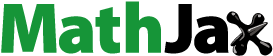
ABSTRACT
The consumption of eggshell powder (ES) as an affluent source of calcium carbonate (CaCO3) can efficiently solve both ecological and financial interest. The use of eggshell waste in eco-composite materials (ECPCMs) is an attempt to reduce waste's negative effects. Eco-composite powders of polyethylene glycol (PEG) and calcium carbonate (CaCO3) were obtained by mechanical grinding. Compression molding was used to produce plates from the ground powders. FTIR spectroscopy and X-ray diffraction analysis showed that the ECPCMs were physically combined and the crystallinity of the two components was affected. According to TGA, the thermal stability of ECPCMs was improved, thanks to the use of eggshell waste powder. On the other hand, the results of the DSC showed that ECPCM with the addition of 90 wt% of PEG in the mixture provides excellent thermal stability and high energy storage density. In light of its high latent heat storage capacity of 156.1 J/g as well as its ability to prevent PEG exudation. Significant enhancement in melting-solidification time shows an improvement in Thermal Energy Storage (TES) response time by adding ES to the PCM. The obtained results indicate a good potential for industrially applied ECPCMs.
Highlights
Eco-composite (ECPCMs) prepared by compression molding method.
The addition of EG gives further support for the shape stabilization.
ECPCM provides excellent thermal stability and high energy storage density.
Enhancement in melting-solidification time by adding ES to the PCM.
ECPCM as a candidate for an application in buildings of hot and dry climates.
Introduction
Over the past decades, extensive research into latent heat thermal energy storage (LHTES) materials, also known as phase change materials (PCM), has aimed to improve energy density, durability, lifespan, thermal properties and profitability (Citation1–4). The use of phase change materials (PCM) allows large amounts of heat to be stored and released with reduced volumes using latent heat storage during melting and solidification at specific temperatures. Indeed, thanks to the solid–liquid phase shift, PCMs reduce temperature variations and improve solar energy consumption (Citation5). A wide range of promising inorganic and organic PCMs, including ice, salt hydrates, fatty acids, paraffin waxes, and n-carboxylic acids, have been studied for latent heat storage applications. Among various organic PCMs, polyethylene glycol (PEG) is the most promising one due to its suitable phase change temperature, high latent heat storage capacity, good chemical and thermal reliability, lower vapor pressure in the melt, biodegradability, and is commercially available at competitive prices (Citation6).
The properties of PEG, such as melting temperature and LHTES capacity, can be adjusted based on its average molecular weight, as evaluated by Kim and co-workers (Citation7). The molecular weight of PEG ranges from 100 to 600,000. The physical properties of PEG are largely determined by its chain length. Usually, PEG with a molecular weight greater than 2000 is a hard crystalline solid with a melting point of about 60°C (Citation8). The broad molecular weight distribution of PEG provides the opportunity to obtain the necessary phase change temperature. However, pure PCMs struggle to meet all these requirements, facing problems such as low thermal conductivity, low stability and phase segregation. To address these challenges, additives have been used to modify pure PCMs (Citation9, Citation10, Citation11). Although these approaches have improved the performance of PCM, they have also complicated the manufacturing process and increased costs, making large-scale production difficult. To overcome this problem, cost-effective technologies for bio-composite phase change materials (ECPCM) need to be developed, which can be easily scaled up at low cost (Citation12). Additionally, there is a lack of understanding regarding the relationship between manufacturing processes and PCM performance.
For low temperature applications, ECPCMs can be incorporated into building insulation materials (Citation13), used for domestic space heating (Citation14) or woven into fabrics for thermal comfort (Citation15). ECPCMs are capable of maintaining shape stability and preventing PCM leakage during melting by being made of a PCM for heat storage, a support material (matrix) for structural stability and/or of an additive to improve thermal conductivity. Support materials must be compatible with the PCM chemically and structurally under working conditions. Several types of bio-additives can be used in phase change materials (Citation16). In the field of technical engineering research, there is an increasing emphasis on sustainable and environmentally friendly products. As a result, recycled materials or waste from nature, such as chicken eggshells, are used as a green alternative in construction. Chicken eggshell powder which is generally made of ceramic materials consisting of the cuticle, crystal layer, spongy calcareous layer pores, cores and mammillary layer (Citation17).
The chemical composition (by weight) of the eggshell by-product has been reported as follows: calcium carbonate (94%), magnesium carbonate (1%), calcium phosphate (1%), and organic matter (4%) (Citation18). Notably, the by-product eggshell generated by food processing and manufacturing plants is inevitably composed of calcium carbonate (eggshell) and eggshell membrane. Sometimes, few by-products were reused as fertilizer or soil conditioner due to their high content of nutrients such as calcium, magnesium and phosphorus (Citation19). Based on the recovery and reuse of bioresources, the value-added use of this food processing by-product has increased slightly in recent years. It was reported to target the use of chicken eggshell as a possible bone substitute (Citation20), as a starting material for the preparation of calcium phosphate-based bio-ceramics (e.g. hydroxyapatite) (Citation21), and as a low-cost adsorbent for the removal of ionic pollutants from aqueous solution. The use of waste eggshells in composite materials (Citation22) is an attempt to reduce the negative effects of waste. The nano-porosity structure derived from eggshells allows interaction with polymer matrices. There are scientific reports on the use of biogenic eggshell fillers to modify polymers such as polystyrene, LLDPE, epoxy, polypropylene, NBR, HDPE, PLA and PVA (Citation23–28).
Although interest in using waste eggshells as polymer fillers is growing, there is little information available on the use of waste eggshells to prevent PCM leakage during melting and maintain shape stability. Studies on the thermal properties of these composites are still limited, so more in-depth studies could be carried out. In this experimental study, the innovative idea of mixing polyethylene glycol (PEG)/eggshell powder (ES) is investigated as a natural energy storage material that would be beneficial in technical engineering applications. To maintain the ecological quality of the materials obtained, we have implemented a new own production process based on fine grinding in a planetary ball mill.
Considering the efficient utilization of eggshell particles, it is necessary to make finer powder by the size reduction method because the properties (e.g. surface area) of the powder material mainly depend on its size of particle, its shape and its porosity (Citation29). Mechanical milling of bio-composite phase change materials (ECPCM) is a facile and low-cost process. However, the ideas and concepts of using mechanical alloying for processing polymeric materials first appeared by Shaw in 1988 (Citation30), where he and his team presented through their preliminary experiments in the early 1990s the possibility of using mechanical alloying technique for processing in Polymer materials and the extent of their implementation and promising for the future (Citation31, Citation32). After the initial efforts and success of Shaw's team, various studies were conducted to use MA for polymer processing. For example, Ishida reported a study on MA for PTFE and PE milled separately and as 50/50 blends (Citation33). Likewise, Farrel et al. studied MA and MM blends of PP and Vectra B950 using a SPEX 8000 mixer/grinder with a feed ratio of 4:1 (Citation34). Castricum et al. also worked on the grinding of pure polymers and structural phase transformation, including PS and polyethylene glycol (PEG) using a vibrating mill and PE using a planetary mill (Citation35). Later, many studies with different ideas and concepts were carried out (Citation36, Citation37). For example, using MA to coat a ceramic (BaTiO3) with a polymer (LaRC-TPI) for grain boundary composite capacitor applications (Citation38), and studying the miscibility of low-density polyethylene (LDPE) and isotactic polypropylene (PP) by (CO2 mechanical alloy assisted) (Citation39).
The major problem of renewable energy is intermittent. Integrating Latent heat (LHTES) systems into renewable energy production is an efficient way to overcome the problem and supply energy according to demand. There was a prevalent use of biobased PCMs with PEG. The task at hand was to identify an inorganic supporting matrix that occurs naturally and is easily accessible and abundant. Calcium carbonate (CaCO3) is one such compound that satisfies both needs.
The aim is to investigate ECPCMs that are eco-friendly, cheap, and have efficient energy storage capacity. As a result, recycled or waste materials sourced from nature, such as chicken eggshells, are being used as a green alternative in construction. Chicken eggshells are widely available as waste from various sources like hatcheries, fast food restaurants, poultry industries, egg product factories, and households. However, the disposal of eggshells presents challenges related to odor, cost, abrasiveness, and the availability of disposal sites. The consumption of eggshell powder (ES) as an affluent source of calcium carbonate (CaCO3) can efficiently solve both ecological and financial interest. The use of eggshell waste in eco-composite materials (ECPCMs) is an attempt to reduce waste's negative effects.
In this experimental study, the innovative idea of a shape stabilized composite phase change material based on polyethylene glycol (PEG)/eggshell powder (ES) is investigated as a natural energy storage material which would be beneficial in technical engineering applications. Using CaCO3 as a support material provides excellent form stability and allows for a high PEG loading capacity. The preparation process and materials used are environmentally friendly and sustainable. These eco-composites demonstrate exceptional thermal stability and can be easily reused, making them a promising option for incorporating ECPCM in different applications, particularly in building thermal management. This eco-friendly technique offers a sustainable solution for various uses.
Experimental section
Waste eggshells recovered from chicken eggs already cooked for half an hour at 60°C. The internal membranes were detached and the eggshells were exposed to sunlight for a week. Then they were crushed in an agar mortar. The powder thus obtained is subjected to finer grinding in a planetary ball mill (Fritsch Pulverisette 7) at a speed of 400 rpm for 4 h. The grinding is stopped every 30 min for 10 min.
The PCM used in this study was polyethylene glycol PEG-6000 (Molecular Weights 6000 g.mol−1) of approximately 55°C and a density of 1.2 g.cm−3. PEG and crushed shell powders at 0, 10, 20, 30, 40 and 50% by weight were mechanically alloyed for 2 h under the same conditions of grinding eggshell waste. The mechanically alloyed powders were then compression molded to produce PEG/eggshell (P/E) composite plates from the melt at 60°C into cylindrical shaped plates measuring 100 mm × 80 mm × 0.7 mm using a 10-ton AMS hot melt press (). The various mass ratios of the constituent elements in each of the 20 g samples are displayed in
.Table 1. Summary of ECPCMs (PEG/eggshell) composition (wt. %).
Characterization included FTIR spectroscopy (ATR), X-ray diffraction (XRD), thermogravimetric analysis (TG), differential scanning calorimetry (DSC), and IR thermography (IRT) observations. Infrared spectroscopy was examined using a Perkin Elmer FTIR BX spectrum system employing an ATR mode between 4000 and 500 cm−1. X-ray diffraction (XRD) was carried out using an X-ray diffractometer of the Philips PW1700 Automated Powder Diffractometer type (40 kV and 40 mA) with a wavelength λ was 1.5418 Å and a speed scanning (2θ) of 2°/min. Thermogravimetric analysis (TGA) was carried out on a Perkin-Elmer TGA7 analyzer with a heating rate was 10°C/min and the weight of the sample was about 4 mg under an oxygen atmosphere at a flow rate of 20 ml/min. The DSC calorimeter used in this work is a Perkin-Elmer DSC7 under nitrogen at a flow rate of 20 ml/min of a sample of approximately 6 mg sealed in an aluminum pan under a heating rate of 10°C/min.
To determine the effectiveness of heat transfer across different types of ECPCM samples, an IR thermography (IRT) test was conducted with a FLIR C3 IR camera. illustrates the schematic setups used for Infrared thermography (IRT) analysis. The thermal camera was placed at a distance of 400 mm to record the IR images. A sample with a cylindrical shape measuring 14 mm in diameter was placed on a glass petri dish on a hot plate. The PCM and each ECPCM samples were heated to 70°C and then cooled to room temperature. By conducting an IRT test at different time intervals of 120 s, the temperature distribution on the samples’ surface during this test was captured.
Results and discussions
The interactions between PEG and support materials (eggshell waste) were characterized by FTIR spectroscopy at room temperature. shows the FT-IR spectra of (a) eggshell powder, (b) PEG, and (c) PEG/eggshell sample. The FT-IR spectrum ((a)) of the chicken eggshell waste sample in form of fine powder ground for 4 h shows vibration bands confirming that is essentially composed of the carbonate phase (Citation22). The most intense band observed at 1415 cm−1 is associated with the presence of carbonate minerals in the eggshell matrix (Citation40). Furthermore, the two well-defined bands at approximately 876 and 713 cm−1 are respectively attributed to the asymmetric stretching and out-of-plane and in-plane deformation modes of the carbonate group in CaCO3 (Citation41). On the PEG spectrum ((b)), the band around 1100 cm−1 is due to the stretching vibration of C–O–C. The strong peaks at 2878 and 962 cm−1 result from the stretching vibrations of the CH2 functional group (Citation42). The FTIR spectrum of PEG/eggshell shown in (c) contains bands due to both the eggshell (CaCO3) and PEG. Indeed, the widening of bands around 1450 cm−1 and the appearance of a low intensity band at 860 cm−1 is linked to the vibration of carbonate groups coming from eggshell particles. The absence of either additional peaks or shifts of individual peaks in the spectrum of the PEG/eggshell composite confirms that the two components are well mixed and only physical mixing occurs. Therefore, we conclude that the combination of eggshell and PEG only results in the physical absorption of PEG into the eggshell particles and no chemical interactions occur.
XRD
The PEG is observed to show major XRD peaks at two theta of 19.8, 23.8 and some minor peaks at 26.9, 36.6, 40.5 and 46.2 as also reported elsewhere (Citation43, Citation44). The X-ray diffraction patterns of PEG-6000 (PEG), eggshells alone and the ECPCM are shown in . It can be observed that the diffractogram of eggshells is very similar to that of CaCO3, showing only a single crystalline phase–calcite (Citation19, Citation20, Citation45). The high-intensity XRD peaks appearing between 2θ = 28° and 50° are characteristic peaks of the calcite phase (CaCO3). These results confirm the presence of calcite as the main component of the ES powder (Citation17, Citation18). These observations are in good agreement with the FTIR characterization, which demonstrates the presence of CaCO3 as the major composition of the ES micro-particles. The XRD of the bio-composite allowed us to confirm the presence of all peak’s characteristic both of ES and PEG. The compared XRD pattern of different samples are quite similar, except for a little difference related to the intensity of the peaks that could be related to the variation of the composition associated with eggshell confirming that the mixture is physical. However, there is a variation in the intensity of the peaks with a widening and also a shift in the positions of the peaks. The intensity of the peak around 29° ((b)) related to the eggshell decreases from compound P50E50 to the other two compounds P70E30 and P90E10 and this is due to the integration of PEG into the eggshell structure. This means that the crystal structure of eggshells is preserved upon PEG integration with weak contraction of the crystal lattice proven by the shift of diffraction peaks towards high values of 2θ (Citation46). The displacement observed on the outgoing peak towards 29° characterizing the plane (104) of the eggshell ((b) and ) can be examined by calculating the inter-planar distance d (104) by applying Bragg's law (n.λ = 2.dhkl.sinθ). It is clear that the microstructure of the eggshell material was modified by mechanical stress during grinding, thus reflecting a change in the crystalline parameters of the eggshell powder (Citation46). The Scherrer equation was used to calculate the crystallite size of eggshell powder as follows: d = K. λ/ (β. cosθ). Where d is the diameter of crystallite, β is Full-Width Half Maximum (FWHM), K is the constant (0.89–0.9), and λ is the wavelength (1.5406 Å). According to and , a correlation exists between the sample's FWHM and crystallite size. Larger crystallite sizes are actually indicated by higher FWHMs, consistent with the theoretical calculation of the Scherrer equation. Similar results of the evolution of structural properties were found after grinding powders such as polymer (Citation47), talc (Citation48) and titanium silicatite (Citation48). On the other hand, the intensity of the two peaks around 19 and 23 related to PEG increases from the compound P50E50 to the compounds P70E30 and P90E10, which is due to the increase in the amount of PEG and to the decrease of the PEG crystallinity by the presence of eggshell powder ((c)).
Figure 2. The pattern of X-ray diffraction of (a) egg-shell, PEG and PEG/egg-shell composites; (b) 2θ domain 28.5–30 and (c) 2θ domain 18.5–20.
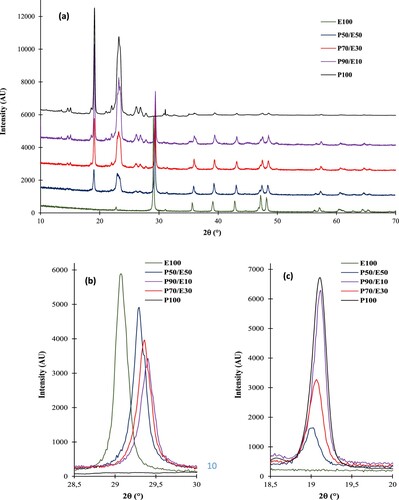
Table 2. Intensity, FWHM, D-spacing, and crystallite size of eggshell powders.
The X-ray diffraction results observed on eggshell powder in the presence of PEG can be attributed to the diffusion of PEG chains into the microstructure of the eggshell powder during grinding leading to deformation (Citation49) and the reduction in the size of calcite crystals. Indeed, the PEG used, like a PCM, has a stabilizing effect in the formation of eco-composites based on eggshell without agglomeration. Additionally, PEG plays an important role in the field of nanotechnology, where PEG is used as a reducing and stabilizing agent. Using PEG, inorganic nanoparticles were prepared without agglomeration (Citation50, Citation51, Citation52).
TGA/DTG
Thermogravimetry was carried out to evaluate the thermal stability of the samples. The TGA/DTG curves of PEG, eggshell and the different eco-composites are illustrated in . It can be seen that PEG and eggshell exhibit a mainly degraded trend in a single step. The DTG curve of PEG presents a degradation peak towards east of 409°C characteristic of the total decomposition of the organic chain of the polymer. On the other hand, eggshell has good thermal stability up to 630°C. Complete eggshell calcination was observed between 630°C and 780°C with a weight loss of 43%, probably linked to the decomposition of CaCO3 into CO2 and CaO (Citation53). In terms of thermal stability of the composites, the TGA thermogram in the presence of eggshell waste demonstrates that these microparticles can function in a similar way to a flame retardant (Citation54, Citation55, Citation56). The TGA curves of the P/E eco-composites show an increase in the decomposition onset temperature compared to PEG ((a)). The characteristic thermal decomposition variables, notably T20% (temperature at which mass loss is 20%), are shown in table of (a). For temperatures at 20% mass loss, we observe a significant increase in the degradation temperature of ECPCMs compared to pure PEG. According to the TGA curves, the T20% of PEG and eggshell are 374°C and 740°C, respectively. The table shows that the T20% of the ECPCM are higher than that of pure PEG. For all compositions, where T20% is strictly greater than 374°C, demonstrating thermal stability. Comparatively, the P90/E10 eco-composite with the lowest eggshell content has a T20% = 380°C, while the P50/E50 has a much higher T20% = 405°C. The results suggest that P/E eco-composites maintain good thermal stability below 380°C.
Leakage-proof properties
Leakage-proof is an important characteristic to evaluate the form stability, efficiency, and durability of ECPCMs. To determine the shape stability, samples were heated above the melting point of the PCM and compared. The initial sample mass, denoted as M0, was placed on a filter paper and then placed in a thermostat set at 70 degrees Celsius. The sample was allowed to naturally cool, and its weight was measured every hour using an analytical balance. This process was repeated in successive cycles of one hour each, with the filter paper being replaced after each cycle. Mn is the mass of the sample after each heat treatment cycle.
The amount of leakage can be determined using the equation provided in reference (Citation4).
(a) displays the plotted relationships between time and leakage rates of six BCPCMs. Additionally, (b) shows seepage photos of all the samples on filter paper after consecutive hours of heating. After one-hour, noticeable seepage of P90/E10 to P50/E50 occurred, with leakage rates of 1.1%, 0.9%, 0.9%, 0.7% and 0.7% respectively. The main cause of leakage was attributed to residual paraffin on the surface resulting from the melt blending process (Citation57). The leakage rate curves for all samples stabilized after 15 h.
Figure 4. (a) Leakage tests of ECPCMs samples according to time. (b) Shape-stable photographs of all samples after consecutive hours of heating (1, 10 and 20 h).
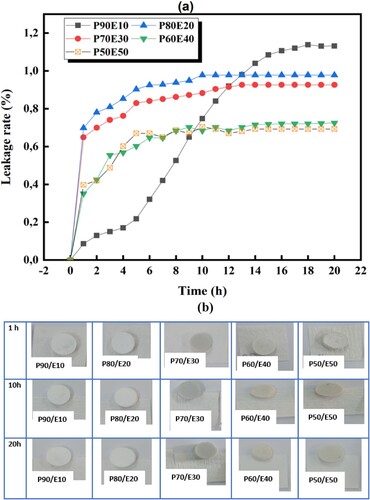
Accordingly, the presence of CaCO3 as a support material ensures exceptional form stability and a high PEG loading capacity. The eggshell hindered the movement of paraffin chains within the matrix, thus reducing paraffin leakage in the composites. The good stability observed can be attributed to the high compatibility of the eggshell with the hydrocarbon chain of PEG. This particular blend can absorb and retain a significant volume of liquid PEG, resulting in a thermally stable PCM. Using ground eggshells as a filler in PCM compounds is a great way to handle this bio-waste. This bio-waste can be effectively managed by using ground eggshells as a filler in PCM compounds, as they have a similar composition to CaCO3 and do not need any special treatment. The ideal amount of eggshell (ES) in the compound should take into account its ability to stabilize the shape and its latent heat.
DSC
This study presents the results of investigation a novel bio-based Phase Change Material for LHTES application. The determination of the latent heat of PEG (P100) and bio-composite of PCM (ECPCMs) with various PEG mass fractions as a function of temperature with sufficient accuracy in enthalpy and temperature is particularly attractive due to the ability of bio-based PCM to provide high-energy storage density in a quasi-isothermal process and crucial in PCM application. The structural evolution of the different bio-composite as a function of temperature and the study of their thermal energy storage capacity were followed by DSC analyses. The DSC was used to investigate the phase change properties of the PCM and the innovative bio-composite (PEG/Eggshell) during their respective endothermic and exothermic cycles. As shown in , DSC curves of the bio-based PCM (P100) and the prepared ECPCMs during the melting and solidification processes respectively. From the DSC results, the ECPCM melts at 55.7°C and solidifies at 44.8°C. Consequently, it can be stated that PEG is associated with a relatively high supercooling, i.e. about 10.9°C. In all plots, as expected, the thermal properties were influenced by the additives of eggshell as presented in . According to the obtained results, the measured values of ΔHm and ΔHs of P100 are 180.4 and 164.6 J. g−1, respectively. This result shows that PEG has a higher heat storage capacity compared to paraffins like RT55, which typically have a fusion temperature of 50–60°C (Citation58). This demonstrates that PEG is a cost-effective and bio-based solution with excellent thermal properties. However, it occurs at much lower temperatures, which is an interesting application in terms of seasonal passive building envelope components (Citation59).
Table 3. Thermal properties of PCM and all ECPCM samples.
Overall, PEG content and dimensional stability are considered to be two key factors affecting the thermal energy storage capability of ECPCM. In this study, the maximum mass fraction of PEG in ECPCM was 90%, and there was no liquid leakage during the phase change process. In all figures, the thermal properties are affected by the addition of eggshells, as expected. As shown in , the measured melting peak temperatures (Tpm) of P100, P90E10, P80E20, P70E30, P60E40, and P50E50 were 55.6°C, 55.5°C, 54.8°C, 51.1°C, 50.9°C, and 50.8°C, and the melting enthalpy was 180.4, 156.1, 135.6, 116.1, 97.4 and 77.5 J/g. The solidification temperatures of P100, P90E10, P80E20, P70E30, P60E40 and P50E50 were 46.5°C, 44.9°C, 45.9°C, 46.4°C and 48.6°C, respectively, while the solidification enthalpy was 164.6, 142.1, 123.9, 106.0, 80.7 and 70.7 J/g, respectively. For all ECPCMs, it can be seen that the phase transition temperature increases with increasing PEG ().
The reason can be attributed to the phase change process ‘application of the second law of thermodynamics (Citation60).
(1)
(1) where S is the change in entropy during the phase change transition, ΔH is the phase change heat per unit mass, and T is the phase change temperature of ECPCMs. ΔH improves while S declines as the mass fraction of PEG rises. The temperature of the phase change consequently drops. Moreover, supercooling of PCMs must be considered as another crucial factor in practical applications. According to the DSC measurement results in , the degree of supercooling may have aided the phase change transition process by reducing the temperature difference between melting and solidification. The results of the corresponding evaluation are shown in . The amount of supercooling of the ECPCMs relative to PEG gradually decreased as the mass fraction of PEG increased P90E10, P80E20, P70E30, P60E40, and P50E50 all had less supercooling than the PEG by 0%, 21%, 45%, 1%, 48%, and 49%, respectively. The findings demonstrate that by adding 50% eggshell powder, the degree of supercooling for the ideal sample can be effectively reduced to 49.3%. The theoretical enthalpy of ECPCMs can be obtained by multiplying the phase change enthalpy of the PCM (ΔHPCM) with its mass fraction in the bio-composite (η), and the equation is as follows:
(2)
(2)
Figure 7. Evolution of supercooling ΔT for PEG (P100) and all ECPCMs (P/E); (Tpm: melting peak temperature of DSC curve. Tpc: crystallization peak temperature of DSC curve).
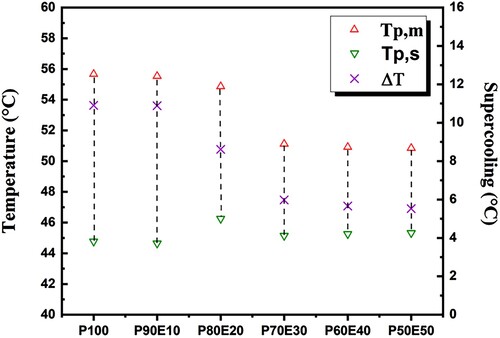
displays a comparison between the real and expected enthalpies of the heat storage mixtures. It is clear that the prepared ECPCMs’ melting and solidifying enthalpies were lower than their theoretical values. Therefore, the actual enthalpies of ECPCMs were lower than the theoretical enthalpies (Citation61). It was likely that the steric effect and drag effect constrained the crystal arrangement and orientation of PEG molecular chains, which caused a decline in the regularities of crystal-line regions and an increase in lattice defects. These deductions are in agreement with the already described XRD results.
Figure 8. Theoretical and measured melting and solidification enthalpies for PCM (P100) and all ECPCMs (P/E).
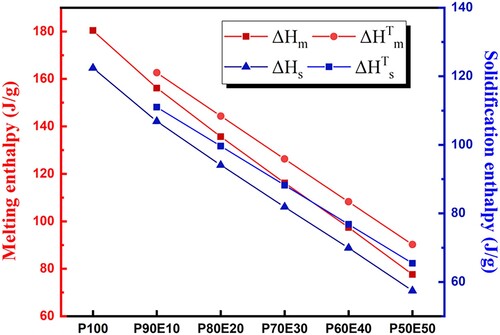
It's interesting to note that the values between the two parameters can be calculated using a simple linear interpolation. It's important to note that the actual enthalpies essentially match the theoretical values. Based on the relationship between the ECPCM's enthalpy and the PEG mass fraction shown in , there is a linear correlation between the loading of PEG and the phase change enthalpy of the bio-composite PCMs. While going through a cyclic endothermic and exothermic process, the heat loss percentage of each prepared composite () barely changed. The prepared composite PCM's phase change performance was further assessed using a typical parameter of heat storage efficiency, and the resulting equation is as follows:
(3)
(3) where
and
represent the phase change enthalpies for melting and solidification, respectively. Furthermore, according to , the percentage of heat loss in pure PEG during the endothermic and exothermic cycles is 8.75% less compared to P90/E10 bio-composite. Four crucial variables, including the impregnation ratio (R), impregnation efficiency (E), thermal storage capability
and relative enthalpy efficiency
, may be used to gauge how well the prepared samples perform during phase changes. The parameters were all calculated using the four equations listed below (Citation62, Citation63).
(4)
(4)
(5)
(5)
(6)
(6)
(7)
(7)
Figure 9. The relation between the PEG mass fraction, enthalpy and the corresponding heat loss percentage for all samples.
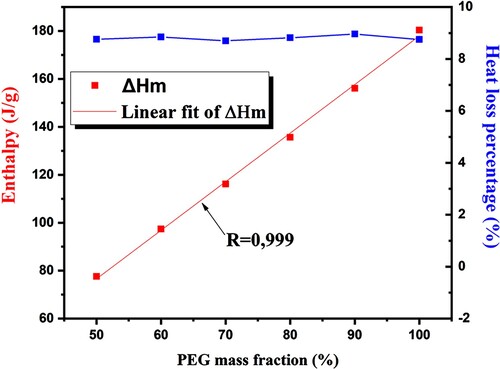
All of the ECPCMs’ calculated results for (R), (E), and
, are displayed in . A high impregnation ratio of 86.54% and an efficiency of 86.45% were attained by the prepared P90/E10 bio-composite. However, the theoretical PEG mass ratio is less than these two values. In actuality, R denotes an efficient PEG impregnation within the eggshell powder structure, while E denotes a PEG performance within the composite for effective latent heat storage. Due to the confinement effect on molecule motion, the phase change of PEG inside the tiny pores hardly ever happens. All of the PEG could not actually function as PCMs. It's interesting to note that the prepared’s thermal storage capacity was 100%, showing that nearly all PEG molecule chains could efficiently store/release heat through a phase transition.
IR thermography
In order to examine how heat is absorbed and released, infrared thermal imaging was employed to display the temperature distribution on the surface of various samples. The temperature scale bar, represented by different colors ranging from dark blue (the lowest) to light blue, yellow, and finally red (the highest), indicates the temperature levels. Through the thermal images (), it was observed that a small and uniform hot region gradually expanded from the top to the middle, with the highest temperature peak at the center (Citation12). At the beginning, both the PCM and ECPCMs have a similar blue color, indicating that their surface temperature matches the room temperature. However, after 120 s, when the hotplate is switched on, the surface temperature of the PCMs starts to gradually increase, leading to a change in colors from blue to light blue and yellow. According to the data shown in (a), the composite P90E10 demonstrates a faster response time for charging (melting) in just 720 s. By observing the color changes in the samples and their relationship with temperature values, we can conclude that the energy storage capacity of the PCMs is significantly enhanced in the blend (Citation5, Citation64). All the blends showed an increase in temperature from room temperature to a temperature higher than 60°C, which is above the melting temperature of pure PEG. However, their stable form was maintained. It was observed that each blend reached a point where the surface temperature started to rise more rapidly, indicating the melting of all PEG. As the surface temperature went beyond the melting point of the PCM, its ability to control temperature gradually decreased. At this stage, the energy began to accumulate in the matrix as sensible heat once again (Citation65, Citation66). When comparing the thermal charge and discharge times of PCM and ECPCMs in , it is evident that the heat storage and release rates of PCM decrease slowly after the addition of ES. Bio-composites typically take longer to complete the heat storage and release process compared to PCM. For example, charging times for P90E10, P80E20, P70E30, P60E40, and P50E50 are 33.33%, 42.86%, 50%, 55.55%, and 60% higher, respectively, compared to P100. Discharging times for the same ECPCMs are also longer, with increases of 23.53%, 31.6%, 35%, 43.48%, and 44.7%, respectively, compared to PCM. Experimental results show that the addition of eggshell powder as a low-cost bio-waste can improve the performance of TES as a heat storage material. The inclusion of eggshell powder in PCM improves the TES response time to demand, but the process of energy release takes a longer time since coagulation began.
Figure 12. Temperature evolution of PCM and ECPCMs during the heat charging and discharging process.
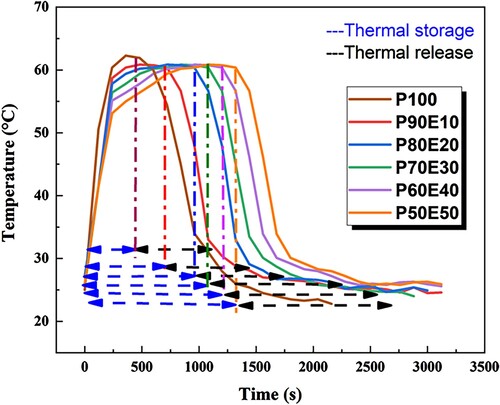
The top surface of the material in contact with the hot plate formed a solid layer of PCM. This layer acts as insulation, separating the liquid PCM from the cooling source and preventing it from losing heat quickly (Citation67, Citation68). Comparatively, the release process took much longer than the melting process as seen in (b). The low thermal conductivity of PCMs leads to slow response rates, but this can be overcome by mixing PCMs with highly thermally conductive materials. The results suggest that the ECPCMs used in this study have the potential to be effective support materials for storing thermal energy and regulating indoor temperature in buildings as presented in .
Table 4. Compares the phase change characteristics of the bio-PCM blends prepared in this study with those of some other bio-PCM blends in the literature.
Conclusion
In this study, we investigated experimentally the thermal potential of a novel eco-composite phase change materials (ECPCMs) composed of PEG (polyethylene glycol) and Eggshell (recovered from the food industry) prepared by compression molding method.
These results demonstrate that the fabricated eco-composite possess excellent thermal energy storage performances, as the PCMs successfully encapsulated inside matrix (Eggshell) can absorb, store and release amounts of latent heat in an almost isothermal phase transition process. This good stability is actually a result of the eggshell's high compatibility with the hydrocarbon chain of PEG. The maximum weight percentage for PEG dispersed in the PCM bio-composites without any leakage of the melted PEG was found as high as 90%. Based on the above discussion, following conclusions can be drawn:
The preparation process and materials used are environmentally friendly and sustainable.
The FT-IR and XRD analyses indicated that no chemical reactions occurred during the preparation process.
The DSC results showed that P90E10 had a large enthalpy of 156.1 J/g and suitable melting temperature (Tpm = 55.5°C), which presents great potential in mid-high temperature TES applications. Five important parameters, including the impregnation ratio (R), impregnation efficiency (E), thermal storage capability
, heat storage efficiency
(%) and relative enthalpy efficiency
, which might represent the phase change performance of the prepared samples. Six indexes were calculated based on experimental results, including supercooling, specific heat of liquid and solid phase, latent heat, heat storage and release time and then they were integrated into the total efficacy coefficient of each eco- composite.
According to the DSC results, the supercooling degree is decreased for the all ECPCM with the lowest supercooling degree by 5.6°C for E50/P50.
IRT observations demonstrated that the ECPCM was successfully retained by its matrix. The thermal storage/release performances of PEG and ECPCMs were investigated by measuring the temperature evolution during the heat charging and discharging process. The addition of shape supporter into the PCM can improved charging/discharging time compared to P100.
These phase change characteristics make the material suitable for use in buildings located in hot and dry climates, where daytime temperatures are typically very high (above 40°C) and drop significantly at night (around 1–10°C). Such weather conditions allow the phase change material to switch between phases, helping to minimize temperature fluctuations inside the building.
Acknowledgements
The author would like to thank the colleagues in the research group for their rich discussion and advice.
Disclosure statement
No potential conflict of interest was reported by the author(s).
Data and code availability
Authors confirm that all relevant data are included in the article. The data that support the findings of this study are available from the corresponding author upon reasonable request.
References
- Tripathi, B.M.; Shukla, S.K.; Rathore, P.K.S. A Comprehensive Review on Solar to Thermal Energy Conversion and Storage Using Phase Change Materials. J. Energy Storage 2023, 72, 108280. doi:10.1016/j.est.2023.108280.
- Rathore, P.K.S.; Gupta, K.K.; Patel, B.; Sharma, R.K.; Gupta, N.K. Beeswax as a Potential Replacement of Paraffin Wax as Shape Stabilized Solar Thermal Energy Storage Material: An Experimental Study. J. Energy Storage 2023, 68, 107714. doi:10.1016/j.est.2023.107714.
- Chavan, S. Thermal Energy Storage Methods and Materials, 2023; pp 39–61. doi:10.1007/978-981-19-4502-1_3.
- Trigui, A.; Abdelmouleh, M. Improving the Heat Transfer of Phase Change Composites for Thermal Energy Storage by Adding Copper: Preparation and Thermal Properties. Sustainability 2023, 15 (3), 1957. doi:10.3390/su15031957.
- Moulahi, C.; Trigui, A.; Karkri, M.; Boudaya, C. Thermal Performance of Latent Heat Storage: Phase Change Material Melting in Horizontal Tube Applied to Lightweight Building Envelopes. Compos. Struct. 2016, 149, 69–78. doi:10.1016/j.compstruct.2016.04.011.
- Gowthami, D.; Sharma, R.K.; Tyagi, V.V.; Rathore, P.K.S.; Sarı, A. Development of a Novel Form-Stable Phase Change Material Based on Alkali Activated Date Seed Biochar to Harvest Solar Thermal Energy. J. Energy Storage 2024, 83, 110699. doi:10.1016/j.est.2024.110699.
- Kim, A.; Wert, N.A.; Gowd, E.B.; Patel, R. Recent Progress in PEG-Based Composite Phase Change Materials. Polym. Rev. 2023, 63 (4), 1078–1129. doi:10.1080/15583724.2023.2220041.
- Soni, J.; Sahiba, N.; Sethiya, A.; Agarwal, S. Polyethylene Glycol: A Promising Approach for Sustainable Organic Synthesis. J. Mol. Liq. 2020, 315, 113766. doi:10.1016/j.molliq.2020.113766.
- Xie, F.; Dai, X.; Zhuo, L.; Dai, Q.; He, C.; Lu, Z. Robust BNNS/ANF Aerogel Skeleton-Based PEG Composite Phase Change Materials with High Latent Heat for Efficient Thermal Management. Compos. Struct. 2023, 323, 117479. doi:10.1016/j.compstruct.2023.117479.
- Singh, P., Sharma, R.K.; Goyal, R.; Hekimoğlu, G.; Sarı, A.; Rathore, P.K.S.; Tyagi, V.V. Development and Characterization a Novel Leakage-Proof Form Stable Composite of Graphitic Carbon Nitride and Fatty Alcohol for Thermal Energy Storage. J. Energy Storage 2022, 55, 105761. doi:10.1016/j.est.2022.105761.
- Xu, C.; Zhang, H.; Fang, G. Review on Thermal Conductivity Improvement of Phase Change Materials with Enhanced Additives for Thermal Energy Storage. J. Energy Storage 2022, 51, 104568. doi:10.1016/j.est.2022.104568.
- Souissi, M.; Trigui, A.; Jedidi, I.; Loukil, M.S.; Abdelmouleh, M. Bio-Based Composite as Phase Change Material Including Spent Coffee Grounds and Beeswax Paraffin. Korean J. Chem. Eng. 2023, 40 (9), 2342–2355. doi:10.1007/s11814-023-1448-5.
- Lu, S.; Jia, Y.; Liang, B.; Wang, R.; Lin, Q.; He, Z. Optimal Design and Thermal Performance Study of a Two-Stage Latent Heat Thermal Energy Storage Technology for Heating Systems. Appl. Therm. Eng. 2023, 232, 121073. doi:10.1016/j.applthermaleng.2023.121073.
- Kenisarin, M.; Mahkamov, K. Solar Energy Storage Using Phase Change Materials⋆. Renew. Sustain. Energy Rev. 2007, 11 (9), 1913–1965. doi:10.1016/j.rser.2006.05.005.
- Yang, T.; Ding, Y.; Li, B.; Athienitis, A.K. A Review of Climate Adaptation of Phase Change Material Incorporated in Building Envelopes for Passive Energy Conservation. Build. Environ. 2023, 244, 110711. doi:10.1016/j.buildenv.2023.110711.
- Simonsen, G.; Ravotti, R.; O’Neill, P.; Stamatiou, A. Biobased Phase Change Materials in Energy Storage and Thermal Management Technologies. Renew. Sustain. Energy Rev. 2023, 184, 113546. doi:10.1016/j.rser.2023.113546.
- Haddad, B.; Mittal, A.; Mittal, J.; Paolone, A.; Villemin, D.; Debdab, M.; Mimanne, G.; Habibi, A.; Hamidi, Z.; Boumediene, M.; Belarbi, E. Synthesis and Characterization of Egg Shell (ES) and Egg Shell with Membrane (ESM) Modified by Ionic Liquids. Chem. Data Collect. 2021, 33, 100717. doi:10.1016/j.cdc.2021.100717.
- Zhou, G.-T.; Yu, J.C.; Wang, X.-C.; Zhang, L.-Z. Sonochemical Synthesis of Aragonite-Type Calcium Carbonate with Different Morphologies. New J. Chem. 2004, 28 (8), 1027. doi:10.1039/b315198k.
- Niju, S.; Sheriffa Begum, K.M.M.; Anantharaman, N. Preparation of Biodiesel from Waste Frying oil Using a Green and Renewable Solid Catalyst Derived from egg Shell. Environ. Prog. Sustain. Energy 2015, 34 (1), 248–254. doi:10.1002/ep.11939.
- Pradhan, A.K.; Sahoo, P.K. Synthesis and Study of Thermal, Mechanical and Biodegradation Properties of Chitosan-g-PMMA with Chicken egg Shell (Nano-CaO) as a Novel bio-Filler. Mater. Sci. Eng. C 2017, 80, 149–155. doi:10.1016/j.msec.2017.04.076.
- Urtekin, G.; Hazer, S.; Aytac, A. Effect of Eggshell and Intumescent Flame Retardant on the Thermal and Mechanical Properties of Plasticised PLA. Plast. Rubber Compos. 2021, 50 (3), 127–136. doi:10.1080/14658011.2020.1844522.
- Tsai, W.T.; Yang, J.M.; Lai, C.W.; Cheng, Y.H.; Lin, C.C.; Yeh, C.W. Characterization and Adsorption Properties of Eggshells and Eggshell Membrane. Bioresour. Technol. 2006, 97 (3), 488–493. doi:10.1016/j.biortech.2005.02.050.
- Wu, S.; Yan, T.; Kuai, Z.; Pan, W. Thermal Conductivity Enhancement on Phase Change Materials for Thermal Energy Storage: A Review. Energy Storage Mater. 2020, 25, 251–295. doi:10.1016/j.ensm.2019.10.010.
- Kong, J.; Li, Y.; Bai, Y.; Li, Z.; Cao, Z.; Yu, Y.; Han, C.; Dong, L. High-performance Biodegradable Polylactide Composites Fabricated Using a Novel Plasticizer and Functionalized Eggshell Powder. Int. J. Biol. Macromol. 2018, 112, 46–53. doi:10.1016/j.ijbiomac.2018.01.153.
- Mustapha, K.; Ayinla, R.; Ottan, A.S.; Owoseni, T.A. Mechanical Properties of Calcium Carbonate/Eggshell Particle Filled Polypropylene Composites. MRS Adv. 2020, 5 (54–55), 2783–2792. doi:10.1557/adv.2020.323.
- Skórczewska, K.; Lewandowski, K.; Szewczykowski, P.; Wilczewski, S.; Szulc, J.; Stopa, P.; Nowakowska, P. Waste Eggshells as a Natural Filler for the Poly(Vinyl Chloride) Composites. Polymers (Basel) 2022, 14 (20), 4372. doi:10.3390/polym14204372.
- Vandeginste, V. Food Waste Eggshell Valorization Through Development of new Composites: A Review. Sustain. Mater. Technol. 2021, 29, e00317. doi:10.1016/j.susmat.2021.e00317.
- McGauran, T.; Dunne, N.; Smyth, B.M.; Cunningham, E. Incorporation of Poultry Eggshell and Litter ash as High Loading Polymer Fillers in Polypropylene. Compos. Part C Open Access 2020, 3, 100080. doi:10.1016/j.jcomc.2020.100080.
- Ramli, N.F.; Ghani, S.A.; Leng, T.P.; Keat, Y.C. Effects of Poly(Vinylchloride)-Maleic Anhydride as Coupling Agent on Mechanical, Water Absorption, and Morphological Properties of Eggshell Powder Filled Recycled High Density Polyethylene/Ethylene Vinyl Acetate Composites. J. Adv. Res. Appl. Sci. Eng. Technol. 2022, 28 (1), 33–43. doi:10.37934/araset.28.1.3343.
- Shaw, W.J. Current Understanding of Mechanically Alloyed Polymers. 1998.
- Jehanno, C.; Alty, J.W.; Roosen, M.; De Meester, S.; Dove, A.P.; Chen, E.Y.-X.; Leibfarth, F.A.; Sardon, H. Critical Advances and Future Opportunities in Upcycling Commodity Polymers. Nature 2022, 603 (7903), 803–814. doi:10.1038/s41586-021-04350-0.
- Chen, J.; Liu, X.; Tian, Y.; Zhu, W.; Yan, C.; Shi, Y.; Kong, L.B.; Qi, H.J.; Zhou, K. 3D-Printed Anisotropic Polymer Materials for Functional Applications. Adv. Mater. 2022, 34 (5). doi:10.1002/adma.202102877.
- Ishida, T. Mechanical Alloying of Polytetrafluoroethylene with Polyethylene. J. Mater. Sci. Lett. 1994, 13 (9), 623–628. doi:10.1007/BF00271215.
- Farrell, M.P.; Kander, R.G.; Aning, A.O. Polymer Blends Formed by Solid-State Mechanical Alloying. J. Mater. Synth. Process. 1996, 4, 151–161.
- Castricum, H.L.; Yang, H.; Bakker, H.; Van Deursen, J.H. A Study of Milling of Pure Polymers and a Structural Transformation of Polyethylene. Mater. Sci. Forum 1997, 235–238, 211–216.
- Gabriel, M.C.; Mendes, L.B.; de Melo Carvalho, B.; Pinheiro, L.A.; Capochi, J.D.T.; Kubaski, E.T.; Cintho, O.M. High-Energy Mechanical Milling of Ultra-High Molecular Weight Polyethylene (UHMWPE). Mater. Sci. Forum 2010, 660–661, 325–328. doi:10.4028/www.scientific.net/MSF.660-661.325.
- Xiong, M.; Wu, L.; Zhou, S.; You, B. Preparation and Characterization of Acrylic Latex/Nano-SiO 2 Composites. Polym. Int. 2002, 51 (8), 693–698. doi:10.1002/pi.968.
- Namboodri, S.L.; Zhou, H.; Aning, A.; Kander, R.G. Formation of Polymer/Ceramic Composite Grain Boundary Capacitors by Mechanical Alloying. Polymer (Guildf) 1994, 35 (19), 4088–4091. doi:10.1016/0032-3861(94)90580-0.
- Cavalieri, F.; Padella, F.; Bourbonneux, S. High-energy Mechanical Alloying of Thermoplastic Polymers in Carbon Dioxide. Polymer (Guildf) 2002, 43 (4), 1155–1161. doi:10.1016/S0032-3861(01)00721-2.
- Manoli, F.; Dalas, E. Spontaneous Precipitation of Calcium Carbonate in the Presence of Ethanol, Isopropanol and Diethylene Glycol. J. Cryst. Growth 2000, 218 (2–4), 359–364. doi:10.1016/S0022-0248(00)00560-1.
- Busca, G.; Resini, C. Vibrational Spectroscopy for the Analysis of Geological and Inorganic Materials. In Encyclopedia of Analytical Chemistry; Wiley, 2000. doi:10.1002/9780470027318.a5612m.
- Wang, C.; Feng, L.; Li, W.; Zheng, J.; Tian, W.; Li, X. Shape-stabilized Phase Change Materials Based on Polyethylene Glycol/Porous Carbon Composite: The Influence of the Pore Structure of the Carbon Materials. Sol. Energy Mater. Sol. Cells 2012, 105, 21–26. doi:10.1016/j.solmat.2012.05.031.
- Molina-Boisseau, S.; Le Bolay, N. Characterisation of the Physicochemical Properties of Polymers Ground in a Vibrated Bead Mill. Powder Technol. 2002, 128 (2–3), 99–106. doi:10.1016/S0032-5910(02)00180-8.
- Moore, D.M.; Reynolds Jr., R.C. X-ray Diffraction and the Identification and Analysis of Clay Minerals, Oxford University Press: Oxford, 1989; pp 179–201.
- Mardiana, L.; Ardiansah, B.; Bakri, R.; Cahyana, A. H.; Anita, Y.; Aziza, N. P. Utilization of Eggshell-Derived Material as a Solid Base Catalyst for Efficient Synthesis of Substituted Chalcones. J. Teknol. 2017, 79 (5). doi:10.11113/jt.v79.10220.
- Baláž, M. Ball Milling of Eggshell Waste as a Green and Sustainable Approach: A Review. Adv. Colloid Interface Sci. 2018, 256, 256–275. doi:10.1016/j.cis.2018.04.001.
- Trigui, A.; Aribia, W.B.; Akrouti, A.; Znaidia, S.; AlShammari, N.K.; Abdelmouleh, M. Latent heat storage bio-composites from egg-shell/PE/PEG as feasible eco-friendly building materials. Polym. Compos. May 2024. doi: 10.1002/pc.28575.
- Trong On, D.; Kapoor, M.P.; Thibault, E.; Gallot, J.E.; Lemay, G.; Kaliaguine, S. Influence of High-Energy Ball Milling on the Physico-Chemical and Catalytic Properties of Titanium Silicalite TS-1. Microporous Mesoporous Mater. 1998, 20 (1–3), 107–118. doi:10.1016/S1387-1811(97)00002-4.
- Nye, J.F. Physical Properties of Crystals, Oxford University Press: New York, 1985.
- Šimáková, P.; Gautier, J.; Procházka, M.; Hervé-Aubert, K.; Chourpa, I. Polyethylene-Glycol-Stabilized Ag Nanoparticles for Surface-Enhanced Raman Scattering Spectroscopy: Ag Surface Accessibility Studied Using Metalation of Free-Base Porphyrins. J. Phys. Chem. C 2014, 118 (14), 7690–7697. doi:10.1021/jp5005709.
- Shkilnyy, A.; Soucé, M.; Dubois, P.; Warmont, F.; Saboungi, M.-L.; Chourpa, I. Poly(Ethylene Glycol)-Stabilized Silver Nanoparticles for Bioanalytical Applications of SERS Spectroscopy. Analyst 2009, 134 (9), 1868. doi:10.1039/b905694g.
- Jayaramudu, T.; Raghavendra, G.M.; Varaprasad, K.; Reddy, G.V.S.; Reddy, A.B.; Sudhakar, K.; Sadiku, E.R. Preparation and Characterization of Poly(Ethylene Glycol) Stabilized Nano Silver Particles by a Mechanochemical Assisted Ball Mill Process. J. Appl. Polym. Sci. 2016, 133 (7). doi:10.1002/app.43027.
- Mosaddegh, E. Ultrasonic-assisted Preparation of Nano Eggshell Powder: A Novel Catalyst in Green and High Efficient Synthesis of 2-Aminochromenes. Ultrason. Sonochem. 2013, 20 (6), 1436–1441. doi:10.1016/j.ultsonch.2013.04.008.
- Huang, N.; Wang, J. A TGA-FTIR Study on the Effect of CaCO3 on the Thermal Degradation of EBA Copolymer. J. Anal. Appl. Pyrolysis 2009, 84 (2), 124–130. doi:10.1016/j.jaap.2009.01.001.
- Isitman, N.A.; Dogan, M.; Bayramli, E.; Kaynak, C. Fire Retardant Properties of Intumescent Polypropylene Composites Filled with Calcium Carbonate. Polym. Eng. Sci. 2011, 51 (5), 875–883. doi:10.1002/pen.21901.
- Dhumal, P.S.; Bhakare, M.A.; Lokhande, K.D.; Bondarde, M.P.; Some, S. Bio-waste Derived, Phosphorus Decorated Composite for Highly Efficient Flame Retardant for Cotton Fabric. Cellulose 2022, 29 (16), 8879–8888. doi:10.1007/s10570-022-04783-4.
- Trigui, A.; Abdelmouleh, M.; Boudaya, C. Performance Enhancement of a Thermal Energy Storage System Using Shape-Stabilized LDPE/Hexadecane/SEBS Composite PCMs by Copper Oxide Addition. RSC Adv. 2022, 12 (34), 21990–22003. doi:10.1039/D2RA02437C.
- Righetti, G.; Doretti, L.; Zilio, C.; Longo, G.A.; Mancin, S. Experimental Investigation of Phase Change of Medium/High Temperature Paraffin wax Embedded in 3D Periodic Structure. Int. J. Thermofluids 2020, 5-6, 100035. doi:10.1016/j.ijft.2020.100035.
- Chriaa, I.; Karkri, M.; Trigui, A.; Boudaya, C.; Jedidi, I.; Abdelmouleh, M. Preparation and Thermal Properties of Form Stable LDPE/ Hexadecane/ SEBS Composite for Thermal Energy Storage. International Alliance for Sustainable Urbanization and Regeneration (IASUR), 2end International Conference « Green Building and Smart City », Xian, China, Mar, 2019. ⟨hal-04326423⟩.
- Yang, H.; Wang, Y.; Liu, Z.; Liang, D.; Liu, F.; Zhang, W.; Di, X.; Wang, C.; Ho, S.-H.; Chen, W.-H. Enhanced Thermal Conductivity of Waste Sawdust-Based Composite Phase Change Materials with Expanded Graphite for Thermal Energy Storage. Bioresour. Bioprocess. 2017, 4 (1), 52. doi:10.1186/s40643-017-0182-4.
- Feng, L.; Zhao, W.; Zheng, J.; Frisco, S.; Song, P.; Li, X. The Shape-Stabilized Phase Change Materials Composed of Polyethylene Glycol and Various Mesoporous Matrices (AC, SBA-15 and MCM-41). Sol. Energy Mater. Sol. Cells 2011, 95 (12), 3550–3556. doi:10.1016/j.solmat.2011.08.020.
- Qian, T.; Li, J.; Min, X.; Deng, Y.; Guan, W.; Ma, H. Polyethylene Glycol/Mesoporous Calcium Silicate Shape-Stabilized Composite Phase Change Material: Preparation, Characterization, and Adjustable Thermal Property. Energy 2015, 82, 333–340. doi:10.1016/j.energy.2015.01.043.
- Qian, T.; Li, J.; Min, X.; Guan, W.; Deng, Y.; Ning, L. Enhanced Thermal Conductivity of PEG/Diatomite Shape-Stabilized Phase Change Materials with Ag Nanoparticles for Thermal Energy Storage. J. Mater. Chem. A 2015, 3 (16), 8526–8536. doi:10.1039/C5TA00309A.
- Trigui, A. Techniques for the Thermal Analysis of PCM. In Phase Change Materials - Technology and Applications; IntechOpen, 2022. doi:10.5772/intechopen.105935.
- Trigui, A.; Karkri, M. Latent Heat Storage Using Composite Phase Change Material: Thermophysical Characterization with Heat Flux Sensors. 2014 5th International Renewable Energy Congress (IREC), Mar, 2014; IEEE; pp 1–5. doi:10.1109/IREC.2014.6826924.
- Trigui, A.; Karkri, M.; Krupa, I. Thermal Conductivity and Latent Heat Thermal Energy Storage Properties of LDPE/wax as a Shape-Stabilized Composite Phase Change Material. Energy Convers. Manag. 2014, 77, 586–596. doi:10.1016/j.enconman.2013.09.034.
- Trigui, A.; Karkri, M.; Boudaya, C.; Candau, Y.; Ibos, L.; Fois, M. Experimental Investigation of a Composite Phase Change Material: Thermal-Energy Storage and Release. J. Compos. Mater. 2014, 48 (1), 49–62. doi:10.1177/0021998312468185.
- Moulahi, C.; Trigui, A.; Boudaya, C.; Karkri, M. Smart Macroencapsulated Resin/wax Composite for Energy Conservation in the Built Environment. J. Thermoplast. Compos. Mater. 2017, 30 (7), 887–914. doi:10.1177/0892705715614065.
- Sundararajan, S.; Samui, A.B.; Kulkarni, P.S. Shape-stabilized Poly(Ethylene Glycol) (PEG)-Cellulose Acetate Blend Preparation with Superior PEG Loading via Microwave-Assisted Blending. Sol. Energy 2017, 144, 32–39. doi:10.1016/j.solener.2016.12.056.
- Yazdani, M.R.; Ajdary, R.; Kankkunen, A.; Rojas, O.J.; Seppälä, A. Cellulose Nanofibrils Endow Phase-Change Polyethylene Glycol with Form Control and Solid-to-gel Transition for Thermal Energy Storage. ACS Appl. Mater. Interfaces 2021, 13 (5), 6188–6200. doi:10.1021/acsami.0c18623.
- Liu, L.; Fan, X.; Zhang, Y.; Zhang, S.; Wang, W.; Jin, X.; Tang B. Novel Bio-Based Phase Change Materials with High Enthalpy for Thermal Energy Storage. Appl. Energy 2020, 268, 114979. doi:10.1016/j.apenergy.2020.114979.
- Zahir, M.H.; Rahman, M.M.; Irshad, K.; Rahman, M.M. Shape-Stabilized Phase Change Materials for Solar Energy Storage: MgO and Mg(OH)2 Mixed with Polyethylene Glycol. Nanomaterials 2019, 9 (12), 1773. doi:10.3390/nano9121773.
- Khoddami, A.; Avinc, O.; Ghahremanzadeh, F. Improvement in Poly(Lactic Acid) Fabric Performance via Hydrophilic Coating. Prog. Org. Coatings 2011, 72 (3), 299–304. doi:10.1016/j.porgcoat.2011.04.020.
- Şentürk, S.B.; Kahraman, D.; Alkan, C.; Gökçe, İ. Biodegradable PEG/Cellulose, PEG/Agarose and PEG/Chitosan Blends as Shape Stabilized Phase Change Materials for Latent Heat Energy Storage. Carbohydr. Polym. 2011, 84 (1), 141–144. doi:10.1016/j.carbpol.2010.11.015.
- Wang, W.; Yang, X.; Fang, Y.; Ding, J. Preparation and Performance of Form-Stable Polyethylene Glycol/Silicon Dioxide Composites as Solid–Liquid Phase Change Materials. Appl. Energy 2009, 86 (2), 170–174. doi:10.1016/j.apenergy.2007.12.003.
- Zhang, X.; Huang, Z.; Ma, B.; Wen, R.; Zhang, M.; Huang, Y.; Fang, M.; Liu, Y.-G.; Wu, X. Polyethylene Glycol/Cu/SiO2 Form Stable Composite Phase Change Materials: Preparation, Characterization, and Thermal Conductivity Enhancement. RSC Adv. 2016, 6 (63), 58740–58748. doi:10.1039/C6RA12890D.