ABSTRACT
Additive manufacturing has revolutionised the production of intricate and complex structures, offering numerous applications across diverse industries. Among the additive manufacturing techniques, VAT photopolymerisation (VP) is a promising method for fabricating intricate structures with smooth surface finishes. However, the inherent limitations of 3D printed structures, such as compromised mechanical strength and conductivity, necessitate the incorporation of filler materials. Graphene, a remarkable two-dimensional carbon material renowned for its exceptional mechanical and electrical properties, emerges as a highly desirable filler of various applications. The review addresses the critical parameters that affect the quality and properties of graphene composites fabricated using VP, including the choice of photopolymer resin, exposure parameters, and pre and post-processing techniques. It also explores the functionalisation of graphene materials, multi-material printing and hybrid composite systems. The resulting graphene composites find applications in various fields, including electronics, aerospace, biomedicine and energy storage. This review presents a comprehensive survey of these applications, highlighting the unique advantages of VP-derived graphene composites. The challenges and future prospects in the field of VP for graphene composites are discussed. These encompass improving printability, achieving enhanced graphene dispersion, and exploring novel hybrid materials and innovative applications.
1. Introduction
Additive manufacturing has garnered attention for its capacity to create intricate structures while consuming comparatively fewer raw materials. This technique operates on a bottom-up principle, thereby mitigating wastage of raw materials through efficient recovery and reuse. In stark contrast, conventional machining processes entail the removal of excess material from large blocks to attain the desired structures, resulting in substantial material wastage. In these traditional methods, the retrieval of waste materials demands intricate operations or, in some cases, proves impractical.
VP is a highly sought-after technique in additive manufacturing due to its ability to produce monolithic structures with intricate details and complex geometry [Citation1]. They find application in the fabrication of a wide spectrum of products, ranging from household appliances [Citation2] to cutting-edge biomedical instruments [Citation3]. VP encompasses several techniques for creating 3D objects by selectively curing liquid photopolymer resin layer by layer using light. The primary subtypes include Stereolithography (SLA), Digital Light Processing (DLP) and Continuous Liquid Interface Production (CLIP). SLA uses a laser to solidify each layer, DLP employs a digital light projector, CLIP relies on a continuous liquid interface to grow objects continuously and Two Photon Polymerisation uses a focused beam of light for achieving sub-micron resolution, each offering distinct advantages in terms of speed, resolution and materials compatibility [Citation4–6].
The incorporation of graphene into the polymer resin enhances the mechanical properties of printed objects, leading to improved strength, stiffness and flexibility [Citation7–9]. The inclusion of graphene significantly enhances the thermal conductivity of printed objects, making it beneficial for applications requiring efficient heat dissipation [Citation10,Citation11]. Its exceptional electrical conductivity enables the creation of printed objects with enhanced electrical properties, making them suitable for applications such as electronic circuits and sensors [Citation12–14]. Additionally, graphene-based VP provides a higher print resolution compared to traditional 3D printing methods, facilitating the production of intricate and highly detailed structures [Citation15,Citation16]. Furthermore, this technique minimises material waste as it selectively cures material layer by layer, making it economically and environmentally favourable [Citation17,Citation18]. The versatility of graphene-based VP allows for the incorporation of various functionalities into the polymer, enabling the customisation of printed objects with specific properties [Citation19,Citation20]. Continued research in this field aims to further refine the technique and explore novel applications for graphene-based additive manufacturing [Citation11,Citation21]. Polymers with customised properties can be synthesised and 3D printed using graphene, graphene oxide (GO), reduced graphene oxide (rGO) and functionalised graphene as nanofillers [Citation10,Citation20–23]. However, there are some challenges when graphene or graphene-based materials is used in VP. Graphene tends to agglomerate, which can lead to inconsistent material properties [Citation24]. Additionally, the high cost of high-quality graphene and the need for precise control over the printing process to prevent agglomeration can increase the overall production expenses. Furthermore, the limitations of VP in handling materials with specific thermal or mechanical requirements, which are often associated with graphene composites, may restrict its applicability for certain advanced applications.
Due to their enhanced properties, the photopolymerised graphene nanocomposites have found diverse applications across various industries. In electronics, it is employed to fabricate highly conductive and lightweight graphene-based components, such as flexible circuits, sensors and antennas, due to its excellent electrical properties and precise patterning capabilities [Citation25–27]. In aerospace, VP-produced graphene composites contribute to lightweight yet robust materials for aircraft components, offering enhanced strength and reduced weight [Citation28]. In biomedicine, VP is used to create customised implants and prosthetics with improved biocompatibility and mechanical strength [Citation29,Citation30]. Additionally, energy storage applications benefit from graphene-based VP, where it enables the development of high-capacity, fast-charging batteries and super capacitors [Citation31,Citation32]. Overall, graphene-based VP is at the forefront of innovation, demonstrating its versatility in enhancing materials and products across multiple sectors.
Several reviews had been conducted on graphene based 3D printed materials. Pinargote et al. [Citation33] and Wang et al. [Citation34] reviewed ink based printing methods for the 3D printing of Graphene based nanocomposites. Ponnamma et al. [Citation21] reviewed the recent advances and applications of 3D printed graphene nanocomposites. Mensing et al. [Citation35] reviewed 2D and 3D printing of graphene based super capacitors and batteries. Several other reviews had been conducted on graphene based materials in 3D printed materials used in structural and functional applications. However, as far as our knowledge, there had been no review that focused on VP process for 3D printing of graphene based composite materials and how various factors affects the properties and applications.
In this review, an in depth analysis of VP for fabricating graphene based nanocomposites is given. In the first part, different types of VP processes are outlined. The second part focuses on the synthesis and properties of graphene and graphene based materials. In the third and fourth part, the properties and applications of graphene nanocomposites are examined thoroughly. In the final part, challenges and improvements for future applications are also identified. Overall, this review gives an extensive assessment of VP process for graphene based nanocomposites, their properties and applications.
2. Types of Vat photopolymerisation
VP is used to create three-dimensional polymer-based objects using a photosensitive resin. It uses light to cure and harden the resin, layer by layer, to build up the desired object. The major types of VP include stereolithography (SLA), Digital Light processing (DLP), Continuous Liquid Interface Production (CLIP) and Two-Photon Polymerisation (TPP) as given in .
Figure 1. Different 3D printing techniques (a) SLA and DLP [Citation36] (b) CLIP process[Citation37] (c) TPP [Citation38].
![Figure 1. Different 3D printing techniques (a) SLA and DLP [Citation36] (b) CLIP process[Citation37] (c) TPP [Citation38].](/cms/asset/977cafb4-02aa-4013-ad15-100b660b7d20/nvpp_a_2276250_f0001_oc.jpg)
2.1. Stereolithography
Stereolithography (SLA) is a layer-by-layer preparation technique which uses an ultraviolet laser to selectively cure photopolymer resin where it is being scanned [Citation39]. A 3D computer aided design is sliced into 2D images of different layers. Then the UV laser scans over the vat surface using a scanning mirror to replicate the two-dimensional images of each layer on to the former cured layer to create a 3D object. Upon completion the object, UV light is used to further polymerise any incomplete areas followed by washing and polishing for smoother surfaces. Sanding, and painting is utilised to obtain smoother surface finish [Citation40]. SLA offers exceptional precision and fine detail capabilities, making it well-suited for applications requiring intricate graphene-based structures. Moreover, its compatibility with a wide range of photopolymer resins allows for tailored material formulations [Citation7,Citation41]. However, challenges include the need for specialised formulations to achieve uniform graphene dispersion, potential cost considerations due to expensive SLA equipment and materials, limitations in build volume, and the necessity for post-processing steps, which should be carefully weighed when choosing SLA for graphene composite applications [Citation39,Citation42]. Markandan et al. [Citation43] synthesised graphene–polymer composite structures through SLA. The material had anisotropic mechanical properties. Post processing heat treatment enhanced the modulus and strength of these composite materials. Also, a smaller amount of graphene was needed to achieve similar improvements compared to existing literature. This shows that the SLA-produced graphene–polymer composites have the potential to become a leading material choice for applications demanding high specific stiffness and strength.
2.2. Digital light processing (DLP)
Digital light processing (DLP) utilises UV light to selectively cure photopolymer layer-by-layer, similar to SLA. However, instead of scanning with a laser, DLP projects the entire image onto the surface of the vat containing the liquid resin using a high-resolution digital optical processor [Citation44,Citation45]. Apart from the difference in UV exposure, DLP and SLA are similar techniques in terms of raw materials, pre-processing and post-processing. Both employ layer-by-layer printing, which can introduce a step effect, particularly on curved surfaces, requiring post-treatment for smoother objects. Although the DLP technique is often more expensive, it is quicker compared to SLA. Additionally, it achieves fine resolution and excellent surface finish, ideal for intricate structures [Citation46]. However, challenges include potential difficulty in achieving uniform graphene dispersion within resins, reliance on proprietary materials and equipment, and the need for post-processing steps [Citation47]. Careful consideration of these factors is essential when selecting DLP for graphene composite applications in order to optimise the benefits and mitigate drawbacks [Citation48,Citation49]. Hanon et al. [Citation45,Citation50] studied the mechanical and tribological properties of Gr-resin composites. The composite with 0.5% of graphene showed optimum tribological properties with a homogenous distribution of graphene through the matrix [Citation45]. However, integrating graphene nanoplatelets did not enhance mechanical properties. Graphene caused UV light scattering, reducing curing and leading to sporadic unpolymerised areas, thereby increasing material porosity and higher graphene concentrations worsened mechanical performance due to increased porosity [Citation50].
2.3. Continuous liquid interface production (CLIP)
The continuous liquid interface production (CLIP) 3D printing technique utilises a vat of photosensitive resin and oxygen to maintain a layer of uncured liquid resin at the interface. CLIP exhibits superior production rates and resolution compared to conventional SLA and DLP 3D printing techniques [Citation51]. By utilising a continuous approach instead of a layer-by-layer approach, CLIP achieves remarkably smooth surfaces with fine details at an accelerated pace [Citation52]. It has demonstrated significant capabilities in producing complex components much more easily compared to its predecessors, such as expensive numerically controlled machines [Citation53]. As a result, it is being integrated into a variety of industries, including medical, automotive, air-conditioning and consumer goods. High costs, limited choices of precursor materials and the complexity that requires trained personnel are some challenges associated with CLIP [Citation54]. For rapid printing speeds and superior surface finishes due to its continuous, layer less process, CLIP had been used rarely for graphene based composites as not all graphene based composites may work seamlessly with the technology. Additionally, CLIP systems can be complex and expensive to acquire and maintain, limiting accessibility for some users and industries, and requiring specialised expertise for optimal utilisation. Huang et al. [Citation37] developed photocurable ink using biocompatible Poly(Ethylene Glycol) Diacrylate (PEGDA) and GO. This ink effectively harnessed a low-cost visible light source. GO played a dual role, serving as a photo absorber to enhance visible light absorption for high-resolution CLIP printing and as a reinforcement for the polymer matrix, resulting in excellent mechanical properties in the final products. Notably, CLIP-printed micro lattices with micro textures as thin as 100 μm exhibited exceptional super elasticity alongside outstanding mechanical performance. Impressively, custom geometries of these micro lattice prints demonstrated remarkable resilience, withstanding compressive strains of up to 90%. Zhang et al. [Citation55] developed precise graphene/polymer composites using electrically-assisted CLIP. By integrating an electric field and a polymer matrix capable of dual curing through photo and thermal processes, the authors achieved the fabrication of high-performance, well-structured graphene/polymer composites. However, the printed composite contains less than 2.0 wt% graphene, significantly lower than what other 3D printing methods have achieved. This limitation is mainly attributed to slower refilling due to higher viscosity and increased light-absorption and shadowing by graphene nanoplatelets as graphene content rises. Addressing these challenges will be a focus of future research to enable higher graphene content in the continuous 3D printing process.
2.4. Two photon polymerisation
Two-photon polymerisation (TPP) is another VP technique that employs a vat of monomer resin, which is hardened through photopolymerisation using a focused beam of light. Polymerisation takes place exclusively at the points where the laser is focused [Citation56,Citation57]. This enables the creation of 3D structures with sub-micrometer dimensions, reaching sizes as small as 100 nm. By utilising non-contact processes, this technique preserves intricate and delicate details with ease. TPP finds extensive applications, including tissue engineering scaffolds and microfluidic devices, among others [Citation58,Citation59]. The sub micrometer resolution keeps its surface finish better compared to other vat photo polymerisation techniques. Nekrasov et al. [Citation6] printed bovine serum albumin (BSA)/ GO composites using TPP. During TPP, there is a potential for GO reduction, leading to an increase in active oxygen groups. This, in turn, can promote BSA polymerisation in proximity to graphene flakes. The photochemical reduction of GO reduces negative charges on surfaces, thereby reducing the repulsive energy of BSA and consequently increasing the coverage of BSA on the GO surface.
3. Graphene based materials for VP
Graphene is an allotrope of sp2 hybridised single layer carbon atoms to create a 2D honeycomb structure. It has high carrier density, optical transparency and thermal conductivity with excellent flexibility and mechanical strength [Citation60–62]. Graphene is both a jack of all trades and master of some where it has been used from energy to biomedical applications [Citation63,Citation64] with more than 1 million scientific articles to its credit. Graphene is frequently employed in VP as a reinforcement material for enhancing the mechanical and electrical properties of 3D-printed objects. By incorporating graphene into photopolymer resins, VP can produce high-strength composites that exhibit exceptional durability and electrical conductivity. Additionally, graphene's excellent thermal conductivity makes it valuable in VP for creating objects with efficient heat dissipation properties, expanding its utility in various industrial and research applications. Since graphene's structure and form affect its properties and applications, tuneable production techniques are important. This is because the synthesis method directly impacts the quality, characteristics and dispersion of graphene within the photopolymer resin, which, in turn, profoundly influences the performance of the 3D-printed objects. Properly synthesised graphene, with well-defined layers and minimal defects, ensures optimal reinforcement properties and electrical conductivity in VP-produced composites. Additionally, the method used can affect the compatibility of graphene with the photopolymer resin, influencing the printability and overall success of the VP process. Exfoliating graphite in liquid phase is the most typical way to produce few layered graphene by chemical vapour deposition process [Citation65]. Graphene also can incorporate diverse moieties onto its surface via the functionalisation process, which is critical for tailoring the material to the specific application and improving cohesiveness when utilised as next-generation composites [Citation60,Citation66]. Graphene can be utilised in its various forms such as graphene oxide, reduced graphene oxide, graphene platelets, graphene-based ink and graphene flakes as given in [Citation64,Citation67]. However, for 3D printing, oxidative intercalation which alters the chemical composition of graphite to produce graphene oxide (GO) or reduced graphene oxide (rGO) is more commonly used as these materials are more dispersible and easily manageable [Citation68]. Other than oxidation, use of surface functionalisation and surfactants are also employed to achieve better dispersability [Citation23,Citation69,Citation70]. Graphene differs greatly from other carbon allotropes such as carbon nanotubes, fullerenes and bulk graphite and provides a novel method for exploring the unique physics of 2D materials [Citation71]. Compared to other carbon allotropes, graphene's flat structure and ease of dispersion within photopolymer resins make it a preferred choice for achieving consistent and desirable material properties in VP.
Figure 2. Structure of Graphene, few layer graphene, graphite, reduced graphene and graphene oxide commonly used in VP.
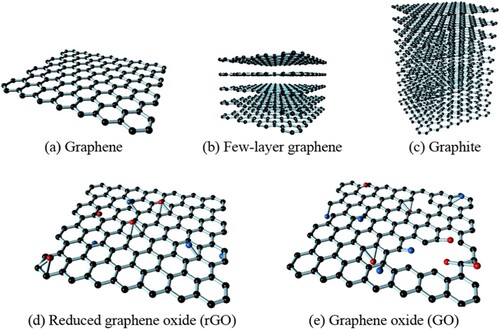
Graphene can be incorporated into the material before [Citation72] and after 3D printing process [Citation60]. If the material is incorporated before 3D printing, graphene is dispersed evenly within the liquid photopolymer resin. This dispersion process often involves methods such as ultrasonication or mechanical stirring to ensure uniform distribution. Once dispersed, the mixture is used as the printing material, and the VP process proceeds as usual, allowing the graphene to be incorporated into the printed object. To add graphene to an already 3D printed material, a post-processing approach is typically employed. This involves either infusing the printed object with a graphene-containing solution or applying a graphene-based coating onto the printed surface. The choice of method depends on the specific requirements of the application and the desired enhancement of mechanical, electrical, or thermal properties.
VP is less commonly used for graphene ceramic printing due to fundamental material and process limitations. Graphene's poor compatibility with typical photopolymer resins used in VP hinders its homogeneous dispersion, making it challenging to achieve uniform material properties. Moreover, ceramics often require high-temperature sintering or densification processes, which are not compatible with VP's curing mechanisms, leading to difficulties in achieving the necessary ceramic consolidation during the printing process. These technical challenges and material incompatibilities have led to the preference for alternative 3D printing methods, such as binder jetting or selective laser sintering, for graphene ceramic printing applications. However, Graphene/Al2O3 nanocomposites were used for making slurry for DLP printing [Citation73]. Incorporating graphene into the Al2O3 slurry offered a solution to the challenge of balancing solid loading with printing accuracy and strength. Graphene addition reduced slurry fluidity, enhancing stability and preventing printing issues in top-down DLP technology. Higher graphene content increased slurry viscosity, UV light absorbance, printing precision and bending strength. The resulting Al2O3 ceramic component displayed uniformity, density and minimal defects, with tight connections between printing layers. A mask based VP was used for synthesising lightweight Gr/Silica composites porous conductive ceramics [Citation74]. Incorporating graphene into silica-based ink allows for the creation of high-resolution 3D structures with controlled macroscale porosity. When combined with mesoporous silica feedstock, the resulting printed sample exhibits a low thermal conductivity of 62 mWm−1K−1 and a density of 0.366 gcm−3. Moreover, the mechanical properties can be fine-tuned by adjusting the graphene content and further strengthened through spark plasma sintering, resulting in a robust strength of 57.947 MPa. Notably, the percolation of graphene within the porous ceramic matrix forms an electrically conductive network, providing high conductivity and exceptional stability, even in elevated temperature environments exceeding 600°C. Quanchao et al. [Citation73] utilised graphene as a small quantity additive in high solid loading Al2O3 (60 vol%)-acrylic resin. The introduction of graphene reduced the slurry fluidity facilitating better print quality and reduced print failure due to backflow during printing. The sedimentation of Al2O3 within the monomer was reduced by the presence of graphene. When graphene was added, printing accuracy, bending strength and UV absorption of the slurry was improved.
Similarly, Graphene-metal composites also are rarely used in VP. However, in cases where metal-like properties are desired in VP-produced objects, composite materials that incorporate graphene with polymers or ceramics can offer enhanced mechanical, electrical or thermal characteristics. These composites may contain metal-like properties to a certain extent, but they are not true metal-graphene composites. Younes et al. [Citation19] developed highly aligned 3D printed Fe3O4@graphene composite using magnetic field assisted VP. Shin et al. [Citation75] used dip coating a 3D printed micro-lattice in graphene with enhanced electroplating of nickel.
3.1. Graphene ink for VP
Huang et al. [Citation37] synthesised high resolution super elastic micro lattices using graphene oxide nanoparticles. Graphene oxide was synthesised from graphite using modified Hummer's process [Citation76]. In this procedure, graphite powder was mixed with H2SO4 and H3PO4. Additionally, KMnO4 was added slowly to the mixture, and the mixture was heated at 50°C while being stirred for 12 h. After adding H2O2 solution, the resulting solution was rinsed with distilled water and HCl to produce GO suspension [Citation37]. Even though, graphene synthesised using Hummer's method provide excellent mechanical and electrical properties enhancement, it lacks in ensuring homogeneous dispersion within the photopolymer resin, which can be intricate. The method's cost-effectiveness for large-scale VP production also limits its scalability in certain applications.
Graphene had been directly mixed into the polymer matrix using sonication and stirring. Han et al. [Citation27] used poly acrylate resin and graphene-dispersed polyaniline (PANI) nanofibers to create DLP ink. Joo et al. [Citation49] employed polyurethanes in the mix system, which increased the printing resolution for the DLP process as well as the tensile strength and conductivity of the materials when compared to the original materials. To increase the dispersability and applicability electrochemically exfoliated graphene ink had been utilised. Optimising the ink formulation for specific VP materials and processes to ensure compatibility and maintaining consistent electrical conductivity throughout the printed object requires careful control of ink properties and processing parameters.
In addition to graphene based ink, aqueous dispersion of GO was also utilised as an ink because it has high dispersability and electrical conductivity. The GO ink was combined with PEGDA, and two photo initiators – Irgacure 819 and Irgacure 1173 – were also added to improve UV light absorption. To create a stable polymeric media, this combination was sonicated. This ink was expected to print efficiently, adhere to surfaces better, and have good printing resolution [Citation22]. GO ink offers distinct advantages over graphene ink in VP. GO's excellent aqueous dispersability facilitates homogeneous mixing with polar photopolymer resins, ensuring uniform material properties and reducing the risk of agglomeration during printing [Citation77]. The oxygen-containing functional groups on GO's surface also enable tunability of its properties, making it versatile for tailoring electrical, mechanical and chemical characteristics in 3D-printed objects. GO's enhanced adhesion due to these functional groups promotes better layer adhesion and structural integrity in VP, resulting in improved print quality and reliability for a wide range of applications.
GO dispersed in N-Methyl pyrrolidone (NMP) also has been used in conjugation with photocurable resins. When cross-linked GO sheets were combined with photocurable acrylates in NMP using a photo initiator, complex and hierarchical 3D architectures composed of cross-linked GO sheets were formed [Citation60,Citation78]. Graphene also was prepared using a similar method. Due to its vast surface area, cross-linked graphene was also found to aid in the creation of porous structures; however, ink formed from pristine graphene sheets did not perform similarly. GO, with its oxygen-containing functional groups, tends to disperse more readily in NMP due to improved interactions with the solvent, resulting in a homogeneous mixture with the photopolymer resin. In contrast, pristine graphene's limited functionalisation can lead to poorer dispersion in NMP, necessitating additional efforts to prevent agglomeration and ensure even distribution throughout the printing material, which can be more challenging.
4. VP 3D printing using graphene based resins
Graphene is introduced into 3D printed system either by adding directly to the resin or by solvent intercalation as given in [Citation79,Citation80]. Solvent intercalation is generally used to get better dispersability as direct addition can lead to aggregation. They are generally referred to as graphene inks as given in section 3.1. It can also be added to the surface post 3D printing either by dip coating or grow within the matrix by injecting or chemical vapour deposition as given in [Citation26,Citation31,Citation81]. These were done to obtain modified surface properties or developing graphene skeletal structures. These techniques and their advantages and disadvantages are explained in . There are different processing techniques used in graphene intercalation within the polymer matrix.
Figure 3. Preprocessing for graphene polymer composite using solvent intercalation. This is the commonly used method for ensuring graphene dispersion within the resin. Solvent intercalation generally helps in stopping agglomeration of different graphene layers [Citation17].
![Figure 3. Preprocessing for graphene polymer composite using solvent intercalation. This is the commonly used method for ensuring graphene dispersion within the resin. Solvent intercalation generally helps in stopping agglomeration of different graphene layers [Citation17].](/cms/asset/d4e8c5f0-2b43-4c3c-a3e2-afed9d3952c6/nvpp_a_2276250_f0003_oc.jpg)
Figure 4. Post processing graphene coating examples, (a) CVD grown graphene onto template [Citation31] (b) 3D graphene structure through post processing; injection of graphene ink followed by hydrothermal treatment and then freeze drying and thermal etching [Citation81].
![Figure 4. Post processing graphene coating examples, (a) CVD grown graphene onto template [Citation31] (b) 3D graphene structure through post processing; injection of graphene ink followed by hydrothermal treatment and then freeze drying and thermal etching [Citation81].](/cms/asset/3d068fcd-173e-4436-8903-290e2bdf607e/nvpp_a_2276250_f0004_oc.jpg)
Table 1. Summary of current works in 3D printed Graphene nanocomposites.
Preprocessing is a critical step in the fabrication of graphene based nanocomposites using VP. Preprocessing techniques like sonication or chemical functionalisation help disperse them uniformly within the polymer matrix, ensuring even distribution of graphene [Citation88,Citation89]. It enhances the interaction between graphene and the polymer matrix, leading to improved mechanical strength, electrical conductivity and thermal properties in the final composite [Citation41,Citation83]. It also allows for precise control of the composite's viscosity, facilitating smooth handling during the VP process [Citation73]. By reducing the likelihood of graphene aggregation, preprocessing ensures a consistent and high-quality material, thus optimising the overall performance of the nanocomposite in various applications. De Armentia et al. [Citation67] investigated variations in print quality of graphene based resin composites as given in (c). They observed that while GO and GNPs did not affect printability, the negative effect of graphene such as UV absorbance led to print failure. This problem also can be tackled using pre and post processing of graphene materials or the printed materials.
Figure 5. Overall process and cell attachment of the bio printed GO composites [Citation91]. The material acts as a good scaffold for cell growth.
![Figure 5. Overall process and cell attachment of the bio printed GO composites [Citation91]. The material acts as a good scaffold for cell growth.](/cms/asset/0c3934b4-b2ed-43fc-bf39-36e0482c2c7b/nvpp_a_2276250_f0005_oc.jpg)
Tsang et al. [Citation92] observed a negative effect on both mechanical properties and thermal propertied when GO was added directly to the photopolymer resin. They, freeze dried GO produced through Hummer's method was solvent intercalated into acrylic resin. The method poses a high risk of aggregation. Feng et al. [Citation17] used solvent intercalation for getting proper dispersion of graphene within polylactic acid – polyurethane matrix. For alginate – GO hydrogels the ionic cross liking between the filler and matrix improves the mechanical properties drastically [Citation93]. Feng et al. [Citation52] investigated graphene composite with polylactic acid-polyurethane based resin with Triethylene glycol dimethacrylate (TEGDMA) as reactive diluent and intercalating solution. The photo initiator was mixed with diluent through sonication. The mixture was degassed to obtain homogenous liquid resin. The addition of graphene nanofillers did not affect the viscosity and thermomechanical properties of the nanocomposite. The rapid curing nature of the method enabled the homogeneous dispersion of nanofillers without the formation of agglomerates, which can occur with traditional resin curing processes.
Guo et al. [Citation83] functionalised GO using BYK copolymer containing amino groups for better dispersability within the matrix followed by post thermal reduction. The final product showed much better conductivity without sacrificing the flexibility of the polymer. Ramirez-Soria et al. [Citation69] functionalised graphene for better dispersability within the matrix using microwave assisted surface bifunctionalisation. Ductile to brittle behaviour transition was observed with increases of surface functionalisation.
Dispersion can also be ensured using surfactants. Lim et al. [Citation70] developed a Gr/photopolymer resin composite nanofluid using Tween 20 as surfactant to achieve homogenous dispersion. As the Tween 20 has high transparency, it did not affect the curing. However, the inclusion of graphene beyond 2 wt% was problematic due to light absorption. Another preprocessing method is to ensure the orientation of the filler material within the resin [Citation19,Citation94]. If the filler material is oriented, the mechanical properties could be improved though it leads to anisotropy.
Different post-processing treatments are employed for graphene-based materials fabricated using VP to further enhance their properties and functionality. They can improve the mechanical performance and durability of the composites. Techniques like thermal annealing can help in curing and strengthening the printed parts by removing any residual solvents and enhancing the intermolecular bonds [Citation20,Citation80]. It can also refine the surface finish and aesthetics of printed structures. Polishing or chemical treatments can smoothen rough surfaces and improve the overall appearance [Citation17]. Moreover, functionalisation methods, such as chemical or plasma treatments, can be used to modify the surface chemistry of graphene-based VP prints. This is crucial for tailoring the material's properties, such as wettability, adhesion, or compatibility with specific applications. Post-processing may involve the integration of additional components, such as coatings or nanoparticles, to impart specific functionalities like corrosion resistance or antibacterial properties to the graphene composites [Citation75].
Different methods have been used for post processing 3D printed graphene based composites. The pyrolysis of polymers and the reduction of GO are both accomplished by the high-temperature annealing process. Annealing improves the electrical and mechanical characteristics of polymers. Additionally, it was discovered that UV-based post curing worked well for in-situ GO reduction of 3D printed components [Citation78]. Markandan et al. [Citation55] developed Gr – polymer octet – truss lattice using SLA. The post baking improved the mechanical properties of the material while solvent addition reduced the mechanical properties and improved ductility. Manapat et al. [Citation46] observed similar result where the annealing 3D printed graphene led to drastic enhancement of mechanical properties. The acid catalysed esterification of filler matrix crosslinking and removal of intercalated solvents improved the mechanical properties. Carbon fiber-GO multifiller material composite investigated by Xiao et al. [Citation56] also showed post print annealing improving mechanical properties. Korhonen et al. [Citation58] used GO to form 3D printed composite PIC100 structures, and pyrolysed it afterwards to reduce the GO and to eliminate the polymer. The pyrolysis led to formation of brittle structures with shrink in dimensions. Nguyen et al. [Citation43] utilised GO– water suspension in PEGDA and to cause of GO hydrazine was used which is then reduced by exposing to UV light. Finally, thermal reduction of the 3D printed part was done in order to attain maximum reduction in oxygen functionalities for desired enhancement of electrical conductivity. De Leon and Molina studied the effect of the degree of curing on the graphene 3D printed composite [Citation54]. While 3D printed parts were inferior in mechanical properties, due to lack of complete curing led by GNP's s UV absorption, post processing through curing under a UV source removed this issue. The post processing treated parts were having better mechanical properties.
Rather than having graphene as a resin additive, Du et al. [Citation31] coated graphene on to 3D printed silica template though chemical vapour deposition. Later, hydrofluoric acid etching was done to get light weight graphite foam resin matrix. Kamat et al. [Citation26] dip coated a printed PDMS (Polydimethylsiloxane)-like elastomer resin graphene dispersed in ethanol and subsequently annealed at 100°C for curing. Zhou et al. [Citation89] developed 3D printed microporous capillary channels for solar steam generation which was coated with graphene for efficient use of sunlight for vapour production followed by a hydrophobic layer for antifouling functionality. The composite and their coating is given in (a,b).
5. Application of VP graphene based 3D printed material
Vat photopolymerised graphene-based composites find versatile applications across multiple industries. Their unique properties, including exceptional mechanical strength, electrical conductivity and thermal stability, make them valuable in additive manufacturing, where they are used to produce lightweight and robust components for aerospace, biomedical, electrical and thermal applications [Citation10,Citation28,Citation67]. In the field of electronics, these composites are employed in printed circuit boards and sensors, capitalising on their excellent conductivity [Citation42]. Biomedical applications include tissue engineering scaffolds and bactericides, harnessing their biocompatibility and controlled release properties [Citation9,Citation17]. Additionally, vat photopolymerised graphene composites have gained traction in energy storage, enhancing the performance of supercapacitors and batteries [Citation31,Citation32]. These applications highlight the wide-ranging potential of these composites in advancing technology and industry.
Many articles on the topic considered the enhancement of mechanical properties due to the exceptional mechanical attributes of graphene and its unique structural characteristics [Citation43,Citation85]. Graphene's exceptional stiffness and strength, with a tensile strength over 130 GPa, make it an ideal reinforcing agent. The graphene sheets act as load-bearing components when incorporated into the polymer matrix during 3D printing processes like DLP and SLA. They distribute external mechanical loads more effectively throughout the composite, preventing crack propagation and improving the final printed objects’ overall strength, stiffness and fracture resistance [Citation95].
Moreover, graphene's 2D structure with a high surface area allows for strong interfacial interactions with the polymer matrix, enhancing the load transfer between the two phases. This improved interfacial adhesion reduces the chances of delamination or material separation, further contributing to enhanced mechanical properties [Citation43]. Graphene's excellent thermal conductivity can help dissipate heat generated during the 3D printing process, reducing the risk of warping or defects in the printed parts [Citation67]. Overall, the incorporation of graphene or graphene-based materials in these 3D printing techniques results in composites with improved mechanical performance, making them suitable for a wide range of applications, including aerospace, automotive and biomedical devices [Citation10,Citation28]. As given in , many research on the topic considered the improvement of mechanical strength of 3D printed components due to the addition of Graphene. They have stipulated the use of these materials in aerospace and automotive applications, even though the studies that are conducted that directly examine these uses are rare.
The concentration of graphene filler in VP composites plays a crucial role in determining their mechanical properties. As the graphene filler concentration increases, several mechanical properties typically improve. The high aspect ratio and exceptional stiffness of graphene sheets contribute to enhanced tensile strength, modulus and overall structural integrity of the composite. This increase in mechanical performance results from the effective load-bearing capability of graphene within the polymer matrix [Citation90]. However, there is an optimal graphene concentration, beyond which a diminishing return in mechanical improvement may occur due to issues related to filler agglomeration or a decrease in the matrix's ability to effectively wet and disperse the graphene sheets. Different studies showed different optimum concentrations of Graphene based materials. 0.5 wt% GO nanocomposites exhibited increased strength, stiffness and ductility when compared to the pristine resin [Citation9]. In another study, 0.5 and 1 wt% samples showed enhanced mechanical performance [Citation86]. As a rule of thumb, more than a 2% addition of graphene typically reduces strength. Therefore, the mechanical properties of VP composites are influenced by the graphene filler concentration, with an optimum concentration that balances reinforcement and dispersion factors to achieve the desired mechanical performance.
The addition of graphene can also significantly impact tribological properties. They work in manifold. Graphene's 2D structure offers exceptional lubrication, reducing friction and wear between interacting surfaces [Citation45]. Its mechanical strength reinforces the material matrix, enhancing its resistance to wear-induced stresses. High thermal conductivity aids in efficient heat dissipation during friction, preventing overheating and wear. Furthermore, it can reduce adhesion between surfaces, minimise sticking and lower the coefficient of friction, contributing to smoother, more efficient tribological interactions. Ultimately, the incorporation of graphene in VP materials can lead to improved friction and wear performance, benefiting various applications.
5.1. Biomedical applications
Vat photopolymerised graphene nanocomposites have garnered significant attention in the field of biomedicine due to their unique properties and versatile applications. These nanocomposites find use in tissue engineering as scaffolds for bone, cartilage and neural regeneration, benefitting from graphene's mechanical strength and electrical conductivity. Additionally, they serve as a promising candidate for bactericidal activities and neurological applications [Citation29]. These nanocomposites have great potential to advance various biomedical applications, spanning regenerative medicine, diagnostics and therapeutic interventions.
Zhou et al. [Citation91], combined various concentrations of GO ranging from 0 to 1 mg/mL with a mixture of gelatine-methacrylate (GelMA) and PEGDA to create a biocompatible photopolymerisable ink. Subsequently, 3D-printed scaffolds were produced using stereolithography-based printing with a UV laser. The optimal combination for scaffold fabrication was determined to be 15% GelMA + PEGDA with GO incorporated at 0.1 mg/mL. When human mesenchymal stem cells (MSCs) were cultured on these scaffolds for 5 days, they exhibited spreading and extension. Importantly, the GelMA-PEGDA-GO scaffolds induced chondrogenic differentiation of MSCs and enhanced the production of glycosaminoglycans and collagen. Furthermore, gene expressions related to chondrogenesis, including Collagen II, SOX 9, and Aggrecan, were significantly upregulated on the scaffolds, making them promising candidates for applications in cartilage regeneration. shows the overall performance of the bioprinted composites.
Angulo-Pineda et al. [Citation96] created SLA composite scaffolds using polycaprolactone (PCL) infused with thermally reduced rGO nanoparticles at concentrations surpassing the percolation threshold. When an electric voltage was applied across their surface, it exhibited a bactericidal effect. Additionally, within the same electrical stimulation regimen, these scaffolds exhibited improved adhesion and viability of human stem cells when compared to pure PCL scaffolds, both with and without electrical stimulation.
A biodegradable UV-cured resin was produced using SLA with commercial polyurethane (PU) resin as an oligomer, trimethylolpropane trimethacrylate (TEGDMA) as a reactive diluent, and phenylbis(2,4,6-trimethylbenzoyl)-phosphine oxide (Irgacure 819) as a photoinitiator. The 3D printed specimens exhibited a tensile strength of 68 MPa, a remarkable 62% increase compared to reference specimens produced by direct casting. Moreover, the flexural strength and modulus reached 115 MPa and 5.8 GPa, respectively. Utilising a solvent-free method, graphene reinforced nanocomposite structures, including porous bone architectures and gyroid scaffolds for bone tissue engineering, were successfully printed [Citation17].
de Armentia et al. [Citation67] studied the effect of polymerisation parameters in SLA printing on the applicability of GO and Graphite nanoplatelets (GpNP) for biomedical applications. Despite the adverse impact of GpNP on polymerisation, the incorporation of 0.1 wt% of both GO and GpNP into the photocured resin did not significantly compromise printing quality, making them suitable for creating new nanofilled photocurable resins for SLA printing. However, it was observed that adding 0.1 wt% of G had a notably detrimental effect on printability. This discrepancy could be attributed to differences in type, functionalisation, and structure of graphene based nanomaterials, which affect dispersibility and light absorption. Nonetheless, the challenges posed by G in printing can be overcome by optimising printing parameters to counter its negative impact on polymerisation. Even though, they haven't done any biocompatibility or cell proliferation studies on the scaffold these materials can be used in biomedical applications. There are only few avenues where VP based graphene composites are used in biomedical applications. These materials should be explored for drug delivery, biosensing and bioelectric applications.
5.2. Advanced electronics
Vat photopolymerised graphene composites have emerged as promising materials for supercapacitor and smart electronics applications [Citation90]. By incorporating graphene into the composite structure, they benefit from the material's high surface area, excellent electrical conductivity and mechanical strength [Citation35]. The precise control afforded by the SLA [Citation97,Citation98] and DLP [Citation42] process enables the design of intricate electrode structures, enhancing the overall capacitance and energy storage capacity of the supercapacitor. Additionally, the fast charge–discharge kinetics of graphene composites make them suitable for rapid energy storage and delivery, offering potential solutions for energy storage challenges in various electronic devices and renewable energy systems.
When fabricating Energy-Storage and Energy-Conversion Devices, in-plane designs are more commonly preferred for techniques like DIW and IJP, while sandwich designs are readily adopted for SLA-based 3D printing. This preference arises because SLA utilise insulating polymer matrices, limiting the options for creating conductive composites, which are crucial for Energy-Storage and Energy-Conversion Device construction. Another fundamental reason is that SLA-based 3D printing can directly produce objects with complete form factors, including coin cells, thin film cells, outer casings and complex electrodes in a single or multi-step printing process [Citation99]. Fu et al. [Citation100] utilised SLA technology to manufacture conductive substrates based on polymer graphene, which were subsequently electrophoretically coated with anode material (LTO), LiAlO2-PEO membrane and cathode material (LFP) using a trilayer sandwiched design. These cells, cycled at 0.1C, demonstrated an areal capacity of 400–500 μAhcm−2.
Utilising stereolithography, Xue et al. [Citation32] created metallic composite lattices with octet-truss structures, incorporating 3D hierarchically porous graphene onto the scaffolds for quasi-solid supercapacitor applications. The resulting supercapacitor exhibited promising characteristics, including a high areal capacitance (57.75 mFcm−2), impressive rate capability (70% retention from 2 to 40 mAcm−2), long lifespan (96% retention after 5000 cycles) and a superior energy density of 0.008 mWhcm−2, comparable to leading carbon-based supercapacitors. This combination of stereolithographic 3D printing and hierarchically porous graphene architecture offers a novel approach to manufacturing energy storage devices and opens avenues for creating high-performance functional electronics.
Joo et al. [Citation49] fabricated polyurethane (PU) composites for DLP-type 3D printing, incorporating polyaniline (PANI) nanomaterial and graphene sheets (GS). Sculptures of varying sizes and shapes using PU/PANI and PU/GS composites with different filler contents exhibited significantly improved sheet resistance, with PU/PANI being up to 8.57 × 104 times lower (1.19 × 106 Ω/sq) and PU/GS up to 1.27 × 105 times lower (8.05 × 105 Ω/sq) compared to pristine PU (1.02 × 1011 Ω/sq). Furthermore, the tensile strengths of PU/PANI and PU/GS composites were 1.41 times (44.5 MPa) and 2.19 times (69.3 MPa) higher, respectively, compared to pristine PU (31.6 MPa). Even though, they cannot be considered as a supercapacitor, the materials showed highly conductive nature. gives the 3D printed electronic components manufactured using this technique.
Figure 6. The entire procedure for conductive 3D printing involves the use of polyurethane (PU) resin solutions combined with a mixture of polyaniline (PANI) nanofiber (NF) and a graphene sheet (GS). Presented below are digital images of 3D-printed PU composites featuring various filler contents:(b) 1 wt% PANI, (c) 3 wt% PANI, (d) 6 wt% PANI, (e) 0.33 wt% GS, (f) 1.00 wt% GS and (g) 2.00 wt% GS. The scale bar dimensions for each image are as follows: (b) 1 cm, (c) 1 cm, (d) 1 cm, (e) 1 cm, (f) 1 cm and (g) 1 cm [Citation49].
![Figure 6. The entire procedure for conductive 3D printing involves the use of polyurethane (PU) resin solutions combined with a mixture of polyaniline (PANI) nanofiber (NF) and a graphene sheet (GS). Presented below are digital images of 3D-printed PU composites featuring various filler contents:(b) 1 wt% PANI, (c) 3 wt% PANI, (d) 6 wt% PANI, (e) 0.33 wt% GS, (f) 1.00 wt% GS and (g) 2.00 wt% GS. The scale bar dimensions for each image are as follows: (b) 1 cm, (c) 1 cm, (d) 1 cm, (e) 1 cm, (f) 1 cm and (g) 1 cm [Citation49].](/cms/asset/0f45baf5-649b-4aa4-8596-c620ab2b2a34/nvpp_a_2276250_f0006_oc.jpg)
Guo et al. [Citation83] used a one-step, environmentally friendly ultrasonication technique to create functionalised graphene oxide (fGO). This fGO exhibited exceptional dispersion and stability when introduced into an acrylate-based solution, significantly increasing the solid content of fGO in suspensions for SLA 3D printing. The incorporation of 5 wt% fGO enhanced the nanocomposite's flexibility and minimised dimensional shrinkage during thermal post-curing. Furthermore, due to the thermal reduction of fGO within the acrylate-based nanocomposite, the electrical conductivity dramatically increased to 2.6 × 10−4 S/cm, surpassing the neat resin's conductivity by 108 times (5 × 10−12 S/cm). Moreover, the nanocomposite displayed a static decay time of less than 0.1 s when subjected to voltages ranging from 1000 to 100 V. As a result, this SLA-printed nanocomposite, characterised by its high flexibility, thermal stability and static dissipative properties, holds substantial promise for advanced smart electronics applications.
5.3. Thermal applications
VP graphene composites find compelling applications in the thermal domain. The exceptional thermal conductivity of graphene allows these materials to efficiently conduct and dissipate heat, making them valuable for various thermal management applications [Citation11]. In electronics, VP graphene composites are used for heat sinks, ensuring efficient cooling of electronic components. Additionally, in industries requiring high thermal conductivity materials, such as aerospace and automotive, VP-printed graphene composites are employed to enhance heat transfer and improve the performance and longevity of critical components. These applications highlight the versatility and effectiveness of VP graphene composites in addressing thermal challenges across various sectors [Citation24].
Sevik et al. [Citation10] compared the addition of nano-aluminium, nano-copper and GNPs into the resin at a concentration of 0.5% by weight for heat sink applications using SLA. They exhibited a uniform distribution of components. Both experimental and simulated assessments were conducted to evaluate their thermal performance. Notably, angled and channel heat sinks demonstrated superior design characteristics. Among the nanocomposite heat sinks, those containing graphene additives outperformed the others, exhibiting up to a 6.5% improvement over pure resin heat sinks. When considering geometric effects, this improvement increased to 10.7%, implying an approximate 11% enhancement in the maximum junction temperature (Tjmax) of an LED lamp.
Ligati et al. [Citation11] fabricated a composite material consisting of a polymer matrix with initially low thermal conductivity (TC) using DLP. Low TC is substantially improved by incorporating thermally conductive graphene-based filler. To prevent phase separation of Graphene nano platelets (GNP) within the monomer printing solution, sepiolite, which effectively entraps the GNPs were introduced. 2.0 wt% GNP loaded composites, resulting in a remarkable 160% increase in TC compared to the pristine polymer. It also imparted anisotropic TC to the material, characterised by a cross-plane/in-plane (TCcp/TCip) ratio of 1.6. This feature proves advantageous for thermal management systems designed to efficiently dissipate heat vertically from a heat source. given the IR image and the structure of the heat sink constructed.
Figure 7. (a) A heat sink composite, produced using VP printing and containing 1.8% weight of GNP and 4.4% weight of sepiolite. (b) A top-view infrared image of the heat sink composite. (c) A diagram illustrating the heat sink created solely from the pure polymer. (d) A diagram depicting the heat sink made from the composite, both placed on a hot plate at 50°C. The temperatures at the base and fin tips have been determined from the infrared images [Citation11].
![Figure 7. (a) A heat sink composite, produced using VP printing and containing 1.8% weight of GNP and 4.4% weight of sepiolite. (b) A top-view infrared image of the heat sink composite. (c) A diagram illustrating the heat sink created solely from the pure polymer. (d) A diagram depicting the heat sink made from the composite, both placed on a hot plate at 50°C. The temperatures at the base and fin tips have been determined from the infrared images [Citation11].](/cms/asset/a3813362-a28e-4446-8d90-cb229b5cc21c/nvpp_a_2276250_f0007_oc.jpg)
Incorporating graphene-based materials into vat photopolymerised (VP) heat sinks presents several potential challenges. Achieving uniform dispersion of graphene within the polymer matrix is essential, as agglomeration can lead to uneven heat conduction [Citation24]. Optimising the filler concentration, ensuring printability and resolution, addressing cost concerns, ensuring material compatibility with VP technology, and maintaining a smooth surface finish are critical considerations for effective graphene-based VP heat sinks. Additionally, managing thermal anisotropy and ensuring consistent performance across various orientations can be challenging but is vital for efficient heat dissipation [Citation11].
6. Challenges and future perspectives
The issues associated with adding graphene to resin are numerous. The major issues are listed as follows.
Material formulation and Graphene dispersion: Achieving a homogeneous dispersion of graphene within the resin is challenging due to its hydrophobic nature and strong π-π stacking tendencies.
Photopolymerisation kinetics: Graphene's high light absorption interferes with UV light penetration, affecting curing depth and resolution. The presence of graphene may also hinder the polymerisation reaction, resulting in incomplete curing and compromised mechanical properties.
Process optimisation: Parameters such as exposure time, layer thickness, scanning speed and build orientation need optimisation to balance print speed, dimensional accuracy and material properties. Current hardware limitations, including resolution and suitable light sources, must also be addressed.
Despite these challenges, graphene nanocomposite 3D printing has numerous future research areas that need to be explored after optimising printing strategies. In addition to the challenges mentioned above, following parameters also needs to be considered.
Hardware advancements: Advancements in 3D printing hardware, including improvements in resolution and the development of suitable light sources, will contribute to the successful fabrication of high-quality graphene composites.
Multifunctional applications: Exploring the potential of graphene composites for various applications, such as electronics, energy storage, sensors and aerospace, will expand the scope of VP in 3D printing and enable the development of advanced functional materials.
Characterisation techniques: Further research is needed to develop reliable and standardised characterisation techniques to assess the properties and performance of 3D printed graphene composites accurately.
Sustainability considerations: Investigating environmentally friendly and sustainable alternatives for resin formulations and post-processing methods will contribute to the overall sustainability of the VP process for graphene composites.
By addressing these research areas, the utilisation of VP for 3D printing graphene composites can be further advanced, leading to the realisation of their full potential in various applications.
7. Conclusions
In conclusion, the marriage of Vat photopolymerisation (VP) and graphene-based materials represents a promising frontier in additive manufacturing, offering solutions to the challenges posed by the inherent limitations of 3D printed structures. The comprehensive exploration of critical parameters, from photopolymer resin selection to exposure parameters and advanced pre and post-processing techniques, has paved the way for the fabrication of high-quality graphene composites using VP. These composites, characterised by their exceptional mechanical and electrical properties, have found applications across a spectrum of industries, ranging from electronics and aerospace to biomedicine and energy storage. While this review underscores the unique advantages and remarkable potential of VP-derived graphene composites, it also recognises the challenges that must be addressed in the future. These challenges include refining printability, optimising graphene dispersion and innovating with novel hybrid materials and applications, ensuring that VP continues to drive progress and innovation in the realm of graphene-based additive manufacturing.
Acknowledgments
The authors acknowledge Sandooq Al Watan LLC for the research funding (SWARD Program—AWARD, Project code: 8434000391-EX2020-044). We also acknowledge Khalifa University for the research funding (Award No. RCII-2019-003) in support of this research.
Disclosure statement
No potential conflict of interest was reported by the author(s).
References
- Zhang F, et al. The recent development of vat photopolymerization: a review. Addit Manuf. 2021;48:102423. doi:10.1016/j.addma.2021.102423
- Binelli MR, et al. Digital manufacturing of personalised footwear with embedded sensors. Sci Rep. 2023;13(1):1962. doi:10.1038/s41598-023-29261-0
- Roohani I, Newsom E, Zreiqat H. High-resolution vat-photopolymerization of personalized bioceramic implants: new advances, regulatory hurdles, and key recommendations. Int Mater Rev. 2023:1–23. doi:10.1080/09506608.2023.2194744
- Pagac M, et al. A review of vat photopolymerization technology: materials, applications, challenges, and future trends of 3D printing. Polymers (Basel). 2021;13(4):598. doi:10.3390/polym13040598
- Quan H, Zhang T, Xu H, et al. Photo-curing 3D printing technique and its challenges. Bioactive Materials. 2020;5(1):110–115. doi:10.1016/j.bioactmat.2019.12.003
- Nekrasov N, Yakunina N, Nevolin V, et al. Two-photon polymerization of albumin hydrogel nanowires strengthened with graphene oxide. Biomimetics. 2021;6(4):66. doi:10.3390/biomimetics6040066
- Lin D, et al. 3D stereolithography printing of graphene oxide reinforced complex architectures. Nanotechnology. 2015;26(43):434003. doi:10.1088/0957-4484/26/43/434003
- Weigel N, Männel MJ, Thiele J. Flexible materials for high-resolution 3D printing of microfluidic devices with integrated droplet size regulation. ACS Appl Mater Interfaces. 2021;13(26):31086–31101. doi:10.1021/acsami.1c05547
- de León AS, de la Mata M, Delgado FJ, et al. Printable graphene oxide nanocomposites as versatile platforms for immobilization of functional biomolecules. Macromol Mater Eng. 2022;307(3):2100784. doi:10.1002/mame.202100784
- Şevik S, Çiçek B, Özdilli Ö, et al. Thermal performance analysis of aluminum, copper, and graphene nanoplatelets-doped nanocomposite heat sinks manufactured via stereolithography. Appl Therm Eng. 2023;226:120315. doi:10.1016/j.applthermaleng.2023.120315
- Schleifer SL, Regev O. Additive manufacturing of anisotropic graphene-based composites for thermal management applications. Addit Manuf. 2023;70:103567. doi:10.1016/j.addma.2023.103567
- Jeon H, Kim Y, Yu W-R, et al. Exfoliated graphene/thermoplastic elastomer nanocomposites with improved wear properties for 3D printing. Compos Part B Eng. 2020;189:107912. doi:10.1016/j.compositesb.2020.107912
- An X, Butler TW, Washington M, et al. Optical and sensing properties of 1-pyrenecarboxylic acid-functionalized graphene films laminated on polydimethylsiloxane membranes. ACS Nano. 2011;5(2):1003–1011. doi:10.1021/nn102415c
- Xu Y, et al. A graphene hybrid material covalently functionalized with porphyrin: synthesis and optical limiting property. Adv Mater. 2009;21(12):1275–1279. doi:10.1002/adma.200801617
- Wang Y, Zhou W, Cao K, et al. Architectured graphene and its composites: manufacturing and structural applications. Compos Part A Appl Sci Manuf. 2021;140:106177. doi:10.1016/j.compositesa.2020.106177
- Yang R, Zhou J, Yang C, et al. Recent progress in 3d printing of 2d material-based macrostructures. Adv Mater Technol. 2020;5(9):1901066. doi:10.1002/admt.201901066
- Feng Z, et al. Graphene-reinforced biodegradable resin composites for stereolithographic 3D printing of bone structure scaffolds. J Nanomater. 2019;2019:1–13. doi:10.1155/2019/9710264
- Palmieri V, Lattanzi W, Perini G, et al. 3D-printed graphene for bone reconstruction. 2D Mater. 2020;7(2):022004. doi:10.1088/2053-1583/ab6a5d
- Younes H, Kuang X, Lou D, et al. Magnetic-field-assisted DLP stereolithography for controlled production of highly aligned 3D printed polymer-Fe3O4@ graphene nanocomposites. Mater Res Bull. 2022;154:111938. doi:10.1016/j.materresbull.2022.111938
- Korhonen H, et al. Fabrication of graphene-based 3D structures by stereolithography. Phys Status Solidi (a). 2016;213(4):982–985. doi:10.1002/pssa.201532761
- Ponnamma D, Yin Y, Salim N, et al. Recent progress and multifunctional applications of 3D printed graphene nanocomposites. Compos Part B Eng. 2021;204:108493. doi:10.1016/j.compositesb.2020.108493
- Nguyen MTH, et al. Preparation and stability of PEGDA/GO conductive materials by DLP 3D printing. Electron Mater Lett. 2022;18(3):275–281. doi:10.1007/s13391-022-00338-8
- Palaganas JO, Palaganas NB, Ramos LJI, et al. 3D printing of covalent functionalized graphene oxide nanocomposite via stereolithography. ACS Appl Mater Interfaces. 2019;11(49):46034–46043. doi:10.1021/acsami.9b12071
- Rusling JF. Developing microfluidic sensing devices using 3D printing. ACS Sensors. 2018;3(3):522–526. doi:10.1021/acssensors.8b00079
- Qian C, Xiao T, Chen Y, et al. 3D printed reduced graphene oxide/elastomer resin composite with structural modulated sensitivity for flexible strain sensor. Adv Eng Mater. 2022;24(4):2101068. doi:10.1002/adem.202101068
- Kamat AM, Kottapalli AGP. 3D printed graphene-coated flexible lattice as piezoresistive pressure sensor. In: 2021 21st International Conference on Solid-State Sensors, Actuators and Microsystems (Transducers). IEEE; 2021. p. 888–891.
- Han H, Cho S. Fabrication of conducting polyacrylate resin solution with polyaniline nanofiber and graphene for conductive 3D printing application. Polymers (Basel). 2018;10(9):1003. doi:10.3390/polym10091003
- Xiao R, Ding M, Wang Y, et al. Stereolithography (SLA) 3D printing of carbon fiber-graphene oxide (CF-GO) reinforced polymer lattices. Nanotechnology. 2021;32(23):235702. doi:10.1088/1361-6528/abe825
- Miao S, et al. Stereolithographic 4D bioprinting of multiresponsive architectures for neural engineering. Adv Biosyst. 2018;2(9):1800101. doi:10.1002/adbi.201800101
- Zhu W, Harris BT, Zhang LG. Gelatin methacrylamide hydrogel with graphene nanoplatelets for neural cell-laden 3D bioprinting. In: 2016 38th Annual International Conference of the IEEE Engineering in Medicine and Biology Society (EMBC). IEEE; 2016. p. 4185–4188.
- Du J, et al. 3D printing-assisted gyroidal graphite foam for advanced supercapacitors. Chem Eng J. 2021;416:127885. doi:10.1016/j.cej.2020.127885
- Xue J, et al. Stereolithographic 3D printing-based hierarchically cellular lattices for high-performance quasi-solid supercapacitor. Nano-Micro Letters. 2019;11:1–13. doi:10.1007/s40820-018-0235-z
- Solís Pinargote NW, Smirnov A, Peretyagin N, et al. Direct ink writing technology (3d printing) of graphene-based ceramic nanocomposites: a review. Nanomaterials. 2020;10(7):1300. doi:10.3390/nano10071300
- Wang J, Liu Y, Fan Z, et al. Ink-based 3D printing technologies for graphene-based materials: a review. Adv Compos Hybrid Mater. 2019;2:1–33. doi:10.1007/s42114-018-0067-9
- Mensing JP, Lomas T, Tuantranont A. 2D and 3D printing for graphene based supercapacitors and batteries: a review. Sustainable Mater Technol. 2020;25:e00190. doi:10.1016/j.susmat.2020.e00190
- Ji A, Zhang S, Bhagia S, et al. 3D printing of biomass-derived composites: application and characterization approaches. RSC Adv. 2020;10(37):21698–21723. doi:10.1039/D0RA03620J
- Huang B, et al. Visible light 3D printing of high-resolution superelastic microlattices of poly(ethylene glycol) diacrylate/graphene oxide nanocomposites via continuous liquid interface production. Ind Eng Chem Res. 2022;61(35):13052–13062. doi:10.1021/acs.iecr.2c01696
- Fiedor P, Ortyl J. A new approach to micromachining: high-precision and innovative additive manufacturing solutions based on photopolymerization technology. Materials (Basel). 2020;13(13):2951. doi:10.3390/ma13132951
- Chiulan I, Voicu ŞI, Batalu D. The use of graphene and its derivatives for the development of polymer matrix composites by stereolithographic 3D printing. Appl Sci. 2022;12(7):3521. doi:10.3390/app12073521
- Xu J, Xing Y, Hao S. Research progress in graphene/polymer composites processing using 3D printing technology. J Mater Eng. 2018;46(7):1–11.
- Farzan A, Borandeh S, Seppälä J. Conductive polyurethane/PEGylated graphene oxide composite for 3D-printed nerve guidance conduits. Eur Polym J. 2022;167:111068. doi:10.1016/j.eurpolymj.2022.111068
- Tilve-Martinez D, et al. Graphene oxide based transparent resins for accurate 3D printing of conductive materials. Adv Funct Mater. 2023;33(21):2214954. doi:10.1002/adfm.202214954
- Markandan K, Lai CQ. Enhanced mechanical properties of 3D printed graphene-polymer composite lattices at very low graphene concentrations. Compos Part A Appl Sci Manuf. 2020;129:105726. doi:10.1016/j.compositesa.2019.105726
- Akbari-Garakani M, Mehdizadeh M. Effect of long-term service exposure on microstructure and mechanical properties of alloy 617. Mater Des. 2011;32(5):2695–2700. doi:10.1016/j.matdes.2011.01.017
- Hanon MM, Ghaly A, Zsidai L, et al. Tribological characteristics of digital light processing (DLP) 3D printed graphene/resin composite: influence of graphene presence and process settings. Mater Des. 2022;218:110718. doi:10.1016/j.matdes.2022.110718
- Kidalov S, Voznyakovskii A, Vozniakovskii A, et al. The effect of few-layer graphene on the complex of hardness, strength, and thermo physical properties of polymer composite materials produced by digital light processing (DLP) 3D printing. Materials (Basel). 2023;16(3):1157. doi:10.3390/ma16031157
- Jang S, Cho S. The effects of polyaniline nanofibers and graphene flakes on the electrical properties and mechanical properties of ABS-like resin composites obtained by DLP 3D printing. Polymers (Basel). 2023;15(14):3079. doi:10.3390/polym15143079
- Sultanov F, Daulbayev C, Bakbolat B, et al. Advances of 3D graphene and its composites in the field of microwave absorption. Adv Colloid Interface Sci. 2020;285:102281. doi:10.1016/j.cis.2020.102281
- Joo H, Cho S. Comparative studies on polyurethane composites filled with polyaniline and graphene for DLP-type 3D printing. Polymers (Basel). 2020;12(1):67. doi:10.3390/polym12010067
- Hanon MM, Ghaly A, Zsidai L, et al. Investigations of the mechanical properties of DLP 3D printed graphene/resin composites. Acta Polytech Hung. 2021;18(8):143–161. doi:10.12700/APH.18.8.2021.8.8
- Schmidleithner C, Kalaskar DM. Stereolithography. London: IntechOpen; 2018.
- Bagheri A, Jin J. Photopolymerization in 3D printing. ACS Appl Polym Mater. 2019;1(4):593–611. doi:10.1021/acsapm.8b00165
- Lee J-Y, et al. The potential to enhance membrane module design with 3D printing technology. J Membr Sci. 2016;499:480–490. doi:10.1016/j.memsci.2015.11.008
- Balli J, Kumpaty S, Anewenter V. Continuous liquid interface production of 3D objects: An unconventional technology and its challenges and opportunities. In: ASME International Mechanical Engineering Congress and Exposition, vol. 58400. American Society of Mechanical Engineers; 2017, p. V005T06A038.
- Zhang G, et al. Electrically assisted continuous vat photopolymerization 3D printing for fabricating high-performance ordered graphene/polymer composites. Compos Part B Eng. 2023;250:110449. doi:10.1016/j.compositesb.2022.110449
- Nair PNS, et al. Fabrication of opaque and transparent 3D structures using a single material via two-photon polymerisation lithography. Light: Adv Manuf. 2023;4(2):1–8. doi:10.37188/lam.2023.025
- Niesler F, Hermatschweiler M. Two-photon polymerization—a versatile microfabrication tool: from maskless lithography to 3D printing. Laser Tech J. 2015;12(3):44–47. doi:10.1002/latj.201500019
- Xing J-F, Zheng M-L, Duan X-M. Two-photon polymerization microfabrication of hydrogels: an advanced 3D printing technology for tissue engineering and drug delivery. Chem Soc Rev. 2015;44(15):5031–5039. doi:10.1039/C5CS00278H
- McLennan HJ, et al. Nano-liter perfusion microfluidic device made entirely by two-photon polymerization for dynamic cell culture with easy cell recovery. Sci Rep. 2023;13(1):562. doi:10.1038/s41598-023-27660-x
- Gómez IJ, Alegret N, Dominguez-Alfaro A, et al. Recent advances on 2D materials towards 3D printing. Chemistry. 2021;3(4):1314–1343. doi:10.3390/chemistry3040095
- Ferrari AC, et al. Raman spectrum of graphene and graphene layers. Phys Rev Lett. 2006;97(18):187401. doi:10.1103/PhysRevLett.97.187401
- Liu M, Zhang R, Chen W. Graphene-supported nanoelectrocatalysts for fuel cells: synthesis, properties, and applications. Chem Rev. 2014;114(10):5117–5160. doi:10.1021/cr400523y
- Sontakke AD, Tiwari S, Purkait MK. A comprehensive review on graphene oxide-based nanocarriers: synthesis, functionalization and biomedical applications. FlatChem. 2023;38:100484. doi:10.1016/j.flatc.2023.100484
- Tiwari SK, Mishra RK, Ha SK, et al. Evolution of graphene oxide and graphene: from imagination to industrialization. ChemNanoMat. 2018;4(7):598–620. doi:10.1002/cnma.201800089
- Coleman JN, et al. Two-dimensional nanosheets produced by liquid exfoliation of layered materials. Science. 2011;331(6017):568–571. doi:10.1126/science.1194975
- Jacob L, V PK, S MR, et al. Binary Cu/ZnO decorated graphene nanocomposites as an efficient anode for lithium ion batteries. J Ind Eng Chem. 2018;59:108–114. doi:10.1016/j.jiec.2017.10.012
- de Armentia SL, Fernández-Villamarín S, Ballesteros Y, et al. 3D printing of a graphene-modified photopolymer using stereolithography for biomedical applications: A study of the polymerization reaction. Int J Bioprinting. 2022;8(1):182–197.
- Sarno M, Scarpa D, Senatore A, et al. rGO/GO nanosheets in tribology: from the state of the art to the future prospective. Lubricants. 2020;8(3):31. doi:10.3390/lubricants8030031
- Ramírez-Soria E-H, et al. On the effect of ultralow loading of microwave-assisted bifunctionalized graphene oxide in stereolithographic 3D-printed nanocomposites. ACS Appl Mater Interfaces. 2020;12(43):49061–49072. doi:10.1021/acsami.0c13702
- Lim S, Shin B, Kim K. Characterization of products using additive manufacturing with graphene/photopolymer-resin nano-fluid. J Nanosci Nanotechnol. 2017;17(8):5492–5495. doi:10.1166/jnn.2017.14159
- Zhang Y, Tang S, Deng D, et al. Growth direction manipulation of few-layer graphene in the vertical plane with parallel arrangement. Carbon N Y. 2013;56:103–108. doi:10.1016/j.carbon.2012.12.078
- Harnden R, Zenkert D, Lindbergh G. Potassium-insertion in polyacrylonitrile-based carbon fibres for multifunctional energy storage, morphing, and strain-sensing. Carbon N Y. 2021;171:671–680. doi:10.1016/j.carbon.2020.09.042
- Quanchao G, Sun L, Xiaoyu J, et al. High-performance and high-precision Al2O3 architectures enabled by high-solid-loading, graphene-containing slurries for top-down DLP 3D printing. J Eur Ceram Soc. 2023;43(1):130–142. doi:10.1016/j.jeurceramsoc.2022.09.048
- Guo Z, et al. 3D-printed electrically conductive silicon carbide. Addit Manuf. 2022;59:103109. doi:10.1016/j.addma.2022.103109
- Shin CS, Chang YC. Fabrication and compressive behavior of a micro-lattice composite by high resolution DLP stereolithography. Polymers (Basel). 2021;13(5):785. doi:10.3390/polym13050785
- Zhou W, Fan Y, Feng X, et al. Creation of individual few-layer graphene incorporated in an aluminum matrix. Compos Part A Appl Sci Manuf. 2018;112:168–177. doi:10.1016/j.compositesa.2018.06.008
- Ege D, Kamali AR, Boccaccini AR. Graphene oxide/polymer-based biomaterials. Adv Eng Mater. 2017;19(12):1700627. doi:10.1002/adem.201700627
- Hensleigh RM, et al. Additive manufacturing of complex micro-architected graphene aerogels. Mater Horiz. 2018;5(6):1035–1041. doi:10.1039/C8MH00668G
- Ibrahim F, Mohan D, Sajab MS, et al. Evaluation of the compatibility of organosolv lignin-graphene nanoplatelets with photo-curable polyurethane in stereolithography 3D printing. Polymers (Basel). 2019;11(10):1544. doi:10.3390/polym11101544
- Manapat JZ, Mangadlao JD, Tiu BDB, et al. High-strength stereolithographic 3D printed nanocomposites: graphene oxide metastability. ACS Appl Mater Interfaces. 2017;9(11):10085–10093. doi:10.1021/acsami.6b16174
- Zhang Q, Zhang F, Xu X, et al. Three-dimensional printing hollow polymer template-mediated graphene lattices with tailorable architectures and multifunctional properties. ACS Nano. 2018;12(2):1096–1106. doi:10.1021/acsnano.7b06095
- Zuo Y, Yao Z, Lin H, et al. Digital light processing 3D printing of graphene/carbonyl iron/polymethyl methacrylate nanocomposites for efficient microwave absorption. Compos Part B Eng. 2019;179:107533. doi:10.1016/j.compositesb.2019.107533
- Guo B, et al. Highly flexible, thermally stable, and static dissipative nanocomposite with reduced functionalized graphene oxide processed through 3D printing. Compos Part B Eng. 2021;208:108598. doi:10.1016/j.compositesb.2020.108598
- Wu Y, et al. Sustainable 3D printing of recyclable biocomposite empowered by flash graphene. ACS Nano. 2022;16(10):17326–17335. doi:10.1021/acsnano.2c08157
- Li J, et al. Synthesis and characterization of reinforced acrylate photosensitive resin by 2-hydroxyethyl methacrylate-functionalized graphene nanosheets for 3D printing. J Mater Sci. 2018;53:1874–1886. doi:10.1007/s10853-017-1432-8
- De León AS, Molina SI. Influence of the degree of cure in the bulk properties of graphite nanoplatelets nanocomposites printed via stereolithography. Polymers (Basel). 2020;12(5):1103. doi:10.3390/polym12051103
- Park D, Kim Y, Lee S, et al. Selectively distributed graphene in 1, 6-hexanediol diacrylate/epoxy composites via digital light processing 3D printing for enhanced thermal conductivity. Synth Met. 2021;276:116763. doi:10.1016/j.synthmet.2021.116763
- Feng Z, Li Y, Xin C, et al. Fabrication of graphene-reinforced nanocomposites with improved fracture toughness in net shape for complex 3D structures via digital light processing. C – J Carbon Res. 2019;5(2):25. doi:10.3390/c5020025
- Zhou S, et al. A scalable, eco-friendly, and ultrafast solar steam generator fabricated using evolutional 3D printing. J Mater Chem A. 2021;9(15):9909–9917. doi:10.1039/D1TA00674F
- Lai CQ, Markandan K, Luo B, et al. Viscoelastic and high strain rate response of anisotropic graphene-polymer nanocomposites fabricated with stereolithographic 3D printing. Addit Manuf. 2021;37:101721. doi:10.1016/j.addma.2020.101721
- Zhou X, et al. 3D bioprinted graphene oxide-incorporated matrix for promoting chondrogenic differentiation of human bone marrow mesenchymal stem cells. Carbon N Y. 2017;116:615–624. doi:10.1016/j.carbon.2017.02.049
- Tsang CHA, Zhakeyev A, Leung DY, et al. GO-modified flexible polymer nanocomposites fabricated via 3D stereolithography. Front Chem Sci Eng. 2019;13:736–743. doi:10.1007/s11705-019-1836-x
- Valentin TM, et al. Alginate-graphene oxide hydrogels with enhanced ionic tunability and chemomechanical stability for light-directed 3D printing. Carbon N Y. 2019;143:447–456. doi:10.1016/j.carbon.2018.11.006
- Markandan K, Seetoh IP, Lai CQ. Mechanical anisotropy of graphene nanocomposites induced by graphene alignment during stereolithography 3D printing. J Mater Res. 2021;36:4262–4274. doi:10.1557/s43578-021-00400-5
- Du J, Fu G, Xu X, et al. “3d printed graphene-based metamaterials: guesting multi-functionality in one gain,” (in eng). Small. May 2023;19(19):e2207833. doi:10.1002/smll.202207833
- Angulo-Pineda C, Srirussamee K, Palma P, et al. Electroactive 3D printed scaffolds based on percolated composites of polycaprolactone with thermally reduced graphene oxide for antibacterial and tissue engineering applications. Nanomaterials. 2020;10(3):428. doi:10.3390/nano10030428
- Gulzar U, Glynn C, O'Dwyer C. Additive manufacturing for energy storage: methods, designs and material selection for customizable 3D printed batteries and supercapacitors. Curr Opin Electrochem. 2020;20:46–53. doi:10.1016/j.coelec.2020.02.009
- Wu X, Mu F, Lin Z. Three-dimensional printing of graphene-based materials and the application in energy storage. Mater Today Adv. 2021;11:100157. doi:10.1016/j.mtadv.2021.100157
- Sang Tran T, Dutta NK, Roy Choudhury N. Graphene-based inks for printing of planar micro-supercapacitors: a review. Materials (Basel). 2019;12(6):978. doi:10.3390/ma12060978
- Fu K, et al. Graphene oxide-based electrode inks for 3D-printed lithium-ion batteries. Adv Mater. 2016;28(13):2587–2594. doi:10.1002/adma.201505391