Abstract
In this study, chitosan flake was micronized in a ball mill to make fine powder. The effects of the milling on properties of chitosan, such as particle size, molecular parameters, bulk density, crystalline structure, color, chemical structure, and solubility, were investigated. Results showed that the volume weight mean diameter (D[Citation4,Citation3]) of chitosan was reduced to 37.53 μm after 8 h of milling and extended milling did not cause a further decrease in particle size. After milling, the viscosity average molecular weight (Mv) of chitosan was decreased, but the degree of acetylation (DD) remained nearly unchanged. The bulk density of chitosan increased with increasing milling time. The crystalline structure of chitosan was destroyed by the milling. The ball-milling treatment deepened the color of chitosan. UV-vis spectra showed that new C=O groups might be formed during the milling process. Further, the micronized powders showed high dissolution rates in simulated gastric juice.
INTRODUCTION
Chitosan is a natural, cationic aminopolysaccharide copolymer of glucosamine and N-acetylglucosamine, obtained by the alkaline, partial deacetylation of chitin, which originates from shells of crustaceans, such as crabs and prawns.[Citation1,Citation2] Due to the unique polycationic nature, chitosan has been proposed for various applications in food, pharmaceutical, and chemical industries.[Citation3]
Chitosan is often modified with chemical, biological, and physical methods to get products with desired properties. Researchers use chemical methods to enhance its anti-bacterial activity[Citation4,Citation5] or to degrade it.[Citation6,Citation7] Biological methods, mainly concerning the enzymolysis of chitosan, are used to depolymerize chitosan to produce low molecular weight chitosan or chitooligosaccharide.[Citation8,Citation9] Nowadays, more and more attention has been paid to physical modifications, including radiation,[Citation10] ultrasonication,[Citation11] electrical treatment,[Citation12] and mechanical ultrafine milling.[Citation13,Citation14]
Ball-milling is one kind of ultrafine milling, which is widely used in the micronization of food materials, such as starch,[Citation15,Citation16] cellulose,[Citation17] and chitosan.[Citation13] The particle size of chitosan powder is of great importance to its biological activities and drug delivery application. It is believed that the particle size of chitosan affects its hypocholesterolemic effect.[Citation18] Fukumori et al.[Citation13] employed a ball mill to decrease the particle size of chitosan, and the aim was to apply the micronized powder as a carrier for drug release.
So far, there are only a few studies reported to micronize chitosan by ball-milling. Recent researches on ball-milling of chitosan are mainly focused on the optimization of process parameters to obtain finer powders, neglecting the changes of physicochemical and structural properties during the milling process. The aim of this study, therefore, was to investigate the effect of the ball-milling treatment on properties of chitosan, including particle size, molecular parameters, bulk density, crystalline structure, color, and chemical structure. The authors' team has been doing research on the biological activities of chitosan, and assumes that the dissolution performance of chitosan in gastric juice might affect these activities. Thus, the solubility of the micronized chitosan was evaluated in simulated gastric juice (0.01 M hydrochloride acid).
MATERIALS AND METHODS
Materials
Flaky chitosan (3–5 mm) was obtained from Nantong Shuanglin Biotechnology Co. Limited (Jiangsu, China). Sodium hydroxide, acetic acid, and hydrochloride acid, of analytical purity, were supplied by Sinopharm Chemical Reagent Co., Ltd. (Shanghai, China).
Ball-Milling Treatment of Chitosan Flakes
The ball-milling treatment in this study was done with a MQ-SY-A High-Energy Nano-mill (Qinhuangdao Taiji Ring Nano-Products Co., Ltd., Hebei, China). Chitosan flakes (15 g) and zirconium oxide balls (8 mm in diameter) were mixed in a volume ratio of 1:1 in a 200-ml stainless steel grinding chamber, whose temperature was maintained below 30°C by cold water recirculation. The grinding operations were done for 2, 4, 6, 8, and 10 h, respectively.
The powder of the control group was prepared by the following method. Flaky chitosan was dissolved in 1% (w/v) acetate acid under magnetic stirring. When chitosan was completely dissolved, the solution was neutralized with 1 M NaOH to pH 8 to precipitate chitosan. The precipitated chitosan was recovered by centrifugation, washed several times with deionized water, and dried by lyophilization. The dried chitosan was milled with an ordinary mill, Swing Type High Speed Mill (Xinnuo Limited Company, Shanghai, China).
Determination of Molecular Weight and Deacetylation Degree
The molecular weight of chitosan was determined using an Ubbelohde viscometer (Sinopharm Chemical Reagent Co., Ltd., Shanghai, China). The intrinsic viscosity (η) of chitosan was measured at 25°C in a 0.2 M NaCl/0.1 M CH3COOH solution. The viscosity average molecular weight (Mv) was calculated using the Mark-Houwink equation: [η] = k(Mv)α, in which the constants k and α were 1.81 × 10−3 cm3·g−1 and 0.93, respectively.[Citation19] The degree of deacetylation (DD) of chitosan was determined by the method of potentiometric titration, as described by Zhou et al.[Citation20] The chitosan sample (0.2 g) was dissolved in 20 ml of 0.1M HCl, and excess HCl was back titrated with 0.1 M NaOH solution using a DELTA-320-S pH meter (Mettler-Toledo, Halstead, UK). The differential and integral titration curves were drawn between solution pH and volume of alkali added, which produced an integral curve with two inflexions. The DD was calculated using the following equation:
Bulk Density
Bulk density of chitosan was determined with the following procedures described by Cho et al.[Citation21] A certain amount of chitosan sample was placed in a 15-ml tapered graduated centrifuge tube, vibrated on a vortex mixer for 1 min, and packed by gently tapping the tube on the benchtop 10 times. The volume of the sample was recorded. The procedure was repeated three times for each sample, and the bulk density was computed as grams per milliliter of the sample.
Particle Size Distribution
Particle size distribution of chitosan powder was determined using the laser scattering method described by Che et al.[Citation22] with minor modifications. The diffractometer used was a Mastersizer 2000 laser diffractometer (Malvern Instrument Co., Southborough, UK) equipped with a He-Ne laser (wavelength 632.8 nm). Before measurement, the chitosan sample was ultrasonically dispersed in alcohol.
Scanning Electron Microscopy (SEM)
The chitosan powder was fixed on a sample bench using a double glue tape for spraying gold powder. The morphological image of the sample was examined using a SEM (Quanta-200, FEI, Eindhoven, The Netherlands).
X-Ray Diffraction
The X-ray diffraction patterns of chitosan samples were measured using a D8 Advance diffractometer (Bruker AXS, Karlsruhe, Germany) under the following conditions: Cu-Kα radiation, 40 kV, 40 mA and measurement range 2θ 3–60°.
Measurement of Color
The color measurement was performed with a CR 400 chromameter (Konica Minolta, Tokyo, Japan). The results were displayed as CIE Lab tristimulus values (L*a*b* color space). L* represents lightness; a* and b* represent redness and yellowness, respectively. The instrument was standardized using a standard white tile (Monilta calibration plate, No. 21733001).[Citation23] Three duplicate measurements were made for each sample.
UV-Vis Spectroscopy
A chitosan sample (0.15 g) was dissolved in 1% (w/v) HCl solution (50 ml) under magnetic stirring. When the chitosan was completely dissolved, the solution was centrifuged at 3000 g for 10 min to remove the insoluble material. UV-vis absorption spectra were obtained using a UV1000 spectrophotometer (Techcomp Ltd., Shanghai, China) at the range of 200–500 nm.
Solubility Test
A dissolution experiment was carried out in simulated gastric juice (0.01 M HCl) at 37°C. The chitosan sample (0.1 g) was added to ionized water (40 ml), and then ultrasonically dispersed for 1 min. Ten milliliters of 0.05 M HCl was added to the dispersion, and at the same time the pH of the dispersion was recorded. The pH of 0.01 M HCl was hypothesized as the pH of chitosan dispersion at the start of dissolution (t = 0). Each test was replicated three times and the mean values were taken.
Statistical Analysis
The test data were statistically analyzed using DPS 7.05 for windows (Zhejiang University, Hangzhou, China). Duncan's t-test was used to compare means at the 5% significance level.
RESULTS AND DISCUSSION
Granule Size and Morphology
The particle size distributions of chitosan powders made from a flaky sample are shown in . The volume average diameter (D[Citation4,Citation3]) of control powder was 155.19 μm, which was similar with some commercial chitosan powders, since these powders could only pass through a 60 or 80 mesh sieve.[Citation21] As shows, the D[Citation4,Citation3] of micronized chitosan was reduced from 128.98 to 37.53 μm when the milling time was increased from 2 to 8 h. After 8 h of treatment, extended milling did not cause a further decrease in particle size. This finding was consistent with Che et al.,[Citation24] whose research material was starch. As they explained, two effects coexisted in the milling process. On one hand, large particles were crushed and divided into small pieces. On the other hand, small particles tended to join together to form large agglomerates. After 8 h of milling, a dynamic equilibrium might be achieved between the two effects. Compared with Fukumori et al.,[Citation13] the particle sizes of the micronized powders in this study seemed to be larger, which might be attributed to the difference in the milling equipment and milling conditions.
Table 1 Particle size distributions of chitosan powders
The granule morphology of the powders with 4 and 8 h of ball-milling are shown in . The particle sizes of the two micronized powders observed from SEM were consistent with the result from Mastersizer 2000 (Malvern Instrument Co., Southborough, UK) (). As can be seen from , the particles were in irregular shape, and a longer time of ball-milling treatment could pulverize more large granules into small pieces.
Physicochemical Parameters
The basic physicochemical properties of different chitosan samples are shown in . The ball-milling treatment did not change DD significantly. The bulk densities of the powders were much higher than that of original chitosan flake, which could be explained by the fact that the powders could pack densely, but vacant places among flakes was larger. The bulk density generally increased with the increase of milling time, which coincided with the changing trend of the particle size.
Table 2 Physicochemical parameters of chitosan samplesFootnote*
As shows, the Mv of original chitosan flake was higher than those of the powdered chitosans. This result suggested that degradation of chitosan molecules occurred during both ball-milling and preparation process of the control group. For control group, the decrease in Mv might be attributed to two main causes: the slow hydrolysis in acetate acid solution and subsequent milling. As previously reported, the ball-milling treatment could result in the degradation of carbohydrate.[Citation16,Citation25] Tamaki et al.[Citation16] investigated the effect of ball-milling treatment on structural change of potato starch, and the result indicated that starch molecules were degraded and the content of amylose increased during milling. Huang et al.[Citation25] also found that when treated with a ball mill, amylose contents of cassava and maize starches increased, and that longer time treatment of milling aggravated this phenomenon. All these literatures suggested that the ball-milling treatment was powerful enough to break the glycoside bond of carbohydrate. As can be seen from , chitosan was severely degraded during ball-milling and the extent of degradation increased with increasing milling time, which was consistent with the research of Huang et al.[Citation25] on starch.
Crystalline Structure
Six polymorphs have been proposed for chitosan: ‘tendon’, ‘annealed’, ‘1–2’, ‘L-2’, ‘form I’, and ‘form II’.[Citation26] shows the X-ray diffraction patterns of chitosan samples. The WAXD of the initial chitosan flake and control powder exhibited three characteristic peaks at 2θ of 10.8, 20.4, and 22.3°, which coincided with the ‘tendon’ polymorph reported previously by Qin et al.[Citation27]
Figure 2 X-ray diffraction patterns of chitosan samples: (a) original chitosan flake; (b) control group; (c–e) denote the samples with 2, 4, and 8 h of ball-milling.
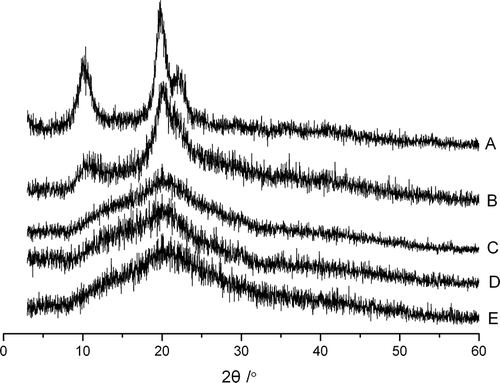
For the micronized powders, halo diffraction patterns were observed, indicating an amorphous state of these powders. Thus, in the ball-milling process, the crystalline structure was destroyed. This was similar with some previous researches about ball-milling of starches and cellulose.[Citation16,Citation17,Citation25] Huang et al.[Citation16,Citation25] found that the treatment of ball-milling changed the crystalline structure of maize, cassava, and potato starches, from polycrystalline states to non-crystalline states. Kocherbitov et al.[Citation17] treated microcrystalline cellulose (MCC) with ball mill, and found that WAXD spectra of the milled MCC consisted of one broad peak and this material was in an amorphous state.
Color
Color is of great importance to the appearance of chitosan product. In the preparing procedure of chitosan, decoloration is always introduced to get a product of bright color.[Citation28 − Citation30] However, the color of this material may get worse during the application or degradation process.[Citation10,Citation30,Citation31] Color L*, a*, and b* values of the chitosan samples are shown in . Compared with original flake, the control powder showed higher L*, suggesting that the combined process of dissolution, freeze-drying and ordinary milling could produce a powder of bright color. However, the L* of micronized powders were lower than that of the control powder and original flake. The dark color of micronized powders might be resulted from browning of chitosan. During the depolymerization process of chitosan, slight browning sometimes happened,[Citation10,Citation31] which might be attributed to the Maillard reaction between amino groups and carbonyl groups of reducing ends. During ball-milling, the degradation of chitosan molecules occurred and the reducing ends increased, so the collision incident between the two groups increased. In the ball-milling process, the particles suffered severe force of extrusion and rubbing from balls and other particles, and therefore collision incident between molecules might be high. As a consequence, browning effect was slightly apparent during ball-milling.
UV-Vis Spectra Analysis
The UV-vis spectra of flaky and powdered chitosan are shown in . Broad absorption between 250 and 300 nm were observed for all the chitosan samples. Based on the data reported in the published literature, the broad absorption could be ascribed to C=O group.[Citation32] It was observed that the absorption intensities of micronized chitosan in this range increased with the increase of milling time. This might be attributed to the degradation of chitosan molecules during milling. Degradation increased the terminals of chitosan, possibly resulting in the increase of C=O groups.
Dissolution Performance
Chitosan is an amino-polysaccharide, and the amino groups will be protonized during dissolution, which may decrease the free H+ ions in solution, leading to an increase in solution pH. Accordingly, the pH change of the solution can judge the dissolution rate to some extent. The changes of solution pH during the dissolution of chitosan samples are shown in . The solution pH of flaky sample increased slowly with the dissolution time, and could not achieve balance in 60 min. The solution pH of the powders rose quickly at the beginning of dissolution, and for micronized powders, the pH stabilized at constant values at the end of dissolution. However, the solution pH of the control powder increased during the whole dissolution process, and the increasing rate gradually decreased. From visual observation, the three micronized powders dissolved quickly after 0.05 M HCl was added into the dispersions, and the final solutions were transparent. However, for control powder, there were still some visible particles after 60 min of dissolution; for flaky chitosan, the majority of large flakes could not dissolve but were only swelled. The results suggested that micronized powders, especially the sample with 8 h of milling, which had the smallest particle size and molecular weight, could dissolve quickly and completely in the simulated gastric juice. Three reasons might account for the high solubility rate of micronized powders. First, the micronized powders had smaller particle sizes and greater specific surface areas compared with the control powder. Amino groups of micronized powders could interact with more H+ ions at the beginning of dissolution. Second, micronized powders were amorphous, so H+ ions and water molecules could easily penetrate into the inner of their granules. Finally, the decrease in chain length could reduce the entanglement degree of chitosan chains, resulting in an increase in chain mobility. Compared with the control group, the micronized chitosans had smaller molecular weights, so it would be easier for their chains to flow from granules into solution during dissolution. As previously reported, chitosan could bind lipid in the gastrointestinal tract, and had hypolipidemic effect.[Citation33,Citation34] The higher dissolution rate of chitosan powder with smaller granularity may be helpful to enhance the biological bioactivity. More work is required to further micronize the granule and test the biological bioactivity of chitosan with different granularity.
CONCLUSIONS
The effects of ball-milling treatment on physicochemical and structural properties of chitosan flake were studied. The flake was micronized to 37.53 μm after 8 h of ball-milling, but further treatment made slight change on particle diameter. The ball-milling treatment resulted in severe degradation of chitosan chains, and the extent of degradation increased with increasing milling time. The crystalline structure of chitosan was destroyed by the milling. The ball-milling treatment deepened the color of chitosan powder. New C=O groups might be formed during the milling process. Besides, the micronization increased the dissolution rates of chitosan in simulated gastric solution. The findings suggest that the ball-milling treatment is an effective method to reduce the particle size of chitosan, and some physicochemical and structural properties will change during the milling process, which may affect its biological activities and deserve to be further researched.
ACKNOWLEDGMENTS
This research was financially supported by the fund for 863 Project (Nos. 2007AA100401 and 2011AA090801), the National Natural Science Funds of China (20876068 and 20571034), the Science and Technology Plan Project of Guangdong Province (No. 2010B090400467), the guidance project of State Key Laboratory of Food Science and Technology (No. SKLF-MB-200805), and the Fund Project for Transformation of Scientific and Technological Achievements of Jiangsu Province (BA2009082).
REFERENCES
- Mahlous , M. , Tahtat , D. , Benamer , S. and Khodja , A.N. 2007 . Gamma irradiation-aided chitin/chitosan extraction from prawn shells . Nuclear Instruments & Methods in Physics Research Section B-Beam Interactions with Materials and Atoms , 265 : 414 – 417 .
- Yen , M.T. , Yang , J.H. and Mau , J.L. 2009 . Physicochemical characterization of chitin and chitosan from crab shells . Carbohydrate Polymers , 75 : 15 – 21 .
- Kumar , M.N.V.R. 2000 . A review of chitin and chitosan applications . Reactive and Functional Polymers , 46 : 1 – 27 .
- Rabea , E.I. , Badawy , M.E.I. , Steurbaut , W. and Stevens , C.V. 2009 . In vitro assessment of N-(benzyl) chitosan derivatives against some plant pathogenic bacteria and fungi . European Polymer Journal , 45 : 237 – 245 .
- Tang , H. , Zhang , P. , Kieft , T.L. , Ryan , S.J. , Baker , S.M. , Wiesmann , W.P. and Rogelj , S. 2010 . Antibacterial action of a novel functionalized chitosan-arginine aginst Gram-negative bacteria . Acta Biomaterialia , 6 : 2562 – 2571 .
- Mao , S.R. , Shuai , X.T. , Unger , F. , Simon , M. , Bi , D.Z. and Kissel , T. 2004 . The depolymerization of chitosan: Effects on physicochemical and biological properties . International Journal of Pharmaceutics , 281 : 45 – 54 .
- Tian , F. , Liu , Y. , Hu , K.A. and Zhao , B.Y. 2004 . Study of the depolymerization behavior of chitosan by hydrogen peroxide . Carbohydrate Polymers , 57 : 31 – 37 .
- Li , J. , Du , Y.M. and Liang , H.B. 2007 . Influence of molecular parameters on the degradation of chitosan by a commercial enzyme . Polymer Degradation and Stability , 92 : 515 – 524 .
- Li , J. , Du , Y.M. , Yang , J.H. , Feng , T. , Li , A.H. and Chen , P. 2005 . Preparation and characterisation of low molecular weight chitosan and chito-oligomers by a commercial enzyme . Polymer Degradation and Stability , 87 : 441 – 448 .
- Choi , W.S. , Ahn , K.J. , Lee , D.W. , Byun , M.W. and Park , H.J. 2002 . Preparation of chitosan oligomers by irradiation . Polymer Degradation and Stability , 78 : 533 – 538 .
- Czechowska-Biskup , R. , Rokita , B. , Lotfy , S. , Ulanski , P. and Rosiak , J.M. 2005 . Degradation of chitosan and starch by 360-kHz ultrasound . Carbohydrate Polymers , 60 : 175 – 184 .
- Luo , W.B. , Han , Z. , Zeng , X.A. and Yu , S.J. 2010 . Study on the degradation of chitosan by pulsed electric fields treatment . Innovative Food Science and Emerging Technologies , 11 : 587 – 591 .
- Fukumori , Y. , Tamura , H. , Miyamoto , K.M. , Tokumitsu , H. , Ichikawa , H. and Block , L.H. 1998 . Dry grinding of chitosan powder by a planetary ball mill . Advanced Powder Technology , 9 : 281 – 292 .
- Seo , M.H. , Lee , S.Y. , Chang , Y.H. and Kwak , H.S. 2009 . Physicochemical, microbial, and sensory properties of yogurt supplemented with nanopowdered chitosan during storage . Journal of Dairy Science , 92 : 5907 – 5916 .
- Huang , Z.Q. , Xie , X.L. , Chen , Y. , Lu , J.P. and Tong , Z.F. 2008 . Ball-milling treatment effect on physicochemical properties and features for cassava and maize starches . Comptes Rendus Chimie , 11 : 73 – 79 .
- Tamaki , S. , Hisamatsu , M. , Teranishi , K. and Yamada , T. 1997 . Structural change of potato starch granules by ball-mill treatment . Starch/Stärke , 49 : 431 – 488 .
- Kocherbitov , V. , Ulvenlund , S. , Kober , M. , Jarring , K. and Arnebrant , T. 2008 . Hydration of microcrystalline cellulose and milled cellulose studied by sorption calorimetry . Journal of Physical Chemistry B , 112 : 3728 – 3734 .
- Xia , W.S. , Liu , P. , Zhang , J.L. and Chen , J. 2011 . Biological activities of chitosan and chitooligosaccharides . Food Hydrocolloids , 25 : 170 – 179 .
- No , H.K. , Park , N.Y. , Lee , S.H. and Meyers , S.P. 2002 . Antibacterial activity of chitosans and chitosan oligomers with different molecular weights . International Journal of Food Microbiology , 74 : 65 – 72 .
- Zhou , H.Y. , Chen , X.G. , Kong , M. , Liu , C.S. , Cha , D.S. and Kennedy , J.F. 2008 . Effect of molecular weight and degree of chitosan deacetylation on the preparation and characteristics of chitosan thermosensitive hydrogel as a delivery system . Carbohydrate Polymers , 73 : 265 – 273 .
- Cho , Y.I. , No , H.K. and Meyers , S.P. 1998 . Physicochemical characteristics and functional properties of various commercial chitin and chitosan products . Journal of Agricultural and Food Chemistry , 46 : 3839 – 3843 .
- Che , L.M. , Li , D. , Wang , L.J. , Özkan , N. , Chen , X.D. and Mao , Z.H. 2007 . Effect of high-pressure homogenization on the structure of cassava starch . International Journal of Food Properties , 10 : 911 – 922 .
- Tarakci , Z. , Temiz , H. , Aykut , U. and Turhan , S. 2011 . Influence of wild garlic on color, free fatty acids, and chemical and sensory properties of herby pickled cheese . International Journal of Food Properties , 14 : 287 – 299 .
- Che , L.M. , Li , D. , Wang , L.J. , Chen , X.D. and Mao , Z.H. 2007 . Micronization and hydrophobic modification of cassava starch . International Journal of Food Properties , 10 : 527 – 536 .
- Huang , Z.Q. , Lu , J.P. , Li , X.H. and Tong , Z.F. 2007 . Effect of mechanical activation on physico-chemical properties and structure of cassava starch . Carbohydrate Polymers , 68 : 128 – 135 .
- Cervera , M.F. , Heinamaki , J. , Rasanen , M. , Maunu , S.L. , Karjalainen , M. , Acosta , O.M.N. , Colarte , A.I. and Yliruusi , J. 2004 . Solid-state characterization of chitosans derived from lobster chitin . Carbohydrate Polymers , 58 ( 4 ) : 401 – 408 .
- Qin , C.Q. , Du , Y.M. and Xiao , L. 2002 . Effect of hydrogen peroxide treatment on the molecular weight and structure of chitosan . Polymer Degradation and Stability , 76 : 211 – 218 .
- Youn , D.K. , No , H.K. and Prinyawiwatkul , W. 2007 . Physical characteristics of decolorized chitosan as affected by sun drying during chitosan preparation . Carbohydrate Polymers , 69 : 707 – 712 .
- Youn , D.K. , No , H.K. , Kim , D.S. and Prinyawiwatkul , W. 2008 . Decoloration of chitosan by UV irradiation . Carbohydrate Polymers , 73 : 384 – 389 .
- Srinivasa , P.C. , Ramesh , M.N. , Kumar , K.R. and Tharanathan , R.N. 2004 . Properties of chitosan films prepared under different drying conditions . Journal of Food Engineering , 63 : 79 – 85 .
- Zainol , I. , Akil , H.M. and Mastor , A. 2009 . Effect of gamma-irradiation on the physical and mechanical properties of chitosan powder . Materials Science & Engineering C-Biomimetic and Supramolecular Systems , 29 : 292 – 297 .
- Cai , Q.Y. , Gu , Z.M. , Chen , Y. , Han , W.Q. , Fu , T.M. , Song , H.C. and Li , F.S. 2010 . Degradation of chitosan by an electrochemical process . Carbohydrate Polymers , 79 : 783 – 785 .
- Zhang , J. , Liu , J.N. , Li , L. and Xia , W. 2008 . Dietary chitosan improves hypercholesterolemia in rats fed high-fat diets . Nutrition Research , 28 : 383 – 390 .
- Liu , J. , Zhang , J. and Xia , W. 2008 . Hypocholesterolaemic effects of different chitosan samples in vitro and in vivo . Food Chemistry , 107 : 419 – 425 .