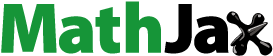
ABSTRACT
This study focuses on the synthesis of a reactive phosphorus-/nitrogen-based intumescent flame retardant (IFR) agent using diethyl phosphite, urea, and glutaraldehyde through Kabachnik-Fields reaction. We further studied the potential applications in IFR modification of cotton fabrics through surface coating approach. The chemical structure of IFR agent and its potential grafting action with cotton fibers were characterized. The thermal stability, smoke and heat release performance, flame retardancy, and durability of the IFR-coated cotton fabrics were explored. Char residue analyses were also performed to confirm the FR mechanism of IFR coating. The results revealed that IFR coating significantly inhibited the heat and smoke generation of cotton. The IFR coating showed high functional efficiency due to phosphorus/nitrogen synergism. The IFR-coated fabrics passed vertical burning B1 level and obtained an limiting oxygen index (LOI) value of higher than 32.0%. The introduction of IFR coating to cotton by covalent bonds imparted excellent washing resistance to cotton as indicated by the self-extinguishing action of the IFR-coated cotton fabrics after 10 launderings. In general, the present study offers a novel strategy to prepare reactive and efficient IFR coating for cellulose-based textiles.
摘要
本研究的重点是通过Kabachnik Fields反应,使用亚磷酸二乙酯、尿素和戊二醛合成活性磷/氮基膨胀型阻燃剂(IFR). 我们进一步研究了表面涂层法在棉织物IFR改性中的潜在应用. 表征了IFR试剂的化学结构及其与棉纤维的潜在接枝作用. 研究了IFR涂层棉织物的热稳定性、烟热释放性能、阻燃性和耐久性. 还进行了残炭分析,以确认IFR涂层的FR机理. 结果表明,IFR涂层显著抑制了棉花的发热和发烟. 由于磷/氮协同作用,IFR涂层显示出高的功能效率. IFR涂层织物通过了垂直燃烧B1水平并获得了高于32.0%的LOI值. 通过共价键将IFR涂层引入棉中,赋予棉优异的耐洗性,如IFR涂层棉织物在10次洗涤后的自熄作用所示. 总的来说,本研究提供了一种新的策略来制备用于纤维素基纺织品的反应性和高效IFR涂层.
Introduction
Cellulose represents the most plentiful polymer globally, and cellulose-based fibers account for over 30% of the world’s total fiber consumption (Nazir et al. Citation2021). As one of the natural resources with the highest purity of cellulose, cotton fiber and its products are widely used in household, office, and industrial fields, thanks to its excellent performance. Cellulose-based materials are prone to fire and lead to a potential tremendous safety hazard in some applications. Indeed, ignitions by household fabrics have become the leading cause for residential home fires (Liu et al. Citation2016). Thus, as the main material source of household fabrics, cotton fabrics need to possess better flame retardant (FR) properties. The development of FR cotton textiles reduces their fire hazards and expands their applications.
Compared with halogen-based FR chemicals, phosphorus (P)-based compounds produce slight corrosive or toxic gases during burning. Therefore, P-based compounds have been researched as promising candidates for excellent FR and are widely used in FR cotton textiles finishing (Rosace et al. Citation2015). P-based FR systems mainly act through the condensed phase mechanism by altering the decomposition pathway of cellulose chain and promoting the generation of protective char layer, achieving FR effect. For P-based FR chemicals, their combination with textiles is a major challenge. The commercialized P-based FR systems, such as Pyrovatex CP, use formaldehyde-based resins to form stable linkages between FR and cellulose hydroxyl groups (Horrocks Citation2011; Qutab et al. Citation2021).
To satisfy the environmental demand and assure effective FR efficiency, intumescent FR (IFR) agents composed of P- and nitrogen (N)-based compounds are of interest. It is considered that P/N synergism is an effective approach to further enhance the FR ability of P element (Abdelkhalik, Makhlouf, and Hassan Citation2019; Gaan and Sun Citation2007; Huang et al. Citation2021). In the burning process, an integrated IFR system can be formed between P/N-based FR system and cellulose (Castellano et al. Citation2019). The FR system is helpful to alter the decomposition pathway of cellulose to promote the char formation instead of the production of flammable species. The swelled char layers act as tight protective barriers against heat, oxygen, and volatile species, preventing the spread of combustion.
Indeed, the washing durability of FR textiles is a main concern in the evaluation of FR and its applications (Vahabi, Sonnier, and Ferry Citation2015). Covalently bonding IFR reagents to hydroxyl-plentiful cellulose fibers by a certain method is a promising approach to improve the FR durability of cotton textiles. The grafting of Schiff base amine and dimethyl phosphate onto the oxidized cellulose fiber also imparted durable FR ability to cotton fabrics, but leads to severe physical damage (Liu et al. Citation2017). Besides, the grafting of Si-P-N synergistic FR systems through the condensation between silanol and cotton hydroxyl groups also displayed high potential to improve the flame retardancy and washing durability of cotton fabric (Chen et al. Citation2021; Liu et al. Citation2020).
The Kabachnik-Fields reaction is an attractive way for synthesizing P/N-based compounds; the reaction occurs in a three-component coupling of carbonyls, amines, and hydrophosphoryl compounds (Balint et al. Citation2013). Diethyl phosphite (DEP) and its derivatives are of interest owing to their effective functionality and reactive P-H unit. Such reactive bond can chemically combine with electron-deficient reagents containing imine, phosphazene, triazine, or triazine-trione unites, developing P/N-based derivatives as effective FR systems (Jiang et al. Citation2018; Wang et al. Citation2017).
This research aimed to prepare a reactive and efficient IFR system for cotton fabrics. This system can be achieved based on the Kabachnik-Fields reaction among DEP, urea, and glutaraldehyde (Gla). Schiff-base imine C=N groups were formed by aldehyde-amine condensation between Gla and urea. Phosphonate groups were then introduced through the Pudovik addition of DEP to Schiff base intermediate (Cytlak et al. Citation2018; Liu et al. Citation2013). The IFR reagent was then introduced into cotton fabrics by facile surface coating technique. The FR ability of cotton was enhanced through the P/N synergistic FR effect of IFR reagent.
Experimental section
Materials
The plain-woven cotton fabrics with density of 190 g/m2 were obtained from Shanghai Textile Industry Institute of Technical Supervision, China. Urea (CH4N2O, ≥99.0%), Gla (C5H8O2), triethanolamine (TEA, C6H15NO3, ≥99.0%), and DEP (C4H11O3P) were purchased from Sinopharm Chemical Reagent Co., Ltd., China. Ethanol (C2H6O) was provided by Jiangsu Chinasun Specialty Products Co., Ltd., China. The soap detergent was provided by Shanghai Textile Industry Institute of Technical Supervision, China.
Synthesis of IFR reagent
The theoretical basis of the IFR reagent preparation is the Kabachnik-Fields reaction between DEP, urea, and Gla, as shown in . The Schiff base reaction occurred between urea and Gla, and then the Pudovik addition occurred between DEP and Shiff base imine intermediate. Urea and Gla with a molar ratio of 1:1 was initially dissolved in the ultrapure water and heated to 80°C and stirred for 60 min. Then, DEP with twice molar weight was added dropwise to the reaction system at 80°C. After 60 min, the reaction solution was lyophilized. The IFR reagent was purified by ethanol. After drying in the lyophilizer, the dried and purified IFR reagent with a yield of 89% was obtained.
Preparation of FR-cotton fabrics
The IFR reagent was dissolved in ultrapure water to prepare IFR solutions with different concentrations (50, 100, 150, and 200 g/L). TEA was added to adjust the pH to 3.0. The cotton fabrics were dipped in the solution with a material-to-solution ratio of 1:30 at 80°C for 30 min. Then, the coated cotton fabrics were rinsed and dried at 80°C for 3 min. The potential reaction mechanism between IFR reagent and cotton fiber is shown in . In acidic condition, the aldehyde groups on IFR reacted with the hydroxyl groups on cellulose to form ester group; so, IFR was grafted onto cotton fiber macromolecules. The fabrics were dried in an oven at 60°C for 30 min and then weighed quickly. The weight gain (WG) of the IFR-coated cotton fabric was determined by using the dry weight of the sample before (W0) and after the modification (W1), as shown in EquationEquation (1)(1)
(1) .
The cotton samples coated by 100 and 150 g/L IFR agent with WG of 10.9% and 13.5% were denoted as Cotton-1 and Cotton-2, respectively.
Characterizations
For IFR agent, the IFR-coated cotton fabrics, and the corresponding char residues, the Fourier transformed infrared (FTIR) spectra were collected using the Thermo Fisher Scientific Nicolet iS50 FTIR spectrometer under a resolution of 4.0 cm−1 in 32 scans. The surface morphologies of the cotton fabrics and the corresponding char residues were observed by Hitachi TM3030 scanning electron microscopy (SEM). The element distribution and changes on surface were determined by energy-dispersive X-ray analysis (EDS). The total P content of the burned and unburned cotton samples was determined by Thermo Fisher Scientific ICAP 6300 DUO inductively coupled plasma optical emission spectrometer (ICP-OES). The limiting oxygen index (LOI) tests were performed with the FTT0080 oxygen index machine (UK) according to the standard of GB/T 5454-1997. The vertical burning test was performed using YG815B automatic machine (China) according to the standard of GB/T 5455-2014 by applying a 40-mm methane flame for 12 s; the combustion performance was classified according to the standard of GB/T 17591-2006: (1) B1 classification: char length ≤15 cm, after-flame time ≤5 s, after-glow time ≤5 s; (2) B2 classification: char length ≤20 cm, after-flame time ≤15 s, after-glow time ≤15 s. The washing durability of the IFR-coated cotton fabrics was evaluated according to the standard of AATCC-61-2013 (1A), and 3.7 g/L washing detergent was used; each wash was conducted at 40°C for 45 min, and one washing cycle was equivalent to five commercial washes. The thermal stabilities were studied using Perkin-Elmer Diamond TG/DTA SII apparatus under N2 and air atmospheres with heating rate of 10°C/min. The smoke and heat release measurements were performed by FTT0064 NBS smoke density chamber and FTT0001 pyrolysis combustion flow calorimetry (PCFC) according to the standard of ISO 5659-2 (radiant flux: 25 kW/m2) and ASTM D7309, respectively. The air permeability of the fabric was tested using the YG461 G fully automatic permeability instrument according to the standard of GB/T 5453-1997. The tensile strength was evaluated using Instron 3365 machine according to the standard of ISO 13934-1-2013 with a specimen of 300 mm length by 50 mm width, and the test was performed five times for each sample. The bending length of the IFR-coated cotton fabrics in warp direction was evaluated according to the standard of GB/T 18318.1-2009 by YG(B) 022D automatic textile stiffness machine, and the test was performed ten times for each sample.
Results and discussion
FTIR analysis
The FTIR spectra of Gla, urea, DEP, aldehyde-amine condensation, IFR, and IFR-coated cotton fabrics are illustrated in . In the spectrum of urea, the peaks at around 3426 and 3328 cm−1 point to the N-H stretching vibration. After the synthesis reactions, the absorption intensity of N-H group decreased but the width increased in the spectrum of IFR. The rocking vibration of N-H at 1154 cm−1 was also observed (Dong, Hou, and Wu Citation2020), which indicated the existence of N-H group in IFR. The peaks at 2938 and 2870 cm−1 correspond to the absorption of CHO group. The C=N Schiff imine group was observed in the spectra of Gla/urea condensation product and IFR agent at around 1653 cm−1 (Li et al. Citation2019; Lv et al. Citation2018). After the Pudovik addition with DEP, the absorption peak of C-N group was found at around 1437 cm−1. Besides, the peak at 1554 cm−1 is assigned to C=O stretching vibration (Dong, Hou, and Wu Citation2020). The peak at 1287 cm−1 points to P=O stretching vibration, which was found at 1254 cm−1 on spectrum of DEP. The spectrum of DEP showed P-O stretching vibration at 957 cm−1 (Siow et al. Citation2014). The peaks at 985 and 927 cm−1 corresponding to P-O and P-C stretching vibration were observed in the spectrum of IFR. These results suggested the successful synthesis of Schiff imine groups and the covalent grafting of DEP onto the Schiff imine groups.
Figure 2. FTIR spectra of (a) chemical reagents and (b) uncoated cotton fabrics and the IFR-coated cotton fabrics, (c–e) SEM images of uncoated cotton and the IFR-coated cotton fabrics.
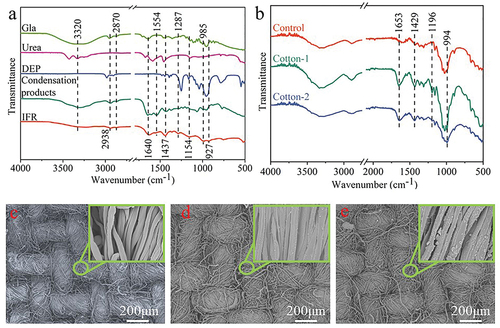
As shown in , the spectrum of the cotton fabrics had a strong and wide absorption peak near 3336 cm−1, which was caused by the stretching vibration of hydroxyl groups. The presence of hydroxyl groups in cellulose provided an access point for active FR reagents that primarily acted in the condensed phase. The peak at about 2891 cm−1 was attributed to the stretching vibration of -CH2 and -CH groups. The broad peaks at around 1026 and 1429 cm−1 were caused by C-H wagging and C-H deformation stretching, respectively (Alongi et al. Citation2013; Fang et al. Citation2015). Regarding the spectra of the IFR-coated fabrics, the new peaks at 1653 and 1437 cm−1 were caused by the stretching vibration of C=N and C-N groups, respectively (Dong, Hou, and Wu Citation2020; Lv et al. Citation2018). The new peak at 1196 cm−1 should be assigned to the absorption of amino groups. The intensity of the absorption peak at 994 cm−1 was enhanced, indicating the existence of P-O and P-C groups in the IFR-coated cotton fabrics. However, compared with the spectrum of IFR, the absorption peaks of P-O and P-C groups at other positions (at 985 and 927 cm−1) were not obvious, which may be due to the overlapping with the wide peak at 1026 cm−1 for cellulose. These results above suggested that IFR coating was successfully introduced on the surface of cotton (). In particular, the introduction of -P=O groups and R-NH- groups makes it possible to develop functional cotton fabrics with better FR and durability.
Surface morphology
The surface structure of fabric is an important factor affecting its handle. The changes of surface structure of the IFR-coated fabrics can be analyzed by SEM images, as shown in . From the SEM images of the cotton fabrics, the arrangement of yarns was orderly and compact, forming a tight fabric structure. The cotton fibers had a smooth surface. The IFR-coated fabrics possessed a surface structure similar to that of the cotton fabrics. Through the comparison of fiber surface structure, it can be found that IFR was uniformly grafted and precipitated on the surface of fiber. Meanwhile, the free gap between tightly entangled fibers in the IFR-coated fabrics maintained the same shape as that of the cotton fabrics. It can be concluded that the coating of IFR had lighter influence on the surface structure of cotton fabrics, so that its good handle could be retained. Compared with Cotton-1 sample, the surface of fibers in Cotton-2 displayed more depositions of IFR and the whole surface was almost covered by the coating, resulting in higher weight gain. Scanning the elements on the surface of the IFR-coated fibers (), it was found that P element was widely and evenly distributed on fiber surface, indicating that the IFR coating had good uniformity.
Flame retardancy
The flame retardancy of the IFR-coated cotton fabrics was evaluated using the vertical burning and LOI tests. As shown in , the cotton fabrics were ignited easily and burned completely, obtaining a char length of 30 cm. Meanwhile, its after-flame and after-glow time were 37.6 and 80.4 s, respectively. The vertical burning process of the IFR-coated cotton fabrics showed that the addition of IFR coating made the cotton fabrics difficult to ignite. The flame retardancy of the IFR-coated cotton fabrics further improved with the increase in the concentration of IFR solution due to the increased P content (). When the concentration of IFR solution reached 100 g/L, the IFR-coated cotton fabrics positively stopped the fire propagation after removing the fire source, displaying no after-flame and after-glow effect, and achieved self-extinguishing level. The addition of IFR also affected the char residue of the fabrics. The char length of Cotton-1 and Cotton-2 samples reduced to 10.7 and 7.9 cm, respectively. Compared with the lower LOI value of the cotton fabrics (18.3%), the LOI of Cotton-1 and Cotton-2 increased significantly, which were 27.5% and 32.1%, respectively. The IFR coating made the cotton fabrics form intumescent and compact char residue layers during the burning process, which effectively prevented the spread of flame and reduced the fire hazards. According to the difference of burning process and burning products, it could be supposed that during heating, IFR reagent decomposed firstly to form an acidic P species that catalyzed char formation. The formed char acted as a thermal barrier against heat and thus protected the underlying polymers (Makhlouf, Abdelkhalik, and Ameen Citation2021).
The results of vertical burning test of the washed IFR-coated cotton fabrics (Cotton-2) showed that the IFR-coated cotton fabrics after 5 and 10 commercial washing cycles self-extinguished and had low char length of 9.5 and 13.7 cm, respectively. These results indicated that the IFR-coated cotton fabrics had good washing durability, which was largely ascribed to firm bonding of IFR coating onto cotton fiber surface (). However, this bonding was not indestructible. Specially, the IFR-coated cotton fabric failed to pass the vertical burning test after 15 washing cycles with a P content of lower than 11.5 mg/g.
Smoke and heat release ability
The specific optical density (Ds) versus time and heat release rate (HRR) versus temperature curves, and some corresponding parameters are shown in . The flame retardancy of the cotton fabrics was inferior, so it burnt robustly with a high maximum Ds (Dsmax) value and peak HRR (pHRR) value of 154.0 and 226.8 W/g, respectively. With the increase in IFR concentration, the Dsmax value of the IFR-coated cotton fabrics decreased to 68.9 and 42.4, getting a reduction rate of about 55.3% and 72.5%, respectively. Besides, the pHRR and the total heat release (THR) also showed the significant reduction. Lower smoke and heat release denote lower fire spread and fire hazard, which is consistent with the vertical burning and LOI tests. Low smoke density and heat release indicated that IFR coating had good smoke and heat suppression ability, which could reduce fire spread and fire risk. This performance of IFR coating could be attributed to its high catalytic carbonization efficiency under thermal radiation, and more char residue was formed in cellulose carbonization process, rather than hot particles and smoke particles.
Thermal stability
The TGA curves under N2 and air atmospheres of the cotton fabrics are shown in and the related data are summarized in . Under N2 atmosphere, the initial degradation temperature (T10%) of cotton fabric was about 306.8°C. At the same time, the main weight loss process was observed in the range of 300–400°C, which was mainly due to the depolymerization of cellulose and the production of volatile gases and aliphatic carbon through transglycosylation reactions (Rosace et al. Citation2015). In comparison, the IFR-coated cotton fabrics had the similar thermal degradation process but lower initial degradation temperature and maximum rate degradation temperature (Tmax1), which should be ascribed to the catalyzed decomposition of cotton by phosphate groups. However, the IFR-coated cotton exhibited lower weight loss above 350°C and higher char residue of above 40% at 600°C. Under air atmosphere, cotton showed a two-step decomposition process due to further oxidation of the aliphatic carbon, leading to the lower char residues at 600°C. Besides, the IFR coating still increased the charring ability at high temperatures of cotton under air atmosphere.
Table 1. TG data of the cotton fabrics under nitrogen and air.
In the IFR-coated cotton fabrics with higher P-content, the reduction in degradation temperatures was more pronounced with enhanced char generation, highlighting the acid-catalyzed degradation of cellulose. The produced phosphoric acid substructures generated by IFR agent degradation could catalyze the decomposition of cellulose to generate carbonaceous residues. The generation of thermally stable O-P-N-based network could also contribute to higher char residue of the IFR-coated cotton fabrics. The large amount of char residues formed at high temperatures would protect the fiber from heat/mass transfer and violent decomposition, thereby improving flame retardancy.
Flame-retardant mechanism
The char morphology and structure of the cotton fabrics and the IFR-coated cotton fabrics are shown in . After vertical burning, the fibers in the cotton fabrics were almost completely pyrolyzed, the fiber structure was severely damaged, and the yarns were broken, so that the tight woven structure was destroyed, leaving little buoyant char with large pores. Under the protection of IFR coating, the pyrolysis of fibers was reduced, and the fiber morphological structure, the arrangement of the yarns, and the tight woven structure were well preserved. The increased char residue reduced the heat and mass transfer, and thus less fuel could be supplied to support the eternal flame zone. A large number of intumescent bubbles were distributed on the surface of the IFR-coated cotton fabrics residue, which was formed by the intumescent bubbling action of IFR. According to ICP-OES analyses, the P content of the IFR-coated cotton char residues was higher than that of the IFR-coated cotton fabrics. The P content of Cotton-1 and Cotton-2 was 20.9 and 29.7 mg/g, and the P content of their corresponding char residues increased to 54.1 and 78.6 mg/g, respectively. These results were also consistent with the EDS analysis. The P-rich and swelled bubbling structures could restrain cellulose decomposition to produce volatile species, preventing the spread of flame.
The chemical structure of the char residues was obtained by FTIR and Raman analyses (). The cotton char residues displayed different spectra compared with that of the unburned fabrics. For the spectrum of cotton char residues, the disappeared peaks at around 3336 and 2891 cm−1 suggested the dehydration of cellulose and the production of hydrocarbon gases. The peak at 1574 cm−1 indicated the formation of polynuclear aromatic residues after combustion. The broad peak at 990 cm−1 was assigned to the out-of-plane deformation vibration of the ring (Cheng et al. Citation2019; Grancaric et al. Citation2017). For the spectra of the IFR-coated cotton fabric residues, the new peak at around 1148 cm−1 could be ascribed to the C-O-C absorption (Zhang et al. Citation2021), indicating the formation of complex carbonaceous structure and the reduction of flammable gases as “fuel” to feedback the flame. The new peaks at 1076, 998, and 874 cm−1 were caused by the absorption vibration of P-O, P-O-C, and P=O (Bellayer et al. Citation2018; Siow et al. Citation2014), confirming the generation of P complex in the IFR-coated cotton char residues. Furthermore, the disappeared peaks at 1653 and 1437 cm−1 indicated the production of nitrogen-containing gases.
As shown in , the peaks at 1348 and 1575 cm−1 were observed due to the disordered carbons (D band) and crystalline graphite residues (G band), respectively. The integral area ratio of the peaks (ID/IG) is recognized as a suitable method to evaluate the graphitization degree of char residues. The char residues with a higher graphitization degree usually present lower ID/IG value (Guizani et al. Citation2017). As can be seen, the cotton char residues had a high ID/IG value of 2.83, while the ID/IG values of Cotton-1 and Cotton-2 char residues were lower, 1.83 and 1.75, respectively. The decrease of ID/IG value indicated that the IFR coating promoted the generation of aromatic char with a high graphitization degree to impede the exchange of heat, oxygen, and combustible species.
The burning process and the FR mechanism of the cotton fabrics and the IFR-coated cotton fabrics are illustrated in . According to the TGA and char residues analysis results, the FR mechanism of the IFR-coated cotton fabrics could be summarized as follows: in the condensed phase, PO generated phosphoric acid, which could enhance the activity of the condensed phase. The amine reacted with phosphoric acid to form an intermediate, which led to phosphorylation of cellulose and the production of polyphosphoric acid, enhancing the condensed phase activity. Phosphorus oxynitride produced from amines and polyphosphoric acids also reinforced the condensed phase activity, while acting as a thermal barrier (Nazir et al. Citation2021). Besides, it is supposed that the formed nitrogen-containing gases are conducive to dilute the concentration of oxygen and flammable gases in combustion zone, and thus retarding the combustion process (Makhlouf, Abdelkhalik, and Ameen Citation2021). As a result, the IFR-coated cotton fabrics possessed excellent flame retardancy through the combined condensed phase and gas phase mechanism.
Physical properties
The air permeability, tensile strength, and handle of the IFR-coated cotton fabrics were assessed. As shown in , cotton fabric displayed little decrease in air permeability after treatment due to the deposition of IFR coating on fabric surface. The tensile strength of Cotton-1 and Cotton-2 had the 8.8% and 10.5% reduction versus pristine cotton fabric, respectively, due to the hydrolysis of cellulose chain in acidic modification process. Besides, the IFR coating also modestly influenced the softness of cotton fabric as suggested by the slightly increased bending length and flexural rigidity. As a conclusion, the IFR coating has little impact on physical properties of cotton fabric.
Table 2. The physical properties of the IFR-coated cotton fabrics.
Conclusions
The FR treatment of cotton fabrics with environmental-friendliness and good washing fastness has always been a research hotspot and challenge. In this research, a novel and reactive P- and N-based IFR was synthesized using DEP, urea, and Gla through Kabachnik-Fields reaction. FR cotton fabrics were developed by grafting IFR onto cellulose surface through crosslinking and surface coating process. The thermal stability, FR performance, and mechanism were studied. The IFR-coated cotton fabrics passed the vertical flammability test, and the LOI value increased to 32.0%. After 10 washings, the IFR-coated cotton fabrics could also pass the burning test and reached B1 level with char length of 13.7 cm. The smoke and heat release of cotton obviously decreased after FR modification, showing lower fire risk. TG analysis demonstrated that IFR coating lowered the decomposition temperature and enhanced the formation of char after combustion. Based on the experimental results and related research analysis, it was speculated that the FR mechanism of IFR was the combination of condensed and gas phase FR under the synergistic action of P/N. The FR coating could catalyze the formation of P-rich bubbling char during combustion and endowed excellent flame retardancy by the intumescent FR action. As a conclusion, the IFR coating imparted effective FR ability to cotton fabrics with good durability, while maintaining good physical properties, demonstrating that it is a potential high-performance material.
Highlights
Reactive synergistic P/N-containing intumescent flame retardant (IFR) is prepared.
IFR coating has high flame retardant ability and washing durability on cotton textile.
IFR coating has good smoke suppression ability on cotton textile.
IFR coating functions through both gas phase and condensed phase action.
IFR coating offers an effective and durable strategy to minimize the fire hazards of cotton textile.
Acknowledgment
This study was found by the Natural Science Foundation of Jiangsu Province (BK20200868).
Disclosure statement
No potential conflict of interest was reported by the author(s).
Additional information
Funding
References
- Abdelkhalik, A., G. Makhlouf, and M. A. Hassan. 2019. Manufacturing, thermal stability, and flammability properties of polypropylene containing new single molecule intumescent flame retardant. Polymers for Advanced Technologies 30 (6):1403–15. doi:10.1002/pat.4573.
- Alongi, J., R. A. Carletto, A. Di Blasio, F. Carosio, F. Bosco, and G. Malucelli. 2013. DNA: A novel, green, natural flame retardant and suppressant for cotton. Journal of Materials Chemistry A 1 (15):4779–85. doi:10.1039/c3ta00107e.
- Balint, E., J. Takacs, L. Drahos, A. Juranovic, M. Kocevar, and G. Keglevich. 2013. α-Aminophosphonates and α-Aminophosphine Oxides by the Microwave-Assisted Kabachnik-Fields Reactions of 3-Amino-6-methyl-2H-pyran-2-ones. Heteroatom Chemistry 24 (3):221–25. doi:10.1002/hc.21086.
- Bellayer, S., M. Jimenez, B. Prieur, B. Dewailly, A. Ramgobin, J. Sarazin, B. Revel, G. Tricot, and S. Bourbigot. 2018. Fire retardant sol-gel coated polyurethane foam: Mechanism of action. Polymer Degradation and Stability 147:159–67. doi:10.1016/j.polymdegradstab.2017.12.005.
- Castellano, A., C. Colleoni, G. Iacono, A. Mezzi, M. R. Plutino, G. Malucelli, and G. Rosace. 2019. Synthesis and characterization of a phosphorous/nitrogen based sol-gel coating as a novel halogen-and formaldehyde-free flame retardant finishing for cotton fabric. Polymer Degradation and Stability 162:148–59. doi:10.1016/j.polymdegradstab.2019.02.006.
- Cheng, X. W., R. C. Tang, F. Yao, and X. H. Yang. 2019. Flame retardant coating of wool fabric with phytic acid/polyethyleneimine polyelectrolyte complex. Progress in Organic Coatings 132:336–42. doi:10.1016/j.porgcoat.2019.04.018.
- Chen, S., H. Li, X. Lai, S. Zhang, and X. Zeng. 2021. Superhydrophobic and phosphorus-nitrogen flame-retardant cotton fabric. Progress in Organic Coatings 159:106446. doi:10.1016/j.porgcoat.2021.106446.
- Cytlak, T., M. Skibińska, P. Kaczmarek, M. Kaźmierczak, M. Rapp, M. Kubicki, and H. Koroniak. 2018. Functionalization of α-hydroxyphosphonates as a convenient route to N-tosyl-α-aminophosphonates. RSC advances 8 (22):11957–74. doi:10.1039/C8RA01656A.
- Dong, Y., L. Hou, and P. Wu. 2020. Exploring the diffusion behavior of urea aqueous solution in the viscose film by ATR-FTIR spectroscopy. Cellulose 27 (5):2403–15. doi:10.1007/s10570-020-02997-y.
- Fang, F., X. Zhang, Y. Meng, Z. Gu, C. Bao, X. Ding, S. Li, X. Chen, and X. Tian. 2015. Intumescent flame retardant coatings on cotton fabric of chitosan and ammonium polyphosphate via layer-by-layer assembly. Surface & Coatings Technology 262:9–14. doi:10.1016/j.surfcoat.2014.11.011.
- Gaan, S., and G. Sun. 2007. Effect of phosphorus and nitrogen on flame retardant cellulose: A study of phosphorus compounds. Journal of Analytical and Applied Pyrolysis 78 (2):371–77. doi:10.1016/j.jaap.2006.09.010.
- Grancaric, A. M., C. Colleoni, E. Guido, L. Botteri, and G. Rosace. 2017. Thermal behaviour and flame retardancy of monoethanolamine-doped sol-gel coatings of cotton fabric. Progress in Organic Coatings 103:174–81. doi:10.1016/j.porgcoat.2016.10.035.
- Guizani, C., K. Haddad, L. Limousy, and M. Jeguirim. 2017. New insights on the structural evolution of biomass char upon pyrolysis as revealed by the Raman spectroscopy and elemental analysis. Carbon 119:519–21. doi:10.1016/j.carbon.2017.04.078.
- Horrocks, A. R. 2011. Flame retardant challenges for textiles and fibers: New chemistry versus innovatory solutions. Polymer Degradation and Stability 96 (3):377–92. doi:10.1016/j.polymdegradstab.2010.03.036.
- Huang, T., F. Xu, P. Zhao, P. Wang, F. Zhang, and G. Zhang. 2021. A novel flame retardant for cotton containing ammonium phosphonic acid and phosphonate prepared from urea. Journal of Natural Fibers 19 (15):1–14. doi:10.1080/15440478.2021.2002779.
- Jiang, Y., P. Yan, Y. Wang, C. Zhou, and J. Lei. 2018. Form-stable phase change materials with enhanced thermal stability and fire resistance via the incorporation of phosphorus and silicon. Materials & Design 160:763–71. doi:10.1016/j.matdes.2018.10.020.
- Li, N., J. Ming, R. Yuan, S. Fan, L. Liu, F. Li, X. Wang, J. Yu, and D. Wu. 2019. Novel eco-friendly flame retardants based on nitrogen–silicone Schiff base and application in cellulose. ACS Sustainable Chemistry & Engineering 8 (1):290–301. doi:10.1021/acssuschemeng.9b05338.
- Liu, J., C. Dong, Z. Zhang, H. Sun, D. Kong, and Z. Lu. 2020. Durable flame retardant cotton fabrics modified with a novel silicon–phosphorus–nitrogen synergistic flame retardant. Cellulose 27 (15):9027–43. doi:10.1007/s10570-020-03370-9.
- Liu, Y., Y. T. Pan, X. Wang, P. Acuña, P. Zhu, U. Wagenknecht, G. Heinrich, X. Q. Zhang, R. Wang, and D. Y. Wang. 2016. Effect of phosphorus-containing inorganic-organic hybrid coating on the flammability of cotton fabrics: Synthesis, characterization and flammability. Chemical Engineering Journal 294:167–75. doi:10.1016/j.cej.2016.02.080.
- Liu, Z., M. Xu, Q. Wang, and B. Li. 2017. A novel durable flame retardant cotton fabric produced by surface chemical grafting of phosphorus-and nitrogen-containing compounds. Cellulose 24 (9):4069–81. doi:10.1007/s10570-017-1391-x.
- Liu, Y., Y. Zhang, Z. Cao, and Z. Fang. 2013. Synthesis and performance of three flame retardant additives containing diethyl phosphite/phenyl phosphonic moieties. Fire safety journal 61:185–92. doi:10.1016/j.firesaf.2013.09.009.
- Lv, M., X. Ma, D. P. Anderson, and P. R. Chang. 2018. Immobilization of urease onto cellulose spheres for the selective removal of urea. Cellulose 25 (1):233–43. doi:10.1007/s10570-017-1592-3.
- Makhlouf, G., A. Abdelkhalik, and H. Ameen. 2021. Synthesis of a novel highly efficient flame-retardant coating for cotton fabrics with low combustion toxicity and antibacterial properties. Cellulose 28 (13):8785–806. doi:10.1007/s10570-021-04076-2.
- Nazir, R., D. Parida, J. Borgstädt, S. Lehner, M. Jovic, D. Rentsch, E. Bülbül, A. Huch, S. Altenried, Q. Ren, et al. 2021. In-situ phosphine oxide physical networks: A facile strategy to achieve durable flame retardant and antimicrobial treatments of cellulose. Chemical Engineering Journal 417:128028. doi:10.1016/j.cej.2020.128028.
- Qutab, H. G., M. Mohsin, N. Ramzan, S. W. Ahmad, and S. Sardar. 2021. Synthesis and application of a formaldehyde-free flame-retardant for cotton fabrics by polymerization between diammonium hydrogen phosphate and citric acid. Journal of Natural Fibers 18 (11):1913–23. doi:10.1080/15440478.2019.1710648.
- Rosace, G., V. Migani, E. Guido, and C. Colleoni. 2015. Flame retardant finishing for textiles. In Flame Retardants, ed. P. M. Visakh and Y. Arao, 209–46. Switzerland: Springer, Cham.
- Siow, K. S., L. Britcher, S. Kumar, and H. J. Griesser. 2014. Deposition and XPS and FTIR analysis of plasma polymer coatings containing phosphorus. Plasma Processes and Polymers 11 (2):133–41. doi:10.1002/ppap.201300115.
- Vahabi, H., R. Sonnier, and L. Ferry. 2015. Effects of ageing on the fire behavior of flame-retarded polymers: A review. Polymer International 64 (3):313–28. doi:10.1002/pi.4841.
- Wang, S., S. Ma, C. Xu, Y. Liu, J. Dai, Z. Wang, X. Liu, J. Chen, X. Shen, J. Wei, et al. 2017. Vanillin-derived high-performance flame retardant epoxy resins: Facile synthesis and properties. Macromolecules 50 (5):1892–901. doi:10.1021/acs.macromol.7b00097.
- Zhang, A. N., H. B. Zhao, J. B. Cheng, M. E. Li, S. L. Li, M. Cao, and Y. Z. Wang. 2021. Construction of durable eco-friendly biomass-based flame-retardant coating for cotton fabrics. Chemical Engineering Journal 410:128361. doi:10.1016/j.cej.2020.128361.