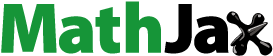
ABSTRACT
Post-neodymium magnets that possess high heat resistance, coercivity, and (BH)max are desired for future-generation motors. However, the candidate materials for post-neodymium magnets such as Sm2Fe17N3 and metastable magnetic alloys have certain process-related problems: low sinterability due to thermal decomposition at elevated temperatures, deterioration of coercivity during sintering, and the poor coercivity of the raw powder. Various developments in powder processing are underway with the aim of overcoming these problems. So far, the development of advanced powder metallurgy techniques has achieved Sm2Fe17N3 anisotropic sintered magnets without coercivity deterioration, and advances in chemical powder synthesis techniques have been successful in producing Sm2Fe17N3 fine powders with huge coercivity. The challenge of a new powder process is expected to open the way to realizing post-neodymium magnets.
GRAPHICAL ABSTRACT
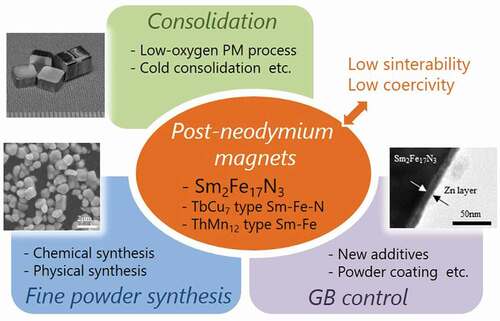
1. Introduction
Electric vehicles and eco-friendly home appliances, which have become indispensable in modern society, were made possible by the advent of interior permanent magnet motors with dramatically higher efficiency. Since motor performance largely depends on the properties of the permanent magnet, higher performance magnets are required for next-generation motors. Nd2Fe14B magnets (neodymium magnets), which are now widely used, are always affected by resource problems [Citation1,Citation2]. In particular, the prices of Nd, the main raw material, and Dy, an additive used to enhance magnetic properties, are easily affected by the international situation because their crustal abundances are very low and production area are eccentrically localized. In view of these problems, the development of a post-neodymium magnet with high performance exceeding the current level and stable raw material procurement conditions has been strongly desired.
compares the potential of various magnetic compounds using the anisotropic magnetic field Ha and saturation magnetization Js, and the theoretical maximum energy product (BH)max. As saturation magnetization and the anisotropic magnetic field increase, higher remanence Br and coercivity Hc can be expected. The theoretical value of (BH)max, which is an important index for motor design, can be calculated by Js2/4μ0, where μ0 represents permeability in a vacuum. To date, only three types of compounds with saturation magnetization and anisotropic magnetic fields comparable to or higher than those of Nd2Fe14B have been discovered: Sm2Fe17N3, TbCu7 type compounds such as (SmZr)(FeCo)10Nx, and ThMn12 type compounds such as Sm(FeCo)12 and NdFe12Nx [Citation3–8]. For example, Sm2Fe17N3 is a magnetic compound that was firstly reported by Iriyama and Coey in 1990 and possesses saturation magnetization equivalent to that of Nd2Fe14B, together with a huge anisotropic magnetic field of 20.7 MA/m, which is about three times that of Nd2Fe14B [Citation3,Citation4]. This huge anisotropic magnetic field is very attractive because larger coercivity has been required in recent motors. Moreover, the Curie temperature of Sm2Fe17N3 is 160 K higher than that of Nd2Fe14B, indicating high heat resistance. The other two candidate compounds have even higher saturation magnetization, as seen in . shows the temperature dependencies of the theoretical (BH)max values estimated from the literature values for the four candidate materials. Here, (BH)max is calculated with 0.8 Js considering some property degradation during processing. Sm2Fe17N3 is expected to exhibit a higher (BH)max above 120°C than the current Nd2Fe14B sintered magnets. In addition to its advantage in heat resistance, the resource problem of Sm2Fe17N3 is far smaller than that of Nd2Fe14B magnets, since the element Sm occurs in a wide range of areas, including North America and Australia, and has few other industrial uses. The TbCu7-type and ThMn12-type compounds are further expected to exhibit much higher (BH)max owing to their large saturation magnetization.
Figure 1. Comparison of magnetic properties of various magnetic compounds. The rectangle, triangle, and circle symbols represent rare-earth alloys, non-rare-earth alloys, and oxides. The same color (except black) means the same crystal structure. Open symbols represent a compound for which a single crystal powder has never been obtained [Citation56]
![Figure 1. Comparison of magnetic properties of various magnetic compounds. The rectangle, triangle, and circle symbols represent rare-earth alloys, non-rare-earth alloys, and oxides. The same color (except black) means the same crystal structure. Open symbols represent a compound for which a single crystal powder has never been obtained [Citation56]](/cms/asset/81e69fcb-d4fd-4e94-a91d-94f48ab6c388/tsta_a_1875791_f0001_oc.jpg)
Figure 2. Comparison of temperature dependencies of (BH)max. The values of Dy-added and hot-deformed Nd2Fe14B sintered magnets are experimental [Citation9,Citation10]. The (BH)max of the other materials are theoretical values that are calculated with 0.8 Js [Citation5,Citation7,Citation8,Citation45,Citation57,Citation58Citation59]
![Figure 2. Comparison of temperature dependencies of (BH)max. The values of Dy-added and hot-deformed Nd2Fe14B sintered magnets are experimental [Citation9,Citation10]. The (BH)max of the other materials are theoretical values that are calculated with 0.8 Js [Citation5,Citation7,Citation8,Citation45,Citation57,Citation58Citation59]](/cms/asset/2b2e3527-f285-44c0-96ee-343cdba66924/tsta_a_1875791_f0002_oc.jpg)
However, there are three major problems in producing practical sintered magnets from these candidate materials. In general, sintered magnets of rare-earth-containing compounds are produced by powder metallurgy processes, that is, preparation of a single crystal fine powder, compaction with a crystalline orientation using an external magnetic field, and sintering. The first problem is the difficulty of sintering while maintaining the performance of the raw powder. In the case of Nd2Fe14B, it is well known that improved coercivity and densification can be obtained because liquid phase sintering can be applied. However, some of candidate materials such as Sm2Fe17N3 and (SmZr)(FeCo)10Nx are nitrides which undergo thermal decomposition at elevated temperatures [Citation5,Citation9,Citation10], making it difficult to apply liquid phase sintering which requires high temperature heating. Solid-phase sintering at a low temperature must be applied is such cases. However, solid-phase sintering does not produce the effects of improving coercivity and densification, and with some candidate materials, it causes a significant reduction in coercivity. The second problem is that even though the candidate materials have a high anisotropic magnetic field, high coercivity commensurate with that anisotropic magnetic field has not been obtained. Because a coercivity improvement effect cannot be expected with solid-phase sintering, as noted above, raw powder with the highest coercivity possible must be prepared from the beginning, but the current coercivity of powders of the candidate materials is significantly low. For example, the highest coercivity obtained in Sm2Fe17N3 powders is still about 7% of the anisotropic magnetic field [Citation11]. The third problem is the difficulty of producing single-crystal powders of TbCu7- and ThMn12-type compounds. Since these materials are metastable phases, the powders have been synthesized by quenching methods, mechanical alloying, and HDDR (hydrogen-disproportionation-desorption-recombination) so far [Citation12–16], but these methods produce only polycrystalline powder, which cannot be used as a raw powder for anisotropic sintered magnets.
In order to bring out the potential of candidate materials such as Sm2Fe17N3, it is necessary to overcome these process-related problems, which do not affect Nd2Fe14B magnets. Therefore, many studies have been carried out to elucidate the phenomena that occur during the processes and to develop new powder processes based on them. This paper presents an overview of research developments related to the powder preparation and powder consolidation processes for the candidate materials. In particular, the focus of this paper is Sm2Fe17N3 because this material is the most widely studied and the other candidate materials also have common issues.
2. Powder sintering and consolidation technologies
2.1. Powder consolidation techniques for thermally degradable rare-earth magnets
Nitride magnets of Sm2Fe17N3 and (SmZr)(FeCo)10Nx undergo thermal decomposition at around 600°C and lose their properties as permanent magnets [Citation5,Citation9,Citation10]. Therefore, unlike Nd2Fe14B magnets, it is impossible simply to apply liquid phase sintering to powders of these compounds because their decomposition temperatures are lower than the liquidus temperature of the Sm-Fe system (720°C). This means that these powders must be densified by solid-phase sintering, which has a densification rate far lower than that of liquid phase sintering. In the early stage of research on Sm2Fe17N3, conventional pressure sintering techniques such as hot-pressing and hot isostatic pressing were applied for densification at temperatures below the decomposition temperature, as indicated in [Citation17,Citation18]. Subsequently, spark plasma sintering and current sintering were tried in order to further reduce the thermal load during sintering [Citation19,Citation20]. Even though these approaches achieved good consolidation of Sm2Fe17N3 powder without apparent decomposition, the problem of significantly decreased coercivity remained. For example, Zhang et al. reported that when Sm2Fe17N3 powder with a coercivity more than 600 kA/m was sintered, coercivity dropped to 300 kA/m at 500°C, even though this temperature is approximately 100°C lower than the decomposition temperature [Citation19]. Including the other methods, sintering deteriorated coercivity by 35% to 75% in comparison with the raw powder. This phenomenon had long been attributed to thermal decomposition, and thus was thought to be unavoidable. Therefore, some researchers applied cold consolidation methods such as shock compaction, aerosol deposition, and compression shearing [Citation21–27]. Some of these approaches were successful in densification without coercivity deterioration, and in particular, compression shearing has achieved a (BH)max of 228 kJ/m3, which was the highest for the Sm2Fe17N3 bulk magnets [Citation27]. However, these cold consolidation processes are not practical techniques due to their low throughput and shape constraints on products.
Table 1. Properties of Sm2Fe17N3 magnets consolidated by various methods. Tcons., Hcj, and ρ represent the consolidation temperature, coercivity, and density, respectively
In contrast to the conventional explanation of coercivity deterioration, a new mechanism was proposed in the recent years: Coercivity decreases due not to thermal decomposition, but due to the existence of an oxide film on the powder surface [Citation20]. The surface oxide film of Sm2Fe17N3 powder is usually composed of Sm2O3 and Fe2O3, and when heated, the following redox reaction occurs between the oxide and the Sm2Fe17N3 matrix:
Since the rare-earth element Sm has a very strong reducing ability, the above reaction proceeds even under heating to several 100°C. As can be seen from the reaction formula, a large amount of α-Fe is precipitated even if Fe2O3 is slightly reduced, and if soft magnetic α-Fe exists on the particle surface, it becomes a nucleation site for reverse domains, resulting in a decreased coercivity. According to this hypothesis, if a powder without an oxide film can be sintered, it should be possible to realize a Sm2Fe17N3 sintered magnet with no decrease in coercivity. The important point here is that the Sm2O3 surface oxide film cannot be removed by the usual hydrogen reduction.
Hence, low-oxygen powder metallurgy techniques, which can produce sintered magnets without forming an oxide film, were developed [Citation28,Citation29]. For example, Takagi et al. attempted to perform all the processes from pulverizing to sintering under a very low oxygen environment below 0.5 ppm O2 in connected gloveboxes, as illustrated in [Citation29]. The oxygen concentration of the fine powder produced by this approach can be suppressed to less than 0.5 wt%, which is from one-half to one-third of the level of air-exposed powders. The powders were sintered below the decomposition temperature while maintaining this low oxygen concentration, and coercivity deterioration was constrained to below 10%, as indicated in . This convincingly demonstrated that a Sm2Fe17N3 anisotropic sintered magnet can be produced by sintering using raw powder with a low surface oxide concentration. Furthermore, this low-oxygen powder metallurgy approach is presumably effective for the other candidate, (SmZr)(FeCo)10Nx, because it is a nitride compound similar to Sm2Fe17N3.
Figure 3. Low oxygen powder metallurgy process for Sm2Fe17N3 sintered magnets [Citation29]
![Figure 3. Low oxygen powder metallurgy process for Sm2Fe17N3 sintered magnets [Citation29]](/cms/asset/f23f9b76-a8d7-4c7a-a480-81dbe04cde48/tsta_a_1875791_f0003_oc.jpg)
Figure 4. Demagnetization curves of powder and sintered magnets produced by the low-oxygen powder metallurgy process [Citation29]
![Figure 4. Demagnetization curves of powder and sintered magnets produced by the low-oxygen powder metallurgy process [Citation29]](/cms/asset/20dbae83-bc0e-48a7-a414-d061e2b5c658/tsta_a_1875791_f0004_oc.jpg)
Other issues have also been clarified in the development of Sm2Fe17N3 sintered magnets so far. As mentioned above, the many low-thermal load consolidation processes studied to date have not yet achieved sufficient densification. For example, the relative density obtained by the sintering approach is 91% at maximum, as indicated in . In addition, although the significant decrease in coercivity due to the surface oxide film was suppressed, a small decrease in coercivity with increasing sintering temperature was found as seen . The possible reason is presumed to be the effect of magnetic coupling due to densification. This needs to be investigated in the future as a new problem. Furthermore, the coercivity is still only about 1 MA/m, which is much lower than the anisotropic magnetic field of 20.7 MA/m. Therefore, further development is needed in order to realize the potential of coercivity as much as possible.
2.2. Powder techniques exploring sintering additives for coercivity enhancement
It is known that the coercivity of Nd2Fe14B magnets is greatly improved by adding a specific other element to the grain boundaries, suggesting the possibility that the same effect can be obtained in Sm2Fe17N3. Therefore, many researchers have attempted to improve coercivity by adding various elements to Sm2Fe17N3 powders and bulk magnets. In particular, Zn addition is well known to yield a substantial improvement in coercivity [Citation30]. For example, Kuhrt et al. reported that huge coercivity of 3.5 MA/m could be achieved by addition of Zn [Citation31]. However, Zn addition cannot improve (BH)max because it inevitably decreases the intrinsic saturation magnetization of Sm2Fe17N3 powder. Therefore, an alternative additive to Zn is required in order to realize high-coercivity sintered magnets. So far, In, Sn, Al, Bi, etc. have been investigated as alternatives to Zn, but no element has exhibited a certain effect in improving coercivity [Citation32]. Moreover, previous studies had been mostly limited to low melting point metals, because the effect of the additive could not be investigated unless it melts and infiltrates into the interparticle. If the effect of additives is to be investigated purely as a means of improving coercivity, the scope should be expanded to materials with high melting points [Citation33,Citation34]. In addition, because the surface oxide film was not sufficiently controlled in these past studies, it cannot be said that the effect of addition was investigated accurately, under a condition of direct contact between Sm2Fe17N3 and the additive element. That is, if the low-oxygen powder metallurgy technology described earlier can be adopted, the additive element can be added directly to the grain boundaries without an oxide film. This approach also has the potential to achieve the maximum effect with the minimum amount of addition.
In order to form a metal film on the surface of magnetic powder, Matsuura et al. developed a low-oxygen powder coating technique utilizing plasma deposition [Citation28]. They applied this process to prepare Zn-bonded magnets, and succeeded in improving the coercivity while suppressing the decrease in remanence [Citation35]. As the result, the obtained magnets exhibited a very excellent (BH) max of 200 kJ/m−3. Yamaguchi et al. also reported a similar coating technique involving sputtering of a metal film [Citation36]. In these techniques, the powder is subjected to coating with mechanical agitation, resulting in a uniform nano-order metal film without any oxide film, as shown by the transmission electron microscopy (TEM) image in the inset in . X-ray photoelectron spectroscopy has demonstrated that the obtained powders have an oxide-free single-phase metal film. Previously, physical and chemical coating methods such as vapor deposition and complex photodecomposition were reported, but those methods had the drawbacks of low coverage and low material selectivity [Citation32,Citation37,Citation38]. The new techniques are able to overcome these problems of the conventional methods.
Figure 5. Summary of the effects of coating 20 non-magnetic metals on the coercivity of Sm2Fe17N3 powders [Citation39]. All coated powders were heat-treated at 500°C. The inset shows a cross-sectional TEM image of a Zn-coated powder [Citation36]
![Figure 5. Summary of the effects of coating 20 non-magnetic metals on the coercivity of Sm2Fe17N3 powders [Citation39]. All coated powders were heat-treated at 500°C. The inset shows a cross-sectional TEM image of a Zn-coated powder [Citation36]](/cms/asset/d124f69d-c1e3-4f7c-a8d7-1173a99ed2da/tsta_a_1875791_f0005_b.gif)
summarizes the change in coercivity of Sm2Fe17N3 powders by coating with 20 different nonmagnetic metals [Citation39]. At present, nine elements that can improve the coercivity of Sm2Fe17N3 when used in conjunction with the low-oxygen powder coating technique have been discovered: Al, Ti, Mn, etc. are new elements which were not found in previous studies using powders with a surface oxide film. Interestingly, these elements do not coincide with the elements for Nd2Fe14B magnets, such as Dy and Ga, suggesting that further research using the low-oxygen powder coating technique may lead to the discovery of new elements and alloys which are capable of enhancing coercivity. In addition, the mechanism that the effect on coercivity differs greatly depending on the element is of academic interest and is also important from the viewpoint of additive design of sintered magnets. Therefore, the mechanism of the effect of each element should be investigated in the future.
3. Powder preparation technologies for high-coercivity rare-earth magnets
3.1. Chemical synthesis approaches
The coercivity of Nd2Fe14B sintered magnets is greatly increased by liquid phase sintering, as mentioned earlier. However, it is not possible to apply liquid phase sintering to thermally degradable and metastable materials such as Sm2Fe17N3. This means that the coercivity of sintered magnets of these materials cannot be increased in sintering unless an effective sintering additive is used, and thus, is basically lower than the coercivity of the raw powder, as indicated in . Therefore, the key to producing high-coercivity sintered magnets of these materials is to prepare a high-coercivity powder as the raw powder.
A sintered magnet is commonly produced from single crystal powder in order to align the crystalline orientation of the magnet with the axis of easy magnetization. Single crystal magnetic powders are previously prepared through a polycrystalline ingot casting process followed by a mechanical pulverizing process such as ball milling and jet milling. However, as shown in , the coercivity of pulverized Sm2Fe17N3 powders is about 1 MA/m, which is significantly inferior to that of Nd2Fe14B sintered magnets (up to 2 MA/m). The pulverized powders have a polygonal shape with sharp corners and surface damage which are prone to the formation of reverse magnetic domains, resulting in low coercivity.
Figure 6. Dependencies of coercivity on particle size for Sm2Fe17N3 fine powders prepared by the mechanical pulverization and reduction diffusion methods [Citation11,Citation41–43]
![Figure 6. Dependencies of coercivity on particle size for Sm2Fe17N3 fine powders prepared by the mechanical pulverization and reduction diffusion methods [Citation11,Citation41–43]](/cms/asset/6e184643-114c-44f0-8131-d428eb271c9c/tsta_a_1875791_f0006_oc.jpg)
As an alternative to mechanical pulverization techniques, Nichia Corporation invented a chemical synthesis process for direct preparation of single crystal Sm2Fe17N3 fine powders based on a conventional reduction diffusion method, which had been used to synthesize coarse polycrystalline powders [Citation11]. As shown in , in this advanced reduction diffusion (RD) method, Sm2Fe17N3 powders are obtained by sequential H2-reduction and Ca-reduction of a complex oxide precursor prepared by a wet synthesis method. This process also includes a water washing step to remove CaO generated as a byproduct in Ca-reduction before the ammonia nitridation step. Because the powders are not pulverized, single crystal powders synthesized by this process have the features of spherical-shaped particles and high crystallinity. Kume et al. synthesized single crystal Sm2Fe17N3 powders with a size of 2 μm that significantly increased coercivity to 1.5 MA/m [Citation11]. Nevertheless, further improvement of coercivity should be possible, as this is still only about 7% of the anisotropic magnetic field.
The coercivity of permanent magnets is well known to be dependent on particle size. That is, coercivity increases in inverse proportion to the logarithm of the square of the particle size [Citation40]. This law should naturally apply to Sm2Fe17N3, and in fact, pulverized Sm2Fe17N3 powders display particle size dependency of coercivity, as shown in . Hirayama and Okada carried out a development project to reduce the synthesis temperature in the RD process for particle size refinement, and succeeded in reducing the synthesis temperature to 900°C from the conventional temperature of 1050°C [Citation41,Citation42]. As a result, the particle size was refined to the submicron size, as seen in , and coercivity was improved by 1.85 MA/m due to the above-mentioned particle size dependency effect. As shown in , the obtained powders have an equiaxed shape and narrow particle size distribution, which would also contribute to high coercivity.
Figure 8. Scanning electron microscopy (SEM) micrograph of Sm2Fe17N3 fine powder synthesized by reduction diffusion process [Citation42]
![Figure 8. Scanning electron microscopy (SEM) micrograph of Sm2Fe17N3 fine powder synthesized by reduction diffusion process [Citation42]](/cms/asset/b6ffd145-dc4b-48de-a0d4-b7e08e0c4cfa/tsta_a_1875791_f0008_b.gif)
Okada et al. found that a Sm-rich Sm-Fe phase forms on the surface of Sm2Fe17 particles in the Ca-reduction process and adversely affects coercivity [Citation43], but gentle oxidation treatment before washing is effective to prevent the formation of this Sm-rich phase. This treatment successfully increased the level of particle size dependency of coercivity by 0.4 MA/m, which appears in as a sudden increase in coercivity from 2017 to 2018. At present, Sm2Fe17N3 powder expresses coercivity of up to 2.55 MA/m [Citation44], which is higher than that of state-of-the-art Nd2Fe14B magnets such as hot-deformed magnets [Citation45]. In recent years, KCl salt was mixed as a flux with the reductant Ca in order to dilute the density of reaction atoms in the reaction field, which suppresses particle growth and particle condensation. This new approach resulted in the development of a SmCo5 powder with a huge coercive force of 5.7 MA/m [Citation46].
As outlined above, the RD process is continuing to evolve year by year, and is expected to lead to powders with even huger coercivity for rare-earth magnets. However, it is not possible to avoid surface oxidation with powders prepared by the current RD process due to the water washing step. Thus, in order to apply RD powder as the raw powder for sintered magnets, it is necessary to develop a technique for suppressing surface oxidation.
3.2. Physical synthesis approaches for nanoparticles
Particle size refinement is very effective for improving coercivity, as indicated in the prior section. Particle size refinement is also expected to be effective for promoting sintering of low-sinterable materials such as Sm2Fe17N3 and metastable magnets. Therefore, preparation of nanosized particles of rare-earth magnets would overcome both the problems of coercivity and densification at once. Furthermore, nanoparticles of rare-earth magnets are expected to be applied as the raw powder for hard phases in nanocomposite magnets, which are desired as an ultimate magnet [Citation47].
Several reports have described efforts to prepare nanoparticles of rare-earth magnets. Hadjipanayis’ group prepared SmCo5 and Nd2Fe14B nanoparticles with a particle size of less than 10 nm by surfactant-assisted ball milling, realizing coercivities of up to 1.48 and 0.3 MA/m, respectively [Citation48,Citation49]. The same group also successfully produced Sm-Co nanoparticles with a size of several nanometers by a physical synthesis approach using a cluster deposition method, but the obtained coercivity was very low [Citation50].
Currently, Hirayama et al. are developing a new synthesis technique to produce rare-earth magnet nanoparticles using a thermal plasma method. In the thermal plasma method, raw coarse powder is evaporated in an induction plasma flame having a temperature of 10 000 K, as shown in [Citation51,Citation52], after which the metal vapor that emerges from the plasma flame due to the downdraft undergoes a nucleus generation/aggregation process and finally forms nanoparticles. Here, the nanodroplets emitted from the plasma flame solidify under ultra-fast quenching at 105 K/s. Since this cooling rate is close to that of melt-spinning (104 to 106 K/s) [Citation53], metastable phase nanoparticles can also be expected. When producing easily oxidizable rare-earth alloy nanoparticles, it is essential to avoid exposure to even a small amount of oxygen.
Figure 9. Schematic of low-oxygen thermal plasma system for synthesizing rare-earth magnet powders [Citation54]
![Figure 9. Schematic of low-oxygen thermal plasma system for synthesizing rare-earth magnet powders [Citation54]](/cms/asset/bea32b04-355a-4fdb-b4f2-305e0d934e20/tsta_a_1875791_f0009_oc.jpg)
Previous study demonstrated that it is possible to prevent surface oxidation of nanoparticles by covering part of the thermal plasma device with a glovebox to create an extremely low-oxygen atmosphere [Citation54]. shows an example of the rare-earth magnet nanoparticles synthesized by this method, in this case, Sm-Co alloy nanoparticles having an average particle size of 70 nm. In addition, nanoparticles of Y-Fe, Nd-Fe, and Sm-Fe alloys have been also produced. In particular, synthesis of metastable phase nanoparticles of a TbCu7 type alloy has been confirmed [Citation55].
4. Summary
Sm2Fe17N3 and metastable materials such as TbCu7 type compounds have attracted attention as alternatives to Nd2Fe14B magnets, but in order to realize practical magnets of these materials, it is necessary to overcome process-related problems such as the difficulty of sintering and low coercivity. Various powder preparation and powder metallurgy approaches have been attempted to overcome these problems. Although efforts to develop a sintering technique for Sm2Fe17N3 have struggled against thermal decomposition and coercivity deterioration for many years, low-oxygen powder metallurgy approaches for overcoming coercivity deterioration have been discovered recently, opening up the possibility of realizing Sm2Fe17N3 sintered magnets. However, a high-coercivity powder is required for production of sintered magnets of these magnetic materials because liquid phase sintering is not possible. As new fine powder preparation techniques, chemical and physical synthesis approaches such as reduction diffusion and thermal plasma processes are being developed, with results surpassing the conventional mechanical pulverization process. In particular, the reduction diffusion process enables direct production of high-quality fine powders of Sm2Fe17N3 which exhibit a huge coercivity of 2.5 MA/m.
Thus, the development of new powder processes is creating the high coercive Sm2Fe17N3 powders and bulk magnets which have been difficult so far. In addition, these new processes can also be expected to be applied to metastable TbCu7-type magnets. On the other hand, problems such as insufficient sintering densification still remain to be solved, but the challenge of a new powder process is expected to open up new paths for high-performance rare-earth permanent magnets.
Disclosure statement
No potential conflict of interest was reported by the authors.
Additional information
Notes on contributors
Kenta Takagi
Kenta Takagi is a senior researcher at the National Institute of Advanced Industrial Science and technology. He obtained his bachelor’s degree and master’s degree in Materials Science from Tohoku University in 1995 and 1997, respectively. Later he obtained his Doctor of Engineering from Tohoku University in 2003. His latest research interests revolve around permanent magnets. In particular, he is motivated in studying on powder processing for lowsinterable and metastable magnetic alloys.
References
- Seo Y, Morimoto S. Comparison of dysprosium security strategies in Japan for 2010-2030. Resour Policy. 2014;39:15–20.
- Watanabe Y. Rare metal text 1. Shigen Chishitsu. 2010;60: 103–122. Japanese.
- Iriyama T, Kobayashi K, Imaoka N, et al. Effect of nitrogen content on magnetic properties of Sm2Fe17Nx (0<x<6). IEEE Trans Magn. 1992;28:2326–2331.
- Coey JMD, Sun H. Improved magnetic properties by treatment of iron-based rare earth intermetallic compound in anmonia. J Magn Magn Mater. 1990;87(3):251–254.
- Sakurada S, Tsutai A, Hirai T, et al. Structural and magnetic properties of rapidly quenched (R,Zr)(Fe,Co)10Nx. J Appl Phys. 1996;79(8):4611–4613.
- Ohashi K, Tawara Y, Osugi R, et al. Magnetic properties of Fe-rich rare-earth intermetallic compounds with a ThMn12 structure. J App Phys. 1988;64(10):5714–5716.
- Hirayama Y, Takahashi YK, Hirosawa S, et al. Intrinsic hard magnetic properties of Sm (Fe1-xCox)12 compound with ThMn12 structure. Scripta Mater. 2017;138:62–65.
- Hirayama Y, Takahashi YK, Hirosawa S, et al. NdFeNx hard magnetic- compound with high magnetization and anisotropy. Scripta Mater. 2015;95:70–72.
- Schnitzke K, Schultz L, Wecker J, et al. High coericivity in Sm2Fe17Nx magnets. Appl Phys Lett. 1990;57:2853–2855.
- Takagi K, Nakayama H, Ozaki K, et al. Fabrication of High- performance Sm–Fe–N isotropic bulk magnets by a combination of high-pressure compaction and current sintering. J Magn Magn Mater. 2012;324(7):1337–1341.
- Kime M, Tomimoto T, Yamamoto S, et al. Progress and prospects of SmFeN magnets. J Jpn Inst Met Mater. 2012;76(1):107–111. Japanese. .
- Katter M, Wecker J, Schultz L. Structural and hard magnetic properties of rapidly solidified Sm–Fe–N. J Appl Phys. 1991;70(6):3188–3196.
- Liu W, Wang Q, Sun XK, et al. Metastable Sm-Fe-N magnets prepared by mechanical alloying. J Magn Magn Mater. 1994;131(3):413–416.
- Takagi K, Jinno M, Ozaki K. Preparation of TbCu7-type Sm-Fe powders by low-temperature HDDR treatment. J Magn Magn Mater. 2018;454:170–175.
- Singleton EW, Strzeszewski J, Hadjipanayis GC, et al. Magnetic and structural properties of melt-spun rare-earth transition-metal intermetallics with ThMn12 structure. J Appl Phys. 1988;64(10):5717.
- Dirba I, Sepehri-Amin H, Ohkubo T, et al. Development of ultra-fine grain sized SmFe12-based powders using hydrogenation disproportionation desorption recombination process. Acta Materialia. 2019;165:373–380.
- Machida K, Nakatani Y, Adachi G. High-pressure sintering characteristics of Sm2Fe17Nx powder. Appl Phys Lett. 1993;62(22):2874–2876.
- Ito S, Kikuchi M, Fujii T, et al. HIP sintering and magnetic properties of Sm2Fe17N3 with Zn additive. J Magn Magn Mater. 2004;280:15–21.
- Zhang DT, Yue M, Zhang JX. Study on bulk Sm2Fe17Nx sintered magnets prepared by spark plasma sintering. Powder Metal. 2007;50(3):215–218.
- Takagi K, Nakayama H, Ozaki K. Microstructural behavior on particle surfaces and interfaces in Sm2Fe17N3 powder compacts during low-temperature sintering. J Magn Magn Mater. 2012;324(15):2336–2341.
- Hu B-P, Rao X-L, Xu J-M, et al. Magnetic properties of sintered Sm2Fe17Ny magnets. J Appl Phys. 1993;74(1):489–494.
- Oda H, Kondo K, Uchida H, et al. A samarium-iron nitride magnet fabricated by shock-compaction technique. Jpn J Appl Phys. 1995;34:L35–37.
- Mashimo T, Huang X, Hirosawa S, et al. Magnetic properties of fully dense Sm2Fe17N3 magnets prepared by shock compression. J Magn Magn Mater. 2000;210(1–3):109–120.
- Chiba A, Ooyabu K, Morizono Y, et al. Shock comsolidation of Sm-Fe-N magnetic powders and magnetic properties. Mater Sci Forum. 2004;449-452:1037–1040.
- Maki T, Sugimoto S, Kagotani T, et al. Microstructure and magnetic properties of Sm-Fe-N thick films produced by the aerosol deposition method. Mater Trans. 2004;45(2):369–372.
- Saito T, Fukui M, Takeishi H. Sm-Fe-N bulk magnets produced by compression shearing method. Scripta Mater. 2005;53(10):1117–1121.
- Saito T, Kitazima H. Hard magnetic properties of anisotropic Sm-Fe-N magnets produced by compression shearing method. J Magn Magn Mater. 2011;323(16):2154–2157.
- Matsuura M, Nishijima Y, Tezuka N, et al. Increase of energy products of Zn-bonded Sm-Fe-N magnets with low oxygen content. J Magn Magn Mater. 2018;467:48–64.
- Takagi K, Soda R, Jinno M, et al. Possibility of high-performance Sm2Fe17N3 sintered magnets by low-oxygen powder metallurgy process. J Magn Magn Mater. 2020;506:166811.
- Otani Y, Moukarika A, Sun H, et al. Metal bonded Sm2Fe17N3−δ magnets. J Appl Phys. 1991;69(9):6735–6737.
- Kuhrt C, Cerva H, Shultz K. Nanostructure of mechanically alloyed zinc-bonded Sm2Fe17Nx magnets. Appl Phys Lett. 1994;64(6):797–799.
- Machida K, Noguchi K, Nishimura M, et al. High-performance alloyed in metal-bonded magnets produced from Zn/Sm2Fe17Nx powders. J Appl Phys. 2000;87,(9):5317–5319.
- Imaoka N, Koyama Y, Nakao T, et al. High electrical resistance composite magnets of Sm2Fe17N3 powders coated with ferrite layer for high frequency application. J Appl Phys. 2008;103(7):07E129.
- Saito T, Deguchi T, Yamamoto H. Magnetic properties of Sm-Fe-N bulk magnets produced from Cu-plated Sm-Fe-N powder. AIP Adv. 2017;7(5):056204.
- Matsunami R, Matsuura M, Tezuka N, et al. Preparation of Sm-Fe-N bulk magnets with high maximum energy products. J Magn Soc Jpn. 2020;44(3):64–69.
- Yamaguchi W, Soda R, Takagi K. Metal-coated Sm2Fe17N3 magnet powder with an oxide-free direct metal-metal interface. J Magn Magn Mater. 2020;498:166101.
- Makita K, Hirosawa S. Coercivity of Zn evaporation-coated Sm2Fe17Nx fine powder and its bonded magnets. J Alloys Compd. 1997;260(1–2):236–241.
- Fukunaga H, Aikawa T, Nagaoka S, et al. Improvement in hard magnetic properties of rapidly quenched Sm-Fe-N flakes by Zn-coating. J Magn Magn Mater. 1996;157(158):105–106.
- Yamaguchi W, Takagi K. Effect of nonmagnetic overlay metal on coercivity Sm2Fe17N3 magnet powders. J Magn Magn Mater. 2020;516:167327.
- Ramesh R, Thomas G, Ma M. Magnetization reversal in nucleation controlled magnets. II. Effect of grain size and size distribution on intrinsic coercivity of Fe‐Nd‐B magnets. J App Phys. 1988;64(11):6416–6423.
- Hirayama Y, Panda AK, Okubo T, et al. High coercivity Sm2Fe17N3 submicron size powder prepared by polymerized-complex and reduction–diffusion process. Scripta Mater. 2016;120:27–30.
- Okada S, Suzuki K, Node E, et al. Preparation of submicron-sized Sm2Fe17N3 fine powders with high coercivity by reduction-diffusion technique. J Alloy Compd. 2017;695:1617–1623.
- Okada S, Node E, Takagi K, et al. Synthesis of Sm2Fe17N3 powder having a new level of high coercivity by preventing decrease of coercivity in washing step of reduction-diffusion process. J Alloy Compd. 2019;804:237–242.
- Press release of national institute of advanced industrial science and technology. Available from: https://www.aist.go.jp/aist_j/press_release/pr2019/pr20191021/pr20191021.html [Accessed 21 Oct 2019].
- Sepehri-Amin H, Liu L, Okubo T, et al. Microstructure and temperature dependent of coercivity of hot-deformed Nd–Fe–B magnets diffusion processed with Pr–Cu alloy. Acta Mater. 2015;99(15):297–306.
- Dong Y, Zhang T, Xia Z, et al. Dispersible SmCo5 nanoparticles with huge coercivity. Nanoscale. 2019;11(36):16962.
- Balamurugan B, Sellmyer DJ, Hadjipanayis GC, et al. Prospects for nanoparticle-based permanent magnets. Scripta Mater. 2012;67(6):542–547.
- Akdogan NG, Hadjipanayis GC, Sellmyer DJ. Anisotropic Sm-(Co,Fe) nanoparticles by surfactant-assisted ball milling. J Appl Phys. 2009;105(7):07A710.
- Akdogan NG, Hadjipanayis GC, Sellmyer DJ. Novel Nd2Fe14B nanoflakes and nanoparticles for the development of high energy nanocomposite magnets. Nanotechnology. 2010;21:1–5.
- Stoyanov S, Skumryev V, Zhang Y, et al. High anisotropy Sm-Co nanoparticles: preparation by cluster gun technique and their magnetic properties. J Appl Phys. 2003;93(10):7592–7594.
- Kambara M, Kitayama A, Homma K, et al. Nano-composite Si particle formation by plasma spraying for negative electrode of Li ion batteries. J Appl Phys. 2014;115:143302.
- Pant A, Seth T, Raut VB, et al. Preparation of nano aluminium powder (NAP) using a thermal plasma: process development and characterization. Cent Eur J Energ Mater. 2016;13(1):53e71.
- Tkatch VI, Limanovskii AI, Denisenko SN, et al. The effect of the melt-spinning processing parameters on the rate of cooling. Mater Sci Eng A. 2002;323(1–2):91–96.
- Hirayama Y, Suzuki K, Yamaguchi W, et al. Cold welding behavior of fine bare aluminum powders prepared by new low oxygen induction thermal plasma system. J Alloy Compd. 2018;768:608–612.
- Hirayama Y, Sigeta M, Liu Z, et al. Anisotropic Nd-Fe ultrafine particles with stable and metastable phases prepared by induction thermal plasma. J Alloy Compd 2021. (submitted).
- Hirayama Y, Miyake T, Hono K. Rare-earth lean hard magnet compound NdFe12N. JOM. 2015;67(6):1344–1349.
- Web site of Hitach Metals Ltd. Available from: http://www.hitachi-metals.co.jp/products/auto/el/pdf/nmx.pdf [Accessed May 1999].
- Yamamoto H, Kosukekawa M, Nishio H, et al. Technical Report: properties, stability and applications of high-performance permanent magnets. Tokyo: The Institute of Electrical Engineers of Japan; 1999. Japanese.
- Takagi K. Development of powder metallurgy process for realization of Sm-Fe-N sintered magnet. KINZOKU. 2020;90: 889–897. Japanese.