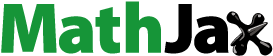
ABSTRACT
Natural cellulose fibers have a great potential for the development of new alternative reinforcement materials that are used in various polymer composite applications. In this study, waru tree trunk fiber was extracted and treated with NaOH and Silane. Meanwhile, the characteristics of chemical, morphological, mechanical, and fiber surfaces were determined through composition analysis, Fourier transforms infrared (FTIR), scanning electron microscope (SEM), and single fiber test. The results showed that the cellulose content increased with the addition of silane treatment which was supported by the high crystalline index of 63.02% waru bark fiber. Based on this treatment, the tensile strength of the single fiber had the highest value of 243.94 Mpa. Therefore, this fiber has the potential as a new reinforcement development in polymer-based products.
摘要
天然纤维素纤维在开发用于各种聚合物复合材料应用的新型替代增强材料方面具有巨大潜力. 在本研究中, 提取了华鲁树干纤维, 并用氢氧化钠和硅烷处理. 同时, 通过成分分析, 傅立叶变换红外光谱 (FTIR), 扫描电子显微镜 (SEM) 和单纤维测试, 确定了化学, 形态, 机械和纤维表面的特征. 结果表明, 纤维素含量随着硅烷处理的添加而增加, 这是由63.02%的瓦鲁树皮纤维的高结晶指数支持的. 在此基础上, 单根纤维的拉伸强度最高, 为243.94mpa. 因此, 这种纤维在聚合物基产品中具有作为一种新的增强剂开发的潜力.
Introduction
Recently, the increase in natural fiber products has attracted a lot of studies due to its environmental sustainability and the emission of new energy toward more environmentally friendly products. In the current COVID-19 pandemic situation, the need for mask materials increased which leads to high demand for cotton and synthetic fiber (Sabarinathan et al. Citation2020). Meanwhile, the long-time effect of using synthetic fiber in medical applications such as the production of masks and other surgical equipment causes environmental pollution. Therefore, the search for other alternative materials such as the use of cellulose fiber has greatly increased (Reis et al. Citation2020).
The use of natural fiber as reinforcement material has also been applied in various aerospace, transportation, and construction product industries such as hybrid crash box materials in high-performance and energy-absorbing tube devices (Supian et al. Citation2020). Meanwhile, the application of natural fiber in reinforcement materials is due to its lower energy consumption compared to synthetic fiber (Rojo et al. Citation2015). Furthermore, the abundance of natural resources also supports the development of natural fiber as reinforcement in polymer composites (Rybin, Utkin, and Baklanova Citation2013). Natural fibers are not only environmentally friendly, but also have other advantages which include lightweight, low price, abundant, easy to obtain, biodegradable, and high mechanical properties (Xue, Tabil, and Panigrahi Citation2007). This provides more interest in studying and considering new natural fiber alternatives as a substitute.
The abundance of cellulose fiber in tropical countries provides an opportunity to explore new reinforcement materials (Kumari, Kumar, and Kumar Citation2014). Since each geographical location has a different characteristic, therefore, it is important to find new reinforcement for polymer matrices. Previous studies had shown that various new natural fibers that have the potential as reinforcement include cantala fiber (Raharjo et al. Citation2018), Bark of Dichrostachys Cinerea (Baskaran et al. Citation2018), mendong fiber (Suryanto et al. Citation2019), guaruman fiber (Reis et al. Citation2020), fishtail palm fiber (Sabarinathan et al. Citation2020), and Pennisetum Orientale grass fiber (Vijay et al. Citation2021). Moreover, the waru tree (Hibiscus tiliaceus) () is commonly found on the coast of Indonesia as a shade tree. The trunk of this plant is used commercially for netting, bags, ropes, and various handicrafts due to its fiber and cellulose content. Similarly, the fiber from waru bark () is known to be strong and tough (Wirawan et al. Citation2020).
The most basic problem with using reinforcement in the matrix is the fiber wettability in the phase which helps to improve the composite characteristics (Senthamaraikannan and Kathiresan Citation2018). This wettability is treated by chemically modifying the surface (Vijay et al. Citation2019). Moreover, several studies have shown that surface modification improves the mechanical, physical, and chemical properties of developed synthetic fiber and matrices (Pankow et al. Citation2019).
Common chemical efforts made to improve fiber interface characteristics consist of various modifications such as alkali treatment, acetality, peroxide, and silane (Kabir et al. Citation2012). Meanwhile, the NaOH treatment was able to increase the roughness on the surface which leads better wettability of the fiber and matrix (Sood and Dwivedi Citation2018). This shows that chemical treatment can remove content such as wax and pectin on the fiber surface which improves the bonding strength (Herlina Sari et al. Citation2018). Furthermore, good wettability enhances the bonding of the fiber and the polymer composite matrix. Although chemical treatment provides a surface bond, it reduces crystalline cellulose to an amorphous material. Moreover, the polar and hydrophilic nature of natural fiber forces its hydrophobicity to require the addition of silane (Chen, Helmi Muhammad, and Ahmad Citation2021). Chemical modification with the addition of a silane coupling agent reduces the hydroxyl groups in the hydrophilic fiber (Elanchezhian et al. Citation2018). This treatment enhances the adhesion of the natural fiber and polymer matrix by forming chemical bonds, which produce silanol groups reaction (Si-OH) and also serve as interfacial agents (Yanjun et al. Citation2010).
The exploration of fiber from natural high-strength materials as reinforcement in polymer composites leads to the development of bark waru for sustainable applications. Therefore, this study examines fiber extraction from the bark of the waru tree (Hibiscus tiliaceus). The fiber was treated, modified chemically, and provided with a silane coupling agent. Furthermore, the modifications due to fiber treatment were characterized by Fourier Transform InfraRed (FT-IR) spectroscopy, X-Ray Diffraction (XRD), Scanning Electron Microscope (SEM), and single fiber tensile test.
Material and method
Fiber material
The fiber was obtained from waru tree farmers from Tulungagung, Indonesia. Meanwhile, fiber extraction started with cutting, cleaning, and separating the bark from stems, leaves, and flowers. After the bark is separated, it was extracted by soaking the fiber in water for 15 to 20 days and was washed thoroughly until the aroma is gone. Fiber with perfect quality, unique color, natural, and shiny is seen after drying.
NaOH alkaline treatment
The alkaline treatment of NaOH was used to remove the waxy layer on the fiber surface. This process began by soaking the bark fiber of the waru tree with 6% by weight of the NaOH solution at room temperature 27°C for 120 minutes. The soaked fiber was rinsed with running water until a neutral pH of 7 is reached, and was air-dried for 24 hours before heating in an oven for 2 hours at 40°C. The reaction of NaOH treatment on waru bark fiber is shown as follows:
Surface modification of NaOH-Silane
The surface modification was carried out by soaking the fiber which had been treated with alkaline NaOH in a methacryloxtrimetoxysilane solution for 4 hours. When immersed in silane, a concentration of 0.75% was used with a mixture of distilled water. The pH of the solution was adjusted by adding acetic acid until a concentration of pH 3 to 4 is reached. Furthermore, the wet fiber was dried at room temperature for 24 hours and heated in an oven at 40°C for 2 hours. The reaction of NaOH-Silane treatment on waru bark fiber is shown as follows:
(2)
Chemical composition analysis
Chemical analysis was conducted to determine the lignin and cellulose content of waru bark fiber extracted and surface modification. In this analysis, the percentage of cellulose and hemicellulose was determined according to ASTM D1103-60 while lignin was based on SNI 0492–2008.
Fourier transform infrared (FTIR) analysis
FTIR testing was conducted to determine the changes in chemical composition such as lignin, cellulose, and hemicellulose on the modified fiber surface (extraction, NaOH, and NaOH-Silane treatment). Meanwhile, 5 grams of pulverized fiber in powder was mixed with 95% KBr and was inserted into the FTIR machine disk. Each spectrum was seen by scanning 32 times at a spatial resolution of 2 cm−1 within the range of 400 to 4000 cm−1 wavenumbers.
X-Ray diffraction (XRD) analysis
This analysis was conducted to obtain particle size and determine single crystals from waru bark fiber that has been treated with alkaline NaOH and NaOH-Silane surface treatments. The X-ray pattern was obtained with 30 kV Cu-kα radiation at 17.5 mA. Meanwhile, step size and scan of 0.075° and 2.5/s were used at readings of approximately 10 to 60°. The degree of crystallinity is expressed in terms of CI (crystallinity index) using the equation:
Where CI is the crystallinity index, Cr shows the crystallinity and I101 & I002 is the crystalline intensity. Also, I101 and I002 are the maximum peak intensities of the crystalline and amorphous parts, respectively. In the sample plane, I002 is associated with the Miller index (002) in the range 2θ = 22–23°, while I101 is associated with the Miller index (001) at approximately 2θ = 18°
SEM analysis
SEM (Scanning Electron Microscopy) analysis was used to observe morphology on the surface of the extracted specimen, NaOH, and NaOH-Silane treatments. These observations were made with the SEM – EDAX FEI Type inspects S-50 tool to produce high-resolution results using thermal emission electron optics.
Single fiber tensile test
This test was conducted to determine the tensile strength of a single fiber by cutting and selecting the same size with a length of 100 mm and width of 3 mm based on the ASTM C 1557–03 standard as shown in . The selected and cut fiber was bonded to paper using epoxy resin to facilitate the attachment of the clamps to the tensile testing machine. Meanwhile, the load cell given is 10 kN and the crosshead speed is 5 mm/min at room temperature. Furthermore, an average of 10 samples was tested to minimize experimental data errors (Gapsari et al. Citation2021).
Results and discussion
Chemical analysis
The chemical analysis aims to determine the main elements in waru bark fibers such as lignin, hemicellulose, and cellulose. Meanwhile, the high cellulose content affects the strength, stiffness, and stability of natural fibers (Jayaramudu, Guduri, and Varada Rajulu Citation2010). Furthermore, the content of untreated, NaOH, and NaOH-Silane treated waru bark fiber is shown in . The results showed that the fibers with NaOH treatment were able to reduce and decompose the lignin as well as hemicellulose contents in natural fibers, while NaOH-silane treatment increased the cellulose content.
Figure 3. Chemical analysis of waru bark fibers without treatment, with NaOH treatment and NaOH-Silane treatment.
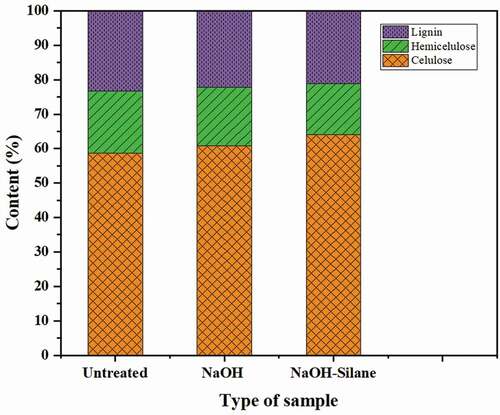
In chemical treatment, the lignin and hemicellulose content that covers the fiber is easily eroded and partly lost because it is amorphous, while cellulose is difficult to dissolve due to its crystalline phase (Kabir et al. Citation2012). Meanwhile, the results showed that the NaOH 6% and Silane 0.75% increased the fiber cellulose to 64.01% compared to the NaOH or without treatment. Similarly, the addition of silane cleans the surface of the cellulose fiber and leads to better strength (Asim et al. Citation2016).
Treatment with NaOH leads to the loss of lignin and hemicellulose content on the surface of natural fibers. shows that the chemical characteristics of the waru bark fibers without treatment have cellulose (hemicellulose (18%) and lignin (23.35%) content higher than the fiber treated with NaOH and NaOH-Silane. These high levels of hemicellulose cause disintegration and reduces strength while high levels of lignin provide a smooth surface which reduces fiber bonding to the polymer matrix. (Indran, Edwin Raj, and Sreenivasan Citation2014).
Table 1. Analysis of the main constituents of new waru bark fibers with various other natural fibers.
Fourier transform infrared (FTIR) analysis
shows the FTIR spectrum of untreated, NaOH, and NaOH-Silane treated waru bark fibers. These results show that waru bark fiber without NaOH treatment has an – OH functional group at wavenumber of 3323.77 cm−1 and C-H stretch (C-H stretching) at a wavenumber of 2921.56 cm−1. Since the wave number stretch for the – OH group is 3100–3600 cm−1, this shows that phenol, alcohol, and water groups are present. Meanwhile, the presence of these functional groups comes from cellulose, hemicellulose, and lignin. Similarly, the C–H number strain between 2500 to 3000 cm−1 also comes from cellulose and hemicellulose (Sabarinathan et al. Citation2020). After the fiber was treated with alkali by giving NaOH, there was a shift in the wavenumber at 3320.32 cm−1, due to the lack of lignin content which has an -OH group. The effect of the NaOH treatment is to remove lignin, hemicellulose, and other impurities. The reduced level of lignin causes the nonpolar level to decrease and strengthen the interfacial adhesion of the fiber (Zhou, Cheng, and Jiang Citation2014). Furthermore, the addition of silane caused a change in the -OH functional group at 3334.93 cm−1. With NaOH-Silane treatment, the intensity of the waves became smaller than the fiber without treatment.
The peak at wavenumber 2921.56 cm−1 shows the presence of the CH2 symmetrical stretching functional group, which is found in various fibers. In the NaOH and NaOH-silane treatment samples, the intensity decreased at wave number 2893.09 cm−1 and 2891.51 cm−1, respectively. This is due to the reduction of impurities on the fiber surface because of the NaOH and NaOH-silane treatments. Furthermore, loss of hemicellulose impurities was also shown by the presence of an invisible wave number on the carbonyl group (C = O) at a wavenumber of 1719.02 cm−1 and a water residue of 1637.81 cm−1 that have bonded with cellulose (Sawpan, Pickering, and Fernyhough Citation2011).
The three samples have wavenumbers between 1500 and 1000 which showed the presence of functional groups -CH, -OH, and CH2 bending that indicated the presence of hemicellulose. Furthermore, the chemical treatment reduced the wave intensity which led to a decrease in the hemicellulose on the fiber surface. Meanwhile, waru bark fiber with silane addition showed a sharp peak at 896.07 cm−1 due to the vibration of silanol groups (Tran, Charles Bénézet, and Bergeret Citation2014).
X-Ray diffraction (XRD) analysis
The amount of crystallinity of waru bark fiber with or without chemical treatment is seen from the peak intensity as shown in the results of the X-Ray Diffraction analysis in .
Figure 5. Analysis of the results of X-Ray diffraction waru bark fiber (a) untreated (b) NaOH treated (c) NaOH-Silane treated.
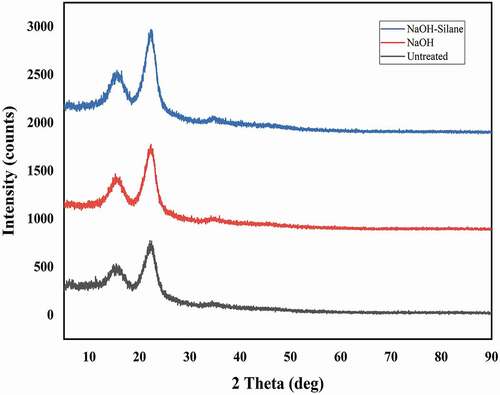
The results showed that there were two high peaks at an angle of 2θ 15.35 = 534 and 2θ 22.38 = 770 (without treatment). Meanwhile, the low angle (I101) is part of the amorphous hibiscus fiber which consists of lignin, hemicellulose, pectin, and wax, while the higher angle (I002) is the crystalline component of hibiscus fiber. These two different peak intensities show that the waru bark fiber is semi-crystalline (Gapsari et al. Citation2021). With the treatment, the peak angle continues to shift and increase in intensity and the angle of 2θ 15.20 = 1470.4 and 2θ 22.28 = 1777.4 is continued in the NaOH treatment. Meanwhile, in the NaOH-silane treatment, the angle was 2θ 15.50 = 2545 and 2θ 22.25 = 2968.8. This shift and increase in intensity made it possible for some of the fibers to be exfoliated, therefore, showing uniform dispersion in the biocomposite matrix (Katerina et al. Citation2014).
shows a graph of the crystallinity index of untreated, NaOH, and NaOH-Silane treated hibiscus bark fibers. From each sample, high diffraction intensity indicates the increasing number of crystalline cellulose contained in the fiber. Furthermore, the crystallinity of cellulose fiber with NaOH silane treatment had the highest index value (63.02%) greater than fiber with NaOH (57.18%) or without treatment (56.54%,). The increase in crystallinity index is due to the greater size of crystalline cellulose and the loss of amorphous fiber parts such as hemicellulose, lignin, and pectin so that the surface of the waru bark fiber is free from impurities. During the treatment process, alkali and hydrated water penetrate the cellulose fiber and develop its crystalline structure. Meanwhile, various models of the crystal structure of the cellulose are due to the confirmation of intramolecular hydrogen bonds through the hydroxyl groups of the fiber morphology and on the packaging of the cellulose chains. This has also been observed in various fibers of previous studies (Suryanto et al. Citation2019) (Vijay et al. Citation2021) (Sabarinathan et al. Citation2020).
SEM analysis
The morphology of the treated and untreated waru bark fiber surface is shown in .
Figure 7. Surface morphology of waru bark fiber (a) untreated (b) NaOH treated (c) NaOH-Silane treated.
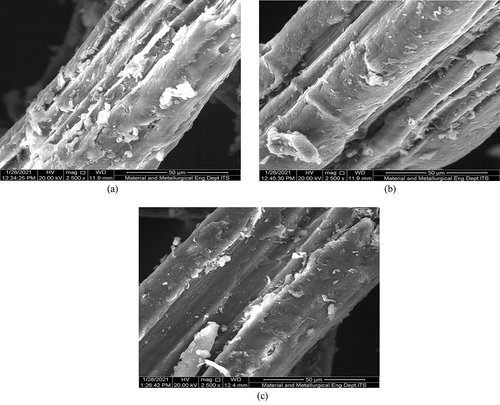
The morphology of the fiber soaked in alkali and silane solution in showed that it has a cleaner surface, compared to the untreated in 7a and the alkali-treated in 7b. Meanwhile, shows that the untreated fiber has a wax-like layer surface and there is dirt attached to it. Similarly, in the alkali-treated fiber, the surface topography is rough because the outer layer was peeled off and many compounds dissolved in the alkaline solution. This shows that non-cellulosic materials such as lignin, hemicellulose have been lost and the surface is cleaner and rougher than the fiber without treatment. In the NaOH treatment on waru bark fiber, there is still a little dirt attached to the cell wall, the pores are opened, irregular, and no uniformity. Therefore, the roughness of the fiber surface enables good adhesion to the matrix. When observed with the imageJ, it found was the diameter become smaller due to the chemical treatment of the fiber. (Herlina Sari et al. Citation2018) (Suryanto et al. Citation2019). Furthermore, the fiber with the addition of silane in showed that the surface is perfectly clean and there is no dirt attached to the cell wall. The cross-section of the fiber tends to layer and form an extended rough groove and the pores shrink is covered by silane to look uniform. This configuration is beneficial because it affects the interfacial bonding strength of the fiber and matrix.
Single fiber tensile test
shows the tensile strength behavior of the test results of a single fiber of hibiscus skin. The chemical treatment of natural fibers with the right concentration has a good impact on the surface bond and mechanical properties of stiffness. From , the chemical treatment of NaOH-silane has the highest mechanical properties of 243.94 Mpa due to the high cellulose content, while the increase in the crystalline index was due to the reduced hemicellulose. Furthermore, silane immersion has an impact on the chemical bonds and the embedded amino groups of silane on the fiber surface, thereby increasing the strength of the hibiscus fiber. The decrease in hemicellulose is shown by a reduction in the average diameter of the fiber. This is also supported by the results of SEM observations where the fiber appears clean. Similar observations were also found in previous studies on the silane treatment of cantala and fishtail fiber (Raharjo et al. Citation2018) (Sabarinathan et al. Citation2020).
Table 2. Peak data of the Fourier transform infrared wave number of waru fiber.
Table 3. Tensile strength value of waru bark fiber.
The fiber that was only treated with NaOH decreased with a strength value of 152.77 MPa compared to the fiber without treatment. There is a possibility that excessive NaOH treatment reduces lignin, hemicellulose, and damage cellulose which are the main constituents of the strength of waru bark fiber. When the alkali treatment is directly applied to the surface roughness and the opening of the OH groups on the cellulose, it increases the interaction between the fiber and silane, which leads to a covalent bond between the silane groups and the matrix chain. Furthermore, the waru without treatment has a higher tensile strength value of 207.30 Mpa than fiber with NaOH. This high fiber content is due to other non-cellulose constituents in higher values and leads to a significant increase in fiber stretch. Meanwhile, This finding is also revealed by other literature (Vijay et al. Citation2019) (Sabarinathan et al. Citation2020).
Conclusion
Based on the bark fiber of the waru tree (Hibiscus tiliaceus) that has been extracted and treated with the chemical for reinforcement in the synthetic resin corridor, it is concluded that: chemical analysis of waru bark fiber showed that the cellulose composition value was high due to the treatment. The highest content of cellulose fiber is 64.01% and was followed by the crystallinity index of the waru bark fiber 63.02%. Morphological observations on the surface of waru bark showed that the fiber appeared cleaner due to the loss of amorphous materials such as lignin, hemicellulose, and other impurities. Chemical treatment with 6% NaOH solution and 0.75% silane addition affects the mechanical properties of waru bark fiber. It was observed that the maximum tensile strength of the fiber was 243.94 MPa higher than the untreated fiber. Waru bark fiber has the same mechanical properties and is better compared to other cellulose fibers, therefore, it has great potential to be developed as a layer of reinforcement in polymer matrix composites such as hybrid crash box applications.
Highlight
Waru bark fiber has better mechanical properties compared to other cellulose fiber
Waru bark fiber has great potential to be developed as a layer of reinforcement in polymer matrix composite
Chemical treatment with NaOH-Silane improving mechanical properties and morphology of waru fiber
Chemical treatment with NaOH-Silane also improving crystallinity index of waru bark fiber
. Analysis of the main constituents of new waru bark fibers with various other natural fibers
. Peak data of the Fourier transform infrared wave number of waru bark fiber
. Tensile strength value of waru bark fiber
Disclosure statement
No potential conflict of interest was reported by the author(s).
References
- Alshammari B A, Alotaibi M D, Alothman O Y, Sanjay M R, Kian L Kia, Almutairi Z and Jawaid M. (2019). A New Study on Characterization and Properties of Natural Fibers Obtained from Olive Tree (Olea europaea L.) Residues. J Polym Environ, 27(11), 2334–2340. 10.1007/s10924-019-01526-8
- Asim, M., M. Jawaid, K. Abdan, and M. Ridzwan Ishak. 2016. Effect of alkali and silane treatments on mechanical and fibre-matrix bond strength of kenaf and pineapple leaf fibres. Journal of Bionic Engineering 13 (3):426–35. doi:10.1016/S1672-6529(16)60315-3.
- Baskaran, P. G., M. Kathiresan, P. Senthamaraikannan, and S. S. Saravanakumar. 2018. Characterization of new natural cellulosic fiber from the bark of dichrostachys cinerea. Journal of Natural Fibers 15 (1):62–68. doi:10.1080/15440478.2017.1304314.
- Chen, R. S., Y. Helmi Muhammad, and S. Ahmad. 2021. Physical, mechanical and environmental stress cracking characteristics of epoxy/glass fiber composites: effect of matrix/fiber modification and fiber loading. Polymer Testing 96:107088. doi:10.1016/j.polymertesting.2021.107088.
- Elanchezhian, C., B. Vijaya Ramnath, G. Ramakrishnan, M. Rajendrakumar, V. Naveenkumar, and M. K. Saravanakumar. 2018. Review on mechanical properties of natural fiber composites. Materials Today: Proceedings 5 (1):1785–90. doi:10.1016/j.matpr.2017.11.276.
- Gapsari, F., A. Purnowidodo, S. Hidayatullah, and S. Suteja. 2021. Characterization of timoho fiber as a reinforcement in green composite. Journal of Materials Research and Technology 13:1305–15. doi:10.1016/j.jmrt.2021.05.049.
- Ilyas R Ahmad et al . (2019). Sugar palm (Arenga pinnata (Wurmb.) Merr) cellulosic fibre hierarchy: a comprehensive approach from macro to nano scale. Journal of Materials Research and Technology, 8(3), 2753–2766. 10.1016/j.jmrt.2019.04.011
- Indran, S., R. Edwin Raj, and V. S. Sreenivasan. 2014. Characterization of new natural cellulosic fiber from cissus quadrangularis root. Carbohydrate Polymers 110:423–29. doi:10.1016/j.carbpol.2014.04.051.
- Jayaramudu, J., B. R. Guduri, and A. Varada Rajulu. 2010. Characterization of new natural cellulosic fabric grewia tilifolia. Carbohydrate Polymers 79 (4):847–51. doi:10.1016/j.carbpol.2009.10.046.
- Kabir, M. M., H. Wang, K. T. Lau, and F. Cardona. 2012. Chemical Treatments on plant-based natural fibre reinforced polymer composites: An overview. Composites Part B: Engineering 43 (7):2883–92. doi:10.1016/j.compositesb.2012.04.053.
- Katerina, K., A. Giannakas, K. Grigoriadi, N. M. Barkoula, and A. Ladavos. 2014. Preparation and characterization of acetylated corn starch-(PVOH)/clay nanocomposite films. Carbohydrate Polymers 102 (1):216–22. doi:10.1016/j.carbpol.2013.11.030.
- Khan A, Vijay R, Singaravelu D Lenin, Sanjay M R, Siengchin S, Jawaid M, Alamry K A and Asiri A M. (2022). Extraction and Characterization of Natural Fibers from Citrullus lanatus Climber. Journal of Natural Fibers, 19(2), 621–629. 10.1080/15440478.2020.1758281
- Kumari, M., R. Kumar, and V. Kumar. 2014. Surface modification of cellulose using silane coupling agent. Carbohydrate Polymers 111:849–55. doi:10.1016/j.carbpol.2014.05.041.
- Loganathan T Moli, Sultan M Thariq, Jawaid M, Ahsan Q, Naveen J and Perumal V. (2022). Characterization of New Cellulosic Cyrtostachys renda and Ptychosperma macarthurii Fibers from Landscaping Plants. Journal of Natural Fibers, 19(2), 669–684. 10.1080/15440478.2020.1758865
- Moshi A Arul, Ravindran D, Bharathi S Sundara, Indran S, Saravanakumar S and Liu Y. (2020). Characterization of a new cellulosic natural fiber extracted from the root of Ficus religiosa tree. International Journal of Biological Macromolecules, 142 212–221. 10.1016/j.ijbiomac.2019.09.094
- Pankow, M., B. Justusson, M. Riosbaas, A. M. Waas, and C. F. Yen. 2019. Effect of fiber architecture on tensile fracture of 3D woven textile composites. Composite Structures 225: Composite Structures: 111139. doi:10.1016/j.compstruct.2019.111139.
- Raharjo, W. W., R. Soenoko, Y. Surya Irawan, and A. Suprapto. 2018. The influence of chemical treatments on cantala fiber properties and interfacial bonding of cantala fiber/recycled high density polyethylene (RHDPE). Journal of Natural Fibers 15 (1):98–111. doi:10.1080/15440478.2017.1321512.
- Reis, R. H. M., L. Fernandes Nunes, M. Souza Oliveira, V. Florêncio De Veiga Junior, F. Da Costa Garcia Filho, M. Alexandrino Pinheiro, V. Scarpini Candido, and S. Neves Monteiro. 2020. Guaruman fiber: another possible reinforcement in composites. Journal of Materials Research and Technology 9 (1):622–28. doi:10.1016/j.jmrt.2019.11.002.
- Rojo, E., M. V. Alonso, M. Oliet, B. Del Saz-Orozco, and F. Rodriguez. 2015. Effect of fiber loading on the properties of treated cellulose fiber-reinforced phenolic composites. Composites Part B: Engineering 68:185–92. doi:10.1016/j.compositesb.2014.08.047.
- Rybin, V. A., A. V. Utkin, and N. I. Baklanova. 2013. Alkali resistance, microstructural and mechanical performance of zirconia-coated basalt fibers. Cement and Concrete Research 53:1–8. doi:10.1016/j.cemconres.2013.06.002.
- Sabarinathan, P., K. Rajkumar, V. E. Annamalai, and K. Vishal. 2020. Characterization on chemical and mechanical properties of silane treated fish tail palm fibres. International Journal of Biological Macromolecules 163:2457–64. doi:10.1016/j.ijbiomac.2020.09.159.
- Sari, H., I. N. G. W. Nasmi, Y. S. Irawan, and E. Siswanto. 2018. Characterization of the chemical, physical, and mechanical properties of NaOH-Treated natural cellulosic fibers from corn husks. Journal of Natural Fibers 15 (4):545–58. doi:10.1080/15440478.2017.1349707.
- Sawpan, M. A., K. L. Pickering, and A. Fernyhough. 2011. Effect of various chemical treatments on the fibre structure and tensile properties of industrial hemp fibres. Composites Part A: Applied Science and Manufacturing 42 (8):888–95. doi:10.1016/j.compositesa.2011.03.008.
- Senthamaraikannan, P., and M. Kathiresan. 2018. Characterization of raw and alkali treated new natural cellulosic fiber from coccinia grandis.L. Carbohydrate Polymers 186 (April):332–43. doi:10.1016/j.carbpol.2018.01.072.
- Siva R, Mobithis M, Ravichandran R, Valarmathi T, Jeya Jeevahan J and Sangeetha M. (2021). Characterization of mechanical, chemical properties and microstructure of untreated and treated Cissus Quadrangularis fiber. Materials Today: Proceedings, 47 4479–4483. 10.1016/j.matpr.2021.05.320
- Sood, M., and G. Dwivedi. 2018. Effect of fiber treatment on flexural properties of natural fiber reinforced composites: A review. Egyptian Journal of Petroleum. Egyptian Petroleum Research Institute 27 (4):775–83. doi:10.1016/j.ejpe.2017.11.005.
- Supian, A. B. M., S. M. Sapuan, M. Y. M. Zuhri, E. S. Zainudin, H. H. Ya, and H. N. Hisham. 2020. Effect of winding orientation on energy absorption and failure modes of filament wound kenaf/glass fibre reinforced epoxy hybrid composite tubes under intermediate-velocity impact (IVI) load Journal of Materials Research and Technology 10 . 1–14. doi:10.1016/j.jmrt.2020.11.103.
- Suryanto, H., S. Sukarni, Y. Rohmat Aji Pradana, U. Yanuhar, and K. Witono. 2019. Effect of mercerization on properties of mendong (Fimbristylis Globulosa) fiber. Songklanakarin Journal of Science and Technology 41 (3):624–30. doi:10.14456/sjst-psu.2019.73.
- Tran, T. P. T., J. Charles Bénézet, and A. Bergeret. 2014. Rice and einkorn wheat husks reinforced poly(Lactic Acid) (PLA) biocomposites: Effects of alkaline and silane surface treatments of husks. Industrial Crops and Products 58:111–24. doi:10.1016/j.indcrop.2014.04.012.
- Vijay, R., D. Lenin Singaravelu, A. Vinod, M. R. Sanjay, S. Siengchin, M. Jawaid, A. Khan, and J. Parameswaranpillai. 2019. Characterization of raw and alkali treated new natural cellulosic fibers from tridax procumbens. International Journal of Biological Macromolecules 125 (March):99–108. doi:10.1016/j.ijbiomac.2018.12.056.
- Vijay, R., A. Vinod, D. Lenin Singaravelu, M. R. Sanjay, and S. Siengchin. 2021. Characterization of chemical treated and untreated natural fibers from Pennisetum orientale grass- a potential reinforcement for lightweight polymeric applications. International Journal of Lightweight Materials and Manufacture 4 (1):43–49. doi:10.1016/j.ijlmm.2020.06.008.
- Wirawan, W. A., M. Agus Choiron, E. Siswanto, and T. Dwi Widodo. 2020 1. Analysis of the fracture area of tensile test for natural woven fiber composites (Hibiscus Tiliaceus-Polyester). Journal of Physics: Conference Series 1700 10.1088/1742-6596/1700/1/012034.
- Xue, L., L. G. Tabil, and S. Panigrahi. 2007. Chemical treatments of natural fiber for use in natural fiber-reinforced composites: A review. Journal of Polymers and the Environment 15 (1):25–33. doi:10.1007/s10924-006-0042-3.
- Yanjun, X., A. S. H. Callum, Z. Xiao, H. Militz, and C. Mai. 2010. Composites : Part a silane coupling agents used for natural fiber/polymer composites : A review. Composites Part A 41 (7):806–19. doi:10.1016/j.compositesa.2010.03.005.
- Zhou, F., G. Cheng, and B. Jiang. 2014. Applied surface science effect of silane treatment on microstructure of sisal fibers. Applied Surface Science 292:806–12. doi:10.1016/j.apsusc.2013.12.054.