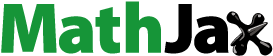
ABSTRACT
Hornification is an irreversible effect that occurs on lignocellulosic fibers when they are subjected to drying and re-wetting cycles. This study aimed to evaluate okra and raffia fibers morphological, physico-chemical, and mechanical properties. The fibers were subjected to four and six wet-dry treatment cycles to assess the effect of the number of cycles on the performance of each fiber. The results show that four wet-dry cycles show an increase in density from 1.40 g/cm3 to 1.78 g/cm3 and from 1.34 g/cm3 to 1.58 g/cm3 for okra and raffia fibers, respectively. Furthermore, a decrease in fiber lumen is observed, resulting in a reduction in water absorption capacity of up to 18.3% for raffia fiber and 56.3% for okra after four hornification cycles. Statistical analysis reveals a significant improvement in the elastic modulus of raffia fiber up to 37% after treatment, while no significant improvement is observed in the elastic modulus and tensile strength of okra fiber. This is attributed to the strengthening of intracellulosic bonds, which resulted in the creation of more available -OH sites on the fibers. The physico-chemical and mechanical changes in fiber properties resulting from wet-dry processing have demonstrated their suitability to replace synthetic fibers in composites.
摘要
木质纤维素纤维在经历干燥和再润湿循环时发生的角质化是一种不可逆的效应. 本研究旨在评估黄秋葵和拉斐亚纤维的形态、理化和机械财产. 对纤维进行4次和6次干湿处理循环,以评估循环次数对每种纤维性能的影响. 结果表明,4次干湿循环分别使okra和rafia纤维的密度从1.40 g/cm3增加到1.78 g/cm3,从1.34 g/cm3增加到1.58 g/cm3. 此外,观察到纤维管腔的减少,导致4个角质化周期后,拉菲亚纤维的吸水能力降低了18.3%,秋葵的吸水能力下降了56.3%。统计分析表明,处理后,拉菲亚纤维的弹性模量显著提高了37%,而秋葵纤维的弹性模数和拉伸强度没有显著提高. 这归因于胞内键的增强,导致纤维上产生更多可用的-OH位点. 干湿加工引起的纤维财产的物理化学和机械变化表明,它们适合取代复合材料中的合成纤维.
Introduction
The use of lignocellulosic fibers from biomass as a reinforcing element in brittle matrices such as concrete, papercrete, paper bricks and cement-stabilized earth bricks is the ultimate green material option, which not only improves resistance to crack propagation (Stanislas et al. Citation2021b) but also valorizes agricultural waste (Akinwande et al. Citation2021; Mejouyo et al. Citation2022). Due to their low density, high strength, low cost compared to synthetic fibers, high availability, especially in tropical countries, and hydrophilic character, lignocellulosic fibers are ideal candidates for the construction sector (Ojo et al. Citation2020; Stanislas et al. Citation2021b). However, the use of lignocellulosic fibers in concrete, papercrete, and paperbricks composites is hampered by their poor adhesion and durability due to their low dimensional stability (Mainier and Mahler Citation2018; Savastano et al. Citation2000). In this sense, the scientific community has made considerable efforts in recent years to develop procedures such as hornification treatment (Ballesteros et al. Citation2019; Mejia-Ballesteros et al. Citation2021) and alkali and silane treatments (Akinwande et al. Citation2021, Citation2021; Youbi et al. Citation2022) to improve the durability of fiber-cement composites (Ballesteros et al. Citation2017, Citation2019) and to reduce the water absorption capacity of the plant fibers to improve the bond between the matrix and the fibers (Ballesteros et al. Citation2015; Ferreira et al. Citation2014, Citation2015b).
The wetting and drying treatment approach on lignocellulosic fibers showed promising results in improving the dimensional stability of the fiber and reducing the hydrophilicity of the fiber, which led to the improvement of the fiber–matrix interface (Mejia-Ballesteros et al. Citation2021). This treatment induces a permanent change in the morphology of the plant fibers, increasing the degree of cross-linking in the microstructure of the fibers, which contributes to modifying the mechanical and physical behavior (Ferreira et al. Citation2014). According to Claramunt et al. (Citation2011), the hornification treatment of cellulose fiber is defined as an irreversible effect that appears on the fiber when it is subjected to wetting and drying cycles. This impact of hornification can be quantified by the percentage decrease in water retention values, which leads to a change in fiber size due to the formation of hydrogen bonds in the cellulose and does not reduce the strength of the fibers compared to the chemical treatment (Claramunt, Ardanuy, and García-Hortal Citation2010). The hornification mechanism was first described by Jayme (Jayme Citation1943), who reported that the drying process of the cellulose fiber progressively closed the capillary voids and could not be completely re-opened by further water intrusion. The irreversibly treated cell wall was less swollen and less flexible compared to the previous state before drying, and if subjected to rewetting, some surfaces remained coalesced, reducing the surface area of the fibers accessible to water (Fernandes Diniz, Gil, and Castro Citation2004). shows the studies on the hornification treatment of various plant fibers to modify dimensional stability, water absorption, and mechanical performance. For instance, Ballesteros et al. (Citation2017) showed that four cycles of hornification of eucalyptus fiber decrease the water retention values and modify the morphology of the fiber such as contraction of the lumen and increase the surface roughness.
Table 1. Previous studies on the hornification treatment of vegetable fibers.
In sub-Saharan Africa (central and western), artisans use raffia vinifera products as a raw material for textiles and in the production of decorative objects such as chairs, mats, baskets, cabinets, or ceilings (Tagne et al. Citation2017). It should be noted that in the West, Center, Littoral, and North-West regions of Cameroon, people use these baskets to transport food products such as tomatoes, chickens, goats, and pigs. Raffia vinifera is an uncultivated plant produced in abundance in tropical areas (Stanislas et al. Citation2020); the fiber of the raffia vinifera stem has a particular internal structure, i.e. it is spongy, which makes it potentially interesting for the development of composites for thermal insulation materials (Tagne et al. Citation2017). Various works have been carried out on the physicochemical and mechanical behavior of raffia fiber (Elenga et al. Citation2009), the kinetics of drying and water absorption (Mbou et al. Citation2017; Sikame Tagne et al. Citation2014), the viscoelastic behavior of raffia fiber (Tagne et al. Citation2018), and the production of cellulose pulp and nanofibrillated cellulose (Stanislas et al. Citation2020, Citation2022). These preliminary investigations by Djoumessi et al. (Citation2022), Mbou et al. (Citation2017), Stanislas et al. (Citation2021b), and Tagne et al. (Citation2013) reveal a high porosity, low density, high water absorption capacity of raffia fiber, with a diameter of approximately 1 mm, suggesting the need for pre-treatment before their application as reinforcement in organic and inorganic matrices (Stanislas et al. Citation2021a, Citation2021b). Recently, Filho et al. (Citation2020) evaluated the effect of alkaline treatment of raffia vinifera fiber on the tensile strength of raffia fiber/polyester composite. The results reveal that composites with alkali-treated fibers showed lower tensile strength values than the untreated state due to poor adhesion between the raffia fiber and the polyester matrix.
Okra fiber, botanical name Abelmoschus esculentus, is a plant of the Malvaceae family extracted from the bark of the okra bahmia (Moniruzzaman, Mohd Maniruzzaman, and Santulli Citation2009). Okra (A. esculentus) is grown on about 2 million hectares and produces about 10 million tonnes of pods worldwide (Schafleitner et al. Citation2021). The largest producer is India, with about 6 million tonnes of fresh pods harvested, followed by Nigeria with about 2 million tonnes (FAOSTAT Citation2020). The economic importance of okra is growing not only due to the increasing local and international demand for fresh vegetables but also for its use as an alternative source of oil for human consumption or as biofuel (Moosavi et al. Citation2018) and for medicinal products (Das, Nandi, and Ghosh Citation2019). However, after harvesting the fruit, the stems are usually left as waste on the farm. According to (Rahman et al. Citation2018), about 2 kg of good-quality okra fiber can be extracted from 37 kg of the stem, which corresponds to a yield of 2–2.5% dry fiber. Previous studies on the morphology and mechanical properties of okra fibers have shown high porosity and a wide variation in tensile strength and modulus values (De Rosa et al. Citation2010) and raise the need for surface treatments to improve their morphology and tensile properties before potential application as reinforcing agents in polymer composites. Moniruzzaman, Mohd Maniruzzaman, and Santulli (Citation2009) subjected okra fiber to chemical treatment (bleaching with sodium hypochlorite, soaking in NaOH, NaSO4, or CH3COOH), and the results reveal that only bleaching treatment slightly improves the tensile strength of okra fiber. The authors attributed the reduction in tensile properties after chemical treatments to the degradation of the lignocellulosic structure of the fiber. Similar behavior was reported by De Rosa et al. (Citation2011), who showed that chemical treatment, including fiber scouring, pure acetylation, sodium sulfite, and sulfuric acid with potassium permanganate, bleaching (pure followed by acetylation or alkalinization) reduced tensile strength, Young's modulus, and inter-fibril bond strength. Although the chemical treatment of okra and raffia fiber improves the dimensional stability (De Rosa et al. Citation2011; Moniruzzaman, Mohd Maniruzzaman, and Santulli Citation2009), the reduced mechanical performance of the fibers associated with their degradation, as well as environmental concerns related to the use of various chemical reagents, are the main limitations to their use. However, the hornification treatment, which corresponds to several wetting and drying cycles, has the effect of modifying the microstructure of the lignocellulosic fibers and promoting the stiffening of the polymeric structure of the fiber cells (Amaral, de Souza Rodrigues, and Spitale Jacques Poggiali Citation2022; Mendes et al. Citation2021; Mendonçaa et al. Citation2018). Santos, de, and Roberto Lopes Lima (Citation2014) subjected sisal fiber to 6, 10, 30, and 34 hornification cycles and the tensile strength results reveal that an excessive number of cycles (more than six cycles) can lead to a decrease in the tensile strength of plant fibers. Furthermore, Ferreira et al., (2015) demonstrated that three and six hornification cycles were sufficient to improve the tensile strength of curaua fiber from 632.14 MPa to 895.40 MPa and 931.52 MPa, respectively. According to these authors, after six cycles, there may be initial damage to the fiber, leading to a reduction in mechanical strength. As this wet-dry treatment mechanism is not fully understood, there are still several gaps regarding the effect of the number of wet-dry cycles on the fiber type and to what extent it can improve the morphology and mechanical behavior of the fiber. To date, information on the hornification treatment of raffia and okra fibers from the stem remains unknown. This study aims to evaluate the effect of the number of wetting and drying cycles on the physicochemical, morphological, and mechanical performance of two different fibers: raffia and okra.
Materials and methods
Materials
The raffia fiber used in this work was extracted from the stem of Raphia vinifera from Melong, Littoral region of Cameroon. It was soaked in distilled water at room temperature for 2 days before being extracted (Stanislas et al. Citation2020) as shown in . The chemical composition of the raffia fiber was 48.3% cellulose, 24.9% hemicellulose, 3.66% lignin, 1.34% fat and wax, 1.04% ash, and 2.59% water extract (Stanislas et al. Citation2020). Okra (Abelmoschus esculentus) is collected in the littoral region and extracted from the bark of stem of the plant by the water immersion process for 15 days as shown in .
Methods
Fiber treatment
The hornification treatment of the raffia and okra fiber was carried out according to the methodology developed by (Ferreira et al., 2015) with a slight modification. Approximately 200 g of each raw material was transferred to a container of water at about 22 ºC and held for 3 hours to reach their maximum water absorption capacity. The fibers were removed and dried at a temperature of 60 ºC in an oven. After 16 hours of drying, the sample was removed and cooled to 22 ºC to avoid possible thermal shock of the fibers. This procedure was repeated 4 and 6 times (Ferreira et al., 2015).
Density determination
An initial weight of 2 g of untreated and treated raffia and okra fibers was oven dried at 70°C for 24 hours and stored in a desiccator at room temperature. The density of each sample was determined by measuring the weight of the dry fiber before introducing it into the Quanta Chrome Instruments multi-pycnometer. Helium gas was used to measure the volume of the fibers using the pycnometer, and the density was determined using the method described by Sreedhara and Tata (Citation2013).
Percentage of water absorption
The evaluation of water absorption before and after treatment was performed using the gravimetric analysis method. An initial weight of 1 g of fiber was oven dried at 70 ºC for 24 hours and then introduced into distilled water in the laboratory room estimated at 23 ºC ±1 ºC. The fiber samples were held under water by stainless steel nuts. The weight was recorded daily until stability was achieved (Mbou et al. Citation2017). The percentage of water absorption (WA) was determined according to EquationEquation 1(1)
(1) (Mbou et al. Citation2017),
where mi is the initial weight (g) and mf is the final weight (g) of the sample.
Morphological characterization
Treated and untreated raffia and okra fibers were examined under a ZEISS EVO/LS10 scanning electron microscope (SEM) for image acquisition at the voltage of 15 kV to assess the effect of the treatments on the modification of their surface properties along their cross-section. The raffia and okra fibers were cut by a razor blade to a short length before cross-sectional analysis. shows that the cross-section has an elliptical shape (Tagne et al. Citation2017), while the cross-section of okra fibers has been assumed to be circular (De Rosa et al. Citation2010). The large and small diameters a and b, respectively, were measured using ImageJ software. The cross-sectional area S of raffia fibers was calculated using equation (2) (Cai et al. Citation2015),
Fourier transform infrared spectroscopy
Fourier transform infrared spectroscopy (FTIR) was used to determine alterations in the functional chemical groups and structure of cellulose after the pulping process. Spectra were obtained using a Thermo Scientific NICOLET iS5 infrared spectrometer and the standard KBr pellet technique, in the 400–4000 cm−1 range. The absorbance of the spectrum was recorded as a function of wave number.
Mechanical testing
The tensile tests of untreated and treated fibers were performed in an electromechanical testing machine MTS Systems Corporation 14,000 Technology Drive with a load cell of 100 N. At least 25 fibers were tested for each cycle number using a displacement speed of 0.1 mm/min. The initial length of the fibers was 40 mm and for better alignment in the machine, the fibers were glued to a paper template for a better grip with the upper and lower jaws, according to ASTM C1557 (Ferreira et al., 2015). The fiber tensile strength and elastic modulus were evaluated according to the methodology described by (Tagne et al. Citation2017). The analysis of variance one-way ANOVA test as well as the Tukey’s HSD (Honestly significant difference) test at a confidence level of 0.95 was carried out to evaluate the effect of hornification treatment on the mechanical performance of the raffia and okra fibers.
Results and discussion
Fiber density and water absorption
The water absorption process of lignocellulosic fibers is mainly driven by the hemicellulose compound, but lignin and crystalline cellulose also play an important role. In this study, the density and water absorption capacity of untreated and treated raffia and okra fibers were determined and the results are reported in . As shown in the hornification treatment of raffia and okra fibers increased the density from 1.34 g/cm3 to 1.58 g/cm3 for raffia fibers and 1.40 g/cm3 to 1.78 g/cm3 for okra fibers, while the water absorption decreased from 691% to 564% for raffia fibers and 326% to 142% for okra fibers. Previous studies on raffia vinifera show that the water absorption and bulk density of its fibers vary between 303% and 662% and 0.12 g/cm3 and 0.24 g/cm3 (Sikame Tagne et al. Citation2014), while the water absorption of its pith varies between 392 and 1331% (Mbou et al. Citation2017). The maximum value of density as well as the minimum value of water absorption of raffia and okra fibers is reached after four cycles of hornification, with a slight tendency to reverse after six cycles. This behavior can be attributed to the collapse of the fiber wall due to the drying condition and also to the closure of the pores in the fiber wall due to the loss of the swelling capacity of the treated fibers (Köhnke et al. Citation2010). This increase in density affects the porosity of the fibers, changing the pore size and reducing their capacity to absorb water (Ballesteros et al. Citation2017). However, the analysis of the reduction of water absorption capacity due to hornification treatment reveals that the water absorption of raffia fiber reduced by 18.3% after four cycles of hornification, while okra fiber decreased to 56.3%. This reduction reflects the percentage of hornification between untreated and treated raffia and okra fibers. According to Ferreira et al. (2015), the decrease in water uptake after hornification treatment of lignocellulosic fiber is related to the modification of the COOH functional group, which leads to an increase in the hydrophobicity of the lignin. A similar trend has been reported on hornification treatment of sisal, curaua and jute fibers (Ferreira et al. Citation2015b), cotton fiber (Claramunt, Ardanuy, and García-Hortal Citation2010), cellulose pulp from eucalyptus (Ballesteros et al. Citation2017; Letková, Letko, and Vrška Citation2011), and pine (Ballesteros et al. Citation2017). In addition, this variation of the physical properties during wetting-drying treatment can be associated with the modification of the polymeric structure of the lignocellulosic fiber (Ferreira et al., Citation2015a).
Morphological properties of Raffia and Okra fibres
The porosity of materials is closely related to the microstructure of the materials. presents the cross-sectional area of untreated and treated raffia fiber (a-c) and okra fiber (d-f). The images show a shrinkage of the fiber cross-section after the wetting-drying process. The slight loss of cross-sectional area after hornification treatment can be attributed to the fact that drying of the lignocellulosic fiber from polar liquids, such as water, induces collapse of the lumens, reduction of the specific fiber surface area and loss of internal surface (Köhnke et al. Citation2010). The evaluation of the cross-sectional area value of the untreated and treated raffia and okra fibers () provides evidence of the irreversible reduction of the morphological properties of the fiber subjected to the hornification treatment. Similar behavior has been reported elsewhere (Ballesteros et al. Citation2019; Köhnke et al. Citation2010; Tonoli et al. Citation2009) and attributed to the decrease in the degree of cross-linking induced by the drying of the fiber wall. However, oscillation in fiber morphological properties during the wetting and drying process () was observed along the cycles, which can be attributed to the dissolution of water-soluble products (Coradini et al. Citation2020). Similar behavior was reported by (Coradini et al. Citation2020) on the hornification of moso bamboo, which according to the authors, may be due to the constrained swelling of the fiber, resulting from the excessive number of wet-dry cycles. Another explanation for this behavior may be the proximity of the fibrils that come into contact after drying (Jayme and Hunger Citation1957), and the polysaccharide chains of the cellulose are packed together (firm packing) with the removal of water (Jayme Citation1943), causing the microfibrils to bind together like a flat band (Ackermann, Gottsching, and Pakarinen Citation2000; Fernandes Diniz, Gil, and Castro Citation2004). All this leads to the irreversible loss of the water retention capacity of the fibers (Ballesteros et al. Citation2017, Citation2019) and to the collapse of the plant fiber without its strength properties being radically altered (Ballesteros et al. Citation2015, Citation2017).
FTIR spectroscopy of Raffia and Okra fibres
The FTIR analysis was carried out to evaluate the effect of hornification treatment on the chemical compound of untreated and treated raffia fiber. shows the spectra of lignocellulosic raffia () and okra () fibers before and after four and six hornification treatments. Okra fibers subjected to four and six repeated cycles of wet-dry treatment show a reduction in the peak intensity of the hemicellulose C=O bond and the lignin C=C bond (aromatic ring) compared to untreated raffia fibers. In addition, the aromatic hydrogen of the lignin compound, represented by the C-H (para) bond, was reduced after four and six cycles of hornification treatment. Furthermore, the reduction in the intensity of the fiber-OH bond peak with the increasing number of hornification cycles at the wave number of 1640 cm−1 for both raffia and okra fibers was observed. This can be attributed to the adsorbed aliphatic water of the cellulose indicating the reduction of the hydrophilic capacity of the raffia and okra fiber after treatment (Tenazoa et al. Citation2019). Compared to the untreated okra and raffia fibers, there is evidence of the reduction of the hemicellulose of the raffia and okra fibers after the hornification treatment. The peak at 1640 cm−1 and the wide range of 3300–3500 cm−1 present in all spectra are attributed to the axial vibrational characteristics of the hydroxyl group of the cellulose (preferably carbon 2, 3, and 6 of glucose) (Correia et al. Citation2016; Li et al. Citation2009; Santos, de, and Roberto Lopes Lima Citation2014). The reduction in the intensity of these peaks after four and six cycles of hornification treatment of okra and raffia fibers is associated with the reduction of the water content of the fiber. The absorption peak at 2927 cm−1 represents the C-H stretching vibration of methyl and methylene groups, which indicated the existence of lignin (Wang et al. Citation2022). The reduction of this peak intensity with increasing wet-dry cycles may be associated with the partial removal of the amorphous compound (lignin) during the hornification process (Mendes et al. Citation2021). These evaluations of all spectra did not identify a complete disappearance of the main peaks. Furthermore, this slight loss of lignin and hemicellulose is correlated with the reduction of the water absorption capacity of the raffia and okra fibers by modification of the chemical bonding, which may lead to a reduction in the hydrophilic character of the fiber.
Mechanical properties
presents the average value and the standard deviation of tensile strength and elastic modulus of raffia and okra fiber before and after the hornification treatment. The results show an improvement of the mechanical performance of both raffia and okra fiber after the wetting and drying treatment. Statistical analysis reveals that increasing the number of cycles significantly improves the elastic modulus of raffia fiber at the 95% confidence level, while no significant improvement is observed in the elastic modulus and tensile strength of okra fiber. This improvement of the mechanical properties is consistent with the density and morphology of the fiber, which can be attributed to the change in pore size of the fiber wall as it collapses during drying (Köhnke et al. Citation2010). Similar behavior has been reported by Ferreira et al. (2015) and Mendes et al. (Citation2021) on sisal fibers. According to Ferreira et al. (2015), the explanation for the increase in tensile strength is attributed to the microstructural change of the fibers due to the modification of the polymer structure of the fiber cells. Moreover, the hydroxyl groups of cellulose, lignin, and hemicellulose compounds form new hydrogen bonds with water molecules during the wetting process, with induced swelling. However, the repetition of wetting–dying cycle applied to raffia and okra fiber increases the number of hydrogen bonds, induces structural changes in fiber cell wall, and increases the number of (−OH) bonds (Ferreira et al., 2015). This increase in the network of lignin macromolecules promotes better interaction between lignin and cellulose and hemicellulose and results in a stronger fiber with high stiffness and deformability (Ferreira et al., 2015). This hornification treatment of okra fiber increases the tensile strength from 224.30 MPa to 238.80 MPa and the modulus of elasticity from 16.06 GPa to 17.17 GPa (), which is within the range of values reported in the literature on chemical treatment of okra fiber (De Rosa et al. Citation2011; Moniruzzaman, Mohd Maniruzzaman, and Santulli Citation2009; Shamsul Alam and Arifuzzaman Khan Citation2007). Compared to chemical treatment, both chemical and hornification treatments lead to the reduction of water absorption capacity and dimensional instability of okra fiber, but the use of chemical reagents affects the structural integrity of the fibers, resulting in the reduction of their tensile strength from 370.7 MPa to 200.6 MPa and elastic modulus from 16.9 GPa to 6.2 GPa (De Rosa et al. Citation2011). In addition, the tensile strength and modulus of elasticity of the raffia fiber increased from 15.95 MPa to 18.48 MPa and from 0.39 GPa to 0.53 GPa, respectively, which are still low compared to the values reported by Tagne et al. (Citation2017) and Youbi et al. (Citation2022) on raffia vinifera fiber. This low value of this untreated raffia fiber compared to the literature may be related to the area of collection of the raw material. Indeed, previous studies conducted on the same raffia fibers collected in two localities in the western region of Cameroon gave different mechanical performances: the modulus of elasticity and tensile strength of the raffia fibers collected in Bandgoun varied from 0.88 to 7.90 GPa, and 24.16 to 48.28 MPa, respectively (Tagne et al. Citation2017), while the modulus of elasticity of the same fiber collected in Baham varied from 1.49 to 2.88 GPa and 32.72 to 91.09 MPa, respectively (Youbi et al. Citation2022). These results suggest the need for a study to evaluate the effect of the collection site of raffia vinifera fibers on their mechanical properties.
Table 2. Mechanical performance in the tensile test expressed as mean ± standard deviation of untreated and hornification treated raffia and okra fibers.
presents the typical stress–strain curve of untreated and hornified raffia () and okra () fibers. The results reveal that hornified treated okra and raffia fibers presented a higher stiffness and tensile strength compared to untreated fibers. Similarly, Mendes et al. (Citation2021) showed that increasing the number of hornification cycles of sisal fiber improved stiffness, while tensile strength decreased. According to the authors, a contact time of 3 hours between water and fibers can promote deeper penetration of water through the pores of the fibers, which can promote efficient partial removal of the hemicellulose compound. In addition, this change may create more -OH sites available on the fibers, which increases the hornification process by creating more and stronger intracellulosic bonds. This increase may be responsible for the increased stiffness of the okra and raffia fibers.
Conclusions
The effect of the number of wetting-drying cycles on the physicochemical and mechanical properties of two different fibers: raffia and okra, was studied. The results reveal an increase in density, tensile strength, and elastic modulus for both raffia and okra fibers after four hornification cycles. This increase in density is associated with a reduction in the water absorption capacity of the raffia fiber estimated at 18.3% and of the okra fiber estimated at 56.3% after four hornification cycles. This behavior is attributed to the deeper penetration of water into the pores of the fibers, which promotes efficient partial removal of hemicellulose and consequently creates more available -OH sites on the fibers, as well as stronger intracellulosic bonds. This is consistent with the microstructures of the fiber cross-section, which shrinks after the hornification process. Furthermore, statistical analysis of the mechanical properties reveals that increasing the number of cycles significantly improves the elastic modulus of the raffia fiber at the 95% confidence level, while no significant improvement is observed on the Young’s modulus and tensile strength of the okra fiber. For okra and raffia fibers, four wet-dry cycles were more effective in partially removing hemicellulose and lignin, reducing water absorption, and increasing tensile properties. The chemical, physical, and mechanical changes in fiber properties resulting from wet-dry processing have demonstrated their suitability for use as an alternative to synthetic fibers in concrete, papercrete, paperbricks, and earth-based composites. However, the low value of tensile strength of raffia fiber compared to the literature suggests the need for a study to assess the effect of the raffia vinifera fiber collection site on its mechanical properties.
Authors’ contributions
I declare that all the authors had a significant participation in the development of this work.
Availability of data and material
The raw data required to reproduce these findings cannot be shared at this time as the data also form part of an ongoing study.
Highlights
Four cycles of hornification induced a reduction in water absorption estimated at 18.3% for raffia fiber and 56.3% for okra fiber,
- The highest density of raffia and okra fibers, which corresponds to the lowest water absorption capacity, is reached after four wet drying cycles,
The modulus of elasticity of raffia fiber increases significantly after wet drying cycles, while no significant changes were found in okra fiber,
The FTIR spectra show a partial removal of hemicellulose, which creates more available -OH sites on the fibers, resulting in stronger intracellulosic bonds.
Acknowledgements
The authors would like to thank Professor Holmer Savastano Junior and all the researchers and technicians of the Construction and Environment Laboratory (FZEA-USP, Brazil) for their collaboration during the nine-month internship at the laboratory.
Disclosure statement
The authors declare that they have no known competing financial interests or personal relationships that could have appeared to influence the work reported in this paper.
References
- Ackermann, C., L. Gottsching, and H. Pakarinen. 2000. Papermaking potential of recycled fiber. Recycled Fiber and Deinking 7:359–15.
- Akinwande, A. A., A. A. Adediran, O. A. Balogun, O. S. Olusoju, and O. S. Adesina. 2021. Influence of Alkaline modification on selected properties of banana fiber paperbricks. Scientific Reports 11 (1):1–18. doi:10.1038/s41598-021-85106-8.
- Akinwande, A. A., A. Adesoji Adediran, A. Balogun, O. Seun Adesina, O. Samuel Olasoju, A. Felix Owa, T. John Erinle, and E. Titilayo Akinlabi. 2021. Assessment of Alkaline treatment of palm Kernel fiber and curing duration on selected properties of cement-paper composite boards assessment of Alkaline treatment of palm Kernel fiber and curing duration on selected properties of cement-paper composite bo. Cogent Engineering 8:1. doi:10.1080/23311916.2021.1909690.
- Amaral, L. M. D., C. de Souza Rodrigues, and F. Spitale Jacques Poggiali. 2022. Hornification on vegetable fibers to improve fiber-cement composites: A critical review. Journal of Building Engineering 48 (December 2021):103947. doi:10.1016/j.jobe.2021.103947.
- Ballesteros, J. E. M., V. dos Santos, G. Mármol, M. Frías, and J. Fiorelli. 2017. Potential of the hornification treatment on eucalyptus and pine fibers for fiber-cement applications. Cellulose. 24(5):2275–86. doi:10.1007/s10570-017-1253-6.
- Ballesteros, J. E. M., S. Francisco Santos, G. Mármol, H. Savastano, and J. Fiorelli. 2015. Evaluation of cellulosic pulps treated by hornification as reinforcement of cementitious composites. Construction and Building Materials 100:83–90. doi:10.1016/j.conbuildmat.2015.09.044.
- Ballesteros, J. E. M., G. Mármol, R. Filomeno, L. Rodier, H. Savastano, and J. Fiorelli. 2019. Synergic effect of fiber and matrix treatments for vegetable fiber reinforced cement of improved performance. Construction and Building Materials 205:52–60. doi:10.1016/j.conbuildmat.2019.02.007.
- Belouadah, Z., A. Ati, and M. Rokbi. 2015. Characterization of new natural cellulosic fiber from Lygeum spartum L. Carbohydrate Polymers 134:429–37.
- Cai, M., H. Takagi, A. N. Nakagaito, M. Katoh, T. Ueki, G. I. N. N. Waterhouse, and L. Yan. 2015. Influence of Alkali treatment on internal microstructure and tensile properties of Abaca fibers. Industrial Crops and Products 65:27–35. doi:10.1016/j.indcrop.2014.11.048.
- Claramunt, J., M. Ardanuy, J. Antonio García-Hortal, and R. Dias Tolêdo Filho. 2011. The hornification of vegetable fibers to improve the durability of cement mortar composites. Cement and Concrete Composites 33 (5):586–95. doi:10.1016/j.cemconcomp.2011.03.003.
- Claramunt, J., M. Ardanuy, and J. A. García-Hortal. 2010. Effect of drying and rewetting cycles on the structure and physicochemical characteristics of softwood fibres for reinforcement of cementitious composites. Carbohydrate Polymers 79 (1):200–05. doi:10.1016/j.carbpol.2009.07.057.
- Coradini, S., G. Cid, D. Carlos, T. Cardoso, and F. De Andrade. 2020. Influence of hornification on the physical and flexural properties of moso bamboo. Construction and Building Materials 248:118701. doi:10.1016/j.conbuildmat.2020.118701.
- Correia, V. D. C., V. dos Santos, M. Sain, S. Francisco Santos, A. Lopes Leão, and H. Savastano Junior. 2016. Grinding process for the production of nanofibrillated cellulose based on unbleached and bleached bamboo organosolv pulp. Cellulose 23 (5):2971–87. doi:10.1007/s10570-016-0996-9.
- Das, S., G. Nandi, and L. K. Ghosh. 2019. Okra and its various applications in drug delivery, food technology, health care and pharmacological aspects-a review. Journal of Pharmaceutical Sciences and Research 11 (6):2139–47.
- Defroirdt, N., S. Biswas, L. De Vriese, J. Van Acker, Q. Ahsan, L. Gorbatikh, A. VanVuure, and I. Verpoest. 2010. Assessment of thetensile properties of coir, bamboo and jute fibre. Composite Part a. Applied Science and Manufacturing 41 (5):588–95.
- De Rosa, I. M., J. M. Kenny, M. Maniruzzaman, M. Moniruzzaman, M. Monti, D. Puglia, C. Santulli, and F. Sarasini. 2011. Effect of chemical treatments on the mechanical and thermal behaviour of Okra (Abelmoschus Esculentus) Fibres. Composites Science and Technology 71 (2):246–54. doi:10.1016/j.compscitech.2010.11.023.
- De Rosa, I. M., J. Maria Kenny, D. Puglia, C. Santulli, and F. Sarasini. 2010. Morphological, thermal and mechanical characterization of okra (abelmoschus esculentus) fibres as potential reinforcement in polymer composites. Composites Science and Technology 70 (1):116–22. doi:10.1016/j.compscitech.2009.09.013.
- Djoumessi, A. K., R. Nicodème Sikame Tagne, T. Tiwa Stanislas, F. Ngapgue, and E. Njeugna. 2022. Optimization of the young’s modulus of woven composite material made by Raphia Vinifiera fiber/epoxy. International Journal for Simulation and Multidisciplinary Design Optimization 13:21. doi:10.1051/smdo/2022014.
- Elenga, R. G., G. F. Dirras, J. Goma Maniongui, P. Djemia, and M. P. Biget. 2009. On the microstructure and physical properties of untreated Raffia textilis fiber. Composites Part A, Applied Science and Manufacturing 40 (4):418–22. doi:10.1016/j.compositesa.2009.01.001.
- FAOSTAT. 2020. “Production Quantities of Okra by Country.” https://www.fao.org/faostat/en/#data/QCL/visualize.
- Fernandes Diniz, J. M. B., M. H. Gil, and J. A. A. M. Castro. 2004. Hornification - its origin and interpretation in wood pulps. Wood Science and Technology 37 (6):489–94. doi:10.1007/s00226-003-0216-2.
- Ferreira, S. R., F. De Andrade Silva, P. Roberto Lopes Lima, and R. Dias Toledo Filho. 2015a. Effect of fiber treatments on the sisal fiber properties and fiber-matrix bond in cement based systems. Construction and Building Materials 101:730–40. doi:10.1016/j.conbuildmat.2015.10.120.
- Ferreira, S. R., F. de Andrade Silva, P. Roberto Lopes Lima, and R. Dias Toledo Filho. 2015b. Effect of Natural Fiber Hornification on the Fiber Matrix Interface in Cement Based Composite Systems. Key Engineering Materials 668:118–25. doi:10.4028/scientific.net/kem.668.118.
- Ferreira, S. R., P. R. L. Lima, F. A. Silva, and R. D. Toledo Filho. 2014. Effect of sisal fiber hornification on the fiber-matrix bonding characteristics and bending behavior of cement based composites. Key Engineering Materials 600:421–32. doi:10.4028/scientific.net/KEM.600.421.
- Filho, E. G. D. O., F. S. D. Luz, R. T. Fujiyama, A. C. R. D. Silva, V. S. Candido, and S. N. Monteiro. 2020. Effect of chemical treatment and length of raffia fiber (Raphia Vinifera) on mechanical stiffening of polyester composites. Polymers 12 (12):1–17. doi:10.3390/polym12122899.
- Jayme, G. 1943. Über Die Reaktionsfähigkeit von Zellstoffen. Cellulosechemie 21:73–86.
- Jayme, G., and G. Hunger. 1957. “The REarrangement of microfibrils in dried cellulose and the implication of this structure alteration on pulp properties.” Fundamentals of Papermaking Fibres, 263–70.
- Köhnke, T., K. Lund, H. Brelid, and G. Westman. 2010. Kraft pulp hornification: A closer look at the preventive effect gained by glucuronoxylan adsorption. Carbohydrate Polymers 81 (2):226–33. doi:10.1016/j.carbpol.2010.02.023.
- Letková, E., M. Letko, and M. Vrška. 2011. Influence of recycling and temperature on the swelling ability of paper. Chemical Papers 65 (6):822–28. doi:10.2478/s11696-011-0089-z.
- Li, R., J. Fei, Y. Cai, L. Yufeng, J. Feng, and J. Yao. 2009. Cellulose whiskers extracted from mulberry: A novel biomass production. Carbohydrate Polymers 76 (1):94–99. doi:10.1016/j.carbpol.2008.09.034.
- Mainier, B., and F. Mahler, and others. 2018. “Study of wet-drying cycles on sisal, jute and white Curaua fibers on the resistance parameters of cement-based composites.”
- Mbou, E., E. N. Tiaya, A. Kemajou, N. R. T. Sikame, and D. Ndapeu. 2017. Modelling of the water absorption kinetics and determination of the water diffusion coefficient in the Pith of Raffia Vinifera of Bandjoun, Cameroon. Advances in Materials Science and Engineering 2017:1–12. doi:10.1155/2017/1953087.
- Mejia-Ballesteros, J. E., L. Rodier, R. Filomeno, H. Savastano, J. Fiorelli, and M. Frias Rojas. 2021. Influence of the fiber treatment and matrix modification on the durability of eucalyptus fiber reinforced composites. Cement and Concrete Composites 124 (September):104280. doi:10.1016/j.cemconcomp.2021.104280.
- Mejouyo, P. W. H., E. Mbou, S. Tagne, S. Tido Tiwa, and E. Njeugna. 2022. Experimental study of water-sorption and desorption of several varieties of oil palm Mesocarp fibers. Results in Materials 14 (May):100284. doi:10.1016/j.rinma.2022.100284.
- Mendes, S., L. Nunes Hugen, R. Daniel DOS Santos, R. Dias Toledo Filho, and S. Rocha Ferreira. 2021. Influence of water amount and immersion time on the sisal fibers hornification process. Journal of Natural Fibers 18 (11):1712–21. doi:10.1080/15440478.2019.1697990.
- Mendonçaa, S., Y. Gabriela dos, B. Zukowskib, R. Dias, and T. Filhoc. 2018. Influence of water hornification and alkaline treatment on the stress-strain behaviour of jute fibers. Non-Conventional Materials and Technologies: NOCMAT for the XXI Century 7:383.
- Moniruzzaman, M., M. A. G. Mohd Maniruzzaman, and C. Santulli. 2009. Lady’s finger fibres for possible use as a reinforcement in composite materials. Journal of Biobased Materials and Bioenergy 3 (3):286–90. doi:10.1166/jbmb.2009.1038.
- Moosavi, S. A., M. Aghaalikhani, B. Ghobadian, and E. Fayyazi. 2018. Okra: A potential future bioenergy crop in Iran. Renewable and Sustainable Energy Reviews 93 (April):517–24. doi:10.1016/j.rser.2018.04.057.
- Ojo, E. B., K. O. Bello, O. F. Ngasoh, T. T. Stanislas, K. Mustapha, H. Savastano Jr, and W. Soboyejo. 2020. Mechanical performance of fiber-reinforced alkali activated un-calcined earth-based composites. Construction and Building Materials 247:118588. doi:10.1016/j.conbuildmat.2020.118588.
- Rahman, M. M., M. Maniruzzaman, M. Rashidul Islam, and M. Saifur Rahman. 2018. Synthesis of nano-cellulose from Okra fibre and FTIR as well as Morphological studies on it. American Journal of Polymer Science and Technology 4 (2):42–52. doi:10.11648/j.ajpst.20180402.11.
- Salmén, L., and J. S. Stevanic. 2018. Effect of drying conditions on the cellulose microfibril aggregation and ”hornification. Cellulose 25 (11):6333–44. doi:10.1007/s10570-018-2039-1.
- Santos, J., R. de, and P. Roberto Lopes Lima. 2014. Effect of treatment of sisal fiber on morphology, mechanical properties and fiber-cement bond strength. Key Engineering Materials 634:410–20. doi:10.4028/scientific.net/kem.634.410.
- Sathishkumar, T. P., P. Navaneethakrishnan, S. Shankar, R. Rajasekar, and N. Rajini. 2013. Characterization of natural fiber and composites-A review. Journal of Reinforced Plastics and Composites 32 (19):1457–76.
- Savastano, J., P. G. Holmer, R. S. P. P. Warden, C. H. Savastano, P. G. Warden, and R. S. P. P. Coutts. 2000. Brazilian waste fibres as reinforcement for cement-based composites. Cement and Concrete Composites 22 (5):379–84. doi:10.1016/S0958-9465(00)00034-2.
- Schafleitner, R., C.Y. Lin, Y.P. Lin, W. Tien-Hor, C.H. Hung, C.L. Phooi, S.H. Chu, Y.C. Jhong, and Y.Y. Hsiao. 2021. The world vegetable center Okra (Abelmoschus Esculentus) core collection as a source for flooding stress tolerance traits for breeding. Agriculture 11 (2):165. doi:10.3390/agriculture11020165.
- Shamsul Alam, M., and G. M. Arifuzzaman Khan. 2007. Chemical analysis of Okra bast fiber (Abelmoschus esculentus) and its physico-chemical properties. Journal of Textile and Apparel, Technology and Management 5 (October 2014):1–9.
- Sikame Tagne, N. R., E. Njeugna, M. Fogue, J. -Y. Drean, A. Nzeukou, and D. Fokwa. 2014. Study of water absorption in raffia vinifera fibres from bandjoun, cameroon. Scientific World Journal 2014:1–11. doi:10.1155/2014/912380.
- Sreedhara, S., and N. Tata. 2013. A novel method for measurement of porosity in Nanofiber mat using pycnometer in filtration. Journal of Engineered Fabrics & Fibers 8 (4):132–37. doi:10.1177/155892501300800408.
- Stanislas, T. T., G. Charles Komadja, O. Fayen Ngasoh, I. Ijeoma Obianyo, J. Foba Tendo, P. Azikiwe Onwualu, and H. Savastano Junior. 2021a. Performance and durability of cellulose pulp-reinforced extruded earth-based composites. Arabian Journal for Science and Engineering 46 (11):0123456789. doi:10.1007/s13369-021-05698-1.
- Stanislas, T. T., J. Foba Tendo, E. Beckley Ojo, O. Fayen Ngasoh, P. Azikiwe Onwualu, E. Njeugna, and H. Savastano Junior. 2020. Production and characterization of Pulp and Nanofibrillated cellulose from selected tropical plants. Journal of Natural Fibers 00 (00):1–17. doi:10.1080/15440478.2020.1787915.
- Stanislas, T. T., G. C. Komadja, Y. R. Nafu, A. A. Mahamat, P. W. H. Mejouyo, J. F. Tendo, E. Njeugna, P. A. Onwualu, and H. Savastano Junior. 2022. Potential of Raffia Nanofibrillated cellulose as a reinforcement in extruded earth-based materials. Case Studies in Construction Materials 16:16. doi:10.1016/j.cscm.2022.e00926.
- Stanislas, T. T., J. F. Tendo, R. S. Teixeira, E. B. Ojo, G. C. Komadja, M. Kadivar, and H. J. Savastano. 2021b. Effect of cellulose Pulp fibres on the physical, mechanical, and thermal performance of extruded earth-based materials. Journal of Building Engineering 39 (July):102259. doi:10.1016/j.jobe.2021.102259.
- Tagne, N. R. S., D. Ndapeu, D. Nkemaja, G. Tchemou, D. Fokwa, W. Huisken, E. Njeugna, M. Fogue, J. -Y. Drean, and O. Harzallah. 2018. Study of the viscoelastic behaviour of the Raffia Vinifera fibres. Industrial Crops and Products 124:572–81. doi:10.1016/j.indcrop.2018.07.077.
- Tagne, N. R. S., E. Njeugna, M. Fogue, J. Y. Drean, and D. Fokwa. 2013. Study of water diffusion through Raffia Vinifera fibres of the stem from bandjoun- Cameroon: Case of drying kinetics. Research Journal of Applied Sciences, Engineering and Technology 6 (19):3547–58. doi:10.19026/rjaset.6.3559.
- Tagne, S., N. Rodrigue, N. Ebénézer, N. Dieunedort, F. Didier, M. Fogue, J.Y. Drean, and O. Harzallah. 2017. Investigation of the physical and mechanical properties of Raffia Vinifera fibers along the stem investigation of the physical and mechanical properties of Raffia Vinifera fibers along the stem. Journal of Natural Fibers 14 (5):621–33. doi:10.1080/15440478.2016.1250025.
- Tenazoa, C., H. Savastano, S. Charca, M. Quintana, and E. Flores. 2019. The effect of alkali treatment on chemical and physical properties of Ichu and Cabuya fibers. Journal of Natural Fibers 00 (00):1–14. doi:10.1080/15440478.2019.1675211.
- Tonoli, G. H. D., U. P. Rodrigues Filho, H. Savastano, J. Bras, M. N. Belgacem, and F. A. Rocco Lahr. 2009. Cellulose modified fibres in cement based composites. Composites Part A, Applied Science and Manufacturing 40 (12):2046–53. doi:10.1016/j.compositesa.2009.09.016.
- Wang, Z., Y. Che, J. Li, W. Wu, B. Yan, Y. Zhang, X. Wang, G. Yu, X. Zuo, and X. Li. 2022. Effects of anaerobic digestion pretreatment on the Pyrolysis of Sargassum: Investigation by TG-FTIR and Py-GC/MS. Energy Conversion and Management 267:115934. doi:10.1016/j.enconman.2022.115934.
- Youbi, S. B. T., N. Rodrigue Sikame Tagne, O. Harzallah, P. William Mejouyo Huisken, T. Tiwa Stanislas, E. Njeugna, J.Y. Drean, and S. Bistac-Brogly. 2022. Effect of Alkali and Silane treatments on the surface energy and mechanical performances of Raphia Vinifera fibres. Industrial Crops and Products 190:115854. doi:10.1016/j.indcrop.2022.115854.