanical Properties of Spruce Wood; Holzforschung: Germany, 2003.
- Kininmonth, J. Effect of Timber Drying Temperature on Subsequent Moisture and Dimensional Changes. NZJ For. Sci. 1976, 6, 101–107.
- Sik, H. S.; Choo, K. T.; Zakaria, S.; Ahmad, S.; How, S. S.; Chia, C. H.; Yusoff, M. Dimensional Stability of High Temperature-Dried Rubberwood Solid Lumber at Two Equilibrium Moisture Content Conditions. Drying Technol. 2010, 28, 1083–1090. DOI: 10.1080/07373937.2010.506162.
- Frühwald, E. Effect of High-Temperature Drying and Restraint on Twist of Norway Spruce. Drying Technol. 2007, 25, 489–496. DOI: 10.1080/07373930601184056.
- Espenas, L. D. Shrinkage of Douglas Fir, Western Hemlock, and Red Alder as Affected by Drying Conditions; Corvallis, Oregon State University School of Forestry, Forest Research Laboratory, 1971.
- Herrera-Díaz, R.; Sepúlveda-Villarroel, V.; Pérez-Peña, N.; Salvo-Sepúlveda, L.; Salinas-Lira, C.; Llano-Ponte, R.; Ananías, R. A. Effect of Wood Drying and Heat Modification on Some Physical and Mechanical Properties of Radiata Pine. Drying Technol. 2018, 36, 537–544. DOI: 10.1080/07373937.2017.1342094.
- Morén, T. The Basics of Wood Drying: Moisture Dynamics, Drying Methods, Wood Responses; Valutec AB: Sweden, 2016.
- Langrish, T. A.; Nijdam, J. J.; Keey, R. B. The Optimisation of Drying Schedules for Pinus radiata Sapwood Boards. Dev. Chem. Eng. Mineral Process. 2004, 12, 237–248. DOI: 10.1002/apj.5500120402.
- Vansteenkiste, D.; Stevens, M.; Van Acker, J. High Temperature Drying of Fresh Sawn Poplar Wood in an Experimental Convective Dryer. Eur. J. Wood Wood Prod. 1997, 55, 307–314.
- Milić, G.; Kolin, B.; Lovrić, A.; Todorović, N.; Popadić, R. Drying of Beech (Fagus sylvatica L.) Timber in Oscillation Climates: Drying Time and Quality. Holzforschung 2013, 67, 805–813. DOI: 10.1515/hf-2012-0203.
- De La Cruz-Lefevre, M.; Rémond, R.; Aléon, D.; Perré, P. Effect of Oscillating Drying Conditions on Variations in the Moisture Content Field inside Wood Boards. Wood Mater. Sci. Eng. 2010, 5, 84–90. DOI: 10.1080/17480272.2010.484103.
- Pang, S.; Simpson, I.; Haslett, T. Cooling and Steam Conditioning after High-Temperature Drying of Pinus radiata Board: Experimental Investigation and Mathematical Modelling. Wood Sci. Technol. 2001, 35, 487–502. DOI: 10.1007/s00226-001-0124-2.
- Lee, N.-H.; Li, C.; Zhao, X.-F.; Park, M.-J. Effect of Pretreatment with High Temperature and Low Humidity on Drying Time and Prevention of Checking during Radio-Frequency/Vacuum Drying of Japanese Cedar Pillar. J. Wood Sci. 2010, 56, 19–24. DOI: 10.1007/s10086-009-1050-4.
- Rautkari, L.; Honkanen, J.; Hill, C. A.; Ridley-Ellis, D.; Hughes, M. Mechanical and Physical Properties of Thermally Modified Scots Pine Wood in High Pressure Reactor under Saturated Steam at 120, 150 and 180 C. Eur. J. Wood Prod. 2014, 72, 33–41. DOI: 10.1007/s00107-013-0749-5.
- Rosenkilde, A.; Widell, K.-O.; Blomberg, J. Högtemperaturtorkning Samt Torkning Vid 90 C, Dess Effekter På Virke Och Kådlåpor; Trätek: Sweden, 2002.