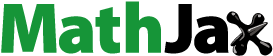
ABSTRACT
Sulfur dioxide (SO2) is one of the main air pollutants from many industries. Most coal-fired power plants in China use wet flue gas desulfurization (WFGD) as the main method for SO2 removal. Presently, the operating of WFGD lacks accurate modeling method to predict outlet concentration, let alone optimization method. As a result, operating parameters and running status of WFGD are adjusted based on the experience of the experts, which brings about the possibility of material waste and excessive emissions. In this paper, a novel WFGD model combining a mathematical model and an artificial neural network (ANN) was developed to forecast SO2 emissions. Operation data from a 1000-MW coal-fired unit was collected and divided into two separated sets for model training and validation. The hybrid model consisting a mechanism model and a 9-input ANN had the best performance on both training and validation sets in terms of RMSE (root mean square error) and MRE (mean relative error) and was chosen as the model used in optimization. A comprehensive cost model of WFGD was also constructed to estimate real-time operation cost. Based on the hybrid WFGD model and cost model, a particle swarm optimization (PSO)-based solver was designed to derive the cost-effective set points under different operation conditions. The optimization results demonstrated that the optimized operating parameters could effectively keep the SO2 emissions within the standard, whereas the SO2 emissions was decreased by 30.79% with less than 2% increase of total operating cost.
Implications: Sulfur dioxide (SO2) is one of the main pollutants generated during coal combustion in power plants, and wet flue gas desulfurization (WFGD) is the main facility for SO2 removal. A hybrid model combining SO2 removal mathematical model with data-driven model achieves more accurate prediction of outlet concentration. Particle swarm optimization with a penalty function efficiently solves the optimization problem of WFGD subject to operation cost under multiple operation conditions. The proposed model and optimization method is able to direct the optimized operation of WFGD with enhanced emission and economic performance.
Introduction
Sulfur dioxide (SO2) is one of the major pollutants contributing to frequent hazy weather in China. A large amount of SO2 in the atmosphere comes from coal combustion. As the amount of coal for power generation accounts for 45% of the total coal consumption in 2015 (National Bureau of Statistics [NBS] Citation2017), the Chinese government has specified the importance of pollutant emissions of coal-fired power plants and emission limits have been tightened (Ministry of Environmental Protection of PRC Citation2011). Owing to the advantages such as a high desulfurization efficiency and proper adaptation to various types of coal, wet flue gas desulfurization (WFGD) has been widely adopted. More than 80% of the power plants in China are using WFGD as their main method for desulfurization (Wang and Hao Citation2012).
In the flue gas treatment systems in coal-fired power plants, WFGD systems are commonly installed downstream of the electrostatic precipitators (Sui et al. Citation2016) and the pressure charging fans, operating at positive pressure. Exhaust flue gas enters the WFGD system from the entrance, which is located at the lower part of the tower. The exhaust gas comes into mass transfer and chemical reactions in countercurrent mode with the limestone slurry droplets, which are introduced through injection nozzles of three to five spray stages in the higher part of the tower. SO2 in the flue gas is absorbed by slurry droplets, reacts with calcium carbonate (CaCO3), and produces CaCO3, which is oxidized to calcium sulfate (CaSO4) before crystallized into gypsum and separated from the slurry.
Aimed at enhanced environmental and economic performance of WFGD, modeling and optimization of SO2 removal in WFGD has been a subject of research in recent years. Mathematical models of WFGD, basing on the microlevel mass transfer theories, including penetration theory (Brogren and Karlsson Citation1997), surface renewal theory (Gerbec, Stergarsek, and Kocjancic Citation1995; Zhong et al. Citation2008), stagnant-film theory (Warych and Szymanowski Citation2001, Citation2002), and two-film theory (Dou et al. Citation2009; Kallinikos et al. Citation2010; Neveux and Le Moullec Citation2011; Zhu et al. Citation2015b), and reaction kinetics, including chemical absorption (Neveux and Le Moullec Citation2011), gypsum conversion (Tan et al. Citation2017), and limestone dissolution (Carletti et al. Citation2015), have been comprehensively studied and shown good agreement with experimental and industrial results. At the same time, data-driven models, based on the large amount of operating data and machine learning platforms, are also generated using various methods such as artificial neural networks (ANNs) (Ren, Sun, and Deng Citation2012; Warych and Szymanowski Citation2002) and regression analysis (Hou, Bai, and Yin Citation2013), results of which have shown a good forecasting performance.
However, because the mathematical models are typically built under the assumption of normal conditions, prediction accuracy is limited, which made it difficult to adapt to environmental changes and equipment aging. And the generalization ability of data-driven models are limited by the training data range, resulting in the decline of forecast ability when the working conditions exceed the training range. For the combined ability of adaptation and generalization, hybrid models have been put forward and applied to the modeling of distillation process (Chen et al. Citation2004), polyethylene production (Hinchliffe et al. Citation2003), fuel cells (Ou and Achenie Citation2005), and batch polymerization reactor (Yuan, Jie, and Morris Citation2001) with enhanced prediction performance, but the utilization of hybrid model on WFGD has been rarely studied.
Economy is also an important concern of WFGD operation. Researchers have made efforts to optimize WFGD on scrubber structure modification (Brown, Kalata, and Schick Citation2014; Li et al. Citation2015; Zhu et al. Citation2015a) and operating parameter tuning (Liu and Yu Citation2012; Liu et al. Citation2012; Wang et al. Citation2010). The control system has also been improved to guarantee stability of the desulfurization process (Villanueva Perales et al. Citation2010, Citation2009; Wu, Shen, and Zhang Citation2011). Besides, sensitivity analysis has been implemented (Liu et al. Citation2011), and factors influencing the desulfurization performance have been explored by means of numerical calculation (Qian et al. Citation2011; Yang et al. Citation2015; Zhong et al. Citation2008) as well as response surface methodology (Zhao, Jin, and Zhong Citation2007). SO2 removal performance of WFGD has been significantly improved. In the view of the cost aspect, however, limited study was carried out. To enhance the cost-effectiveness of industrial processes, metaheuristic global optimization algorithms have been widely used in the optimization of various fields such as power system (Ahmadi, Beromi, and Soleymanpour Citation2016; Chen et al. Citation2016, Citation2014), manufacturing (Colla et al. Citation2016; Kramar et al. Citation2016), automatic control (Chang and Chen Citation2014; Huang and Li Citation2014), etc., which provided successful experience to the optimization of WFGD.
In this paper, different forms of prediction models are studied, and a hybrid modeling method of WFGD is proposed. A comprehensive cost model for industrial WFGD is built before particle swarm optimization (PSO) with a penalty function designed for the optimization of WFGD. A case study is carried out based on the operation data from a 1000-MW unit, and the performance of model prediction and operation optimization is analyzed. Modeling and optimization results proved that the optimized operating parameters are able to minimize the total operating cost, with SO2 emissions meeting the emission standards.
Hybrid model of limestone-gypsum–based WFGD system
A mapping relationship between SO2 emissions and operational parameters, which could be presented as an SO2 emission forecast model, is the foundation for operation optimization. shows the selected parameters that have direct and significant influence on the desulfurization efficiency. The codes and units corresponding to the parameters are listed in .
Table 1. Information on modeling parameters.
A hybrid forecast model was established with the form shown in eq 1.
where refers to the predicted outlet concentration of SO2;
refers to a mathematical model, which was constructed based on the SO2 removal mechanism in WFGD; and
refers to an ANN model.
Factors including boiler load, lime slurry pH, SO2 inlet concentration, and numbers of circulating pumps in operation were taken as the input parameters of the mathematical model. ANN was used to forecast and correct the prediction errors of the mathematical model. ANNs with different structures and inputs were studied, and the hybrid model with the best prediction performance was derived.
Mathematical model
Mathematical model for SO2 removal in WFGD, considering mass transfer and chemical reactions (Hou, Bai, and Yin Citation2013), was chosen as the main part of concentration model for its ability in generalization. For the solving efficiency of models, especially for operation optimization during which the concentration model could be called for thousands of times, simplification of modeling conditions were made:
The gas is in plug flow, and the spray droplets are uniformly dispersed in gas.
There is no slip between the particles and the gas.
The absorption rate of SO2 is proportional to the partial pressure of SO2 because of the instantaneous irreversible reaction with the lime in the liquid phase.
Then, the amount of SO2 removed equals the amount that is absorbed by slurry, and mass transfer equation at certain microelement height can be derived according to mass balance in WFGD:
where refers to the total SO2 mass transfer coefficient of gas phase, molar differential propulsion per unit volume;
is the effective mass transfer area per unit volume;
is the molar fraction of the gas phase SO2;
is the SO2 equilibrium concentration on the side of the gas membrane; and
is the flue gas flux.
The absorption height can be derived by integration of eq 2:
where , which is approximately equal to 1;
and
are the molar fractions of gas phase SO2 at the inlet and outlet of WFGD, respectively; and
is the mean thrust at the gas film side of WFGD.
The part of in eq 3 represents the ability of SO2 removal in a WFGD, which equals to
. Consequently, the basic form of the mathematical model can then be derived as follows (Ortiz et al. Citation2006):
where refers to the prediction of SO2 outlet concentration by mathematical model, and
refers to the number of mass transfer units.
is influenced by the lime slurry pH, calcium-sulfur ratio (Ca/S), and liquid-gas ratio (
) (Hou, Bai, and Yin Citation2013; Zhong et al. Citation2008), which respectively correspond to
,
, and
. And
can be written as
where and
are constants, which are decided by design parameters.
Ca/S is usually set as a constant during operation. is calculated using eq 6.
where Q is the rated flow of the circulating pump.
According to eqs 4, 5, and 6, the specific form of the mathematical model can be presented as
Artificial neural network
The mathematical model considered the main parameters that have influence on the operation of WFGD, whereas certain distortions, such as the gas flow, PM concentration, temperature, lime slurry density, and lime slurry level, were not considered. To eliminate errors caused by distortions, two ANNs that considered different numbers of influencing factors were established. Each ANN was composed of one input layer, one hidden layer with 10 neurons, and one output layer. The activation function of the neurons was sigmoid, and the training method was LM (Levenberg-Marquard). Detailed structures of the ANNs are shown in .
In ANN-a, five parameters, namely, gas flow, particulate matter (PM) concentration, temperature, lime slurry level, and lime slurry density, were taken as the input parameters for error forecasting. For ANN-b, additional influencing factors, including load, SO2 concentration, lime slurry pH, and the number of circulating pumps in operation, were used as input parameters, for a total number of nine parameters. The prediction of ANNs was adopted to compensate the mathematical model for promoted prediction capability. Influence of input parameters on prediction performance was analyzed by comparing performance of the two ANNs.
PSO with a penalty function
PSO framework for WFGD optimization
Particle swarm optimization (PSO) algorithm, originally proposed by Kennedy and Eberhart in 1995 (Kennedy and Eberhart Citation1995), has been one of the most prevalent metaheuristics. Each particle in PSO has a position attribute, which refers to the value of influencing parameters, and a velocity attribute, which refers to the change rate of influencing parameters during iteration. These two attributes are updated, and the value of the objective function corresponding to the particle position is calculated during each iteration to search for the optimal solution. shows the process of PSO. In each iteration, the velocity of each particle is updated using eq 8 to make the particle closer to the current optimal position.
where is the inertia weight; c1 and c2 are the learning factors; r1 and r2 are random numbers ranging from 0 to 1; pbest is the individual extremum that records the best position of the particle; and gbest is global extremum that records the best position of the whole particle swarm.
The position of each particle is updated through eq 9 in each iteration.
The iteration ends when the accuracy meets the requirement or the iteration number reaches the maximum. The value stored in gbest at the end of iteration is regarded the optimal result of PSO.
In this study, a mutation of parameters was used to prevent local optimum. And to enhance the optimization prediction, an adaptive inertia weight ω was adopted, which was equal to 0.9–0.8. Other key parameters for PSO were set following the parameters shown in .
Table 2. Key parameters of PSO.
Constraints and penalty function
As a precondition for the optimization of the operating parameters, the target of desulfurization efficiency (η) and SO2 emissions should be set according to the requirements. Moreover, optimal parameters such as the lime slurry pH and number of circulating pumps in operation also have reasonable and controllable ranges.
Coupled with PSO algorithm, the constraints in this study were divided into two categories: one was on the particle position itself such as the constraints on the pH and the circulating pumps, and the other was on the mapping relationships to the particle position such as the constraints on the desulfurization efficiency and SO2 emissions.
The constraints on the particle position itself can be easily met by limiting the range of the particle position in the relevant dimension. To deal with the constraints on the mapping relationships to the particle position, penalty function method is one of the most popular methods because of its simplicity of implementation. It transforms constrained optimization problems into unconstrained optimization problems by constructing a penalty term to cost function. The general form of the penalty term is σp(x), where σ is a penalty factor and is a penalty function. The strategy for the minimization problem is giving the penalty function a positive value and magnifying it by multiplying the penalty factor to increase the objective function value. This forces the minimum point to be within the feasible domain until the optimal result is found.
Therefore, penalty functions pη and pemi dealing with the constraints of the desulfurization efficiency and SO2 emissions are as follows:
where and
refer to the constraints of the SO2 emissions and the desulfurization efficiency, respectively.
The penalty term is represented as
Optimization object
The aim of parameter optimization is to minimize the total operating cost while maintaining the desulfurization efficiency. Operating cost of WFGD consists of power and material consumption. Power consumption refers to the electrical consumption of the main equipment, such as the circulating pumps and blower fans, and material consumption refers to the desulfurization absorbent.
Circulating pumps and booster fans were regarded as the main equipment influencing desulfurization efficiency of WFGD. The cost of circulating pumps and booster fans
were calculated using eqs 13 and 14.
where ,
, and
are the voltage, current, and power factor of the ith circulating pump;
is the price of electricity;
refers to the pressure drop of the desulfurization tower; and
is the efficiency of the booster fans.
The desulfurization absorbent of WFGD is limestone. According to the mass balances, the cost of limestone consumed per kWhr
is calculated using eq 15:
where and
are the SO2 concentrations at the entrance and exit of WFGD;
and
are the molecular weights of CaCO3 and SO2;
is the calcium sulfur ratio;
is the purity of the limestone; and
is the price of the limestone.
During the consumption of limestone, gypsum is generated, bringing about an economic return. The earnings from gypsum are calculated using eq 16:
where and
are the molecular weight and price of CaCO3, and
is the price of CaSO4.
The total operating cost, in CNY/kW·hr, of WFGD is defined as
In this study, SO2 emissions were restricted to be lower than 50 mg/m3, and the desulfurization efficiency was constrained to be higher than 95%. Consequently, the optimization object would be defined as follows:
Results and discussion
A total of 5035 operation data points from a 1000-MW coal-fired power plant unit, which utilized Shenmu soft coal as main fuel for the ultra-supercritical once-through boiler, were taken as the sample data. By removing incomplete, abnormal, and continuous emission monitoring system blowing data, 3500 data sets were prepared for modeling. The first 2500 data sets were selected as training data, whereas the remaining 1000 data sets were used for model validation.
Modeling and validation
In this work, four models, including one mathematical model (model 1), one ANN (model 2), and two hybrid models (model 3 and model 4), were developed. Model 3 was the hybrid of mathematical model (model 1) and a 5-input, 1-output neural network (ANN-a), whereas model 4 was the hybrid of mathematical model (model 1) and a 9-input, 1-output neural network (ANN-b), as introduced in section "Artificial neural network". Parameters in model 1, including K, α1, and α2, were derived through a regression, the results of which are shown in . The forecast performance of the models on training data are shown in .
Table 3. Results of regression analysis.
To compare the performance of different models, the root mean square error (RMSE) and mean relative error (MRE) criteria, defined through eqs 19 and 20, were adopted.
where n is the number of samples; and and
are the real and predicted response values, which refer to the real and predicted SO2 emissions, respectively.
RMSEs and MREs corresponding to each model are shown in . The results indicate that model 2 had the best prediction capability for training data among the four models, closely followed by model 4. Model 1 was not combined with data-driven model and had the worst prediction performance.
Table 4. RMSEs and MREs on training data set.
To validate the prediction performance out of training data range, the trained models were then used to predict the SO2 emissions on 1000 sets of validation data. Forecasting results are shown in . The RMSEs and MREs are shown in .
Table 5. RMSEs and MREs for validation data set.
As to the validation data, model 4 showed the best prediction performance with an MRE of 11.42%, followed by model 1 with an MRE of 12.08%. The performance of ANN (model 2), which ranked 1st on training set, fell to 3rd among all the four models for the lack of generalization ability. MRE increased in model 3, in which ANN-a was added to the mathematical model, but decreased in model 4, which used ANN-b, illustrating that comprehensive input variables enabled data-driven model to compensate the factors neglected and eliminate the error of mathematical model more effectively. As a result, the mathematical model coupled with ANN-b, a 9-input, 1-output neural network, had the best overall performance.
To further analyze the prediction performance under different operation conditions, model 4 was also used to a period of data with load shifts, which are the main reason for the change of calcium-sulfur ratio and liquid-gas ratio in a WFGD system. As shown in , the prediction performance of model 4 was better during load shifts, during which the change of operating parameters lead to the change of model prediction. Although the performance was not as good when the boiler load is steady, because the effect of fluctuations on outlet concentration was more significant when other parameters are comparatively steady. The overall performance of model 4 was sufficient for operation optimization.
Optimization for multiple conditions
The aim of WFGD optimization is to reduce the operating cost as much as possible under the premise of SO2 emissions reaching the standard. Model 4, which shown a satisfying forecast performance on both the training set and validation set among the four models, was chosen as the forecast model in the optimization process. Setting the SO2 emission limit as 50 mg/m3, the minimum desulfurization efficiency as 95%, the number of particles as 100, and the maximum iteration time as 50, the operating parameters, including the lime slurry pH, temperature, lime slurry density, and number of circulating pumps, were optimized.
Under the condition of 750-MW load, and SO2 inlet concentration of 1000 mg/m3, the convergence of the best PSO fitness is shown in , which indicates that PSO with a penalty function achieves a good convergence when the number of iterations reaches nine. It means that the algorithm has a good convergence and is able to find the optimal solution.
Results corresponding to typical load and SO2 inlet concentration are listed in . compares the optimal cost under different loads and SO2 inlet concentrations. With the same requirement of SO2 emissions and desulfurization efficiency, the optimal cost increased when the SO2 inlet concentration increased and decreased when the load increased.
Table 6. Optimization results under typical conditions.
A total of 1000 sets of validation data were optimized using PSO with a penalty function. The operating cost and SO2 emissions before and after optimization are compared in and . The change rates of operating costs and SO2 emissions after optimization are shown in Through PSO, the SO2 emissions were reduced by 31.02%, meeting the emission requirement, whereas the operating costs were increased by only 1.70%, which is a significant improvement to the operation of WFGD system.
Conclusion
To achieve stable emission and economic operation, an operation optimization method integrating hybrid model and PSO for WFGD is proposed in this paper. The affecting parameters are analyzed, and the mathematical as well as data-driven part of the hybrid model is studied. Structure of PSO with penalty function, including solving method, operation limits, and cost function, is presented. Operation parameters of an industrial WFGD system are optimized under different operation scenarios, and comparison is made with operation data. From the results of the study, the following conclusions are derived:
A hybrid model for a WFGD is built by combining mathematical model with ANN. The hybrid model has both satisfying generalization performance and high prediction accuracy. Among all models considered, the hybrid model consisting of a mechanism model and a 9-input ANN shows the best performance in terms of validation data, with an MRE of 11.42%.
PSO with a penalty function algorithm is applied to improve the economy of desulfurization process. Aimed at the minimization of operating cost, the operating parameters, including lime slurry pH, temperature, lime slurry density, and number of circulating pumps in operation, are optimized. The results show that PSO with a penalty function achieves satisfying convergence performance to reduce operating cost under constraints.
The operating parameters are optimized under the conditions of typical loads and SO2 inlet concentrations, as well as real operating conditions. The results indicate that the optimal cost increases when the SO2 inlet concentration increases and it decreases when the load increases. Through the optimization on validation data, SO2 emissions are reduced by 31.02% with the operating cost increases less than 2%.
Additional information
Funding
Notes on contributors
Yishan Guo
Yishan Guo is a Ph.D. candidate at State Key Laboratory of Clean Energy Utilization, State Environmental Protection Center for Coal-Fired Air Pollution Control, Zhejiang University, Hangzhou, People’s Republic of China.
Zhewei Xu
Zhewei Xu is a graduate student at State Key Laboratory of Clean Energy Utilization, State Environmental Protection Center for Coal-Fired Air Pollution Control, Zhejiang University, Hangzhou, China.
Chenghang Zheng
Chenghang Zheng is an associate professor at State Key Laboratory of Clean Energy Utilization, State Environmental Protection Center for Coal-Fired Air Pollution Control, Zhejiang University, Hangzhou, People’s Republic of China.
Jian Shu
Jian Shu is a graduate student at State Key Laboratory of Clean Energy Utilization, State Environmental Protection Center for Coal-Fired Air Pollution Control, Zhejiang University, Hangzhou, China.
Hong Dong
Hong Dong is an engineer at Zhejiang University Energy Engineering Design and Research Institute Co., Ltd., Hangzhou, People’s Republic of China.
Yongxin Zhang
Yongxin Zhang and Weiguo Weng are senior engineers at State Key Laboratory of Clean Energy Utilization, State Environmental Protection Center for Coal-Fired Air Pollution Control, Zhejiang University, Hangzhou, China.
Weiguo Weng
Yongxin Zhang and Weiguo Weng are senior engineers at State Key Laboratory of Clean Energy Utilization, State Environmental Protection Center for Coal-Fired Air Pollution Control, Zhejiang University, Hangzhou, China.
Xiang Gao
Xiang Gao is a professor at State Key Laboratory of Clean Energy Utilization, State Environmental Protection Center for Coal-Fired Air Pollution Control, Zhejiang University, Hangzhou, People’s Republic of China.
References
- Ahmadi, A., Y. A. Beromi, and H. R. Soleymanpour. 2016. Optimal load shedding by a new binary PSO. Compel Int. J. Comput. Math. Electr. Electron. Eng. 35 (3):898–909. doi:10.1108/compel-01-2016-0033.
- Brogren, C., and H. T. Karlsson. 1997. Modeling the absorption of SO2 in a spray scrubber using the penetration theory. Chem. Eng. Sci. 52 (18):3085–99. doi:10.1016/S0009-2509(97)00126-7.
- Brown, K., W. Kalata, and R. Schick. 2014. Optimization of SO2 Scrubber using CFD Modeling. Procedia Eng. 83:170–80.
- Carletti, C., C. De Basio, E. Makila, J. Salonen, and T. Westerlund. 2015. Optimization of a wet flue gas desulfurization scrubber through mathematical modeling of limestone dissolution experiments. Ind. Eng. Chem. Res. 54 (40):9783–97. doi:10.1021/acs.iecr.5b02691.
- Chang, W.-D., and C.-Y. Chen. 2014. PID controller design for MIMO processes using improved particle swarm optimization. Circuits Syst. Signal Process. 33 (5):1473–90. doi:10.1007/s00034-013-9710-4.
- Chen, G., L. Liu, P. Song, and D. Yangwei. 2014. Chaotic improved PSO-based multi-objective optimization for minimization of power losses and L index in power systems. Energy Convers. Manag. 86:548–60. doi:10.1016/j.enconman.2014.06.003.
- Chen, G. G., L. L. Liu, Y. Y. Guo, and S. W. Huang. 2016. Multi-objective enhanced PSO algorithm for optimizing power losses and voltage deviation in power systems. Compel Int. J. Comput. Math. Electr. Electron. Eng. 35 (1):350–72. doi:10.1108/compel-02-2015-0030.
- Chen, L., Y. Hontoir, D. Huang, J. Zhang, and A. Julian Morris. 2004. Combining first principles with black-box techniques for reaction systems. Control. Eng. Pract. 12 (7):819–26. doi:10.1016/j.conengprac.2003.09.006.
- Colla, V., G. Nastasi, S. Baldetti, and M. Del Seppia. 2016. Multi-Objective Particle Swarm Optimization applied to distribution fitting for industrial data. 2016 Ieee 2nd International Forum on Research And Technologies for Society And Industry Leveraging a Better Tomorrow (Rtsi) 342–47, Bologna, Italy.
- Dou, B., W. Pan, Q. Jin, W. Wang, and L. Yu. 2009. Prediction of SO2 removal efficiency for wet Flue Gas Desulfurization. Energy Convers. Manag. 50 (10):2547–53. doi:10.1016/j.enconman.2009.06.012.
- Gerbec, M., A. Stergarsek, and R. Kocjancic. 1995. Simulation model of wet flue gas desulphurization plant. Comput. Chem. Eng. 19 (Supplement 1):283–86. doi:10.1016/0098-1354(95)87050-4.
- Hinchliffe, M., G. Montague, M. Willis, and A. Burke. 2003. Hybrid approach to modeling an industrial polyethylene process. Aiche J. 49 (12):3127–37. doi:10.1002/(ISSN)1547-5905.
- Hou, P., J. Bai, and J. Yin. 2013. On-line monitoring and optimization of performance indexes for limestone wet desulfurization technology. Appl. Mech. Mater. 9:295–98.
- Huang, Y.-C., and Y.-H. Li. 2014. Experiments of iterative learning control system using particle swarm optimization by new bounded constraints on velocity and positioning. Eng. Computation. 31 (2):250–66. doi:10.1108/ec-01-2013-0013.
- Kallinikos, L. E., E. I. Farsari, D. N. Spartinos, and N. G. Papayannakos. 2010. Simulation of the operation of an industrial wet flue gas desulfurization system. Fuel Process. Technol. 91 (12):1794–802. doi:10.1016/j.fuproc.2010.07.020.
- Kennedy, J., and R. Eberhart. 1995. Particle swarm optimization. Proceedings of IEEE International Conference on Neural Networks, Perth, Australia.
- Kramar, D., D. Cica, B. Sredanovic, and J. Kopac. 2016. Design of fuzzy expert system for predicting of surface roughness in high-pressure jet assisted turning using bioinspired algorithms. Ai Edam-Artif. Intell. Eng. Des. Anal. Manuf. 30 (1):96–106. doi:10.1017/s0890060415000189.
- Li, C., J. Zhang, Y. Zhang, L. Qinwu, C. Zheng, X. Gao, and Z. Luo. 2015. Removal efficiency of high sulfur dioxide in WFGD based on dual-pH value control. Acta Sci. Circumstantiae 35 (12):4081–87.
- Liu, D., and H. Yu. 2012. A study of experimental and improved absorption model for the spray towers of wet flue gas desulfurization. Adv. Mater. Res. 6:550–53.
- Liu, D., L. Xiaowei, Y. Huang, and H. Jianchen. 2011. Sensitivity analysis on limestone density of WFGD. Chin. J. Environ. Eng. 5 (10):2321–25.
- Liu, Y., C. Niu, H. Cheng, and X. Liu. 2012. Target optimization of wet flue gas desulfurization control system in 330 MW unit. Electr. Power 45 (4):68–72.
- Ministry of Environmental Protection of PRC, General Administration of Quality Supervision, Inspection and Quarantine of PRC. 2011. Emission Standard of Air Pollutants for Thermal Power Plants, GB/T 13223-2011.
- National Bureau of Statistics [NBS]. 2017. China energy statistical yearbook 2017. Beijing: National Bureau of Statistics.
- Neveux, T., and Y. Le Moullec. 2011. Wet industrial flue gas desulfurization unit: Model development and validation on industrial data. Ind. Eng. Chem. Res. 50 (12):7579–92. doi:10.1021/ie102239q.
- Ortiz, F. J., G. F. Vidal, P. Ollero, A. L. Salvador, V. Cortés, and A. Giménez. 2006. Pilot-plant technical assessment of wet flue gas desulfurization using limestone. Ind. Eng. Chem. Res. 45 (4):1466–77. doi:10.1021/ie051316o.
- Ou, S., and L. E. K. Achenie. 2005. A hybrid neural network model for PEM fuel cells. J. Power. Sources 140 (2):319–30. doi:10.1016/j.jpowsour.2004.08.047.
- Qian, D. U., G. A. O. Wang Jianfeng, Z. G. Jianmin, and W. U. Shaohua. 2011. Optimization on inlet angle for spray tower of industrial boiler by numerical simulation. J. Therm. Sci. Technol. 10 (2):174–79.
- Ren, Z., L. Sun, and Y. Deng. 2012. Modeling and optimization research of CFB-FGD based on improved genetic algorithms and BP neural network. Adv. Mater. Res. 610–613:1601–1604.
- Sui, Z., Y. Zhang, Y. Peng, P. Norris, Y. Cao, and W.-P. Pan. 2016. Fine particulate matter emission and size distribution characteristics in an ultra-low emission power plant. Fuel 185:863–71. doi:10.1016/j.fuel.2016.08.051.
- Tan, W., Z. Zhang, L. Hongyi, L. Youxu, and Z. Shen. 2017. Carbonation of gypsum from wet flue gas desulfurization process: Experiments and modeling. Environ. Sci. Pollut. Res. 24 (9):8602–08. doi:10.1007/s11356-017-8480-0.
- Villanueva Perales, A. L., F. J. Gutierrez Ortiz, F. Vidal Barrero, and P. Ollero. 2010. Using neural networks to address nonlinear pH control in wet limestone flue gas desulfurization plants. Ind. Eng. Chem. Res. 49 (5):2263–72. doi:10.1021/ie9007584.
- Villanueva Perales, A. L., P. Ollero, F. J. Gutierrez Ortiz, and A. Gomez-Barea. 2009. Model predictive control of a wet limestone flue gas desulfurization pilot plant. Ind. Eng. Chem. Res. 48 (11):5399–405. doi:10.1021/ie801530x.
- Wang, S., H. Sangao, L. Liu, S. Liang, and X. Hong. 2010. Operation optimuation and retrofit study of circulating slurry pump in FGD system of 600 MW unit. Electr. Power 43 (11):46–49.
- Wang, S., and J. Hao. 2012. Air quality management in China: Issues, challenges, and options. J. Environ. Sci. 24 (1):2–13. doi:10.1016/S1001-0742(11)60724-9.
- Warych, J., and M. Szymanowski. 2001. Model of the wet limestone flue gas desulfurization process for cost optimization. Ind. Eng. Chem. Res. 40 (12):2597–605. doi:10.1021/ie0005708.
- Warych, J., and M. Szymanowski. 2002. Optimum values of process parameters of the “Wet Limestone Flue Gas Desulfurization System”. Chem. Eng. Technol. 25 (4):427–32. doi:10.1002/1521-4125(200204)25:4<427::aid-ceat427>3.3.co;2-o.
- Wu, Y., L. Shen, and L. Zhang. 2011. Study on nonlinear pH control strategy based on external recurrent neural network. Procedia Eng. 15 (1):866–71.
- Yang, J., Y. Kan, J. Zhang, and D. Liu. 2015. Simulation of internal flow field in tangential spray desulfurization tower. J. Eng. Therm. Energy Power 30 (4):593–97.
- Yuan, T., Z. Jie, and J. Morris. 2001. Modeling and optimal control of a batch polymerization reactor using a hybrid stacked recurrent neural network model. Ind. Eng. Chem. Res. 40 (21):4525–35. doi:10.1021/ie0010565.
- Zhao, J., B. Jin, and Z. Zhong. 2007. The degree of desulphurization of a limestone/gypsum wet FGD spray tower using response surface methodology. Chem. Eng. Technol. 30 (4):517–22. doi:10.1002/ceat.200600347.
- Zhong, Y., X. Gao, W. Huo, Z.-Y. Luo, N. Ming-Jiang, and K.-F. Cen. 2008. A model for performance optimization of wet flue gas desulfurization systems of power plants. Fuel Process. Technol. 89 (11):1025–32. doi:10.1016/j.fuproc.2008.04.004.
- Zhu, J., W. Zhenyuan, Y. Shichao, Y. Zheng, Y. Yang, and J. Bai. 2015b. Modelling of wet limestone-gypsum flue gas desulfurization system in spray tower. J. Chem. Eng. Chin. Univ. 29 (1):220–25. doi:10.1002/cjoc.201400680.
- Zhu, J., Y. Shi-Chao, J. Bai, W. Zhen-Yuan, Z.-H. Liu, and Y.-F. Yang. 2015a. A concise algorithm for calculating absorption height in spray tower for wet limestone-gypsum flue gas desulfurization. Fuel Process. Technol. 129:15–23. doi:10.1016/j.fuproc.2014.07.002.