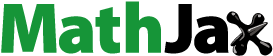
ABSTRACT
All-ceramic Li batteries (CLBs) are expected as next generation energy storage devices because of their potential to have higher energy density and safety than nowadays Li-ion batteries. Garnet structured Li7La3Zr2O12 (LLZO) plays an important role on CLB developments due to its fast Li-ion conductivity, intrinsic stability toward Li and high chemical and electrochemical stabilities. After a decade of researches, many problems have been answered for LLZO-based CLB developments but still numerous challenges left to be solved. This review presents the latest efforts on the development of LLZO based CLBs, which covers the advances in LLZO crystal structure to increase its ionic conductivity and progresses in the use of Li as the electrode, regarding to its intrinsic chemical stability toward Li and interface elaboration for allowing Li dendrite suppression. On the positive electrode developments, chemical compatibility of various active materials and strategies to circumvent the incompatibility issue at high sintering temperatures are inspected.
Introduction
Since the first commercialization in 1991 by Sony, Li-ion batteries (LIBs) have been developed into one of the most popular energy storage device due to their high volumetric and gravimetric energy densities. The application of LIBs for nowadays covers from portable electronic devices, such as smart phones and laptops, to large-scale applications, such as electric vehicles and stationary energy storage for renewable energy sources. Nevertheless, the demand for a battery with even higher energy and power densities is stronger than ever because of the desire for extending working hours for a device between two charges of the used battery. All-ceramic Li batteries (CLBs) have been proposed to be one of the most promising technologies for next generation electrochemical energy storage regarding their high energy density by replacing graphite electrode to metallic Li electrode, extended cycle life because of no accumulated formation of solid electrolyte interface and inherent safety due to the non-flammable ceramic components Citation1Citation2.
One of the key components for a CLB development is having a suitable solid state ionic conductor as its solid electrolyte. Among various Li-ion conductors, garnet structured materials based on Li7La3Zr2O12 (LLZO) has been attracting tremendous attention since the first report by Murugan et al. in 2007, due to its high Li-ionic conductivity (> 10–4 S cm−1 at RT), wide electrochemical window, stability against metallic Li, high ionic transference number (~1) and environment friendliness [Citation3]. However, after more than a decade of intensive development, a demonstration of a practical CLB based on LLZO at/near RT, with area capacity > 3 mAh cm−2, is still not available. Challenges regarding to CLB developments based on LLZO are linked to its Li dendrite formation, interface instability, and high processing temperature that causes chemical instability between the used active electrode material and LLZO and internally elemental diffusion at high temperatures.
In this review, we mainly focus on reviewing the progress of CLB development by using garnet structured LLZO. Therefore, articles that apply organic polymer or liquid electrolytes in the electrochemical performances are excluded from this review. The review starts from the discussion of the ionic conductivity of LLZO by using different substitutions and their chemical stabilities toward metallic Li. It is then followed by the development of negative electrode by using metallic Li that causes interface instability and dendrite formation to short circuiting symmetric Li/LLZO/Li cells. It further covers the chemical compatibilities between LLZOs and active positive electrode materials at high sintering temperatures and strategies that are proposed to circumvent the chemical instability between LLZO and the used positive active electrode materials at high sintering temperatures so that the proof of concept CLBs can be demonstrated.
The developments of Li7La3Zr2O12 solid electrolytes
The increases of Li-ion conductivities
The first highly conductive garnet structured LLZO was reported by Murugan et al. in 2007[Citation3]. It was found at a later time that there are two crystallographic modifications existing for LLZO; a cubic and a tetragonal phase. Due to the full occupation of Li-sites by Li-ions, tetragonal LLZO shows a complete ordering of the Li-ions and long Li–Li hopping distances while that for cubic LLZO only has partial occupation by Li-ions on the Li(1) and Li(2) sites to give short Li–Li hopping distances[Citation4]. Therefore, the formation of tetragonal phase LLZO reduces its Li-ion conductivity from a cubic phase ones, >10−4 S·cm−1, to a much lower value of 1 × 10–6 S·cm−1 at RT [Citation4 Citation5]. It is understood that the material was usually contaminated by Al during their high temperature sintering processes due to the reaction with frequently used alumina crucibles. Further researches on Al-substituted Li7La3Zr2O12 by using XRD, neutron powder diffraction, and TEM precession electron diffraction reveal that Al3+ is incorporated in the garnet lattices on the tetrahedral 24d Li(1) sites, thus stabilizing the LLZO to cubic phase and resulting in the very short Li–Li distance in the migration pathway to give the good Li-ion-conduction properties when compared to the tetragonal one, ) [Citation4,Citation6–Citation8]. Bernstein et al. used density functional theory and variable cell shape molecular dynamics simulations to investigate the driving force for the phase transition from tetragonal to cubic and suggested that the critical substitution concentration of Al3+ necessary to obtain highly conductive cubic phase of LLZO is at 0.2 mol%, i.e. Li6.4 Al0.2La3Zr2O12[Citation9]. Later, Rangasamy et al. experimentally show that 0.204 mol% of Al3+ is required to stabilize LLZO as the cubic phase at RT while 0.389 mol% of Al3+ is the limitation of Al3+ solubility in LLZO[Citation10]. A phase transition from cubic to tetragonal LLZO was identified when the Li-ion content increased from 6.24 to 7.32 mol% due to the filling of Li(2) vacancies by the addition Li-ions, which distorts the structure from cubic to tetragonal phase for further uptake of Li in the garnet structure was also shown, ). Since the incorporation of Al3+ from Al2O3 crucible to LLZO could dramatically affect the finally reported conductivity, a note on the used crucible for the sintering process of LLZO is always important for the evaluation on how a substitution could affect the final total conductivity of a LLZO sample, .
Table 1. List of total conductivity and used crucible for LLZO with different substitutions.
Figure 1. Development of LLZO based solid electrolyte. (a) Crystal structure of cubic Li7La3Zr2O12 (top) and coordination polyhedra around the Li(1) and Li(2) sites (bottom)[Citation4]. Reproduced with permission[Citation4]. Copyright 2011, Elsevier. (b) The loop structures constructed by Li atomic arrangement in cubic (top) and tetragonal (bottom) Li7La3Zr2O12 with occupancy value g for each site in the parenthesis[Citation4]. Reproduced with permission[Citation4]. Copyright 2011, Elsevier. (c) A phase transition from cubic to tetragonal Li7La3Zr2O12 when Li increase from 6.24 mole to 7.32 mole[Citation10]. Reproduced with permission[Citation10]. Copyright 2012, Elsevier. (d) The effect of Li-ion concentration to bulk ionic conductivities in various garnet-type Li3+xLa3M2O12 at RT[Citation11]. Reproduced with permission[Citation11]. Copyright (2012), American Physical Society.
![Figure 1. Development of LLZO based solid electrolyte. (a) Crystal structure of cubic Li7La3Zr2O12 (top) and coordination polyhedra around the Li(1) and Li(2) sites (bottom)[Citation4]. Reproduced with permission[Citation4]. Copyright 2011, Elsevier. (b) The loop structures constructed by Li atomic arrangement in cubic (top) and tetragonal (bottom) Li7La3Zr2O12 with occupancy value g for each site in the parenthesis[Citation4]. Reproduced with permission[Citation4]. Copyright 2011, Elsevier. (c) A phase transition from cubic to tetragonal Li7La3Zr2O12 when Li increase from 6.24 mole to 7.32 mole[Citation10]. Reproduced with permission[Citation10]. Copyright 2012, Elsevier. (d) The effect of Li-ion concentration to bulk ionic conductivities in various garnet-type Li3+xLa3M2O12 at RT[Citation11]. Reproduced with permission[Citation11]. Copyright (2012), American Physical Society.](/cms/asset/0d868b1a-598c-4e02-ae76-76f1b2e45531/ymte_a_1746539_f0001_oc.jpg)
Xu et al. investigated the Li-ion transport mechanism in cubic phase Li3+xLa3M2O12 (M = Te6+, Nb5+, Zr4+) by using ab initio tools[Citation11]. As the materials Li3La3Te2O12, Li5La3Nb2O12 and Li7La3Zr2O12 are compared, the Li concentrations are not the only variables but also the valences of the dopants, i.e. Te6+, Nb5+, Zr4+. They suggest that the conductivity is affected far more by Li-ion concentration than by different dopant elements or lattice parameters for LLZO, . When the Li-ion concentration is low, such as that in Li3LaTe2O12, Li-ions only occupy tetrahedral Li(1) sites and not octahedral Li(2) sites. The Li(1) sites act as energetic traps to immobilize the Li-ions in these positions, leading to a low Li-ion conductivity. When the Li-ion concentration is increased, such as that in Li5La3Nb2O12 (33.34% Li(2) sites full) and Li7La3Zr2O12 (90% Li(2) sites full), the Li-ions on Li(1) sites remain stable but that on Li(2) sites are able to migrate from one site to the other. This migration of Li-ions between Li(2)-Li(2) sites passing their common tetrahedral Li(1) sites to give Li7La3Zr2O12 a very high Li-ion conductivity. The higher occupancy of Li(2) sites, > 90% Li(2) sites full for LLZO, although helpful in promoting more Li-ion transport, leaves insufficient vacancies for ion migration. Therefore, Xu et al. advise against further increasing Li concentration to higher than 7 in the garnet structure materials. Similar conclusion was also drawn experimentally by Li et al. using Ta-substituted LLZO[Citation12]. The high Li-ion conductivity in Li7-xLa3Zr2-xTaxO12 indicates that the appropriate Li-ion concentration in LLZO for Li-ion transport is in the range of 6.4 ≤ x ≤ 6.6. The best ratio of Li-ion occupancy to the vacancy of the octahedral sites in LLZO appears to be around 3: 1.
Further researches on the development of LLZO were focused on obtaining cubic phase and optimize its Li-ion conductivity by using different substitutions while controlling the Li concentration in the LLZO structure in between 6.2 and 7, . The substitutions are mainly carried out on Li-sites by using Al3+ and Ga3+ and on Zr-sites by using Ta5+ and Nb5+, . For the Al-substituted LLZO, the highest total conductivity is reported by Kumazaki et al. for 6.8 × 10–4 S·cm−1 at 25°C[Citation13]. Their ICP result shows that the sample contains 1.7 wt% Al and 0.1 wt% Si due to the contamination from used SiO2 milling ball and Al2O3 crucible. Selected-area electron diffraction (SAED), electron energy-loss spectroscopy (EELS) were used to determine the presence of crystallites of LiAl5O8 and LiAlSiO4 at the grain boundaries that facilitate the Li-ion transport across the grain boundaries and increase the total conductivity of the sample, ) [Citation13 Citation14]. Similar to Al-substitution, the substitution of Ga3+ also replace the Li-ions in LLZO. The highest reported total conductivity by using Ga-substitution is 1.84 × 10–3 S·cm−1 for Li6.65Ga0.15La3Zr1.9Sc0.1O12 at 27°C[Citation15]. Although the substitution of Ga3+ to Li-sites also obstructs the Li+ percolation network, as that for Al-substitution, []71Ga NMR shows that Ga3+ has the preferential occupation of tetrahedral 24d Li(1) sites over the distorted octahedral 96 h Li(2) sites, ). Furthermore, theoretical calculations based on density functional theory and force-field-based molecular dynamic simulations suggest that the lower Ga3+-Li+ repulsion allows Li-ions more easily to diffuse within their immediate surroundings than that for Al3+-Li+ [Citation16,Citation17]. Therefore, the higher population of local mobility Li+ on 96 h Li(2) sites with lower Coulombic repulsion from Ga3+ promotes the long-range diffusion of Li+ in LLZO, which leading to the higher ionic conductivity and lower activation energy of the Ga-substituted LLZO [Citation15,Citation18,Citation19]. Comparing to the substitution of Al3+ and Ga3+, the substitution of Fe3+ to Li-sites is much less studied even though the reported total conductivity of Li6.4Fe0.2La3Zr2O12 is as high as 1.82 × 10–3 S·cm−1[Citation20]. Rettenwander et al. studied Li6.4Fe0.2La3Zr2O12 by using 57Fe Mössbauer spectra to show that about 96% of the total substituted iron occurs as Fe3+ and 4% as Fe2+, ) [Citation21]. Roughly two-thirds of the Fe3+ are assigned to the tetrahedral site 24d Li(1) sites and roughly one-quarter to a highly distorted site 96 h Li(2) sites in the garnet structure, which is similar to that of Ga3+ with 24d Li(1) sites preferential occupation to explain its high total conductivity[Citation21]. However, the Fe3+ in LLZO can be reduced to Fe2+ when in contact with metallic Li, which make it no suitable for solid electrolyte application[Citation22].
Figure 2. Development of LLZO based solid electrolyte. (a) Total conductivity of LLZO with different substitutions. (b) TEM image (top) and selected-area electron diffraction pattern (bottom) of LLZO around a triple-point grain boundary[Citation13]. LiAlSiO4 is acuminated at the grain boundary. Reproduced with permission[Citation13]. Copyright 2011, Elsevier. (c) Solid state 71Ga NMR spectra of Li6.55+yGa0.15La3Zr2−yScyO12 to show Ga3+ has preference to 24d Li(1) sites[Citation15]. Reproduced with permission[Citation15]. Copyright 2017, American Chemical Society. (d) Mössbauer spectra show Fe-ions of Li7−3xFexLa3Zr2O12 at 295 K have a preference to 24d Li(1) sites[Citation112]. Reproduced with permission[Citation112]. Copyright 2013, American Chemical Society.
![Figure 2. Development of LLZO based solid electrolyte. (a) Total conductivity of LLZO with different substitutions. (b) TEM image (top) and selected-area electron diffraction pattern (bottom) of LLZO around a triple-point grain boundary[Citation13]. LiAlSiO4 is acuminated at the grain boundary. Reproduced with permission[Citation13]. Copyright 2011, Elsevier. (c) Solid state 71Ga NMR spectra of Li6.55+yGa0.15La3Zr2−yScyO12 to show Ga3+ has preference to 24d Li(1) sites[Citation15]. Reproduced with permission[Citation15]. Copyright 2017, American Chemical Society. (d) Mössbauer spectra show Fe-ions of Li7−3xFexLa3Zr2O12 at 295 K have a preference to 24d Li(1) sites[Citation112]. Reproduced with permission[Citation112]. Copyright 2013, American Chemical Society.](/cms/asset/21656eb7-4d2f-43c7-a225-409bb12559be/ymte_a_1746539_f0002_oc.jpg)
The researches on Zr-site substitutions are majorly done by using Ta5+ and Nb5+ with concentrations between 0.2 and 0.75 mol%. The resulting total conductivities are usually higher than that for Al-substituted ones because Zr-substitutions do not obstruct the Li+ diffusion path within LLZO structure. The highest conductive Ta-substituted LLZO was reported by Baek et al. 2013 by using spark plasma sintering (i.e. hot-pressing) process to sinter Li6.87La2.97Zr1.60Ta0.56O12-δ[Citation23]. The sample shows a total conductivity as high as 1.35 × 10–3 S·cm−1 at 25°C. Similar results also reported by He et al. on a hot-pressed Li6.375La3Zr1.375Nb0.625O12 which has the highest total conductivity of Nb-substituted LLZO for 1.37 × 10–3 S·cm−1 at 25°C[Citation24]. Other than Ta5+ and Nb5+, elements such as Te6+, W6+, Sb5+ and Mo6+ were also used for Zr-site substitution, . However, the actual valence of these substituted-elements in the LLZO structure was never identified, which means the site occupations are based on the design of starting reagents and the use of Al2O3 crucible could play a big role on the final measured total conductivities. Nevertheless, the Te-substituted LLZO, i.e. Li6.5La3Zr1.75Te0.25O12[Citation25], was reported to have a very high total conductivity of 1.02 × 10–3 S·cm−1 at 30 °C and that for W-substituted LLZO, i.e. Li6.4La3Zr1.7W0.3O12, was 9.11 × 10–4 S·cm−1 at RT[Citation113].
In summary, the understanding of crystal structure and Li-ion diffusion mechanism of LLZO allows the elaborative design of the material to increase its Li-ion conductivity to higher than 1 × 10–3 S·cm−1 at RT by using Ta5+, Nb5+, Ga3+, Fe3+ or Te6+ substitutions. It is suggested that the conductivity is affected far more by Li-ion concentration than by different dopant elements or lattice parameters for which the appropriate Li-ion concentration in LLZO should be in the range of 6.4 ≤ x ≤ 6.6. Nevertheless, how a substitution affects the local environment for allowing easier Li-ion diffusion and higher chemical stability toward metallic Li should also be considered for a higher Li-ion conductive LLZO.
LLZO chemical stability toward metallic Li
LLZOs are generally regarded as stable solid electrolytes when in contact with metallic Li. From a theoretical investigation, Zhu et al. use density functional theory calculations to show that LLZO has a very low reduction potential of 0.05 V vs. Li/Li+ and a very small decomposition reaction energy of only 0.021 eV/atom (49 kJ/mol of LLZO) at 0 V vs. Li/Li+, ) [Citation54]. However, they further stated that their study cannot conclude if LLZO can be reduced by metallic Li or not because the small values of energy and voltage are below the typical accuracy of DFT and the approximations of the scheme. Experimentally, it is found that the chemical stability of LLZO toward metallic Li is affected by its substituted elements. Nemori et al. observed that the interfaces between Nb-substituted LLZOs, i.e. Li6.25La3Nb1.375Sc0.625O12 and Li6.25La3Nb0.75Zr1.25O12, and Li metal were turned into black color after 60 days of in contact to each other while that for Li6.25La3Ta1.375Sc0.625O12 and Li6.25La3Ta0.75Zr1.25O12 were unchanged, ) [Citation55]. The changing of the color for Nb-substituted LLZOs are attributed to the reduction of Nb5+ to lower valence states by metallic Li. Similar to Nb-substituted LLZOs, a black surface coloration at the interface between Fe-substituted LLZO and Li metal was also observed by Rettenwander et al., ) [Citation21]. Raman spectra and nanosecond laser-induced breakdown spectroscopy were further used to reveal the formation of a Li-deficient tetragonal LLZO interlayer at the interface between Fe-substituted LLZO and metallic Li due to the reduction of Fe3+ to Fe2+.
Figure 3. LLZO chemical stability toward metallic Li. (a) First principle calculated electrochemical window (solid color bar) of the solid electrolyte and other materials. The oxidation potential to fully delithiate the material is marked by the dashed line[Citation54]. Reproduced with permission[Citation54]. Copyright 2015, American Chemical Society. (b) A photograph to show that the interface of Nb-substituted LLZO were reduced by Li metal (black color) after in contact for 60 days while Ta-substituted LLZO stayed the same color[Citation55]. Reproduced with permission[Citation55]. Copyright 2015, Elsevier. (c) Raman mapping of the Li6.4Fe0.2La3Zr2O12; the picture (left) shows a cross section after the solid electrolyte has been in contact with metallic Li, spectra for different areas of the cross section (top right) and magnification of the shaded area in spectra. [Citation112] Reproduced with permission[Citation112]. Copyright 2018, American Chemical Society.
![Figure 3. LLZO chemical stability toward metallic Li. (a) First principle calculated electrochemical window (solid color bar) of the solid electrolyte and other materials. The oxidation potential to fully delithiate the material is marked by the dashed line[Citation54]. Reproduced with permission[Citation54]. Copyright 2015, American Chemical Society. (b) A photograph to show that the interface of Nb-substituted LLZO were reduced by Li metal (black color) after in contact for 60 days while Ta-substituted LLZO stayed the same color[Citation55]. Reproduced with permission[Citation55]. Copyright 2015, Elsevier. (c) Raman mapping of the Li6.4Fe0.2La3Zr2O12; the picture (left) shows a cross section after the solid electrolyte has been in contact with metallic Li, spectra for different areas of the cross section (top right) and magnification of the shaded area in spectra. [Citation112] Reproduced with permission[Citation112]. Copyright 2018, American Chemical Society.](/cms/asset/d6547088-b709-4deb-8dd1-ddf1168b6645/ymte_a_1746539_f0003_oc.jpg)
Different from Nb- and Fe-substituted LLZO for which the reduced interfaces can propagate through the material due to the formation of mixed conductors, a cubic phase Al-substituted LLZO, Li6.25Al0.25La3Zr2O12, was found that it can be reduced by metallic Li and is accompanied by the simultaneous implantation of Li-ions into its structure, ) [Citation56]. The findings from aberration-corrected scanning transmission electron microscope show that the implantation of Li-ions into the cubic phase LLZO results in a tetragonal phase LLZO interphase that stabilizes at an extremely small thickness of around five-unit LLZO cells. This interphase also effectively prevented further interfacial reactions for cubic phase LLZO. Further experiments were carried out by Zhu et al. using X-ray photoelectron spectroscopy and impedance spectroscopy for understanding the origins of electrochemical stability of LLZO by systematically studying both surface chemistry and substitution-dependent LLZO/Li interfacial reactivity[Citation57]. The XPS results show that Zr4+ at the surface in all Al-, Ta- and Nb-substituted LLZOs were able to be reduced by metallic Li with the extent of reduction increasing as Ta < Nb < Al and the formation of an ‘oxygen-deficient interphase’ layer that protects LLZO from further reduction, ). Nevertheless, the Nb-ions in Nb-substituted LLZO have a thermodynamic preference to segregate to the LLZO surface and an even stronger preference to the Li/LLZO interface, whereas Ta dopants are nearly isoenergetic in the bulk and at the interface. This preference for surface segregation destabilize the formation of the ‘oxygen-deficient interphase’ and allows the reduction reaction to propagate into the bulk of Nb-substituted LLZO, as the reason for observing the black coloration interface by Nemori et al.
Figure 4. LLZO chemical stability toward metallic Li. (a) HAADF-STEM image of c-LLZO in situ contacted with Li (left). The O K-edges obtained in the EELS line scan (middle). Schematic illustration of the interfacial behavior suggested by the EELS line scan (right)[Citation56]. Reproduced with permission[Citation56]. Copyright 2016, American Chemical Society. (b) Nb 3d and Zr 3d core level XPS spectra from Nb-, Al-, and Ta-doped LLZO with unpolished (top), polished (middle) and UHV heated (bottom) surfaces before (red) and after (blue) Li deposition[Citation57]. Reproduced with permission[Citation57]. Copyright 2019, Wiley-VCH.
![Figure 4. LLZO chemical stability toward metallic Li. (a) HAADF-STEM image of c-LLZO in situ contacted with Li (left). The O K-edges obtained in the EELS line scan (middle). Schematic illustration of the interfacial behavior suggested by the EELS line scan (right)[Citation56]. Reproduced with permission[Citation56]. Copyright 2016, American Chemical Society. (b) Nb 3d and Zr 3d core level XPS spectra from Nb-, Al-, and Ta-doped LLZO with unpolished (top), polished (middle) and UHV heated (bottom) surfaces before (red) and after (blue) Li deposition[Citation57]. Reproduced with permission[Citation57]. Copyright 2019, Wiley-VCH.](/cms/asset/7691e228-3680-4a75-a5bf-2bd67d48b9e0/ymte_a_1746539_f0004_oc.jpg)
It can be concluded that the chemical stability of LLZO toward metallic Li is highly depending on the substitutions. It is more likely that the substitution of transition metals into LLZO could led to the chemical instability of LLZO toward metallic Li. Even though Nb-substituted LLZO was long believed to be stable toward metallic Li, detail experiments show that the Nb-substituted LLZO is not stable when metallic Li is applied to its surface while Al- and Ta-substituted LLZO remains stable with the contact of metallic Li.
Negative electrode developments
Li-ion conductive ceramics were once believed that they can suppress Li dendrite formation due to their intrinsic high toughness, especially the shear modulus of LLZO is as high as ~ 55 GPa and its Li-ion transfer number is ~1 [Citation8 Citation58]. With the replacement of graphite by Li metal, it is expected that CLBs potentially offer a 70% increase of volumetric energy density and a 40% increase of gravimetric energy density of the battery [Citation1,Citation2]. However, abrupt drops of polarization voltages were reported from several groups when cycling Li/LLZO/Li symmetric cells by direct current polarizations [Citation59–Citation63]. Later, directly observations of Li propagation through LLZO along the grain boundaries were confirmed by using different characterization techniques such as high-resolution transmission electron microscopy combine with electron energy-loss spectroscopy and scanning electron microscopy, ) [Citation60 Citation64 Citation65].
Figure 5. The development of a negative electrode for CLBs. (a) SEM Li dendrite structure in cycled LLZO (I) illustration of a fractured surface due to Li dendrite, (II) SEM image of a fracture surface, (III) enlarged SEM micrograph of the boxed area B in (II), (IV) higher magnification SEM image of the web structure in (III), and (V) SEM images of the web structure after exposure to air[Citation64]. Reproduced with permission[Citation64]. Copyright 2017, Elsevier. (b) Optical microscopy images of a polished single crystal of LLZTO. The white silhouette is the propagate crack that created by Li dendrite[Citation66]. Reproduced with permission[Citation66]. Copyright 2017, Wiley-VCH. (c) illustration of Li dendrite formation due to inhomogeneous contact between LLZO and Li electrode that can be solved by a Au interlayer coating[Citation60]. Reproduced with permission[Citation60]. Copyright 2016, American Chemical Society. (d) XPS scan of C 1 s, O 1 s, Zr 3d, and Li 1 s spectra collected in 200 mTorr of Ar at RT: 25°C (bottom) and 250°C (top). The C(CO3) peak at 290 eV completely disappeared indicates Li2CO3 can be remove from LLZO surface by heating up to 250°C[Citation69]. Reproduced with permission[Citation69]. Copyright 2018, American Chemical Society. (e) Contact angle between LLZO and molten Li with Li2CO3 (top) and without Li2CO3 by fine polishing and heat treatment at 500°C (bottom)[Citation16]. Reproduced with permission[Citation16]. Copyright 2017, American Chemical Society.
![Figure 5. The development of a negative electrode for CLBs. (a) SEM Li dendrite structure in cycled LLZO (I) illustration of a fractured surface due to Li dendrite, (II) SEM image of a fracture surface, (III) enlarged SEM micrograph of the boxed area B in (II), (IV) higher magnification SEM image of the web structure in (III), and (V) SEM images of the web structure after exposure to air[Citation64]. Reproduced with permission[Citation64]. Copyright 2017, Elsevier. (b) Optical microscopy images of a polished single crystal of LLZTO. The white silhouette is the propagate crack that created by Li dendrite[Citation66]. Reproduced with permission[Citation66]. Copyright 2017, Wiley-VCH. (c) illustration of Li dendrite formation due to inhomogeneous contact between LLZO and Li electrode that can be solved by a Au interlayer coating[Citation60]. Reproduced with permission[Citation60]. Copyright 2016, American Chemical Society. (d) XPS scan of C 1 s, O 1 s, Zr 3d, and Li 1 s spectra collected in 200 mTorr of Ar at RT: 25°C (bottom) and 250°C (top). The C(CO3) peak at 290 eV completely disappeared indicates Li2CO3 can be remove from LLZO surface by heating up to 250°C[Citation69]. Reproduced with permission[Citation69]. Copyright 2018, American Chemical Society. (e) Contact angle between LLZO and molten Li with Li2CO3 (top) and without Li2CO3 by fine polishing and heat treatment at 500°C (bottom)[Citation16]. Reproduced with permission[Citation16]. Copyright 2017, American Chemical Society.](/cms/asset/3d317f1b-38cf-41fd-9658-ec63a0d9593d/ymte_a_1746539_f0005_oc.jpg)
The formation of Li dendrite in LLZO is recognized as a result of inhomogeneous contact between LLZO and Li electrode rather than as a consequence of low relative density of the used solid electrolytes [Citation16 Citation60]. When inhomogeneous contact is formed, the high ‘effective current density’ at the point contacts could electrochemically deposit metallic Li at defects to open up the rigid LLZO and propagate through the sample as shown by Porz et al. in both polycrystalline and single crystal LLZOs, ) [Citation66]. Research efforts are, therefore, focusing on reducing the inhomogeneous contacts, which usually accompany with high interface resistance, between LLZO and Li electrode by using (I) interlayer coatings or (II) diminishing surface impurities. It is worth to mention that the surfaces of LLZOs for the interlayer coating experiments always need to be freshly polished in either air or inert atmosphere before depositing the interlayer. The Li electrode is usually applied at a temperature higher than the Li melting point. On the other hand, the experiments using diminishing surface impurities for reducing interface resistance usually need to apply a stack pressure to the symmetric cells at a temperature right below Li melting point for some hours to ensure the contact between LLZO and Li electrode, .
Table 2. List of interface modifications and symmetric cell test conditions for LLZOs.
The interlayer coating was first proposed by Tsai et al. who use a thin Au interlayer to improve the contact between LLZO and Li electrode, ) [Citation60]. Because the coating technologies, such as sputter, atomic layer deposition, and wet chemical coatings, can effectively cover the whole surface of LLZO, the working principle of using interlayer coating is to take the advantage from the applied material which is able to in situ forming an alloy with metallic Li to cover the surface of LLZO homogeneously. The interface resistance between LLZO and Li electrode was dramatically reduced from ~1500 Ω·cm2 to 64 Ω·cm2 by the thin layer Au coating, which results in short-circuit-free cells when running a direct current density of 0.5 mA·cm−2 through the LLZO pellets. Since then, various materials, such as Al, Al2O3, ZnO, Mg, Si, Sn, AgNO3 and graphite, have been applied as the interlayer coatings for reducing the interface resistance between LLZO and Li, . Among all, the using of Li–Al alloy was reported that it can effectively reduce the interface resistance to as low as < 1 Ω·cm2 [Citation67].
Most of the publications that using interlayer coatings to reduce interface resistance often shows the wettability of between LLZO and metallic Li is low without their coatings. However, the low wettability between LLZO and metallic Li was found due to the formation of Li2CO3 at the surface of LLZO from Li+/proton exchange when the sample was exposed to the ambient environment [Citation16 Citation63 Citation68]. The formation of Li2CO3 also block the Li-ion diffusion paths to give high interface resistance since Li2CO3 is not a good Li-ion conductor. Nevertheless, the formation of Li2CO3 can be erased by fine polish or acid etching of the surface of LLZO or restore the Li-ions from Li2CO3 back to LLZO by heating the sample under an inert atmosphere at a temperature higher than 250°C, [Citation69 Citation70]. Sharafi et al. further show that LLZO and Li can wet each other very well to give an interface resistance as low as 2 Ω·cm2 by fine polishing the surface of LLZO in Ar atmosphere which followed by a heat treatment of the LLZO at 500°C in an inert atmosphere to remove Li2CO3, ) [Citation16]. Nevertheless, a stack pressure of 350 kPa at 175°C is needed to apply to their symmetric cell for 12 h to ensure a good contact between LLZO and Li electrode. More recently, Zheng et al. reported that the removing of impurity on the surface of used metallic Li, such as Li2O, is as important as that on the surface of LLZO[Citation71]. By ensuring an impurity-free at the interface between LLZO and Li, Zheng et al. show that the interface resistance can be diminished to 6.95 Ω·cm2 which allows a Li/LLZO/Li symmetric cell to cycle with a high current density of 13.3 mA·cm2 for ~100 s per cycle step, i.e. 0.4 mA h cm−2, or 2.2 mA·cm2 for 24 min per cycle step, i.e. 0.88 mA h cm−2, ).
Figure 6. The development of negative electrode for CLBs. (a) Galvanostatic cycling of Li/LLZO/Li at 2.2 mA·cm−2 for 0.88 mA h·cm−2 for 100 cycles[Citation71]. Reproduced with permission[Citation71]. Copyright 2019, Wiley-VCH. (b) Morphology of the lithium metal electrode before assembling the symmetric cell (I) and after stripping at 100 μA·cm−2 anodic load (III). The potential profile and impedance contributions shows a complete contact loss of Li electrode after around 12 h of stripping (II). (c) Schematic of the different mechanisms that facilitate charge transfer at the lithium metal electrode under anodic load (limiting cases)[Citation92]. (I) local current density does not exceed the vacancy diffusion limit. (II, III) local current density exceeds the diffusion limit (IV) external pressure is applied[Citation92]. Reproduced with permission[Citation92]. Copyright 2019, American Chemical Society.
![Figure 6. The development of negative electrode for CLBs. (a) Galvanostatic cycling of Li/LLZO/Li at 2.2 mA·cm−2 for 0.88 mA h·cm−2 for 100 cycles[Citation71]. Reproduced with permission[Citation71]. Copyright 2019, Wiley-VCH. (b) Morphology of the lithium metal electrode before assembling the symmetric cell (I) and after stripping at 100 μA·cm−2 anodic load (III). The potential profile and impedance contributions shows a complete contact loss of Li electrode after around 12 h of stripping (II). (c) Schematic of the different mechanisms that facilitate charge transfer at the lithium metal electrode under anodic load (limiting cases)[Citation92]. (I) local current density does not exceed the vacancy diffusion limit. (II, III) local current density exceeds the diffusion limit (IV) external pressure is applied[Citation92]. Reproduced with permission[Citation92]. Copyright 2019, American Chemical Society.](/cms/asset/cb7d3c36-9bc9-41b9-92df-08e5d7bf6628/ymte_a_1746539_f0006_oc.jpg)
While all the papers claim that their method could effectively suppress Li dendrite formation, the demonstrated cycle performance by using Li/LLZO/Li symmetric cells are only able to deliver capacities much lower than a practical one, i.e. the used Li thicknesses are much thinner than 14.3 μm or ≪ 3 mAh·cm−2 in energy density, unless the operational temperature was increased to 60°C[Citation91], . At here, it is important to notice that some reports of galvanostatic cycling of Li symmetric cells with high current densities and capacities are in fact the result of ‘soft shorts’ (stable electronic connections between the Li electrodes) as suggested by Albertus et al. [Citation1]. The reliability of the reported results can be easily examined by using Ohm’s law to calculate the cell resistance, which should not be lower than the resistance from the used solid electrolyte itself. Therefore, it can be expected that there are more mechanisms hindering the use of metallic Li as the negative electrode for CLB. By measuring pressure-dependent electrode kinetics, Krauskopf et al. show that the vacancy diffusion limitation in the Li metal restricts the rate capability of the Li electrode because of contact loss caused by vacancy accumulation and the resulting pore formation near the interface, [Citation92]. They further concluded that the interface between LLZO and Li would only remain morphologically stable when an applied current density is lower than 100 μA·cm−2 from a theoretical calculation based on their experimental results. This low current density means a planar geometry Li electrode is not high enough for practical cell application. How to resolve the diffusion limitation, e.g. increase Li diffusion coefficient by dopants, would be the next challenge for the Li electrode development for CLB.
Positive electrode developments
The compatibilities between LLZO and different positive active electrode materials near LLZO sintering temperature, i.e. ~ 1000 °C, are serving as the key factors for CLB fabrications due to the necessary of high temperature sintering process to form low resistive ionic diffusion paths. Positive active electrode materials including LiMn2O4, LiFePO4, LiCoMnO4, LiFe0.5Mn1.5O4, LiNi0.5Mn1.5O4, LiNi1/3Co1/3Mn1/3O2 and LiCoO2 (LCO) had been examined for their compatibilities with LLZO at elevated temperatures [Citation93–Citation98]. X-ray diffraction (XRD) results show that LiMn2O4, LiFePO4, LiCoMnO4, LiFe0.5Mn1.5O4 and LiNi0.5Mn1.5O4 reacted with LLZO at temperatures between 400 and 600°C while LiNi1/3Co1/3Mn1/3O2 is stable up to 800°C. First principle calculations suggest that the decomposition of the positive active electrode materials act as oxidisers for the decomposition of LLZO[Citation94]. Therefore, the low reaction temperatures make these materials difficult to be used in the traditionally high temperature sintering process for CLB fabrication.
The experimental results for the compatibility between LLZO and LCO are rather diverse. A closer examination of the reported publications can found that amorphous Li-Co-O precursors, which deposited by technologies such as plused laser depositions, physical vapor depositions and sol-gel methods, has a much lower reaction temperature with LLZO, ~700 °C, than those who use crystalline LCO, ~1085°C [Citation96–Citation98]. Kim et al. suggest that La2CoO4 is the reaction byproduct at the interface of their pulsed laser deposited (PLD) Li-Co-O and LLZO, ) [Citation97]. It is worth to note that the Li-Co-O film was deposit directly on LLZO at 700°C by PLD. Therefore, it is reasonable to deduce that the formation of Li2CoO4 is highly correlative to the vacuum environment because Co2+ is not a stable state for cobalt when it is in a high temperature and oxygen rich environment.
Figure 7. The development of positive electrode for CLBs. (a) Cross-sectional TEM image of an LLZ/PLD deposited LCO thin film interface (top) and the EDS line profile (bottom)[Citation97]. Reproduced with permission[Citation97]. Copyright 2011, Elsevier. (b) TEM images of crystalline LCO/LLZO that was directly obtained from LCOon a LLZO pellet and the corresponding EDS elemental mappings to show Al3+ diffused into LCO after heat treated at 700°C[Citation96]. Reproduced with permission[Citation96]. Copyright 2013, American Chemical Society. (c) High-resolution micro-Raman mapping of a CLB cross-section which was sintered at 1050°C in air. (I) Optical image of the SSLB cross-section and its mapping area. The Raman mappings and the spectra for (II) LCO, (III) LLZ:Ta and (IV) epoxy[Citation99]. Reproduced with permission[Citation99]. Copyright 2019, Royal Society of Chemistry.
![Figure 7. The development of positive electrode for CLBs. (a) Cross-sectional TEM image of an LLZ/PLD deposited LCO thin film interface (top) and the EDS line profile (bottom)[Citation97]. Reproduced with permission[Citation97]. Copyright 2011, Elsevier. (b) TEM images of crystalline LCO/LLZO that was directly obtained from LCOon a LLZO pellet and the corresponding EDS elemental mappings to show Al3+ diffused into LCO after heat treated at 700°C[Citation96]. Reproduced with permission[Citation96]. Copyright 2013, American Chemical Society. (c) High-resolution micro-Raman mapping of a CLB cross-section which was sintered at 1050°C in air. (I) Optical image of the SSLB cross-section and its mapping area. The Raman mappings and the spectra for (II) LCO, (III) LLZ:Ta and (IV) epoxy[Citation99]. Reproduced with permission[Citation99]. Copyright 2019, Royal Society of Chemistry.](/cms/asset/edc9b89f-5d59-4ba9-a1f0-daf888bfdee3/ymte_a_1746539_f0007_oc.jpg)
When crystalline LCO is considered, Wakasugi et al. reported that the XRD patterns and charge-discharge behavior of a LCO and Li6.25Al0.25La3Zr2O12 mixture did not change after the heat treatment at 800°C by using ethylene carbonate/ethyl methyl carbonate/LiPF6 liquid electrolyte[Citation93]. Nevertheless, a detail study by using TEM and SIMS show that Al3+ in Al-substituted LLZO has a preference to diffuse into LCO when the LLZO/LCO mixture was calcined at 700°C, ) [Citation96]. The departure of Al3+ from Al-substituted LLZO surface transformed cubic phase LLZO into the tetragonal phase one, which leading to a high interfacial resistance due to the low ionic conductivity of tetragonal phase LLZO. On the other hand, Uhlenbruck et al. reported that a rapid reaction between Li6.75La3Zr1.6Ta0.4O12 (LLZTaO) and crystalline LCO only takes place at a temperature of 1085°C by using XRD and differential scanning calorimetry measurement[Citation98]. Later, Tsai et al. confirmed LLZTaO and crystalline LCO are chemically stable to each other up to 1050°C by using micro-Raman mapping of their sintered LCO/LLZTaO composite electrode, ) [Citation99]. Although a reaction byproduct, LaCoO3, was reported to give an extra Raman band at 691 cm−1 when crystalline LCO and Li6.75La3Zr1.75Ta0.25O12 was heat up to 900°C[Citation95], Tsai et al. further verified that the extra peak at 693 cm−1 is due to a small concentration of Co3+ diffused into LLZTaO to give a photoluminescence peak at 693 cm−1 by using Co-substituted LLZO.
To summarize the compatibility between LCO and LLZO, it is reasonable to give a conclusion that amorphous Li-Co-O has a higher Gibbs free energy than that for crystalline LCO, which makes amorphous Li-Co-O more reactive to LLZO than crystalline LCO at lower temperatures. When a mixture of crystalline LCO and LLZO is examined, the elemental substitution of LLZO could affect its chemical stability towards crystalline LCO, where Ta-substituted LLZO has better chemical stability than Al-substituted LLZO.
CLB fabrications can be classified into two different approaches when using garnet structured LLZO solid electrolyte. One of the class is using thin film technologies such as pulsed laser deposition [Citation100 Citation101], sputter deposition [Citation114] and sol-gel deposition [Citation102 Citation103] to deposit active electrode materials on dense LLZO pellets to form CLBs. The results demonstrate electrochemical reactions from the deposited LCO but the areal capacities were very low, due to their low loadings and utilizations of LCO from lacking of Li-ion diffusion paths. These results are good to demonstrate the possibility of using LLZO to fabricate functional CLB but not for the practical due to the use of very thick LLZO solid electrolytes that gives their energy densities too low to be used at anywhere, .
Table 3. List of composition of the positive electrode for all-ceramic Li batteries and their test conductions.
The other type of batteries can be classified as ‘bulk-type’ CLBs due to the use of casting method for composite positive electrode (CPE) fabrication or high yield deposition methods that are potentially able to achieve high energy densities. The most common approach of CPE fabrication is consisted of crystalline LCO and Li3BO3 (LBO) or its derivatives. In these CPEs, LBO is serving as a sintering additive which melts at 700°C to cement LCO and LLZO together and provides Li-ion transport pathways across grain boundaries due to its very low Li-ion conductivity, ~ 2 × 10–6 S cm−1, at RT, ) [Citation96,Citation104–Citation110]. The low melting point of LBO at 700°C could effectively avoid the formation of a highly resistive interface from the reaction between LLZO and LCO during high temperature sintering of CLB. These batteries offer very stable electrochemical performance up to 100 cycles but usually, less than 10 cycles were shown in the publications, ) and . Another approach for making CPE was proposed by Tsai et al. by using crystalline LCO and LLZTaO, instead of using more reactive Li-Co-O precursors or Al-substituted LLZO, because both materials are chemically stable up to 1050°C and do not form highly resistive tetragonal phase LLZO at the interface[Citation99]. Their micro-Raman, energy-dispersive X-ray spectroscpoy mapping and cyclic voltammetry scan of fabricated CLB show that the well sintered interfaces are free from detrimental secondary phases that allows the CLB to increase its specific areal capacity for 10 times higher than other reports at 1.63 mAh cm−2 (i.e.110 mA h g−1) with a much higher charge/discharge current density of 50 μA cm−2, ). The CLB also able to discharge at very high current densities up to 500 μA cm−2 at 50°C due to the minimized cell areal resistance. However, the fabricated cell show a fast capacity degradation due to its microstructure failure from LCO breathing during charge/discharge cycling.
Figure 8. The development of positive electrode for CLBs. (a) Cross-sectional SEM images of secondary electron (top) and backscattering electron (bottom) images of the interface between the positive electrode layer (LCO positive active electrode material and Li3BO3 solid electrolyte) and the Li6.75La3Zr1.75Nb0.25O12 solid electrolyte[Citation106]. Reproduced with permission[Citation106]. Copyright 2013, Elsevier. (b) Thermally soldering LCO and LLZO through the reaction between the Li2.3C0.7B0.3O3 and the Li2CO3 that can be spontaneously coated Li2.3-xC0.7+xB0.3-xO3 interphase on both LLZO and LCO. The CLB with such a CPE exhibits high cycling stability and high rate performance[Citation104]. Reproduced with permission[Citation104]. Copyright 2018, Cell.(c) CLB using LCO/LLZTaO as CPE allows high discharge current densities and capacities[Citation99]. Reproduced with permission[Citation99]. Copyright 2019, Royal Society of Chemistry. (d) Cross-sectional SEM images and EDX mapping of a LiNi1/3Co1/3Mn1/3O2 (NMC)-LATP composite film on Si/SiO2 wafer by aerosol deposition (left). TEM image of a NMC/LATP interface in the NMC-LATP composite film and its EDX line profiles to show no interface reaction between NMC and LATP during aerosol deposition[Citation115]. Reproduced with permission[Citation115]. Copyright 2016, Elsevier.
![Figure 8. The development of positive electrode for CLBs. (a) Cross-sectional SEM images of secondary electron (top) and backscattering electron (bottom) images of the interface between the positive electrode layer (LCO positive active electrode material and Li3BO3 solid electrolyte) and the Li6.75La3Zr1.75Nb0.25O12 solid electrolyte[Citation106]. Reproduced with permission[Citation106]. Copyright 2013, Elsevier. (b) Thermally soldering LCO and LLZO through the reaction between the Li2.3C0.7B0.3O3 and the Li2CO3 that can be spontaneously coated Li2.3-xC0.7+xB0.3-xO3 interphase on both LLZO and LCO. The CLB with such a CPE exhibits high cycling stability and high rate performance[Citation104]. Reproduced with permission[Citation104]. Copyright 2018, Cell.(c) CLB using LCO/LLZTaO as CPE allows high discharge current densities and capacities[Citation99]. Reproduced with permission[Citation99]. Copyright 2019, Royal Society of Chemistry. (d) Cross-sectional SEM images and EDX mapping of a LiNi1/3Co1/3Mn1/3O2 (NMC)-LATP composite film on Si/SiO2 wafer by aerosol deposition (left). TEM image of a NMC/LATP interface in the NMC-LATP composite film and its EDX line profiles to show no interface reaction between NMC and LATP during aerosol deposition[Citation115]. Reproduced with permission[Citation115]. Copyright 2016, Elsevier.](/cms/asset/ccd64b40-2493-4266-82ca-fc9c221e57de/ymte_a_1746539_f0008_oc.jpg)
The other approach for preparing bulk-type CLBs is using aerosol deposition [Citation111 Citation115]. Kato et al. fabricated their bulk-type CLB by using aerosol deposition that contains LiNi1/3Co1/3Mn1/3O2 + Li-Al-Ti-P-O glass-ceramic as CPE to deposit on a LLZO pellet, ) [Citation115]. The cell was able to deliver a high specific areal capacity of 0.5 mAh cm−2 and a high operational current density of 50 μA cm−2 at 100°C. The same technology was used by Inada et al. to deposit TiNb2O7 thin film on LLZO. However, only one charge/discharge cycle was shown with relatively low current density, 2 μA·cm−2, at 60°C in the report[Citation111]. It is worth to mention that aerosol deposition has a major advantage of no need of high-temperature sintering process when CLB is fabricated, which avoids the interface reaction between the used active electrode material and solid electrolyte. Therefore, a low interface resistance of constructed CLB can be expected by using this technology.
It is important to notice that the CLBs with very low specific areal loadings, usually < 2 mg cm−2, and very low operational current densities, < 10 μA cm−2, are good to demonstrate the proof of concepts but not able to show their potential for practical use in the future, . For example, the CLBs using LCO, LLZO and LBO as CPE were usually made with active electrode material loadings ~ 1 mg·cm−2 and operational current densities ~ 5 μA·cm−2, . When the specific areal loading is increased, the electrochemical performance of this type of CLB is dramatically reduced by the low ionic conductivity of LBO and high tortuosity of Li-ion diffusion paths within the CPE as shown by Liu et al. [Citation110]. Although an argument of increasing specific areal capacity could simply be a technological issue instead of a scientific one, some physical problems such as establish of effective ionic diffusion paths, lower tortuosity for ionic diffusion, and reduce of microstructure fracture due to breathing behavior of active electrode materials may not able to be observed and solved easily for the cases with low active material loadings. Therefore, a demonstration of good CLB should contain reasonable active material loading to show that the electrochemical performance of the fabricated CLB can utilize most of the active materials from the CPE instead of only the materials on the interface, especially if the CLB is aiming for becoming a high energy density cell in the further.
Summary and perspectives
The discovery of fast Li-ion conductive garnet structured LLZO has been attracting much attention in electrochemical society due to their perspective of fabricating all-ceramic Li battery that gives much higher safety and energy density than conventional Li-ion batteries. After more than a decade of researching on LLZO, the understanding of the material properties has dramatically increased. On the development of LLZO, the accumulated knowledge has led to the increase of Li-ion conductivity for LLZO up to 1.8 × 10–3 S·cm−1 by substituting Fe or co-substituting Sc and Ga into LLZO. When using metallic Li as the negative electrode for CLB, detail researches found that the stability of LLZO toward metallic Li depends on the substituting elements, for which Ta shows the highest stability than Nb- and Al-substituted ones. Moreover, the high interface resistance between LLZO and Li electrode was found to be the consequence of impurity formations, such as Li2CO3, on the interface and inhomogeneous contact between LLZO and Li electrode. By carefully removing the impurities on the surface of LLZO and interlayer coatings, the interface resistance can be effectively reduced to a negligible number to relief the Li dendrite formation. Nevertheless, the Li dendrite problem is still lingered around when using metallic Li as the negative electrode. A depth investigation into the properties of metallic Li, such as atomic self-diffusion and mechanical properties, would be necessary for further solving the Li dendrite problem, especially the working principle of CLB is relying only on the solid-state diffusion mechanism. Although many publications have proposed different approaches for the positive electrode development, the active material loading and performance are still far away from a real application. Problems, such as internal elemental diffusion and high interface resistance, from conventional high temperature sintering process, is still not yet fully understood and need to be solved. On the full CLB level, many data are still needed so that CLB performance can be optimized. For example, the knowledge on how to maximize the active material loading to achieve highest energy density, how the Li-ion percolation paths affects CLB performance, how to optimize the microstructure of CLB to accommodate the volume change of active material during charge/discharge cycling and even finding a more suitable positive electrode material for CLB development are still need to be fulfilled.
Disclosure
No potential conflict of interest was reported by the authors.
Acknowledgments
This work is financially supported by the project of “US-German Cooperation on Energy Storage” under the funding programs of “CatSe- Interfaces and Interphases in Rechargeable Li Based Batteries: Cathode/Solid Electrolyte” (Project No.: 13XP00223A) and “LISI- Lithium Solid Electrolyte Interfaces” (Project No.: 03XP0224B) from the Bundesministerium für Bildung und Forschung (BMBF).
Additional information
Funding
References
- Albertus P, Babinec S, Litzelman S, et al. Status and challenges in enabling the lithium metal electrode for high-energy and low-cost rechargeable batteries. Nature Energy. 2017;3(1):16–21.
- Janek J, Zeier WG. A solid future for battery development. Nature Energy. 2016;1(9). DOI:https://doi.org/10.1038/nenergy.2016.141
- Murugan R, Thangadurai V, Weppner W. Fast Lithium ion conduction in garnet-type Li7La3Zr2O12. Angew Chem Int Ed Engl. 2007;46(41):7778–7781.
- Awaka J, Takashima A, Kataoka K, et al. Crystal structure of fast Lithium-ion-conducting cubic Li7La3Zr2O12. Chem Lett. 2011;40(1):60–62.
- Awaka J, Kijima N, Hayakawa H, et al. Synthesis and structure analysis of tetragonal Li7La3Zr2O12 with the garnet-related type structure. J Solid State Chem. 2009;182(8):2046–2052.
- Li Y, Han J-T, Wang C-A, et al. Ionic distribution and conductivity in lithium garnet Li7La3Zr2O12. J Power Sources. 2012;209:278–281.
- Geiger CA, Alekseev E, Lazic B, et al. Crystal chemistry and stability of “Li7La3Zr2O12” garnet: a fast lithium-ion conductor. Inorg Chem. 2011;50(3):1089–1097.
- Buschmann H, Dolle J, Berendts S, et al. Structure and dynamics of the fast lithium ion conductor “Li7La3Zr2O12”. Phys Chem Chem Phys. 2011;13(43):19378–19392.
- Bernstein N, Johannes MD, Hoang K. Origin of the structural phase transition in Li7La3Zr2O12. Phys Rev Lett. 2012;109(20):205702.
- Rangasamy E, Wolfenstine J, Sakamoto J. The role of Al and Li concentration on the formation of cubic garnet solid electrolyte of nominal composition Li7La3Zr2O12. Solid State Ion. 2012;206:28–32.
- Xu M, Park MS, Lee JM, et al. Mechanisms of Li+ transport in garnet-type cubic Li 3+ x La 3 M 2 O 12 (M= Te, Nb, Zr). Phys Rev B. 2012;85(5):052301.
- Li Y, Han J-T, Wang C-A, et al. Optimizing Li+ conductivity in a garnet framework. J Mater Chem. 2012;22(30):15357–15361.
- Kumazaki S, Iriyama Y, Kim K-H, et al. High lithium ion conductive Li7La3Zr2O12 by inclusion of both Al and Si. Electrochem commun. 2011;13(5):509–512.
- Kim KH, Hirayama T, Fisher CAJ, et al. Characterization of grain-boundary phases in Li7La3Zr2O12 solid electrolytes. Mater Charact. 2014;91:101–106.
- Buannic L, Orayech B, López Del Amo J-M, et al. Dual substitution strategy to enhance Li+ ionic conductivity in Li7La3Zr2O12 solid electrolyte. Chem Mater. 2017;29(4):1769–1778.
- Sharafi A, Kazyak E, Davis AL, et al. Surface chemistry mechanism of ultra-low interfacial resistance in the solid-state electrolyte Li7La3Zr2O12. Chem Mater. 2017;29(18):7961–7968.
- Garcia Daza FA, Bonilla MR, Llordes A, et al. Atomistic insight into ion transport and conductivity in Ga/Al-substituted Li7La3Zr2O12 solid electrolytes. ACS Appl Mater Interfaces. 2019;11(1):753–765.
- Rettenwander D, Redhammer G, Preishuber-Pflugl F, et al. Structural and Electrochemical Consequences of Al and Ga Cosubstitution in Li7La3Zr2O12 Solid Electrolytes. Chem Mater. 2016;28(7):2384–2392.
- Bernuy-Lopez C, Manalastas W, Lopez Del Amo JM, et al. Atmosphere controlled processing of Ga-substituted garnets for high Li-Ion conductivity ceramics. Chem Mater. 2014;26(12):3610–3617.
- Wu JF, Chen EY, Yu Y, et al. Gallium-doped Li7La3Zr2O12 garnet-type electrolytes with high lithium-ion conductivity. ACS Appl Mater Interfaces. 2017;9(2):1542–1552.
- Song S, Chen B, Ruan Y, et al. Gd-doped Li7La3Zr2O12 garnet-type solid electrolytes for all-solid-state Li-Ion batteries. Electrochim Acta. 2018;270:501–508.
- Baek S-W, Lee J-M, Kim TY, et al. Garnet related lithium ion conductor processed by spark plasma sintering for all solid state batteries. J Power Sources. 2014;249:197–206.
- He M, Cui Z, Chen C, et al. Formation of self-limited, stable and conductive interfaces between garnet electrolytes and lithium anodes for reversible lithium cycling in solid-state batteries? J Mater Chem A. 2018;6(24):11463–11470.
- Deviannapoorani C, Dhivya L, Ramakumar S, et al. Lithium ion transport properties of high conductive tellurium substituted Li7La3Zr2O12 cubic lithium garnets. J Power Sources. 2013;240:18–25.
- Luo Y, Li X, Chen H, et al. Influence of sintering aid on the microstructure and conductivity of the garnet-type W-doped Li 7 La 3 Zr 2 O 12 ceramic electrolyte. J Mater Sci. 2019;30(18):17195–17201.
- Tsai C-L, Dashjav E, Hammer E-M, et al. High conductivity of mixed phase Al-substituted Li7La3Zr2O12. J Electroceram. 2015;35(1–4):25–32.
- Dhivya L, Karthik K, Ramakumar S, et al. Facile synthesis of high lithium ion conductive cubic phase lithium garnets for electrochemical energy storage devices. RSC Adv. 2015;5(116):96042–96051.
- Allen JL, Wolfenstine J, Rangasamy E, et al. Effect of substitution (Ta, Al, Ga) on the conductivity of Li7La3Zr2O12. J Power Sources. 2012;206:315–319.
- Wang Y, Lai W. High ionic conductivity lithium garnet oxides of Li7− ×La3Zr2− ×Ta×O12 compositions. Electrochem Solid State Lett. 2012;15(5):A68.
- Cao Y, Li Y-Q, Guo -X-X. Chin Phys B. 2013;22(7).
- Gu W, Ezbiri M, Prasada Rao R, et al. Effects of penta- and trivalent dopants on structure and conductivity of Li7La3Zr2O12. Solid State Ion. 2015;274:100–105.
- Cao Y, Li Y.-Q, Guo X.-X. Densification and lithium ion conductivity of garnet-type Li7–×La3Zr2–×TaxO12(×− 0.25) solid electrolytes. Chin. Phys. B. 2013;22(7):078201.
- Huang M, Shoji M, Shen Y, et al. Preparation and electrochemical properties of Zr-site substituted Li7La3(Zr2−xMx)O12 (M = Ta, Nb) solid electrolytes. J Power Sources. 2014;261:206–211.
- Buschmann H, Berendts S, Mogwitz B, et al. Lithium metal electrode kinetics and ionic conductivity of the solid lithium ion conductors “Li7La3Zr2O12” and Li7−xLa3Zr2−xTaxO12 with garnet-type structure. J Power Sources. 2012;206:236–244.
- Xia W, Xu B, Duan H, et al. Reaction mechanisms of lithium garnet pellets in ambient air: the effect of humidity and CO2. J Am Ceram Soc. 2017;100(7):2832–2839.
- Naoki HAMAO, Kunimitsu KATAOKA, KIJIMA N, et al. J Ceram Soc Jpn. 2016;124(6):P6-1-P6-3.
- Huang X, Lu Y, Guo H, et al. Beyond shape engineering of TiO2 nanoparticles: post-synthesis treatment dependence of surface hydration, hydroxylation, Lewis acidity and photocatalytic activity of TiO2 anatase nanoparticles with dominant {001} or {101} facets. ACS Appl Energy Mater. 2018;1:5355–5365.
- Hamao N, Kataoka K, Kijima N, Akimoto J. Synthesis, crystal structure and conductive properties of garnet-type lithium ion conductor Al-free Li7–xLa3Zr2–×TaxO12 (0 ≤ × ≤ 0.6). J Ceram Soc Jpn. 2016;124(6):P6-1–P6-3.
- Wolfenstine J, Ratchford J, Rangasamy E, et al. Synthesis and high Li-ion conductivity of Ga-stabilized cubic Li7La3Zr2O12. Mater Chem Phys. 2012;134(2–3):571–575.
- Yi E, Wang W, Kieffer J, et al. Key parameters governing the densification of cubic-Li7La3Zr2O12 Li+ conductors. J Power Sources. 2017;352:156–164.
- Wu J-F, Pang WK, Peterson VK, et al. Garnet-type fast Li-Ion conductors with high ionic conductivities for all-solid-state batteries. ACS Appl Mater Interfaces. 2017;9(14):12461–12468.
- Howard MA, Clemens O, Kendrick E, et al. Effect of Ga incorporation on the structure and Li ion conductivity of La3Zr2Li7O12. Dalton Trans. 2012;41(39):12048–12053.
- El Shinawi H, Janek J. Stabilization of cubic lithium-stuffed garnets of the type “Li7La3Zr2O12” by addition of gallium. J Power Sources. 2013;225:13–19.
- Murugan R, Ramakumar S, Janani N. High conductive yttrium doped Li7La3Zr2O12 cubic lithium garnet. Electrochem commun. 2011;13(12):1373–1375.
- Hitz GT, Wachsman ED, Thangadurai V. Highly Li-Stuffed garnet-type Li7+xLa3Zr2-xYxO12. J Electrochem Soc. 2013;160(8):A1248–A1255.
- Dhivya L, Janani N, Palanivel B, et al. Li+ transport properties of W substituted Li7La3Zr2O12 cubic lithium garnets. AIP Adv. 2013;3(8):082115.
- Zhang Y, Hu D, Deng J, et al. Li+ transport channel size governing Li+ migration in garnet-based all-solid-state lithium batteries. J Alloys Compd. 2018;767:899–904.
- Rangasamy E, Wolfenstine J, Allen J, et al. The effect of 24c-site (A) cation substitution on the tetragonal–cubic phase transition in Li7−xLa3−xAxZr2O12 garnet-based ceramic electrolyte. J Power Sources. 2013;230:261–266.
- Huang M, Dumon A, Nan C-W. Effect of Si, In and Ge doping on high ionic conductivity of Li7La3Zr2O12. Electrochem commun. 2012;21:62–64.
- Liu X, Li Y, Yang T, et al. High lithium ionic conductivity in the garnet-type oxide Li7−2xLa3Zr2−xMoxO12(x=0-0.3) ceramics by sol-gel method. J Am Ceram Soc. 2017;100(4):1527–1533.
- Hanc E, Zając W, Molenda J. Synthesis procedure and effect of Nd, Ca and Nb doping on structure and electrical conductivity of Li7La3Zr2O12 garnets. Solid State Ion. 2014;262:617–621.
- Ramakumar S, Satyanarayana L, Manorama SV, et al. Structure and Li+ dynamics of Sb-doped Li7La3Zr2O12 fast lithium ion conductors. Phys Chem Chem Phys. 2013;15(27):11327–11338.
- Dumon A, Huang M, Shen Y, et al. High Li ion conductivity in strontium doped Li7La3Zr2O12 garnet. Solid State Ion. 2013;243:36–41.
- Zhu Y, He X, Mo Y. Origin of outstanding stability in the lithium solid electrolyte materials: insights from thermodynamic analyses based on first-principles calculations. ACS Appl Mater Interfaces. 2015;7(42):23685–23693.
- Nemori H, Matsuda Y, Mitsuoka S, et al. Stability of garnet-type solid electrolyte LixLa3A2-yByO12 (A=Nb or Ta, B=Sc or Zr). Solid State Ion. 2015;282:7–12.
- Ma C, Cheng Y, Yin K, et al. Interfacial stability of Li metal–solid electrolyte elucidated via in situ electron microscopy. Nano Lett. 2016;16(11):7030–7036.
- Zhu Y, Connell Y, Tepavcevic S, et al. High energy density polymer dielectrics interlayered by assembled boron nitride nanosheets. Adv Energy Mater. 2019;9(12):1903062.
- Ni JE, Case ED, Sakamoto JS, et al. Room temperature elastic moduli and Vickers hardness of hot-pressed LLZO cubic garnet. J Mater Sci. 2012;47(23):7978–7985.
- Ishiguro K, Nemori H, Sunahiro S, et al. Ta-doped Li7La3Zr2O12 for water-stable lithium electrode of lithium-air batteries. J Electrochem Soc. 2014;161(5):A668–A674.
- Tsai C-L, Roddatis V, Chandran CV, et al. Li7La3Zr2O12 interface modification for Li dendrite prevention. ACS Appl Mater Interfaces. 2016;8(16):10617–10626.
- Ishiguro K, Nakata Y, Matsui M, et al. Stability of Nb-doped cubic Li7La3Zr2O12 with lithium metal. J Electrochem Soc. 2013;160(10):A1690–A1693.
- Sudo R, Nakata Y, Ishiguro K, et al. Interface behavior between garnet-type lithium-conducting solid electrolyte and lithium metal. Solid State Ion. 2014;262:151–154.
- Cheng L, Crumlin EJ, Chen W, et al. The origin of high electrolyte–electrode interfacial resistances in lithium cells containing garnet type solid electrolytes. Phys Chem Chem Phys. 2014;16(34):18294–18300.
- Cheng EJ, Sharafi A, Sakamoto J. Intergranular Li metal propagation through polycrystalline Li6.25Al0.25La3Zr2O12 ceramic electrolyte. Electrochim Acta. 2017;223:85–91.
- Matsuki Y, Noi K, Deguchi M, et al. Lithium dissolution/deposition behavior of Al-doped Li7La3Zr2O12 ceramics with different grain sizes. J Electrochem Soc. 2019;166(3):A5470–A5473.
- Porz L, Swamy T, Sheldon BW, et al. Mechanism of lithium metal penetration through inorganic solid electrolytes. Adv Energy Mater. 2017;7(20):1701003.
- Lu Y, Huang X, Ruan Y, et al. An in situ element permeation constructed high endurance Li–LLZO interface at high current densities. ?J Mater Chem A. 2018;6(39):18853–18858.
- Sharafi A, Yu S, Naguib M, et al. Impact of air exposure and surface chemistry on Li–Li7La3Zr2O12 interfacial resistance. ?J Mater Chem A. 2017;5(26):13475–13487.
- Cheng L, Liu M, Mehta A, et al. Garnet electrolyte surface degradation and recovery. ACS Appl Energy Mater. 2018;1(12):7244–7252.
- Motoyama M, Tanaka Y, Yamamoto T, et al. The active interface of Ta-doped Li7La3Zr2O12 for Li plating/stripping revealed by acid aqueous etching. ACS Appl Energy Mater. 2019;2(9):6720–6731.
- Zheng H, Wu S, Tian R, et al., Adv Funct Mater. 2019.
- Yonemoto F, Nishimura A, Motoyama M, et al. Temperature effects on cycling stability of Li plating/stripping on Ta-doped Li7La3Zr2O12. J Power Sources. 2017;343:207–215.
- Shao Y, Wang H, Gong Z, et al. Drawing a soft interface: an effective interfacial modification strategy for garnet-type solid-state Li batteries. ACS Energy Lett. 2018;3(6):1212–1218.
- Inada R, Yasuda S, Hosokawa H, et al. Formation and stability of interface between garnet-type Ta-doped Li7La3Zr2O12 solid electrolyte and lithium metal electrode. Batteries. 2018;4(2):26.
- Zheng H, Wu S, Tian R, Xu Z, Zhu H, Duan H., Liu H. Intrinsic Lithiophilicity of Li–Garnet Electrolytes Enabling High-Rate Lithium Cycling. Adv. Funct. Mater.. 2019;30(6):1909189.
- Cai M, Lu Y, Su J, et al.. ACS Appl Mater Interfaces. 2019;11(38):35030–35038.
- Liu K, Li Y, Zhang R, et al. Facile surface modification method to achieve an ultralow interfacial resistance in garnet-based Li metal batteries. ACS Appl Energy Mater. 2019;2(9):6332–6340.
- Basappa RH, Ito T, Yamada H. Contact between garnet-type solid electrolyte and lithium metal anode: influence on charge transfer resistance and short circuit prevention. J Electrochem Soc. 2017;164(4):A666–A671.
- Wen J, Huang Y, Duan J, et al. Highly adhesive Li-BN nanosheet composite anode with excellent interfacial compatibility for solid-state Li metal batteries. ACS Nano. 2019;13(12):14549–14556.
- Sun B, Jin Y, Lang J, et al. A painted layer for high-rate and high-capacity solid-state lithium–metal batteries. Chem Commun (Camb). 2019;55(47):6704–6707.
- Han X, Gong Y, Fu KK, et al. Negating interfacial impedance in garnet-based solid-state Li metal batteries. Nat Mater. 2017;16(5):572–579.
- Luo W, Gong Y, Zhu Y, et al. Transition from superlithiophobicity to superlithiophilicity of garnet solid-state electrolyte. J Am Chem Soc. 2016;138(37):12258–12262.
- Wang C, Xie H, Zhang L, et al. Universal soldering of lithium and sodium alloys on various substrates for batteries. Adv Energy Mater. 2018;8(6):1701963.
- Wang C, Gong Y, Liu B, et al. Conformal, nanoscale ZnO surface modification of garnet-based solid-state electrolyte for lithium metal anodes. Nano Lett. 2017;17(1):565–571.
- Zhou C, Samson AJ, Hofstetter K, et al. A surfactant-assisted strategy to tailor Li-ion charge transfer interfacial resistance for scalable all-solid-state Li batteries. Sustainable Energy Fuels. 2018;2(10):2165–2170.
- Fu KK, Gong Y, Liu B, et al. Toward garnet electrolyte–based Li metal batteries: an ultrathin, highly effective, artificial solid-state electrolyte/metallic Li interface. Sci Adv. 2017;3(4):e1601659.
- Fu KK, Gong Y, Fu Z, et al. Transient behavior of the metal interface in lithium metal-garnet batteries. Angew Chem Int Ed Engl. 2017;56(47):14942–14947.
- Luo W, Gong Y, Zhu Y, et al. Semiconducting nanowire-based optoelectronic fibers. Adv Mater. 2017;29(22). DOI:https://doi.org/10.1002/adma.201700681
- Yang C, Zhang L, Liu B, et al. Continuous plating/stripping behavior of solid-state lithium metal anode in a 3D ion-conductive framework. Proc Natl Acad Sci U S A. 2018;115(15):3770–3775.
- Liu B, Zhang L, Xu S, et al. 3D lithium metal anodes hosted in asymmetric garnet frameworks toward high energy density batteries. Energy Storage Mater. 2018;14:376–382.
- Taylor NJ, Stangeland-Molo S, Haslam CG, et al. Demonstration of high current densities and extended cycling in the garnet Li7La3Zr2O12 solid electrolyte. J Power Sources. 2018;396:314–318.
- Krauskopf T, Hartmann H, Zeier WG, et al. Toward a fundamental understanding of the lithium metal anode in solid-state batteries—an electrochemo-mechanical study on the garnet-type solid electrolyte Li6.25Al0.25La3Zr2O12. ACS Appl Mater Interfaces. 2019;11(15):14463–14477.
- Wakasugi J, Munakata H, Kanamura K. Thermal stability of various cathode materials against Li6.25Al0.25La3Zr2O12 electrolyte. Electrochemistry. 2017;85(2):77–81.
- Miara L, Windmuller A, Tsai CL, et al. About the compatibility between high voltage spinel cathode materials and solid oxide electrolytes as a function of temperature. ACS Appl Mater Interfaces. 2016;8(40):26842–26850.
- Ren Y, Liu T, Shen Y, et al. Chemical compatibility between garnet-like solid state electrolyte Li6.75La3Zr1.75Ta0.25O12 and major commercial lithium battery cathode materials. J Materiom. 2016;2(3):256–264.
- Park K, Yu B-C, Jung J-W, et al. Electrochemical nature of the cathode interface for a solid-state lithium-ion battery: interface between LiCoO2 and garnet-Li7La3Zr2O12. Chem Mater. 2016;28(21):8051–8059.
- Kim KH, Iriyama Y, Yamamoto K, et al. Characterization of the interface between LiCoO2 and Li7La3Zr2O12 in an all-solid-state rechargeable lithium battery. J Power Sources. 2011;196(2):764–767.
- Dornseiffer J, Uhlenbruck S, Lobe S, et al. Cathode-electrolyte material interactions during manufacturing of inorganic solid-state lithium batteries. J Electroceram. 2017;38(2–4):197–206.
- Tsai C-L, Ma Q, Dellen C, et al. A garnet structure-based all-solid-state Li battery without interface modification: resolving incompatibility issues on positive electrodes. Sustainable Energy Fuels. 2019;3(1):280–291.
- Kato T, Hamanaka T, Yamamoto K, et al. In-situ Li7La3Zr2O12/LiCoO2 interface modification for advanced all-solid-state battery. J Power Sources. 2014;260:292–298.
- Ohta S, Kobayashi T, Seki J, et al. Electrochemical performance of an all-solid-state lithium ion battery with garnet-type oxide electrolyte. J Power Sources. 2012;202:332–335.
- Ren Y, Liu T, Shen Y, et al. Garnet-type oxide electrolyte with novel porous-dense bilayer configuration for rechargeable all-solid-state lithium batteries. Ionics. 2017;23(9):2521–2527.
- Kotobuki M, Munakata H, Yoshida T. Compatibility of Li[sub 7]La[sub 3]Zr[sub 2]O[sub 12] solid electrolyte to all-solid-state battery using Li metal anode. J Electrochem Soc. 2010;157(10):A1076–A1079.
- Han F, Yue J, Chen C, et al. Interphase engineering enabled all-ceramic lithium battery. Joule. 2018;2(3):497–508.
- Ohta S, Seki J, Yagi Y, et al. Co-sinterable lithium garnet-type oxide electrolyte with cathode for all-solid-state lithium ion battery. J Power Sources. 2014;265:40–44.
- Ohta S, Komagata S, Seki J, et al. All-solid-state lithium ion battery using garnet-type oxide and Li3BO3 solid electrolytes fabricated by screen-printing. J Power Sources. 2013;238:53–56.
- Feng L, Li L, Zhang Y, et al. Low temperature synthesis and ion conductivity of Li7La3Zr2O12 garnets for solid state Li ion batteries. Solid State Ion. 2017;310:129–133.
- Liu T, Zhang Y, Zhang X, et al. Enhanced electrochemical performance of bulk type oxide ceramic lithium batteries enabled by interface modification. ?J Mater Chem A. 2018;6(11):4649–4657.
- Liu T, Zhang Y, Chen R, et al. Non-successive degradation in bulk-type all-solid-state lithium battery with rigid interfacial contact. Electrochem commun. 2017;79:1–4.
- Liu T, Ren Y, Shen Y, et al. Achieving high capacity in bulk-type solid-state lithium ion battery based on Li 6.75 La 3 Zr 1.75 Ta 0.25 O 12 electrolyte: interfacial resistance. J Power Sources. 2016;324:349–357.
- Inada R, Yasuda S, Tojo M, et al. Development of lithium-stuffed garnet-type oxide solid electrolytes with high ionic conductivity for application to all-solid-state batteries. Front Energy Res. 2016;4. DOI:https://doi.org/10.3389/fenrg.2016.00028
- Rettenwander D, Geiger CA, Amthauer G. Synthesis and crystal chemistry of the fast Li-Ion conductor Li7La3Zr2O12 doped with Fe. Inorg Chem. 2013;52(14):8005–8009.
- Jin Y, McGinn PJ. Al-doped Li7La3Zr2O12 synthesized by a polymerized complex method. J Power Sources. 2011;196(20):8683–8687.
- Kotobuki M, Kanamura K, Sato Y, et al. Fabrication of all-solid-state lithium battery with lithium metal anode using Al2O3-added Li7La3Zr2O12 solid electrolyte. J Power Sources. 2011;196(18):7750–7754.
- Kato T, Iwasaki S, Ishii Y, et al. Preparation of thick-film electrode-solid electrolyte composites on Li7La3Zr2O12 and their electrochemical properties. J Power Sources. 2016;303:65–72.
- Liu B, Fu K, Gong Y, et al. Rapid thermal annealing of cathode-garnet interface toward high-temperature solid state batteries. Nano Lett. 2017;17(8):4917–4923.
- Jin Y, McGinn PJ. Bulk solid state rechargeable lithium ion battery fabrication with Al-doped Li7La3Zr2O12 electrolyte and Cu0.1V2O5 cathode. Electrochim Acta. 2013;89:407–412.
- Wang C, Zhang L, Xie H, et al. Mixed ionic-electronic conductor enabled effective cathode-electrolyte interface in all solid state batteries. Nano Energy. 2018;50:393–400.
- Koo M, Park KI, Lee SH, et al. Bendable inorganic thin-film battery for fully flexible electronic systems. Nano Lett. 2012;12(9):4810–4816.