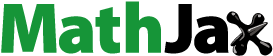
ABSTRACT
The corrosion of magnesium (Mg) alloy anodes poses a significant challenge in the development of magnesium-based batteries. In this study, the inhibition effect of different concentrations of TSP in sodium chloride (NaCl) solution on the corrosion behaviour of Mg alloy anodes in magnesium batteries was investigated. The immersion periods were varied to assess the long-term efficacy of TSP as a corrosion inhibitor. Tafel polarisation analysis revealed a shift in corrosion potential towards more noble values with increasing TSP concentration, indicating enhanced corrosion resistance. EIS measurements provided insights into the changes in charge transfer resistance and double-layer capacitance, corroborating the protective effect of TSP against corrosion. Furthermore, CV and LSV analyses elucidated the dynamic corrosion processes and confirmed the efficacy of TSP as a corrosion inhibitor. This study comprehensively investigates the inhibition mechanism of TSP on the corrosion behaviour of Mg alloy anodes in magnesium batteries.
Introduction
Magnesium (Mg) alloys have garnered significant attention as promising materials for anodes in various battery technologies due to their exceptional properties, including high specific capacity, abundance, low cost, and low reduction potential. The demand for high-energy-density rechargeable batteries has intensified with the growing need for portable electronics, electric vehicles, and grid-scale energy storage systems. To meet these demands, researchers are actively exploring alternative electrode materials beyond conventional lithium-ion batteries. Mg alloys possess a theoretical specific capacity much higher than that of conventional lithium-ion battery materials such as graphite. The high theoretical specific capacity of Mg (2205 mAh/g) makes it an attractive candidate for next-generation battery systems. The practical application of Mg alloys as anodes in batteries faces several challenges, primarily related to their high reactivity and susceptibility to corrosion. Mg alloys readily react with the electrolyte, leading to the formation of surface films and passivation layers, which can impede charge transfer kinetics and degrade battery performance over time. To address these challenges, extensive research efforts have been directed towards understanding the corrosion mechanisms of Mg alloys by exploring novel electrolyte formulations and additives to improve battery performance and stability. Mg-1Sn has higher corrosion resistance than Mg-5Sn and Mg-9Sn owing to the formation of a strong protective tin oxide layer [Citation1,Citation2]. Alloying elements Ce, Y, and Zn contribute to the corrosion resistance of the Mg by forming the rich passivating oxide/hydroxide layers on the alloy surface [Citation3]. The addition of Ca, Mn, and Sn in Mg enhances the ductility and improved yield strength of 450 MPa. This has resulted in the elongation of the current alloy by 3 times as compared to T×22alloy(Mg-2Sn-2Ca). Furthermore, the dragging mechanism of the nano-Mn particles limits their development and increases the rate of nucleation for dynamic recrystallization, eventually forming ultrafine grains [Citation4]. The performance of a layered buserite on Mg-Mn oxide cathode in an aqueous rechargeable Mg-ion battery exhibited high specific capacity, good cycling stability, and high-rate capability, indicating its potential as a promising cathode material for Mg-ion batteries [Citation5]. The addition of Ca in Mg-Mn alloy enhances the electronegativity of the open circuit potential of the alloy resulting in the breakdown of the passive layer resulting in a process of dissolution between underneath surface alloy species and the ions [Citation6]. The addition of Zn improved the corrosion resistance of the Mg-1Sn alloy anode, resulting in better electrochemical performance and increased stability during battery operation [Citation7]. Mg-Zn-Sn alloy anode has a higher operating voltage than the Mg-Zn anode [Citation8]. Impedance analysis of magnesium alloys such as AZ31, AZ61, and AP65 immersed in magnesium perchlorate solution exhibited the activation-controlled mechanism in anode-electrolyte interface [Citation9]. A specific capacity of 1411.8 mAh g−1 and energy density of 1153 mWhg −1 was obtained for AZ31–5.8Gd at the current density of 40 mA cm−2 [Citation10]. Magnesium anode shows reduced corrosion rates in CaSO4-Mg (OH)2 solution compared to NaCl solution, due to the formation of a protective layer of magnesium hydroxide (Mg(OH)2) on the anode surface [Citation11]. The addition of plasticizers in solid polymer electrolytes of poly(ethylene oxide) and magnesium triflate which are plasticized with propylene carbonate (PC), ethylene carbonate (EC), and a mixture of PC and EC, improves the conductivity of electrolyte [Citation12]. Mg-Al-Pb-In alloy showed a higher utilization efficiency and more negative potential compared to Mg-Al-Pb alloy and the peak power density was observed as 94.5 mW cm−2 [Citation13]. The intensified efficiency of (SDBS) on the corrosion inhibition of Mg-Al-Zn-Mn alloy in aqueous ethylene glycol solution (30%) containing chloride ions is examined. Sodium dodecyl benzene sulphonate containing trisodium phosphate and sodium benzoate inhibited the corrosion of Mg-Al-Zn-Mn alloy in ethylene glycol solution which was analysed through potentiodynamic polarization tests [Citation14]. Decyl glucoside, which is derived from natural sources such as glucose and fatty alcohols, has been found to have excellent surface-active properties inhibiting the corrosion process resulting in better electrolyte penetration into the electrode, ionic conductivity improves the performances of the battery [Citation15]. Phosphate and vanadate electrolyte additives can significantly enhance the discharge capacity, energy efficiency, and cycle life of Mg-air batteries. Phosphate shows a better efficiency than vanadate [Citation16]. Sodium alginate (SA) and phosphate (SP) are used as inhibitor in this study. The effect of those inhibitors as individual and combined is tested in the study. During EIS, the efficiency of the joint (SA-SP) showed better and reached the value of 98% [Citation17]. Murrayya koenigii leaf extract was used as an inhibitor for corrosion studies of mild steel in 1 M HCl and 0.5 M H2SO4 and it was observed that inhibitor efficiency increases with the increase in its concentration [Citation18]. A lower self-corrosion rate and high discharge performance were observed in AZ80-xSm anodes than in AZ80 [Citation19]. Mg-Al-Pb-RE alloy strips exhibited excellent electrochemical performance as anodes for Mg-air batteries with a high specific capacity of 993 mAh/g and a low discharge voltage [Citation20]. High corrosion current density was found in Mg-6Al-1In than in Mg-6Al-1In-1Ce [Citation21]. Linear sweep voltammetry method is used to examine the corrosion property of stainless steel in different concentrations of NaCl and H2SO4 solution. As the concentration of both solutions increases the pitting corrosion of steel starts to decrease [Citation22]. Mg-5Sn exhibits superior battery discharge performance at low current densities < 2mAcm−2 compared to pure Mg and other Mg-Sn alloy anodes [Citation23]. The increase in the concentration of chloride ions shows a rise in the corrosion rate. The corrosion rate of AZ63 alloy increases with the decrease in pH value [Citation24]. ZE41 in 1 M NaCl with pH 3 has the highest corrosion rate and more active corrosion potential [Citation25]. Mg-2Zn-0.5 Nd-0.5 Zr alloy was subjected to solution treatment at different temperatures, and it was found that the alloy treated at 500°C had a lower degradation rate compared to the untreated alloy [Citation26]. The authors investigated the mechanical properties of triaxial forged Mg-2An-2Gd alloy and they found that ultra-strength and ductility were achieved owing to the ultra-fine grain size refinement and the drastic reduction in the size of W-phase precipitates [Citation27]. The rapid rolling process was carried out on the AZ91 sheet by setting the speed ratio between upper and lower roll as 1, 1.1, 1.2, and 1.3 and it was observed that the dynamic recrystallization fraction rate of grains increases with the increase in rolling speed ratio helps to improve its strength and toughness [Citation28]. The compression behaviour of AZ91 alloy at 200°C and 300°C was investigated, and it was observed that at higher temperatures, there might be a possibility of the precipitation of finer secondary phases at the shear bands which is not liable for deformation [Citation29]. The authors have investigated the strength and deformation behaviour of symmetric and asymmetric rolling processing conditions on AZ91 alloy, and they found that asymmetric rolled alloy showed better strength and deformation attributed to grain refinement and weaker basal texture [Citation30]. The electrochemical corrosion and discharge performance characteristics of Mg alloys as anodes in 3.5 wt.% NaCl was reviewed for high-performance battery applications [Citation31]. Mg-0.5Bi-0.5Ca-0.5Ag exhibited a stable discharge behaviour in 3.5 wt.% NaCl due to the uniform dissolution of the anode than Mg-0.5Bi owing to the protection of corrosion products favoured with the addition of Ca and Ag [Citation32]. The deposition of Ag ions on the surface of the Mg-1Ag anode promotes the dissolution of the Mg and the formation of a non-homogeneous corrosion product layer accelerating the discharge activity [Citation33]. The discharge performance was found to be better in ZM61 - 0.6Nd alloy owing to the formation of corrosion products and its breaking effect [Citation34]. From the works of scientific literature, it was understood that the alloying, heat treatment, and secondary processing contribute to improving the strength, ductility, and corrosion resistance of Mg and its alloys. Furthermore, the addition of inhibitors plays a major role in the corrosion mechanism of any material. Sn, Ca, and Mn were identified to add on Mg which has a positive effect on controlling the dissolution of Mg in electrolytes and could help to improve the battery life. Mg-Sn-Ca alloy resulted in low grain refinement and brittle [Citation4]. Mn refines grain growth and improves the mechanical properties of metal by enhancing ductility [Citation4,Citation5]. So, tin(Sn), Calcium (Ca), and Manganese (Mn) are used. Corrosion can affect the structural integrity of alloys and make them hazardous for battery usage. By improving the corrosion resistance, the risk can be minimised, and the performance of the battery will be increased. In this context, this study aims to investigate the corrosion behaviour of Mg alloy anode in battery systems using 3.5 wt.% NaCl and evaluate the effectiveness of trisodium phosphate (TSP) as a corrosion inhibitor. Through comprehensive electrochemical analyses, including Tafel polarisation, Electrochemical Impedance Spectroscopy (EIS), Cyclic Voltammetry (CV), and Linear Sweep Voltammetry (LSV), this research seeks to elucidate the inhibition mechanism of TSP and its impact on the long-term stability and performance of Mg-based battery systems. Such insights are crucial for advancing the development of Mg alloy anodes and accelerating the commercialisation of magnesium-based batteries for diverse applications in energy storage and beyond.
Methodology
The dilute Mg alloy was prepared by adding the alloying elements with minor concentrations of 5 wt% Sn, 0.2 wt.% Ca and 0.2 wt.% Mn was fabricated using the stir and squeeze casting technique. Sn was used since it has a high theoretical specific capacity (903 mA h g−1) and low reaction voltage (0.15 V vs. Mg2+/Mg) [Citation1]. Mg anode’s discharge voltage will increase with the addition of Ca as an alloying element [Citation6]. The addition of Mn causes the alloy’s grains to become more refined and lower the corrosion rate [Citation4]. Pure magnesium along with Sn ingots, Ca, and Mn granules loaded in the furnace and heated to the temperature of 720◦C. The melt was stirred at the speed of 600 rpm with an intermittent duration of 5 minutes during the process of melting. The molten material further flowed downwards towards the preheated mould of 400°C and the molten metal was squeezed by applying the pressure of 40 tons for rapid solidification. Since Mg is inflammable the whole casting process is taken under a controlled atmosphere of pure argon gas. The samples are ground in grit paper and polished using diamond paste. Glycol [HNO3 -0.1 ml, ethylene glycol- 7.5 ml, and water- 2.5 ml] is used as the etchant. The morphology of as-cast Mg-5Sn-0.5Ca-0.5Mn alloy was analysed using optical microscopy, and a Scanning Electron microscope (SEM). Energy Dispersive Spectrometer [EDS] was used to analyse the presence of alloying elements and their composition. Image J software was used to find the volume fraction and average grain size of as cast Mg-Sn-Ca-Mn alloy. To improve the corrosion properties sodium salts of phosphate, silicate, vanadate, alginate and sodium benzoate are widely used [Citation14,Citation16,Citation17]. The products formed over the layer of magnesium after the addition of phosphate are crack-free and moderately eroded compared to vanadate [Citation16]. So, Tri-sodium phosphate [TSP] was used as an inhibitor along with 3.5 wt. % NaCl solution in this study. The immersion tests were conducted for the samples in electrolytes with and without the addition of TSP inhibitors for different immersion times. The as-cast samples were immersed in the electrolyte and the weight loss and pH were noted to measure the weight loss/gain. The anode was immersed in electrolyte for 72 hours with different concentrations of the inhibitor to check the inhibitor efficiency. The electrochemical corrosion tests were performed by having an as-cast sample act as a working electrode with a 0.375 cm2 area of exposure, the saturated calomel electrode (SCE) act as the reference electrode, and the platinum wire as a counter electrode. Different concentrations of TSP [0.1 wt. %, 0.2 wt. % and 0.3 wt. %] added along with 3.5 wt.% NaCl [Citation18] to evaluate the inhibiting efficiency of Mg alloy corrosion. Interface 1010, Gamry Instruments was used to conduct the electrochemical test according to ASTM G3–14(2019). Open circuit potential was run for 200 seconds to observe the behaviour of the Mg anode and to determine its stability. The electrochemical corrosion properties of the material are measured with the help of EIS (electrochemical impedance spectroscopy), Tafel scan, and physical electrochemistry tests (cyclic voltammetry, linear sweep voltammetry). Potentiostatic EIS tests were carried out to observe the electrochemical behaviour and measure the charge/discharge property of the material. The potentiostatic method is where the current was measured with the potential being constant for a certain period and hence charge transfer values are obtained from the resultant graph. A potentiostatic test was conducted between the frequency of 10 kHz to 0.1 Hz with AC voltage as 10 mV rms. Tafel tests or potentiodynamic tests are used to measure corrosion properties such as icorr (corrosion current density), Ecorr(corrosion potential), and the corrosion rate of the material. The protective ability of the material was measured by the polarization resistance [Rp]. Tafel extrapolation plotted with the range of voltage from -0.3 V to 0.3 V with 0.5 mV/s scan rate. Using Anodic (βa) and cathodic (βc) values, the polarisation resistance value was calculated from the Equationequation (1)(1)
(1) .
Using the Equationequation (2)(2)
(2) , the efficiency of the inhibitor for the short term and after 72 hours of immersion can be calculated,
ixcorr – represents the corrosion current density before the inhibitor and iycorr represents the corrosion current density after using the inhibitor. Cyclic voltammetry was carried out to find the current by sweeping the potential front and back. The peaks obtained from the graph can be calculated to find the standard electrode potential. Linear sweep voltammetry (LSV) was a similar technique in which the potential was scanned in only one direction. LSV was performed at the sweeping voltage of 0.5 V to 0 V.
Results and discussion
shows the SEM micrographs, optical images, and EDS of the as-cast sample. The chemical composition was measured by EDS to 92.44% - Mg, 6.62% -Sn, 0.5%-Mn, and 0.44% Ca. In addition, some fine nanoscale and submicron-scale precipitates were observed in the grain interior and along the grain boundary. The phases (α-Mg+ Mg2Sn+Mg2Ca) are formed following a eutectic reaction during solidification. The grey area represents the α-Mg phase and black strip is Mg2Sn and the small spherical particles represent the Mg2Ca phases as shown in ). Less content of calcium and Manganese are observed. The volume fraction of α-Mg is 71.65% and the remaining phases Mg2Sn and Mg2Ca are 28.35%. The average grain size of the as-cast alloy was found to be 250 μm depicted in the ).
Figure 1. As cast Mg-5Sn-0.2Ca-0.2Mn (a) SEM micrograph, (b) optical micrograph, (c) EDS spectrum and (d) average grain size distribution.
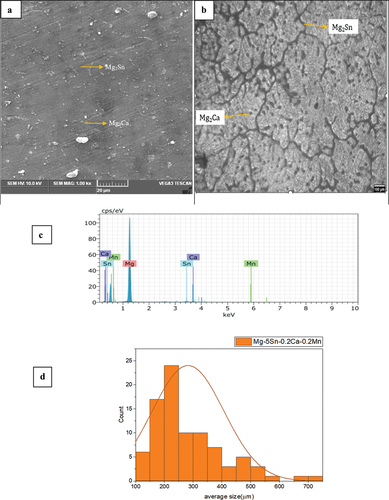
shows the SEM micrographs and EDS spectrum of as-cast samples immersed in NaCl and NaCl with TSP for 72 h. The presence of phosphate and sodium was observed and shows the composition of corroded samples. There may be a possibility of the formation of Mg(OH)2 in the electrolyte which acts as the buffer to reduce the acidic content and increases the pH value in the electrolyte (Equationequation 3(3)
(3) ). The formation of layer Mg(OH)2 is due to the self-corrosion of Magnesium in H20. The oxide layer decreases the contact area between the alloy and electrolyte. The layer acts as a barrier which improves corrosion resistance and decreases the corrosion rate. The EDS () shows the presence of P (phosphate) on the surface of immersed samples. Mg3(PO4)2 layer formed by Equationequation (4)
(4)
(4) . The deposited magnesium phosphate [Mg3(PO4)2] layer is denser and stronger than the magnesium hydroxide layer. The Mg3(PO4)2 deposited on the pores between Mg(OH)2 [Citation14,Citation16,Citation17]. TSP helps prevent corrosion by forming a protective layer on metal surfaces. TSP is alkaline and can be used to adjust the pH of solutions. Corrosion processes are often accelerated in acidic environments, so by adding TSP increasing the pH helps to mitigate corrosion. TSP can form complexes with metal ions present in the solution. These complexes can stabilise the metal ions and reduce their reactivity, thus slowing down the corrosion process. When TSP is added to a solution containing magnesium ions and NaCl, the reaction occurs as given in Equationequation 3
(3)
(3) and Equation4
(4)
(4) respectively and illustrated in .
Figure 2. SEM micrographs and EDS spectrum of as cast Mg-5Sn-0.2Ca-0.2Mn immersed in (a) NaCl, (b) NaCl +0.1 wt.% TSP, (c) NaCl +0.2 wt.% TSP, (d) NaCl +0.3 wt.% TSP.
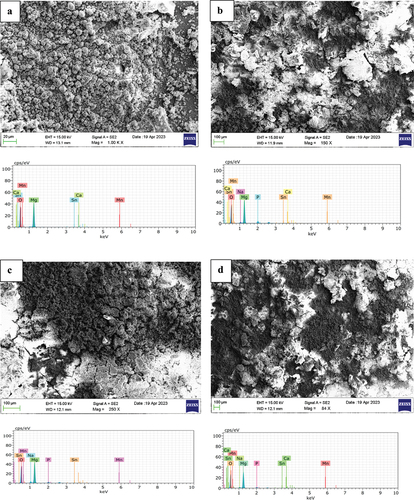
Table 1. Chemical composition of corroded samples.
The precipitation of Magnesium phosphate helps to remove Mg2+ ions from the electrolytic solution which reduces its concentration and supports against corrosion. The weight loss/gain of the samples was observed after 72 hours of immersion given in and the pH was measured at different intervals of 24 h, 48 h, and 72 h respectively as shown in . The pH value of NaCl was noted to be 6.9. As the immersion time increases, the pH rises to 10 and the pH was maintained at the range of 11 at 72 h of immersion. pH for electrolytes along with the different concentrations of electrolyte start from 11 and on further immersion is maintained between 10. This indicates that a strong oxide layer was formed over the surface. The minimal loss of Mg ions shows the longevity of the alloy. The slow degradation of Mg alloy ensures an extended functional period of battery. The immersion test confirms the layers formed over the anode surface prevent further corrosion.
Table 2. Weight gain of Mg alloy during 72 hours of immersion.
The main purpose of the open Circuit Potential was to observe the anode behaviour during the immersion. and shows the result of the OCP curve of the Magnesium alloy anode in 3.5 wt. % NaCl electrolyte and with different concentrations of TSP for short-term and 72 hours of immersion. The graph shows that slight increase in potential values for the curves of Mg alloy immersed in NaCl electrolyte along with TSP inhibitor. The sample immersed in a NaCl electrolyte solution for 72 hours has the highest stable potential, and the potential values show a gradual shift towards the positive direction with the addition of respective concentrations of inhibitors to the immersed samples. The OCPs can be ranked in a decreasing series as: 0.1 wt. % [ST] < NaCl [ST] < 0.2 wt. % [ST] < 0.3 wt. % [ST] < 0.2 wt. % [72 h] < 0.3 wt. % [72 h] < 0.1 wt. % [72 h] < NaCl [72 h]. The anti-corrosion layer formed on the surface of the Mg alloy during immersion exhibited a stable potential. The increase in potential value denotes the formation of a protective passive layer. The curve lines depict a stable potential value indicating that the electrode system is in equilibrium form. Nquist and bode plots (Z curve and phase angle curve) obtained for the as-cast Mg alloy immersed in NaCl and NaCl with different concentrations of TSP under various immersion periods are shown in . The results were analysed by fitting with the electrical circuits as depicted in . The electrical equivalent circuit model of the Mg alloy samples consists of Rs [R1] as the electrolyte resistance, Rc [R2] and CPEc [Yo1] represent the resistance and constant phase capacitance of the Mg anode, while CPEdl [Yo2] and Rct [R3] represent the constant phase capacitance of the electric double layer and the charge transfer resistance [Citation3], and W represent infinite Warburg. The Warburg impedance is the diffusional impedance for the diffusion layer of infinite thickness, which is characterized by the electrode. The impedance was represented using real and imaginary parts. The Nyquist plot is plotted against the real part (Zreal) in the X-axis and the imaginary part (Zimag) in the Y-axis. ) shows that the solution resistance (Rs) value for short-term immersion was similar and the lowest Rct value was recorded for the as-cast sample immersed in NaCl solution for a short term. The increase in charge transfer was measured when an inhibitor was added to the NaCl solution. This indicates that the charge transfer was better with the addition of an inhibitor. The Rct value of the as-cast sample increased in the presence of an inhibitor. The highest value was recorded when adding 0.2 wt. % of tri-sodium phosphate [2 g/l] to NaCl solution for a short-term duration. shows the obtained EIS result from the Nyquist plot. The polarization resistance was the sum of solution resistance and charge transfer resistance. The polarization resistance (Rp) value of the as-cast sample in NaCl solution is 232.43Ω. The highest Rp value for the short term was recorded at 0.2 wt. % of TSP which is 479.25Ω. This shows there is an increase in efficiency with the addition of inhibitors. The increasing tendency of immersed samples shows better charge transfer value and polarisation resistance than the short-term duration of immersion. But from the Nyquist plots in , the diameter of the formed semi-circular curve was bigger for the sample immersed for 72 hours in NaCl solution and also in the presence of an inhibitor. This implies that the efficiency and resistance of the material have increased upon immersing it in the NaCl solution along with the inhibitor. The inductive resistance in short-term immersion at low frequency shows that electrochemical activity occurred through radical intermediate. The impedance curve of 0.3 wt. % of TSP goes on increasing for 72 hours immersed sample. The semicircle of the Nyquist plot is large, and the 45° line was less visible indicating the slow electron transfer rate. When the semicircle is too small and the 45° line is large, it indicates a very fast electron transfer rate. So, 0.3 wt. % of TSP shows has the highest charge transfer value than the other possibilities. The Bode plot consists of phase angle and modulus plotted as a function of frequency. The phase angle and modulus are calculated using real and imaginary parts. represent the Z curve and phase angle curve. The as-cast Mg alloy of ST showed a higher value than the others initially. The higher phase angle value during the short term indicates that the protective oxide layer was stronger and less porous. However, the initial values of the immersed samples were negative. As the frequency increases after 500, the phase angle value starts to increase for all the samples. Concerning Z curve, the as-cast sample immersed for 72 hrs in NaCl with the presence of 0.3% inhibitor has the higher initial modulus value. With the increasing frequency, there is a decrease in modulus value. The highest value was recorded when adding 0.3% of tri-sodium phosphate to the NaCl solution. This concludes that it has better charge transfer resistance compared to others.
Table 3. Open potential circuit results after 200 seconds.
Table 4. EIS results of Mg-Sn-Ca-Mn alloys.
Tafel test was conducted in NaCl electrolyte with and without inhibitor for short-term and 72 hours of immersion. As the result of Tafel extrapolation, corrosion current density (icorr), corrosion potential (Ecorr), anodic (βa) and cathodic (βc) current are obtained. shows the result of Tafel extrapolation of Mg-5Sn-0.2Ca-0.2Mn anode in different concentrations of inhibitor. During Short-term immersion, the Tafel plot of Mg-5Sn-0.2Ca-0.2Mn extends between −2.0 V to −1.25 V. Adding Sn, Ca, and Mn has improved the corrosive property of Magnesium. The addition of those alloys had increased the Ecorr of the alloy. Ecorr of Mg alloy in NaCl is -1.560 V exhibiting the potential of the samples with inhibitor was higher. The addition of Ca along with Magnesium increases the anodic reaction rate. The anode immersed in an inhibitor for the short term exhibits a cathodic reaction like the cathodic reaction of an anode immersed only in NaCl. Whereas the anodic kinematics of the sample-immersed inhibitor has decreased. This shows that TSP acts as an anodic inhibitor for a short-term duration by enhancing the anodic reaction. Anode with the presence of an inhibitor shows high corrosion potential [Ecorr]. Electrolyte with 0.2 and 0.3 wt. % TSP has the potential of -1.500 V. And 0.1 wt. % of TSP shows a higher potential of -1.470 V than other concentrations. After 72 hours of immersion, the Tafel curve shifted backwards which indicated that the anodic kinematics decreased. Both the anodic and cathodic curves of the 72 h immersed sample had shifted. Trisodium phosphate acted as a mixed inhibitor during the 72 hours of immersion. A decrease in corrosion current density (icorr) was noted. The decreasing trend in corrosion current denotes more corrosion resistance was offered by the inhibitor. The sample immersed for 72 h shows passivation between -0.5 V to -0.2 V. The trans-passivation region started to form after -0.2 V and later formed a secondary passivity region. The sample was immersed in 0.1 wt. % of TSP has the current density of 0.402 μA and the sample was immersed in 0.3 wt. % TSP has a lower icorr of 0.0609 μA. The immersed samples for 72 hours have more corrosion resistance than the sample immersed in the short term. From , the sample was immersed for 72 h in 0.3 wt. % TSP has a low corrosion rate, corrosion current density, and high corrosion potential of -533 mV. Polarisation resistance shows the protective ability of the electrodeposited coating on the material. From samples immersed in electrolyte for 72 hours have high polarisation resistance that indicates the protective layer is formed over the surface of the anode and it resists further corrosion. From Equationequation (2)(2)
(2) , the efficiency of the inhibitor concentration was calculated. shows the result of the inhibitor efficiency. 0.2 wt. % of TSP shows better efficiency during the short term and 0.3 wt. % of TSP show better efficiency for 72 h of immersion.
Figure 11. Tafel curves of Mg-5Sn-0.2Ca-0.2Mn for different immersion period in different electrolyte concentrations
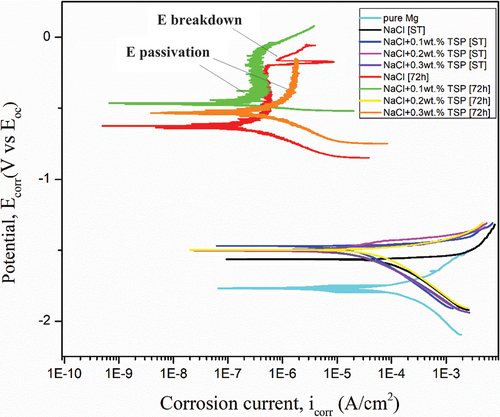
Table 5. Corrosion results of Mg-5Sn-0.2Ca-0.2Mn alloys estimated by the tafel extrapolation method.
Table 6. Inhibitor efficiency of trisodium phosphate.
Cyclic voltammetry (CV) was a widely used and effective electrochemical method utilised to examine the oxidation and reduction processes of molecules. It is involved in obtaining qualitative kinetic information about a capacitive electrochemical cell, including characteristics like capacitance, voltage range, and cycle durability. Each peak observed in a CV dataset corresponds to a specific electrochemical process, with the peak height indicating the inhibitor concentration. During CV, the current passing through the electrochemical cell was depicted as the voltage range was systematically varied. In a CV experiment, the electrolyte is typically either oxidised or reduced by bringing it into contact with the electrode. By integrating the CV curve, it is possible to directly determine the amount of charge transferred during the electrochemical reaction. illustrate the CV curves of the Mg alloy for three cycles (1st cycle represented by black, 2nd cycle by red, and 3rd cycle by blue). Upon immersing the samples for 72 hours, a noticeable decrease in current was observed during subsequent scans due to the activation of the anode materials resulting increase in reaction surface area. On voltammetry, the magnitude current of a short-term immersed anode has high current peaks. On the other hand, both the cathodic and anodic current was observed to be minimal for the samples immersed for 72 hours. The formation of a passivating layer on the magnesium alloy was likely seen by extra peaks forming in samples that were immersed for the short term [Citation12]. These findings indicated that the cathodic deposition on the magnesium alloy anode was not advantageous, whereas the cathodic deposition and anodic stripping of the Mg alloy during the 72 h immersion at the interface between the magnesium anode despite the presence of the surface film. There were no oxidation and reduction peaks observed for the immersed sample. The formation of the oxide layer over Mg alloy suppressed the oxidation and reduction peaks completely. This result showed that TSP can suppress the oxidation and reduction reactions of as-cast Mg alloy during 72 hours of immersion.
Figure 12. CV curves of Mg alloy in (a) NaCl (b) 0.1wt. % TSP (c) 0.2wt. % TSP (d) 0.3wt. % TSP for short term of immersion.
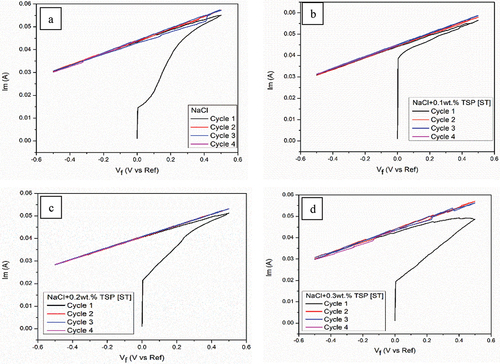
Figure 13. CV curves of Mg alloy in (a) NaCl (b) 0.1wt. % TSP (c) 0.2wt. % TSP (d) 0.3wt. % TSP for 72 hours of immersion.
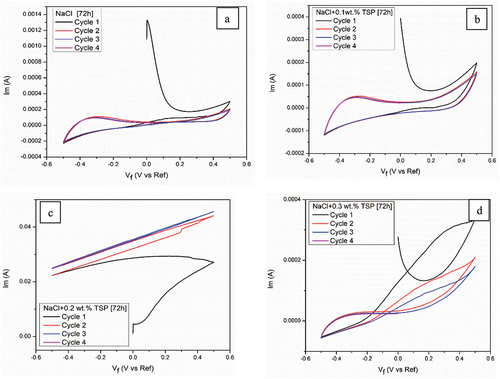
Linear Sweep Voltammetry (LSV) was a simplified form of Cyclic Voltammetry that involves a single unidirectional voltage sweep. In LSV, the voltage sweep ranged from 0.5 V to 0 V. The current-potential curve was obtained for each concentration of the inhibitor. By analysing , it was observed that the current increases for samples immersed for a short period. This rise in current was attributed to the availability of more electrons after depleting the passive layer. However, after 72 hours of immersion, the current started to decrease notably, with a concentration of 0.3 wt. % TSP records a lower current of 34.47 µA. Beyond a certain voltage, the current begins to rise again, indicating the occurrence of a sharp increase at a specific potential known as the pitting potential (EP). The pitting potentials were determined for samples immersed in NaCl with various inhibitor concentrations. Specifically, the pitting potentials for the anode immersed in NaCl, 0.1 wt. % TSP, and 0.3 wt. % TSP are 134.1 mV, 84.17 mV, and 88.18 mV, respectively. This suggests that the formation of an oxide layer during immersion raises the required voltage, making it more challenging to break down the oxide layer. A higher pitting potential indicates greater corrosion resistance. The samples immersed for 72 hours exhibit higher pitting potentials, indicating enhanced corrosion resistance.
Conclusion
The electrochemical corrosion performance of Mg-5Sn-0.2Ca-0.2Mn alloy anode was investigated in 3.5 wt. % NaCl solution with the presence of different concentrations of Tri-sodium phosphate. The following conclusions were drawn to determine the potential of using as an anode in alkaline Mg batteries: Mg-5Sn-0.2Ca-0.2Mn shows a higher impedance during short-term immersion in the NaCl with 0.2 wt. % TSP and high electron transfer rate with 0.3 wt. % of TSP. The lesser corrosion current density and higher potential were observed for 72 h immersed as-cast Mg alloy in 0.3 wt. % TSP. Tri-sodium phosphate acts as an anodic inhibitor during short term and a mixed inhibitor during 72 hours of immersion. The inhibitor efficiency of 82.03% was attained with 0.3 wt. % of TSP. The oxide layer formed on the anode layer acts as a double-layer capacitor and increases charge transfer. The addition of TSP in the electrolyte was a positive attempt to improve the corrosion resistance of Mg alloy which paves the way for serving as the anode in the alkaline Mg batteries.
Disclosure statement
No potential conflict of interest was reported by the author(s).
Additional information
Funding
References
- Han L, Zhang Y, Guo Y, et al. Electrochemical behaviors and discharge performance of Mg-sn binary alloys as anodes for Mg-air batteries. Mater Res Express. 2021;8(12):126531. doi: 10.1088/2053-1591/ac4439
- Chen X, Wei S, Tong F, et al. Electrochemical performance of Mg-Sn alloy anodes for magnesium rechargeable battery. Electrochimica Acta. 2021;398:139336. doi: 10.1016/j.electacta.2021.139336
- Wang N, Wang R, Feng Y, et al. Discharge and corrosion behavior of Mg-Li-Al-Ce-Y-Zn alloy as the anode for Mg-air battery. Corros Sci. 2016;112:13–14. doi: 10.1016/j.corsci.2016.07.002
- Zhang A, Kang R, Wu L, et al. A new rare-earth-free Mg-Sn-Ca-Mn wrought alloy with ultra-high strength and good ductility. Mater Sci Eng A. 2019;754:269–274. doi: 10.1016/j.msea.2019.03.095
- Sun C, Wang H, Yang F, et al. Layered buserite Mg-mn oxide cathode for aqueous rechargeable Mg-ion battery. J Magnesium Alloys. 2023;11(3):840–850. doi: 10.1016/j.jma.2022.11.005
- Shamsudin SR, Rahmat A, Isa MC, et al. Electrochemical corrosion behavior of Mg-(Ca, Mn) sacrificial anodes. In: AMR. Vol. 795. 2013. p. 530–534. doi: 10.4028/www.scientific.net/amr.795.530
- Karudesh E, Francis AL, Sreekanth D, et al. Effect of zinc on electrochemical corrosion behavior of Mg-1Sn alloy as anode for Mg batteries. Mater Today Proc. 2023. doi: 10.1016/j.matpr.2023.03.244
- Tong F, Chen X, Wei S, et al. Microstructure and battery performance of Mg-zn-sn alloys as anodes for magnesium-air battery. J Magnesium Alloys. 2021;9(6):1967–1976. doi: 10.1016/j.jma.2021.08.022
- Udhayan R, Bhatt DP. On the corrosion behavior of magnesium and its alloys using electrochemical techniques. J Power Sources. 1996;63(1):103–107. doi: 10.1016/S0378-7753(96)02456-1
- Li Q, Xiong W, Yu S, et al. Effect of Gd content on the discharge and electrochemical behaviors of the magnesium alloy AZ31 as an anode for Mg-air battery. J Mater Sci. 2021;56(22):12789–12802. doi: 10.1007/s10853-021-06135-2
- Guadarrama-Munoz F, Mendoza-Flores J, Duran-Romero R, et al. Electrochemical study on magnesium anodes in NaCl and CaSO4–mg (OH) 2 aqueous solutions. Electrochimica Acta. 2006;51(8–9):1820–1830. doi: 10.1016/j.electacta.2005.02.144
- Kumar GG, Munichandraiah N. Effect of plasticizers on magnesium-poly (ethyleneoxide) polymer electrolyte. J Electroanal Chem. 2000;495(1):42–50. doi: 10.1016/S0022-0728(00)00404-6
- Wang N, Wang R, Peng C, et al. Discharge behavior of Mg-Al-Pb and Mg-Al-Pb-In alloys as anodes for Mg-air battery. Electrochimica Acta. 2014;149:193–205. doi: 10.1016/j.electacta.2014.10.053
- Medhashree H, Shetty AN. Synergistic inhibition effect of trisodium phosphate and sodium benzoate with sodium dodecyl benzene sulphonate on the corrosion of Mg-Al-Zn-Mn alloy in 30% ethylene glycol containing chloride ions. J Adhes Sci Technol. 2019;33(5):523–548. doi: 10.1080/01694243.2018.1543529
- Deyab MA. Decyl glucoside as a corrosion inhibitor for magnesium–air battery. J Power Sources. 2016;325:98–103. doi: 10.1016/j.jpowsour.2016.06.006
- Zhao Y, Huang G, Zhang C, et al. Effect of phosphate and vanadate as electrolyte additives on the performance of Mg-air batteries. Mater Chem Phys. 2018;218:256–261. doi: 10.1016/j.matchemphys.2018.07.037
- Hou L, Dang N, Yang H, et al. A combined inhibiting effect of sodium alginate and sodium phosphate on the corrosion of magnesium alloy AZ31 in NaCl solution. J Electrochem Soc. 2016;163(8):C486. doi: 10.1149/2.0941608jes
- Quraishi MA, Singh A, Singh VK, et al. Green approach to corrosion inhibition of mild steel in hydrochloric acid and sulphuric acid solutions by the extract of murraya koenigii leaves. Mater Chem Phys. 2010;122(1):114–122. doi: 10.1016/j.matchemphys.2010.02.066
- Chen X, Liao Q, Le Q, et al. The influence of samarium (Sm) on the discharge and electrochemical behaviors of the magnesium alloy AZ80 as an anode for the Mg-air battery. Electrochimica Acta. 2020;348:136315. doi: 10.1016/j.electacta.2020.136315
- Wang N, Li W, Huang Y, et al. Wrought Mg-Al-Pb-RE alloy strips as the anodes for Mg-air batteries. J Power Sources. 2019;436:226855. doi: 10.1016/j.jpowsour.2019.226855
- Li Y, Ma J, Wang G, et al. Effect by adding Ce and in to Mg–6Al alloy as anode on performance of Mg-air batteries. Mater Res Express. 2019;6(6):066315. doi: 10.1088/2053-1591/ab0fb6
- Rajendrachari S. Investigation of electrochemical pitting corrosion by linear sweep voltammetry: a fast and robust approach. In: Voltammetry. London, UK: IntechOpen; 2018. p. 77–90.
- Tong F, Chen X, Teoh TE, et al. Mg–Sn alloys as anodes for magnesium-air batteries. J Electrochem Soc. 2021;168(11):110531. doi: 10.1149/1945-7111/ac3716
- Altun H, Sen S. Studies on the influence of chloride ion concentration and pH on the corrosion and electrochemical behavior of AZ63 magnesium alloy. Mater Design. 2004;25(7):637–643. doi: 10.1016/j.matdes.2004.02.002
- Zhao MC, Liu M, Song GL, et al. Influence of pH and chloride ion concentration on the corrosion of Mg alloy ZE41. Corros Sci. 2008;50(11):3168–3178. doi: 10.1016/j.corsci.2008.08.023
- Chen J, Wei S, Tan L, et al. Effects of solution treatment on mechanical properties and degradation of Mg-2Zn-0.5 Nd-0.5 Zr alloy. Mater Technol. 2019;34(10):592–601. doi: 10.1080/10667857.2019.1603657
- Weaver MR, Maldonado AJ, Banuelos JL, et al. On precipitation hardening behaviour in a triaxial forged Mg-2Zn-2Gd alloy and relationship to mechanical properties. Mater Technol. 2023;38(1):2215038. doi: 10.1080/10667857.2023.2215038
- Wang D, Jing Y, Gao Y, et al. Enhanced mechanical properties of AZ91 magnesium alloy by asynchronously large-strain high-efficiency rolling with bimodal grain structure. J Mater Res Technol. 2023;27:4430–4439. doi: 10.1016/j.jmrt.2023.10.205
- Wang D, Lin B, Jing Y, et al. Deformation mechanism of AZ91 alloy during compression at different temperatures. Mater Test. 2023;65(1):87–93. doi: 10.1515/mt-2022-0239
- Wang D, Jing Y, Lin B, et al. On the structure, mechanical behavior, and deformation mechanism of AZ91 magnesium alloy processed by symmetric and asymmetric rolling. Mater Charact. 2022;194:112444. doi: 10.1016/j.matchar.2022.112444
- Zhuk A, Belyaev G, Borodina T, et al. Magnesium–air battery with increased power using commercial alloy anodes. Energies. 2024;17(2):400. doi: 10.3390/en17020400
- Cheng W, Hao X, Shangguan F, et al. Electrochemical behavior and discharge performance of dilute Mg-Bi-based alloy as an anode for primary Mg-air battery. Mater Charact. 2024;209:113688. doi: 10.1016/j.matchar.2024.113688
- Shi XB, Cheng WL, Yu LF, et al. Electrochemical behaviors and discharge performance of the low-alloyed Mg-Ag alloy as anode for Mg-air battery. Acta Metall Sin. 2024:0–0. doi: 10.11900/0412.1961.2023.00332
- Ding DY, DU YH, Tang MF, et al. Corrosion and discharge behavior of Mg− Zn− Mn− Nd alloys as primary Mg− air batteries anode. Trans Nonferrous Met Soc China. 2023;33(7):2014–2029. doi: 10.1016/S1003-6326(23)66240-5