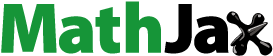
ABSTRACT
The adverse environmental effects of synthetic fibers have forced researchers to use natural fibers in composite preparation. Pinus Roxburghii Needles (PRNs) are widely available in the hilly region of Uttarakhand state, India. Utilizing the fiber extracted from PRNs as reinforcement in bio-composite preparation can reduce synthetic fiber and emphasize the use of natural resources. In this study, we extract the Pinus Roxburghii Fibers (PRFs) from PRNs using the water retting method. Their physical, chemical, thermal, and morphological aspects were investigated and reported. The average diameter and density of the extracted PRFs were obtained as 145 ± 17.36 µm and 1020 ± 20.27 kg/m3, respectively. The chemical analysis revealed that the extracted PRFs contain 58.30% cellulose content. Thermal stability and maximum degradation temperature of the extracted PRFs were assessed using thermogravimetric analysis (TGA) and found to be 225°C and 355.84°C, respectively. Field Emission Scanning Electron Microscope (FESEM) and Atomic Force Microscope (AFM) were used to study the surface morphology and surface roughness of PRFs, respectively. Further, the FTIR analysis of the extracted PRFs confirmed the presence of different functional groups of cellulose, hemicellulose, and lignin. The crystallinity index (43.52%) and crystal size (4.03 nm) of the extracted PRFs were determined using X-ray diffraction (XRD) analysis.
摘 要
合成纤维的不利环境影响迫使研究人员在复合材料制备中使用天然纤维. 在印度北阿坎德邦的丘陵地区,刺针(PRN)随处可见. 利用从PRN中提取的纤维作为生物复合材料制备中的增强材料,可以减少合成纤维,并强调利用自然资源. 本研究采用水浸法从刺梨松中提取刺梨松纤维. 对它们的物理、化学、热和形态进行了研究和报道. 提取的PRF的平均直径和密度分别为145 ± 17.36 µm和1020 ± 20.27 kg/m3. 化学分析表明,提取的PRF含有58.30%的纤维素含量. 使用热重分析(TGA)评估提取的PRF的热稳定性和最大降解温度,发现分别为225°C和355.84°C. 利用场发射扫描电子显微镜(FESEM)和原子力显微镜(AFM)分别研究了PRF的表面形貌和表面粗糙度. 此外,提取的PRF的FTIR分析证实了纤维素、半纤维素和木质素的不同官能团的存在. 使用X射线衍射(XRD)分析测定提取的PRF的结晶度指数(43.52%)和晶体尺寸(4.03 nm).
Introduction
Synthetic fibers, such as glass and carbon, have been used in composite preparation for a few decades even though several environmental issues are associated with them (Ranakoti, Rakesh, and Gangil Citation2021). Alternatively, natural fibers have no impact on the environment as they are renewable and biodegradable resources (Kulandaivel, Muralikannan, and Kalyana Sundaram Citation2018). The environment-friendly nature of natural fiber has resulted in its enormous demand in composite fabrication. In addition, natural fibers have more advantages, such as lightweight, low density, ease in processing, non-abrasive, non-hazardous, and mainly low cost compared to synthetic fibers (Shanmugasundaram and Rajendran Citation2016). Natural fibers can be obtained from various sources, including plants, minerals, and animals. Asbestos or basalt is the primary component of mineral-based natural fibers, whereas protein is the primary component of animal-based natural fibers. Asbestos is currently regarded as hazardous to human health, and its use has been banned in most countries, whereas animal-origin fibers are becoming less available and more expensive (Pickering, Efendy, and Le Citation2016; Vinod et al. Citation2021).
Plant selection for natural fiber is essential for fabricating high-strength composites as the fiber’s property depends on the cellulose content, cross-section, and chemical composition, which varies from plant to plant (Faruk et al. Citation2012). Plant-based cellulosic fibers such as bamboo, cotton, flax, jute, sisal, kenaf and ramie fibers, have been used in composite preparation due to their excellent mechanical properties and biodegradability (Pickering, Efendy, and Le Citation2016; Tahir et al. Citation2011). However, bamboo takes more than three to four years to achieve its full height and strength, whereas flax, hemp, sisal, jute, and cotton fiber need proper harvesting, resulting in enhanced cost (Lee et al. Citation2020; Ramesh Citation2018). However, the mechanical strength of kenaf fiber-based composites is less because of the poor compatibility of kenaf fiber with the polymer matrix (Radzuan et al. Citation2019). Moreover, these fibers have the issue of their maturity time and cost. Therefore, the need of the hour is to find readily available and low-cost plant-based materials, which can be used to fabricate cost-effective polymer composites.
Pinus Roxburghii Needles (PRNs) are abundant in India’s Himalayan areas, which continuously grow and shed from the Pinus Roxburghii tree. Every summer, PRNs catch fire in the forest, resulting in a massive loss of flora and fauna and eventually causing environmental pollution and energy loss (Thakur, Singha, and Thakur Citation2013). As per the literature, the annual gross availability of PRNs in Uttarakhand, India, is 1.37 to 2.37 million tonnes (Kala and Subbarao Citation2018). However, utilizing these PRNs as fibers would be beneficial in making an environment-friendly composite from readily available needles, reducing the massive forest loss.
Singha and Thakur (Citation2008) fabricated pine needles reinforced resorcinol formaldehyde composite and revealed that the pine needles reinforced composite’s mechanical properties were better than the matrix alone. Kumar et al. (Citation2022) used PRNs leaves in asbestos-free brake friction material by sun drying and alkali treatment. The composition of 10% PRNs has shown excellent mechanical properties for the brake material. Gairola et al. (Citation2019) prepared the hybrid composite reinforcing PRNs and pistachio shells in the epoxy matrix. The impact strength of these hybrid composites was found to be 22.33 kJ/m2. Thus, PRNs are an excellent option for cellulosic reinforcement in composite fabrication. Besides the composite preparation, pine needles in various forms have different applications such as food packing, bedding material for domestic animals, energy feedstock, etc. (Kadam, Singh, and Gaikwad Citation2021; Kala and Subbarao Citation2018). Various research has been done on utilizing raw PRNs as reinforcement in composite fabrication. However, these needles have various impurities and contain a high amount of lignin, which may reduce the strength of the composite (Faruk et al. Citation2012). Therefore, research was extended to extract the fibers from the PRNs to fabricate the composites.
Various extraction methods, such as mechanical, chemical, water retting, and steam explosions, have been used to extract plant-based natural fibers (Md et al. Citation2020). All these methods have their benefits and drawbacks. Tahir et al. (Citation2011) compared the tensile strength of the Kenaf fiber extracted using mechanical and chemical retting methods. They reported that the chemical retting was much cleaner, but tensile properties were poor. The traditional approach to extract the natural fiber is water retting. The water retting method is environmentally friendly and cost-effective. This method requires two to four weeks to break the lignin of the fiber. The water retting method uses anaerobic bacteria fermentation and fungal colonization on fiber bundles to create enzymes that hydrolyze fiber-binding components. Retting is a biological process in which enzymatic activity removes non-cellulosic components linked to the fiber bundle, resulting in detached cellulosic fibers. Clostridium, an anaerobic bacterium found in lakes, rivers, and ponds, is the primary source of this bacterial and fungal fermentation in the water retting method (Akin et al. Citation2004; Lee et al. Citation2020). Few studies have reported the use of raw PRNs in composite fabrication. However, the extraction of the PRFs is not reported till date as per the author’s knowledge. Extracting high-quality PRFs with better cellulose content is still challenging.
Therefore, the present research focused on extracting PRFs using the water retting process. After water retting, the fibers were separated using the traditional manual combing process. Further, the investigations were carried out on the extracted fibers’ physical, chemical, morphological, and thermal properties and their comparison with the other plant-based natural fibers. The study was further extended to investigate the tensile strength of the single extracted fiber.
Materials and method
PRFs extraction
The Pinus Roxburghii tree, also known as the Chir or Himalayan long-leaf tree, typically grows up to 40–50 m in height. The PRNs used for this work were collected from Srinagar, Uttarakhand, India, in August 2021 (). The leaf part of the Pinus Roxburghii tree is generally known as the Pinus Roxburghii needle because of its needlelike structure. PRNs have an average length of 22 cm and a diameter of approximately 1.2 mm (). The top and bottom parts of the PRNs were trimmed to make them a uniform length of ~20 cm, as shown in . The PRNs were soaked in water for 4 weeks at room temperature for microbial degradation, as shown in . Once the soaking period (4 weeks) is completed, the fibers are extracted by a traditional manual combing process on retted needles with the help of a wired brush (Manimaran et al. Citation2016). PRFs were washed with demineralized water several times during extraction to efficiently remove unwanted materials from the fiber surface (). The washed PRFs were dried under sun exposure for 7 days. The final extracted PRFs are shown in .
Analysis of physical properties
Measurement of average diameter
The extracted PRFs are irregular in shape and longitudinally non-uniform, similar to the hemp fiber used by Kabir et al. (Citation2013). Therefore, it is difficult to measure the exact diameter of the extracted PRFs and, hence, an average diameter is reported in this study. Four observations were taken at random lengths in the longitudinal direction for each sample to measure the average diameter, using a Radical RSMr-3 optical microscope, as shown in . The same procedure was adopted for 30 samples of extracted PRFs, and the average value of these observed data is reported as the diameter of PRFs.
Measurement of density
Density was measured using the pycnometer setup, a standard method for determining the density of any substance (Indran and Raj Citation2015). In this study, toluene was used as a reference liquid having a density (ρtoluene) of 866 kg/m3 at 25°C.
Analysis of chemical composition
Numerous approaches have been used to determine the percentage of components in plant-based natural fibers. The present study determines % of cellulose, hemicellulose, lignin, wax, ash, and moisture. The cellulose present in the extracted PRFs was calculated using Kurschner and Hoffer’s techniques. The hemicellulose constituent was determined using the NFT standard 120–008 (Raja et al. Citation2021). For lignin content evaluation, the Klason technique was used (Manimaran et al. Citation2018). The Conrad technique was used to calculate the wax content in the extracted PRFs (Indran, Raj, and Sreenivasan Citation2014). The ASTM D2654–67 and E1755–01 standards were used to estimate the moisture and ash content, respectively (Krishna, Kailasanathan, and NagarajaGanesh Citation2020).
Fourier-Transform Infrared Spectroscopy (FTIR) analysis
The functional group components present in the extracted PRFs were studied using an infrared spectrum obtained from FTIR equipment (Perkin Elmer/Spectrum-2). The spectrum was recorded in the wavenumber range from 4000 to 400 cm−1 with 32 scans/minute and a resolution of 2 cm−1 (Moshi et al. Citation2020). The crushed and oven-dried extracted PRFs (~2 mg), mixed with potassium bromide (200 mg), were used to capture the absorbance spectrum (Vinod et al. Citation2021).
X-ray Diffraction (XRD) analysis
The Bruker D8 equipment was used for XRD analysis with the CuKα radiation at a wavelength of 1.54 Å. During the analysis, the diffractometer was set to 40 kV and 15 mA. The powdered samples of the extracted PRFs were scanned from 10° to 80° (a step of 0.02°) with a 10°/min scanning speed (Manimaran et al. Citation2016). Equation 1 is used to evaluate the PRFs’ crystallinity index (CI) (Segal et al. Citation1959).
Where, Iamorphous and Icrystalline are the intensities of the peaks associated with the amorphous and crystalline phases, respectively. The crystallite size (CS) is found using EquationEquation (2)(2)
(2) (Manimaran et al. Citation2018). The value for Scherer’s constant (K) was taken as 0.89.
Where is Bragg’s angle,
is full width at the half-maximum and
is the wavelength.
Thermal analysis
Thermal analysis of natural fibers is essential in deciding the maximum temperature limits during composite fabrication (Moshi et al. Citation2020). TGA was accomplished by utilizing EXSTAR thermal analyzer (SII 6300 model). The differential thermogravimetric (DTG) analysis is also done using the same equipment as TGA. A total of 10 mg crushed extracted PRFs were filled in an alumina crucible before keeping them in the TG analyzer machine. This process was accomplished in a Nitrogen atmosphere (100 ml/min flow rate) at a temperature range from 35°C to 600°C (Vijay et al. Citation2019).
Morphological study
The morphology of the PRFs was examined using NOVA Nanosem 450 FESEM equipment, which was operated at 20 kV accelerated voltage for surface analysis and 10 kV accelerated voltage for cross-section analysis. The extracted PRFs surface was gold-coated to provide a conducting surface for microscopic inspection (Manimaran et al. Citation2018). Energy Dispersive X-ray Spectroscopy (EDX) of type Apreo EDX APEX-Octane Elite Plus attached with the FESEM was used to examine the presence of various elements. The distribution of the elements was recorded at three distinct locations of the fiber, and its average value is considered (Raja et al. Citation2021). In addition, the surface roughness profile of the PRFs was measured using atomic force microscopy (AFM) with the Ntegra (NT-MDT, Russia) machine and Nova (NT-MDT, Russia) image processing software having a 3–50 nm tip radius of curvature.
Single fiber tensile test
The mechanical properties such as tensile strength, Young’s modulus, and elongation-at-break of single extracted PRFs were determined using Zwick/Roell INSTRON 5982 universal testing equipment (Md et al. Citation2020). A single PRF sample of 65 mm length and 25 mm of gauge length was prepared according to ASTM D3822–07. During the experiment, the sample of single extracted PRFs was put through at a constant speed of 18 mm/min while under a pre-load of 0.1 N and at 23°C with 65% relative humidity (Krishna, Kailasanathan, and NagarajaGanesh Citation2020). The same procedure was repeated for 30 samples, and the average tensile strength was noted. Young’s modulus and elongation at break were also measured.
Results and discussion
Average diameter and density measurement
Diameter calculation in PRFs is complex as fibers have irregular shapes and sizes throughout their length. However, it is assumed to have a circular shape for calculating mechanical properties (Amutha and Senthilkumar Citation2021). The average diameter of the extracted PRFs of 30 samples was measured as explained in section 2.2.1 and observed as 145 ± 17.36 µm. It is also essential to estimate the density of the extracted fiber. It is a decisive factor in checking the eligibility of fibers in fabricating lightweight composites. The density of the extracted PRFs was measured and estimated as 1020 ± 20.27 kg/m3, which is very close to other plant-based natural fibers, such as Acacia arabica bark (1028 kg/m3), mulberry (1070 kg/m3) and so on, as shown in . This shows that the extracted PRFs can be extensively used for lightweight applications.
Table 1. Comparison of various properties of PRFs with other natural fibers.
Chemical composition of PRFs
Cellulose is the main component of natural fibers as it significantly impacts their mechanical properties, whereas others act as a matrix or binder (Moshi et al. Citation2020). The chemical composition study reveals that the extracted PRFs have a cellulose content of 58.30%, which is comparable to various other plant-based natural fibers, such as Pigeon pea (55.03%), Artisdita hystrix (59.54%), and Cardiospermum halicacabum (59.82%), as mentioned in . The higher proportion of hemicellulose is unfavorable for fiber strength due to the disintegration of cellulose microfibrils (Raja et al. Citation2021). The extracted PRFs have 19 wt% of hemicellulose, which is closest to already known fibers such as Heteropogon Contortus (19.34%), Phoenix dactylifera L. (leaf sheath) (24%) and Seagrass (38%), as shown in . High lignin content could affect the fiber-matrix compatibility resulting in lesser mechanical properties and weak bonding with matrix materials (Porras, Maranon, and Ashcroft Citation2015). The extracted PRFs achieved optimum lignin content (20.2%) which is comparable to previously extracted plant-based natural fibers (). If a natural fiber has a lower weight percentage of wax content, the bond between the matrix and the fiber will be stronger while fabricating composite structures. The extracted PRFs have 0.94 wt% of wax content, which is lower than the wax contents of Cardiospermum halicacabum (1.3 wt%), flax (1.5 wt%), and Pigeon pea (2.38 wt%). Furthermore, the results revealed that the extracted PRFs have 9.48% moisture and 1.60% ash.
Table 2. Percentage of chemical constituents present in PRFs and other natural fibers.
FTIR spectroscopic analysis
shows the FTIR spectrum of the extracted PRFs comprising the primary (4000–1500 cm−1) and fingerprint areas (1500–400 cm−1). The prominent peak at 3419 cm−1 is the absorbance owing to hydrogen-bonded OH (alcohol group) stretching vibrations, indicating the presence of cellulose molecules. This result agrees with the observations made by Kathiresan et al. (Citation2016). The second sharp peak at 2923 cm−1 resulted from C-H stretching vibrations, confirming the existence of cellulose and hemicellulose (Vijay et al. Citation2019). However, the absorbance at 1630 cm−1 is related to the OH bending of moisture, indicating water retention in PRFs (Hyness et al. Citation2018). The absorbance peaks at 1512 cm−1, 1406 cm−1, and 1383 cm−1 are owing to C = C stretching, C – H bending and – C=O bending in the aromatic ring of the lignin and hemicellulose (Indran, Raj, and Sreenivasan Citation2014; Kulandaivel, Muralikannan, and Kalyana Sundaram Citation2018). The peak at 1160 cm−1 is cellulose’s C-O-C asymmetric stretching vibration’s absorbance (Saravanakumar et al. Citation2014). The peak at 1033 cm−1 results from symmetric C-O stretching (lignin) and 617 cm−1 is associated with C-OH bending in cellulose (Kulandaivel, Muralikannan, and Kalyana Sundaram Citation2018).
XRD analysis
reveals the diffractogram of extracted PRFs, showing the two prominent peaks at 15.08° and 22.26°, representing the amorphous (110) and crystalline parts (200) of hemicellulose, lignin, and cellulose in the PRFs, respectively. These two peaks also show the presence of cellulose I, having a monoclinic crystal structure. A similar result was also reported by Raja et al. (Citation2021) with Cymbopogon flexuosus fiber. The CI of PRFs was found to be 43.52%, which is comparable to various other plant-based natural fibers like Ficus religiosa fiber (42.92%), Phaseolus vulgaris (43.01%), Artisdita hystrix leaf (44.85%), etc. as shown in . PRFs were found to have a CS value of 4.03 nm, which is lower than that of Ficus religiosa fiber (5.18 nm) and Albizia julibrissin (6.79 nm).
TGA and DTG analysis
The TGA curve of the PRFs shows a three-step degradation behavior, as shown in . The water evaporation from PRFs results in initial mass loss from 35°C to 120°C (9.39%) whose maximum loss is at 67.46°C, as shown in (Babu et al. Citation2022). The second stage of degradation is the most considerable mass loss of 50.42% due to the cellulose and hemicellulose degradation present inside the PRFs. This change occurs from 225°C to 376°C, whose maximum weight loss is at 355.84°C, as shown in the DTG curve (Jeyabalaji et al. Citation2021). The mass loss of 14.90% after 376°C is due to the degradation of fiber’s lignin and wax content (Moshi et al. Citation2020).
Morphological analysis
reveals the morphology of the extracted PRFs obtained from FESEM. The void space present in the PRFs confirms their hydrophilic nature, as shown in . The wax and lignin present on the PRFs surface make it shiny, as shown in . The extracted PRF was observed to be nearly circular in shape, as shown in .
Figure 5. FESEM images of the PRFs (a) Showing void space (b) Showing wax content (c) Circular cross-section.
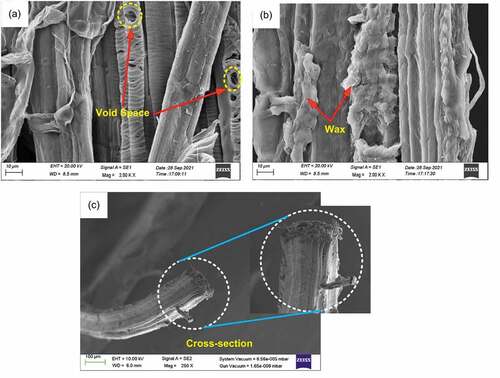
The PRFs’ surface has a parallel set of micro-fibrils, causing roughness along the width of the fiber. This enhances the mechanical interlocking between the fiber and matrix during the composite fabrication (Madhu et al. Citation2019). shows the 2D and 3D AFM images of PRFs, respectively. This analysis is done to understand the topological behavior of PRFs. The PRFs have an average roughness (Ra) of 118.473 nm, which is higher than the Senna Auriculata fiber (Ra = 75.99 nm) (Nagaraja et al. Citation2019) and Eichhornia Crassipes fibers (Ra = 101.84 nm) (Palai, Sarangi, and Mohapatra Citation2021). However, it is lower than Cornhusk fiber having Ra = 189.74 nm (Kambli et al. Citation2016). The higher Ra value indicates less impurity present on the fiber’s surface. The 10-point height and root mean square (RMS) values of PRFs are 899.40 nm and 144.18 nm, respectively, while the peak-to-peak height value is 1514.52 nm. The ratio of RMS and Ra values for PRFs is found to be 1.22, similar to the values obtained for Areca palm leaf (1.19) (Shanmugasundaram, Rajendran, and Ramkumar Citation2018) and Acalypha Indica L (1.25) (Jeyabalaji et al. Citation2021). This property makes PRFs suitable for tribological applications as they are close to their acceptance value of 1.25 to 1.33 (Krishna, Kailasanathan, and NagarajaGanesh Citation2020).
Surface kurtosis is another crucial characteristic that shows how widely the spikes are spread concerning the mean position. The surface kurtosis of PRFs is −0.38. The lower kurtosis value indicates that the roughness of the PRFs is sufficient for the proper mechanical interlocking during the composite fabrication (Jeyabalaji et al. Citation2021).
EDX analysis
EDX attached with FESEM is used for the elemental analysis of PRFs. The EDX spectrometric graph shows the presence of carbon (C), oxygen (O), and calcium (Ca) in the fiber. The EDX spectrum validates the existence of the main constituents of carbon and oxygen in PRFs, whose weight percentage was 65.20% and 34.40%, respectively, as shown in . The impurity present is much less in PRFs as only 0.4 wt% of Ca over fiber’s surface. A similar result was reported by Md et al. (Citation2020).
Single fiber tensile test
It was observed from the SEM images () that the cross-section area of the extracted single PRFs is nearly circular. Therefore, the tensile strength of the fiber is calculated considering that the cross-section of the fiber is circular (Amutha and Senthilkumar Citation2021; Fiore, Scalici, and Valenza Citation2014; Kabir et al. Citation2013). An aggregate of 30 extracted PRFs samples were tested for tensile strength, out of which the maximum strength of 99.17 MPa was obtained. The average tensile strength of 30 samples was obtained as 51.48 ± 19.75 MPa with 3.6% elongation-at-break. The value of average tensile strength is close to that of other plant-based natural fibers such as Tridax procumbens (25.75 ± 2.45 MPa), Manicaria saccifera palm (72.09 ± 15.73 MPa), and so on, as shown in . The tensile strength of the extracted PRFs is comparable with other natural plant-based fibers, which can be further improved with surface modifications. Stress–strain curves for all 30 specimens are shown in . The extracted PRFs have an average Young’s modulus of 1.44 ± 0.67 GPa, which is near to Tridax procumbens fiber (0.94 ± 0.09 GPa), Artisdita hystrix (1.57 ± 0.04 GPa), and Pigeon pea (2.1 GPa) ().
Conclusions
The present study reveals that fiber can be extracted from the naturally available Pinus Roxburghii needle in the Himalayan region using the water retting method and traditional combing process. The extracted PRFs have shown excellent physico-chemical, mechanical, thermal, and morphological properties; therefore, they may extensively be used for making biocomposites. Based on the findings, the following conclusions are made:
The density of extracted PRFs (1020 ± 20.27 kg/m3) is much less than that of synthetic fibers, making them suitable for lightweight composite fabrication.
The EDX analysis indicated that the main elements of extracted PRFs were carbon and oxygen, confirming the fiber to be organic.
The chemical composition analysis shows that the extracted PRFs are cellulosic in nature and have nearly 58.30% of cellulose content.
The crystallinity index and crystal size of the extracted PRFs were obtained as 43.52% and 4.03 nm, respectively.
The FESEM image reveals that the cross-section of the extracted PRF is nearly circular and the nature of the fiber is hydrophilic.
The mechanical properties of the extracted PRFs such as average single fiber tensile strength, Young’s modulus, and elongation-at-break were obtained as 51.48 ± 19.75 MPa, 1.44 ± 0.67 GPa, and 3.6%, respectively.
Highlights
Novel Pinus Roxburghii needle fibers were extracted by water retting process.
The physical and chemical composition and mechanical behavior of the extracted Pinus Roxburghii needle fibers were investigated.
The extracted Pinus Roxburghii needle fibers may be a potential reinforcement in the development of polymer composites
Acknowledgement
The authors gratefully acknowledge the Institute Instrument Center, IIT Roorkee; and South India Textile Research Association, Tamilnadu, for providing support for this work.
Disclosure statement
No potential conflict of interest was reported by the authors.
Additional information
Funding
References
- Akin, D. E., G. Henriksson, J. D. Evans, A. P. S. Adamsen, J. A. Foulk, and R. B. Dodd. 2004. Progress in enzyme-retting of flax. Journal of Natural Fibers 1 (1):21–15. doi:10.1300/J395v01n01_03.
- Alotaibi, M. D., B. A. Alshammari, N. Saba, O. Y. Alothman, M. R. Sanjay, Z. Almutairi, and M. Jawaid. 2019. Characterisation of natural fiber obtained from different parts of date palm tree (Phoenix dactylifera L.). International Journal of Biological Macromolecules 135:69–76. doi:10.1016/j.ijbiomac.2019.05.102.
- Amutha, V., and B. Senthilkumar. 2021. Physical, chemical, thermal, and surface morphological properties of the bark fiber extracted from acacia concinna plant. Journal of Natural Fibers 18 (11):1661–74. doi:10.1080/15440478.2019.1697986.
- Babu, B. G., D. Princewinston, S. S. Saravanakumar, A. Khan, P. V. A. Bhaskar, S. Indran, and D. Divya. 2022. Investigation on the physicochemical and mechanical properties of novel alkali-treated Phaseolus vulgaris fibers. Journal of Natural Fibers 19 (2):770–81. doi:10.1080/15440478.2020.1761930.
- Bledzki, A. K., and J. Gassan. 1999. Composites reinforced with cellulose-based fibers. Progress in Polymer Science 24 (2):221–74. doi:10.1016/S0079-6700(98)00018-5.
- Davies, P., C. Morvan, O. Sire, and C. Baley. 2007. Structure and properties of fibres from sea-grass (Zostera marina). Journal of Materials Science 42 (13):4850–57. doi:10.1007/s10853-006-0546-1.
- Faruk, O., A. K. Bledzki, H. P. Fink, and M. Sain. 2012. Biocomposites reinforced with natural fibers: 2000– 2010. Progress in Polymer Science 37 (11):1552–96. doi:10.1016/j.progpolymsci.2012.04.003.
- Fiore, V., T. Scalici, and A. Valenza. 2014. Characterisation of a new natural fiber from Arundo donax L. as potential reinforcement of polymer composites. Carbohydrate Polymer 106:77–83. doi:10.1016/j.carbpol.2014.02.016.
- Gairola, S., S. Gairola, H. Sharma, and P. K. Rakesh. 2019. Impact behavior of pine needle fiber/pistachio shell filler-based epoxy composite. Journal of Physics Conference Series, Kurukshetra, Haryana, India, 2019 February 18–22, 1240:1–7.
- Hyness, N. R. J., N. J. Vignesh, P. Senthamaraikannan, S. S. Saravanakumar, and M. R. Sanjay. 2018. Characterisation of new natural cellulosic fiber from heteropogon contortus plant. Journal of Natural Fibers 15 (1):146–53. doi:10.1080/15440478.2017.1321516.
- Indran, S., and R. E. Raj. 2015. Characterisation of new natural cellulosic fiber from Cissus quadrangularis stem. Carbohydrate Polymer 117:392–99. doi:10.1016/j.carbpol.2014.09.072.
- Indran, S., R. E. Raj, and V. S. Sreenivasan. 2014. Characterisation of new natural cellulosic fiber from Cissus quadrangularis root. Carbohydrate Polymer 110:423–29. doi:10.1016/j.carbpol.2014.04.051.
- Jeyabalaji, V., G. R. Kannan, P. Ganeshan, K. Raja, B. NagarajaGanesh, and P. Raju. 2021. Extraction and characterization studies of cellulose derived from the roots of Acalypha Indica L. Journal of Natural Fibers 19 (12):1–13. doi:10.1080/15440478.2020.1867942.
- Kabir, M. M., H. Wang, K. T. Lau, and F. Cardona. 2013. Tensile properties of chemically treated hemp fibers as reinforcement for composites. Composites Part B: Engineering 53:362–68. doi:10.1016/j.compositesb.2013.05.048.
- Kadam, A. A., S. Singh, and K. K. Gaikwad. 2021. Chitosan based antioxidant films incorporated with pine needles (Cedrus deodara) extract for active food packaging applications. Food Control 124:107877. doi:10.1016/j.foodcont.2021.107877.
- Kala, L. D., and P. M. V. Subbarao. 2018. Estimation of pine needle availability in the central Himalayan state of Uttarakhand, India for use as energy feedstock. Renewable Energy 128:9–19. doi:10.1016/j.renene.2018.05.054.
- Kambli, N., S. Basak, K. K. Samanta, and R. R. Deshmukh. 2016. Extraction of natural cellulosic fibers from cornhusk and its physico-chemical properties. Fibers and Polymers 17 (5):687–94. doi:10.1007/s12221-016-5416-0.
- Kathiresan, M., P. Pandiarajan, P. Senthamaraikannan, and S. S. Saravanakumar. 2016. Physicochemical properties of new cellulosic Artisdita hystrix leaf fiber. International Journal of Polymer Analysis and Characterization 21 (8):663–68. doi:10.1080/1023666X.2016.1194636.
- Krishna, M. G., C. Kailasanathan, and B. NagarajaGanesh. 2020. Physico-chemical and morphological characterisation of cellulose fibers extracted from Sansevieria roxburghiana Schult & Schult. f leaves. Journal of Natural Fibers 19:1–17.
- Kulandaivel, N., R. Muralikannan, and S. Kalyana Sundaram. 2018. Extraction and characterisation of novel natural cellulosic fibers from pigeon pea plant. Journal of Natural Fibers 17 (5):769–79. doi:10.1080/15440478.2018.1534184.
- Kumar, N., J. S. Grewal, N. Kumar, S. Kumar, and S. Ali. 2022. A novel Pinus roxburghii natural leaves fiber used as reinforcement polymer composite: As asbestos‐free brake friction material. Polymer Composites 43 (1):566–73. doi:10.1002/pc.26399.
- Lee, C. H., A. Khalina, S. H. Lee, and M. Liu. 2020. A comprehensive review on bast fibre retting process for optimal performance in fibre-reinforced polymer composites. Advances in Materials Science and Engineering 2020:1–27. doi:10.1155/2020/6074063.
- Madhu, P., M. R. Sanjay, S. Pradeep, K. S. Bhat, B. Yogesha, and S. Siengchin. 2019. Characterisation of cellulosic fibre from Phoenix pusilla leaves as potential reinforcement for polymeric composites. Journal of Materials Research and Technology 8 (3):2597–604. doi:10.1016/j.jmrt.2019.03.006.
- Manimaran, P., M. R. Sanjay, P. Senthamaraikannan, M. Jawaid, S. S. Saravanakumar, and R. George. 2018. Synthesis and characterisation of cellulosic fiber from red banana peduncle as reinforcement for potential applications. Journal of Natural Fibers 16 (5):768–80. doi:10.1080/15440478.2018.1434851.
- Manimaran, P., S. S. Saravanakumar, N. K. Mithun, and P. Senthamaraikannan. 2016. Physicochemical properties of new cellulosic fibers from the bark of Acacia arabica. International Journal of Polymer Analysis and Characterization 21 (6):548–53. doi:10.1080/1023666X.2016.1177699.
- Md, J. S., S. Madhu, K. S. Chakravarthy, and J. S. N. Raju. 2020. Characterization of natural cellulose fibers from the stem of Albizia Julibrissin as reinforcement for polymer composites. Journal of Natural Fibers 19 (6):2204–17. doi:10.1080/15440478.2020.1807440.
- Moshi, A. A. M., D. Ravindran, S. R. S. Bharathi, S. Indran, S. S. Saravanakumar, and Y. Liu. 2020. Characterisation of a new cellulosic natural fiber extracted from the root of Ficus religiosa tree. International Journal of Biological Macromolecules 142:212–21. doi:10.1016/j.ijbiomac.2019.09.094.
- Nagaraja, G. B., P. Ganeshan, P. Ramshankar, and K. Raja. 2019. Assessment of natural cellulosic fibers derived from Senna auriculata for making light weight industrial biocomposites. Industrial Crops and Products 139:111546. doi:10.1016/j.indcrop.2019.111546.
- Palai, B. K., S. K. Sarangi, and S. S. Mohapatra. 2021. Investigation of physiochemical and thermal properties of eichhornia crassipes fibers. Journal of Natural Fibers 18 (9):1320–31. doi:10.1080/15440478.2019.1691110.
- Pickering, K. L., M. A. Efendy, and T. M. Le. 2016. A review of recent developments in natural fibre composites and their mechanical performance. Composites Part A, Applied Science and Manufacturing 83:98–112. doi:10.1016/j.compositesa.2015.08.038.
- Porras, A., A. Maranon, and I. A. Ashcroft. 2015. Characterisation of a novel natural cellulose fabric from Manicaria saccifera palm as possible reinforcement of composite materials. Composites Part B: Engineering 74:66–73. doi:10.1016/j.compositesb.2014.12.033.
- Radzuan, M. N. A., N. F. Ismail, M. K. F. M. Radzi, Z. B. Razak, I. B. Tharizi, A. B. Sulong, C. H. C. Haron, and N. Muhamad. 2019. Kenaf composites for automotive components: Enhancement in machinability and moldability. Polymers 11 (10):1707. doi:10.3390/polym11101707.
- Raja, S., R. Rajesh, S. Indran, D. Divya, and G. S. Priyadharshini. 2021. Characterization of industrial discarded novel Cymbopogon flexuosus stem fiber: A potential replacement for synthetic fiber. Journal of Industrial Textiles 51 (1_suppl):1207S–34S. doi:10.1177/15280837211007507.
- Ramesh, M. 2018. Hemp, jute, banana, kenaf, ramie, sisal fibers. In Handbook of properties of textile and technical fibres, 301–25. Woodhead Publishing. doi:10.1016/B978-0-08-101272-7.00009-2.
- Ranakoti, L., P. K. Rakesh, and B. Gangil. 2021. Effect of Tasar silk waste on the mechanical properties of Jute/Grewia optiva fibers reinforced epoxy laminates. Journal of Natural Fibers 19 (15):10462–74. doi:10.1080/15440478.2021.1994089.
- Rao, K. M. M., A. V. R. Prasad, M. N. V. R. Babu, K. M. Rao, and A. V. S. S. K. S. Gupta. 2007. Tensile properties of elephant grass fiber reinforced polyester composites. Journal of Materials Science 42 (9):3266–72. doi:10.1007/s10853-006-0657-8.
- Saravanakumar, S. S., A. Kumaravel, T. Nagarajan, and I. G. Moorthy. 2014. Effect of chemical treatments on physicochemical properties of Prosopis juliflora fibers. International Journal of Polymer Analysis and Characterization 19 (5):383–90. doi:10.1080/1023666X.2014.903585.
- Segal, L., J. J. Creely, A. E. Martin, and C. M. Conrad. 1959. An empirical method for estimating the degree of crystallinity of native cellulose using the x-ray diffractometer. Textile Research Journal 29 (10):786–94. doi:10.1177/004051755902901003.
- Shanmugasundaram, N., and I. Rajendran. 2016. Characterisation of raw and alkali-treated mulberry fibers as potential reinforcement in polymer composites. Journal of Reinforced Plastics and Composites 35 (7):601–14. doi:10.1177/0731684415625822.
- Shanmugasundaram, N., I. Rajendran, and T. Ramkumar. 2018. Characterisation of untreated and alkali treated new cellulosic fiber from an Areca palm leaf stalk as potential reinforcement in polymer composites. Carbohydrate Polymer 195:566–75. doi:10.1016/j.carbpol.2018.04.127.
- Singha, A. S., and V. K. Thakur. 2008. Synthesis and characterization of pine needles reinforced RF matrix based biocomposites. E-Journal of Chemistry 5 (S1):1055–62. doi:10.1155/2008/395827.
- Tahir, P. M., A. B. Ahmed, S. O. A. Saiful Azry, and Z. Ahmed. 2011. Retting process of some bast plant fibers and its effect on fiber quality: A review. Bio Resources 6 (4):5260–81.
- Thakur, V. K., A. S. Singha, and M. K. Thakur. 2013. Fabrication and physico-chemical properties of high-performance pine needles/green polymer composites. International Journal of Polymeric Materials and Polymeric Biomaterials 62 (4):226–30. doi:10.1080/00914037.2011.641694.
- Vijay, R., D. L. Singaravelu, A. Vinod, M. R. Sanjay, S. Siengchin, M. Jawaid, A. Khan, and J. Parameswaranpillai. 2019. Characterisation of raw and alkali treated new natural cellulosic fibers from Tridax procumbens. International Journal of Biological Macromolecules 125:99–108. doi:10.1016/j.ijbiomac.2018.12.056.
- Vinod, A., R. Vijay, D. L. Singaravelu, M. R. Sanjay, S. Siengchin, Y. Yagnaraj, and S. Khan. 2021. Extraction and characterisation of natural fiber from stem of cardiospermum halicababum. Journal of Natural Fibers 18 (6):898–908. doi:10.1080/15440478.2019.1669514.