ABSTRACT
Microcrystalline cellulose (MCC) grafted with n-octadecyl isocyanate (18C-g-MCC) was introduced as the reinforcing filler in epoxidised soybean oil (ESO) polymer. The wetting characteristics of 18C-g-MCC were evaluated by static contact angle and the results show that the hydrophobicity of MCC was improved by the introduction of nonpolar alkyl groups. The ESO composites were synthesised with different contents of 18C-g-MCC (from 0 to 25 wt%) by a thermally cured method. The reinforcing effects of 18C-g-MCC were evaluated by scanning electron microscopy, mechanical test, dynamic mechanical analysis and thermal stability test. The results show that the tensile strength, the impact strength, Young's modulus, the flexural strength and glass transition temperature of the composites increase gradually with the increase of 18C-g-MCC content, while the elongation at break begins to decrease with 18C-g-MCC content of more than 20 wt%. Contact angle and water absorption analysis of the composites indicate the addition of 18C-g-MCC increases the water absorption of the ESO polymer.
1. Introduction
Bio-based materials have attracted immense research interest because of their fascinating properties that potentially compete with the most advanced materials in nature and great potential for producing a variety of high-value products with low impact on the environment. Vegetable oil, as the cheapest and most abundant biological feedstock, has been studied extensively in recent years for composites and coating materials because of its advantages such as low toxicity and inherent biodegradability.[Citation1,Citation2] There were many reports that modified vegetable oils could be used to synthesise segmented polyurethane,[Citation3] thermoplastic polyurethanes,[Citation4] poly(methyl methacrylate)-multigraft copolymers,[Citation5] novel thermosets rubbers,[Citation6] hydrogels [Citation7] and bio-based composites.[Citation8] It is found that these renewable polymers could serve as an alternative to the traditional petroleum-based polymers through innovative design, because these novel bio-based polymers could be more cost-effective and eco-friendly than the existing petroleum-based polymers.
Epoxidised soybean oil (ESO) is extremely promising as inexpensive renewable material for industrial applications because it shares many of the characteristics and properties of conventional epoxy formulations. Bio-based thermosets can be produced by curing the ESO with conventional curing agents, such as amines,[Citation9] carboxylic acid anhydrides[Citation10] and carboxylic acids,[Citation11] through thermal and UV approaches.[Citation12,Citation13] However, the mechanical and thermal properties of ESO thermosets are generally lower than those of petroleum-based thermosets,[Citation14,Citation15] which should be due to the low crosslink density and flexibility of the backbone structure in ESO. In order to improve these properties, reinforcing fillers, such as clay and cellulose, were incorporated into ESO while maintaining their inherently bio-based properties.
Microcrystalline cellulose (MCC) is a hydrolysed cellulose consisting of a large amount of cellulose microcrystals together with amorphous areas. It is well known as a biodegradable material that is often used for packaging food products and widely used in different industrial fields, such as pharmaceuticals, cosmetics, medical applications and food processing. Apart from these, MCC is a very promising cellulosic reinforcement for polymers due to the advantages of being biodegradable, renewable, low density, low cost, little abrasion to equipment and good mechanical properties.[Citation16,Citation17] Many polymer composites such as polylactic acid, polyurethane, poly(vinyl alcohol) and rubber have been investigated by using MCC as the reinforcing filler.[Citation18–21] In our previous study, MCC and its oxidised product dialdehyde cellulose were introduced as the reinforcing filler in ESO polymer.[Citation22] However, the main drawback of cellulosic filler is its hydrophilic nature, which inhibits its homogeneous dispersion in nonpolar polymer matrices and limits the compatibility between the reinforcing phase and the matrix. Therefore, tensile strength and break elongation of the MCC/ESO composites were slightly improved.[Citation22]
Surface chemical modification is a typical and classical approach to transform the polar hydroxyl groups at the surface of cellulosic particles into moieties that can enhance interactions with the matrix. Over the last decade, many approaches involved the grafting of polymers onto the surface of the fibres have been investigated. Nevertheless, most of these strategies have already been tested onto cellulose nanocrystals or nanofibrillated cellulose.[Citation23,Citation24] To the best of our knowledge, the grafting of long chain or polymer on MCC has been rarely studied. In this study, n-octadecyl isocyanate was grafted to the surface of MCC (18C-g-MCC) and the modified MCC was introduced as the reinforcing fillers to the preparation of the composites. Because of the similar long aliphatic chains of ESO and n-octadecyl isocyanate, it is anticipated that the mechanical properties of 18C-g-MCC filled ESO polymer will be increased. The effects of 18C-g-MCC incorporation amount on the final properties of the ESO composites were studied using scanning electron microscopy analysis, and the mechanical performance was examined using conventional tensile testing and dynamic mechanical thermal analysis.
2. Experimental
2.1. Materials
Epoxidised soybean oil (ESO, epoxy value: 0.375 mol/100 g) was purchased from Wuhu Aladdin Chemical Additives Co., Ltd. (Wuhu, China). The hardener cis-1,2-cyclohexanedicarboxylic anhydride (HHPA, >99%) and catalyst 1-methylimidazole (1 MI, >99%) were obtained from Aladdin Industrial Corporation (Shanghai, China). MCC was purchased from Sinopharm Chemical Reagent Co., Ltd. (Shanghai, China). Both MCC and ESO were dried in vacuo overnight before use. The chemical structures of ESO and MCC are shown in . Toluene, n-octadecyl isocyanate (C18H37NCO), n-butyltindilaurate, ethanol and acetone were purchased from Nanjing Chemical Reagent Co., Ltd. (Nanjing, China) and used without further purification.
2.2. Chemical modification of MCC (18C-g-MCC)
In a three-necked round-bottomed flask equipped with a reflux condenser, 3 g of MCC and 100 mL of toluene were added. The system was kept under nitrogen atmosphere. An excess of n-octadecyl isocyanate (2.2 g, 2 equivalent in comparison with OH groups available at the surface of a cellulose (∼4%)) [Citation24] was added slowly (drop by drop) at room temperature. When n-octadecyl isocyanate was fully added, 1 mL of n-butyltindilaurate as a catalyst was added and the temperature of the system was increased to 90 °C and kept for 2 h. The toluene suspension of modified MCC was then filtered and washed with ethanol to remove amine formed during the reaction and n-octadecyl isocyanates that did not react. Afterwards, the grafted material 18C-g-MCC was centrifuged and dried in vacuo overnight.
2.3. Preparation of ESO composites
The ESO composites were synthesised by a thermally cured method. Blending was performed in a one-stage process by the direct mixing of epoxy monomers with a stoichiometric amount of HHPA (1: 0.75 molar ratio of epoxy/anhydride) and 3 wt% of catalyst 1 MI (on the basis of the anhydride weight). 18C-g-MCC powder was dispersed in acetone using an ultrasonic bath for 15 min. The content of additional cellulose was expressed as weight percentage of ESO (0, 5%, 10%, 15%, 20% and 25%). All formulations were placed in a glass round-bottom flask and stirred at 60 °C for 30 min. The mixing process was carried out under reduced pressure (∼10 mmHg) to reduce the volume of air bubbles entrapped in the bulk. Subsequently, the reactive mixture was transferred into a polytetrafluoroethylene mold with a dimension of 125 × 115 × 10 mm3. The mold had been previously heated to a temperature of 80–90 °C in order to avoid thermal shock when the liquid resin was poured into the mold. The curing cycle chosen was heating for 1.5 h at 90 °C, curing for 2 h at 100 °C and post-curing for 1 h at 110 °C. ESO composite samples with different sizes were cut according to the different test standards. The scheme of the grafting reaction to form 18C-g-MCC and the formation of ESO composites were depicted as
2.4. Characterisation
The morphology of 18C-g-MCC and the fractured surfaces produced from the tensile samples were investigated by scanning electron microscopy (SEM) (Quanta 200, FEI, USA). The samples were gold-coated to provide an electrically conductive surface. The accelerating voltage was lower than 20 kV to avoid excessive charge building up. Fourier transform infrared spectroscopy (FT-IR) (VETERX 70, BRUKER, Germany) was used to obtain FT-IR spectra of the samples. Two milligram of cellulose powder was mixed with 200–300 mg of KBr by milling within a mortar. All spectra were recorded between 4000 and 500 cm−1, with a resolution of 4 cm−1 and 32 scans. X-ray diffraction (XRD) measurements were performed on dry powders of cellulose at ambient temperature on an X-ray diffractometer (Ultima IV, RIGAKU, Japan) using Cu Kα radiation (40 kV and 30 mA) at a scan rate of 2 °/min with a step size of 0.02°. Thermogravimetric analysis (TGA) was carried out under nitrogen atmosphere with a Thermogravimetric Analyzer (TG209F1, NETZSCH, Germany) at a heating rate of 10 °C/min from 25 to 600 °C.
For evaluation of the wetting characteristics of 18C-g-MCC and the ESO composites, the static contact angle between the liquid and the solid substrate was measured using a contact angle measuring instrument (DSA 100, KRUSS, Germany). At least five specimens of each sample were measured, with degree of reproducibility within ±1°. Water absorption studies were performed following the ASTM D 570-98 standard. Six specimens of every sample were submerged in distilled water at 40 °C. The specimens were removed from the water at certain periods of time and weighted in a high precision balance and then submerged again in water. The content of water was calculated by the weight difference.
The mechanical properties including tensile strength (σb), elongation at break (ϵb) and Young's modulus (E) of the composite samples with a dimension of 75 × 6 × 1.5 mm3 (length × width × thickness) were carried out at ambient condition on a universal testing machine (CMT5504, SUNS, China) with a loading rate of 100 mm min−1 at room temperature according to the standard of ISO 527-3:1996 (E). An average value of five replicates was taken. The un-notched impact strength and the notched impact strength of composites were tested according to the standard ASTM D256-1997, test sample size is 25 × 6 × 2 mm3 (length × width × thickness). Flexural strength test is based on ASTM D 790-790, the flexural strength test of bending rate of 5 mm/min, the span is 80 mm. Five samples of each type were tested and averaged.
The dynamic mechanical properties of the neat ESO polymer and MCC reinforced composites were evaluated by a Dynamic Mechanical Analyzer (DMA 242 E, NETZSCH, Germany). Samples with a dimension of 35 × 5 × 1 mm3 were tested in a single cantilever mode over a temperature range from −50 to 100 °C, with a heating rate of 3 °C/min at a frequency of 1 Hz to obtain storage modulus and tan delta.
3. Results and discussion
3.1. Structure and properties of 18C-g-MCC
(a,b) shows SEM images of untreated MCC and 18C-g-MCC with the sizes of about 20–150 µm, and it reveals that after surface modification there were no changes in the morphology. Using FT-IR spectroscopy, the grafting reaction is characterised by the appearance of a new peak in 1710 cm−1 ((c)) that was associated with the formed ester group, as illustrated in . The broad and strong band ranging from 3200 to 3600 cm−1 are assigned to –OH or –NH group. The band at 2901 and 1633 cm−1 can be ascribed to C–H stretching vibration and O–H bending vibration of absorption water of cellulose, respectively.[Citation25] The intensity of the band at 2901 cm−1 decreases after treatment, corresponding to the decreased –OH groups after the grafting reaction.
Figure 2. SEM images of untreated MCC (a) and 18C-g-MCC (b), FT-IR spectra (c) and XRD patterns (d).
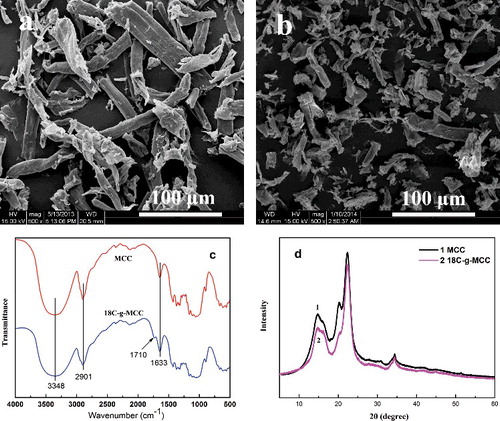
The impact of chemical modification on the crystallite structure of the cellulose was further investigated using XRD analysis. The diffraction patterns for MCC and 18C-g-MCC are presented in (d), and both show the typical diffraction peaks of the three angles located at about 22.6°, 16.4° and 34.4°.[Citation26] It indicates that the original inner crystalline structure of 18C-g-MCC is maintained after grafting with n-octadecyl isocyanate, although the diffraction peaks are less well-defined after surface modification probably due to the formation of a grafted layer at the surface of MCC.
summarises the equilibrium contact angles for water, diiodomethane and ethylene glycol on MCC and 18C-g-MCC. The −OH covered MCC surface is more capable of attaching to water and consequently has a lower initial contact angle.[Citation27] The 18C-g-MCC has a sharp increase in θwater from 35.7° to 67.8°, an increase in θdiiodomethane from 38.2° to 43.5° and an increase in θethylene glycol from 19.6° to 25.3°. Such results indicate that chemical modification has induced dramatic changes in surface polarity of MCC. With the introduction of nonpolar alkyl groups onto the surface of MCC, the polar component decreases considerably.
Table 1. Contact angle on MCC and 18C-g-MCC.
3.2. Morphology of the composites
The fracture morphologies of ESO composites with different 18C-g-MCC contents were observed using SEM analysis. From (a), it can be seen that the neat ESO polymer shows a smooth fracture surface. With the increase of 18C-g-MCC content, the fracture surfaces exhibit a rougher surface with small voids and few cavities gradually (indicated by the arrows in (b–f). It is due to that the presence of rigid particles offers obstacles to the advance of the crack, which must find new paths for growing, contributing to increase the surface roughness.[Citation28] However, obvious gaps between the fibres and the matrix or the holes derived from fibre pull-out cannot be found, indicating the good miscibility between ESO polymer and 18C-g-MCC. However, when the filler content reaches 25%, some large cellulose fragments appear on the fracture surfaces (designated by a circle), suggesting that 18C-g-MCC begins to self-aggregate and the binding to matrix becomes weak.
3.3. Mechanical properties of the composites
shows the effects of 18C-g-MCC content on the mechanical properties of ESO/18C-g-MCC composites including tensile strength (σb), elongation at break (ϵb) and Young's modulus (E). The E and σb of the composites increase gradually with the increase of 18C-g-MCC content, while the ϵb increases with the 18C-g-MCC content up to 20 wt% and then decreases. It is well known that the mechanical properties of the composites are determined by several factors, such as nature of the reinforcement filler and filler-matrix interfacial adhesion. The improvement in tensile strength and Young's modulus at the presence of 18C-g-MCC is expected as MCC is much stiffer than ESO polymer matrix. Furthermore, the homogeneous dispersion of 18C-g-MCC (as demonstrated by the SEM analysis) leads to a great enhancement of mechanical properties of the composites. The synchronous increase of the elongation at break can be explained by plastic deformation of the matrix polymer induced by the interfacial debonding.[Citation29] As comparison with the mechanical properties of untreated MCC composites (ESO/MCC) previously reported,[Citation22] the tensile strength of 18C-g-MCC composites is nearly double and the elongation at break increases by 60%.
Figure 4. Effects of 18C-g-MCC content on tensile strength σb, Young's modulus E and elongation at break ϵb of the composites.
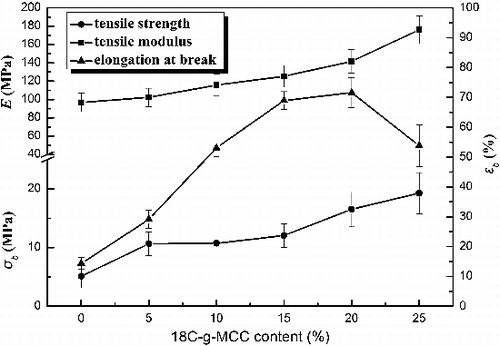
The effects of varying 18C-g-MCC amounts on the impact properties of the ESO composites are presented in . The results of notched impact strength and un-notched impact strength of the composites show the similar tendency, indicating 18C-g-MCC has a significant effect on improving the impact properties of the composites. The energy transferred to the matrix before its break is substantially increased with the increase of 18C-g-MCC content. The possible mechanism of impact properties of composites can be explained by considering the crack propagation.[Citation30] Basically, the crack propagates freely in the neat ESO polymer. In the case of ESO/18C-g-MCC composites, crack occurs first and then peeling tends to take place from the cracked surface along the 18C-g-MCC, followed by cutting or by pulling out of the fillers from the matrix thus increasing the absorbed energy. The effects of 18C-g-MCC reinforcement on flexural strength (FS) and flexural modulus (FM) of ESO/18C-g-MCC are shown in . A substantial increase of FS and FM is observed with the increase of 18C-g-MCC content from 5 up to 25 wt%, which is consistent with the results and trend obtained from tensile testing and impact testing. These results also exhibit an effective reinforcement of 18C-g-MCC for ESO polymer due to the rigidity of 18C-g-MCC and the better compatibility with the matrix.
3.4. Dynamic mechanical analysis
Dynamic mechanical analysis allows determination of the thermal-mechanical properties of materials over a broad temperature range and is strongly sensitive to the structure of the composites. shows the storage modulus and tan δ of ESO/18C-g-MCC composites, as a function of temperature. The storage modulus spectra show three district regions, which could be identified as glassy (temperature lower than −40 °C), glass transition and rubbery regions (higher than 50 °C). The composites show increased storage modulus over the entire temperature range with the increase of 18C-g-MCC content, indicating that the cellulose imparts stiffness to the material. ESO/18C-g-MCC composites show higher storage modulus at the same cellulose content than ESO/MCC composites.[Citation22] For instance, when the cellulose content is 25 wt%, the storage modulus of ESO/MCC is 3024 MPa at −50 °C and 1662 MPa at 100 °C as compared with 3443 and 2228 MPa for ESO/18C-g-MCC composites, respectively. On the other hand, the glass transition temperature (Tg) of ESO polymer matrix gradually shifts to a higher temperature. It can be ascribed to the intermolecular interactions between the fillers and matrix, which reduces the flexibility of molecular chains of the matrix.[Citation31]
3.5. Thermogravimetric analysis
TG analysis was conducted to investigate the thermal stability of 18C-g-MCC and ESO/18C-g-MCC composites. From (a), it can be apparently seen that 18C-g-MCC has a lower thermal stability compared to the neat ESO polymer or ESO/18C-g-MCC composites. The differential thermogravimetry (DTG) curves ((b)) show only one thermal decomposition peak corresponding to the maximum degradation temperature. presents some data extracted from the TGA curves: onset decomposition temperature (Tonset), the temperature at 20% weight loss (T20), the maximum decomposition temperature (Tmax) and the weight of residue at 600 °C. It can be seen that the decomposition temperature of the composites at various stage decreases gradually with the increase of the 18C-g-MCC content due to its relative low thermal stability. The residue of the composites at 600 °C is very low and almost the same, suggesting the composites were decomposed completely. As comparison with ESO/MCC composites, 18C-g-MCC composites have better thermal stability.
Table 2. Thermal characteristics of ESO/18C-g-MCC composites recorded from TGA and DTG.
3.6. Contact angle and water absorption analysis
Since the ester crosslinks formed in ESO polymer are sensitive to hydrolysis by water, the wettability of the ESO polymer is conducive to biodegradation.[Citation32,Citation33] To verify the change in the hydrophilicity of the composites after adding 18C-g-MCC, the water contact angles of the neat ESO polymer, ESO/MCC and ESO/18C-g-MCC composites were measured. From (a), the contact angle values of both ESO/MCC composites and ESO/18C-g-MCC composites are lower than the neat ESO polymer and the values decrease with the increase of the cellulose contents, which is due to the hydrophilicity of cellulose.[Citation34] As comparison with ESO/MCC composites,[Citation22] ESO/18C-g-MCC composites exhibit higher contact angles, which confirm that grafting of long nonpolar chains on MCC modifies the surface properties of the composites.
Figure 9. Comparison of water contact angle to ESO/MCC composites (a) and in vitro water uptake (b) of ESO/18C-g-MCC composites.
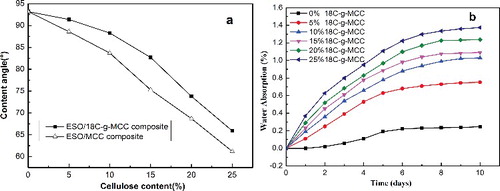
The amount of water absorbed in the ESO composites was calculated by the weight difference between the samples exposed to water and the dried samples. (b) shows the percentage of water absorbed plotted against time for all the samples. The neat ESO polymer demonstrates a hydrophobic characterisation that the absorbed water content is less than 0.2% after 10 days of exposure. However, the composites absorb water rapidly during the first stages (0–6 days) reaching a saturation point, and after that the content of water in the composites increases slowly. The hydrophilic character of cellulose is responsible for the water absorption in the composites, and therefore a higher content of 18C-g-MCC leads to a higher amount of water absorbed.
4. Conclusions
Bio-based ESO composites were prepared by using n-octadecyl isocyanate modified MCC as the reinforcing fillers. The grafting reaction of long-chain isocyanate is fulfilled by reacting with −OH groups on cellulose surface and that is confirmed by FT-IR analysis. The fracture morphologies analysis of the composites shows a good miscibility between ESO polymer and 18C-g-MCC. Tensile strength, impact strength, Young's modulus, flexural strength and glass transition temperature of the composites increase with the increase of 18C-g-MCC content, while the elongation at break increases with the 18C-g-MCC content up to 20 wt% and then decreases. As comparison with untreated MCC composites, tensile strength of 18C-g-MCC composites is nearly doubled and elongation at break increases by 60%. The maximum degradation temperature of the composites decreases gradually with the increase of the 18C-g-MCC content due to its low thermal stability. Contact angle and water absorption analysis suggest that the composites exhibit a lower contact angle values than that of the neat ESO polymer and the amount of water absorbed increases with the increase of 18C-g-MCC contents.
Acknowledgments
This work was supported by Natural Science Foundation of Jiangsu Province, China (BK 20141469). The authors gratefully acknowledge Advanced Analysis & Testing Center of Nanjing Forestry University.
Disclosure statement
No potential conflict of interest was reported by the authors.
Additional information
Funding
References
- Quirino RL, Ma Y, Larock RC. Oat hull composites from conjugated natural oils. Green Chem. 2012;14:1398–1404.
- Boquillon N, Fringant C. Polymer networks derived from curing of epoxidised linseed oil: influence of different catalysts and anhydride hardeners. Polymer. 2000;41:8603–8613.
- Keles E, Hazer B. Synthesis of segmented polyurethane based on polymeric soybean oil polyol and poly (ethylene glycol). J Polym Environ. 2009;17:153–158.
- Petrovic ZS, Xu YJ, Milic J, et al. Biodegradation of thermoplastic polyurethanes from vegetable oils. J Polym Environ. 2010;18:94–97.
- Cakmakli B, Hazer B, Acikgoz S, et al. PMMA-multigraft copolymers derived from linseed oil, soybean oil, and linoleic acid: protein adsorption and bacterial adherence. J Appl Polym Sci. 2007;105:3448–3457.
- Xia Y, Henna PH, Larock RC. Novel thermosets from the cationic copolymerization of modified linseed oils and dicyclopentadiene. Macromol Mater Eng. 2009;294:590–598.
- Liu ZS, Erhan SZ. Ring-opening polymerization of epoxidized soybean oil. J Am Oil Chem Soc. 2010;87:437–444.
- Zhang J, Hu S, Zhan GZ, et al. Biobased nanocomposites from clay modified blend of epoxidized soybean oil and cyanate ester resin. Prog Org Coat. 2013;76:1683–1690.
- de Espinosa LM, Ronda JC, Galia M, et al. A new enone-containing triglyceride derivative as precursor of thermosets from renewable resources. J Polym Sci Pol Chem. 2008;46:6843–6850.
- Miyagawa H, Mohanty AK, Burgueno R, et al. Development of biobased unsaturated polyester containing functionalized linseed oil. Ind Eng Chem Res. 2006;45:1014–1018.
- Dogan E, Kuesefoglu S. Synthesis and in situ foaming of biodegradable malonic acid ESO polymers. J Appl Polym Sci. 2008;110:1129–1135.
- Miyagawa H, Mohanty AK, Burgueno R, et al. Novel biobased resins from blends of functionalized soybean oil and unsaturated polyester resin. J Polym Sci Pol Phys. 2007;45:698–704.
- Kim JR, Sharma S. The development and comparison of bio-thermoset plastics from epoxidized plant oils. Ind Crops Prod. 2012;36:485–499.
- Supanchaiyamat N, Shuttleworth PS, Hunt AJ, et al. Thermosetting resin based on epoxidised linseed oil and bio-derived crosslinker. Green Chem. 2012;14:1759–1765.
- Tan SG, Ahmad Z, Chow WS. Interpenetrating polymer network structured thermosets prepared from epoxidized soybean oil/diglycidyl ether of bisphenol A. Polym Int. 2014;63:273–279.
- Cateto CA, Barreiro MF, Rodrigues AE, et al. Optimization study of lignin oxypropylation in view of the preparation of polyurethane rigid foams. Ind Eng Chem Res. 2009;48:2583–2589.
- Ma XF, Chang PR, Yu JG. Properties of biodegradable thermoplastic pea starch/carboxymethyl cellulose and pea starch/microcrystalline cellulose composites. Carbohydr Polym. 2008;72:369–375.
- Haafiz MKM, Hassan A, Zakaria Z, et al. Properties of polylactic acid composites reinforced with oil palm biomass microcrystalline cellulose. Carbohydr Polym. 2013;98:139–145.
- Luo XG, Mohanty A, Misra M. Green composites from soy-based biopolyurethane with microcrystalline cellulose. Macromol Mater Eng. 2013;298:412–418.
- Sun XW, Lu CH, Liu Y, et al. Melt-processed poly(vinyl alcohol) composites filled with microcrystalline cellulose from waste cotton fabrics. Carbohydr Polym. 2014;101:642–649.
- Bai W, Li KC. Partial replacement of silica with microcrystalline cellulose in rubber composites. Compos Part A-Appl S. 2009;40:1597–1605.
- He M, Zhou J, Zhang H, et al. Microcrystalline cellulose as reactive reinforcing fillers for epoxidized soybean oil polymer composites. J Appl Polym Sci. 2015;132:42488–42495.
- Siqueira G, Bras J, Dufresne A. New process of chemical grafting of cellulose nanoparticles with a long chain isocyanate. Langmuir. 2010;26:402–411.
- Missoum K, Bras J, Belgacem MN. Organization of aliphatic chains grafted on nanofibrillated cellulose and influence on final properties. Cellulose. 2012;19:1957–1973.
- Watanabe A, Morita S, Kokot S, et al. Drying process of microcrystalline cellulose studied by attenuated total reflection IR spectroscopy with two-dimensional correlation spectroscopy and principal component analysis. J Mol Struct. 2006;799:102–110.
- Liu H, Liu D, Yao F, et al. Fabrication and properties of transparent polymethylmethacrylate/cellulose nanocrystals composites. Bioresour Technol. 2010;101:5685–5692.
- Lin N, Huang J, Chang PR, et al. Surface acetylation of cellulose nanocrystal and its reinforcing function in poly(lactic acid). Carbohydr Polym. 2011;83:1834–1842.
- Wik VM, Aranguren MI, Mosiewicki MA. Castor Oil-based polyurethanes containing cellulose nanocrystals. Polym Eng Sci. 2011;51:1389–1396.
- Xu X, Liu F, Jiang L, et al. Cellulose nanocrystals vs. cellulose nanofibrils: a comparative study on their microstructures and effects as polymer reinforcing agents. ACS Appl Mat Interfaces. 2013;5:2999–3009.
- Dwan'isa JPL, Mohanty AK, Misra M, et al. Biobased polyurethane and its composite with glass fiber. J Mater Sci. 2004;39:2081–2087.
- Qiu WL, Endo T, Hirotsu T. Interfacial interactions of a novel mechanochemical composite of cellulose with maleated polypropylene. J Appl Polym Sci. 2004;94:1326–1335.
- Shogren RL, Petrovic Z, Liu ZS, et al. Biodegradation behavior of some vegetable oil-based polymers. J Polym Environ. 2004;12:173–178.
- Yew GH, Yusof AMM, Ishak ZAM, et al. Water absorption and enzymatic degradation of poly(lactic acid)/rice starch composites. Polym Degrad Stab. 2005;90:488–500.
- Zhang Z, Wu Q, Song K, et al. Using cellulose nanocrystals as a sustainable additive to enhance hydrophilicity, mechanical and thermal properties of poly(vinylidene fluoride)/poly(methyl methacrylate) blend. ACS Sustainable Chem Eng. 2015;3:574–582.