ABSTRACT
In an effort to increase sustainability and reduce CO2 emissions in the automotive sector, the use of renewable wood-based materials for structural elements in vehicles is gaining attention. Less durable, but locally available, wood species can be modified chemically or physically to increase their stability against degradation and make them a viable alternative to less sustainable materials even in outdoor applications. One common wood modification process is acetylation. With regard to using modified veneers in the outer layers of plywood for vehicle components, this study investigates the resistance of acetylated radiata pine veneers to automotive chemicals (distilled water, acetone, biodiesel, gasoline, anti-freeze). The specimens were exposed to the chemicals through two methods, the (1) immersion and (2) blotting paper test. Then, tensile tests were conducted to explore the influence of those chemicals on the mechanical behavior of the veneers. While in the immersion test, the highest mass increase was observed for distilled water (126 wt%), in the blotting paper test, it was found for the anti-freeze (81 wt%). In general, the acetylated veneers showed a good chemical resistance. No statistically significant influence of the chemicals on the tensile strength was observed.
Introduction
Sustainability has become a major target for many industries as legislation, particularly on a European level, is forcing manufacturers to reduce CO2 emissions of their processes and products (European Commission 17.05. Citation2018). In this context, vehicles, either for personal use, public transport or transport of goods, play an important role with the electrification of cars being an already visible and unstoppable trend that replaces fossil-fuelled combustion engines by electric engines (Ruiz et al. Citation2018, Gryparis et al. Citation2020). However, a car contains a wealth of non-sustainable parts (Ryntz and Kozora Citation2019). This comprises in particular different types of polymers that are used for interior or exterior applications, as well as a range of metals that are employed as structural elements of a car frame. These materials are used because they have certain physical properties (e.g. polymers: deformation properties, low weight; metals: mechanical strength), making them difficult to be replaced by more sustainable materials. According to (Andresen et al. Citation2012) first initiatives for bio-based products in car-structures were already taken by Henry Ford back in the 1930s. He demonstrated that soybean-based plastic can be used for structural purposes in automotive applications. Further studies on the potential of using bio-based materials and composites in industrial applications like the automotive industry were conducted by Chum (Citation1989), Rowell (Citation1992) or Holbery and Houston (Citation2006). The motivation for using wood-based materials in mechanical engineering has been diverse: limited metal raw material supply and metal workers (DeHavilland Mosquito), low up-front costs for machines (Marcos GT1600) or good vibration damping (MyEsel bike, alpine skis). Recent initiatives indicate that the use of renewable materials – especially wood – for load-bearing or impact-absorbing elements in cars is yielding promising results (Jost et al. Citation2014, Leitgeb et al. Citation2016, Jost et al. Citation2018, Baumann et al. Citation2019, Baumann et al. Citation2020, Große et al. Citation2022). Past and current research in this domain include for example the projects HAMMER, For(s)tschritt, WoodC.A.R., MoveWood and CARpenTiER. Wood is an anisotropic material and its properties depend strongly on the species concomitant with its chemical composition, growing features, growth-ring-structure, environmental aspects, and harvesting season (Kollmann Citation1951, Desch and Dinwoodie Citation1996). Wood is biodegradable, although its chemical composition and morphology makes it rather stable against short time degradation (Zimmer et al. Citation2003). Stability against degradation is hugely dependent on the moisture content which goes hand in hand with the vulnerability against bacteria and fungi (Levy and Eveleigh Citation1990). Apart from the material degradation, the moisture content hugely impacts the dimensional stability and mechanical properties up to the fiber saturation point (USDA Forest Service, Forest Products Laboratory Citation2021). The fiber saturation point defines the level of moisture content where water can no longer be bonded in the cell walls but instead is appearing as free water in the lumen and cavities. This point is dependent on the wood species and on the general location within the tree but averages at a moisture content of roughly 30%. Influencing factors for the wettability of wood are the polarity, heterogeneity, surface roughness porosity and grain-direction (Moghaddam et al. Citation2014). According to (Ahmed et al. Citation2011), the permeability is influenced by factors like the anatomical structure, the liquid properties as well as the capillary radius of wood cells.
For outdoor applications requiring particular stability against degradation, often tropical wood species with high durability as well as a high dimensional stability have been used so far (Militz and Krause Citation2004, Lankveld et al. Citation2014, Žlahtič-Zupanc et al. Citation2018). For naturally less durable wood species, treatment procedures are needed to achieve the required durability. These either comprise a chemical (e.g. impregnation with biocides) or physical treatment (e.g. drying) (Teacă and Tanasă Citation2020).
A typical chemical treatment is the so called acetylation. Research on this kind of wood modification dates back to the late 1920s (Fuchs Citation1928) and (Horn Citation1928) who made first attempts on the acetylation of spruce and beech wood. According to (Ibach and Rowell Citation2021) research on the acetylation of wood has been taken up during the second half of the 1940s at the Forest Products Laboratory starting to use ketene gas in order to modify spruce samples. During the mid-1950s a report was published by (Tarkow and Stamm Citation1955) who concluded that acetylation leads to an improvement of the surface properties and a dimensional stabilization without affecting the mechanical properties. However, they concluded that further research would be required in order to assess the glue- and paintability as well as possible corrosion on metals and economic aspects. According to (Slabohm et al. Citation2022) further decades of research on solid wood and composites up to 1990s and early 2000s lead to the first commercially available acetylated wood products.
Ideally, the treated wood should not release any toxic substances and no biocidal substances should be used to achieve biological resistance (Hill Citation2006). Further, the disposal of treated wood should be environmentally uncritical (Jones and Sandberg Citation2020, Teacă and Tanasă Citation2020; Lai and Plönning Citation2019). Environmentally uncritical means that treated wood can be disposed at the end of life without any greater hazards than with unmodified wood (Jones and Sandberg Citation2020) According to (Hill Citation2006) wood modification involves the action of a chemical, biological or physical agent upon the material, resulting in a desired property enhancement during the service life of the modified wood. The modified wood itself should be nontoxic under service conditions and furthermore, there should be no release of any toxic substances during service or at end of life, following disposal or recycling of the modified wood. If the modification is intended for improved resistance to biological attack, then the mode of action should be non-biocidal. As many authors point out, wood modification can be applied to increase dimensional stability, durability, moisture resistance, biological resistance and weathering (UV) resistance (Hill Citation2006, Lahtela and Karki Citation2015, Jones and Sandberg Citation2020; Lai and Plönning). Sustainable chemical modification of wood and its components involve the use of hydrophobization agents that render the wood surface less accessible for water and microorganisms that both curb durability of wood (Mantanis Citation2017). A common strategy is to employ fatty acids or their anhydrides (particularly acetic acid anhydride – “acetylation”) for wood modification as those compounds can also be produced from biomass (Lahtela and Karki Citation2015, Graf et al. Citation2019, Jones and Sandberg Citation2020). In an article from 2004, Militz and Krause (Militz and Krause Citation2004) further write that acetylation does not alter the main mechanical properties of wood such as its flexural strength, compressive strength, Young’s modulus and impact bending strength. However, the literature is not clear concerning this aspect since e.g. Wang et al. (Citation2021) state that the influence of acetylation on these properties depends strongly on the modified wood species. This modification leads to a replacement of hydroxyl groups in the cell walls by acetyl groups, a lower cell wall moisture content and a decreased accessibility of remaining non-modified hydroxyl groups, which are the main functional groups for the interaction with water molecules (Mantanis Citation2017, Beck et al. Citation2018, Digaitis et al. Citation2021). The resulting increase in dimensional stability can be quantified using the anti-swelling efficiency (ASE), which increases with the weight percent gain (WPG) that happens as a result of acetylation (Militz and Krause Citation2004, Engelung Thybring Citation2013, Hom et al. Citation2020). For yellow birch, the ASE is around 70% at a WPG of 23% (Engelung Thybring Citation2013). For beech, values are around 50% (WPG = 10%) and 72% (WPG = 18%), respectively (Engelung Thybring Citation2013). Generally, the WPG of acetylated wood is approximately 20% (Mantanis Citation2017). The equilibrium moisture content (MC) at standard climate (20°C, 65% RH) is reduced from 10% to 12% to approximately 5% in hardwoods (beech) (Graf et al. Citation2019). The commercially available acetylated radiata pine wood (Accoya®) has an 80% reduced swelling compared to unmodified radiata pine and an equilibrium moisture content of 3.3, 4.1 and 7.5% at a temperature of 20°C and a relative humidity of 65%, 80% and 90%, respectively.
However, for the use of wood-based materials as load bearing elements in cars, one needs to consider many more liquids other than water that might potentially come into contact with the car frame since they could promote degradation (Austrian Standards International). These involve fluids needed for the operation of the vehicle, such as gasoline, engine oils, hydraulic oils, brake fluids, anti-freeze agents, body sealing compounds, cavity sealing compound, windscreen-washer fluid and cold cleaner, as well as fluids from the environment, such as pine resin, bird excrements and different types of salts (e.g. NaCl) used in winter to prevent ice formation on streets (Austrian Standards International).
In general, wood is very resistant to many chemicals like weak acids and alkaline solutions, salt solutions, alcohols and gasoline (Kass et al. Citation1970, O'Halloran Citation1975, Kollmann Citation1982). However, the resistance varies depending on the species and hardwoods like birch and beech tend to have a lower chemical resistance than softwoods like radiata pine (Kass et al. Citation1970). The chemicals, which can degrade wood most strongly are acids and alkaline solutions with a very low (< 2) and a very high (> 10) pH value, respectively (Kass et al. Citation1970, O'Halloran Citation1975, Schnabel Citation2009). While strong acids can destroy wood, strong alkaline solutions lead to swelling and weakening (O'Halloran Citation1975). Diluted acids and alkaline solutions may weaken wood depending on temperature, pH-value and chemical composition in some cases but are generally expected to have little effect on wood (O'Halloran Citation1975). Regarding the adsorption of test liquids like ethylene glycol, isopropyl alcohol or gasoline, the behavior between untreated and acetylated wood is quite dependent on the liquid (Ibach and Rowell Citation2021). For balsa wood, acetylation decreases the adsorption of ethylene glycol and isopropyl alcohol, but increases the adsorption of liquid gasoline.
Laminated veneer lumber (LVL) and plywood are widely used in vehicle construction, e.g. as a load-bed in trailers, trucks and refrigerated bodies, due to their combination of favorable properties like low price, high strength-to-weight ratio, good noise vibration behavior, global availability and reasonable ecology (APA – The Engineered Wood Association; Metsä Group; Corrado Cremonini et al. Citation2015). Their durability is increased through a phenolic resin moisture barrier, which is synthesized from phenol and formaldehyde (PF) (Galos et al. Citation2017, Grinins et al. Citation2021). Commercially produced PF is sourced from petroleum and therefore limits the sustainability of products where it is used as paint, adhesive or coating (Jia et al. Citation2020, Sarika et al. Citation2020).
The hypothesis of this study is that the durability of LVL and plywood can be increased by a modification of the outer plies – in particular when exposed to chemicals that it might face during service life – and with a limited effect on the sustainability. With regard to using plywood in structural car parts, the present study explores – as a first step – the effect of automotive chemicals on the mechanical behavior of veneers, which later shall be employed in hybrid modified-untreated plywood panels. As a measure for the mechanical performance, the tensile strength is used because it is a common measure and easier to determine than the bending strength, which is also often used (Buchelt and Wagenführ Citation2008, Buchelt and Pfriem Citation2011, Pramreiter et al. Citation2021). Other methods like compression tests are not well feasible for veneer materials. Non-mechanical aspects like e.g. discoloration are not of interest since they are not relevant for function and safety related aspects. The research questions of this study are:
To what extent are the different test liquids absorbed and adsorbed by the veneer samples?
Do the test liquids influence the tensile strength of the veneer samples?
Materials and methods
Sliced veneers of acetylated Radiata pine with a thickness of 0.8 mm, a width of 180 mm and a length of 2600 mm were provided by M. Hechenblaickner Holzhandel GmbH, Graz, Austria. The veneers were produced by slicing already acetylated boards from Radiata pine. The wood modification (acetylation) of the boards was carried out under industrial conditions by Accsys Technologies; Arnhem, the Netherlands PLC.
Employing a laser-cutter (Trotec Speedy 360 flexx), dog-bone shaped samples (see ) (Pramreiter et al. Citation2021) were extracted from the veneer sheets. After cutting and prior to conducting the tests, the samples were stored in a climate chamber at standard climate conditions (23°C, 50 RH) (Austrian Standards Institute 01.03. Citation1994) until theoretical mass constancy was achieved.
Figure 1. Dimensions of dog-bone shaped samples (Pramreiter et al. Citation2021).
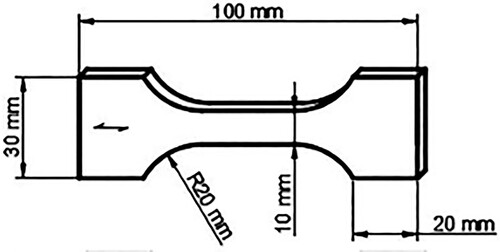
The samples were weighed and visually graded prior to testing and assigned evenly to the two method groups (blotting paper test/immersion test) as well as to the different test groups considering density and visual grain angle. While the method group refers to the applied test method, the test groups within each method group refer to the different test liquids that the samples are exposed to. A total of 102 samples was prepared.
Five test liquids were used, namely:
Distilled water (DIN43530 and EN285)
Acetone (> 50 wt.% purity)
Biodiesel (EN 14214)
Gasoline (EN228 (ROZ 95))
Anti-freeze liquid (water-glycol mixture with the ratio 1:1, the anti-freeze prior to mixing consisted of < 93% monoethylene glycol)
Biodiesel and gasoline were obtained from an ordinary petrol station. The test liquids were selected with the aim of representing a range of chemicals that may come into contact with structural car parts and have a potentially negative impact on their mechanical properties if they are made of wood. As a first reference, the environmental attack chart by Ashby (Ashby Citation1999, p. 62) was taken into account, which addresses aerated water, salt water, strong acids, strong alkalis, organic solvents and UV radiation. Of these categories only water and organic solvents were identified as liquids that commonly appear around vehicles and may alter the mechanical properties of wooden parts. All test liquids but acetone were then selected considering the list of test substances for automotive coatings proposed in the ISO 2812-1:2018 (Austrian Standards International) and ISO 2812-2:2019 (Austrian Standards International). Oils were rejected as test liquids since they usually have a positive rather than a negative effect on the mechanical properties of wood (Küch Citation1939). Acetone was chosen as an additional test liquid to represent cleaning products.
The two different methods used for the exposure of the samples to the chemicals ((1) immersion test and (2) blotting paper test) are explained in more detail below. For each liquid, 6 samples were tested in the immersion test and 13 in the blotting paper test.
Test procedure of the immersion tests
Prior to the liquid exposure, the mass, the thickness and the width of the samples were determined using a balance and a digital caliper. Then, the samples were put into glass containers (see ). The samples were stacked on top of each other, with metal spacers in between to prevent the samples from floating. A stainless steel alloy was used in order to avoid any reactions between the metal spacers and the test liquids. The respective test liquid was carefully added until all samples were fully submerged. The glass containers were closed with a lid to prevent evaporation of the test liquid. While the samples were exposed to their respective test liquid for 24 h (exception: acetone: only two minutes), the samples of the reference test group remained in the climate chamber. The reason why acetone was the only test liquid with an exposure time of only two minutes is its high volatility.
When removing the samples from the containers, excess liquid was removed by placing the samples between two blotting papers. Then, their mass, thickness and width were determined again, so that liquid absorption and dimensional stability could be evaluated. Immediately after the measurements, tensile tests (in longitudinal direction) were conducted using the universal-testing-machine Zwick-Roell Z020 in order to measure the effect of the liquids on the tensile strength. The test speed was set to 100 mm/min. The ambient temperature and humidity conditions at which the tensile strength tests were performed, were identical to the climate chamber (23°C, 50% RH).
Test procedure of the blotting paper tests
During the immersion tests, failure in the clamping zone was observed in several samples (see (a)). Even if this was not the standard failure type, the blotting paper test samples were reinforced at the ends to prevent failure in the clamping zone and to promote breaking in the central part of the sample. For this reinforcement, birch veneers (30 × 15 × 1 mm) were glued on both sides and at both ends of each sample with the fiber orientation perpendicular to the tensile test direction, so that a three-layer, locked structure was obtained (see (b)). According to the norm EN789-2005 (Austrian Standards Institute 01.04. Citation2005), which proposes tests to determine mechanical properties of wood based panels, test results of samples with failure like the one shown in (b) need to be reported separately because the failure is in the transition zone. However, only very few samples failed in a “correct” way. Therefore, to be able to statistically compare the results of the different test groups, all of the samples were considered as valid. Prior to the liquid exposure, the mass, thickness and width of the samples were determined using a balance (accuracy: ±0.0001 g) and a digital calliper (accuracy: ±0.01 mm). Then, a blotting paper strip (10 × 20 mm) was placed on the central area of each sample and on the side that displayed fewer resin channels, which appear as brown narrow rays and can be clearly seen macroscopically (see (c)).
Figure 3. (#a) Non-reinforced sample with failure in the clamping zone, (b) Reinforced sample with failure closer to the central area as observed in the majority of the reinforced samples, (c) Sample with blotting paper strip.
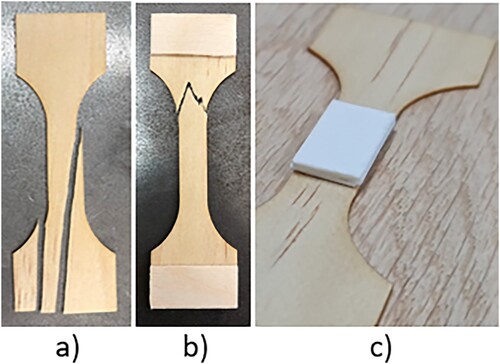
Afterwards, a defined amount of liquid (see ) was dripped onto the blotting paper strip and a cover was placed on top to prevent evaporation of the test liquid. To ensure proper wetting of all samples throughout the exposure time, liquid was reapplied to some samples after a certain time (). Unlike the anti-freeze, biodiesel and distilled water samples, which were exposed to the liquid for 24 h, the acetone and gasoline samples were exposed to the liquid for a reduced time of 1 h because of the strong tendency of those liquids to evaporate quickly. While the samples were exposed to their respective test liquid, the samples of the reference test group remained untouched. Immediately after the blotting paper was removed, the mass, thickness and width of each sample were determined again, so that liquid absorption and dimensional stability could be evaluated. Then, tensile tests (ZwickRoell Proline 20kN) were performed to measure the tensile strength. The test speed was set to 0.75 mm/min and the force cut-off threshold was set to 30% of the maximum force. The ambient temperature and humidity, at which the tensile tests were performed, were identical to the climate chamber (23°C, 50% RH).
Table 1. Amount of test liquid and exposure time of the blotting paper test samples.
Results
Absorbance and adsorbance of test liquids by the samples
One strategy to measure the liquid intake of the samples was to measure their thickness before and after exposure using a calliper. However, due to the soft and spongy nature of the veneer samples, especially after the exposure, the necessary pressure for the measurement could not be achieved and therefore, the measured results were imprecise. Furthermore, swelling alone is not an ideal indicator as it is only leading to a volume change up to the fiber saturation point. Further liquids within the lumen or cavities do not affect the volume at all. Thus, relying on the mass increase of the samples in % as an indicator for the absorbance and adsorbance of the test liquids seemed more reasonable. shows the density of the samples before (ordinate) and their mass increase in % after (abscissa) the exposure to the test liquid. The average density of the blotting paper test samples was 382.27 ± 28.02 g, while it was 356.22 ± 24.57 g for the immersion test samples. It should be noted that in the blotting paper tests, the density is distorted because the applied reinforcements were made of a different wood species than the samples themselves and because the mass, which included the reinforcements was correlated to the volume excluding the reinforcements. Therefore, the densities between the immersion and the blotting paper test must not be compared. Concerning the mass increase due to the exposure to the liquid, it must be noted that the immersion test samples were fully submerged in the test liquids. In the blotting paper tests, though, only the central part of each sample was exposed to the liquid. It was not possible to evaluate how much the liquid in the blotting paper tests spread from the central part over the whole sample.
Figure 4. Mass increase in % of the immersion test samples (a) and the blotting paper test samples (b). While the anti-freeze was absorbed well in both tests, the distilled water was absorbed very well in the immersion tests but very poorly in the blotting paper tests.
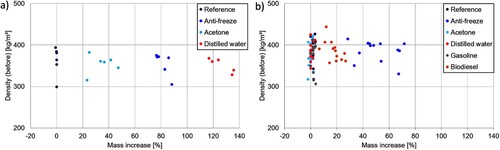
It must be noted further that the acetone evaporated very quickly after removing the samples from the liquid (immersion test). The rate of mass loss during weighing amounted to approximately 0.01 grams per second. By the time the tensile tests were performed (approximately 7 min after taking the samples out of the liquid), the acetone samples were already dry.
In , it can be observed that the anti-freeze was absorbed well in both tests. Interestingly, the distilled water, which was absorbed most in the immersion tests, did not seem to be absorbed in the blotting paper tests at all.
Moreover, it was observed that the distilled water became brownish and lead to a bleaching of the veneer samples in the immersion tests (see ). In the case of the other test liquids, no such color changes were noted.
Influence of test liquids on the tensile strength of the samples
Since the density of veneer has an influence on its tensile strength (Staudacher Citation2015), the samples were assigned as evenly as possible to the different method and test groups considering their density as described in the methods section. To investigate whether the test liquids have an influence on the tensile strength of the samples, first an influence of the different density distributions needs to be ruled out. shows boxplots of the density of the samples of each test group prior to their exposure to the liquids. The stars denote the mean value of each test group. A more thorough legend for the boxplots can be found in the Appendix. For the reasons mentioned in the previous chapter, the displayed densities of the blotting paper test samples are higher than the ones of the immersion test samples. Within one method group (immersion/blotting paper) though, the measured densities seem (see ) to be in the same range and should therefore not influence the tensile strength values.
Figure 6. Boxplots of the density before exposure to liquid of the immersion tests (a) and the blotting paper tests (b). Within each kind of method group, the densities of the different test groups lie within the same range. *A legend for the boxplots can be found in the Appendix.
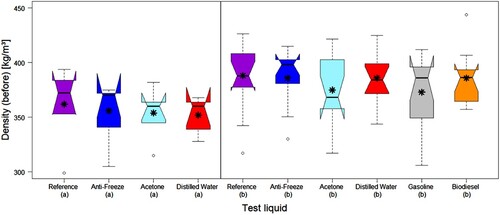
To verify whether there is a statistically significant difference between the means of the densities, an analysis of variance (ANOVA) was conducted. According to the ANOVA, no difference between the mean densities within the immersion test groups (p = 0.92 > 0.05) and the blotting paper test groups (p = 0.66> 0.05) was found. Since the ANOVA assumes homogeneity of variance and normality of the test data, the Levene’s test as well as the Shapiro–Wilk test were carried out for all test groups. The estimated p-value of Levene’s test is 0.91 (> 0.05). Therefore, similar variances of all test groups can be expected. The calculated values of the Shapiro–Wilk tests are given in and for the immersion and the blotting paper test groups, respectively. For three of the ten test groups, the p-value of the Shapiro–Wilk test is < 0.05, which means that normality was only found for the seven remaining groups. Therefore, the non-parametric Kruskal–Wallis test was additionally conducted and a p-value of 0.59 and 0.78 was found for the immersion test groups and the blotting paper test groups, respectively. Therefore, the Kruskal–Wallis test results agree with the results from the ANOVA and there is no significant variation of the density values between the different test groups. Therefore, it can be concluded that the density values of the different density groups do not influence the results of the tensile tests.
Table 2. Results from the Shapiro-Wilk test, the ANOVA and the Kruskal-Wallis test of the density (before) of the immersion test samples.
Table 3. Results from the Shapiro-Wilk test, the ANOVA and the Kruskal-Wallis test of the density (before) of the blotting paper test samples.
In , boxplots of the tensile strength of the samples of each test group are presented. According to Levene’s test (p = 0.50 > 0.05), homogeneity of variance between all test groups is given. The results of the unpaired t-tests as well as the Shapiro–Wilk tests are presented in for the immersion tests and in for the blotting paper tests. According to the unpaired t-tests between each test group and the corresponding reference group, no statistically significant influence of the test liquids on the tensile strength exists. Since according to the estimated p-values of the Shapiro–Wilk tests, normality can be assumed for all but one test group (Gasoline (b): p = 0.02), the non-parametric Mann–Whitney-U test was conducted additionally for that case. The estimated p-value (p = 1.00) of the Mann–Whitney-U test confirms that there is also no significant difference between the tensile strength of the gasoline and the reference test group.
Figure 7. Tensile strength boxplots of the immersion tests (a) and the blotting paper tests (b). No statistically significant influence of the test liquids on the tensile strength was found. *A legend for the boxplots can be found in the Appendix.
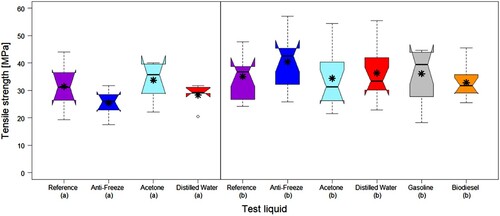
Table 4. Results from the Shapiro-Wilk test and the unpaired t-test of the tensile strength of reference samples vs. exposed samples from the immersion tests.
Table 5. Results from the Shapiro-Wilk test and the unpaired t-test of the tensile strength of reference samples vs. exposed samples from the blotting paper tests.
Discussion
As mentioned before, the anti-freeze was absorbed well in both test methods. However, the distilled water, which was absorbed most in the immersion tests, did not seem to be absorbed in the blotting paper tests at all. Possibly, the blotting paper absorbs the water so well, that it does not pass on the liquid to the veneer any more. Another explanation might be that the vapor pressure of ethylene glycol (main constituent of undiluted anti-freeze) is approximately 0.089 mg Hg at 25°C, which is much lower than the vapor pressure of water (23.769 mm Hg at 25°C) (Wexler Citation1976, Rusdi et al. Citation2005, Roy Citation2016). If the (surrounding) pressure is lower than the vapor pressure of a liquid substance, the liquid evaporates (Persaud et al. Citation2005). Therefore, the anti-freeze test liquid, which is a water-ethylene glycol mixture evaporates much less easily than water or acetone (Rusdi et al. Citation2005). The little amount of liquid that was available for absorbance in the blotting paper tests – as opposed to the immersion tests where the liquid could also be absorbed via the end grains – in combination with the stronger tendency of water to evaporate might have led to little to non-existent increase of weight of the distilled water samples in the blotting paper tests. The vapor pressure might not have played such a large role in the immersion tests, since in that case, the liquids could arguably penetrate deeper and more easily into the wood due to the exposure of the end-grain wood and the larger amount of available liquid. If the liquid is stored deeper inside the wood, it might not be able to escape and evaporate as easily even if it had a higher vapor pressure. Following these assumptions, the blotting paper test should only be used for liquids with a low vapor pressure. For liquids with a high vapor pressure, the use of the immersion test would be recommended.
As already pointed out in the results, any statistically significant influence of the test liquids on the tensile strength was not observed. This stays in contrast to results published by (Fodor et al. Citation2017), who pointed out that the bending strength of acetylated wood, when exposed to water, is decreasing. However, the (fluid-induced) weakening is significantly less than that in untreated wood. There are a number of aspects to consider when comparing the results obtained in the present study with values from the literature:
First of all, the mechanical performance tested in this study is based on the tensile strength parallel to the fiber. According to (Kretschmann Citation2007) who gives an exemplarily overview on the effect of moisture content (MC) on various strength characteristics; (1) Bending strength as well as compression strength is decreasing with MC, up to fiber saturation point. (2) Longitudinal tensile strength is increasing with MC from 5 to roughly 13%. Beyond that strength it is mildly decreasing.
This decrease of the tensile strength is far less pronounced than the decrease of the before described bending strength. To the authors knowledge there are no studies on the effect of moisture content on the tensile strength of acetylated wood. Furthermore, other studies have focused on the effect of acetylation on board level, but not veneer level. Therefore, results cannot be directly compared due to possible size effects and processing-related influences. As a third point it has to be mentioned that the tensile strength properties of wood usually exhibit a large variation and the experiments in this study are no exception. This large variation can mask smaller changes in strength. According to (Kim and Park Citation1991) also the direction of liquid penetration plays an important role which can quite differ between the radial and tangential direction.
Generally, in future studies, the use of reinforcements like they were applied in the blotting paper tests is recommended and the number of samples in each test group should be increased to achieve statistically more reliable results. The failure in the transition zone as it occurred for the majority of the samples could be due to a higher triaxiality in that region, which has been found in FE simulations for other materials (Chen et al. Citation2018). A higher triaxiality is related to a larger stress perpendicular to the direction of the tensile test and therefore to the fiber orientation in our case and might therefore promote cracking in this area.
To achieve more accurate measurements of the sample dimensions, a micrometer or dial indicator should be used instead of the digital calliper in future research. The use of a micrometer might also facilitate to avoid “squeezing” of the sample during the measurements, especially after the exposure to the liquid, because the samples tend to become “spongier/bloated”. Additionally, the efficiency during the test procedure should be enhanced further, so that the time between the end of liquid exposure and the measurements and tensile tests is kept at a minimum. This is particularly important in the case of quickly evaporating liquids like acetone. To better understand how quickly the evaporation takes place and be able to more precisely estimate how much liquid is present in the sample during tensile testing, the samples could be weighed again after the tensile testing, as well.
Furthermore, the blotting paper tests could be improved by including weighing of the blotting paper before and after the test. This way, the amount of test liquid that remains in the blotting paper and consequently also the amount of evaporated liquid could be determined. This could also help to understand better why the absorption of distilled water and anti-freeze were so different in the two different test methods.
If one assumes that the weight increase in the immersion tests represents the maximum weight increase, in the case of the anti-freeze it amounts to 0.427 g or 81 wt% on average. In the blotting paper tests, the average weight increase of the anti-freeze specimens was 0.298 g. This means, assuming a maximum weight increase of 81 wt%, that 70% of the blotting paper sample has taken up anti-freeze. In other words, the liquid was not only absorbed by the specimen directly under the blotting paper, but diffused far into the adjacent areas. This would include more than half of the clamping zones at the sample ends. By additionally investigating the blotting paper test samples using Near-infrared spectroscopy (NIRS), it might be possible to gain a broader understanding regarding how far the different test liquids spread.
It would be interesting to compare the findings of this study with non-modified veneers and to investigate changes in the microstructure due to the acetylation, which might have an influence on the chemical resistance, as well. During veneer production, the wood is usually steamed prior to the actual cutting of the veneers to ensure the required pliability and minimize veneer cracks (Tanritanir et al. Citation2006). In the case of the acetylated wood, the steaming process was found to be less successful than usual. It is assumed that this is due to the water not being able to penetrate into the cell walls as easily as in unmodified wood. Therefore, in the future, the veneers should be cut prior to the modification to achieve better mechanical properties. Besides, the chemical resistance of differently modified wood veneers (e.g. furfurylated), veneers from other wood species and rotary-cut veneers should be investigated in future studies to better understand the influence of these different factors. Additionally, determining the tensile strength at varying load-to-grain angles should be considered, since the grain structure has a strong influence on the mechanical properties of wood. This has already been studied for acetylated and unmodified birch plywood (Wang et al. Citation2022) and the results would be interesting to compare with those on ply-level. To test also other mechanical properties, e.g. compression, it might be useful to consider adapting methods from other research areas. For example, standard compression tests for wood are not feasible for testing veneers, but e.g. the short-span compression test (SCT), which is often used for testing paperboard could be a promising option.
Conclusion
Sliced veneers from acetylated radiata pine were exposed to five chemicals. Within each method group, there was no statistically significant difference between the test groups concerning their density before the exposure to the liquids. The two employed exposure methods were the blotting paper test and the immersion test.
The blotting paper test allowed to equip the specimens with doubler materials at their ends. This prevented unwanted transverse failure in the clamping zone.
The highest mass increase was observed with distilled water (0.427 g, immersion test) and anti-freeze fluid (0.298 g, blotting paper test). The anti-freeze fluid diffused far into the adjacent areas of the actual contact zone with the blotting paper.
The acetylated radiata pine veneers used in this study showed a good resistance against chemicals. No statistically significant influence of the chemicals on the tensile strength was observed.
Outlook
In a follow-up study, which is currently in preparation, the chemical resistance and durability of rotary cut veneers from birch will be analyzed. The in-depth study will consider various modification methods (physical and chemical). The study will include a direct comparison with unmodified veneers of the same wood species.
Acknowledgements
The research leading to these results has received funding from the Mobility of the Future program through the project “BioLIB – Biobased Multifunctional Laminates in Battery Housings” (FFG 884364). Mobility of the Future is a research, technology and innovation funding program of the Republic of Austria, Ministry of Climate Action. The Austrian Research Promotion Agency (FFG) has been authorized for the program management.
Disclosure statement
No potential conflict of interest was reported by the author(s).
Additional information
Funding
References
- Accoya product certificate [online], available at: https://www.accoya.com/app/uploads/2020/05/Accsys-Technologies-ENG-33058-21-KOMO-product-certificate.pdf [Accessed 28 January 2022].
- CARpenTiER [online]. Accessed 23 May 2022, available at: https://projekte.ffg.at/projekt/3915331.
- Explore wood [online]. Accessed 1 June 2022, available at: https://www.metsagroup.com/metsawood/explore-wood/?ba=937&ct=955.
- For(s)tschritt [online]. Accessed 23 May 2022, available at: https://www.tff-kassel.de/forschung/projekte/forstschritt/.
- HAMMER [online]. Accessed 23 May 2022, available at: http://www.projekt-hammer.de/.
- WoodC.A.R [online]. Accessed 23 May 2022, available at: https://www.woodcar.eu/index_de.html.
- Wood Handbook. Wood as an Engineering Material (2021) USDA Forest Service, Forest Products Laboratory.
- Ahmed, S. A., Chun, S. K., Miller, R. B., Chong, S. H., and Kim, A. J. (2011) Liquid penetration in different cells of two hardwood species. Journal of Wood Science, 57(3), 179–188.
- Andresen, C., Demuth, C., Lange, A., Stoick, P., andPruszko, R. (2012) Biobased automobile parts investigation.
- Ashby, M. F. (1999) Materials Selection in Mechanical Design (2nd ed.). (Oxford: Butterworth-Heinemann).
- Austrian Standards Institute (1994) ÖNORM ÖNORM EN 20187:1994: 01.03.1994: Österreichisches Normungsinstitut.
- Austrian Standards Institute (2005) ÖNORM ÖNORM EN 789:2005-04-01: 01.04.2005: Austrian Standards plus GmbH.
- Austrian Standards International. ÖNORM ÖNORM EN ISO 2812-1:2018 03 15.
- Austrian Standards International. ÖNORM ÖNORM EN ISO 2812-2:2019 04 15.
- Baumann, G., Brandner, R., Müller, U., Kumpenza, C., Stadlmann, A., and Feist, F. (2020) Temperature-related properties of solid birch wood under quasi-static and dynamic bending. Materials, 13(23), 5518.
- Baumann, G., Brandner, R., Müller, U., Kumpenza, C., Stadlmann, A., and Feist, F. (2021) A comparative study on the temperature effect of solid birch wood and solid beech wood under impact loading. Materials, 14(24), 15.
- Baumann, G., Stadlmann, A., Kurzböck, C. and Feist, F. (2019) Crash-proof wood composites in lightweight bodyworks of the future. ATZ Worldwide, 121(11), 48–51.
- Beck, G., Thybring, E. E. and Thygesen, L. G. (2018) Brown-rot fungal degradation and de-acetylation of acetylated wood. International Biodeterioration & Biodegradation, 135, 62–70.
- Buchelt, B. and Pfriem, A. (2011) Influence of wood specimen thickness on its mechanical properties by tensile testing: solid wood versus veneer. Holzforschung, 65(2), 1–3.
- Buchelt, B. and Wagenführ, A. (2008) The mechanical behaviour of veneer subjected to bending and tensile loads. Holz als Roh- und Werkstoff, 66(4), 289–294.
- Chen, X., Chen, G., Huang, L., and Shi, M.F. (2018) Calibration of GISSMO Model for fracture prediction of a super high formable advanced high strength steel.
- Chum, H. L. (1989) Assessment of biobased materials.
- Cremonini, C., Negro, F. and Zanuttini, R. (2015) Wood-based panels for land transport uses. Drewno, 58, 127–135.
- Desch, H. E. and Dinwoodie, J. M. (1996) Timber Structure, Properties, Conversion and Use (London: Macmillan Education UK).
- Digaitis, R., Thybring, E. E., Thygesen, L. G. and Fredriksson, M. (2021) Targeted acetylation of wood: a tool for tuning wood-water interactions. Cellulose, 28(12), 8009–8025.
- Engelung Thybring, E. (2013) The decay resistance of modified wood influenced by moisture exclusion and swelling reduction. International Biodeterioration & Biodegradation, 82, 87–95, available at: https://www.sciencedirect.com/science/article/pii/S0964830513000589#!
- European Commission (ed.) (2018) Annex to the communication from the comission to the European parliament, the council, the European economic and social committee and the committee of the regions. Europe on the move Sustainable Mobility for Europe: safe, connected and clean. Brussels.
- Fodor, F., Lankveld, C. and Németh, R. (2017) Testing common hornbeam (Carpinus betulus L.) acetylated with the Accoya method under industrial conditions. iForest - Biogeosciences and Forestry, 10(6), 948–954.
- Fuchs, W. (1928) Zur Kenntnis des genuinen Lignins, I.: Die Acetylierung des Fichtenholzes, available at: https://doi.org/10.1002/cber.19280610512.
- Galos, J., Sutcliffe, M. and Newaz, G. (2017) Mechanical behaviour of phenolic coated Finnish birch plywood with simulated service damage. Wood Material Science and Engineering, 12(5), 307–315.
- Graf, J., Klopfer, R. and Röver, D. (2019) Neue Potentiale im konstruktiven Holzbau durch acetylierte Buche.
- Grinins, J., Biziks, V., Marais, B. N., Rizikovs, J., and Militz, H. (2021) Weathering stability and durability of birch plywood modified with different molecular weight phenol-formaldehyde oligomers. Polymers, 13(2), 2–3. https://www.mdpi.com/2073-4360/13/2/175.
- Große, T., Fischer, F., Kohl, D., Müller, U., Feist, F., and Kurzböck, C. (2022) Modellierung von Holz in crash-relevanten Fahrzeugstrukturen am Beispiel eines crashrohrs [Modelling of wood in crash-relevant vehicle structures using the example of a crash tube]. In A. Wagenführ (ed.) Tagungsband des 20. Holztechnologischen Kolloquiums Dresden 28.-29. April 2022 (Dresden: Technische Uni Dresden).1–19.
- Gryparis, E., Papadopoulos, P., Leligou, H. C. and Psomopoulos, C. S. (2020) Electricity demand and carbon emission in power generation under high penetration of electric vehicles. A European Union perspective. Energy Reports, 6, 475–486.
- Handbook, Wood. Wood as an Engineering Material. (2021) USDA Forest Service, Forest Products Laboratory.
- Hill, C. A. S. (2006) Wood Modification. Chemical, Thermal and Other Processes (Chichester: Wiley).
- Holbery, J. and Houston, D. (2006) Natural-Fiber-Reinforced Polymer Composites in Automotive Applications.
- Hom, S. K., Ganguly, S., Bhoru, Y.U., and Samani, A. (2020) Effect of chemical modification on dimensional stability of Pinus radiata D. Don using acetic anhydride. Journal of Forest Science, 66(5), 208–217.
- Horn, O. (1928) Zur Acetylierung des Buchenholzes, available at: https://doi.org/10.1002/cber.19280611122.
- Ibach, R. E. and Rowell, R. M. (2021) USDA forest service forest products laboratory: acetylation of wood 1945–1966. Forests, 12(3), 260.
- Jia, L., Chu, J., Li, J., Ren, J., Huang, P. and Li, D. (2020) Formaldehyde and VOC emissions from plywood panels bonded with bio-oil phenolic resins. Environmental Pollution, 264, 114819.
- Jones, D. and Sandberg, D. (2020) A review of wood modification globally – updated findings from COST FP1407. Interdisciplinary Perspectives on the Built Environment, 1, 2.
- Jost, T., Müller, U. and Feist, F. (2014) Holzverbundwerkstoffe im Automobilbau der Zukunft? – Grundvoraussetzung: Crashsimulation von Holzkomponenten. Fachaufsatz Werkstoffprüfung.
- Jost, T., Müller, U. and Feist, F. (2018) Wood composites for future automotive engineering? – Basic requirement: wood composites for future automotive engineering? – Basi requirement; crash simulation of wood-based components. Konstruktion, 70, 74–82.
- Kass, A., Wangaard, F. and Schroeder, H. A. (1970) Chemical degradation of wood: the relationship between strength retention and pentosan content.
- Kim, J. Y. and Park, J. S. (1991) An Anatomical Research on Liquid-Penetration and Penetration-Path of Wood, available at: https://koreascience.kr/article/JAKO199100238220148.pdf.
- Kollmann, F. (1951) Anatomie und Pathologie, Chemie, Physik Elastizität und Festigkeit (Berlin: Springer Berlin Heidelberg).
- Kollmann, F. (1982) Technologie des Holzes und der Holzwerkstoffe, 201–400.
- Kretschmann, D. E. (2007) Kirk-Othmer Encyclopedia of Chemical Technology.
- Küch, W. (1939) Untersuchungen an Holz, Sperrholz und Schichthölzern im Hinblick auf ihre Verwendung im Flugzeugbau. Holz als Roh- und Werkstoff, 2. Jahrgang (7/8), 258–259.
- Lahtela, V. and Karki, T. (2015) Determination and comparison of some selected properties of modified wood. Wood Research, 60, 763–772.
- Lai, G. and Plönning, S. (2019) Fracture characteristics of acetylated birch – experimental and numerical studies.
- Lankveld, C., Alexander, J., Tangen, A., Olson, T. and Bongers, F. (2014) Accoya® wood flooring and decking in extreme environments. European Conference on Wood Modification.
- Leitgeb, W., Jost, T., Mayrhofer, P., Wagner, W., Kirschbichler, S., and Müller, U. (2016) Holz im strukturellen Fahrzeugbau. 2. internationales Fahrzeugkolloquium, 35–46.
- Levy, J. F. and Eveleigh, D. E. (1990) The Natural History of the Degradation of Wood [and Discussion].
- Mantanis, G. (2017) Chemical modification of wood by acetylation or furfurylation: A review of the present scaled-up technologies. Bioresources, 12, 4478–4489.
- Militz, H. and Krause, A. (2004) Holzmodifizierung für den Fenster- und Fassadenbau: Mehr als nur Holz. glaswelt Spezial (6), 40–42.
- Moghaddam, M. S., Claesson, P. M., Wålinder, M. E. P. and Swerin, A. (2014) Wettability and liquid sorption of wood investigated by Wilhelmy plate method. Wood Science and Technology, 48(1), 161–176.
- MoveWood. [online]. Accessed 23 May 2022, available at: https://www.innovationszentrum-weiz.at/veranstaltungen-aktuelles/detail/projekt-movewood.
- O'Halloran, M. R. (1975) Plywood in hostile environments: Physical properties and applications. APA Research report (132).
- Persaud, N., Lehr, J., and Keeley, E. (2005) Vapor pressure. Water encyclopedia (2005). Water Encyclopedia.
- Pramreiter, M., Bodner, S. C., Keckes, J., Stadlmann, A., Feist, F., Baumann, G., Maawad, E. and Müller, U. (2021) Predicting strength of Finnish birch veneers based on three different failure criteria. Holzforschung, 75(9), 847–856.
- Rowell, R. M. (1992) Opportunities for value-added bio-based composites.
- Roy, W. R. (2016) The environmental fate of representative antistatic agents and components. In Handbook of Antistatics (Elsevier), pp. 421–431.
- Ruiz, V., Pfrang, A., Kriston, A., Omar, N., Van den Bossche, P. and Boon-Brett, L. (2018) A review of international abuse testing standards and regulations for lithium ion batteries in electric and hybrid electric vehicles. Renewable and Sustainable Energy Reviews, 81, 1427–1452.
- Rusdi, M., Moroi, Y., Nakahara, H., and Shibata, O. (2005) Evaporation from water−ethylene glycol liquid mixture. Langmuir: The ACS Journal of Surfaces and Colloids, 21(16), 7308–7310.
- Ryntz, R. and Kozora, S. (2019) Sustainable materials in automotive. Physical Sciences Reviews, 4(12), 1–4.
- Sarika, P. R., Nancarrow, P., Khansaheb, A. and Ibrahim, T. (2020) Bio-Based alternatives to phenol and formaldehyde for the production of resins. Polymers, 12(10), 2237.
- Schnabel, T. (2009) Holzoberflächen - Klassifizierung, Modellbildung und Umweltsimulation von optischen Eigenschaften. Dissertation. Technische Universität München.
- Slabohm, M., Mai, C. and Militz, H. (2022) Bonding acetylated veneer for engineered wood products-a review. Materials (Basel, Switzerland), 15(10), 1.
- Staudacher, R. (2015) Ausgewählte mechanische Eigenschaften von Furnier der Holzarten Fichte, Birke und Buche. Master thesis. Technical University of Graz.
- Tanritanir, E., Hiziroglu, S. and As, N. (2006) Effect of steaming time on surface roughness of beech veneer. Building and Environment, 41(11), 1494–1497.
- Tarkow, H. and Stamm, A. J. (1955) Acetylated Wood.
- Teacă, C.-A. and Tanasă, F. (2020) Wood surface modification—classic and modern approaches in wood chemical treatment by esterification reactions. Coatings, 10(7), 629.
- Wang, Y., Wang, T., Crocetti, R. and Wålinder, M. (2021) Mechanical Properties of Acetylated Birch Plywood Loaded Parallel to the Face Grain (World Conference on Timber Engineering).
- Wang, Y., Wang, T., Crocetti, R., and Wålinder, M. (2022) Experimental investigation on mechanical properties of acetylated Birch plywood and its angle-dependence. SSRN Electronic Journal.
- Wexler, A. (1976) Vapor pressure formulation for water in range 0 to 100°C. A revision. Journal of Research of the National Bureau of Standards Section A: Physics and Chemistry, 80A(5-6), 775–785.
- Zimmer, B., Hölzl, F., Bongers, F., Nüske, J., and Winkler, J. (2003) Erprobung eines Acetylierungsverfahrens für heimische Holzarten und Holzprodukte. Zusammenfassender Bericht der Ergebnisse.
- Žlahtič-Zupanc, M., Lesar, B. and Humar, M. (2018) Changes in moisture performance of wood after weathering. Construction and Building Materials, 193, 529–538.
Appendix
Figure A1. Legend and case study description boxplots with notches (Baumann et al. Citation2021).
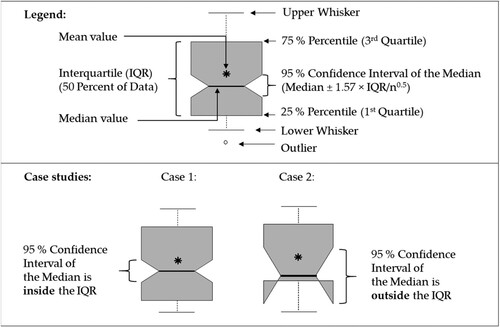