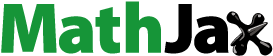
ABSTRACT
Based on the principle of local resonance and the strategy of hybrid design, in this paper we propose three truss-plate hybrid multifunctional lattice metamaterials featured by the cubic cell topology with a central truss-plate unit connected by the elastic beams to the eight corners. Finite element (FE) simulations were validated by experimental tests on specimens made of TPU substrate material through SLS additive manufacturing technique. At the relative density of 0.31, the specific energy absorption reaches 2.71 J/g, the bandgap width reaches 2.624 KHz, and the elastic wave transmission attenuation at 1400 Hz frequency reaches – 270 dB. Parametric analyses were carried out to investigate the effects of different geometric parameters on the performance indicators. These results highlight the proposed truss-plate hybrid metamaterial as an intriguing multifunctional material with excellent performances in both energy absorption and vibration attenuation, that can be applied to scenarios with multiple engineering requirements.
1. Introduction
In order to protect human head and body regions from heavy impacts, various protective devices such as helmets, bulletproof vests and knee pads have been invented [Citation1–3]. The outer shell of these protective devices is featured with high stiffness and damage tolerance, which prevent the piercing of external sharp objects that can cause injuries to the human body, and the internal liner serves as a cushioning and energy absorption function [Citation4]. Most of the existing liners utilise the extensive plastic deformation of foam material [Citation5], which has the disadvantages of heavy weight, less designability and considerable scattering in the mechanical properties.
As an artificially designed periodic porous structure [Citation6] with load-bearing and energy-absorption capacities beyond those of conventional materials, lattice metamaterials are widely used in various fields, such as aerospace [Citation7], rail transportation [Citation8], biomedical [Citation9], and submarine [Citation10]. There are a number of researches devoted to the investigation of their mechanical properties such as energy absorption. Wang et al [Citation11] prepared the plate lattice metamaterials with semi-open holes by selective laser melting (SLM) technique. Numerical simulations and experimental results show that the specific energy absorption (SEA) of the semi-open-hole plate lattice metamaterial is two times as high as that of the truss lattice metamaterial. Liu et al [Citation12] designed a novel 3D lattice structure based on synergistic mechanisms of gradient and hybrid reinforcements. It was experimentally verified that the energy dissipation induced by the synergistic mechanisms featured by the Z-shaped shear bands is larger than that induced by the conventional single reinforcement mechanism. Li et al [Citation13] proposed a synthetic bionic lattice structure (SBLS) with variable cross-section, and achieved better energy absorption performance compared with the conventional fixed cross-section lattice. Alkhatib et al [Citation14] investigated the energy absorption of 3D-printed titanium-based lattice structures with optimised isotropic topology under quasi-static compression. The optimised lattice exhibits a stretching-bending mixed deformation pattern, showing near-perfect SEA isotropy.
With the fast development of various metamaterials, architecting novel protective devices with multiple functions has become an intriguing topic. For instance, the elastic waves generated by the explosion can pass around the protectee through the external protective devices to avoid acting directly on the fragile protectee. The current vibration attenuation structures mainly resort to the mechanisms used in the phononic crystals [Citation15–17] and acoustic metamaterials [Citation18–20] to effectively modulate the elastic waves, which are based on the Bragg scattering mechanism and local resonance mechanism, respectively. Kudela et al [Citation21] proposed a new topology optimisation method of phononic crystals using the non-uniform rational basis spline (NURBS) curves instead of pixel grids to control the cell shape of the phononic crystals. Ding et al [Citation22] carried out an experimental study of chiral phononic crystals without mirror symmetry similar to Thomson scattering, and achieved 66% lower bandgap initiation frequency than that of conventional phononic crystals. Tao et al [Citation23] proposed an acoustic metamaterial plate based on a negative Poisson's ratio structure, which allows for lower attenuation frequencies, wider bandgaps, and larger adjustability compared with the conventional porous plates. Zhang et al [Citation24] designed a lightweight acoustic metamaterial for low-frequency noise and vibration control based on multi-parameter optimisation. The weight of the optimised structure can be reduced by 60.7% and the overall radiated transmission loss can reach 3.9 dB.
It is noted that most existing phononic crystals and acoustic metamaterials have poor performances in load-bearing capacity and cushioning energy absorption, which is not desirable for the development of multi-function integrated protective devices. From the extensive researches in the literature, lattice metamaterials have been reported to possess various peculiar properties such as negative Poisson's ratio [Citation25–27], negative coefficient of thermal expansion [Citation28–30], negative stiffness [Citation31–33], and high acoustic absorption [Citation34–36], in addition to their excellent mechanical properties. There have been several studies on the combination of the mechanical properties and vibration attenuation properties of the lattice materials. An et al [Citation37] proposed a novel three-dimensional lattice structure composed of chiral microstructures, where the chirality is introduced by slotting on the line of the plate lattice structure of the high load-bearing property to achieve broadband vibration attenuation. Li et al [Citation38] proposed meta-lattice sandwich plates composed of a single/double-layer conical truss core, and investigated their vibration suppression performance and bandgap generation mechanism through theoretical, numerical and experimental approaches. Fan et al [Citation39] proposed a 3D stretching-dominated truss lattice structure to effectively regulate the band gap and load-carrying capacity, by increasing the cross-section of the cell's outer frame. Zhang et al [Citation40] proposed a new lattice structure consisting of a hollow rhombic dodecahedron and six cylindrical tubes, and obtained multi-function integration of better vibration isolation and higher collision resistance through multi-objective optimisation.
At this stage, multifunctional lattice metamaterials are mainly processed and manufactured by additive manufacturing technologies such as SLA and SLS [Citation41, Citation42]. Compared with SLA technology, SLS technology is less dependent on the introduction of supports, and is thus chosen for printing the lattice metamaterials containing a large number of overhanging components in this work. A disadvantage of the SLS technique is the necessity of removing the residual powders. Therefore, holes of sufficient size are often introduced to the plate or shell based lattice materials for powder clearance. The current lattice metamaterial designs for both mechanical and vibration attenuation performances still have limitations in terms of excessive cell size, poor energy absorption, high bandgap frequency and narrow bandgap width. To overcome these limitations of traditional lattice metamaterials, in this paper we propose three designs of truss-plate multifunctional lattice metamaterials based on the local resonance principle and the hybrid design strategy. The vibration attenuation and energy absorption performances of the proposed truss-plate hybrid lattice metamaterials are investigated through numerical simulations and experimental tests, with further discussions given on their multifunctionality.
2. Design strategy and sample fabrication
2.1. Design strategies for lattice metamaterials
Conventional lattice metamaterials can be classified into stretching-dominated and bending-dominated classes according to their different stress responses. Relevant studies have shown [Citation43] that the truss-plate hybrid lattice metamaterials are superior to the single truss or plate lattice metamaterials in terms of energy absorption and load-bearing capacities. The deformation mode changes from the conventional layer-by-layer collapse to the X-shaped shear band collapse, with a high and stable plateau stress response.
Although much attention has been paid to the energy absorption property and considerable improvement has been reported for the truss-plate hybrid lattices, their elastic wave attenuation performances are rarely investigated. Therefore, in this paper, three new kinds of truss-plate hybrid lattice metamaterials are proposed to incorporate the elastic wave attenuation capability based on the local resonance mechanism. The design strategy of the lattice cell is shown in . The central node of the body-centered cubic (BCC) truss lattice is replaced with a truss-plate unit hybridised by the SC plate cell and one conventional truss cell among BCC, face-centered cubic (FCC) and simple cubic (SC) topologies, rendering the truss-plate hybrid lattice denoted as body–body-centered cubic truss plate (BBTP), face-body-centered cubic truss plate (FBTP) and simple-body-centered cubic truss plate (SBTP), respectively. The design of the new lattices is featured by the aggregated mass of the central unit connected by the elastic beams to the eight corners of the cell. According to the local resonance theorem, this lattice metamaterial design strategy is beneficial for the improvement of the vibration attenuation capability. At the same time, the stress-strain curve in the compression process shows a secondary plateau character, which further improves the cushioning and energy-absorbing effect of the lattice metamaterial. To facilitate the internal powder cleaning during the additive manufacturing process, hole openings are introduced to the plate panels at the centre or along the coordinate axes. The geometries of the three truss-plate lattice metamaterials are shown in . The following geometric parameters are included: outer strut diameter dout, inner strut diameter din, aperture size dp, plate thickness t, and single-cell size L.
2.2. Specimen fabrication
Considering the processing accuracy, processing cost and material properties, the lattice specimens were fabricated by the selective laser sintering (SLS) additive manufacturing technique using TPU as the substrate material for its low cost and excellent mechanical performances such as high strength, high toughness and wear resistance. First, the specimen model was created by the 3D software Solidworks. Then, the model was exported in STL format and imported into a 3D printer (TPM3D P360). Next, the specimen was printed layer-by-layer by scanning the 2D profiles of its model in the 3D printer. And finally, the specimen is treated by powder cleaning and other post-processing treatments. The tensile specimens were printed with the width direction oriented upwards. The main printing parameters include the effective scanning space of 350 × 350 × 590 mm, the laser power of 60 W, the layer thickness of 0.12 mm, the forming speed of 15 m/h, the maximum scanning speed of 15,000 mm/s, the focused spot diameter of 0.25 mm, and the maximum operating temperature of 230 °C on the powder bed.
To evaluate the printing quality of the specimens, a digital microscope (Dino-Lite Premier AM4113ZT) was used to examine the printed specimens. The obtained microscope images of specimens of the three lattice metamaterials are shown in , with the images in the middle showing the overall views and those at the top and bottom showing the enlarged views. From , it can be seen that the overall printing quality is satisfactory, with no obvious defects such as breakage of struts or fracture of plates observed. The enlarged images clearly show the fine particles adhered to the surface after sintering, rendering an intermediate and uniform surface roughness. The satisfactory printing quality lays the foundation for later validation tests on mechanical and vibration attenuation properties.
3. Validation of FE model through experimental tests
3.1. Vibration attenuation validation
The constitutive parameters of the TPU substrate material need to be determined before the compression tests. Three dog-bone tensile specimens were printed and tested for this purpose. As shown in (a), the tensile tests were carried out by an electronic testing machine, and the nominal stress-strain curves shown in (b) were obtained from the force and displacement recorded during the tests. The curves of the three tensile specimens are generally consistent with each other, indicating satisfactory repeatability. The TPU substrate material has density ρs of 1.10 g/cm3, elastic modulus E of 50 MPa, and Poisson's ratio v of 0.47. To analyze the bandgap properties and vibration modes of the truss-plate lattice metamaterials, the single-cell structure was numerically analyzed by means of FE software COMSOL Multiphysics. The equation of elastic wave propagation in an isotropic medium can be expressed as.
(1)
(1) where, λ and μ are Lamé constants, u is the displacement vector, ρ is the density, and ω is the angular frequency. According to Bloch's theory, the displacement solution of the fluctuation equation for an elastic wave propagating in a structure with periodicity satisfies
(2)
(2) where Rn is the position vector, k is the wave vector, and uk(r) is a vector function with the same periodicity as the lattice structure. The bloch-floquet boundary conditions can be set for each couple of opposite sides of the single-cell model in the FE simulations. The eigenvalue equation of the single-cell model of lattice metamaterial after discretization is
(3)
(3) where K is the stiffness matrix, M is the mass matrix, and U is the displacement array. The boundary of the first irreducible Brillouin zone is scanned by the wave vector k as shown in (c). Solving the single-cell eigenvalue equation, the dispersion relation curves of the lattice metamaterial are finally obtained.
Figure 4. (a) Tensile test on the dog-bone specimen, (b) Stress-strain curves of three tensile tests, (c) First irreducible Brillouin zone of the lattice metamaterials.
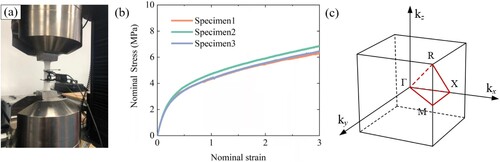
Examining the dispersion relation between the frequency and the wave vector, it is convenient to identify the bandgap characteristics of lattice metamaterials, which are however difficult to verify by experiments. Therefore, the elastic wave propagation characteristics in lattice metamaterials are investigated, and the FE numerical simulations are combined with the vibration attenuation experiments to further verify the vibration attenuation effect. shows the experimental setup for the attenuation tests which is composed of a shaker, two accelerometers, a power amplifier and a PC system. The shaker vibration attenuation test is performed according to the GB/T 11349.3-2006 standard. The test is mainly implemented by generating a harmonic excitation signal through the computer. The signal is transmitted to the shaker through the power amplifier and then the shaker starts working according to the operating frequency. One accelerometer is installed at the input end along with the shaker actuator strut, and the other accelerometer is installed at the output end. The transmission spectrum for evaluating the attenuation performance is calculated from the input and output signals.
(4)
(4) Where Aout is the amplitude of the vibration signal at the output end and Ain is the amplitude at the input end. The truss-plate hybrid lattice metamaterial specimen is composed of a 2 × 2 × 6 periodic array of cells. The same geometric parameters and the same loading conditions are adopted for the numerical simulations, to impartially compare the numerical simulation results with the experimental test results.
Figure 5. Vibration attenuation tests on the lattice metamaterial specimen: (a) Loading scenario, (b) power amplifier, (c) accelerometer, (d) PC system.
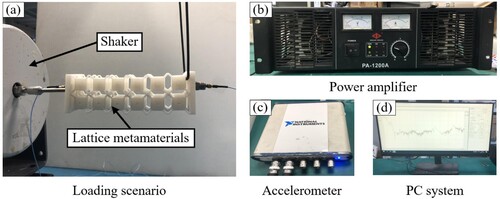
The geometric parameters of the three truss-plate lattice specimens for the vibration attenuation tests are shown in . The designed weights and measured weights are compared for each design of the truss-plate hybrid lattice metamaterials in . Satisfactory printing accuracy is achieved as shown by the small relative error of the weight of the printed specimens (maximum 5.6%). The obtained bandgap characteristics are shown in (a), (c), and (d) for the three metamaterials, respectively. The normalised frequencies are used here and hereafter, which are defined as fn = fL/ct, where f is the original frequency, L is the size of the lattice cell, ct = (E/2ρs(1 + v))1/2 is the transverse wave velocity of the substrate material, and E and v are its Young’s modulus and Poisson ratio. The normalised frequency can better demonstrate the local resonance characteristics of the proposed hybrid lattices that utilise the periodic cells of sub-wavelength dimensions to attenuate the waves, i.e. fn < 1. In these graphs, the blue curves in these graphs are the dispersion curve, while the green region indicates the complete bandgap frequency range, at which the elastic wave propagation is fully prohibited. It can be seen that the bandgap always takes place between the 6th-order eigenfrequency and the 7th-order eigenfrequency. The insets in the red boxes of (a), (c), and (d) show the vibrational modes of the three truss-plate lattice metamaterials at the upper and lower bandgap boundaries, with the colour contours indicating the magnitude of the displacement field. The vibrational modes exhibit distinct local resonance characteristics. As shown in (a), the vibration mode of BBTP at the lower boundary of the frequency bandgap mainly depends on the lateral resonance of the central resonator. The vibration mode at the upper boundary of the frequency bandgap mainly depends on the bending vibration of the surrounding connecting beams. Similar resonance characteristics are also observed for FBTP and SBTP.
Figure 6. (a) Bandgap and vibration modes, and (b) simulated and experimental curves of elastic wave transmission for BBTP lattice metamaterial, (c) and (d) are for FBTP lattice metamaterial, and (e) and (f) are for SBTP.
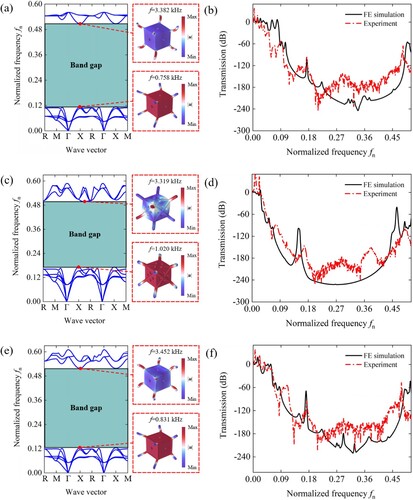
Table 1. Geometric parameters of three truss-plate lattice specimens for vibration attenuation tests.
(b), (d), and (f) compare the elastic wave transmission spectra from the FE simulations with those from the experiments for the three truss-plate lattice metamaterials, respectively, and demonstrate satisfactory agreement between numerical results and experimental results. In addition, the frequency ranges with evident elastic wave attenuation in (b), (d), and (f) are consistent with the bandgaps in (a), (c), and (d). These results provide validation for our FE numerical models. Comparing the vibration attenuation performance between the three truss-plate lattice metamaterials at the same relative density, BBTP has the best performance, with bandwidth as large as 2.624 kHz, and elastic wave transmission loss as low as – 270 dB at 1400 Hz. It indicates that BBTP has better elastic wave attenuation ability and a wider attenuation range than the other two.
According to the vibration pattern of the lattice metamaterial at the frequency within the bandgap, we established an equivalent analytical model of the truss-plate lattices using the mass-spring system. Through the equivalent analytical model, the mechanism of bandgap formation can be further explored. The unit cell of the lattice can be represented by the mass-spring system composed of the concentrated mass representing the truss-plate central block and the spring representing the eight beams connected to the eight corners of the cell. The central mass m is obtained from the components of the central block, and the equivalent stiffness of the outer spring k is determined from the tensile and shear deformations of the outer struts during vibration as follows,
(5)
(5) where λ and μ are Lame's constants, α and β are constant coefficients, and Ae and le are the cross-sectional area and the length of the outer struts, respectively. The natural frequency of the mass-spring system can be expressed as
(6)
(6) The analytical and numerical results of the lower-bound frequency of BBTP bandgap under different outer strut diameters are presented in . The relative error between the analytically predicted results and the numerically obtained results is small. With the increase of the outer strut diameter, both the analytical and numerical models predict the increase tendency of the bandgap lower-bound frequency, which can be explained by the increase of the stiffness of the spring in the equivalent mass-spring system. The analytical model can well illustrate the mechanism of the bandgap formation.
Table 2. Lower-bound frequency of BBTP bandgap obtained from numerical of analytical approaches for different outer strut diameters.
3.2. Quasi-static compression validation
In this section, the quasi-static compression tests for the printed lattice specimens were carried out using a 5t electronic universal testing machine (WDW-50), to investigate the mechanical performance of the three truss-plate hybrid lattice metamaterials under compression. The dimensions of the compression specimens are 60 × 60 × 60 mm. The compression tests follow the standard ASTM D638-14. During the tests, the specimens were placed between two rigid plates, with the lower plate fixed, and the upper plate moving downward at a speed of 2 mm/min to compress the specimen. The force-displacement data were recorded through sensors and stored in the computer system, and the deformation patterns during the compression were shot by a camera. The geometric parameters of the three truss-plate lattice metamaterial specimens for the compression tests are listed in . Similar to the results in , satisfactory printing accuracy is achieved as shown by the small relative error of the weight of the printed specimens (maximum 4.6%). The relative weight deviations of the two compression specimens for each lattice design are also added in . The deviations are negligible, indicating satisfactory repeatability of the printed specimens.
Table 3. Geometric parameters of the three lattice specimens for quasi-static compression tests.
The quasi-static compression simulations were performed using the commercial FE software ABAQUS. The first-order Ogden hyperelastic model was used as the constitutive model of the substrate material TPU, with the nominal stress-strain data obtained from the tensile tests. The hard contact algorithm was used to model the contact along the normal direction to prevent penetration, and the penalty algorithm with a friction coefficient of 0.3 was used for the tangential direction. The upper and lower plates are modelled as discrete rigid bodies. The loading speed was chosen as 2 mm/min so that the kinetic energy does not exceed 5% of the internal energy and the quasi-static compression condition is guaranteed ().
Figure 7. Quasi-static compression experiments and corresponding FE simulations on SBTP lattice metamaterials.
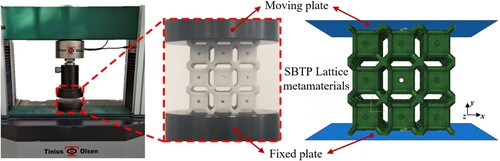
The stress responses from the compression FE simulations are compared with those form the experiments to verify the accuracy of the FE simulation results. (a)-(f) shows the stress-strain curves and the deformation modes for the three kinds of lattice metamaterials. The stress responses from the numerical simulations and the experiments are consistent with each other, both can be divided into four stages. The first stage is the elastic stage, with all components in the specimen deformed elastically, with larger stress in the outer struts near the nodes as shown in the snapshot of 0.1 strain on the right side hand of . The second stage is the transition stage featured by the bending of the outer struts near the nodes, corresponding to the snapshot at the strain of 0.3 on the right-hand side. A significant stress concentration can be observed near the junctions of the oblique struts and vertical plates. The third stage is the plateau stage, during which the central truss-plate hybrid unit undergoes overall elastic buckling. The stresses are mainly concentrated at the plate junctions on both sides of the plates. The fourth stage is the densification stage corresponding to the collapse of the whole structure.
Figure 8. Comparison of the compression performances between the FE simulations and the experiments for (a-b) BBTP, (c-d) FBTP, and (e-f) SBTP lattice metamaterials, with the left subfigures (a), (c) and (e) showing the stress-strain curves and SEA, and the right subfigures (b), (d) and (f) showing the deformation modes.
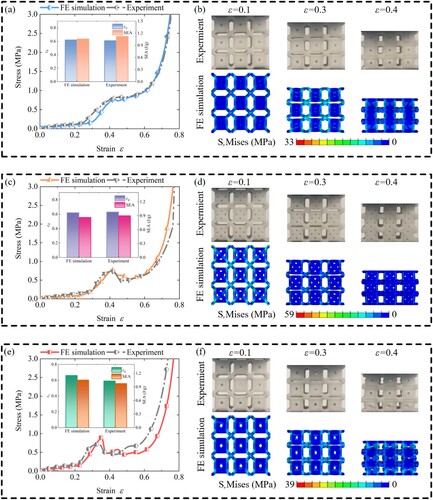
The consistency between the FE numerical and experimental results in terms of the stress-strain curves and deformation modes provides validation for the quasi-static compression simulations. Next, quantitative comparisons between the numerical simulations and the experiments were conducted through the indicators of the energy absorption performance, including the specific energy absorption (SEA) and the densification strain ϵd. SEA is defined as the energy absorption capacity per unit mass, calculated by the following equation
(7)
(7) where ρr is the relative density and ρs is the density of the substrate material. On the other hand, ϵd is determined by the maximum point of the curve of the energy absorption efficiency (EAE), which is defined as
(8)
(8) where
is the maximum stress up the strain ϵ. The numerically and experimentally obtained SEA and ϵd results are shown in (a), (c), and (e) for the three lattice metamaterials, respectively. The maximum relative errors between the FE numerical and experimental results for ϵd and SEA do not exceed 10% and 8%, respectively. The accuracy of the FE numerical models for quasi-static compression is again validated.
Comparing the energy absorption performances of the three metamaterials, it can be seen that BBTP exhibits the highest SEA, which is 25% higher compared to FBTP. From the stress-strain curves, the densification strains of the three lattice metamaterials are similar, while BBTP has a much smoother stress response in the plateau stage than FBTP and SBTP, for which the stress-strain curves take on a significant initial peak, followed by a rapid drop. It is illustrated that the hybrid design combining the stretching-dominated SC plates and the bending-dominated BCC trusses effectively improves the mechanical properties of the lattice structures. It also endows the BBTP lattice metamaterials with enhanced energy absorption capacity which can be used as cushioning and energy absorption components in engineering applications.
Since the vibration attenuation properties of the three truss-plate hybrid lattice metamaterials are all based on the local resonance principle, their bandgap characteristic is generally similar. Among the three metamaterials, BBTP has the best vibration attenuation and energy absorption performance. Therefore, for the parametric studies in the subsequent sections, BBTP lattice metamaterials are taken as the investigation objects.
4. Results of parametric study
4.1. Single parameter analysis
In this and subsequent sections, parametric studies are carried out to investigate the effects of various geometric parameters on the vibration attenuation and energy absorption performances of the BBTP metamaterial using the FE numerical simulations. For this purpose, a benchmark case is selected with the inner strut diameter din = 2 mm, outer strut diameter dout = 2.5 mm, and plate thickness t = 2.5 mm. Each time one parameter is varied with other parameters fixed as the benchmark values to investigate the effect of that parameter.
4.1.1. Influence of strut diameter
Firstly, attention is paid to the influence of the strut diameter. (a)-(b) show the vibration attenuation and energy absorption properties of BBTP lattice metamaterials with different inner and outer strut diameters, for which the inner strut diameter varies in the range of 1–3 mm and the outer strut diameter varies in the range of 2–3 mm. To demonstrate the effect of various parameters on the bandgap width more clearly, we define the variable of normalised bandwidth as.
(9)
(9) where fl is the bandgap upper bound frequency and fu is the bandgap lower bound frequency. (c)-(d) shows the variation of frequencies of the bandgap and energy absorption indicators with different outer strut diameters. It can be seen that the upper bound frequency is almost unaffected by the outer strut diameter, and the lower bound frequency increases gradually with the increase of the outer strut diameter, rendering a decreased trend of bandwidth with the increase of outer strut diameter. It indicates that a slender outer strut is more desirable for BBTP to regulate towards the low-frequency broadband. There is no significant change in densification strain and SEA with increasing the outer strut diameter. It indicates that the plastic dissipation of BBTP is not significantly affected by the outer strut diameter.
Figure 9. Parametric study for the influence of strut diameter on BBTP performances, (a-b) model geometry with the variation of (a) the inner and (b) the outer strut diameter, (c-d) influence of outer strut diameter on the bandgap and energy absorption characteristics, (e-f) influence of inter strut diameter on the bandgap and energy absorption characteristics.
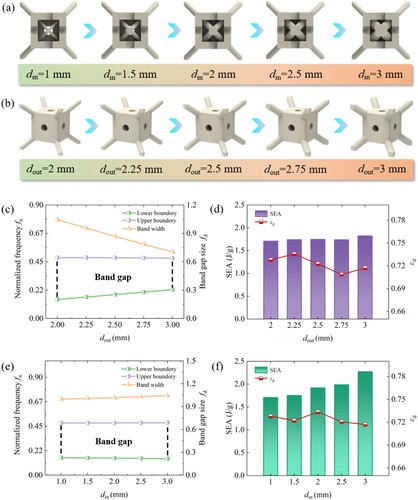
(e-f) shows the variation of the bandgap and energy absorption of BBTP with different inner strut diameters. The upper and lower bounds of the frequency band change little with the variation of the inner strut diameter, with normalised bandwidth between 0.9 and 1. It indicates that the variation of the inner strut diameter has less effect on the modes of the local resonance. From (f), the densification strain decreases gradually with the increase of the inner strut diameter. As the inner strut diameter increases, the space between the inner struts and the plates becomes smaller, leading to the advancement of the densification point. At the same time, the increase in the inner strut diameter strengthens the deformation resistance of the inner struts, leading to the enhancement of SEA.
4.1.2. Influence of plate thickness
Besides the strut diameter, the plate thickness is also an important geometric parameter that may affect the performances of the truss-plate hybrid lattice metamaterials. The cell geometries of BBTP with different plate thicknesses ranging between 2 mm and 3 mm are shown in (a). (b) shows the results of the bandgap characteristics, where the lower bound frequency gradually decreases and the upper bound frequency gradually increases as the plate thickness increases, rendering the gradual increase of the bandwidth with the plate thickness. This indicates that the increase in plate thickness is favourable for the realisation of low-frequency broadband. As the plate thickness increases, the agglomerate mass of the central strut-plate unit increases, which can effectively strengthen the local resonance mechanism of the structure.
Figure 10. Parametric study for the influence of plate thickness on BBTP performances, (a) model geometry with different plate thicknesses, (b-c) influence of plate thickness on (b) the bandgap characteristics, and (c) the energy absorption characteristics.

(c) shows the densification strain and SEA of BBTP for different plate thicknesses. As the thickness increases, the internal cavity of the strut-plate unit gradually decreases and the densification point is gradually advanced. On the other hand, a thicker plate results in larger resistance to buckling deformation and generates more energy dissipation, which provides better cushioning and energy absorption performance. The increase in plate thickness is favourable to improving the vibration attenuation and energy absorption properties of BBTP lattice metamaterials. For better performance regulation, the parameter sensitivity needs to be further analyzed.
4.2. Combined parameter analysis
In previous sections, the effect of various parameters on the performance of the proposed metamaterial is investigated separately, i.e. each time the effect of one parameter is investigated. To further compare the sensitivity of different performance indicators to different parameters, a combined parametric analysis is performed in this section. For this purpose, the variation of the performance indicator with two parameters is ascertained each time. The investigated performance indicators include the relative density ρr, the upper bound frequency of bandgap fl, the lower bound frequency of bandgap fu, the bandwidth size fd, the densification strain ϵd, and SEA. The investigated parameters include the inner strut diameter din, the outer strut diameter dout, and the plate thickness.
4.2.1. Combined influence of inner and outer strut diameters
The combined effects of the inner and outer strut diameters on the performance indicators of BBTP are investigated firstly. (a)−(f) show the contours of ρr, fl, fu, fd, ϵd, and SEA on the plane of din and dout, respectively, where the three black dash-dot lines indicate the contours of the relative density ρr at 0.21, 0.23, and 0.24, respectively. From (a), it can be seen that the inner and outer strut diameters have comparable influences on the relative density of the metamaterial.
Figure 11. Combined effect of inner and outer strut diameters on different performance indicators: (a) the relative density ρr, (b) the upper bound frequency of bandgap fl, (c) the lower bound frequency of bandgap fu, (d) the bandgap width fd, (e) the densification strain ϵd, and (f) the specific energy absorption SEA.
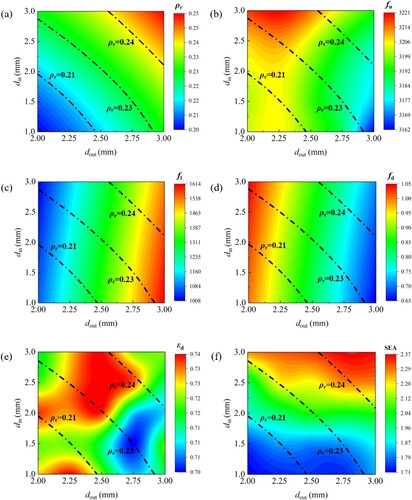
From (b)–(f), the sensitivities of different performance indicators to the two parameters din and dout can be depicted. (b)–(d) show that the vibration attenuation characteristics are more sensitive to the outer strut diameter dout, and less dependent on the inner strut diameter din. The metamaterial with thinner outer struts and thicker inner struts possesses a smaller fl, a higher fu, and a wider bandwidth fd. (e) shows that the densification strain ϵd is not much affected by the strut diameters, with the relative difference not exceeding 5%. (f) shows that SEA is more sensitive to the inner strut diameter din than to the outer strut diameter dout . This is probably attributed to the interaction between the inner struts and the plates during the compression and thicker struts produce stronger impact resistance.
4.2.2. Combined influence of strut diameter and plate thickness
In this section, double-parameter analyses are carried out to ascertain the relative influences of the strut diameter and the plate thickness t on different performance indicators of BBTP. From the analysis in the previous section, the vibration attenuation properties of BBTP lattice metamaterials are more sensitive to the outer strut diameter dout. Therefore, the influence of the plate thickness t is compared with that of dout on the vibration attenuation performance. (a) shows the dependence of the relative density ρr on dout and t, and indicates that ρr is more sensitive to t than to dout. (b)−(d) show the combined effects of dout and t on the vibration attenuation indicators fl, fu, fd, respectively. Similar to the previous section, the three dash-dot lines indicate the contours of the relative densities 0.21, 0.23, and 0.24, respectively. From (b) and (c), the upper bound frequency of the bandgap is more sensitive to the plate thickness t, while the lower bound frequency is more sensitive to the outer strut diameter dout. (d) indicates that the effect of dout exceeds that of t, rendering a larger sensitivity of the bandwidth on dout than on t.
Figure 12. Combined influences of the strut diameter and the plate thickness on different performance indicators: (a) the relative density ρr, (b) the upper bound frequency of bandgap fl, (c) the lower bound frequency of bandgap fu, (d) the bandgap width fd, (e) the densification strain ϵd, and (f) the specific energy absorption SEA.
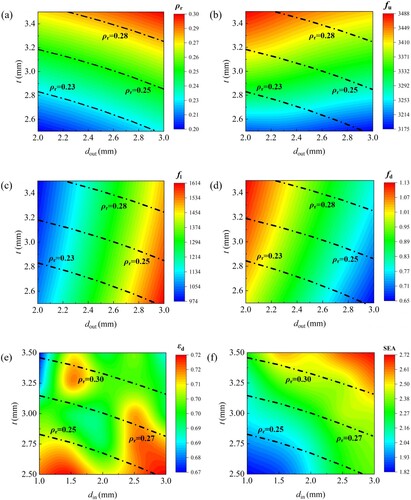
From Sect. 4.2.1, the energy absorption performance of the metamaterial is more sensitive to the inner strut diameter din. Therefore, the influence of the plate thickness t is compared with that of din when analyzing energy absorption performance indicators, i.e. ϵd and SEA. The dependences of ϵd and SEA on din and t are shown in (e) and (f), respectively. The three dash-dot lines correspond to the relative densities of 0.25, 0.27, and 0.30, respectively. From (e), the densification strain is more sensitive to the plate thickness, indicating that an increase in plate thickness is more likely to advance densification. From (f), SEA is relatively more sensitive to the plate thickness t than to the strut diameter din, which may be attributed to the fact that increasing the plate thickness is more effective in enhancing the buckling resistance during the compression process. The vibration attenuation and energy absorption characteristics of the proposed lattice metamaterials can be effectively controlled by properly adjusting the geometric parameters to meet the engineering requirements of different application scenarios.
5. Integration of multifunction
In the above sections, investigations are devoted to different performance aspects of the BBTP truss-plate hybrid lattice metamaterials including vibration attenuation and energy absorption. To further demonstrate the multifunctionality of the proposed lattice metamaterials, we here use the radar diagram to compare their various properties with those of existing architected materials in the literature in . The proposed BBTP lattice metamaterials have a cell size of only 20 mm which is smaller than the conventional local-resonance vibration attenuation metamaterials usually having cell size larger than 40 mm, while they possess better vibration attenuation performance than the conventional metamaterials. The smaller cell size makes the BBTP lattice metamaterials more adaptable to be applied in space-constrained scenarios. The BBTP lattice metamaterials exhibit higher SEA and higher plateau stresses compared to traditional 2D and 3D lattice structures, which is conducive to their application in protective structures. In terms of vibration attenuation performance, the BBTP lattice metamaterials have comparable low-frequency bandgaps and wider bandgap width compared with conventional acoustic metamaterials.
Figure 13. Comparison of the properties of BBTP lattice metamaterials with other structures and materials [Citation44–46].
![Figure 13. Comparison of the properties of BBTP lattice metamaterials with other structures and materials [Citation44–46].](/cms/asset/ef486894-14c4-4591-b603-ddc5544174bc/nvpp_a_2345386_f0013_oc.jpg)
These results highlight the proposed truss-plate hybrid metamaterial as an intriguing multifunctional material with excellent performances in both energy absorption and vibration attenuation. In addition, the proposed metamaterials can be simply and economically manufactured using existing additive manufacturing techniques without multi-material requirements, and facilitate the powder cleaning during the powder-based printing process through the hole openings in the design. The integrated advantages in both energy absorption and vibration attenuation endow the proposed metamaterials with bright application potentials in aerospace, automobile, civil engineering and biomedical fields. A typical example is the structures of the transportation vehicles in aerospace and automobile. The increasing requirement for comfort and the pressing tendency of lightweight bring about new demands of multifunction integration for the composing structures. On one hand, the structures need to isolate the vibration from the engine or the road to improve the ride comfort of the occupants. On the other hand, safety consideration needs the structures to possess strong energy absorption capacity to mitigate the damage from the impact instances. The proposed truss-plate hybrid lattice materials can meet these requirements without introducing additional weight.
6. Conclusions
In summary, three kinds of truss-plate hybrid lattice metamaterials with excellent vibration attenuation and energy absorption properties are proposed based on the local resonance mechanism and hybrid design principle. Through vibration attenuation and quasi-static compression experiments and FE numerical simulations, the mechanical properties and vibration attenuation characteristics of the three lattice metamaterials are systematically investigated. The validated FE numerical models are used to conduct parametric studies for the effects of various geometric parameters on the vibration attenuation and energy absorption performances of the BBTP metamaterials. The following conclusions can be drawn.
The proposed truss-plate hybrid lattice metamaterials possess excellent performances in both vibration attenuation and energy absorption, and can meet the multifunction requirements of different application scenarios. Among the three truss-plate lattice metamaterials with a relative density of 0.225, BBTP has the highest bandwidth of 2.624 kHz. Its elastic wave transmission loss reaches – 270 dB at a frequency of 1400 Hz. Its SEA is 25% larger than FBTP. The vibration attenuation properties of BBTP lattice metamaterials are significantly affected by the outer strut diameter and the plate thickness, with thicker plates and thinner outer struts corresponding to the lower frequency of the bandgap. The energy absorption performances are mainly affected by the inner strut diameter and the plate thickness, with thicker inner struts and thicker plates corresponding to stronger energy absorption capability. The upper bound frequency of the bandgap of BBTP lattice metamaterials is more sensitive to the plate thickness, and the lower bound frequency and the bandgap width are more sensitive to the outer strut diameter. The densification strain and SEA are both more sensitive to the plate thickness.
Disclosure statement
No potential conflict of interest was reported by the author(s).
Data availability statement
The data that support the findings of this study are available from the corresponding author upon reasonable request.
Additional information
Funding
References
- Bhudolia SK, Gohel G, Subramanyam ESB, et al. Enhanced impact energy absorption and failure characteristics of novel fully thermoplastic and hybrid composite bicycle helmet shells. Mater Des. 2021;209:110003, doi:10.1016/j.matdes.2021.110003
- Huang X, Chang L, Zhao H, et al. Study on craniocerebral dynamics response and helmet protective performance under the blast waves. Mater Des. 2022;224:111408, doi:10.1016/j.matdes.2022.111408
- Nasim M, Hasan MJ, Galvanetto U. Impact behavior of energy absorbing helmet liners with PA12 lattice structures: a computational study. Int J Mech Sci. 2022;233:107673, doi:10.1016/j.ijmecsci.2022.107673
- Caserta GD, Iannucci L, Galvanetto U. Shock absorption performance of a motorbike helmet with honeycomb reinforced liner. Compos Struct. 2011;93:2748–2759. doi:10.1016/j.compstruct.2011.05.029
- Bliven E, Rouhier A, Tsai S, et al. Evaluation of a novel bicycle helmet concept in oblique impact testing. Accid Anal Prev. 2019;124:58–65. doi:10.1016/j.aap.2018.12.017
- Wang F, Brøns M, Sigmund O. Non-hierarchical architected materials with extreme stiffness and strength. Adv Funct Mater. 2023: 33, doi:10.1002/adfm.202211561
- Zhou H, Zhang DZ, He N, et al. Topology optimization of multi-morphology composite lattice structure with anisotropy properties. Compos Struct. 2023;321:117294, doi:10.1016/j.compstruct.2023.117294
- Li X, Zhao M, Yu X, et al. Multifunctional and customizable lattice structures for simultaneous sound insulation and structural applications. Mater Des. 2023;234:112354, doi:10.1016/j.matdes.2023.112354
- Timercan A, Terriault P, Brailovski V. Axial tension/compression and torsional loading of diamond and gyroid lattice structures for biomedical implants: simulation and experiment. Mater Des. 2023;225:111585, doi:10.1016/j.matdes.2022.111585
- Xue B, Peng YX, Ren SF, et al. Investigation of impact resistance performance of pyramid lattice sandwich structure based on SPH-FEM. Compos Struct. 2021;261:113561, doi:10.1016/j.compstruct.2021.113561
- Wang X, Zhang L, Song B, et al. Tunable mechanical performance of additively manufactured plate lattice metamaterials with half-open-cell topology. Compos Struct. 2022;300:116172, doi:10.1016/j.compstruct.2022.116172
- Liu X, Wang Y, Liu X, et al. Synergetic control mechanism for enhancing energy-absorption of 3D-printed lattice structures. Int J Mech Sci. 2023: 108711, doi:10.1016/j.ijmecsci.2023.108711
- Li Q, Xiao M, Wang D, et al. Energy absorption characteristics of starfruit-inspired biomimetic lattice structure under non-axial compression loading. Eng Struct. 2023: 294, doi:10.1016/j.engstruct.2023.116767
- Alkhatib SE, Karrech A, Sercombe TB. Isotropic energy absorption of topology optimized lattice structure. Thin-Walled Struct. 2023;182:110220, doi:10.1016/j.tws.2022.110220
- Yang S, Chang H, Wang Y, et al. A phononic crystal suspension for vibration isolation of acoustic loads in underwater gliders. Appl Acoust. 2024;216:109731, doi:10.1016/j.apacoust.2023.109731
- Cheng SL, Liang JM, Ding Q, et al. Analysis of the band gap characteristics of a new type of three-dimensional single phase phononic crystal. Wave Motion. 2023;122:103195, doi:10.1016/j.wavemoti.2023.103195
- Pan Y, Liu R, Bin G, et al. Vibration and noise reduction of phononic crystal structure laid on the noise transmission path of axial piston pump. Appl Acoust. 2022;200:109075, doi:10.1016/j.apacoust.2022.109075
- Sheng P, Fang X, Dai L, et al. Synthetical vibration reduction of the nonlinear acoustic metamaterial honeycomb sandwich plate. Mech Syst Signal Process. 2023;185:109774, doi:10.1016/j.ymssp.2022.109774
- Liu Y, Yang J, Yi X, et al. Enhanced vibration suppression using diatomic acoustic metamaterial with negative stiffness mechanism. Eng Struct. 2022;271:114939, doi:10.1016/j.engstruct.2022.114939
- Lee S, Ahn CH, Lee JW. Vibro-acoustic metamaterial for longitudinal vibration suppression in a low frequency range. Int J Mech Sci. 2018;144:223–234. doi:10.1016/j.ijmecsci.2018.05.010
- Kudela P, Ijjeh A, Radzienski M, et al. Deep learning aided topology optimization of phononic crystals. Mech Syst Signal Process. 2023: 110636, doi:10.1016/j.ymssp.2023.110636
- Ding W, Chen T, Yu D, et al. Isotacticity in chiral phononic crystals for low-frequency bandgap. Int J Mech Sci. 2023: 108678, doi:10.1016/j.ijmecsci.2023.108678
- Tao Z, Ren X, Zhao AG, et al. A novel auxetic acoustic metamaterial plate with tunable bandgap. Int J Mech Sci. 2022;226:107414, doi:10.1016/j.ijmecsci.2022.107414
- Zhang J, Yao D, Peng W, et al. Optimal design of lightweight acoustic metamaterials for low-frequency noise and vibration control of high-speed train composite floor. Appl Acoust. 2022;199:109041, doi:10.1016/j.apacoust.2022.109041
- Zhang W, Yin H, Wu Y, et al. A novel auxetic 3D lattice structure for enhancing energy absorption. Compos Struct. 2023;326:117620, doi:10.1016/j.compstruct.2023.117620
- Gao Y, Wei X, Han X, et al. Novel 3D auxetic lattice structures developed based on the rotating rigid mechanism. Int J Solids Struct. 2021;233:111232, doi:10.1016/j.ijsolstr.2021.111232
- Sahariah BJ, Namdeo A, Khanikar P. Composite-inspired multilattice metamaterial structure: an auxetic lattice design with improved strength and energy absorption. Mater Today Commun. 2022;30:103159, doi:10.1016/j.mtcomm.2022.103159
- Peng XL, Bargmann S. Tunable auxeticity and isotropic negative thermal expansion in three-dimensional lattice structures of cubic symmetry. Extrem Mech Lett. 2021;43:101201, doi:10.1016/j.eml.2021.101201
- Sahoo SS, Gupta MK, Mittal R, et al. Lattice dynamics and negative thermal expansion in layered mercury-based halides. Mater Today Commun. 2022;31:103323, doi:10.1016/j.mtcomm.2022.103323
- Bai L, Xu W, Wang W, et al. Thermal expansion regulation and bandgap analysis of a novel dual-constituent negative Poisson’s ratio lattice metamaterial. Mater Today Commun. 2023;35:106311, doi:10.1016/j.mtcomm.2023.106311
- White BC, Garland A, Alberdi R, et al. Interpenetrating lattices with enhanced mechanical functionality. Addit Manuf. 2021;38:101741, doi:10.1016/j.addma.2020.101741
- Chen S, Liu X, Hu J, et al. Elastic architected mechanical metamaterials with negative stiffness effect for high energy dissipation and low frequency vibration suppression. Compos Part B Eng. 2023;267:111053, doi:10.1016/j.compositesb.2023.111053
- Ha CS, Lakes RS, Plesha ME. Cubic negative stiffness lattice structure for energy absorption: numerical and experimental studies. Int J Solids Struct. 2019;178–179:127–135. doi:10.1016/j.ijsolstr.2019.06.024
- Li Z, Zhai W, Li X, et al. Additively manufactured dual-functional metamaterials with customisable mechanical and sound-absorbing properties. Virtual Phys Prototyp. 2022;17:864–880. doi:10.1080/17452759.2022.2085119
- Li X, Yu X, Zhao M, et al. Multi-level bioinspired microlattice with broadband sound-absorption capabilities and deformation-tolerant compressive response. Adv Funct Mater. 2023: 33, doi:10.1002/adfm.202210160
- Li X, Yu X, Zhai W. Less Is more: hollow-truss microlattice metamaterials with dual sound dissipation mechanisms and enhanced broadband sound absorption. Small. 2022;18:1–12. doi:10.1002/smll.202204145
- An X, Lai C, He W, et al. Three-dimensional chiral meta-plate lattice structures for broad band vibration suppression and sound absorption. Compos Part B Eng. 2021;224:109232, doi:10.1016/j.compositesb.2021.109232
- Li H, Hu Y, Huang H, et al. Broadband low-frequency vibration attenuation in 3D printed composite meta- lattice sandwich structures. Compos Part B Eng. 2021;215:108772, doi:10.1016/j.compositesb.2021.108772
- An X, Lai C, He W, et al. Three-dimensional meta-truss lattice composite structures with vibration isolation performance. Extrem Mech Lett. 2019;33:100577, doi:10.1016/j.eml.2019.100577
- Zhang L, Bai Z, Zhang Q, et al. On vibration isolation performance and crashworthiness of a three-dimensional lattice metamaterial. Eng Struct. 2023;292:116510, doi:10.1016/j.engstruct.2023.116510
- Yang W, Bai X, Zhu W, et al. 3D printing of polymeric multi-layer micro-perforated panels for tunable wideband sound absorption. Polymers (Basel). 2020;12(2):360, doi:10.3390/polym12020360
- Yang W, An J, Chua CK, et al. Acoustic absorptions of multifunctional polymeric cellular structures based on triply periodic minimal surfaces fabricated by stereolithography. Virtual Phys Prototyp. 2020;15:242–249. doi:10.1080/17452759.2020.1740747
- Wu J, Zhang Y, Yang F, et al. A hybrid architectural metamaterial combing plate lattice and hollow-truss lattice with advanced mechanical performances. Addit Manuf. 2023;76:103764, doi:10.1016/j.addma.2023.103764
- Zhang XG, Jiang W, Zhang Y, et al. Bending performance of 3D re-entrant and hexagonal metamaterials. Thin-Walled Struct. 2023;188:110829, doi:10.1016/j.tws.2023.110829
- Li H, Hu Y, Chen J, et al. Lightweight meta-lattice sandwich panels for remarkable vibration mitigation: analytical prediction, numerical analysis and experimental validations. Compos Part A. 2022;163:107218, doi:10.1016/j.compositesa.2022.107218
- Sun P, Guo H, Jin F, et al. Mechanics and extreme low-frequency band gaps of auxetic hexachiral acoustic metamaterial with internal resonant unit. Appl Acoust. 2022;200:109046, doi:10.1016/j.apacoust.2022.109046