ABSTRACT
Reducing the kerf width in bandsawing has potential in reducing waste while optimising the yield. To be able to reduce the kerf width, understanding the cutting forces becomes critical. In this work, nine cutting teeth with varying band-body thicknesses and side clearances were tested by cutting both heartwood and sapwood of Norway spruce (Picea abies (L.) Karst.) and Scots pine (Pinus sylvestris L.) in frozen and non-frozen conditions. Single cutting teeth were moved into rotating wood samples in the 90–90° cutting direction, with chip thicknesses of 0.9 mm per cut. The main and normal cutting forces were measured. Scots pine had a higher density than Norway spruce and, therefore, a higher main cutting force. Non-frozen sapwood, non-frozen heartwood and frozen heartwood resulted in similar main cutting forces, but frozen sapwood resulted in significantly higher main cutting forces. Reducing the cutting width by about 45% resulted in an approximately 40% reduction in the main cutting force. The normal forces were not significantly affected by the species or cutting width. Frozen heartwood, non-frozen heartwood and non-frozen sapwood had similar normal cutting forces. Frozen sapwood had negative normal forces, and thus self-feeding was observed.
KEYWORDS:
Introduction
In Sweden, approximately 80% of forest owner’s profit on their forests comes from selling to sawmills. In sawmilling, only about 50% of the log will result in sawn timber, their primary income product. The rest is processed into low-value by-products, mainly sawdust, paper-pulp chips and dry chips (Lundahl Citation2009, Lestander Citation2011). An increase in sawn-timber volume yield has significant financial gains and environmental benefits, e.g. increasing the volume of end products that bind carbon dioxide for a long time, such as building material and furniture. Sawdust and other by-products are used as fuel or for paper production, which have very short life cycles.
One approach to achieve higher sawn-timber yield is to use thinner sawblades that create a narrower kerf. Fredriksson and Svensson (Citation2020) showed that the volume yield of sawmills could be increased by 1.5 percentage points per millimetre reduction in kerf width. Current cutting widths of bandsaws in Swedish sawmills are around 3 mm, and reducing this to for example 2 mm, will roughly give an annual economic contribution of 0.5 million euros per year for Swedish sawmills using bandsaws in their production that yield approximately 200,000 m3 of boards per year (Ekevad et al. Citation2017). When reducing the kerf width, it is essential to also maintain the feeding speed in order not to reduce production capacity. Vibrations of the band must be limited to maintain both the surface quality and the sawn timber dimensional accuracy.
When developing sawing tools with a thin kerf, it is vital to study the cutting process and the interaction between tool and workpiece. This has been done since the 1950s when Kivimaa (Citation1950) carried out cutting force tests. Measuring single tooth cutting forces is an accurate approach intended to determine how different tooth parameters, wood conditions, and feeding conditions affect the forces. Cutting force testing is the fundamental way to determine how the wood and cutting tool will interact and behave. The cutting forces are split into three different force directions: the main cutting force directed along the edge movement direction, the normal force (also called the feeding force) and the lateral force (a relatively small side force that can indicate asymmetry in the cutting tools) (Kivimaa Citation1950). The main force has been significantly studied, whereas the normal and lateral forces have been studied less. With thinner kerfs, there is less material removed (if tool stability is maintained) which will likely result in lower cutting forces. Ekevad et al. (Citation2019), however, found no significant effect of the kerf width on the single tooth cutting forces. They reduced the cutting width from 2.9 to 2.5 mm, but they did not see a drop in the main force. Orlowski (Citation2007, Citation2010) tested a narrow kerf frame saw with band thicknesses between 0.8 and 1 mm and found that a 0.2 mm decreases in band thickness lead to a reduced cutting resistance of approximately 20%.
Sawmills operate throughout the year, this means that logs are processed in all temperature conditions. In the north of Sweden, this means that temperatures may drop well below −20°C for extended periods of time, and the sawmills must cut through frozen wood. The moisture content plays an important role when cutting into frozen wood, and consequently the cutting forces can differ considerably between heartwood (HW) and sapwood (SW). Frozen wood tends to have higher mechanical properties such as modulus of rupture, modulus of elasticity, bending strength, shear strength, etc. compared to non-frozen wood, especially at a high moisture content (Hernández et al. Citation2014). This is as, when water freezes, two phenomena are occurring: (1) Above the fibre saturation point (FSP), the free water in the cell lumina freezes and expands, which exerts a compressive force on the cell walls. This makes frozen wood harder to cut as the ice reinforces the cell wall and makes it more rigid (Hernández et al. Citation2014); (2) When temperatures drop below 0°C, water in the cell walls migrates out and condenses as ice crystals on the cell walls, acting as additional reinforcement (Kubler et al. Citation2007). This migration also leaves the cell walls drier (Shmulsky and Shvets Citation2006), increasing the mechanical properties, which results in higher cutting forces.
Axelsson et al. (Citation1993) tested the main cutting forces between −15°C and +20°C and found that at low moisture content (8%), the effect of temperature was negligible on the main cutting force, but at high moisture contents (100% i.e. green sapwood) when there is free water in the wood, the main force increased with decreasing temperatures. Vazquez-Cooz and Meyer (Citation2006) found that a lower temperature resulted in higher main, lateral and normal forces when cutting into two maple species. Tests were done at a moisture content of approximately 13% between −8°C and −19°C. The cutting force into pure ice was significantly lower than that of wood since ice is very brittle. Vazquez-Cooz and Meyer (Citation2006), along with Kollmann and Cote (Citation1968), Kivimaa (Citation1950) and Axelsson et al. (Citation1993) amounted the increase in the main cutting force of frozen wood to the ice crystals that form in the cell wall and cavities which consequently stiffens the cell wall as mentioned above. Orlowski et al. (Citation2009) demonstrated that the specific cutting force increased when cutting into frozen Scots pine with narrow kerf saws (kerf width of 1.25 mm). The specific cutting force is a term to describe the force per volume of material removed. These researchers found that an increase in moisture content could result in a 10–35% increase in the specific cutting force when processing frozen wood. The surfaces of the tested wood were smoother due to the brittleness of frozen wood. Frozen wood has less elastic spring-back as it is more rigid and brittle, resulting in cleaner cuts with a smoother surface. This indicates that lower side clearances could be used (Lunstrum Citation1985). Additionally, the friction, and therefore temperatures of the sawblade, were lower due to the low temperature of frozen wood (Orlowski et al. Citation2009). When analysing the cutting power, Ispas and Campean (Citation2014) found that the cutting forces of frozen wood increased due to the low sawdust evacuation and not due to the interaction between the sawblade and the wood. Orlowski et al. (Citation2009) mention that using a chip breaker could help to clear the gullet from sawdust.
The environmental and economic impacts of reducing kerf widths of saws are highly significant, and therefore thin kerf saw teeth tests were conducted. This research aimed to investigate single cutting teeth cutting forces with varying band thicknesses and clearances, which directly affects the cutting width and, therefore, the kerf width. The interaction between cutting teeth and frozen and non-frozen heart- and sapwood was tested by measuring the main and normal cutting forces. Since Norway spruce and Scots pine are abundant in Scandinavian forests and are the primary species processed in the sawmill industry, they were selected as test material.
Materials and methods
Wood specimen
Specimens were collected from Norway spruce (Picea abies (L.) Karst.) with an average dry density of 300 kg/m3 and Scots pine (Pinus sylvestris L.) with an average dry density of 460 kg/m3. The moisture content (mass of water/mass of dry wood) of Norway spruce was 72% and 154% for heartwood and sapwood, respectively. The moisture content of Scots pine was 44% and 81% for heartwood and sapwood, respectively. Logs were collected from the same forest in the north of Sweden during spring (the growing season), from which specimen of 70 × 70 × 200 mm were cut. The non-frozen specimens were tested at 20°C, whereas the frozen samples were tested at minus 20°C. Examples of the cross-sections can be seen in the CT (computed tomography) scans of . In addition to the cutting of wood, pure ice was also cut. Ice blocks with dimensions 70 × 70 × 200 mm were created using a mould.
Cutting tools
Cutting teeth were cut out from a newly produced industrial bandsaw steel blade with stellite tips. Each tooth’s geometry is described in , where tooth 1 is the reference tooth currently being used in many Swedish sawmills using bandsaws. The other geometries are small alterations from the reference which were decided based on a questionnaire from several sawmillers, as to keep the changed parameters realistic for practical use in the sawmills.
Table 1. Overview of cutting teeth geometries.
Cutting force measurements
Testing was conducted in the 90–90° cutting direction () like rip sawing with a bandsaw. According to Kivimaa (Citation1950) the cutting directions are defined as the orientation of the cutting edge with respect to the grain direction (the first angle) and the movement of the tool relative to the grain (second angle). The cutting speed was 15 m/s, and the depth of cut was 0.9 mm/cut. Ten cuts per kerf and 10 kerfs were made in total for each tooth, resulting in a total kerf depth of 9 mm and a total of 100 cuts. A custom-made cutting force testing machine was used (Axelsson et al. Citation1993). An arm with a diameter of 1 m held the wood specimen, which rotated (controlling the cutting speed) against a stationary cutting tool which was fed towards the wood specimen using a stepper motor (controlling the feed) for each revolution. The main, feeding and lateral forces were measured with three piezoelectric sensors located on the tooth holder. The cutting forces and a schematic of the equipment can be seen in .
Figure 2. Definition of cutting directions. Cutting force tests were made in the 90–90° cutting direction, i.e. the cutting edge and the feeding direction were both 90° to the longitudinal grain direction of the wood.
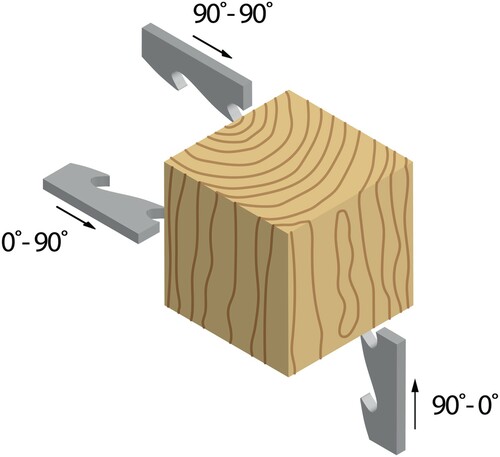
Figure 3. Cutting forces acting on the tool. The experimental setup shows how the wood piece rotates while the tool is moved into the wood by the tooth holder.
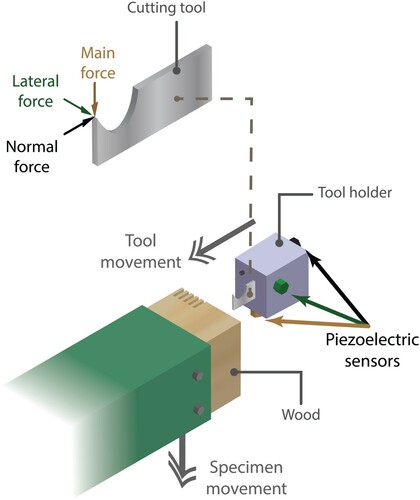
Piezoelectric sensors generate an electric charge (measured as a voltage) when undergoing a force. The three voltages (one per force in each direction) were amplified using three charge amplifiers (Type 2635 Brüel & Kjær), one for each force, and converted using an A/D converter. These signals were read at a frequency of 25 kHz and processed using a custom-made LabView program. The program filtered the signals to reduce unwanted noise and vibrations. A portion of the signal near the kerf's entrance and exit was filtered out in the time domain. The signal was then averaged in time along one cut. Finally, the 10 time-averaged force signals per cut were averaged for each kerf. The presented results are the averages and standard deviations of all 10 kerfs.
Results and discussion
Main cutting force
The effect of cutting width and different wood conditions is clearly shown by comparing tooth no. 1 (w = 2.87 mm) and tooth no. 9 (w = 1.60 mm) in (a,b) respectively. The behaviours in the different wood conditions are similar, but the forces were lower for a narrower cutting width. A reduction of up to about 40% can be seen in the main cutting force when reducing the cutting width approximately 45%. This is a significant reduction in the main force and can result in an increased volume yield for sawmills. Despite the reduction in the main force, the narrowest tool had a small clearance of 0.3 mm. In practice, a clearance of 0.3 mm does not leave much room for resharpening and narrower tools can wear or even break faster. The main cutting forces for pine were almost double the forces when cutting spruce. This was due to the difference in density between the species. This influence of density is well known from the literature (Kivimaa Citation1950, Franz Citation1958, Eyma et al. Citation2004, Lhate et al. Citation2011, Moradpour et al. Citation2013, Chuchala et al. Citation2014, Andrade et al. Citation2019).
Figure 4. Main cutting forces of (a) tooth no.1 (width 2.87 mm) and (b) tooth no. 9 (width 1.6 mm) for sapwood (SW) and heartwood (HW) in frozen and non-frozen condition for Norway spruce and Scots pine.
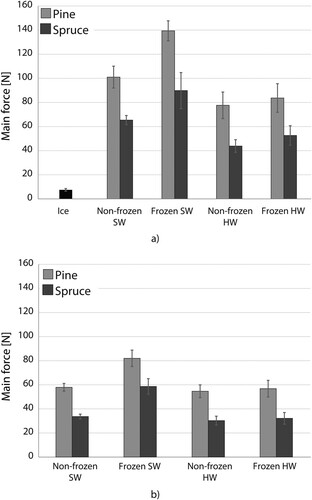
Frozen heartwood resulted in a slightly higher main force when compared to non-frozen heartwood. However, frozen sapwood resulted in significantly higher forces when compared to non-frozen sapwood or frozen heartwood. This corresponds to the results obtained by Axelsson et al. (Citation1993). A lower clearance can be used for cutting frozen sapwood as it has less elastic spring-back. This means that the cutting width could be lower due to a lower clearance. The contribution of force by cutting through ice was small, verifying the work by Vazquez-Cooz and Meyer (Citation2006).
shows the influence of the cutting width on the main cutting force for the four cases of sapwood and heartwood in frozen and non-frozen condition for pine and spruce. Frozen sapwood gave the highest force, and the other three cases gave about equal forces for both species, as shown in .
Figure 5. Main cutting force as a function of cutting width for (a) Norway spruce and (b) Scots pine in frozen and non-frozen sapwood (SW) and heartwood (HW).
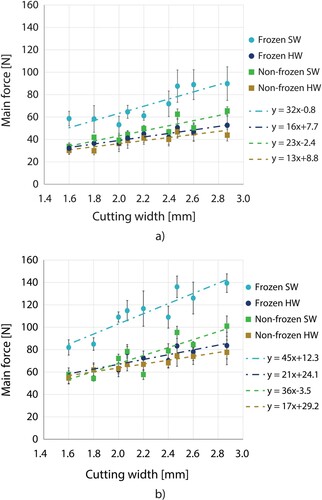
For Scots pine, the y-axis intercepts were not zero (12.3, 24.1 and 29.2 N, respectively) for frozen sapwood, frozen heartwood and non-frozen heartwood. This indicates that even if the cutting width is reduced to zero, there is an element contributing to the main cutting force. One explanation for this is a force contribution from cutting that occurs on the side faces of the tool in which case cutting is done in the 0–90° cutting direction (see ). Side cutting becomes more influential when the cutting width is decreased. In the case of non-frozen sapwood, the y-intercept force was very close to zero. For this case, the side cutting contribution was small. For Norway spruce, the y-axis intercepts were lower but also not zero (7.7 and 8.8 N, respectively) for frozen heartwood and non-frozen heartwood.
Normal cutting force
In , the differences can be seen between tooth no. 1 and no. 9 for different wood conditions. Here no apparent differences can be observed, and the normal force values were very close to zero for frozen heartwood, non-frozen heartwood and non-frozen sapwood for both tooth no. 1 and tooth no. 9. Scots pine tended to have a negative normal force, but the values were very close to zero and did not differ significantly from the Norway spruce values. These minor differences were in line with the work done by Kivimaa (Citation1950).
Figure 6. Normal cutting forces of (a) tooth no.1 (width 2.87 mm) and (b) tooth no. 9 (width 1.6 mm) for sapwood (SW) and heartwood (HW) in frozen and non-frozen condition for Norway spruce and Scots pine.
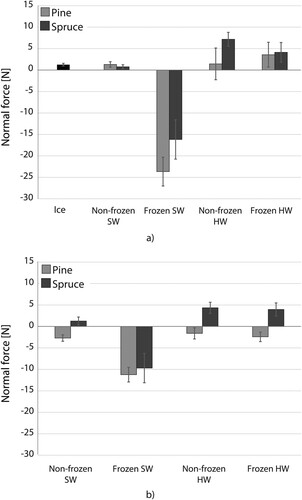
The normal force of frozen sapwood stands out among these results as the force was considerably more negative and thus self-feeding occurred. The ice that reinforced the cell wall, as discussed previously, played an important role here as well. The frozen sapwood's increased rigidity led to less elastic spring-back and less contact between wood and tool on the clearance face. Less contact on the clearance face resulted in less force pushing the tooth away and thus more self-feeding. For non-frozen wood, there was slight contact between the teeth and the wood on the clearance face due to the elastic springback, and thus there was a force pushing the tool away from the wood, which meant less self-feeding. In practice, self-feeding may cause problems since the band is being pulled into the wood. Commonly, the normal force is more affected by tool geometries such as the rake angle (Kivimaa Citation1950) and sharpness (Kivimaa Citation1950, Aknouche et al. Citation2009). The normal force is positive (the tool is pushed away from the wood) at low rake angles. The tool becomes so sharp at higher rake angles that it wears much faster and counteracts the reduction in force due to increased rake angle (Kivimaa Citation1950). The tool geometry can, therefore, be altered to avoid self-feeding when cutting frozen sapwood.
The normal cutting forces are presented in as a function of the cutting width for Norway spruce ad Scots pine. The normal forces increased with increasing cutting widths for frozen heartwood, non-frozen sapwood and non-frozen heartwood. The differences between these results were minimal, and the different conditions (frozen heartwood, non-frozen heartwood and non-frozen sapwood) did not significantly affect the normal forces. The gradients and y-intercepts of the best-fit lines were also very similar. This corresponds to the results obtained by Ekevad et al. (Citation2019).
Figure 7. Normal cutting force as a function of cutting width for (a) Norway spruce and (b) Scots pine in frozen and non-frozen sapwood (SW) and heartwood (HW).
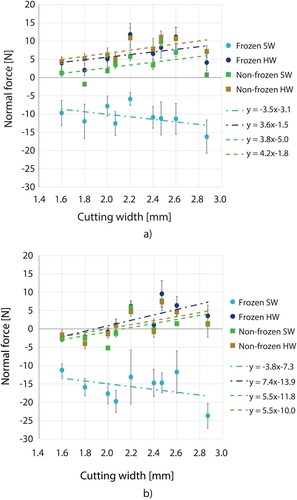
The normal force for frozen sapwood was negative (self-feeding), and the normal force decreased with increasing cutting width. Albeit negative, the gradient was very similar to the frozen heartwood, non-frozen heartwood and non-frozen sapwood.
Surface roughness
The surface roughness was not measured quantitatively, but there was a visual difference in the roughness of the side surfaces between frozen heartwood and frozen sapwood. For all teeth, the cut surfaces of the frozen sapwood were much smoother (in the left half of ), while the cut surfaces of frozen heartwood were rougher (in the right half of ). Fibres were pulled out in the frozen heartwood during cutting. The rigidity of the ice-reinforced sapwood resulted in a smoother breaking of the wood when being cut, resulting in a smoother cut surface, as reported by Lunstrum (Citation1985).
Conclusions
This research aimed to investigate single teeth cutting forces with varying band thicknesses and clearances of non-frozen and frozen sapwood and heartwood of Norway spruce and Scots pine.
The main observations from this research were: (1) Scots pine had a higher main cutting force compared to Norway spruce due to its high density while the normal force remained unaffected. (2) A low cutting width results in a low main cutting force in both frozen and non-frozen heartwood and sapwood. The normal force tends to be low when the cutting width is narrow for frozen heartwood, non-frozen heartwood and non-frozen sapwood, but for frozen sapwood, the normal force is high. (3) A linear trend was observed when comparing the cutting width and main force. The data indicated side cutting by the tool’s side faces under all conditions, which becomes more influential when the cutting width is decreased. (4) High moisture contents (sapwood) in both frozen and non-frozen conditions resulted in higher cutting forces than the counterparts with lower moisture contents (heartwood). (5) Frozen sapwood results in a significantly higher main cutting force compared to frozen heartwood, non-frozen sapwood and non-frozen heartwood. The normal force shows no trends between frozen heartwood, non-frozen heartwood and non-frozen sapwood, whereas frozen sapwood is highly negative, leading to a phenomenon called self-feeding. (6) It was observed that the side surfaces of sapwood were considerably smoother than that of heartwood.
Disclosure statement
No potential conflict of interest was reported by the author(s).
Additional information
Funding
References
- Aknouche, H., Outahyon, A., Nouveau, C., Marchal, R., Zerizer, A. and Butaud, J. C. (2009) Tool wear effect on cutting forces: In routing process of Aleppo Pine wood. Journal of Materials Processing Technology, 209(6), 2918–2922.
- Andrade, A. C. A., Xavier, C. N., Simetti, R. and da Silva, J. (2019) Influence of wood density on the specific cutting force during planning. In Proceedings of the 24th International Wood Machining Seminar, pp. 283–290.
- Axelsson, B., Lundberg, Å and Grönlund, A. (1993) Studies of the main cutting force at and near a cutting edge. Holz als Roh- und Werkstoff, 51, 43–48.
- Chuchala, D., Orlowski, K. A., Sandak, A., Sandak, J., Pauliny, D. and Barański, J. (2014) The effect of wood provenance and density on cutting forces while sawing Scots pine (Pinus sylvestris L.). BioResources, 9(3), 5349–5361.
- Ekevad, M., Berg, S., Öhman, M. and Guo, X. (2017) Potential yield increase with reduced saw kerf deviations when curve sawing. In Proceedings of the 23rd International Wood Machining Seminar (Gdansk University of Technology), pp. 36–42.
- Ekevad, M., Öhman, M. and Guo, X. (2019) Single tooth cutting forces in green Norway Spruce: Experimental results. In Proceedings of the 24th International Wood Machining Seminar (Oregon State University (OSU)), pp. 9–22.
- Eyma, F., Méausoone, P. J. and Martin, P. (2004) Study of the properties of thirteen tropical wood species to improve the prediction of cutting forces in mode B. Annals of Forest Science, 61(1), 55–64.
- Franz, N. C. (1958) An Analysis of the Wood-Cutting Process. The Engineering Research Institute, November, p148.
- Fredriksson, M. and Svensson, M. (2020) A sawmill simulation study of the volume yield changes when sawing with thinner kerfs. In Proceedings of the 2020 Society of Wood Science and Technology International Convention: Renewable Resources for a Sustainable and Healthy Future (International Society of Wood Science and Technology (SWST)), pp. 363–376.
- Hernández, R. E., Passarini, L. and Koubaa, A. (2014) Effects of temperature and moisture content on selected wood mechanical properties involved in the chipping process. Wood Science and Technology, 48(6), 1281–1301.
- Ispas, M. and Campean, M. (2014) Experimental research on sawing frozen wood. Bulletin of the Transilvania University of Brasov. Forestry, Wood Industry, Agricultural Food Engineering. Series II, 7(1), 51.
- Kivimaa, E. (1950) Cutting Forces in Wood Working (Helsinki: Julkaisu/Valtion teknillinen tutkimuslaitos).
- Kollmann, F. F. and Cote, W. A. (1968) Principles of Wood Science and Technology: I Solid Wood (Berlin: Springer).
- Kubler, H., Liang, L. and Chang, L. (2007) Thermal expansion of moist wood. Wood and Fiber Science, 5(3), 257–267.
- Lestander, D. (2011) Competition for forest fuels in Sweden – Exploring the possibilities of modeling forest fuel markets in a regional partial equilibrium framework. Master Thesis, Swedish University of Agricultural Sciences, Uppsala, Sweden.
- Lhate, I., Cristóvão, L., Ekevad, M. and Sitoe, R. (2011) Cutting forces for wood of lesser used species from Mozambique. In Proceedings of the 20th International Wood Machining Seminar (Skellefteå: Luleå University of Technology), pp. 444–451.
- Lundahl, C. G. (2009) Total quality management in sawmills. PhD Thesis. Luleå University of Technology, Skellefteå, Sweden.
- Lunstrum, S. J. (1985) Balanced saw performance. U.S. Department of Agriculture, Forest Service, Forest Products Utilization, Technical report no. 12, pp. 1–17.
- Moradpour, P., Doosthoseini, K., Scholz, F. and Tarmian, A. (2013) Cutting forces in bandsaw processing of oak and beech wood as affected by wood moisture content and cutting directions. European Journal of Wood and Wood Products, 71(6), 747–754.
- Orlowski, K. (2007) Experimental studies on specific cutting resistance while cutting with narrow-kerf saws. Advances in Manufacturing Science and Technology, 31(1), 49–63.
- Orlowski, K., Sandak, J., Negri, M. and Dzurenda, L. (2009) Sawing frozen wood with narrow kerf saws: energy and quality effects. Forest Products Journal, 59(3), 79–83.
- Orlowski, K. (2010) The fundamentals of narrow-kerf sawing: The mechanics and quality of cutting. Technical University in Zvolen.
- Shmulsky, R. and Shvets, V. (2006) The effect of subzero temperatures on FSP of cottonwood. Forest Products Journal, 56(2), 74.
- Vazquez-Cooz, I. and Meyer, R. W. (2006) Cutting forces for tension and normal wood of maple. Forest Products Journal, 56(4), 26–34.