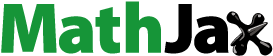
ABSTRACT
Multi jet fusion (MJF), a powder-based additive manufacturing technology, is suitable for fabricating fibre-reinforced polymer composites. However, the types of reinforcement fibres applied in MJF are limited due to the incompatibility between the fibres and polymer. Herein, a simple and cost-effective surface modification method for Fe3O4-coated aramid fibres (Fe3O4@AF hybrids) is proposed to fabricate polyamide 12 (PA12) composites by MJF. The optimal fibre content for Fe3O4@AF/PA12 composites is 6 wt%, which resulted in 10.83% and 16.05% higher ultimate tensile strength and Young’s modulus, respectively, compared with AF/PA12. The addition of Fe3O4@AF hybrids also improved the flame retardancy of AF/PA12 by reducing the peak heat release rate (PHRR) and postponing the temperature at PHRR. This practical surface modification method can be potentially applied to other reinforcement fibres for fabricating functional polymer composites by other powder-based manufacturing technologies.
GRAPHICAL ABSTRACT

1. Introduction
Powder bed fusion (PBF) is an additive manufacturing technology in which powder materials are selectively consolidated layer-by-layer into three-dimensional (3D) objects by an energy source (Chatham, Long, and Williams Citation2019; Singh et al. Citation2020). PBF has attracted great attention because of its ability to fabricate complex 3D objects without support structures (Awad et al. Citation2021). The PBF fabrication process is generally classified into three sub-processes, including powder recoating, energy input, and powder coalescence (Chatham, Long, and Williams Citation2019). After a fresh layer of powder is spread on the print bed by a roller or recoating blade, powder particles in selective regions absorb heat from the energy source (such as an infrared lamp or a laser) and melt, and the molten powder particles coalesce and solidify. This process repeats until the entire 3D object is printed.
Multi Jet Fusion (MJF) and selective laser sintering (SLS) are two PBF techniques used for fabricating polymer parts. In MJF, two printing agents, including the fusing agent and the detailing agent, are selectively dispensed onto the powder layer according to the computer-aided design model, and the entire print bed is irradiated by infrared lamps (Tan, Zhu, and Zhou Citation2020). Powder particles in the regions with the black fusing agent absorb heat provided by the infrared lamps and fuse together. The boundaries of the regions are deposited with the colourless detailing agent, which lowers the local temperature of the surrounding powder to ensure fine details of the printed parts. In contrast, the SLS technique employs a laser beam to selectively sinter polymer particles in a point-wise scanning track (Tan, Zhu, and Zhou Citation2020). The difference in the energy input process endows MJF with ten-times higher production speed than that of SLS (Xu et al. Citation2019; Cai et al. Citation2021).
Fibre-reinforced polymer composites possess advantages such as high specific strength and modulus, light weight, and flexible design, which lead to widespread usage in the aerospace, automotive, military, and biomedical industries (Dickson, Abourayana, and Dowling Citation2020; Zhang et al. Citation2021). To improve the mechanical performance of PBF-printed parts, different types of reinforcement fibres, such as carbon fibres (Yan et al. Citation2011), glass fibres (Liu et al. Citation2021), and aramid fibres (Chen et al. Citation2022), have been mixed with polymer powder to fabricate fibre-reinforced polymer composites. Reinforcement fibres tend to align along the powder recoating direction due to particle shear flow during the recoating process, and this phenomenon is especially prominent for fibres with high aspect ratios (Chen et al. Citation2021; Liu et al. Citation2022). As a result of the fibre alignment in the powder bed, mechanical properties of the printed parts show an anisotropic enhancement (Khudiakova et al. Citation2020). As printing-induced anisotropy is a key issue complicating the simple design of additively manufactured parts, it would be highly desirable if the enhancement in mechanical performance can be achieved in all printing orientations.
Aramid fibres (AF) have low density, superior mechanical properties, good chemical stability, and high temperature resistance (Zhang et al. Citation2021; Zeng et al. Citation2018). However, the surface of AF is relatively smooth and chemically inert, thus limiting the interfacial bonding with polymer matrices and hindering the reinforcement effect (Ehlert and Sodano Citation2009; Nasser et al. Citation2019). To enhance the mechanical interlocking and interfacial bonding between AF and the polymer matrix, various surface modification approaches for AF have been reported, such as etching, ultrasonic treatment (Liu et al. Citation2008), plasma treatment (Li et al. Citation2014), chemical grafting (Sa et al. Citation2014), dip-coating (Chen et al. Citation2014; Nasser et al. Citation2019), and the whiskerization technique (Ehlert and Sodano Citation2009). However, these approaches involve multi-step procedures, long reaction time, strict reaction conditions, and toxic materials (Zeng et al. Citation2018). Therefore, there is a need to introduce a simple, cost-effective, and non-toxic surface modification method for AF.
Polyamide 12 (PA12) has wide sintering window and high dimensional stability, and is commonly used for PBF printing. However, PA12 is flammable and can release dense smoke and toxic gases during combustion, which seriously endanger human safety (Liu et al. Citation2021; Lin et al. Citation2018). At present, there are few studies on improving the flame retardancy of fibre-reinforced PA12 composites printed by PBF. Studies have shown that AF can improve the thermal stability of PA12 samples, but there is no report on the thermal oxidation resistance and flame retardancy of AF/PA12. The fabrication process of iron(II,III) oxide (Fe3O4) nanoparticles is simple, and studies on its use as a surface modifier to improve the flame-retardant properties of materials have been reported (Kalali, Wang, and Wang Citation2016; Ghanbari and Salavati-Niasari Citation2015). With the presence of Fe3O4, the peak heat release rate (PHRR) and total heat release (THR) can be greatly reduced.
In this work, a novel surface modification method is proposed for synthesising Fe3O4-modified AF (Fe3O4@AF hybrids) as a reinforcement to improve the mechanical performance and flame-retardant properties of MJF-printed polyamide 12 (PA12) parts. This work first presented the synthesis method for the Fe3O4@AF hybrids, followed by characterisation of the surface morphology and chemical composition of the fibres and the flowability of the powder feedstock. Next, the thermal stability and thermal oxidation resistance of the MJF-printed specimens using pure PA12, AF/PA12, and Fe3O4@AF/PA12 were investigated. Subsequently, the mechanical performance (including tensile and flexural properties) of specimens with different fibre content and printing orientations were compared, and the reinforcement mechanisms were comprehensively studied. Lastly, the effect of surface modification on the flame retardancy of PA12 composites was studied.
2. Materials and methods
2.1. Materials
Iron chloride tetrahydrate (FeCl2·4H2O) was purchased from Macklin. Iron chloride hexahydrate (FeCl3·6H2O) was purchased from Aladdin. Ammonium hydroxide (NH4OH) solution and oleylamine were purchased from Sigma-Aldrich Pte. Ltd. PA12 powder (median size of 52.6 µm) was provided by HP Inc. (USA). Aramid fibres with an average length of 0.8 mm were purchased from Tech-in Materials Co. Ltd., China.
2.2. Surface modification of AF
The surface of AF was modified by Fe3O4 through the process illustrated in a. The Fe3O4@AF hybrids in the weight ratio of 1:10 (Fe3O4 to AF) were fabricated using the as-received AF. First, 4.4 g AF was sieved and dispersed in 500 mL deionised water by probe sonication for 1 h. The solution was then transferred into a three-neck round-bottom flask and stirred with a mechanical mixer. Next, FeCl3·6H2O (1 g) and FeCl2·4H2O (0.4 g) were dissolved in 50 mL deionised water and transferred into the same flask. Under fast stirring, 2.5 mL NH4OH was added. After 10 min, the mixture was heated to 90 °C and 0.25 mL oleylamine was added. After stirring and heating at 90 °C for 1 h, the mixture was filtered and thoroughly washed with deionised water. Finally, the Fe3O4@AF hybrids were dried in an oven at 80 °C for 5 h.
Figure 1. Surface modification of AF and fabrication of the Fe3O4@AF/PA12 composites: (a) schematic of the proposed reaction process, (b) MJF printing process, (c) fibre alignment during powder recoating and printing orientations of specimens in the powder bed, and (d) schematic showing the fibre alignment in specimens printed in different orientations.
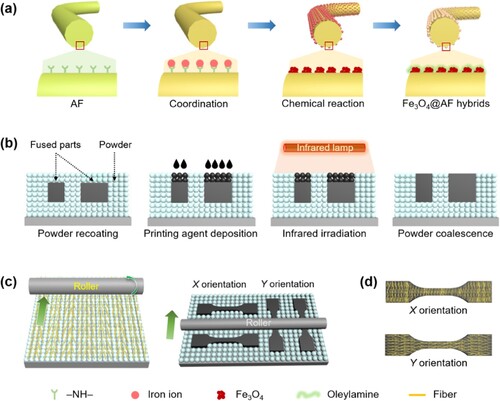
Fe3O4 nanoparticles were also synthesised by the same process without adding AF. Note that the oleylamine-capped Fe3O4 synthesised as free nanoparticles or on the fibre surface is referred to as Fe3O4 for simplicity.
2.3. MJF printing process
The mixed powders were prepared by mechanically mixing the pure PA12 powder with fibres (pristine AF or Fe3O4@AF hybrids) at different fibre weight ratios, including 2, 4, 6, and 8 wt%. The mixed powders containing the pristine AF and the Fe3O4@AF hybrids are denoted as AF-x/PA12 and Fe3O4@AF-x/PA12, respectively, where x represents the fibre content at x wt%.
In this work, specimens were fabricated from three types of powder, including pure PA12, AF-x/PA12, and Fe3O4@AF-x/PA12 powders, using the MJF printing testbed (HP Inc. USA). Specimens for tensile testing and three-point bending testing were printed according to the ASTM D638-14 type V and ASTM C393 standard, respectively.
The printing was performed by repeating the process of powder recoating, printing agent deposition, infrared irradiation, and powder coalescence (b). Each powder layer with a thickness of 80 μm was spread on the print bed at a recoating speed of 200 mm/s. The supply ratio was set at 2.4 to ensure sufficient powder spreading. The black fusing agent was selectively deposited onto the powder layer as designed. The region with the fusing agent was heated to 210–220°C by infrared irradiation, and the powder particles were fused together after heat absorption. In contrast, the boundary region with the detailing agent was at a temperature lower than the melting temperature of PA12 to ensure the dimensional accuracy of the printed specimens. A new layer of powder was then spread again by the roller, and the process was repeated until the designed 3D specimens were printed. The printed specimens were cooled naturally and then cleaned by bead blasting.
Specimens in two orientations were prepared. Specimens positioned perpendicular or parallel to the roller recoating direction were denoted to be in the X or Y printing orientation, respectively (c). It was observed that fibres tended to align in the roller recoating direction, thus resulting in different fibre alignment in the specimens printed in the X and Y printing orientations (d).
2.4. Characterisation
2.4.1. Characterisation of the fibres and powder
The crystal properties of AF, Fe3O4, and Fe3O4@AF hybrids were characterised by X-ray diffraction (XRD, Shimadzu 6000, Japan). The surface groups were detected by Fourier Transform Infrared (FTIR) spectroscopy (IR Prestige 21, Shimadzu, Japan). The morphology of AF and Fe3O4@AF hybrids was observed by JSM-5600 LV scanning electron microscopy (SEM, JEOL, Japan), and elemental compositions of them were detected by energy-dispersive X-ray spectroscopy (EDS).
The flowability of pure PA12, AF/PA12, and Fe3O4@AF/PA12 powders were investigated by measuring the dynamic avalanche angle using Revolution Powder Analyzer (Basel, Switzerland) for 250 times at a drum rotation speed of 0.6 r/min.
2.4.2. Characterisation of the printed specimens
The MJF-printed specimens were characterised by thermogravimetric analysis (TGA, Q500, TA Instruments, New Castle, DE), differential scanning calorimetry (DSC, TA Instruments, UK), optical microscopy, tensile testing, three-point bending testing, SEM, dynamic rheological testing, and microscale combustion calorimetry (MCC).
TGA was conducted using samples of around 10 mg (obtained by cutting from the MJF-printed specimens), which were heated from 50°C to 800°C at 20°C/min under nitrogen and air conditions. DSC was conducted on DSC-Q200 by heating from 20°C to 250°C and then cooling from 250°C to 20°C at 10°C/min, at a nitrogen flow rate of 40 mL/min.
To investigate the orientations of the fibres, the samples were polished using Tegramin-25 (Struers, Denmark). The optical microscopy images of the polished surfaces were captured by SZX16 (Olympus Corp., Japan) and processed by the software ImageJ.
The tensile and three-point bending testing was performed on the Shimadzu AGX 10 kN universal tester at a crosshead speed of 10 mm/min. Five specimens were measured for each parameter set. SEM was performed using JSM-5600 LV (JEOL, Japan) to investigate the fracture surfaces of the tensile specimens.
The dynamic rheological testing was conducted at 220°C using a rotational rheometer (Discovery HR-30, TA Instruments, New Castle, USA) equipped with a pair of parallel plates with diameter of 25 mm and a separation distance of 0.8 mm.
The MCC was conducted on GOVMARK MCC-2 following the ASTM D 7309–07 standard to test samples of 20 mg.
3. Results and discussion
3.1. Characterisation of Fe3O4@AF hybrids
The crystal structure of the Fe3O4@AF hybrids was characterised by XRD. As shown in a, all of the diffraction peaks matched well with the normal characteristic diffractions of the Fe3O4 inverse spinel structure (PCPDFWIN v.2.02, PDF No. 89-0691) (Zhuang et al. Citation2015). No obvious XRD peaks arising from impurities were found, indicating that the surface modification process did not affect the formation of Fe3O4 crystals. In the XRD pattern of AF, the appearance of two characteristic aramid peaks can be verified, whose reflections corresponded to crystallographic planes (110) and (200), indicating that the crystal structure comprised of orthorhombic or pseudo-orthorhombic unit cells (Nascimento et al. Citation2020). The new peaks that appeared in the XRD pattern of the modified AF were well matched with Fe3O4 features, indicating the successful synthesis of Fe3O4@AF hybrids.
Figure 2. Characterisation of AF, Fe3O4, and Fe3O4@AF hybrids: (a) XRD curves, (b) FTIR spectra, and (c) TGA results.
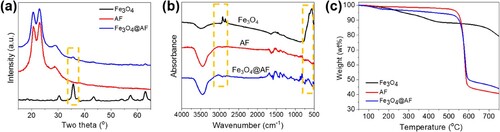
The FTIR spectra of AF, Fe3O4, and Fe3O4@AF hybrids were similar except for some characteristic peaks, which stems from the structural similarity between the AF and the oleylamine capping the Fe3O4 (b). Characteristic FTIR peaks related to N–H were observed in all three substances. The N–H stretching vibration is located at 3380 cm−1, and the observed band around 1605 cm−1 is attributed to the combination of –NH shear vibration and N–H bending vibration. The characteristic peak observed at 581 cm−1 relates to Fe–O stretching vibration, which appears in the FTIR spectra of Fe3O4 and Fe3O4@AF hybrids, confirming the successful formation of Fe3O4 (Can et al. Citation2010). Meanwhile, the C–H stretching modes (2856 and 2927 cm−1) in the FTIR spectrum of Fe3O4 further confirmed the presence of oleylamine ligands on the surface of the as-synthesised Fe3O4 (He et al. Citation2010). The structural similarity potentially endows good compatibility between Fe3O4 and AF, which will promote the formation of well assembled hybrids.
TGA tests under nitrogen conditions were performed to evaluate the thermal stability of Fe3O4@AF hybrids and calculate the weight percentage of Fe3O4 in the hybrids. As shown in c, the initial weight loss (5 wt%) of Fe3O4 caused by the pyrolysis of oleylamine confirms the presence of organic compounds in Fe3O4. The thermal stability of AF is sufficient to meet the application requirements of PA12. Fe3O4@AF hybrids showed a similar pyrolysis process to AF, but with a higher residue weight. The final residue weights of AF, Fe3O4, and Fe3O4@AF hybrids were 40.76, 79.39, and 44.02 wt%, respectively. Based on the equation.
(1)
(1) where w is the weight percentage of Fe3O4 in the Fe3O4@AF hybrids and
,
, and
are the final residue weight of Fe3O4, AF, and Fe3O4@AF hybrids, respectively. The content of Fe3O4 in the hybrids is calculated to be 8.44%, which matched well with the designed composition.
The AF and Fe3O4@AF hybrids were observed by SEM to study the effect of surface modification on the fibre morphology. As shown in , no impurities were found on the smooth surface of pristine AF, however, rough surfaces with some particles deposited were observed after the surface modification. EDS was used to characterise the elemental composition, as shown in Figure S1a. The newly appeared peak in the EDS curve of Fe3O4@AF located at 8.1 eV was ascribed to the Fe element. Combined with the above analyses, it can be concluded that the deposited particles were Fe3O4, indicating the successful synthesis of the Fe3O4@AF hybrids. The height distribution of the fibre surface was obtained by analysing the SEM images of AF and Fe3O4@AF hybrids using the ImageJ software (Figures S1b and c), and the images were inset into b and d, respectively. The height difference in Fe3O4@AF hybrids was much larger than that in AF, indicating greater roughness of the surface of the hybrids. The elemental distribution was also examined by SEM in the mapping mode to evaluate the dispersion of Fe3O4 on the surface of AF. As shown in Figure S1d, the distribution of C, O, and Fe fitted perfectly with the distribution of Fe3O4 in the scanned region, indicating an even distribution of particles on the surface of AF.
3.2. Powder flowability
Powder flowability is an important factor affecting the powder recoating process in MJF. Poor powder flowability adversely affects the powder bed density and uniformity, resulting in void formation and uneven heat absorption that deteriorate the mechanical performance of MJF-printed parts. The powder flowability can be quantitively studied by measuring the avalanche angle, which is obtained from a linear regression of the free powder surface prior to the start of the powder avalanche occurrence, as illustrated in a (Amado et al. Citation2011). Typically, a higher median avalanche angle and broader angle distribution correlate to poorer powder flowability. However, this trend may be affected by particles with complex geometrical shapes or compounds with different aspect ratios, such as fibres, due to the heterogeneity of the materials (Amado et al. Citation2011).
Figure 4. Dynamic avalanche angle measurement and results: (a) schematic of the cross-sectional view of the rotating drum; (b–f) histograms of avalanche angle distribution fitted by Gaussian functions (red curves) and images of the powder during the measurement for (b) PA12, (c) AF-2/PA12, (d) Fe3O4@AF-2/PA12, (e) AF-6/PA12, and (f) Fe3O4@AF-6/PA12.
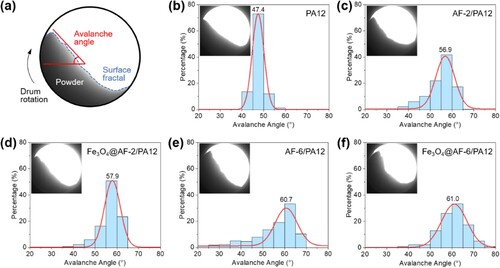
As shown in b–f and S2, the median avalanche angle and the angle distribution generally increased with the fibre content, signifying hindered movement of the PA12 powder by the fibres. For powder with fibre content less than 8 wt%, the median avalanche angles were comparable to previous works (Chen et al. Citation2022; Chen, Zhao, and Zhou Citation2022). At the same fibre content, the median avalanche angles of AF/PA12 and Fe3O4@AF/PA12 powders were very similar, indicating that powder mixed with the surface modified fibres had comparable flowability to that with pristine AF.
Although the median avalanche angle of Fe3O4@AF-8/PA12 was smaller than expected, the broad angle distribution signifies poor powder flowability. This result can be attributed to the high content of Fe3O4@AF hybrids with large aspect ratio and high surface roughness, which aggravated the heterogeneity of the mixed powder.
3.3. Fibre orientation
Orientated fibres affect the mechanical properties of PA12 composites by coherently resisting external forces. The effect of the surface modification on fibre orientation in the PA12 matrix is quantified by the fibre orientation angle (a). The quantitative characteristics of the fibre orientation for PA12 composites with different fibre contents are given in b-d, Figure S3, and . Fibre orientation ranges from 0° to 180°. The peak values of Gaussian fitting curves for all specimens indicate that the preferred orientation of AF and Fe3O4@AF hybrids was around 90°, parallel to the moving direction of the roller. Because of the high fibre content (8 wt%), the flowability of the mixed powders was reduced, which led to a decrease in the orientation of the fibres. Specifically, the percentage of fibre orientation in the range of 70–110° exceeded 40% in all samples, indicating that the alignment of AF was minimally influenced by its surface modification.
Figure 5. Fibre orientation: (a) schematic illustration of the fibre orientation angle, i.e. the angle between a horizontal line and the fibre in tensile specimens printed in the Y orientation; (b–d) distribution of the fibre orientation for (b) Fe3O4@AF-2/PA12, (c) Fe3O4@AF-4/PA12, and (d) Fe3O4@AF-6/PA12.
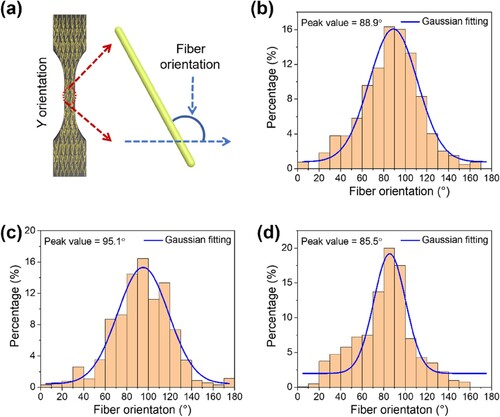
Table 1. The quantised characteristics of the fibre orientation for PA12 composites with different fibre contents. Peak value and percentage denote the peak value of fitted Gauss curve and fibre orientation within 70-110°, respectively.
3.4. Thermal stability and thermal oxidation resistance
Thermal stability and thermal oxidation resistance of the PA12 and its composites were tested by TGA tests. As shown in a, the pure PA12 specimen exhibited excellent thermal stability, and the initial degradation temperature Ti (at 5 wt% weight loss) was higher than 400°C. AF had minimal effect on the Ti values of AF/PA12 composites but added a high-temperature degradation process to the TGA curves of the composites. Based on the analysis of the pyrolysis process of AF, the newly appeared process is ascribed to the further degradation of AF. The TG curves of the Fe3O4@AF/PA12 composites exhibited similar tendency (b). Compared to the pure PA12 and AF/PA12 specimen, the Ti and the temperature at half weight loss Thalf of the Fe3O4@AF/PA12 composites increased significantly after adding the hybrids, confirming improved thermal stability.
Figure 6. TG curves of specimens: AF/PA12 composites and (b, d) Fe3O4@AF/PA12 composites under nitrogen and air conditions, respectively.
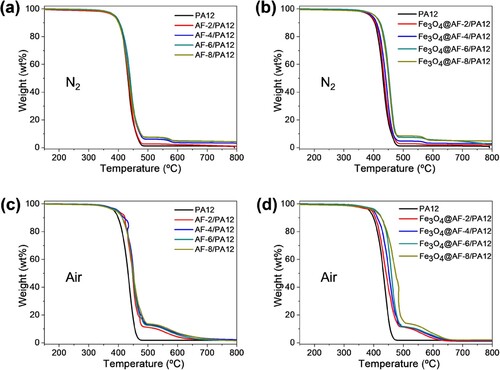
The thermal stability of the samples is also assessed by the temperature at the maximum degradation rate Tmax in the derivative thermogravimetry (DTG) curves. Figures S4a and b show the difference between the AF and Fe3O4@AF in increasing the degradation temperature of the composites. AF negligibly affected the Tmax of the PA12 matrix, whereas Fe3O4@AF raised the Tmax from 433.32°C for PA12 to 456.34°C for Fe3O4@AF-8/PA12. The increase in these characteristic temperatures indicates that Fe3O4@AF hybrids had a better advantage than AF in improving the thermal stability of PA12.
The thermal oxidation resistance of polymers is commonly evaluated by thermal degradation under air. As shown in c and d, the addition of AF and Fe3O4@AF increased the Ti and Thalf of the PA12 composites, signifying improved thermal oxidation resistance. Comparing to AF/PA12 composites, Fe3O4@AF/PA12 composites had higher Ti and Thalf. According to the DTG curves of PA12 composites shown in Figures S4c and d, the Fe3O4@AF hybrids had better performance in raising the Tmax than AF. Detailed information can be found in .
Table 2. Ti, Thalf, and Tmax data of PA12 composites collected from TGA tests under nitrogen and air conditions.
It can be concluded that the addition of Fe3O4@AF hybrids and AF improved the thermal stability and thermal oxidation resistance of PA12 composites, and Fe3O4@AF possessed superior thermostability to AF.
3.5. Mechanical performance
and show the tensile properties of the specimens printed in the X and Y orientations. The tensile properties between the pure PA12 specimens in the X and Y orientations were very similar. However, with the addition of AF and Fe3O4@AF hybrids, the specimens in the Y orientation exhibited higher ultimate tensile strength (UTS) and Young's modulus than those in the X orientation (a–d). The anisotropic mechanical performance observed in the specimens could be ascribed to the different fibre alignment in the PA12 matrices. It has been reported that fibres tend to align parallel to the direction in which the roller is moving. During the layer-by-layer assembly process in MJF, the quantity of fibres oriented along the Y printing orientation increased in the composite, which could withstand external loads and thus giving the composite better mechanical properties in the loading direction.
Figure 7. Tensile properties of the specimens printed in X and Y orientations: stress–strain curves of (a, b) AF/PA12 composites and (c, d) Fe3O4@AF/PA12 composites; data of (e) UTS and (f) Young's modulus. A-x and F-x denotes x wt% of AF and Fe3O4@AF hybrids in the PA12 composites, respectively.
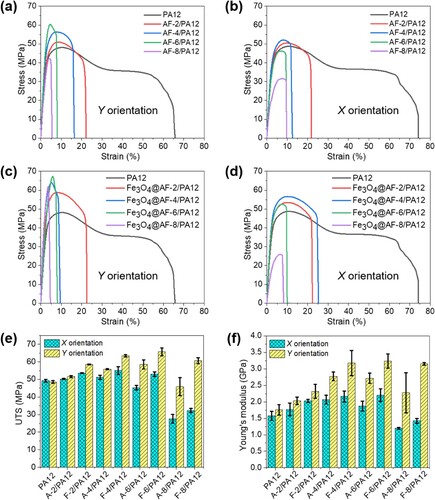
Table 3. Comparison of the tensile and flexural properties of the specimens printed in X and Y orientations.
The UTS of both the AF/PA12 and Fe3O4@AF/PA12 composites first increased with fibre content and then decreased as the fibre content reached 8 wt% (Y orientation) and 6 wt% (X orientation), as shown in e. For specimens in the Y orientation, the changes in the UTS were mainly attributed to the poor powder flowability of the mixed powder at high fibre content, which introduced defects (voids, over-fused zones, and unmelted zones) and impaired the continuity of the printed specimens. These defects weakened the ability of the matrix to act as a medium to withstand and transmit loads, thereby reducing the UTS of the composites. In contrast, for specimens printed in the X orientation, the fibres aligned perpendicular to the direction of the external force and actively bore the load with an impairment to the continuity of the PA12 matrix as a force medium. When the fibre content increased to a certain extent, the negative effect dominated and weakened the mechanical properties of the composites. Fe3O4@AF hybrids performed better in improving the UTS of the PA12 composites than AF in both printing orientations. In the Y orientation, the UTS of pure PA12 increased from 48.59 MPa to 58.58 MPa for AF-6/PA12 and 65.70 MPa for Fe3O4@AF-6/PA12. In the X orientation, the UTS of pure PA12 increased from 49.30 MPa to 51.20 MPa for AF-4/PA12 and 55.06 MPa for Fe3O4@AF-4/PA12. Compared to pristine AF, Fe3O4@AF hybrids had higher surface roughness and larger surface area, which improved their interfacial interaction with the PA12 matrix, and thus exhibiting better reinforcement effect.
Porosity inside printed parts can impair mechanical properties by creating points of stress concentration(Chen, Zhao, and Zhou Citation2022). The porosity of a material can be calculated from its density (tested by a densimeter, XS204, Mettler Toledo, USA). Four printed parts were tested for each sample, and detailed information can be found in Table S1 and Figure S7. The density of PA12 composites slightly increased due to the higher density of fillers at low concentration (4 wt% fot AF and 6 wt% for Fe3O4@AF). But when the content of fillers reached to 8 wt%, the density decreased sharply, and the porosity of PA12 composites reached the highest values (3.15% for AF-8/PA12 and 4.12% for Fe3O4@AF-8/PA12). This phenomenon can be caused by the inferior flowability of powders at 8 wt% content of fillers, resulting much more voids inner polymer matrices. However, these adverse effects on mechanical properties due to the increase of porosity are far less than the reinforcement effect of fibres, so the mechanical properties of the material are still improved.
The Young’s modulus of the PA12 composites had a similar tendency to the UTS, as shown in f. Clearly, Fe3O4@AF hybrids had better performance in improving the Young’s modulus of the PA12 composites than AF. At low fibre content (< 6 wt%), there were only slight increases in the Young’s modulus for specimens printed in the X orientation. However, for specimens printed in the Y orientation, compared with pure PA12 (1.755 GPa), the maximum increase in the Young's modulus of AF/PA12 exceeded 58% (2.775 GPa with 4 wt% AF), while the maximum increase in that of Fe3O4@AF/PA12 exceeded 84% (3.237 GPa with 6 wt% Fe3O4@AF). Therefore, the surface modification method proposed in this work showed a great enhancement effect on the mechanical properties of the PA12 composites.
The flexural properties of the printed specimens are presented in . The higher the flexural strength, the more impact force a material can withstand. The flexural strength of the specimens increased with the addition of fibres and reached the maximum at 4 wt% fibre content regardless of the printing orientation. Similarly to the tensile properties, the flexural strength of the specimens printed in the Y orientation was higher than that in the X orientation. For specimens printed in the Y orientation, the flexural strength increased from 68.71 MPa for pure PA12 to 84.32 MPa for AF-4/PA12 and 90.24 MPa for Fe3O4@AF-4/PA12. The poor flowability of the powder with a high fibre content led to the inferior flexural properties for PA12 composites with 8 wt% fibres.
Figure 8. Flexural properties of the specimens printed in X and Y orientations: flexural strength–stroke curves of AF/PA12 and Fe3O4@AF/PA12 composites printed in the (a) X and (b) Y orientation; data of (c) flexural strength and (d) flexural modulus. A-x and F-x denotes x wt% of AF and Fe3O4@AF hybrids in the PA12 composites, respectively.
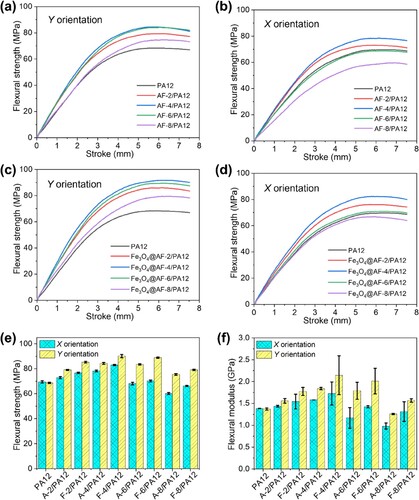
The flexural modulus represents the ease of bending deformation. The larger the flexural modulus, the better the flexural resistance. The addition of fibres (< 8 wt%) clearly increased the flexural modulus of PA12. Compared with pure PA12, the maximum increase of the flexural modulus of AF-4/PA12 was 34.14%, while that of Fe3O4@AF-4/PA12 exceeded 56.53%, signifying the superior reinforcement performance of Fe3O4@AF hybrids to AF. Therefore, the surface modification process promoted the reinforcement effect of AF on improving the tensile and flexural properties of PA12.
3.6. Reinforcement mechanism analyses
The microstructure of polymer composites determines their properties. The reinforcement mechanism was investigated by observing the fracture surface of the composite specimens as well as studying the crystallization behaviour and viscosity changes.
3.6.1. Fracture analysis
The obvious orientation behaviours of fibres can be seen in , S5, and S6. With the increase in the fibre content, the number of fibres in the field of view also increased gradually. Although the fibres used were longer than reported ones (Chen, Zhao, and Zhou Citation2022), no agglomeration or intertwining of AF or Fe3O4@AF hybrids were observed, confirming the good dispersion of fibres. Taking PA12 composites with 6 wt% fibre content as examples, there was no significant difference between AF-6/PA12 and Fe3O4@AF-6/PA12 specimens in the Y orientation observed under low magnification. However, in the enlarged areas, the voids between the pristine AF and the PA12 matrix were obvious, whereas no voids were observed in the SEM fractography of the Fe3O4@AF-6/PA12 composites, indicating the surface modification process improved the compatibility between Fe3O4@AF hybrids and the PA12 matrix. For specimens printed in the X orientation, most of the AF were pulled out from the PA12 matrix under external forces, while Fe3O4@AF hybrids remained embedded in the polymer matrix. This phenomenon also indirectly reflected the poor compatibility between the pristine AF and the PA12 polymer matrix. Under high magnification, the appearance of filaments and cracks indicated that part of Fe3O4@AF hybrids was broken when resisting external forces. The resistance of Fe3O4@AF hybrids to external forces is favourable to the reinforcement of PA12 and enhancement of the mechanical properties.
Figure 9. Fracture morphology of AF-6/PA12 composites printed in the (a, b) Y and (c, d) X orientation and Fe3O4@AF-6/PA12 composites printed in the (e, f) Y and (g, h) X orientation.
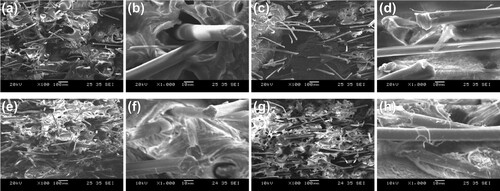
When the fibre content reached 8 wt%, many irregular particles and voids appeared in the fracture surfaces of AF/PA12 and Fe3O4@AF/PA12 composites, which were due to unmelted PA12 powder particles and poor powder flowability, respectively. These defects can cause stress concentration or break the continuity of external force transmission. Therefore, external forces failed to be efficiently transmitted to the stiff fibres, thus resulting in unsatisfactory mechanical properties.
3.6.2. Non-isothermal crystallization behaviour
The crystallization behaviour of a semi-crystalline polymer directly affects its mechanical performance. Since molecular chains in the crystalline regions are more regularly arranged than those in amorphous regions, greater forces are required to pull them. The degree of crystallinity Xc can be calculated by.
(2)
(2) where
is the melting enthalpy of the sample,
is the melting enthalpy of fully crystalline PA12 (209.3 J/g), and w represents the filler content.
DSC results of PA12 composites are portrayed in and S8. Although the addition of fibres negligibly affected the melting temperature Tm of the PA12 composites (a and S8a), the values of changed significantly compared with that of pure PA12, denoting the changes in Xc (f and S8f). The presence of fibres raised the Xc of PA12 composites, and Fe3O4@AF performed superior improvement to AF. The maximum Xc of both composites appeared at 6 wt%. Compared with pure PA12 (20.56%), the Xc raised to 24.23% for AF-6/PA12 and 25.67% for Fe3O4@AF-6/PA12. The increased Xc directly justifies the outstanding mechanical performance at 6 wt% fibre content.
Figure 10. DSC results of Fe3O4@AF/PA12 composites: (a) melting and (b) cooling curves; relative crystallinity as a function of (c) temperature and (d) time; (e) Avrami plots of the specimens; (f) Xc, t0.5, and Zc collected from the DSC curves.

b and Figure S8b show the non-isothermal crystallization processes of the Fe3O4@AF/PA12 and AF/PA12 composites, respectively. The addition of fibres affected the crystallization rate of PA12 composites, which could be further evaluated by relative crystallinity X(T) against temperature curves. The X(T) can be obtained by the ratio of the crystallization peak area at temperature T to the total crystallization peak area at the completion of crystallization (T = ∞). X(T) is expressed as.
(3)
(3) where Hc denotes the crystallization enthalpy. The X(T)–T curves of PA12 composites are shown in c and S8c. Since the crystallization time t can be expressed as
(4)
(4) where T(t) is the temperature at time t and Φ is the cooling rate, therefore, the X(T)–T curves can be transformed into X(t)–t curves (d and S8d). The half-crystallization time t0.5 denotes the time when X(t) halves, which is used to evaluate the crystallization rate. Interestingly, the addition of AF slightly raised the t0.5 relative to pure PA12, while the addition of Fe3O4@AF hybrids reduced it significantly.
The crystallization kinetics of polymers are assessed by the overall kinetic rate constant Zc from the modified equations (Jeziorny Citation1978):
(5)
(5)
(6)
(6) The Avrami plots of the printed specimens are shown in e and S8e. The values of Zc are calculated from the intercept of the fitted lines and plotted in f and S8f. The addition of fibres affected the t0.5 values, but the overall kinetic rate remained almost unchanged, indicating that the AF and Fe3O4@AF hybrids negligibly affected the overall crystallization rate of the PA12 composites. Although the t0.5 of the PA12 composites decreased, their Xc increased. Therefore, it took a long time to fully complete the crystallization process, and thus the changes in Zc were not obvious.
Based on the above analyses, it can be speculated that pristine AF with smooth surfaces had less heterogeneous nucleation, but their large specific surface area still provided sites for anchoring molecular chains, thus increasing the Xc of the specimens. The rough surfaces of Fe3O4@AF hybrids not only provided larger surface area relative to pristine AF, but the heterogeneous nucleation also became more significant. Therefore, the addition of these fibres could increase the crystallinity of PA12 composites, and Fe3O4@AF hybrids were superior to AF. The increased Xc endowed the PA12 composites with enhanced deformation resistance, resulting in improved mechanical performance.
3.6.3. Rheological behaviours
The shear viscosity of the composites decreased with the increase in the shear rate, and all specimens showed the phenomenon of shear thinning, indicating that the PA12 melt and PA12 composite melts belonged to pseudoplastic fluids (a and b). The melt fluidity deteriorated and the complex viscosity of the PA12 composites increased with increasing fibre content. This is because the motion of the polymer macromolecular chains was sterically hindered by Fe3O4@AF hybrids. When the shear rate gradually increased, the complex viscosity of the composites approached that of the pure PA12. This is because the shear flow field destroyed the network structure formed between the fibres and the polymer molecular chains, reducing the molecular orientation resistance. Fe3O4@AF/PA12 composites had higher complex viscosity than AF/PA12, indicating stronger interaction between Fe3O4@AF and PA12 molecular chains and the superior performance of Fe3O4@AF hybrids in hindering molecular movement at high temperatures.
Figure 11. Rheological behaviour of the printed specimens: complex viscosity of (a) AF/PA12 and (b) Fe3O4@AF/PA12 composites; storage modulus of (c) AF/PA12 and (d) Fe3O4@AF/PA12 composites.
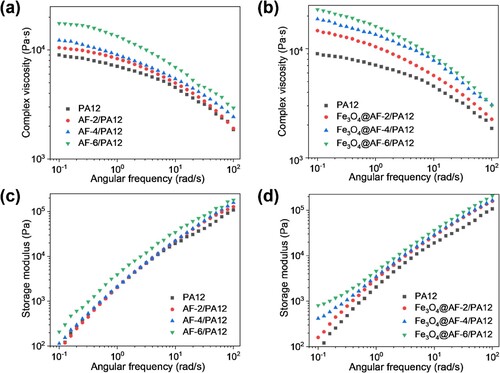
The dependence of the storage modulus on angular frequency also provides important information regarding the formation of the percolated structure. c and d illustrate the storage modulus against angular frequency for the composites with different fibre content. The storage modulus of the AF/PA12 composites remained almost unchanged in the whole frequency range, and only slightly increased when the AF content reached 6 wt%. In contrast, the storage modulus increased in the low-frequency region as the quantity of Fe3O4@AF hybrids increased, suggesting the development of a 3D network structure formed by the interconnected fibres. In the entire frequency range studied, the storage modulus values of Fe3O4@AF/PA12 composites were significantly higher than those of AF/PA12, signifying the formation of a higher degree of fibre network (Pötschke et al. Citation2004). Therefore, the surface modification helped to enhance the interaction between Fe3O4@AF hybrids, thereby promoting the network formation.
Based on the analyses of the fracture surfaces, non-isothermal crystallization, and rheological behaviours, the reinforcement mechanisms of AF and Fe3O4@AF hybrids were comprehensively investigated. The surface modification to pristine AF not only endows Fe3O4@AF hybrids with larger surface area and greater surface roughness, but also improves the compatibility between the PA12 matrix and Fe3O4@AF hybrids, thus reducing or even eliminating voids between the polymer matrix and fibres, thereby effectively transmitting external loads to the fibres. The Fe3O4@AF hybrids have a superior advantage on improving the crystallinity of PA12 than pristine AF, due to heterogeneous nucleation. The increased crystallinity theoretically makes the PA12 composites stiffer and stronger, as compared with pure PA12. Meanwhile, the surface-modified fibres have a greater tendency to form a network structure in the polymer matrix, which is also beneficial to enhancing the mechanical properties of PA12 composites printed by MJF. Therefore, surface modification by Fe3O4 is critical to further improve the reinforcement effect of AF.
3.7. Flame retardancy
PHRR and THR are important parameters used to evaluate the fire safety performance of polymer composites. A high PHRR value means that more heat is released per unit time, which will aggravate the development of fires. As shown in a and , compared with pure PA12 (846.5 kW/m2), the PHRR values decreased after adding the fibres. At the same fibre content (6 wt%), Fe3O4@AF hybrid reduced the PHRR of composites (727.2 kW/m2) more significantly than AF (811.4 kW/m2), signifying that the material has better flame-retardant properties. The addition of AF and its hybrids can significantly increase the temperature corresponding to PHRR, which indicates that the flame retardancy of the material is improved. THR determines the total heat released by a material during combustion, which is usually directly related to the char-formation properties of the material. From the TGA analysis, the addition of AF and its hybrids has a promotion effect on the final char yield of PA12, but the effect of Fe3O4@AF hybrid is more pronounced. Reflected in the value of THR is a more significant reduction (b).
Table 4. MCC data of the printed specimens.
Overall, the addition of AF and its hybrids enhanced the flame-retardant properties of PA12 composites. Since research on the flame retardancy of PBF-printed fibre-reinforced PA12 composites is still in its infancy, more endeavours should be made in this regard to make printed parts more suitable for scenarios requiring high mechanical strength and high temperatures.
4. Conclusions
In this work, Fe3O4@AF hybrids were successfully synthesised using the proposed surface modification method to AF. The modified fibres were used as reinforcements for fabricating PA12 composites by MJF printing. The printed composites showed enhanced mechanical performance in both printing orientations, and the reinforcement mechanisms were comprehensively discussed. The heat release behaviours of PA12 composites were also revealed by the MCC test.
The proposed surface modification method can effectively increase the surface roughness of fibres, improve the compatibility between the PA12 polymer matrix and Fe3O4@AF hybrids, and promote crystallization and fibre network formation. Consequently, stiffer and stronger PA12 composites with less defects can be fabricated. The experimental results proved the superior reinforcement capability of Fe3O4@AF hybrids than pristine AF. The highest average UTS values of AF-6/PA12 and Fe3O4@AF-6/PA12 reached 58.58 and 65.70 MPa, which were 20.56% and 35.21% higher than that of the pure PA12. Meanwhile, the highest average flexural strength values of AF-4/PA12 and Fe3O4@AF-4/PA12 reached 84.32 and 90.24 MPa, which were 22.72% and 31.33% higher than that of the pure PA12. Considering the results of the mechanical tests and the analyses of the reinforcement mechanisms, the optimal fibre content for Fe3O4@AF/PA12 is determined to be 6 wt%.
The addition of 6 wt% Fe3O4@AF hybrids into PA12 also achieved the best flame retardancy, whereby the value of PHRR and THR decreased by 14.1% and 12.4%, respectively. Compared with neat AF, the presence of Fe3O4 promoted the final char yield of PA12 composites, and thus reduced the heat release.
The proposed fibre surface modification method is simple, cost-effective, and non-toxic, providing a practical perspective to improving the mechanical performance and flame retardancy of fibre-reinforced PA12 composites printed by MJF. The surface modification of AF with Fe3O4 not only does not impair the application of AF/PA12, but also improves the service life of Fe3O4@AF/PA12 composites in the same application scenario due to improved mechanical properties, thermostability, and flame retardancy. This surface modification method can be potentially applied to other reinforcement fibres for fabricating functional polymer composites by different PBF techniques and other manufacturing technology.
Acknowledgement
This study was supported by the RIE2020 Industry Alignment Fund – Industry Collaboration Projects (IAF-ICP) Funding Initiative, Singapore and the cash and in-kind contributions from the industry partner, HP Inc.
Disclosure statement
No potential conflict of interest was reported by the author(s).
Additional information
Funding
Notes on contributors
Yanbei Hou
Yanbei Hou is a Research Fellow in HP-NTU Digital Manufacturing Corporate Lab, School of Mechanical and Aerospace Engineering, Nanyang Technological University, Singapore.
Ming Gao
Ming Gao is a PhD student in HP-NTU Digital Manufacturing Corporate Lab, School of Mechanical and Aerospace Engineering, Nanyang Technological University, Singapore.
Jiayao Chen
Jiayao Chen is a Research Fellow in HP-NTU Digital Manufacturing Corporate Lab, School of Mechanical and Aerospace Engineering, Nanyang Technological University, Singapore.
Wei Shian Tey
Wei Shian Tey is a PhD candidate in HP-NTU Digital Manufacturing Corporate Lab, School of Mechanical and Aerospace Engineering, Nanyang Technological University, Singapore.
Mei Chen
Mei Chen is a Research Fellow in HP-NTU Digital Manufacturing Corporate Lab, School of Mechanical and Aerospace Engineering, Nanyang Technological University, Singapore.
Han Zheng
Han Zheng is a PhD candidate in Singapore Centre for 3D Printing, School of Mechanical and Aerospace Engineering, Nanyang Technological University, Singapore.
Boyuan Li
Boyuan Li is a PhD candidate in Singapore Centre for 3D Printing, School of Mechanical and Aerospace Engineering, Nanyang Technological University, Singapore.
Lihua Zhao
Lihua Zhao is the Global Head of 3D Lab at HP Labs, HP Inc., USA, and a principal investigator in HP-NTU Digital Manufacturing Corporate Lab, School of Mechanical and Aerospace Engineering, Nanyang Technological University, Singapore.
Kun Zhou
Kun Zhou is a Professor in HP-NTU Digital Manufacturing Corporate Lab, School of Mechanical and Aerospace Engineering, Nanyang Technological University, Singapore.
References
- Amado, A., Manfred Schmid, Gideon Levy, and Konrad Wegener. 2011. “Advances in SLS Powder Characterization.” Paper Presented at the 2011 International Solid Freeform Fabrication Symposium.
- Awad, Atheer, Fabrizio Fina, Alvaro Goyanes, Simon Gaisford, and Abdul W. Basit. 2021. “Advances in Powder Bed Fusion 3D Printing in Drug Delivery and Healthcare.” Advanced Drug Delivery Reviews 174: 406–424. doi:10.1016/j.addr.2021.04.025.
- Cai, Chao, Wei Shian Tey, Jiayao Chen, Wei Zhu, Xingjian Liu, Tong Liu, Lihua Zhao, and Kun Zhou. 2021. “Comparative Study on 3D Printing of Polyamide 12 by Selective Laser Sintering and Multi jet Fusion.” Journal of Materials Processing Technology 288: 116882. doi:10.1016/j.jmatprotec.2020.116882.
- Can, Musa Mutlu, Sadan Ozcan, Abdullah Ceylan, and Tezer Firat. 2010. “Effect of Milling Time on the Synthesis of Magnetite Nanoparticles by Wet Milling.” Materials Science and Engineering: B 172 (1): 72–75. doi:10.1016/j.mseb.2010.04.019.
- Chatham, Camden A, Timothy E Long, and Christopher B Williams. 2019. “A Review of the Process Physics and Material Screening Methods for Polymer Powder bed Fusion Additive Manufacturing.” Progress in Polymer Science 93: 68–95. doi:10.1016/j.progpolymsci.2019.03.003.
- Chen, Jiayao, Pengfei Tan, Xiaojiang Liu, Wei Shian Tey, Adrian Ong, Lihua Zhao, and Kun Zhou. 2022a. “High-strength Light-Weight Aramid Fibre/Polyamide 12 Composites Printed by Multi Jet Fusion.” Virtual and Physical Prototyping 17 (2): 295–307. doi:10.1080/17452759.2022.2036931.
- Chen, Jiayao, Lihua Zhao, and Kun Zhou. 2022b. “Improvement in the Mechanical Performance of Multi Jet Fusion–Printed Aramid Fiber/Polyamide 12 Composites by Fiber Surface Modification.” Additive Manufacturing 51: 102576. doi:10.1016/j.addma.2021.102576.
- Chen, Jianrui, Yaofeng Zhu, Qingqing Ni, Yaqin Fu, and Xiang Fu. 2014. “Surface Modification and Characterization of Aramid Fibers with Hybrid Coating.” Applied Surface Science 321: 103–108. doi:10.1016/j.apsusc.2014.09.196.
- Chen, Hui, Wei Zhu, Haibin Tang, and Wentao Yan. 2021. “Oriented Structure of Short Fiber Reinforced Polymer Composites Processed by Selective Laser Sintering: The Role of Powder-Spreading Process.” International Journal of Machine Tools and Manufacture 163: 103703. doi:10.1016/j.ijmachtools.2021.103703.
- Dickson, Andrew N., Hisham M. Abourayana, and Denis P. Dowling. 2020. “3D Printing of Fibre-Reinforced Thermoplastic Composites Using Fused Filament Fabrication—A Review.” Polymers 12 (10): 2188. doi:10.3390/polym12102188.
- Ehlert, Gregory J., and Henry A. Sodano. 2009. “Zinc Oxide Nanowire Interphase for Enhanced Interfacial Strength in Lightweight Polymer Fiber Composites.” ACS Applied Materials & Interfaces 1 (8): 1827–1833. doi:10.1021/am900376t.
- Ghanbari, Davood, and Masoud Salavati-Niasari. 2015. “Synthesis of Urchin-Like CdS-Fe3O4 Nanocomposite and its Application in Flame Retardancy of Magnetic Cellulose Acetate.” Journal of Industrial and Engineering Chemistry 24: 284–292. doi:10.1016/j.jiec.2014.09.043.
- He, Jinbo, Pongsakorn Kanjanaboos, N Laszlo Frazer, Adam Weis, Xiao-Min Lin, and Heinrich M Jaeger. 2010. “Fabrication and Mechanical Properties of Large-Scale Freestanding Nanoparticle Membranes.” Small 6 (13): 1449–1456. doi:10.1002/smll.201000114.
- Jeziorny, Andrzej. 1978. “Parameters Characterizing the Kinetics of the non-Isothermal Crystallization of Poly(Ethylene Terephthalate) Determined by DSC.” Polymer 19 (10): 1142–1144. doi:10.1016/0032-3861(78)90060-5.
- Kalali, Ehsan Naderi, Xin Wang, and De-Yi Wang. 2016. “Synthesis of a Fe3O4 Nanosphere@ Mg–Al Layered-Double-Hydroxide Hybrid and Application in the Fabrication of Multifunctional Epoxy Nanocomposites.” Industrial & Engineering Chemistry Research 55 (23): 6634–6642. doi:10.1021/acs.iecr.5b04873.
- Khudiakova, A., M. Berer, S. Niedermair, B. Plank, E. Truszkiewicz, G. Meier, H. Stepanovsky, M. Wolfahrt, G. Pinter, and J. Lackner. 2020. “Systematic Analysis of the Mechanical Anisotropy of Fibre-Reinforced Polymer Specimens Produced by Laser Sintering.” Additive Manufacturing 36: 101671. doi:10.1016/j.addma.2020.101671.
- Li, Shuang, Keqing Han, Huaiping Rong, Xuanzhe Li, and Muhuo Yu. 2014. “Surface Modification of Aramid Fibers via Ammonia-Plasma Treatment.” Journal of Applied Polymer Science 131 (10), doi:10.1002/app.40250.
- Lin, Xue-Bao, Li Chen, Jia-Wei Long, Du Shuang-Lan, and Yu-Zhong Wang. 2018. “A Hybrid Flame Retardant for Semi-Aromatic Polyamide: Unique Structure Towards Self-Compatibilization and Flame Retardation.” Chemical Engineering Journal 334: 1046–1054. doi:10.1016/j.cej.2017.10.101.
- Liu, L., Y. D. Huang, Z. Q. Zhang, Z. X. Jiang, and L. N. Wu. 2008. “Ultrasonic Treatment of Aramid Fiber Surface and its Effect on the Interface of Aramid/Epoxy Composites.” Applied Surface Science 254 (9): 2594–2599. doi:10.1016/j.apsusc.2007.09.091.
- Liu, Xiaojiang, Wei Shian Tey, Jasper Yeng Chee Choo, Jiayao Chen, Pengfei Tan, Chao Cai, Adrian Ong, Lihua Zhao, and Kun Zhou. 2021. “Enhancing the Mechanical Strength of Multi Jet Fusion–Printed Polyamide 12 and its Glass Fiber-Reinforced Composite via High-Temperature Annealing.” Additive Manufacturing 46: 102205. doi:10.1016/j.addma.2021.102205.
- Liu, Xiaojiang, Wei Shian Tey, Pengfei Tan, Kah Kit Leong, Jiayao Chen, Yujia Tian, Adrian Ong, Lihua Zhao, and Kun Zhou. 2022. “Effect of the Fibre Length on the Mechanical Anisotropy of Glass Fibre–Reinforced Polymer Composites Printed by Multi Jet Fusion.” Virtual and Physical Prototyping 17 (3): 734–748. doi:10.1080/17452759.2022.2059638.
- Nascimento, Rodrigo Fernandes, Anderson Oliveira da Silva, Ricardo Ponde Weber, and Sergio Neves Monteiro. 2020. “Influence of UV Radiation and Moisten Associated with Natural Weathering on the Ballistic Performance of Aramid Fabric Armor.” Journal of Materials Research and Technology 9 (5): 10334–10345. doi:10.1016/j.jmrt.2020.07.046.
- Nasser, Jalal, Jiajun Lin, Kelsey Steinke, and Henry A. Sodano. 2019. “Enhanced Interfacial Strength of Aramid Fiber Reinforced Composites Through Adsorbed Aramid Nanofiber Coatings.” Composites Science and Technology 174: 125–133. doi:10.1016/j.compscitech.2019.02.025.
- Pötschke, Petra, Mahmoud Abdel-Goad, Ingo Alig, Sergej Dudkin, and Dirk Lellinger. 2004. “Rheological and Dielectrical Characterization of Melt Mixed Polycarbonate-Multiwalled Carbon Nanotube Composites.” Polymer 45 (26): 8863–8870. doi:10.1016/j.polymer.2004.10.040.
- Sa, Rina, Yan Yan, Zhenhai Wei, Liqun Zhang, Wencai Wang, and Ming Tian. 2014. “Surface Modification of Aramid Fibers by Bio-Inspired Poly(Dopamine) and Epoxy Functionalized Silane Grafting.” ACS Applied Materials & Interfaces 6 (23): 21730–8. doi:10.1021/am507087p.
- Singh, Riya, Akash Gupta, Ojestez Tripathi, Sashank Srivastava, Bharat Singh, Ankita Awasthi, S. K. Rajput, Pankaj Sonia, Piyush Singhal, and Kuldeep K Saxena. 2020. “Powder Bed Fusion Process in Additive Manufacturing: An Overview.” Materials Today: Proceedings 26: 3058–3070. doi:10.1016/j.matpr.2020.02.635.
- Tan, Lisa Jiaying, Wei Zhu, and Kun Zhou. 2020. “Recent progress on polymer materials for additive manufacturing.”
- Xu, Zhiyao, Yue Wang, Dingdi Wu, K. Prem Ananth, and Jiaming Bai. 2019. “The Process and Performance Comparison of Polyamide 12 Manufactured by Multi Jet Fusion and Selective Laser Sintering.” Journal of Manufacturing Processes 47:419-426. doi:10.1016/j.jmapro.2019.07.014.
- Yan, Chunze, Liang Hao, Lin Xu, and Yusheng Shi. 2011. “Preparation, Characterisation and Processing of Carbon Fibre/Polyamide-12 Composites for Selective Laser Sintering.” Composites Science and Technology 71 (16): 1834–1841. doi:10.1016/j.compscitech.2011.08.013.
- Zeng, Lei, Xuqing Liu, Xiaogang Chen, and Constantinos Soutis. 2018. “Surface Modification of Aramid Fibres with Graphene Oxide for Interface Improvement in Composites.” Applied Composite Materials 25 (4): 843–852. doi:10.1007/s10443-018-9718-9.
- Zhang, Bo, Lihua Jia, Ming Tian, Nanying Ning, Liqun Zhang, and Wencai Wang. 2021. “Surface and Interface Modification of Aramid Fiber and its Reinforcement for Polymer Composites: A Review.” European Polymer Journal 147: 110352. doi:10.1016/j.eurpolymj.2021.110352.
- Zhuang, Lin, Wei Zhang, Yongxin Zhao, Hui Shen, Han Lin, and Jinhua Liang. 2015. “Frugivorous Bird Guild Seasonal Patterns in Semiarid Chaco Forests are Linked to Habitat Seasonality but Reveal Phylogenetic Signature.” Journal of Scientific Research and Reports 5 (1): 1–5. doi:10.9734/JSRR/2015/14076.