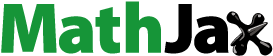
ABSTRACT
The objective of this work was to investigate the rate of knife wear during the beech wood chipping process and to evaluate the changes in the chemical and microscopic structure of wood. A knife coated with AlCrN was selected for the study. This coating creates an abrasion resistant layer on the knife and has a higher resistance to abrasive wear and, therefore, a longer life. After chipping, the degree of knife wear was assessed using a gravimetric method and 3D scanning analysis. Microstructural and surface characterisation revealed that cracking and abrasive wear were the main causes of tool blunting. The maximum removal of material on the cutting edge was 240 µm, the average weight loss of 0.58 g. In relation to wear, wood fragments remained on the cutting knife. Infrared spectroscopy of wood fragments showed changes in the chemical composition due to the high temperatures in the blade of the knife, and elemental analysis, the higher content of Al, Cr, and N elements in the wood fragments, probably due to the presence of particles from the coating of the knives. Microscopic analysis of the chips revealed the presence of metal particles from the knives on the structural wood elements.
Introduction
Wood chipping is an important process in forestry, wood processing, and primarily in pulp processing. As almost 35% from the overall number of trees harvested on all continents is used for pulp production (Aremu et al. Citation2015). For pulp production, it is important to use wood chips of a good quality, whereas there is a direct relationship with the effectiveness of the pulping process (Malkov et al. Citation2001, Ding et al. Citation2009, Freitas et al. Citation2018, Eugenio et al. Citation2019). Wood-chipping machines were designed to obtain chips from small and medium-diameter logs with very low production of sawdust in one operation (Kuljich et al. Citation2017). For good chip quality, one of the most important parameters is the condition of the knife edge during chipping (Heidari et al. Citation2013, Spinelli et al. Citation2014, Nadolny et al. Citation2020). Knowledge of local wood properties, including resistance to chipping, is significant for the improvement of structural components such as chipping tools (Pichler et al. Citation2018). Tool wear increases the cutting force, which leads to an increase in temperature, which results in lower cutting stability. The high temperature of the knife is also caused by the tension of the material and depends on the type of conditions and the cutting mode (Kara and Li Citation2011). Wear of the cutting tool has a significant effect on the quality of the machined part. Ramasamy and Ratnasingam (Citation2010), as well as Okai et al. (Citation2005), noted that mechanical, thermal, and chemical interactions between the cutting tool and wood are important factors for tool wear. According to several studies (Klamecki Citation1979, Porankiewicz et al. Citation2005, Citation2006), the chemical composition of wood may play a role in cutting tool wear rates. The presence of silica content and other abrasive agents in wood (Porankiewicz and Grönlund Citation1991, Cristóvaõ et al. Citation2011, Ekevad et al. Citation2012), as well as the wood extractives content (Cristóvaõ et al. Citation2011) influences knives wear rate. When the cutting tool wears, it is damaged (abrasion, chipping) at the micro level (Jeon et al. Citation2017). An effective method of reducing tool wear is its modification with a thin hard coating produced by PVD (Physical Vapour Deposition) or CVD (Chemical Vapour Deposition methods) (Schalk et al. Citation2022, Warcholinski and Gilewicz Citation2022). The coating of tools is used to reduce the wear of the cutting edges, which should ensure an increase in their service life. Priority is given to the coating of tools for chip machining or metal forming. Cho et al. (Citation2015) and Kazlauskas et al. (Citation2022) have confirmed the importance of using this surface treatment technology on tools. Also coating of tools also for wood chipping in secondary production (e.g. mills, drills, knives for veneer peeling) is becoming a common practice and brings many advantages. Such as increasing the life of the tool, as well as the quality of the resulting product, was observed by e.g. Kalincová et al. (Citation2018), Nadolny et al. (Citation2020) and Warcholinski and Gilewicz (Citation2022). However, the tools for the primary processing of wood, the coating method is not so commonly used and is not sufficiently described in the literature.
The temperature of the cutting tool, as one of the most important factors affecting tool wear in wood processing, causes a change in its basic properties, such as hardness, toughness, and chemical stability (Ekevad et al. Citation2012). The temperature of the knife depends on several factors, including the cutting speed, the continuity of the cutting process, the depth of the cut, and the shape of the tool (Horman et al. Citation2014). During the processing of wood with knives, the source of heat is the friction work performed on the contact surfaces. The temperature is influenced by the properties of the cutting tool, its geometric properties, the thermal conductivity of the material and its specific heat. During friction, energy is consumed, and shear stress creates deformations in both contacting materials. Frictional heat is generated at the interface between the chip and the tool, while a smaller part of the heat flows into the chip and a larger part flow into the knife (Kumar and Jagath Citation2013). The temperature in some places of the cutting tool is more than 500°C (Horman et al. Citation2014). The effect of high temperatures on wood causes changes in its chemical structure and main constituens (cellulose, hemicelluloses, lignin, extractives) (Sandberg et al. Citation2013, Kamperidou Citation2019). These processes take place through various reactions such as oxidation, dehydration, hydrolysis, decarboxylation, while changes in lignin-saccharide structures can be characterised using infrared spectroscopy (FTIR) (Kubovský et al. Citation2020). Changes in the chemical structure can influence the quality of wood chips. Moreover, the result of the chip production process is that, in addition to the wear, the fragments of wood remained on the cutting knife. Due to the repeated exposure to the high temperatures of the cutting tool, the chemical composition of the wood fragments will be changed compared to the processed original material or the resulting product – wood chips.
In the primary processing of wood, cutting tools are used in their basic state (uncoated), which have their own service life. Changing knives is a time-consuming process, which is reflected in the lower performance of the machine itself. By increasing the service life of cutting tools, the costs of chip production will be reduced, energy requirements will be reduced, and the machine performance and the chip quality will be increased.
The aim of this paper is to assess the wear rate of knives wear during the beech wood chipping and to evaluate the changes in the microscopic and submicroscopic structure of wood.
In this paper, knives coated with CROSAL plus based on AlCrN (Aluminium Chromium Nitridate) were used for the experiment. They were selected based on resistance test and hardness measurement. This coating is mainly used to increase the life of cutting tools in the metalworking and woodworking industries, while it was only used for the primary processing of wood in this experiment.
Material and methods
Material
Beech wood trees (Fagus sylvatica L.) with a trunk diameter of 18 cm ± 1 cm and an age up to 50 years, harvested in the middle part of Slovakia (Zvolen region, Tŕnie forest district) in April 2022, were used for the chipping process. The moisture content (w) of the green beech wood was determined in a RADWAG moisture analyser, MAC series (INTERTEC, Banská Bystrica, Slovakia), and density (ρ) using the gravimetric method.
Chemical composition of raw beech wood
The beech wood was disintegrated into sawdust and fractions of 0.5 to 1.0 mm in size were used for chemical analyses. The extractives content (EXT) was determined on a Soxhlet apparatus with a mixture of absolute ethanol for analysis (Merck, Germany) and toluene for analysis (Merck, Germany) (2:1, v:v) according to the ASTM D1107-21 (Citation2021). Lignin (LIG) was determined according to Sluiter et al. (Citation2012), holocellulose (HOLO) according to the method of Wise et al. (Citation1946), and cellulose content (CEL) according to the method of Seifert (Citation1956). Hemicelluloses (HEMI) were calculated as the difference between the holocellulose and the cellulose content. Measurements were performed on four replicates per sample. The results () are presented as percentages of oven-dry wood.
Table 1. Characteristic of green beech wood material: moisture, density, extractive content (EXT), lignin content (LIG), holocellulose content (HOLO), cellulose content (CEL), hemicellulose content (HEMI).
Methods
Selection of knife material
Before the beech wood chipping process, an abrasive wear resistance test and HRC (Hardness Rockwell C) measurement were performed, and a better quality knife material was selected for the experiment.
Two materials were used in the experiment: uncoated () and coated (). The basis of both is steel X48CrMoV8-1-1 (Citation2019) (WNr. 1.2360) (PILANA Group a.s., Hulín, Czechia) with a diameter of 248 mm × 115 mm × 13 mm; edge of 25°/35°; 3×groove, size of 14 mm (knife designed for the type of chipping machine of PEZZOLATO H 780/200). It was an alloy steel tool, designed for dies for forging presses, die inserts, extrusion tools, tools with good compressive strength and especially with high abrasion resistance. This type of material is usually used to sharpen strained knives. The chemical composition according to the material sheet (www.dashofer.cz) is shown in .
Table 2. Chemical composition of steel X48CrMoV8-1-1.
The strength limit of steel in the hardened and tempered state Rm is from 1270 to 2100 MPa. The achievable hardness is declared according to the selected tempering speed in the range of 40 ± 1.5 to 56 ± 0.4 HRC. This material was hardened at a temperature of 1032 °C and the tempered temperature was T = 542°C.
The coated tool () was coated with CROSAL plus. It is a new generation coating based on AlCrN (Aluminium Chromium Nitridate) (voestalpine High Performance Metals Division, s.r.o., Martin, Slovakia). This coating is an advanced development of the older, but practice proven, well-established CROSAL coating. This coating is characterised by high resistance to oxidation and wear, excellent adhesion, and heat hardness. Its basic applications are for e.g. metalworking and forming tools, used for high-performance cutting. The basic properties are listed in . The coating on the base of AlCrN according to Souza et al. (Citation2020) has a lower friction coefficient and wear rate than the TiAlN coating under distinct (mild and severe) sliding.
Table 3. Properties of the coating with CROSAL plus stated by the manufacturer.
Abrasive wear resistance test and HRC hardness measurement
The test of abrasive wear resistance was performed according to the GOST 23.208-79 (Citation1979) standard GOST 3647-80 (Citation1982) method consists in comparing the weight loss of the tested material with that of the standard material under the same test conditions. Electrocorundum with a grain size of 100–250 µm is used as an abrasive material, with a maximum moisture content of 0.15%. Its hardness corresponds to the 9th degree according to the Mohs scale. When assessing wear resistance in specific wear conditions, it is allowed to use an abrasive material corresponding to the material that acts during operation, but with a grain size of no more than 1.0 mm (GOST 23.208-79 Citation1979). The test was carried out in the laboratory of the Faculty of Technology of the Czech University of Life Sciences in Prague using Tester T-07 test equipment, ITC PIB Institution of Technology Radom, with the controller BT-16 (Institute for Sustainable Technologies, Radom, Poland). Each sample was prepared using abrasive water jet cutting technology, milled and ground on a magnetic plane grinder to dimensions of 30 mm × 30 mm × 10 mm with a surface roughness Ra of 0.4 µm. The test conditions were established as follows:
length of the friction track in one cycle R = 153.6 m,
rubber disc diameter D = 48.9 mm,
pressing force F = 15.48 N,
number of turns in one cycle n = 1000,
abrasive – silica sand OTTAWA with a grain size of 0.1 mm and
hardness of the abrasive material 54 HRC.
Each test sample was weighed three times before the test and placed on the test device. Subsequently, the abrasive feed was started and the rubber disk was pressed against the test sample. After each cycle was completed, the sample was reweighed three times. From the results weights, the average weight loss wh for each material was calculated.
Rockwell hardness was performed in accordance with ISO 6508-1:Citation2016. A Rockwell hardness tester, type UH250 (Buehler Ltd., Lake Bluff, Illinois, USA) with a loading force F of 1471 N was used to determine the hardness. Measurements were performed on five replicates per sample as shown in and .
Figure 3. Samples of uncoated (left) and coated knives (right) after the test of resistance to abrasive wear and measurement of HRC hardness.
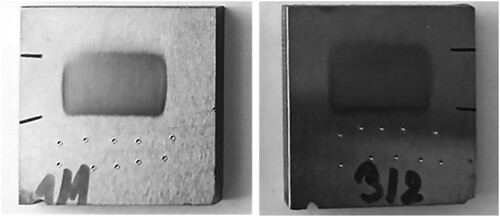
Table 4. Results of the resistance test to abrasive wear and HRC hardness measurement.
Relative resistance to abrasive wear was calculated according to:
(1)
(1) where whR is weight loss of the uncoated sample (g), whC is weight loss of the coated sample (g).
Coefficient of hardness KT
Coefficient of hardness KT of uncoated sample HR – abrasive Ha
(2)
(2) Coefficient of hardness KT of coated sample Hc – abrasive Ha
(3)
(3) where: HR – hardness of the uncoated sample (HRC), Ha is hardness of the abrasives (HRC), HC is hardness of the coated sample (HRC).
Chipping process, gravimetric analysis, and 3D scanning of knives
The realisation of the experimental measurement consists of a control weight method for testing chipping knives, where the weight of each knife was recorded before the measurement. Weighing was carried out on a professional laboratory balance RADWAG PS3500R2 (Libra, Bratislava, Slovakia), 3500 g capacity, 0.01 g readability. Before performing the experimental measurements, a control measurement and 3D scanning of the geometrical parameters of the chipping knives were required by a non-contact method, using the Alicona Infinity Focus device (Bruker Alicona, Graz, Austria). The experimental measurement was carried out on a Pezzolato H780/200 cardan-mounted mower (Pezzolato S.P.A, Envie CN, Italy) at a constant speed of 540 rpm, driven by a Zetor Proxima wheeled tractor (ZETOR TRACTORS, a.s., Brno, Czechia). After processing of green beech wood, the coated chipping knives (three pieces) were disassembled and the final weighing and 3D scanning were carried out to evaluate the wear rate of the cutting edge. The volume of green beech processed was determined based on previous experiments with basic uncoated knives. The results of these experiments are the subject of other upcoming publications.
Chemical changes in the wood structure
After the chipping process, the wood fragments remained on the knives. The total weight of the wood fragments was 0.43 g (taken from the three knives). The wood fragments taken from the knives were analysed by ATR-FTIR spectroscopy and elemental analysis compared to green beech wood.
ATR-FTIR spectroscopy
Samples of beech wood and wood fragments of wood taken from knives were analysed using ATR-FTIR spectroscopy. The measurements were carried out using a Nicolet iS10 FTIR spectrometer equipped with Smart iTR attenuated total reflectance sampling accessory with diamond crystal (Thermo Fisher Scientific, Madison WI, USA). The spectra were recorded in the wavenumber range of 4000 to 650 cm−1. The resolution was established at 4 cm−1 and 32 scans were recorded for each analysis. Four analyses were performed per both specimens. Spectra were evaluated using the OMNIC 8.0 software (Thermo Fisher Scientific, Madison WI, USA).
Elemental analysis
Elemental analysis of beech wood and the wood fragments of wood taken from the knives was carried out. The determination of carbon (C) was carried out according to the ISO 13878 (Citation1998) standard, and nitrogen (N) according to the STN ISO 10694 (Citation2001) standard using the EA-TCD elemental analysis by thermal-conductivity detection. Other elements: phosphorus (P), calcium (Ca), magnesium (Mg), potassium (K), sodium (Na), iron (Fe), manganese (Mn), zinc (Zn), aluminium (Al), boron (B), copper (Cu), silicon (Si), chrome (Cr) were determined in the mineral by microwave decomposition in the presence of HNO3 and H2O2 according to the ISO 11885 (Citation2007) standard using AES-ICP (atomic emission spectrometry with inductively coupled plasma).
SEM analysis of wood chips
SEM analysis was performed to detect the presence of metal particles in the wood chips originating from the chipping process. The evaluation of the metal particles was performed with an electron microscope detection system, using the backscattered electrons (BSE) detector. The BSE signal originates from the interaction of the primary electron beam with the sample. Larger atoms scatter the electrons more than the light atoms do thereby, creating a higher signal for the BSE detector (Reimer Citation1998, Salh Citation2011). The number of backscattered electrons detected with the BSE detector is proportional to the atomic number of the investigated material. Phases with a higher atomic number (metal particles) will be displayed as brighter regions. This effect allows for the identification of different phases in the materials.
Wood chip mounting samples were attached to the aluminium stubs using conductive carbon adhesive tape, and the circumference was covered with conductive colloidal silver paint, sputter coated with gold in device K650X (Quorum Technologies Ltd., Laughton, UK), and examined with high-vacuum scanning electron microscopy using a Tescan Vega SEM (Tescan, Brno, Czech Republic) operating at 30.0 kV. The electron source was a tungsten filament. The operating conditions, including magnification and scale bar, were recorded on the data bar at the foot of the SEM image.
Results and discussion
Evaluation of knives abrasive wear resistance and HRC hardness
The quality of the chips is closely related to the quality of the knives used for the chipping process. Chipping knives made of steel without heat-chemical surface treatment are commonly used for the chipping process. Knives with surface treatment are mainly used in the woodworking and metalworking industries (Kazlauskas et al. Citation2022). In this work, an experiment was carried out, where knives with thermal-chemical surface treatment were used for the first time for the production of wood chips. Based on the chemical composition of the chipping knife material and the wood chipping process, a surface treatment was proposed. In order to confirm the better resistance of the knife with surface treatment (coated), a comparison of resistance to abrasive wear and HRC hardness with an uncoated knife was performed.
In laboratory conditions, it was verified that coating the knife with an AlCrN coating (CROSAL plus) mentioned properties were improved.
Relative resistance to abrasive wear calculated according to the EEquationequation (1)
(1)
(1) was:
Sample with the AlCrN coating reached relative resistance to abrasive wear
better by 7%.
Coefficient of hardness KT calculated according to the EquationEquation (2)(2)
(2) of uncoated sample HR – abrasive Ha:
Coefficient of hardness KT calculated according to the EquationEquation (3)
(3)
(3) of coated sample Hc – abrasive Ha:
The sample with the CROSAL plus coating reached HRC hardness better by 13%.
Based on the experiments, it was proven that coated knives have a better resistance to abrasive wear and HRC hardness compared to uncoated ones.
Gravimetric analysis and 3D scanning of cutting knives
When the cutting tools wear, their weight also decreases, and may lead to an unbalanced cutting mechanism and an increase in vibrations (Poje et al. Citation2018). The results of the gravimetric analysis of the knives with a coating based on AlCrN () show that after wood chipping, the weight of the knives decreased (on average by 0.56 g) due to the knives wear. After the experiment, a certain amount of wood fragments remained () on the knives in the range from 0.11 g to 0.18 g.
Table 5. Gravimetric analysis of knives and wood fragments taken from knives.
The 3D scanning microscopic analysis of the cutting knife showed slight damage to the cutting edge, removal of material on the cutting edge by a maximum of 370 µm (). In the picture it can be seen an overlay of the scans of the cutting edge before and after the chipping process. Green points displayed on the cutting edge (grey area) indicate positive or negative deformations. Surface treatment of the knife with a AlCrN coating did not prevent the formation of a wood particles on the knives. Nevertheless, the damage of the chipping knife cutting edge is minimal.
Figure 5. Evaluation of the primary surface of the knife, cutting edge (grey area), before and after chipping. Green points show positive (+) or negative (–) deformations.
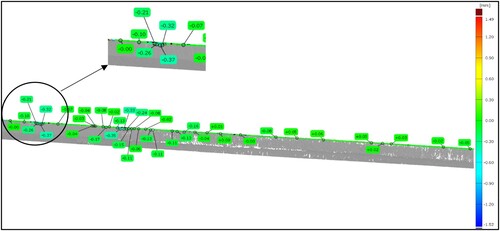
Varghese et al. (Citation2022) modelled cutting edge degradation by chipping in micro-milling. The length of the chipped portions of the cutting edges was between 15.76 and 96 µm, whereas their width was between 7 and 29 µm, and they were found to have a positive correlation.
Krilek et al. (Citation2021) performed a stress analysis FEM on a chipping knife in its basic condition (without surface treatment) material type EN 41 9802. The result of the stress analysis of a knife with a flat blade edge indicated a deformation greater than 14.44 μm. Stress analysis showed that this material is suitable to produce cutting knives for the processing of wood waste and dendromass. The comparison between the durability of uncoated and coated knives was evaluated by Kalincová et al. (Citation2018). The use of the CrN/TiN coating on tools for woodworking technology lead to a significant increase in the resistance against the thermal influence and to a decrease in abrasive wear of the cutting edge, which is also in comparison with results by Warcholinski and Gilewicz (Citation2011) and Jaroš and Fiala (Citation2016). Wu et al. (Citation2023a, Citation2023b) who investigated the abrasive wear of blade tip on the knives made from martensitic steels. The wear rate of steels has been determined to be 1.98 × 10−4 mm3/(Nm) for 5Cr15MoV and 1.5 × 10−4 mm3/(Nm) for 9Cr18MoV, respectively. According to authors, volume is proportional to the cutting cycles and actual applied load.
During the primary processing of the wood, in the interaction of the tool and the wood, the energy demand during the transverse cutting of the wood was monitored. The results show a reduction in the energy consumption of the entire wood splitting process when using a PVD coating based on AlTiN (Aluminium Titanium Nitride) on saw blades (Kováč et al. Citation2022).
The geometric deviation of flatness before the experiment was 61 μm, and after the experiment was 71 μm ().
The surface roughness of the cutting edge of the knife (Rz) was 18 µm before the experiment. This value was averaged over the entire length of the cutting edge. The roughness of the cutting edge after experimental measurements was 8 µm, which represents a decrease of 56%. %. It can be stated that wood behaves as an abrasive material and affects roughness. On the one hand, this can be positive due to a decrease in roughness, which will be reflected in reduced energy requirements during wood processing. Also, the cutting edge the cutting edge of the knife material wears out, which leads to an increase in the radius of the cutting edge and its deformations, to a decrease in chips quality and productivity. Using material with lower wear resistance leads to the fast dulling and bending of materials (Kováč et al. Citation2014). According to Spinelli et al. (Citation2014), knife wear determines a 20% decrease in chip productivity and a dramatic decline in chip quality. Facello et al. (Citation2013) showed that knife wear caused a 50% reduction in productivity. Ťavodová et al. (Citation2022) analysed harvester delimbing knives manufactured from special hardened and tempered Borarc alloy steel. Based on their results, the knives worn abrasively. The thickness of the knife was gradually decreased, the profile of the knife lost stability, and it was plastically deformed with the final phase of breaking the integrity.
Chemical changes in the wood structure
When high temperatures, such as those reached at the point of contact of the knife blade with the wooden material, the chemical structure of the wood changes. After our experiment, wood fragments with a changed chemical structure compared to green wood were found on the knives, which is confirmed by the results of the FTIR analysis ().
The comparison of the spectrum of beech wood and the spectrum of wood fragments taken from the knives (), shows considerable differences in several regions. When interpreting the differences in the spectra, considering the facts that during the cutting of chips, there is an increase in temperature at the point of contact of the knife’s material with the wood, and therefore observed changes in the wood fragments taken from the knives related to the thermal degradation of the wood sample.
The absorption band in the range 3700–3000 cm−1 is in the spectrum of the wood fragments taken from knives is more intensive, and its maximum is shifted to a higher wavenumber (3357 cm−1 vs. 3345 cm−1 in the spectrum of beech wood). This band is associated with vibrations of the OH groups. The differences mentioned above can be caused by an increase in the intensity of O-H from the phenolic groups in lignin. It is a well-known fact that the lignin percentage increases because of carbohydrate degradation due to increased temperature (Esteves et al. Citation2013, Výbohová et al. Citation2018, Hill et al. Citation2021, Čermák et al. Citation2022).
Another important region is the region of characteristic for stretching the vibrations of the C=O groups. In the spectrum of the wood fragments taken from the knives, we observe a higher intensity of the absorption band at 1732 cm−1 and its shift to lower wavenumbers compared to the spectrum of wood, where the maximum of this band is at 1735 cm−1. These differences may be due to an increase in carbonyl or carboxyl groups in lignin by oxidation (Tjeerdsma and Militz Citation2005, Esteves et al. Citation2013).
It is very well-known fact that the thermal stability of lignin is higher compared to the other wood components and the increase in its percentage after the chipping process in the wood fragments taken from the knives is evident by an increase in the intensity of the absorption bands at 1593 and 1508 cm−1. These bands correspond to aromatic ring stretching vibrations. Their observable broadening suggests that in the wood fragments taken from the knives there is a greater structural diversity around the benzene rings than in the wood (Esteves et al. Citation2013). The different position of the maximum of the second peak in compared spectra (1508 cm−1 in the spectrum of wood fragments taken from the knives vs. 1505 cm−1 in the spectrum of wood) indicates that lignin macromolecule in the wood fragments taken from the knives has lower methoxyl groups. It can be assumed that the higher temperature during chipping causes demethoxylation of lignin, respectively easier cleavage of syringyl units since these are less condensed by C–C bonds than guaiacyl units (Faix et al. Citation1990).
Also, the mentioned spectra differ in the shape of the peak in the region from 1350 to 1300 cm–1. The peak maximum is found at 1323 cm−1 in the spectrum of the wood fragments taken from the knives, is shifted to a higher wavenumber, namely to 1327 cm−1. Based on the peak assignments according to Bhagia et al. (Citation2022) it can be assumed that this is caused by a decrease in the intensity of absorption bands originated from vibrations of thermally less stable polysaccharides, which are found at lower wavenumber. On the other hand, the band at 1327 cm−1, which corresponds to more stable monomers of the lignin macromolecule, maintains its intensity.
It is difficult to interpret the differences between 1180–910 cm−1 because in this region more absorption bands are characterised for various groups and bonds in all wood components overlapped. The highest absorption band, with a maximum at 1030 cm−1, corresponds to the C–O–C vibrations. When the differences in this region of spectra are compared, we can state that in the spectrum of the wood fragments taken from the knives the ratio of the intensity of absorption bands H1030/H1370 considerably increased which means that the proportion of C–O–C bonds is higher in the sample of wood fragments taken from the knives compared to beech wood.
The wear of the knives was also confirmed by elementary analysis. Comparing the results between the wood fragments taken from the knives and green beech wood () shows the lower amount of elements: P, Mg, Ca, Mn and Cu and the highest amount of N, C, K, Na, Fe, B, Si, Al and Cr in the wood fragments taken from the knives. The presence of a higher content of Al, Cr, and N elements in the wood fragments taken from the knives could be due to the wear of the surface part of the knife material, the coating of which is formed by the elements Al, Cr, and N. Cristóvaõ et al. (Citation2011) and Porankiewicz et al. (Citation2005) showed that the cutting-edge damage can be associated with the interaction between the tool and large silica particles in the early stage of the cutting-edge wear process. In beech wood samples were recorded a higher content of Si (688 mg/kg) compared to the results obtained by Anca-Couce et al. (Citation2020), with Si content of 106 mg/kg.
Table 6. The elemental analysis of green beech wood and the wood fragments taken from the knives.
According to Telmo et al. (Citation2010), the typical values in hardwoods for minor elements contents in mg/kg are Cd (0.10), Cr (1.0), Cu (2.0), Ni (0.5) and Zn (10). Anca-Couce et al. (Citation2020) performed an elemental analysis of beech wood and found the following concentrations of elements: 65 mg/g of Al; 3668 mg/g of Ca; 60 mg/g of Fe; 1490 mg/g of K; 654 mg/g of Mg; 65 mg/g of Na; 106 mg/g of Si and 2 mg/g of Zn. Our results show the highest content of carbon element of 451 g/kg. Compared with the results obtained by Anca-Couce et al. (Citation2020), we found a higher content of all the elements determined. Mineral concentrations in trees depend on several factors, such as species, age, part of the tree and growth state, and especially the forest soil affects the uptake of minerals by trees through the root system (Szász-Len et al. Citation2016).
Scanning electron microscopy analysis
The quality of chips is very important for the needs of the pulp industry. When chipping wood, the knives wear out, which is manifested by the presence of metal particles in the chips.
The metal deposition in conjunction with organic xylem fragments is shown in . Metal particles were captured in the lumens of both early and late vessels (, B5). Knife wear was certainly caused by mechanical tissue (libriform fibres). Deposits of metal particles together with xylem fragments were located in the lumens of vessels, which are more porous compared to libriform fibres. Smaller metal particles were caught on the libriform fibres, which is probably due to the higher density of their cell wall compared to early and late vessels (, B3). It is assumed that in the processing of soft wood, e.g. poplar, willow, the metal particles would occur more evenly due to the wider lumens of libriform fibres. However, the question is whether the soft wood will cause wear at such level.
Figure 8. Presence of metal particles originating from the chipping process in the beech wood chips imaged by secondary (A1–A3) and BSE detectors (B1–B5). Scale bars = 100 μm (or 50 μm, exceptionally in exceptional cases B4, 20 μm in cases B5).
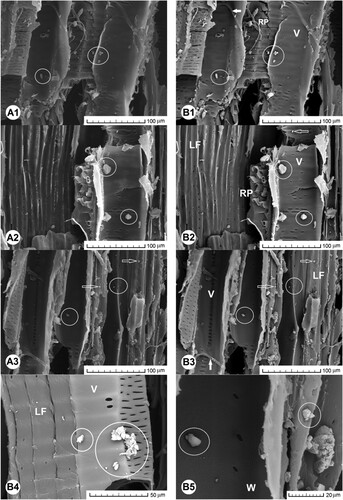
Abbreviations: V, vessel; LF, libriform fibres; RP, ray parenchyma cells; W, warty layer on the S3 wall of the latewood vessel; white arrow – a simple perforation plate between vessels; white circles and arrow outlines – metal particles.
For the needs of the pulp production industries, the solution of cooking chemicals must completely penetrate the wood chips. The solution penetrates the wood chips by diffusing through the cellular elements of the wood. The increased temperature and effect of chemicals cause the delignification of the wood (removal of the majority of lignin) being inevitable for paper production. Incomplete penetration of chemicals into the wood chips is the major reason for inhomogeneous delignification during this process (Malkov et al. Citation2001). The presence of inorganic compounds could mean a problem for good penetration of the cooking chemicals into the entire volume of the chip. For this reason, it is necessary to use the best quality knives for the chipping process to achieve the best quality of the wood chip.
Conclusions
The production of high-quality wood chips requires the correct selection of the cutting tool, its setting, and careful maintenance. Using a high-quality knife in the chipper leads to an increase in productivity, a decrease in specific fuel consumption, the incidence of small chips, and fines decrease. In the present study, a knife coated with CROSAL plus based on AlCrN (Aluminium Chromium Nitridate) was selected for the chipping process based on its better abrasive wear resistance of 7% and HRC hardness of 13% compared to the uncoated, commonly used knife.
The wood chipping process causes:
• a loss of knife material on an average of 0.56 g,
• slight damage to the cutting edge and a maximum depth of material removal of 240 µm,
• an increase of the geometric deviation of the flatness by 16% and the decreas of roughness by 56%.
• the changes in the wood structure as a result of the effect of high-temperature forming on the knives during the chipping process,
• an increase in carbonyl or carboxyl groups in lignin by oxidation reactions , and its demethoxylation.
Based on the results of microscopic analysis, the presence of inorganic components from chipping knives on the surface of the cellular structural elements was detected in the chips.
Based on the achieved results, it can be concluded that the coated knives are suitable not only for woodworking and metalworking, but also for the chipping process. We found only slight wear of the knives. The wear of the knives is also reflected in the wood, by the presence of elements from the knife in the wood chips as well as in the wood particles that remained on the knife after chipping.
Disclosure statement
No potential conflict of interest was reported by the author(s).
Additional information
Funding
References
- Anca-Couce, A., et al., 2020. Assessment of biomass pyrolysis TGA with an international round robin. Fuel, 276, 118002. doi:10.1016/j.fuel.2020.118002.
- Aremu, M.O., Aperolola, S.O., and Dabonyan, O.O., 2015. Suitability of Nigerian corn husk and plantain stalk for pulp and paper production. European Scientific Journal, 11 (30), 146–152.
- ASTM D1107-21, 2021. Standard test method for ethanol-toluene solubility of wood. West Conshohocken, PA: ASTM International.
- Bhagia, S., et al., 2022. Nanoscale FTIR and mechanical mapping of plant cell walls for understanding biomass deconstruction. ACS Sustainable Chemistry & Engineering, 10 (9), 3016–3026. doi:10.1021/acssuschemeng.1c08163.
- Čermák, P., et al., 2022. Wood-water interactions of thermally modified, acetylated and melamine formaldehyde resin impregnated beech wood. Holzforschung, 76 (5), 437–450. doi:10.1515/hf-2021-0164.
- Cho, I.S., Amanov, A., and Kim, J.D., 2015. The effects of AlCrN coating, surface modification and their combination on the tribological properties of high speed steel under dry conditions. Tribology International, 81, 61–72. doi:10.1016/j.triboint.2014.08.003.
- Cristóvaõ, L., et al., 2011. Tool wear for lesser known tropical wood species. Wood Material Science and Engineering, 6 (3), 155–161. doi:10.1080/17480272.2011.566355.
- Ding, F., et al., 2009. Effects of some wood chip properties on pulp quality. Pulp and Paper Canada, 110 (6), 20–23.
- Ekevad, M., Cristóvaõ, L., and Marklund, B., 2012. Wear of teeth of circular saw blades. Wood Material Science and Engineering, 7 (3), 1–4. doi:10.1080/17480272.2012.669405.
- Esteves, B., et al., 2013. Chemical changes of heat treated pine and eucalyptus wood monitored by FTIR. Maderas: Ciencia y Tecnología, 15 (2), 245–258.
- Eugenio, M.E., et al., 2019. Alternative raw materials for pulp and paper production in the concept of a lignocellulosic biorefinery. In: A. Pascual and M. Martin, eds. Cellulose. IntechOpen. doi:10.5772/intechopen.90041.
- Facello, A., et al., 2013. The effect of knife wear on chip quality and processing cost of chestnut and locust fuel wood. Biomass and Bioenergy, 59, 468–476. doi:10.1016/j.biombioe.2013.07.012.
- Faix, O., Meier, D., and Fortmann, I., 1990. Thermal-degradation products of wood. Gas chromatographic separation and mass spectrometric characterization of monomeric lignin derived products. Holz als Roh-und Werkstoff, 48 (7–8), 281–285.
- Freitas, T.P., et al., 2018. Environmental effect on chemical composition of eucalyptus clones wood for pulp production. CERNE, 24 (3), 219–224. doi:10.1590/01047760201824032558.
- GOST 23.208-79, 1979. Ensuring of wear resistance of products. Wear resistance testing of materials by friction against loosely fixed abrasive particles.
- GOST 3647-80, 1982. Abrasives. Grain sizing. Graininess and fraction. Test methods.
- Heidari, M., et al., 2013. Study of the wear mechanisms of chipper-canter knives used in primary transformation of wood. In: Materials science and technology conference and exhibition, MS&T’13, Montreal, 8 p.
- Hill, C., Altgen, M., and Rautkari, L., 2021. Thermal modification of wood – a review: chemical changes and hygroscopicity. Journal of Materials Science, 56, 6581–6614. doi:10.1007/s10853-020-05722-z.
- Horman, I., Busuladžić, I., and Azemović, E., 2014. Temperature influence on wear characteristics and blunting of the tool in continuous wood cutting process. Procedia Engineering, 69, 133–140.
- ISO 11885, 2007. Water quality. Determination of selected elements by inductively coupled plasma optical emission spectrometry (ICP-OES).
- ISO 13878, 1998. Soil quality – determination of total nitrogen content by dry combustion (“elemental analysis”).
- ISO 6508-1, 2016. Metallic materials – Rockwell hardness test – part 1: test method.
- Jaroš, A. and Fiala, Z., 2016. Investigation of the influence of PVD coatings deposited on HSS milling cutter. Manufacturing Technology, 16 (3), 506–512.
- Jeon, S., et al., 2017. Knife-edge interferometry for cutting tool wear monitoring. Precision Engineering, 50, 354–360. doi:10.1016/j.precisioneng.2017.06.009.
- Kalincová, D., Ťavodová, M., and Jakubéczyová, D., 2018. Quality evaluation of the coatings and its influence on the wood machining tool wear. Manufacturing Technology, 4, 578–584.
- Kamperidou, V., 2019. The biological durability of thermally- and chemically-modified black pine and poplar wood against basidiomycetes and mold action. Forests, 10 (12), 1111. doi:10.3390/f10121111.
- Kara, S. and Li, W., 2011. Unit process energy consumption models for material removal processes. IRP Annals, 60 (1), 37–40. doi:10.1016/j.cirp.2011.03.018.
- Kazlauskas, D., et al., 2022. Wear behaviour of PVD coating strengthened WC-Co cutters during milling of oak-wood. Wear, 498–499, 204336. doi:10.1016/j.wear.2022.204336.
- Klamecki, B., 1979. A review of wood cutting tool wear literature. Holz als Roh-und Werkstoff, 37, 265–276.
- Kováč, J., et al., 2014. The impact of design parameters of a horizontal wood splitter on splitting force. Drvna Industrija, 65 (4), 263–271. doi:10.5552/drind.2014.1335.
- Kováč, J., et al., 2022. The influence of the coating on the saw blade on the energy intensity of cross-cutting of wood. Coatings, 12, 1803. doi:10.3390/coatings12121803.
- Krilek, J., et al., 2021. Design of a stationary disc chipper project for dendromass chipping with stress analysis FEM methods. BioResources, 16 (4), 8205–8218.
- Kubovský, I., Kačíková, D., and Kačík, F., 2020. Structural changes of oak wood main components caused by thermal modification. Polymers, 12, 485. doi:10.3390/polym12020485.
- Kuljich, S., Hernández, R.E., and Blais, C., 2017. Effects of cutterhead diameter and log infeed position on size distribution of pulp chips produced by a chipper-canter. European Journal of Wood and Wood Products, 75 (5), 747–760. doi:10.1007/s00107-016-1150-y.
- Kumar, R. and Jagath, C., 2013. Boundary element methods for thermal problems – review. International Journal of Engineering Research & Technology (IJERT), 2 (10), 2486–2496. doi:10.17577/IJERTV2IS100669.
- Malkov, S., Tikka, P., and Gullichsen, J., 2001. Towards complete impregnation of woodchips with aqueous solutions. Paperi Ja Puu, 83 (6), 468–473.
- Nadolny, K., et al., 2020. Experimental studies on durability of PVD-based CrCN/CrN-coated cutting blade of planer knives used in the pine wood planing process. Materials, 13, 2398. doi:10.3390/ma13102398.
- Okai, R., Tanaka, C., and Iwasaki, Y., 2005. Influence of mechanical properties and mineral salts in wood species on tool wear of high-speed steels and satellite-tipped tools – consideration of tool wear of the newly developed tip-inserted band saw. Holz als Roh- und Werkstoff, 64, 45–52.
- Pichler, P., et al., 2018. Evaluation of wood material models for the numerical assessment of cutting forces in chipping processes. Wood Science and Technology, 52, 281–294. doi:10.1007/s00226-017-0962-1.
- Poje, A., et al., 2018. The effect of feedstock, knife wear and work station on the exposure to noise and vibrations in wood chipping operations. Silva Fennica, 52 (1), 1–14. doi:10.14214/sf.7003.
- Porankiewicz, B., et al., 2006. Highspeed steel tool wear during wood cutting in the presence of high-temperature corrosion and mineral contamination. Wood Science and Technology, 40 (8), 673–682. doi:10.1007/s00226-006-0084-7.
- Porankiewicz, B. and Grönlund, A., 1991. Tool wear-influencing factors. In: Proceedings of the 10th International Wood Machining Seminar, University of California, Richmond, CA, USA, October 21–23, 220–229.
- Porankiewicz, B., Sandak, J., and Tanaka, C., 2005. Factors influencing steel tool wear when milling wood. Wood Science and Technology, 39 (3), 225–234. doi:10.1007/s00226-004-0282-0.
- Ramasamy, G. and Ratnasingam, J., 2010. A review of cemented tungsten carbide tool wear during wood cutting processes. Journal of Applied Sciences, 10 (22), 2799–2804. doi:10.3923/jas.2010.2799.2804.
- Reimer, L., 1998. Electron scattering and diffusion. In: Scanning electron microscopy. Springer series in optical sciences. Berlin: Springer, Vol. 45, 57–134. doi:10.1007/978-3-540-38967-5_3.
- Salh, R., 2011. Silicon nanocluster in silicon dioxide: cathodoluminescence, energy dispersive X-ray analysis and infrared spectroscopy studies. In: S. Basu, ed. Crystalline silicon – properties and uses. Rijeka: InTech. doi:10.5772/22607.
- Sandberg, D., Haller, P., and Navi, P., 2013. Thermo-hydro and thermo-hydro-mechanical wood processing: An opportunity for future environmentally friendly wood products. Wood Material Science and Engineering, 8 (1), 64–88. doi:10.1080/17480272.2012.751935.
- Schalk, N., Tkadletz, M., and Mitterer, C., 2022. Hard coatings for cutting applications: physical vs. chemical vapor deposition and future challenges for the coatings community. Surface and Coatings Technology, 429, 127949. doi:10.1016/j.surfcoat.2021.127949.
- Seifert, V.K., 1956. About a new method for rapid determination of pure cellulose (in German). Das Papier, 10, 301–306.
- Sluiter, A., et al., 2012. Determination of structural carbohydrates and lignin in biomass. Golden, CO: National Renewable Energy Laboratory, NREL/TP-510-42618.
- Souza, P.S., et al., 2020. Analysis of the surface energy interactions in the tribological behavior of ALCrN and TIAlN coatings. Tribology International, 146, 106206. doi:10.1016/j.triboint.2020.106206.
- Spinelli, R., Glushkov, S., and Markov, I., 2014. Managing chipper knife wear to increase chip quality and reduce chipping cost. Biomass and Bioenergy, 62, 117–122. doi:10.1016/j.biombioe.2014.01.007.
- STN ISO 10694, 2001. Soil quality. Determination of organic and total carbon after dry combustion (elementary analysis).
- Szász-Len, A.M., Holonec, L., and Pamfil, D., 2016. Mineral substances in stem wood tissue of European beech (Fagus sylvatica L.). ProEnvironment, 9, 41–55.
- Ťavodová, M., et al., 2022. Analysis of damaged delimber knives and the possibility of increasing their service life. Manufacturing Technology, 22 (1), 80–88. doi:10.21062/mft.2022.011.
- Telmo, C., Lousada, J., and Moreira, N., 2010. Proximate analysis, backwards stepwise regression between gross calorific value, ultimate and chemical analysis of wood. Materials Science Bioresource Technology, 101 (11), 3808–3815. doi:10.1016/j.biortech.2010.01.021.
- Tjeerdsma, B. and Militz, H., 2005. Chemical changes in hydrothermal treated wood: FTIR analysis of combined hydrothermal and dry heat-treated wood. Holz als Roh- und Werkstoff, 63 (2), 102–111.
- Varghese, A., Kulkarni, V., and Joshi, S.S., 2022. Modeling cutting edge degradation by chipping in micro-milling. Wear, 488–489, 204141. doi:10.1016/j.wear.2021.204141.
- Výbohová, E., et al., 2018. The effect of heat treatment on the chemical composition of ash wood. BioResources, 4, 8394–8408. doi:10.15376/biores13.4.8394-8408.
- Warcholinski, B. and Gilewicz, A., 2011. Multilayer coatings on tools for woodworking. Wear, 271, 2812–2820.
- Warcholinski, B. and Gilewicz, A., 2022. Surface engineering of woodworking tools, a review. Applied Sciences, 12, 10389. doi:10.3390/app122010389.
- Wise, L.E., Murphy, M., and D’ Addieco, A.A., 1946. Chlorite holocellulose, its fractionation and bearing on summative wood analysis and on studies on the hemicelluloses. Paper Trade Journal, 122, 35–44.
- Wu, D., et al., 2023a. A quantitative model that correlates sharpness retention and abrasive wear of knife blades. Wear, 518–519, 204634. doi:10.1016/j.wear.2023.204634.
- Wu, D., et al., 2023b. Enhanced wear resistance of blades made of martensitic steels: A study of diverse α′-matrix/carbide microstructures. Materials Characterization, 201, 112939. doi:10.1016/j.matchar.2023.112939.
- X48CrMoV8-1-1, 2019. Lexicon of metals 2.7 (in Czech). Praha: Verlag Dashöfer, 4/2019. Available from: https://www.dashofer.cz/ [Accessed 27 February 2023].