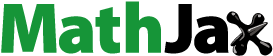
Abstract
Uniform filler dispersion and fillers, such as nanomaterials, with distinct but superior qualities compared to the typical matrix component can be used to create high performance composites. The current study used molecular dynamics simulations to investigate the effect of graphene reinforcement on the mechanical properties of Kevlar/Diglycidyl Ether of Bisphenol-A (DGEBA). Diethyl toluene diamine (DETDA) serves as the curing agent for DGEBA, and graphene is randomly reinforced at 1, 1.5, and 2 weight percent in the DGEBA/DETDA epoxy matrix. A layered (epoxy-Kevlar-epoxy, EKE) is constructed by maintaining Kevlar fibre in horizontal position in between the graphene-reinforced DGEBA/DETDA as illustrated in the figure. Energy minimization, geometry optimization, and dynamics are used to further stabilise the constructed structure. The method of constant strain is used to determine mechanical parameters. The MD simulation revealed that mechanical properties increased with increasing graphene content, with 21.42%, 36.47%, and 42.49% for 1, 1.5, and 2 weight percentages of graphene, respectively, when compared to pure EKE. The increasing trends in elastic moduli corroborate the experimental findings. The ultimate strength increases as graphene content increases.
1. Introduction
High performance composites can be produced by uniform filler dispersion and when the filler, i.e. nanomaterials, has different but superior properties to the standard matrix component. They are now useful in a variety of fields, including biomedical, sensing, energy conversion and storage, structural components with a high strength-to-weight ratio, and so on. Recent developments have also led to their use in gas barriers, food packaging, environmental protection, biomedical materials and making things less likely to catch fire [Citation1–2]. Nanocomposites are multiphase materials formed by combining a matrix and a nano-dimensional material. A nano-dimensional material could be carbon nanotube, graphene, nanoplatelet, nanofibers etc. The reinforcement of these materials significantly improves the mechanical properties as well as the electrical and thermal conductivities of the base composite [Citation3]. Over the last few decades, much research has been conducted on polymer nanocomposites, with graphene, carbon nanotubes (CNTs), molybdenum disulphide, and tungsten disulphide used as reinforcements to fabricate mechanically strong polymeric nanocomposites. Since the discovery of carbon nanotubes [Citation4–6], a significant amount of study has been carried out with the majority of the work finished in the previous two decades. CNTs benefit from a variety of mechanical properties, including high stiffness and tensile strength, as well as the ability to withstand large deformations without fracture. Researchers discovered single-walled carbon nanotubes (SWCNTs) with diameters ranging from 1 nm to 2 nm and some of the highest values of Young’s modulus, around 1 TPa [Citation7–8]. This can be accounted to their plastic [Citation9], and their fracture behavior under tensile loading [Citation10]. They are also well-organized and have a high aspect ratio. Its tensile strength is nearly 150 GPa because it can withstand up to 15% tensile strain before fracture. This is possible because carbon nanotubes can release high stresses through a process known as elastic buckling [Citation11]. CNTs have a thermal conductivity of 1800–6000 W (m-K) at room temperature, demonstrating their significance in thermal properties as measured by experimental measurements and theoretical calculations [Citation12–13]. Because improving mechanical properties is of particular interest in this paper, observations of CNTs imparting their appealing mechanical properties to brittle materials have been made. As a result, it is a promising filler for polymer nanocomposites. Moreover, numerous industries, including as strain sensing [Citation14], supercapacitors [Citation15], EMI shielding, aerospace applications [Citation16], and high-tech sporting goods [Citation17], have benefited from the use of CNT-Polymer nanocomposites.
Polymers and resins were also thought to be blended with CNTs in order to impart their qualities into the matrix for load bearing purposes [Citation18]. The addition of roughly 1 weight percent (wt.%) of multi-walled carbon nanotubes (MWCNTs) to epoxy resin, for instance, boosted its stiffness and fracture toughness by 6% and 23%, respectively [Citation19–20]. Haggenmueller et al. [Citation21] used a combination of solvent casting and melt mixing to scatter SWNT materials in PMMA. The process also included spinning the composite fibres with a melt spinning technique. The elastic modulus and yield strength of the composite were measured, and the results showed that the properties improved significantly as the percentage loading was increased. A SWCNTs-isotactic polypropylene (iPP) composite was made by Manchado et al. [Citation22] using shear mixing. The findings showed that the Young’s modulus increases in parallel with the SWNT loading in the polymer matrix. The outcomes also demonstrated that the IPP’s tensile modulus improved by 40%, from 0.85 GPa to 1.19 GPa, with a nanomaterial content of 0.75% by weight in the composite. Cadek et al. [Citation23] performed tensile tests on composite films made of polyvinyl alcohol (PVA) and six different types of carbon nanotubes at various nanotube loading levels. The tests revealed that the Young’s modulus increased by a factor of two in all cases. Blake et al. [Citation24] discovered significant improvements in Young’s modulus, strength, and toughness for PVC-based composites reinforced with chlorinated polypropylene grafted carbon nanotubes. Wu and Xu [Citation25] performed MD simulations using Dreiding2.21 and advanced compass force-field on DGEBA/DETDA. The authors have achieved conversions up to 93.7%. Significant improvement was observed on the elastic modulus with degree of conversion. The nano-indentation hardness of the composite above the isolated polymer was increased by 271%, according to research by Gupta et al. [Citation26] on composites comprised of a PU polymer matrix and MWCNT fillers. Additionally, the authors found that a composite loaded with 10 weight percent MWCNT outperformed neat polymer composite in terms of elastic modulus by 290%. Navneeth et al. [Citation27] conducted a number of tests on nanocomposites, including epoxy and polyester nanocomposites with and without CNT reinforcement. Tensile, flexural, shear, and impact tests were performed. In all of the tests, the nanocomposites outperformed the polymers alone. When compared to the Polyester nanocomposites, the Epoxy nanocomposite produced better results. Patel et al. [Citation28] studied 0.1 wt.% Poly(methyl methacrylate) (PMMA)/CNT nanocomposites injection moulded from micro compounders with a co-rotating twin screw extruder. Significant improvement was observed in tensile, fracture, and compressive strength of the reinforced polymer over the pure polymer. Dikshit et al. [Citation29] developed an epoxy, DGEBA, as a matrix that was hardened with DETDA and reinforced with CNT. MD simulations were used to predict the mechanical properties, which were then compared to the properties of epoxy without reinforcement. The study found that the Young’s modulus improved from 2.429 GPa for the non-reinforced epoxy to 13.27 GPa for the reinforced epoxy (DGEBA-DETDA) nanocomposite. Furthermore, as the stain amplitude increased, the Young’s modulus of both models decreased.
Aromatic polyamides are referred to as ‘aramid fibres’ (Afs). These synthetic fibres have a high level of heat resistance, making them a good and trustworthy choice for aerospace and defence technology. These are also utilised for ballistic purposes in the present-day technological period, which ultimately results in rated body armour fabric. Afs have low electrical conductivity and behave as insulators. Due to its chemically inert surface, it has the significant drawback of poor adhesion. The surface adhesion is being improved by researchers employing a variety of techniques, such as chemical activation [Citation30]. Additionally, several studies demonstrate that aramid fibres can be strengthened with nanomaterials like CNTs to increase their electrical conductivity [Citation31]. Kevlar is a synthetic fibre that is both heat-resistant and exceptionally strong. It is a type of para-aramid that is also known by the chemical name PPTA. In the beginning, it was utilised in the tyre industry as a substitute for steel. Although it is possible to employ this as a matrix in composites, very little research has been done on the subject. In order to make hybrid composites, it is combined with other matrix materials and utilised as a co-matrix. When it is spun, it possesses a tensile strength of 3.62 GPa and a relative density of 1.44 g/cm3 [Citation32]. It finds use in a variety of industries, including the ballistics fabrics [Citation33], the automotive industry, and the acoustic industry. Kesiya et al. [Citation34] found that the tensile strength of an EPDM/Kevlar fibre hybrid that was reinforced with nano-silica as a filler had approximately a 109% surplus over its original value. Abdel-Mourad et al. [Citation35] conducted research on the resistance to damage of a number of different nano-fillers when combined with Kevlar KM2 plus/epoxy nanocomposite. The laminated Kevlar/epoxy composite with 0.5 wt.% of MWCNT had the best results when it came to the material’s resistance to damage. Taraghi et al. [Citation36] had reported that the elastic and bending modulus of woven Kevlar/epoxy can be improved by 20% and 40%, respectively, by adding a small amount of MWCNT (less than 1%). The impact strength increased by 45%. The authors have further revealed that the greatest improvements were noticed for a MWCNT concentration of 0.5%. Alsaadi et al. [Citation37] found that the mechanical properties, such as tensile strength, flexural strength, flexural modulus, and toughness, all increased by 6.1%, 31.1%, 8.7%, and 11.8%, respectively, when 0.25 wt.% of graphene nanoplatelets were reinforced in Kevlar epoxy nanocomposite. Sharma et al. [Citation38] reported a 56% increase in elastic modulus at 0.3 Wt.% MWCNT reinforced Kevlar-epoxy nanocomposite. The increased elastic modulus was attributed to improved interfacial properties between the Kevlar fibre and the epoxy matrix. Madarvoni et al. [Citation39–40] conducted DMA analysis on carbon, Kevlar, and hybrid fabrics reinforced with graphene and hexagonal boron nitride and discovered that mechanical properties such as storage modulus and loss modulus increased by 49% and 38%, respectively. Shiju et al. [Citation41] investigated the thermal mechanical properties of a Kevlar-Nomex copolymer using graphene oxide platelets. According to the authors, there was a greater shift in glass transition temperature and improved interfacial interaction between the matrix chain and the reinforcement.
According to the existing literature, the experimental investigation reveals that various nanostructures such as graphene (Gr), hexagonal boron nitride nanosheets (h-BNNS), and carbon nanotubes (CNTs) may improve the mechanical and thermal properties of Kevlar fiber-epoxy nanocomposites. The experimental investigations have not revealed the failure mechanisms of these nanocomposites. The failure of EKE can be studied at the atomic level. Furthermore, the experimental procedures are very expensive in terms of setting the process parameters. There is very little research based on MD simulations to study the mechanical properties of EKE nanocomposites. In the present research, the authors have made an effort to use MD simulations to build a single layer EKE nanocomposite. The layers produced resemble the experimental technique known as the hand layup process. Gr was previously reinforced in the DGEBA/DETDA matrix at weight percentages of 1, 1.5, and 2, and the layer was created in the Material Studio environment. The prepared layer was further processed to obtain the mechanical properties. This study is the first of its kind which may provide a complete explanation of the failure mechanism of Gr reinforced DGEBA/DETDA-Kevlar fiber, taking into account the interaction between DGEBA/DETDA and Kevlar fibre. The manuscript is organised as follows: Specific introduction and literature are presented in section 1; atomistic modelling of DGEBA, DETDA, Gr, and Kevlar fibre and methodology are presented in section 2; construction of DGEBA/DETDA-Kevlar-DGEBA/DETDA layer at different Gr content is presented in section 3; simulation results and discussion are presented in section 4; and conclusions are presented in section 5.
2. Modelling and methodology
In the present research, MD simulation has been performed to study the mechanical properties of Gr and h-BNNS reinforced Kevlar-epoxy nanocomposite. The atomistic models have been created using the Material Studio software and further simulations were done using Large-scale Atomic/Molecular Massively Parallel Simulator (LAMMPS). MD is a computer simulation method which is used to analyze the physical movements or motions of atoms and molecules. The analysis is simulated by allowing the atom and molecules to interact with each other for a fixed amount of time. This is followed by solving Newton’s equations of motions to determine the trajectories of atoms and molecules. It employs the usage of interatomic potentials or force fields to calculate the forces or potential energy between interacting particles.
Diglycidyl Ether of Bisphenol-A (DGEBA) has been selected epoxy for the reinforcement purpose. DGEBA is a thermosetting polymer which is extensively used in aerospace and electronics industries for adhesives, composites, coatings etc. It has excellent cross-linking properties and an irreversible network structure that forms polymer chains when chemically reacting with hardeners such as amines and anhydrides. The resultant compound exhibits exceptional thermomechanical and structural properties. The properties of the final compound closely depend on the cross-linking and network structure [Citation42]. In pure form, DGEBA is a weak material, and its rigidity may be increased by curing with a suitable hardener considering the cross linking properties. In the present research, Diethyl toluene diamine (DETDA) is selected as the hardener due to its superior properties over other hardeners. In the MD method, the curing of the DGEBA and DETDA may be achieved in two methods. In first method includes sketching of the individual molecule of DGEBA and DETDA and manually creating the crosslinked structure based on the possible degree of cross-linking. The created structure is further used for constructing a simulation volume called an amorphous cell with periodic boundary conditions with an initial density lower than the actual density and desired number of molecules. The constructed amorphous cell also defined as the representative composite and MD simulations such as energy minimization, geometry optimization, dynamics, etc. run for stabilizing the model and further used for predicting various mechanical, thermal, and physical properties [Citation43]. In the second method, creating a representative simulation volume with primary molecules of DGEBA and DETDA without any manual crosslinking and imposing various minimization and equilibrium runs to achieve a certain degree of cross-linking. The mechanical, thermal, and physical properties are predicted after running several MD simulations steps.
The second method is relatively cumbersome than the former method which is realistic and more accurate [Citation44]. However, the degree of cross-linking is influenced by several parameters such as cut-off distance, the ratio of hardener and epoxy, and reaction priorities. The first method is used in this study to obtain the simulation volume with chemically cross-linked DGEBA and DETDA. First, in a material studio environment, an atomistic model of DGEBA and DETDA was created. Three molecules of DETDA and seven molecules of DEBGA were used to create a rigid triangular model [Citation45] as shown in . Mechanical properties of the pure DGEBA/DETDA are very low [Citation46–47] which can be enhanced by reinforcing with the nanomaterials such as Gr, CNT, and h-BNNS etc., which has superior mechanical properties. Graphene (Gr) has been demonstrated as one of the potential reinforcement materials for improving the mechanical properties of epoxy, which has an exceptionally high stiffness and strength The influence of Gr reinforcement in DGEBA/DETDA matrix is well established in the previous literature [Citation47–49,Citation57,Citation58]. Thus, based on previous literature, in the present research, DGEBA/DETDA is randomly reinforced with 1%, 1.5%, and 2% Gr. depicts the atomistic model of Gr. The amorphous cell module is used to reinforce the DGEBA/DETDA at a lower density than the actual density. The created model is the representative composite, which is then simulated using energy minimization, geometry optimization, and dynamics. At room temperature, the dynamics are run using a normal temperature pressure (NPT) ensemble. The total simulation time was 10 Pico seconds (ps), with a time step of 0.1 femto seconds (fs) and a total of 100,000 steps.
An atomistic representation of the Kevlar molecule with a chain length of five was constructed within the environment of Material Studio. A representation of an atomistic model containing a repetition unit, head, and tail atoms may be seen in .
The created Kevlar homopolymer is put into the simulation cell with a loading size of 10 polymers and simulated further to achieve an experimental density equivalent to that of the real Kevlar polymer. The simulated density is found to be 1.33 g/cm3, which is very close to the experimental density of 1.44 g/cm3 [39] shown in .
Table 1. Control parameters employed for dynamics.
3. Modelling of epoxy-Kevlar layered composite
To obtain the coating of Gr reinforced DGEBA/DETDA on the Kevlar fibre, a layer was formed with the Kevlar fibre sandwiched between the Gr reinforced DGEBA/DETDA. The layers are referred to as EKE0, EKE1, EKE1.5, and EKE2 based on the wt.% of Gr, where EKE represents epoxy-Kevlar-epoxy and the numeric value represents the wt.% of Gr in epoxy. Energy minimization, geometry optimization, and dynamics are used to stabilise the developed model using the COMPASS II forcefield [Citation52–53]. From the previous literature [Citation24,Citation41,Citation47–49,Citation54–56] it has found that COMPASS II is the most suitable forcefield for polymers which has given satisfactory results for variety of polymers. Moreover, COMPASS II contains a 22 classes of polymers which includes 144 homopolymers and 297 copolymers.
The dynamic simulatuion was conducted using NPT ensemble at room temperature (300 K). The control parameters setting for dynamics run are shown in . Number of atoms at different reinforcement of Gr, final density, initial and final cell parameters are dipicted in . The geometric structures of EKE1, EKE1.5, and EKE2 before and after the equibilaration are shown in . For all the structures, the convergence analysis has been done in geometric optimization steps. The structures converged at 4000 of the optimization steps. From it can be seen that there is small change in the Kevar layer after dynamics simulation which may be due to the application of compressive force. The dynamics simulation results for EKE1, EKE1.5, and EKE2 are shown in . It can be seen that the developed molecular model becomes stable with simulation time. It has been found that the energies of the developed model initially fluctuate with simulation time and become stable as the simulation progresses, as shown in for all the three structures EKE1, EKE1.5, and EKE2. The lower the energy, the higher the stability of the model. The kinetic energy of the model is very low, which shows the stability of the model. The non-bond energy was found to be almost constant throughout the simulation, which supports the claim. Since the simulation was performed at room temperature, the final temperature of the model should have been 300 K. A large fluctuation in the model temperature was observed with the initial simulation, resulting in further energy loss. However, the model stabilised near room temperature, as shown in . The four models EKE0, EKE1, EKE1.5, and EKE2 have final simulated densities of 1.27, 1.29, 1.33, and 1.26 g/cm3, respectively, which is very close to the experimental density of 1.44 g/cm3 of pure Kevlar.
Figure 4. EKE1: (a) before Simulation (b) after simulation; EKE1.5: (c) before simulation (d) after simulation and EKE2: (e) before simulation (f) after simulation.
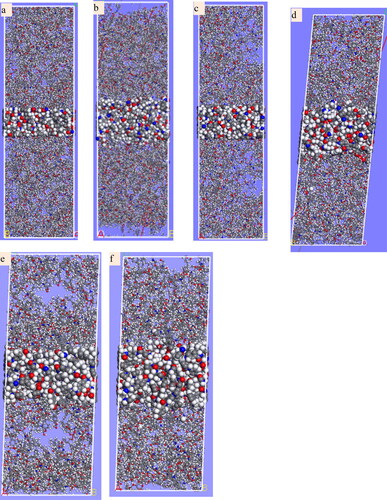
Table 2. Effect of dynamics run on intital and final structure of EKE.
4. Results and discussion
To predict the mechanical properties using the MD simulations three methods viz. constant strain minimization, constant stress, and fluctuation methods are widely used. In the present research constant strain minimization method has been employed with six strain patterns. Some assumptions in this method include the fact that deformation of fixed bond length and angle, as well as configurational entropy, have a negligible impact on mechanical properties such as elastic modulus [Citation24,Citation48]. A small deformation of 0.003 strain amplitude within the elastic range has been applied on the stabilized structures EKE0, EKE1, EKE1.5, and EKE2. Beforehand, the simulated model was allowed for pre-minimization using the smart algorithm without change in geometric properties such as cell parameters. The pre-minimization was run to ensure the prediction of mechanical properties for the most stable model. The possible agglomeration has been studied using the radial distribution function (RDF) which describes how the atoms are radially packed around each other in the system [Citation50]. The RDF study for the Gr reinforced DGEBA/DETDA for 1.5 wt.% of Gr is shown in . From it can be seen that there are three major peaks under 1.5 Å. The two major peaks are at very close distance 1.09 Å and 1.11 Å which reveals that the initial interaction is at the short range. No long-range bond formation occurred which shows that there is no agglomeration occurred and dispersion was adequate. Similar results were obtained for the 1% and 2% of Gr.
The stress-strain relationship in MD simulations for linear elastic materials is governed by Hook’s law, which can be expressed in second order as:
(1)
(1)
σi and εj represent the six-dimensional stress and strain vectors and Cij is a 6 × 6 matrix. The energy method was used to calculate the stiffness matrix which is given by [Citation47]:
(2)
(2)
For the isotropic materials, stress-strain behavior is represented by the Lame coefficients (λ, µ) as:
(3)
(3)
λ, µ may be calculated from Cij as:
(4)
(4)
Other important mechanical properties such as elastic modulus (E), shear modulus (G), bulk modulus (K), and Poisson’s ratio (ν) may be derived from the Lame coefficients (λ, µ) as follows:
(5)
(5)
The Lame coefficients (λ, µ) are identified from the stiffness matrix obtained by the MD simulation at a very small strain amplitude (0.003) using the constant strain method. The identified values are then used to calculate the various average mechanical properties using EquationEquation (5)(5)
(5) . The simulated average elastic modulus of EKE0 was found to be 48.12 GPa, which is higher than the experimental value (39.31 GPa) as reported in [Citation40]. The simulated elastic modulus of 44.85 GPa was discovered by [Citation40] using the mean-field homogenization method (Digimat software), which is quite similar to the outcome (48.12 GPa) of the current study. The experimental values of average elastic modulus depend on various parameters such as processing of epoxy and Kevlar, experimental setup, number of layers, etc., which may introduce defects in the experimental sample. In the present research, simulations have been carried out on a single layer (i.e. one crystal of EKE), which is defect free, thus resulting in a higher average elastic modulus than the experimental value. However, the average elastic modulus is smaller than the pure Kevlar. The experimental elastic modulus of pure Kevlar is 200 GPa [Citation49] and MD simulation revealed 325 GPa for single layer crystal in the loading direction [Citation50]. The reduction in the elastic modulus may be due to the lower value of average elastic modulus of DGEBA/DETDA (2.71 GPa [Citation51,Citation59,Citation60]). However, MD simulations reveals that there is significant enhancement in the average elastic modulus when Gr is added in the of EKE model. At 1%, 1.5%, and 2% of Gr reinforcement, the elastic modulus was found to be 58.43 GPa, 65.67 GPa and 68.57 GPa respectively. The increase in the elastic modulus is attributed to the increased interface properties and stress transfer from DGEBA/DETDA to the Kevlar fiber due to the increasing Gr content in the DGEBA/DETDA matrix. However, the triangular structure of DGEBA/DETDA provides more rigidity to the matrix, and the effective mechanical property of Gr is transferred to the DGEBA/DETDA matrix, which ultimately improves the elastic property of KEK and enables the matrix material to withstand loads, dispersion pressure, and external forces. Gr, on the other hand, may not interact with aliphatic polymer chains due to its nature. The carbon atoms in Gr are connected to one another by three sigma bonds, but the pi electrons, which are present above and below the sheets, are quite mobile. represents the comparison of elastic modulus of EKE0, EKE1, EKE1.5 and EKE2. The rate of increase in elastic modulus at 1 and 1.5% of Gr is more compared to the 2% Gr. This may be due to the short-range agglomeration of Gr at higher percentage. The agglomeration weakens the Kevlar-DGEBA/DETDA interface and also cause for stress concentration. Moreover, the percentage change in elastic modulus is found to be 21.42%, 36.47% and 42.49 for EKE1, EKE1.5 and EKE2 respectively compared to EKE0. The Poisson’s ratio for all the EKE models was found to be in the range of 0.32 to 0.39.
The stress-strain pattern for Gr reinforced EKE nanocomposite is found to be linear as evident from . As evident from , the tensile strength of the EKE0 is 499.53 GPa which increases with the addition of Gr. The maximum stress at break point of EKE 1, EKE1.5 and EKE2 are 958.65 GPA, 1291.89 GPA, and 1765.75 GPa respectively. The profile of stress-strain curve indicates that the nanocomposite has brittle nature. From , it is also evident that the brittleness increases with the increasing content of Gr. In all the cases, as the Gr content increased, the strain rate fell. A similar observation was present in [Citation40]. In typical composites, interphase is primarily thought to contribute to the effect of load transfer. From the MD simulation, it is found that the stress carrying capacity increases with the Gr reinforcement which is attributed to superior interface properties of Gr reinforced DGEBA/DETDA and Kevlar fiber. Unlike to experimental results [Citation36], the strength of the Gr reinforced EKE nanocomposite increases with Gr content which reveals that the addition of Gr enhances the interfacial as well as intermolecular properties and, thus, increase in the load carrying capacity. The ultimate strength of the Gr reinforced EKE is depicted in which also increases with the Gr content in EKE nanocomposite. However, the maximum strain amplitude for the ultimate strength decreases with an increase in the Gr content. EKE0 fails at strain amplitude of 0.012 while EKE1 and EKE1.5 fail at 0.01 strain amplitude respectively and EKE2 at 0.009 strain amplitude.
5. Conclusions
In the present research, DGEBA/DETDA was reinforced with Gr at three wight percent viz. 1%, 1.5% and 2% in order to study the effect on the elastic modulus of layered DGEBA/DETDA-Kevlar using the MD simulations. A layer of Gr reinforced DGEBA/DETDA was applied on both sides of the Kevlar fiber and elastic modulus was predicted using the constant strain method using MD simulations. The following conclusions can be drawn from the present research:
The elastic modulus of the EKE increases with the increasing Gr content in DGEBA/DETDA. The percentage change in elastic modulus is found to be 21.42%, 36.47% and 42.49 for EKE1, EKE1.5 and EKE2 respectively compared to EKE0.
The rate of increase in elastic modulus is more with 1% of Gr when compared to 1.5% and 2% of Gr amounting 21.42%, 12.39% and 4.41% respectively.
The brittleness of the EKE increases with increasing Gr content and the maximum strain amplitude found to be 0.012 for EKE, 0.01 EKE1 and EKE1.5 while EKE2 fails at 0.009 strain amplitude.
The MD simulation revealed that the ultimate compressive strength increases with increasing Gr content.
The current study used industrial recommendations to cross-link DGEBA and DETDA. Future research could investigate the effect of DGEBA/DETDA crosslinking and the reinforcement mechanism of Gr in the epoxy matrix on the elastic modulus of EKE. The predicted elastic moduli in this study are based on a single layer of EKE. The MD simulation can be run by stacking multiple layers. However, increasing the number of layers results in a greater number of atoms, which may necessitate more computational time.
Author contributions
Neetu Chaudhary, Mithilesh K. Dikshit, C Labesh Kumar, Pankaj Sonia, Vimal Kumar Pathak, Kuldeep K Saxena, Sana Sulaiman Hamid and N.Ummal salmaan had substantial contributions to the conception or design of the work and interpretation of data for the work; Neetu Chaudhary, Mithilesh K. Dikshit, C Labesh Kumar were involved in the acquisition, analysis, or interpretation of data for the work; Pankaj Sonia, Vimal Kumar Pathak, Kuldeep K Saxena, Sana Sulaiman Hamid and N.Ummal salmaan drafted the work and revised it critically for important intellectual content and finally approved the version to be published; Vimal Kumar Pathak, Sana Sulaiman Hamid agrees to be accountable for all aspects of the work in ensuring that questions related to the accuracy or integrity of any part of the work are appropriately investigated and resolved.
Disclosure statement
No potential conflict of interest was reported by the author(s).
Data availability statement
The data underlying the results presented in the study are available within the manuscript.
Additional information
Notes on contributors
Neetu Chaudhary
Neetu Chaudhary research student at the Infrastructure Technology Research and Management (IITRAM). She is pursuing her PhD in the department of Mechanical and Aerospace Engineering. Currently, she is working on the Atomistic Simulation of Structural and Thermo-mechanical Properties of h-BNNS Reinforced Nanocomposite. Her area of interest is molecular dynamic simulation and material development.
Mithilesh K. Dikshit
Mithilesh K. Dikshit is an Assistant Professor at India’s Institute of Infrastructure Technology Research and Management (IITRAM). He has a Ph.D. in Mechanical Engineering and a master’s degree in production engineering. He has more than 11 years of teaching and research experience. High Speed Machining, Metal Cutting Mechanics, Composite Materials, Molecular Dynamics, Vibration and Control, and Optimization are among his major research interests. He has organised several conferences and symposiums. He has over 35 research papers and journal articles to his credit.
C. Labesh Kumar
C Labesh Kumar is Assistant Professor in the Department of Mechanical Engineering, Institute of Aeronautical Engineering, Hyderabad, India. His core research expertise’s are in the domain of Production Technology, Joining Process, Automation Quality Control, Advance Manufacturing, Industrial Management, Technology Management, Supply Chain etc. He has rich experience of 11 year in teaching and research. He has published many indexed papers in well reputed journals.
Pankaj Sonia
Pankaj Sonia is Assistant Professor in the Department of Mechanical Engineering, GLA University Mathura, India. His core research expertise’s are in the domain of Materials processing, composite development and synthesis, microstructural characterization and joining of materials. He has rich experience of 12 year in teaching and research. He has published many indexed papers and chapters in well reputed journals and books.
Vimal Kumar Pathak
Vimal Kumar Pathak received his Ph.D. degree in Mechanical Engineering (design) from MNIT Jaipur. He received his M. Tech degree from ISM Dhanbad, India. Currently, he is working as an Assistant Professor in the Department of Mechanical Engineering at Manipal University Jaipur, Jaipur, Rajasthan. His research interest includes optimization, soft computing, composites, metrology etc. He has published more than 70 articles in international Conferences and reputed Journals.
Kuldeep K. Saxena
Kuldeep K Saxena Prof. (Dr.) has done his B.Tech, in Mechanical Engineering and M.Tech in Material Science and Engineering from MNNIT Allahabad. He has completed his doctoral degree from IIT Roorkee. He has 13+ years of experience in academics, research and industry. Prof. Saxena holds expertise in hot deformation behaviour of materials, microstructural characterization of materials, and micro manufacturing. He has served as Senior Research Fellow (SRF) for 2 years and 8 months on a project sponsored by Board of Research in Nuclear Sciences (BRNS), a research unit of Bhabha Atomic Research Centre, Trombay, Mumbai. Dr. Saxena is an author of many book chapters published by reputed publishers such as Elsevier and many more. He has authored 292+ research papers which are published in reputed international journals indexed by SCI/ Scopus. He has organised many International Conferences in India and Abroad. He is currently working as Professor and Head, Department of Research Impact and Outcome (LFTS) in the Division of Research and Development, Lovely Professional University, Phagwara, India. He is an active member of The Indian Institute of Metals (IIM) and Secretary of The Indian Institute of Metals Mathura Chapter. He is also a guest editor in many reputed journals such as Journal of Process Mechanical Engineering (SAGE, SCI, IF 1.8), Indian Journal of Engineering and Materials Science (CSIR, SCI, IF 0.8), International Journal of Interactive Design and Manufacturing (Springer, Scopus & ESCI), Materials today Proceedings at Elsevier platform and many more.
Sana Sulaiman Hamid
Sana Sulaiman Hamid is from Iraq, She is 29 years old, She has received his PhD. from Turkey, and a Master degree from Iraq, Baghdad. She has many research papers on the subject of data aggre-gation, wireless sensor, BEE, optimization technique, right now She is a Faculty on Al-Farahidi University, Communication Technical Engineering, Baghdad, Iraq.
N. Ummal Salmaan
N. Ummal salmaan is Assistant Professor in the Department of Automotive Engineering, Aksum Institute of Technology, Axum, Ethiopia. His core research expertise’s are in the domain of development of various types of composites and their synthesis, microstructural characterization, Materials processing and joining of materials. He has rich experience of 08 year in teaching and research. He has published many indexed papers and chapters in well reputed journals and books.
References
- Gilman JW, Kashiwagi T, Nyden M, et al. Flammability studies of polymer layered silicate nanocomposites: polyolefin, epoxy, and vinyl ester resins. Chem Technol Polymer Addit. 1999;14:1–19.
- Gupta TK, Budarapu PR, Chappidi SR, et al. Advances in carbon based nanomaterials for bio-medical applications. Curr Med Chem. 2019;26(38):6851–6877. doi:10.2174/0929867326666181126113605.
- Kumar PSS, Allamraju KV. A review of natural fiber composites [jute, sisal, kenaf]. Mater Today Proc. 2019;18:2556–2562.
- Budarapu PR, Yb SS, Javvaji B, et al. Vibration analysis of multi-walled carbon nanotubes embedded in elastic medium. Front Struct Civ Eng. 2014;8(2):151–159. doi:10.1007/s11709-014-0247-9.
- Sharma K, Saxena KK, Shukla M. Effect of multiple Stone-Wales and vacancy defects on the mechanical behavior of carbon nanotubes using molecular dynamics. Procedia Engin. 2012;38:3373–3380. doi:10.1016/j.proeng.2012.06.390.
- Saxena KK, Lal A. Comparative molecular dynamics simulation study of mechanical properties of carbon nanotubes with number of stone-Wales and vacancy defects. Procedia Engin. 2012;38:2347–2355. doi:10.1016/j.proeng.2012.06.280.
- Meyyappan M. Carbon nanotubes: Science and Applications. Florida: CRC Press; 2005.
- Yu MF, Files BS, Arepalli S, et al. Tensile loading of ropes of single wall carbon nanotubes and their mechanical properties. Phys Rev Lett. 2000;84(24):5552–5555. doi:10.1103/PhysRevLett.84.5552.
- Yakobson BI. Mechanical relaxation and “intramolecular plasticity” in carbon nanotubes. Appl Phys Lett. 1998;72(8):918–920. doi:10.1063/1.120873.
- Yakobson BI, Brabec CJ, Bernholc J. Structural mechanics of carbon nanotubes: from continuum elasticity to atomistic fracture. J Computer-Aided Mater Des. 1996;3(1-3):173–182. doi:10.1007/BF01185652.
- Lu JP, Han J. Carbon nanotubes and nanotube-based nano devices. Int J Hi Spe Ele Syst. 1998;09(01):101–123. doi:10.1142/S0129156498000063.
- Yi W, Lu L, Dian-Lin Z, et al. Linear specific heat of carbon nanotubes. Phys Rev B. 1999;59(14):R9015–R9018. doi:10.1103/PhysRevB.59.R9015.
- Savin AV, Hu B, Kivshar YS. Thermal conductivity of single-walled carbon nanotubes. Phys Rev B. 2009;80(19):195423. doi:10.1103/PhysRevB.80.195423.
- Zhao J, Dai K, Liu C, et al. A comparison between strain sensing behaviors of carbon black/polypropylene and carbon nanotubes/polypropylene electrically conductive composites. Compos Part A Appl Sci Manufact. 2013;48:129–136. doi:10.1016/j.compositesa.2013.01.004.
- Li D, Liu Y, Lin B, et al. Synthesis of ternary graphene/molybdenum oxide/poly (p-phenylenediamine) nanocomposites for symmetric supercapacitors. RSC Adv. 2015;5(119):98278–98287. doi:10.1039/C5RA18979A.
- Budarapu PR, Y B SS, Natarajan R. Design concepts of an aircraft wing: composite and morphing airfoil with auxetic structures. Front Struct Civ Eng. 2016;10(4):394–408. doi:10.1007/s11709-016-0352-z.
- De Volder MF, Tawfick SH, Baughman RH, et al. Carbon nanotubes: present and future commercial applications. Science. 2013;339(6119):535–539. doi:10.1126/science.1222453.
- Chou T-W, Gao L, Thostenson ET, et al. An assessment of the science and technology of carbon nanotube-based fibers and composites. Compos Sci Technol. 2010;70(1):1–19. doi:10.1016/j.compscitech.2009.10.004.
- Jat RC, Arora K, Anuragi N, et al. 2015. Carbon nanotubes: advance. Ment in science and technology.
- Yang K, Wu Z, Zhou C, et al. Comparison of toughening mechanisms in natural silk-reinforced composites with three epoxy resin matrices. Compos Part A Appl Sci Manufact. 2022;154:106760. doi:10.1016/j.compositesa.2021.106760.
- Haggenmueller R, Gommans HH, Rinzler AG, et al. Aligned single-wall carbon nanotubes in composites by melt processing methods. Chem Phys Lett. 2000;330(3-4):219–225. doi:10.1016/S0009-2614(00)01013-7.
- Manchado ML, Valentini L, Biagiotti J, et al. Thermal and mechanical properties of single-walled carbon nanotubes–polypropylene composites prepared by melt processing. Carbon. 2005;43(7):1499–1505. doi:10.1016/j.carbon.2005.01.031.
- Cadek M, Coleman JN, Ryan KP, et al. Reinforcement of polymers with carbon nanotubes: the role of nanotube surface area. Nano Lett. 2004;4(2):353–356. doi:10.1021/nl035009o.
- Blake R, Coleman JN, Byrne MT, et al. Reinforcement of poly (vinyl chloride) and polystyrene using chlorinated polypropylene grafted carbon nanotubes. J Mater Chem. 2006;16(43):4206–4213. doi:10.1039/b612305h.
- Wu C, Xu W. Atomistic molecular modelling of crosslinked epoxy resin. Polymer. 2006;47(16):6004–6009. doi:10.1016/j.polymer.2006.06.025.
- Gupta TK, Singh BP, Dhakate SR, et al. Improved nanoindentation and microwave shielding properties of modified MWCNT reinforced polyurethane composites. J Mater Chem A. 2013;1(32):9138–9149. doi:10.1039/c3ta11611e.
- Navneeth V, Sankar SP, Prasanth RS, et al. Investigation on the mechanical and stealth behavior of CNT based polymer composites. Mater Today Proc. 2021;39:1682–1687. doi:10.1016/j.matpr.2020.06.152.
- Patel V, Joshi U, Joshi A. Investigating the mechanical properties of nonfunctionalized MWCNT reinforced polymer nanocomposites. Mater Today Proc. 2021;43:3511–3515. doi:10.1016/j.matpr.2020.09.812.
- Dikshit MK, Engle PE. Investigation of mechanical properties of CNT reinforced epoxy nanocomposite: a molecular dynamic simulations. Mater Phys Mechan. 2018;37(1):224–233.
- Thomas S ,Joseph K ,Malhotra SK, et al. (Eds.). Polymer composites, macro-and microcomposites. Vol. 1. Germany: John Wiley & Sons; 2012.
- Xiang C, Lu W, Zhu Y, et al. Carbon nanotube and graphene nanoribbon-coated conductive kevlar fibers. ACS Appl Mater Interfaces. 2012;4(1):131–136. doi:10.1021/am201153b.
- Bencomo-Cisneros JA, Tejeda-Ochoa A, García-Estrada JA, et al. Characterization of kevlar-29 fibers by tensile tests and nanoindentation. J Alloys Compd. 2012;536: S456–S459. doi:10.1016/j.jallcom.2011.11.031.
- Nair AN, Sundharesan S, Al Tubi ISM. Kevlar-based composite material and its applications in body armour: a short literature review. IOP Conf Ser Mater Sci Eng. 2020;987(1):012003. doi:10.1088/1757-899X/987/1/012003.
- George K, Biswal M, Mohanty S, et al. Nanosilica filled EPDM/kevlar fiber hybrid nanocomposites: Mechanical and thermal properties. Mater Today: proc. 2021;41:983–986. doi:10.1016/j.matpr.2020.02.817.
- Mourad AHI, Idrisi AH, Zaaroura N, et al. Damage assessment of nanofiller-reinforced woven kevlar KM2plus/epoxy resin laminated composites. Polymer Testing. 2020;86:106501. doi:10.1016/j.polymertesting.2020.106501.
- Taraghi I, Fereidoon A, Mohyeddin A. The effect of MWCNTs on the mechanical properties of woven kevlar/epoxy composites. Steel Compos Struct. 2014;17(6):825–834. doi:10.12989/scs.2014.17.6.825.
- Alsaadi M, Younus B, Erklig A, et al. Effect of graphene nano-platelets on mechanical and impact characteristics of carbon/kevlar reinforced epoxy hybrid nanocomposites. Proc Instit Mechan Engin Part C J Mechan Engin Sci. 2021;235(23):7139–7151. doi:10.1177/09544062211016883.
- Sharma S, Pathak AK, Singh VN, et al. Excellent mechanical properties of long multiwalled carbon nanotube bridged kevlar fabric. Carbon. 2018;137:104–117. doi:10.1016/j.carbon.2018.05.017.
- Madarvoni S, Ps Rama S. Dynamic mechanical behaviour of graphene, hexagonal boron nitride reinforced carbon-kevlar, hybrid fabric-based epoxy nanocomposites. Polym Polym Compos. 2022;30: doi:10.1177/09673911221107289.
- Madarvoni S, Sreekanth RP. Mechanical characterization of graphene—hexagonal boron Nitride-Based kevlar–carbon hybrid fabric nanocomposites. Polymers. 2022;14(13):2559. doi:10.3390/polym14132559.
- Shiju J, Al-Sagheer F, Ahmad Z. Thermal mechanical properties of graphene nano-composites with Kevlar-Nomex copolymer: a comparison of the physical and chemical interactions. Polymers. 2020;12(11):2740. doi:10.3390/polym12112740.
- Wu C, Xu W. Atomistic molecular simulations of structure and dynamics of crosslinked epoxy resin. Polymer. 2007;48(19):5802–5812. doi:10.1016/j.polymer.2007.07.019.
- Zhang L, Xiong D, Su Z, et al. Molecular dynamics simulation and experimental study of tin growth in SAC lead-free microsolder joints under thermo-mechanical-electrical coupling. Mater Today Commun. 2022;33:104301. doi:10.1016/j.mtcomm.2022.104301.
- Li C, Strachan A. Molecular dynamics predictions of thermal and mechanical properties of thermoset polymer EPON862/DETDA. Polymer. 2011;52(13):2920–2928. doi:10.1016/j.polymer.2011.04.041.
- Tack JL, Ford DM. Thermodynamic and mechanical properties of epoxy resin DGEBF crosslinked with DETDA by molecular dynamics. J Mol Graph Model. 2008;26(8):1269–1275. doi:10.1016/j.jmgm.2007.12.001.
- Dikshit MK, Nair GS, Pathak VK, et al. Investigation of mechanical properties of graphene reinforced epoxy nanocomposite using molecular dynamics. Mater Phys Mechan. 2019;42(2):224–233.
- Chaudhary N, Dikshit MK. A state of art review on the graphene and carbon nanotube reinforced nanocomposites: a molecular dynamics approach. Mater Today Proc. 2021;47:3235–3241.
- Shokuhfar A, Arab B. The effect of cross linking density on the mechanical properties and structure of the epoxy polymers: molecular dynamics simulation. J Mol Model. 2013;19(9):3719–3731. doi:10.1007/s00894-013-1906-9.
- Yang HH. Kevlar aramid fiber. New York (NY): John Wiley & Sons: 1991.
- Chowdhury SC, Sockalingam S, Gillespie JW.Jr, Molecular dynamics modeling of the effect of axial and transverse compression on the residual tensile properties of ballistic fiber. Fibers. 2017;5(1):7. doi:10.3390/fib5010007.
- Qi B, Zhang QX, Bannister M, et al. Investigation of the mechanical properties of DGEBA-based epoxy resin with nanoclay additives. Compos Struct. 2006;75(1-4):514–519. doi:10.1016/j.compstruct.2006.04.032.
- Al Mahmud H, Radue MS, Chinkanjanarot S, et al. Multiscale modeling of epoxy-based nanocomposites reinforced with functionalized and non-functionalized graphene nanoplatelets. Polymers. 2021;13(12):1958. doi:10.3390/polym13121958.
- Yadav A, Kumar A, Sharma K, et al. Determination of elastic constants of functionalized graphene-based epoxy nanocomposites: a molecular modeling and MD simulation study. J Mol Model. 2022;28(6):143. doi:10.1007/s00894-022-05134-7.
- Wazalwar R, Sahu M, Raichur AM. Mechanical properties of aerospace epoxy composites reinforced with 2D nano-fillers: current status and road to industrialization. Nanoscale Adv. 2021;3(10):2741–2776. doi:10.1039/d1na00050k.
- Gholizadeh R, Wang Y. Molecular dynamics simulation of the aggregation phenomenon in the late stages of silica materials preparation. Chem Eng Sci. 2018;184:62–71. doi:10.1016/j.ces.2018.03.045.
- Sun H, Jin Z, Yang C, et al. COMPASS II: extended coverage for polymer and drug-like molecule databases. J Mol Model. 2016;22(2):47. doi:10.1007/s00894-016-2909-0.
- Kumar A, Sharma K, Dixit AR. A review on the mechanical and thermal properties of graphene and graphene-based polymer nanocomposites: understanding of modelling and MD simulation. Mol Simul. 2020;46(2):136–154. doi:10.1080/08927022.2019.1680844.
- Yadav A, Kumar A, Singh PK, et al. Glass transition temperature of functionalized graphene epoxy composites using molecular dynamics simulation. Integr Ferroelectr. 2018;186(1):106–114. doi:10.1080/10584587.2017.1370331.
- Chaudhary N, Dikshit MK. Study of the cross-linking density effect on the mechanical properties of h-BNNS reinforced epoxy nanocomposite part-1: a molecular dynamics simulation. J Mol Model. 2023;29(5):146. doi:10.1007/s00894-023-05552-1.
- Zhang W, Kang S, Liu X, et al. Experimental study of a composite beam externally bonded with a carbon fiber-reinforced plastic plate. J Build Engin. 2023;71:106522. doi:10.1016/j.jobe.2023.106522.