Abstract
In food process simulation studies, geometrical characterization of agricultural produce is extremely difficult due to their irregular shapes. Further simplifications and assumptions can be applied to overcome this problem. Also, applying 3D scanners may easily and realistically lead to more accurate results from simulations. The aim of this work was to study this discrepancy in the obtained values of the elastic parameters of organic materials under a compression case using a finite element method and experimental data. The Zaria variety of pumpkin seed was chosen as a typical sample of an organic material. A 3D scanner, high speed camera, and simulations using a finite element method were used to investigate modulus of elasticity, force, energy, and stress distribution of the pumpkin seed under the condition of parallel plate compression. The results of a compression test were used as experimental analysis. The force/deformation curve generated by the finite element method modeling matched the curve from the experimental test remarkably well up to 0.9 mm combined deformation and showed that the finite element method can be used to describe accurately mechanical behavior of pumpkin seed under compression.
INTRODUCTION
Knowing different properties of agricultural produce is necessary to carry out a good design for harvesting and processing equipment. The obtained knowledge can also be used to avoid conducting any destructive tests, such as a compression test for evaluation of the quality of produce. Many researchers have shown that the quality of the agricultural produce could be determined by their internal and external characteristics. These characteristics can be presented as size, shape, smell, appearance, produce presentation, and texture.[Citation1–Citation3] On the other hand, the subject of mechanical damage has a significant effect on the quality of agricultural produce. Mechanical damage mostly occurs during harvesting, handling, transportation, and storage. In addition to mechanical effects, agricultural produce may be influenced by thermal, electrical, optical, and acoustical effects during various processes.[Citation4] The damage imposed can contribute to decreasing quality of the produce through biological degradation, such as rotting. Therefore, prediction of the level of damage, stress distribution, and deformation of the organic material under the external forces has become a very important subject.
In fact, it is very difficult to measure internal stresses, which are caused by mechanical effects, due to the biological cell structure of fruit and vegetables. Numerical methods can be utilized as an alternative solution for prediction of the stresses. Analytical methods for stress investigations are available today only for a few simple cases, and so their applications are limited. Available technology, the proliferation of computers and software, allows engineers to solve complicated problems using computer aided design (CAD) technology and numerical methods in a virtual way without committing to physical manufacture and testing.[Citation5] The practical cases occurring in agricultural engineering mostly represent complex problems, which may be solved only by numerical methods.[Citation6] One of these approaches is to estimate the stress field of organic materials using a finite element method (FEM).[Citation7] FEM is a numerical procedure that can be used to obtain solutions for complicated or large-scale engineering problems involving stress analysis, heat transfer, electromagnetism, and fluid flow. The method has been improved since the 1950s, and during the 1960s investigators began to apply FEM to other disciplines of engineering.[Citation8]
Studies relating to the use of FEM applications for postharvest modeling and estimation of stress distributions in fruits and vegetables are abundant in the literature. Cardenas-Weber et al.[Citation7] applied FEM to estimate both deformations and stresses with application to robot gripping. They concluded that finite element analysis can predict the stresses better than the Hertz contact model. Jancsok[Citation9] developed a complex geometrical modeling system based on computer vision taking the natural variability of the products into account so that the shape of different agricultural materials for finite element modeling purposes can be described. Rong et al.[Citation10] simplified grape as a spherical isotropic solid with two kinds of materials. They assumed the materials of both the skin and the flesh tissue to be isotropic, homogeneous, and linear. Their FEM simulation confirmed the experimental results. Kafashan et al.[Citation11] developed a new method to model fruit geometry using image processing, which can be implemented in FEM domains. Hernandez and Belles[Citation12] developed a 3D finite element model of the sunflower. They noted that the simulated patterns of failure closely agree with those observed after compressive loading on fruits.
Also, several studies have appeared in the scientific literature on modal analysis of fruits using the finite element method.[Citation13–Citation18] These studies show that FEM can be a suitable method for calculating some of the properties and behavior of the organic materials. The aim of this study is to understand the mechanical behavior of a pumpkin seed, such as modulus of elasticity, force, energy, and to analyze stress distribution of whole pumpkin seed under the condition of parallel plate compression utilizing FEM simulations and visual investigations. In the study, a 3D solid model of the pumpkin seed was created by using a 3D scanner and 3D parametric solid modeling software. The accuracy of the obtained results was investigated by applying experimental data.
THREE-DIMENSIONAL SOLID MODELING OF THE PUMPKIN SEED
Owing to the complex shape of most agricultural produce and their associated complex structure, the determination of reliable elastic parameters present a number of problems. Three-dimensional (3D) scanners can be utilized as an alternative solution. A 3D scanner can be described as a device to analyze an object for collecting data on its shape and possibly its appearance (i.e., color). Collected data can then be used to construct digital 3D models and can be solved by numerical methods for a wide variety of applications including food processing. As such, a 3D scanner (NextEngine’s Desktop 3D Scanner, NextEngine Company, USA) was used for generating a surface model of the pumpkin seed. Then the surface model was processed into a 3D solid model using Solidworks 3D parametric solid modeling software. The 3D solid model and mesh construction of the pumpkin seed are presented in .
MATERIALS AND METHODS
Material
The Zaira variety as one of the common varieties of pumpkin seed was selected for this research work. This cultivar was obtained randomly from Kvardeh village of Khorasan Razavi province, Iran, during the autumn season in 2011. Twenty seeds of pumpkin were randomly selected. These seeds were utilized for uniaxial compression tests with a parallel plate compression tool. The seeds were manually cleaned to remove all foreign matters, such as dust, dirt, stones, immature and broken seeds. The initial moisture content of seeds were determined to be 8% d.b. using the standard hot air oven method with a temperature setting of 105 ± 1°C for 24 h.[Citation19−Citation21] Before conducting compression tests, the geometry of each seed was measured by digital caliper (Diamond, China) with an accuracy of ±0.02 mm. The volume and density of each seed were determined from the measurements of mass and buoyancy force.
Nonlinear Analysis and FEM Simulation
Nonlinear structural behavior arises from a number of causes, which can be grouped into the following principal categories: changing status, geometric nonlinearities, and material nonlinearities. While a pumpkin seed was compressed by loading plates, a rigid-to-flexible contact problem takes place between the seed and the plates. In general, contact forms are distinctive and important subsets of the category of changing-status nonlinearities. Geometric nonlinearities occur, for example, when a structure experiences large deformations, such that its changing geometric configuration can cause it to respond nonlinearly. Material nonlinearities arise due to nonlinear stress–strain relationships of the particular material.[Citation22] In this research, the changing status and geometric nonlinearities were considered in the nonlinear analysis of pumpkin seed compression. For the analysis described in this article, normal strains and equivalent stresses were calculated. The normal strain is the normalized deformation in a direction perpendicular to the surface of the object. Equivalent stresses are functions of the three principal stresses: r1, r2, and r3. The principal stresses act on the perpendicular planes, which have no shear stresses. The equivalent stress can be calculated from the principal stresses according to the following equation:[Citation23]
The concept of equivalent stress has been routinely used in failure analysis of ductile engineering materials. Liu[Citation24], Irudayaraj,[Citation25] and Cardenas-Weber et al.[Citation7] have proposed that it can be applied to agriculture materials. The equivalent stress analysis gives predictions, which follow the Von Mises criteria for failure. In fact, Von Mises stress (equivalent stress) is a scalar function of the components of the stress tensor that gives an appropriate overall magnitude of the tensor. This allows the onset and amount of failure under triaxial loading to be predicted from the results of a sample uniaxial compression test.
The finite element analysis of the whole pumpkin seed compression was conducted using the commercial finite element software Solidworks.[Citation26] The program offers a wide range of options regarding element types, material behavior, and numerical solution controls, as well as nonlinear analysis and sophisticated postprocessors. A model for pumpkin seed consisting of a total of 6855 elements (tetrahedral elements) was made (). Each element node had three degrees of freedom to facilitate translational deformations with respect to the three axes. The skin model of pumpkin seed was assumed to have homogeneous text with the same properties. To simulate the condition of the actual compression test, contact pairs were formulated using rigid target elements for the upper and lower plates and contact elements for the model of pumpkin seed.
Augmented Lagrangian function was utilized as a contact condition, and Gauss points were utilized to detect the locations of contact points.[Citation26] The horizontal movement of nodes in upper and lower layers (i.e., the initial contact points between the compression device and produce) was assumed to be zero. It prevents the translational motion of the model of pumpkin seed under applied load because of the geometry of produce. The FEM simulation was based on static-displacement control including gravity force, and nonlinear geometry was utilized to analyze mechanical behavior. To determine the modulus of elasticity of each model of pumpkin seed by FEM simulation, its value was continuously adjusted until the difference between the reaction forces obtained by the actual compression test and FEM simulation fell below 1%. A fixed value of 0.307 was utilized for the Poisson’s ratio of the pumpkin seed model.[Citation27] As already stated above, stress distribution within each model of pumpkin seed was analyzed at the same loading condition by using Von Mises stress.[Citation28] Finally, the results of the FEM model analysis were compared to the experimental data. Comparisons were made for force–deformation data.
Uniaxial Compression Test
Quasi-static compression tests were performed with a Universal Testing Machine (Model H5KS, Tinius Olsen Company) equipped with a 500 N compression load cell (). Each individual seed was loaded between two parallel plates () and compressed at a fixed crosshead speed of 2.0 mm/min until the hull ruptured.[Citation1] It was assumed that rupture occurred at the bio-yield point, which is the point in the force–deformation curve, where there is a sudden drop in force. As soon as the bio-yield point was detected, the compression test was stopped. Many researchers have used this method to determine the bio-yield point of agricultural produce.[Citation1,Citation3,Citation4,Citation29] The absorbed energy by the sample at the rupture point and sample deformation was directly displayed by the instrument. The absorbed energy was determined by calculating the area under the force–deformation curve up to the rupture point.
Validation of the FEM Model and Its Sensitivity to Determine Mechanical Behavior of Pumpkin Seed
In order to check the validity of the FEM model, the force/deformation (F/D) curve generated from the FEM modeling was analyzed and compared to the results of the compression test. Then, to ensure the sensitivity of the model to the determined mechanical behavior of the pumpkin seed, the experimental data of the compression test were compared with the corresponding obtained FEM values for studied variety of pumpkin seed using XY scatter plots. The models were considered validated if the following criteria were satisfied:
The intercept of the linear regression analysis between the modeled and experimental results should be almost zero.
The coefficient of linear regression analysis between the modeled and experimental results should be almost unity.
The correlation coefficient between the modeled and experimental values should be statistically significant.
Elastic Analysis Based on the ASAE Standard
To investigate the results of FEM analysis with the values obtained by experimental data of applying the ASAE standard for loading geometrics of a single plate in contact with a curved surface such as in this study, the following two equations were utilized to determine apparent modulus of elasticity and the maximum normal contact stress:[Citation30]
KU is a constant determined from after calculating cosθ (Eq. 6) using the radii of curvature of the sample, RU and R’U. Smax is the maximum normal contact stress; C1 and C2 are constants related to the contact area. The values of C1 and C2 were also determined from by linear interpolation after finding the values of cosθ from Eq. (3) at the points of contact with upper and lower plates.[Citation30]
TABLE 1 Values of C1, C2, and KU (dimensionless) for various values of θ (degrees)[Citation30]
RESULTS AND DISCUSSION
Results of the Validation of the FEM Model and the Investigation on the Sensitivity of the Model
Using a FEM model to predict the mechanical behavior of an agricultural produce instead of conducting destructive tests always is a matter of interest for researchers. To illustrate this shape-based comparison, the FEM model was validated by comparing the force/deformation (F/D) curve generated from the FEM modeling with that obtained from the compression test on the pumpkin seed. The F/D curve generated by the FEM modeling matched the curve from the experimental test remarkably well up to 0.9 mm combined deformation (). As the load further increased, the difference between the FEM-modeled and experimental F/D curves started to increase. At the bio-yield point, the FEM-modeled displacement was about 15% greater than that from the experiment. This relatively big difference at large displacement was likely due to the increasingly nonlinear behavior of the produce. Overall, the FEM model well described the mechanical response of the pumpkin seed under contact loading.
FIGURE 3 (A) Comparison of the finite element modeling results with the experimentally measured force/deformation curves for pumpkin seed. (B) Experimental versus predicted values of force (N).
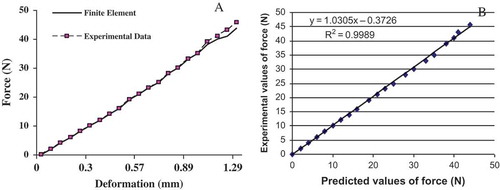
As already stated above, to achieve satisfied results the sensitivity of the model was checked using XY scatter plots between experimental and predicted results (). A difference of +0.03 with unity was observed for regression coefficients. The resulted value of 0.37, which is close to zero for the intercepts of the regression lines, was obtained. Also, a resulted correlation coefficient of 0.99 proved the validity of the studied model. The FEM analysis showed that when pumpkin seed was subjected to contact loading, the normal stress was dominant in comparison with the shear stress. Hence, it is reasonable to expect that normal stress is primarily responsible for the bio-yield failure of pumpkin seed tissues. In the following paragraphs, the FEM modeling results are comprehensively discussed.
Evaluation of Force, Deformation, and Energy
After completing the FEM pre-processor operations, a solving operation was generated. The deformation behavior, energy, and reaction forces of the pumpkin seed were obtained for each sample. The reaction force and energy obtained by FEM simulation were compared to those of the experiment in . As anticipated, the difference in reaction force between FEM simulation and experiment was less than 1% target value. Furthermore, the energy that was continuously calculated by integrating the F-D curves obtained by FEM simulation was 0.16% larger than that of the experiment on average. These small discrepancies in the reaction force and energy would demonstrate the validity of the FEM simulation method to determine modulus of elasticity and to analyze stress distribution within whole pumpkin seed. According to the FEM simulation results, the maximum energy of 10.12 MJ and maximum reaction force of 46.7 N occurred in sample 1.
TABLE 2 The results of reaction force (F) and energy (W) for FEM simulation and experimental data (Exp)
Modulus of Elasticity
As shown in , when the experimental data was utilized, the apparent elastic modulus ranged from 52.79 to 70.99 MPa for actual pumpkin seeds. The elastic modulus determined by FEM simulation ranged from 54.23 to 57.51 MPa, 7% smaller on the average than the apparent elastic modulus of actual pumpkin seeds by compression tests. This confirms the reliability of the FEM geometry model notwithstanding the relatively large discrepancies in the radius of curvature from actual pumpkin seeds. The correlation coefficient between the results of the two methods was 0.46. It is normal in elastic mechanical behavior that as geometry volume and contact surface of compressive elastic materials increase, the modulus of elasticity decreases accordingly under the same condition of reaction force and Poisson’s ratio. Thus, the results of poor linear correlation in elastic modulus between FEM simulation and experiments might be strongly influenced by the upper and lower contact volumes and existing many irregular surface curvatures, which were not considered in the ASAE standard (Eq. 1).
TABLE 3 Comparison of elastic modulus between experimental data (Exp) and FEM simulation
Stress Evaluation
shows the maximum contact stresses at initial contact points evaluated by the experimental data of Eq. (3) and the Von Mises stress evaluated by FEM simulation at a loading condition.[Citation26,Citation28,Citation34] The maximum contact stress averaged 341.14 kPa at the contact point. The effect of surface curvature at contact points was well reflected in the values of maximum contact stress. On the other hand, the average Von Mises stress of FEM simulation at the contact point was 335.02 kPa. Unlike the maximum contact stress by the ASAE standard based on the maximum and minimum radii of surface curvature at a contact point, the maximum Von Mises stress was influenced by the gravity effect and the geometry of the pumpkin seed, including curvatures in all directions at measuring points and contact points. As a result, the correlation between the maximum contact stress and the maximum Von Mises stress was satisfactory (r = 0.88).
CONCLUSION
Investigation of the behavior of organic material, which is under loading case, is mostly difficult. Trying to visually understand this behavior like other engineering phenomenon is almost impossible. Simulation of the behavior of organic material with a complex structure can allow researchers to visually examine the behavior of organic produce under loading case. According to this research, some concluding points can be presented as follows: (i) Through FEM simulation on four model pumpkin seeds resembling the shape of actual counterparts by 3D digitization, the average elastic modulus of 55.93 MPa was obtained. This average value was 20% smaller than the average apparent modulus of elasticity predicted by applying a compression test to the actual pumpkin seeds under the same loading condition. (ii) The maximum Von Mises stress at the point of contact with the compression device evaluated by FEM simulation was about 36% smaller than the maximum contact stress determined by the compression test, showing very poor linear correlation between results of the two methods. (iii) Based on the results of the research, we propose that the generally accepted protocol of ASAE standard S368.4 for compression test of food materials of convex shape needs further study for its appropriateness in predicting the modulus of elasticity. Finally, to investigate different orientated compression tests, the simulation parameters can be redefined by researchers and results can be interpreted visually if preferred. Besides, as the previous studies highlighted, it should not be ignored that the simulation results and bruise susceptibility change not only depend on mechanical properties, but also depend on humidity, harvest time, and pumpkin seed variety.
FUNDING
The authors would like to thank Ferdowsi University of Mashhad for providing financial support and the laboratory facilities for this work.
REFERENCES
- Khodabakhshian, R.; Emadi, B.; Abbaspour Fard, M.H.; Saiedirad, M.H. The effect of variety, size and moisture content of sunflower seed and its kernel on their terminal velocity, drag coefficient and Reynold’s number. International Journal of Food Properties 2012, 15, 262–273.
- Emadi, B.; Kosse, V.; Yarlagadda, P. Mechanical properties of melon measured by compression, shear and cutting modes. International Journal of Food Properties 2009, 12, 780–790.
- Saiedirad, M.H.; Tabatabaeefar, A.; Borghei, A. Effect of moisture content, seed size, loading rate and seed orientation on force and energy required for fracturing cumin seed under quasi-static loading. Journal of Food Engineering 2008, 86, 565–572.
- Mohsenin, N.N. Physical Properties of Plant and Animal Materials, 2nd Revised and Updated Edition; Gordon and Breach Science Publishers: New York, 1986.
- Topakci, M.; Celik, H.K.; Canakci, M.; Rennie, A.E.W.; Akinci, I.; Karayel, D. Deep tillage tool optimization by means of finite element method: Case study for a subsoiler tine. Journal of Food Agriculture and Environment 2010, 8, 531–536.
- Sitkei, G. Mechanics of Agricultural Materials; Elsevier Science Publisher: Budapest, Hungary, 1986.
- Cardenas-Weber, M.; Storoshine, R.L.; Haghighi, K.; Edan, Y. Melon material properties and finite element analysis of melon compression with application to robot gripping. Transaction of ASAE 1991, 34, 920–929.
- Moaveni, S. Finite Element Analysis; Prentice Hall Publication: New Jersey, USA, 1991.
- Jancsok, P.T. Geometrical model generation for finite element meshes of biological products based on digital image processing. Ph.D. Thesis, Faculty of Agricultural and Applied Biological Sciences, Katholeike University: Leuven, Belgium, 1999.
- Rong, W.; Qunying, J.; Deqiang, W. On the mechanical damage of grape using finite element analysis. ASAE/CSAE Annual International Meeting; Ottawa, Canada, August 1–4, 2004.
- Kafashan, J.; Tijskens, B.; Moshou, D.; Bravo, C.; De Baerdemaeker, J.; Ramon, H. A new method to model a 3D shape of biomaterials for using in post-harvest modelling. In: Proceedings of 4th IFAC/CIGR Workshop: Control Applications in Post-Harvest and Processing Technology (CAPPT2006), Issue 55; Bornimer Agrartechnische Berichte: Potsdam, Germany, 2006; 223–229.
- Hernandez, L.F.; Belles, P.M. A 3-D finite element analysis of the sunflower (Helianthus annuus L.) fruit. Biomechanical approach for the improvement of its hullability. Journal of Food Engineering 2007, 78, 861–869.
- Chen, H.; De Baerdemaeker, J.; Bellon, V. Finite element study of the melon for nondestructive sensing of firmness. Transaction of ASAE 1996, 39, 1057–1065.
- Jancsok, P.T.; Clijmans, L.; Nicolai, B.M.; De Baerdemaeker, J. Investigation of the effect of shape on the acoustic response of ‘conference’ pears by finite element modeling. Postharvest Biology and Technology 2001, 23, 1–12.
- Areias, P.M.A.; Belytschko, T. A comment on the article “A finite element method for simulation of strong and weak discontinuities in solid mechanics” by A. Hansbo and P. Hansbo. Computer Methods in Applied Mechanics and Engineering 2004, 195, 1275–1276.
- Nourain, J.; Ying, Y.B.; Wang, J.P.; Rao, X.Q.; Yu, C.G. Firmness evaluation of melon using its vibration characteristic and finite element analysis. Journal of Zhejiang University Science 2005, 6B, 483–490.
- Sadrnia, H.; Rajabipour, A.; Jafari, A.; Javadi, A.; Mostofi, Y.; Kafashan J.; Dintwa, E.; De Baerdemaeker, J. Internal bruising prediction in watermelon compression using nonlinear models. Journal of Food Engineering 2008, 86, 272–280.
- Petru, M.; Novak, O.; Herak, D.; Simanjuntak, S. Finite element method model of the mechanical behaviour of Jatropha curcas L. seed under compression loading. Biosystem Engineering 2012, 40, 412–421.
- Altuntas, E.; Yildiz, M. Effect of moisture content on some physical and mechanical properties of faba bean (Vicia faba L.) grains. Journal of Food Engineering 2007, 78, 174–183.
- Coskun, M.B.; Yalcin, I.; Ozarslan, C. Physical properties of sweet corn seed (Zea mays saccharata Sturt.). Journal of Food Engineering 2005, 74, 523–528.
- Khodabakhshian, R.; Emadi, B.; Abbaspour Fard, M.H. Some engineering properties of sunflower seed and its kernel. Journal of Agricultural Science and Technology 2010, 4, 37–46.
- Belytschko, T.; Liu, W.K.; Moran, B. Nonlinear Finite Elements for Continua and Structures; John Wiley and Sons Inc.: Michigan, USA, 2000.
- Beer, F.P.; Johnston, E.R. Mechanics of Materials; McGraw-Hill: New Jersey, USA, 1985.
- Liu, M. Mechanical properties of soybean during processing. M.S. Thesis, Agricultural Engineering Department, Purdue University: West Lafayette, Indiana, 1989.
- Irudayaraj, J. Finite element simulation of viscoelastic biomaterial behavior during drying. Ph.D. Thesis, Agricultural Engineering Department, Prudue University: West Lafayette, Indiana, 1990.
- CosmosWorks Product Document. Training Manual, Document Number PMT0181-ENG, 2007.
- Khodabakhshian, R. Poisson’s ratio of pumpkin seeds and their kernels as a function of variety, size, moisture content and loading rate. Commission of Agricultural and Biosystems Engineering (CIGR) 2012, 14, 203–209.
- Walter, D. Formulars for Stress, Strain, and Structural Matrices; John Wiley and Sons Inc.: Michigan, USA, 1994.
- Gupta, R.K.; Das, S.K. Fracture resistance of sunflower seed and kernel to compressive loading. Journal of Food Engineering 2000, 46, 1–8.
- ASAE. Standard S368.4: Compression test of food materials of convex shape. In: ASAE Standards; American Society of Agricultural and Biological Engineers, Chicago, Illinois, 2003; 585–592.
- Shelef, L.; Mohsenin, N.N. Evaluation of the modulus of elasticity of wheat grains. Cereal Chemistry 1967, 44, 392–402.
- Yoshizaki, S.; Miyahara, Y. Husking properties of rough rice grain (I)—Husking properties by pseudo-static friction force. Journal of Japanese Society of Agricultural Machinery 1984, 46, 309–315.
- Shitanda, D.; Niishiyama, Y.; Koide, S. Husking characteristics of short and long grain rice by rubber roll husker. XIV CIGR World Congress; Tsukuba, Japan, 2000.
- Kim, G.W.; Kim, M.S.; Sagara, Y.; Bae, Y.; Lee, I.-B.; Do, G.S.; Lee, S.H.; Kang, S. Determination of the viscoelastic properties of apple flesh under quasi-static compression based on finite element method optimization. Food Science and Technology Research 2008, 14, 221–231.