ABSTRACT
Copper-based functionally gradient composite material is developed using powder metallurgy processing technique, as a potential wind turbine brake pad material. The developed composite has a gradient composition of Cu, CeO2, Al2O3, Fe, and Cg to enable joint strength at the interface (brake calliper) and wear resistance at the contact surface (brake disc). The article presents a comprehensive analysis on the microstructure, microhardness, and tribological performance of the developed composite. The wear mechanism is deduced through surface morphology, elemental composition, and phase composition analysis using field emission scanning electron microscope, energy dispersive X-ray spectroscope, X-ray diffractometer, and X-ray photoelectron spectroscope. A maximum hardness of 198.2 HV was obtained at the contact surface. Experimental values from tribology tests show that a decreasing trend was obtained with a wear rate of 2.013 × 10−7 g N-m−1 and a friction coefficient was 0.215.
GRAPHICAL ABSTRACT
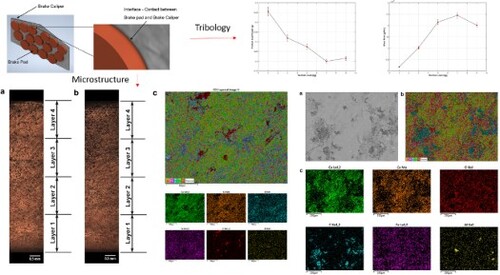
Acknowledgements
Vummitti Chandhan Kumar contributed to the conceptualization, devised the methodology, performed the formal analysis of the data, and writing – original draft preparation; G. Srivathsan performed the investigation, validation of the data, and writing – original draft preparation; A. Vignesh Ram processed the data analysis, visualization of the work, and contributed to the resources; Vallabhaneni Sravan carried out the investigation and performed data analysis; Dr. M. Govindaraju contributed to the resources, performed formal analysis, designed the methodology, reviewed and supervised the work; Dr. R. Vaira Vignesh contributed to the conceptualization, processed formal analysis of the research data, aided in project administration, and writing – review of the manuscript; Mr K Rajesh Kannan carried out validation of the data and performed formal analysis of the data.
Disclosure statement
No potential conflict of interest was reported by the author(s).
Data availability statement
All data generated or analysed during this study are included in this published article.
Correction Statement
This article was erroneously published in the first issue of 2023, 17-01 (Special issue on Manufacturing: Tribology, Surface Engineering and Lubricants). Please see Correction (https://doi.org/10.1080/17515831.2023.2240065)