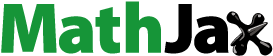
ABSTRACT
Separating cathode material and Al foil from spent lithium-ion batteries (LIBs) is a critical step for LIBs recycling. As compared to chemical dissolving and decomposition, the pyrolysis pretreatment is an alternative and simple method. In this work, the pyrolysis kinetics of cathode material were comparatively studied using various isoconversional methods, including Flynn-Wall-Ozawa (FWO), Friedman, Kissinger-Akahira-Sunose, Starink, Tang, and Boswell. The thermal degradation mechanism was investigated by the Coats-Redfern (CR) and master-plot methods as well. The thermogravimetric analysis revealed that cathode material decomposition could be divided into three stages with mass losses of 1.51%, 0.787%, and 0.449%, respectively. Activation energy (Eα) calculated using the six model-free methods showed a similar trend, gradually increasing as the degree of conversion (α) increased from 0.001 to 0.009, and then significantly elevating. The FWO method gave the best fitting and Eα values first increased from 12.032 to 24.433 kJ·mol−1 with α elevating from 0.001 to 0.009, then increased further to 43.187 kJ·mol−1. Both CR and Criado methods indicated that the degradation of cathode material can be explained by the diffusion models.
Implications: The rapid growth in the production and consumption of lithium-ion batteries (LIBs) for portable electronic devices and electric vehicles has resulted in an increasing number of spent LIBs. Thermal treatment offers advantages of high-efficiency and simple operation. Understanding the thermal process of spent LIBs and probing its kinetic are significant for the large-scale treatment. Through this study, it will be significant for the reactor designing and optimizing in practice.
Introduction
Among numerous energy storage devices, the lithium-ion batteries (LIBs) have attracted more attentions due to their higher power density, environmental benignity, and long cycle life. However, concomitant with the fast-growing service consumption of LIBs, the generation of spent LIBs has been increasing immensely (Gao et al. Citation2019, Li et al. Citation2018; Wang, Tan, and Li et al. Citation2018; Yao et al. Citation2020a). In view of this waste’s negative effects on the environment and valuable metals present within it, recycling the waste is highly desirable. Recently, many sophisticated technologies (Liu et al. Citation2019; Liu et al. Citation2019; Lv et al. Citation2018) – such as mechanical treatment, pyro-metallurgy, hydrometallurgy, bio-metallurgy, and a combination of the mentioned – have been developed. However, separating cathode materials and Al foil are difficult during these recycling processes, because they are firmly adhered by polyvinylidene fluoride (PVDF) binder. The commonly used approaches of detaching cathode materials involve dissolving Al foil using chemicals, dissolving PVDF with organic solvents, and decomposing the binder with oxidants. But applying chemicals will generate wastewater and increase the recycling cost. In addition, it will pose threats to workers’ health.
As a comparison, thermal treatment has the advantages of simple operation and high efficiency (Cheng et al. Citation2019; Qi et al. Citation2019; Reis et al. Citation2019; Yu et al. Citation2019). Zhang et al. (Citation2019, Citation2018, Citation2019) removed the PVDF binder using pyrolysis treatment. The optimum pyrolysis temperature of organic binders in electrode materials was determined as 500°C with a heating rate of 10°C/min and pyrolysis time of 15 min. Wang et al. (Citation2018) removed the binder by roasting at 450°C for 15 min. Wang et al. (Citation2019) developed a novel molten salt technique to degrade the binder. The AlCl3-NaCl system could melt PVDF efficiently at a temperature of 160°C with a holding time of 20 min. However, there are sparse researches on the thermodynamic kinetics of these treatments, which will be critical for the reactor design, optimization, and scaleup during industrial-scale treatments of spent LIBs. Therefore, in this work, the pyrolysis kinetics of cathode material was investigated by different isoconversional methods. The possible degradation mechanism of cathode material was studied as well.
Material and methods
Materials
The spent LIBs were supplied by local cellular phone repair shops. Prior to usage, they were discharged using 3.5% NaCl solution to mitigate the potential risk of short circuiting or LIB blast. After drying, they were dismantled manually, and the cathode and anode were separated. The cathode was crushed and used as raw material.
Experimental procedure
The cathode powder with weight of approximately 2 mg was put in crucibles and heated from 30°C under a N2 flow. The experiments were repeated at different heating rates of 5, 10, and 20 K·min−1. Each test was repeated at least three times.
Basic theories
The principle theories of model-free methods and model-fitting methods can be found in literatures (Da Silva et al. Citation2018; Fernandez et al. Citation2020, Citation2019; Qi et al. Citation2020; Yao et al. Citation2020; Yao et al. Citation2020b). In this work, the pyrolysis kinetics of cathode material was studied using six model-free methods, including Flynn-Wall-Ozawa (FWO), Friedman, Kissinger-Akahira-Sunose (KAS), Starink, Tang, and Boswell. The thermal degradation mechanism was investigated by the Coats-Redfern (CR) and master-plot methods.
Mathematical resolution by FWO integral isoconversional method is based on the Doyle approximation equation and can be expressed as
where β and A refer to the heating rate (K·min−1) and pre-exponential factor (min−1). Eα is the apparent activation energy (kJ·mol−1). T and R represent the absolute temperature (K) and universal gas constant (8.314 J·(mol·K)−1), respectively. g(α) shows the integral form of reaction model, f(α).
The Friedman method is based on the assumption that solids decomposition depends only on the rate of mass loss and is independent from temperature. The equations for Friedman method are given below.
The integral isoconversional method proposed by KAS involves an approximation using the Murray and White equation that can be described as:
Another integral isoconversional method originates from the Starink approximation equation can be expressed as follows:
Tang method was developed based on a different estimation of Arrhenius temperature integral and is given as follows:
The Boswell method is also an integral isoconversional method and can be expressed as
For each α, corresponding T and β from thermogravimetric data are used to plot lnβ versus ,
versus
,
versus
,
versus
,
versus
and
versus
. The Eα values can be determined from the regression slope for these model-free methods.
Results and discussion
Thermogravimetric analysis
The TG-DTG profiles of the cathode material are illustrated in . The weight loss profiles showed a similar trend for these three heating rates. The whole decomposition process could be divided into three stages. At the low heating rate of 5 K·min−1, three weight losses of 1.51%, 0.787%, and 0.449% were detected throughout temperatures of 30–500°C, 500–700°C, and 700–1000°C, respectively. The first weight loss was ascribed to the degradation of PVDF, consistent with the reported temperature of below 500°C (Rathore, Madhav, and Jaiswar et al. Citation2019; Xu et al. Citation2010, Zhao et al. Citation2017). The following stage was attributed to the oxidization of acetylene black. Cho et al. (Citation2013) observed an exothermic peak temperature for the decomposition of acetylene black at 604°C, and Nie et al. (Citation2015) revealed the acetylene black oxidization at 620°C. The last weight loss was due to the decomposition of lithium cobalt oxide and cobalt oxide (Antolini and Ferretti Citation1995; Zhang et al. Citation2014). In this study, the first two stages were the major decomposition stages for the cathode material, and were thus selected for the following kinetic study.
Activation energy calculation
The linear fitting from six model-free methods is displayed in . For these methods, a large gap between the straight lines in the α range of 0.001–0.002 was observed, indicating a slower conversion of cathode material at initial stage, i.e., the low temperature cannot offer energy for rupturing the C-F bonds present in PVDF. Subsequently, the temperatures elevated enough to break down the molecules (Yao et al. Citation2020a).
The calculated Eα and R from different model-free methods are shown in and . The obtained Eα values showed an increasing trend, which slightly increased in the α range of 0.001–0.009, and then significantly increased. The later drastic increasement was representative of the great variety of chemical bonds and the multiphasic character of the conversion. Comparing these different model-free methods, the Eα values were comparable among KAS, Starink and Tang methods. The slight differences could be ascribed to the different approximations of temperature integral (Da Silva et al. Citation2018) and systematic error. The Eα values displayed a descending order: FWO > Boswell > Friedman > Tang, Starink and KAS. Since the FWO method gave the best fitting, the Eα values it yielded were applied for further decomposition mechanism study. This situation was consistent with that found in other literatures (Khiari, Moussaoui, and Jeguirim et al. Citation2019, Ma et al. Citation2018; Sokoto et al. Citation2016). For FWO method (), the obtained Eα values slightly increased from 12.032 to 24.433 kJ·mol−1 with α elevating from 0.001 to 0.009, and increased further to 43.187 kJ·mol−1.
Table 1. Kinetic parameters derived from the model-free methods
Estimation of reaction mechanisms
The CR method (Coats and Redfern Citation1964) is an integral model-fitting method. For a given β and proposed reaction mechanisms g(α), plotting versus
gives a straight line. The linear fittings were plotted and illustrated in . The activation energy for all g(α) functions in can be obtained from the slope. Comparing the coefficients, they were distinct for these models. The diffusion models showed better linear fitting, with R values of 0.9786 for D1, 0.9787 for D2, 0.9788 for D3, and 0.9788 for D4. The corresponding Eα values were 31.658, 31.694, 31.730, and 31.705 kJ·mol−1, respectively. This situation has also been observed in the pyrolysis of biomass (Tonbul Citation2008) and plastics (Sinfronio et al. Citation2005). The degradation mechanism was studied by master-plots method. illustrates the comparison between the theoretical master curves and the experimental curve confirming that the fitting of experimental curve to the diffusion models.
Table 2. Expressions of f(α) and g(α) for reaction mechanisms
Conclusion
As compared to chemical dissolving and decomposition, the pyrolysis pretreatment is an alternative and simple method. In this work, the pyrolysis kinetics of cathode material were comparatively studied. The thermal degradation mechanism was investigated by the CR and master-plot methods as well. The thermogravimetric analysis revealed that the degradation of cathode material from spent LIBs could be divided into three stages. Weight losses of 1.51%, 0.787%, and 0.449% were detected for the temperature ranges of 30–500°C, 500–700°C, and 700–1000°C, respectively. The Eα values calculated displayed a similar trend and were comparable among KAS, Starink and Tang methods. They slightly increased in the α range of 0.001–0.009, and then significantly increased. The FWO method offered the highest coefficients and the Eα values gradually increased from 12.032 to 24.433 kJ·mol−1 as α increased from 0.001 to 0.009, then increased further to 43.187 kJ·mol−1. Both CR and Criado methods indicated that the degradation of cathode material could be better described by using the diffusion models. This study will give significant references for the reactor design, optimization, and scaleup during industrial-scale treatments of spent LIBs.
Disclosure statement
No potential conflict of interest was reported by the authors.
Additional information
Funding
Notes on contributors
Shaoqi Yu
Shaoqi Yu is postgraduate in Hangzhou Dianzi University.
Baogui Zhang
Baogui Zhang is an engineer in Beijing Institute of Space Mechanics & Electricity.
Jingjing Xiong
Jingjing Xiong is postgraduate in Hangzhou Dianzi University.
Zhitong Yao
Zhitong Yao is a researchers in Hangzhou Dianzi University.
Daidai Wu
Daidai Wu is a researcher in Chinese Academy of Sciences.
Jie Liu
Jie Liu is a researchers in Hangzhou Dianzi University.
Shaodan Xu
Shaodan Xu is a researchers in Hangzhou Dianzi University.
Junhong Tang
Junhong Tang is a researchers in Hangzhou Dianzi University.
References
- Antolini, E., and M. Ferretti. 1995. Synthesis and thermal stability of LiCoO2. J. Solid State Chem. 117 (1):1–7. doi:10.1006/jssc.1995.1238.
- Cheng, S., Y. Qiao, J. Huang, W. Wang, Z. Wang, Y. Yu, and M. Xu. 2019. Effects of Ca and Na acetates on nitrogen transformation during sewage sludge pyrolysis. P. Combust. Inst. 37 (3):2715–22. doi:10.1016/j.proci.2018.08.018.
- Cho, T., C. Han, Y. Jun, and S. Yoon. 2013. Formation of artificial pores in Nano-TiO2 photo-electrode films using acetylene-black for high-efficiency, dye-sensitized solar cells. SCI Rep. 3:1496. doi:10.1038/srep01496.
- Coats, A. W., and J. P. Redfern. 1964. Kinetic parameters from thermogravimetric data. Nature 201 (4914):68. doi:10.1038/201068a0.
- Da Silva, J. C. G., J. L. F. Alves, W. V. D. A. Galdino, S. L. F. Andersen, and R. F. de Sena. 2018. Pyrolysis kinetic evaluation by single-step for waste wood from reforestation. Waste Manage. 72:265–73. doi:10.1016/j.wasman.2017.11.034.
- Fernandez, A., L. R. Ortiz, D. Asensio, R. Rodriguez, and G. Mazza. 2020. Kinetic analysis and thermodynamics properties of air/steam gasification of agricultural waste. J. Environ. Chem. Eng. 8 (4):103829. doi:10.1016/j.jece.2020.103829.
- Fernandez, A., J. Soria, R. Rodriguez, J. Baeyens, and G. Mazza. 2019. Macro-TGA steam-assisted gasification of lignocellulosic wastes. J. Environ. Manage. 233:626–35. doi:10.1016/j.jenvman.2018.12.087.
- Gao, G., X. Luo, X. Lou, Y. Guo, R. Su, J. Guan, Y. Li, H. Yuan, J. Dai, and Z. Jiao. 2019. Efficient sulfuric acid-vitamin C leaching system: Towards enhanced extraction of cobalt from spent lithium-ion batteries. J. Mater. Cycles Waste 21 (10):942–49. doi:10.1007/s10163-019-00850-4.
- Khiari, B., M. Moussaoui, and M. Jeguirim. 2019. Tomato-processing by-product combustion: Thermal and kinetic analyses. Materials 12 (4):553. doi:10.3390/ma12040553.
- Li, L., Y. Bian, X. Zhang, Q. Xue, E. Fan, F. Wu, and R. Chen. 2018. Economical recycling process for spent lithium-ion batteries and macro- and micro-scale mechanistic study. J. Power Sources 377:70–79. doi:10.1016/j.jpowsour.2017.12.006.
- Liu, C., J. Lin, H. Cao, Y. Zhang, and Z. Sun. 2019. Recycling of spent lithium-ion batteries in view of lithium recovery: A critical review. J. Clean. Prod. 228:801–13. doi:10.1016/j.jclepro.2019.04.304.
- Liu, P., L. Xiao, Y. Tang, Y. Chen, L. Ye, and Y. Zhu. 2019. Study on the reduction roasting of spent LiNixCoyMnzO2 lithium-ion battery cathode materials. J. Therm. Anal. Calorim. 136:1323–32. doi:10.1007/s10973-018-7732-7.
- Lv, W., Z. Wang, H. Cao, Y. Sun, Y. Zhang, and Z. Sun. 2018. A critical review and analysis on the recycling of spent lithium-ion batteries. ACS Sustain. Chem. Eng. 6 (2):1504–21. doi:10.1021/acssuschemeng.7b03811.
- Ma, Z., J. Wang, Y. Yang, Y. Zhang, C. Zhao, Y. Yu, and S. Wang. 2018. Comparison of the thermal degradation behaviors and kinetics of palm oil waste under nitrogen and air atmosphere in TGA-FTIR with a complementary use of model-free and model-fitting approaches. J. Anal. Appl. Pyrol. 134:12–24. doi:10.1016/j.jaap.2018.04.002.
- Nie, H., L. Xu, D. Song, J. Song, X. Shi, X. Wang, L. Zhang, and Z. Yuan. 2015. LiCoO2: Recycling from spent batteries and regeneration with solid state synthesis. Green Chem. 17 (2):1276–80. doi:10.1039/C4GC01951B.
- Qi, W., G. Liu, C. He, S. Liu, S. Lu, J. Yue, Q. Wang, Z. Wang, Z. Yuan, and J. Hu. 2019. An efficient magnetic carbon-based solid acid treatment for corncob saccharification with high selectivity for xylose and enhanced enzymatic digestibility. Green Chem. 21:1292–304. doi:10.1039/C8GC02854K.
- Qi, W., W. Yang, Q. Xu, Z. Xu, Q. Wang, C. Liang, S. Liu, C. Ling, Z. Wang, and Z. Yuan. 2020. Comprehensive research on the influence of nonlignocellulosic components on the pyrolysis behavior of chinese distiller’s grain. ACS Sustain. Chem. Eng. 8 (8):3103–13. doi:10.1021/acssuschemeng.9b05848.
- Rathore, S., H. Madhav, and G. Jaiswar. 2019. Efficient nano-filler for the phase transformation in polyvinylidene fluoride nanocomposites by using nanoparticles of stannous sulfate. Mater. Res. Innovations 23 (4):183–90. doi:10.1080/14328917.2017.1406572.
- Reis, J. S., R. O. Araujo, V. M. R. Lima, L. S. Queiroz, C. E. F. da Costa, J. J. R. Pardauil, J. S. Chaar, G. N. Rocha Filho, and L. K. C. de Souza. 2019. Combustion properties of potential amazon biomass waste for use as fuel. J. Therm. Anal. Calorim. 138:3535–39. doi:10.1007/s10973-019-08457-5.
- Sinfronio, F., J. Santos, L. Pereira, A. Souza, M. Conceicao, V. Fernandes Jr, and V. Fonseca. 2005. Kinetic of thermal degradation of low-density and high-density polyethylene by non-isothermal thermogravimetry. J. Therm. Anal. Calorim. 79:393–99. doi:10.1007/s10973-005-0072-4.
- Sokoto, M. A., R. Singh, B. B. Krishna, J. Kumar, and T. Bhaskar. 2016. Non-isothermal kinetic study of de-oiled seeds cake of African star apple (Chrosophyllum albidum) using thermogravimetry. Heliyon 2 (10):e172. doi:10.1016/j.heliyon.2016.e00172.
- Tonbul, Y. 2008. Pyrolysis of pistachio shell as a biomass. J. Therm. Anal. Calorim. 91 (2):641–47. doi:10.1007/s10973-007-8428-6.
- Wang, F., T. Zhang, Y. He, Y. Zhao, S. Wang, G. Zhang, Y. Zhang, and Y. Feng. 2018. Recovery of valuable materials from spent lithium-ion batteries by mechanical separation and thermal treatment. J. Clean. Prod. 185:646–52. doi:10.1016/j.jclepro.2018.03.069.
- Wang, M., Q. Tan, and J. Li. 2018. Unveiling the role and mechanism of mechanochemical activation on lithium cobalt oxide powders from spent lithium-ion batteries. Environ. Sci. Technol. 52 (22):13136–43. doi:10.1021/acs.est.8b03469.
- Wang, M., Q. Tan, L. Liu, and J. Li. 2019. Efficient separation of aluminum foil and cathode materials from spent lithium-ion batteries using a low-temperature molten salt. ACS Sustain. Chem. Eng. 7 (9):8287–94. doi:10.1021/acssuschemeng.8b06694.
- Xu, B., S. Hou, M. Chu, G. Cao, and Y. Yang. 2010. An activation-free method for preparing microporous carbon by the pyrolysis of poly(vinylidene fluoride). Carbon 48 (10):2812–14. doi:10.1016/j.carbon.2010.04.011.
- Yao, Z., S. Yu, W. Su, W. Wu, J. Tang, W. Qi, et al. 2020. Comparative study on the pyrolysis kinetics of polyurethane foam from waste refrigerators. Waste Manage. Res. 38 (3):271–78. doi:10.1177/0734242X19877682.
- Yao, Z., S. Yu, W. Su, D. Wu, W. Wu, and J. Tang. 2020a. Kinetic modeling study on the combustion treatment of cathode from spent lithium-ion batteries. Waste Manage. Res. 38 (1):100–06. doi:10.1177/0734242X19879224.
- Yao, Z., S. Yu, W. Su, W. Wu, J. Tang, and W. Qi. 2020b. Kinetic studies on the pyrolysis of plastic waste using a combination of model-fitting and model-free methods. Waste Manage. Res. 38 (1_suppl):77–85. doi:10.1177/0734242X19897814.
- Yu, S., W. Su, D. Wu, Z. Yao, J. Liu, J. Tang, and W. Wu. 2019. Thermal treatment of flame retardant plastics: A case study on a waste TV plastic shell sample. Sci. Total Environ. 675:651–57. doi:10.1016/j.scitotenv.2019.04.264.
- Zhang, G., Z. Du, Y. He, H. Wang, W. Xie, and T. Zhang. 2019. A sustainable process for the recovery of anode and cathode materials derived from spent lithium-ion batteries. Sustainability 11 (8):1–11.
- Zhang, G., Y. He, Y. Feng, H. Wang, T. Zhang, W. Xie, and X. Zhu. 2018. Enhancement in liberation of electrode materials derived from spent lithium-ion battery by pyrolysis. J. Clean. Prod. 199:62–68. doi:10.1016/j.jclepro.2018.07.143.
- Zhang, G., Y. He, H. Wang, Y. Feng, W. Xie, and X. Zhu. 2019. Application of mechanical crushing combined with pyrolysis-enhanced flotation technology to recover graphite and LiCoO2 from spent lithium-ion batteries. J. Clean. Prod. 231:1418–27. doi:10.1016/j.jclepro.2019.04.279.
- Zhang, Z., W. He, G. Li, J. Xia, H. Hu, and J. Huang. 2014. Ultrasound-assisted hydrothermal renovation of LiCoO2 from the cathode of spent lithium-ion batteries. Int. J. Electrochem. Sci. 9 (7):3691–700.
- Zhao, J., L. Liao, F. Shi, T. Lei, G. Cheng, A. Pei, J. Sun, K. Yan, G. Zhou, J. Xie, C. Liu, Y. Li, Z. Liang, Z. Bao, and Y. Cun. 2017. Surface fluorination of reactive battery anode materials for enhanced stability. J. Am. Chem. Soc. 139 (33):11550–58. doi:10.1021/jacs.7b05251.