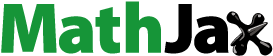
Abstract
To study the effects of coal dust particle size and mass of coal dust on gas-coal dust hybrid explosions, we conducted sedimentary gas-coal dust explosion experiments using a pipe network system that included multiple components and individual interactions, which were independently designed and constructed. Experimental conclusions were then theoretically verified based on factor response surface theory. The results demonstrated that when the particle size of coal dust was constant, the pressure peak, flame front velocity peak, and flame front temperature peak of the explosion initially increased and then decreased with increasing mass. When the mass of coal dust was constant, the pressure peak, flame front velocity peak, and flame front temperature peak of the explosion also initially increased and then decreased with increasing particle size. The mass and particle size values of the coal dust were 25 g and 48–52 μm, respectively, and under these conditions, the explosion was the most violent. The effects of mass on the pressure peak and flame front temperature peak were greater than the particle size of the coal dust, and the effect of particle size on the flame front velocity was greater than the mass of the coal dust.
1. Introduction
Gas-coal dust mixture has a higher potential for reaching the detonation stage than other fuels, which endangers the safety of underground personnel (Sanchirico et al. Citation2014, Citation2015, Citation2020). When coal dust is present, the gas explosion power becomes significantly more volatile, and when suspended coal dust is heated, a large amount of combustible gas will become volatilized and attach to the coal dust. As the gas reaches a certain concentration and absorbs significant amounts of heat, a chain reaction will occur. The heat released by oxidation will cause particle flashover, and at a certain point, the explosion power will increase (Gieras et al. Citation2015; Pinaev et al. Citation2015; Sanchirico et al. Citation2018; Niu et al. Citation2021). In pipeline gas explosions, the explosion intensity will increase significantly after mixing with coal dust. In addition, the distance between the pressure peak of the hybrid explosion and the explosion source will be greater than the pressure peak of the gas explosion. Thus, the larger the proportion of large coal dust particles in the hybrid coal dust, the smaller the peak pressure of the explosion. At a low gas concentration, the type of coal dust and the particle size of coal dust will have more of an effect on the lower limit of the gas-coal dust mixture explosion (Wang Citation2017; Wang, Gou et al. Citation2019; Jing et al. Citation2021; Lin et al. Citation2022). However, coal dust affects gas explosions slightly less than hybrid gas-coal dust explosions in spherical explosive tanks (Kundu et al. Citation2018; Qi et al. Citation2021).
Representative studies on methane-coal dust hybrid explosions have mainly used straight pipes and spherical explosion-proof tanks. Guo et al. (Citation2020) carried out low-concentration gas-coal dust hybrid explosion experiments in a long straight pipeline, and the results indicated that the addition of low-concentration coal dust increased the gas explosion pressure and explosion flame propagation speed. The volatility and gas content of the coal dust had a great influence on the explosion intensity. After the addition of pulverized coal, and under the action of a reflected shock wave, the speed of the explosion flame reached the detonation level. Jing et al. (Citation2020) studied the duration of the explosion flame in a straight transparent tube, which was produced by the coupling explosion of coal dust and gas at different concentrations. The results showed that when the concentration of coal dust was 25–200 g/m3, the time required for complete development of the flame front of the gas-coal dust coupled explosion was 50%–78.3% of the time required for the complete development of the flame front in the single-phase gas explosion. When coal dust was added, the time required for the gas-coal dust coupled explosion flame to propagate from the ignition position to the pipe outlet was significantly shortened. The addition of coal dust also greatly stimulated the development of the explosion flame in the propagation tube, the flame front speed increased to different degrees, and the increase rate reached 314.3%. Zhang et al. (Citation2021) concluded that gas explosions can rapidly cause the explosion of deposited dust. After the explosion, the peak overpressure of the shock wave increased sharply, and then decreased slowly at the corner, and the overpressure decay rate increased with an increase in bending angle of the pipeline. The flame front velocity decreased at the corners and then increased significantly. Furthermore, the rate of change of the flame front velocity was positively related to the bending angle of the pipe, and the growth rate of the flame front area was positively related to the bending angle of the pipe. Jing et al. (Citation2019) experimentally studied hybrid explosions using an experimental gas with a concentration of 9%, as well as different coal dust mass fractions and particle sizes, and obtained time-dependent pressure results for the explosion chamber and pipeline, including change rules for the pressure change rate and distance. Li et al. (Citation2020) used a 20 L spherical explosion tank to study the effects of injection pressure and ignition delay time on the explosion parameters of a methane-coal mixture. The results indicated that the instantaneous movement of the coal particles could be categorized into four continuous stages. At different injection pressures, the particle dispersion and stabilization times were significantly different, and these results could help prevent methane-coal particle explosions. Niu et al. (Citation2020) established an experimental methane-pulverized coal hybrid explosion system, and the overpressure evolution and flame propagation of the coal dust with different moisture content in the gas explosion were studied in a straight pipe. The results demonstrated that the explosion risk of coal dust with water content less than 15.12% significantly increased. When the moisture content of the deposited coal dust was 9.57%, the overpressure and flame velocity of the deposited coal dust explosion reached their peak. However, when the moisture content exceeded 20.28%, the coal dust did not explode, and at this point the deposited coal dust exhibited a suppression effect on the gas explosion.
Previously conducted studies on gas-coal dust hybrid explosions have focused on long straight pipes and spherical explosion tanks; however, the effects of mass of coal dust and particle size on hybrid gas-coal dust explosions have not been thoroughly investigated for pipe networks. Mine roadway systems are typically composed of multiple roadways, which are connected with each other, while the gas coal dust explosion characteristics in a straight pipe or explosion tank are not of universal significance, and the conclusion is not close to the explosion disaster in the actual roadway. Therefore, it is necessary to study the effects of coal dust parameters on hybrid gas-coal dust explosions in pipe networks containing multiple and interconnected components, to obtain a more universal law and provide a theoretical basis for preventing underground disasters.
2. Experimental platform
2.1. Experimental system
The experimental system () was composed of a pipe network and an explosion chamber. The pipes in the pipe network were connected with screws, the outlets of the pipe networks were closed with flanges, and threaded holes were used to install sensors on the pipes. Sealing gaskets were installed at each pipe joint, to ensure that the equipment was properly sealed. Polytetrafluoroethylene film was also used to separate the explosion chamber from the pipes. After the explosion chamber was vacuumed, the experimental gas with a volume fraction of 9.5% was passed through the chamber, the coal dust samples used in the experiment were evenly laid in the pipeline, and atmospheric air was piped into the pipe. The ignition device is controlled by computer, and the explosion experiment is carried out after 3 s of ignition delay.
The ignition system mainly included a DX-GDH high-energy igniter, high-energy sparkplugs, high-voltage-resistant and high-temperature-resistant cables, power supply cables, and external trigger devices. The ignition control box was connected with an external trigger wire. The sparkplugs were placed at the front end of the explosion chamber, the ignition voltage was about 2200 V, and the one-time energy storage was 30 J. A TST6300 data acquisition system was used to collect the data in real time, which mainly consisted of a CYG1721 high precision pressure sensor, NANMAC-E6 series fast-response thermocouple with an aggressive probe, and a CKG100 photosensitive flame sensor. Assuming that the distance between two flame sensors was L, the flame front passed through the two adjacent sensors at different moments t1 and t2, and these values were recorded. Then, the flame front velocity was calculated by the following formula:
(1)
(1)
The positions of coal dust, branches, and measuring points in the experimental pipe network are shown in . The far left-hand side of the gas explosion chamber contained the axis, where the horizontal direction was the X-axis, and the vertical direction was the Y-axis. The positions for each measured point were given as M1, M2, M3, M4, M5, M6, M7, M8 and M9 in sequence. The equivalent distance parameters between each measurement point and the explosion cavity are listed in . Two transmission paths were present in the pipe network, starting from point O, where the first was O-A-C-D and the second was O-A-B-D. Coal dust was then placed at point O in the experiment, as shown in . Before the experiment, the gas concentration was set to 9.5%, and the mass of the coal dust were 15 g, 25 g and 35 g (Jing et al. Citation2019, Citation2020), with particle sizes of 22–26 μm, 48–52 μm and 72–76 μm (Tan et al. Citation2020; Zhou et al. Citation2022). All coal dust samples were dried in an incubator at 50 °C for more than 12 hours to remove moisture from the samples.
Table 1. Equivalent coordinate values at each measurement point.
2.2. Physical and chemical characteristics of the coal samples
Research has shown that coking coal has the most violent combustion and explosion reaction among the different types of coal dust. Therefore, coking coal with an explosion index of 30.69% in the Buertai Coal Mine was selected as the experimental coal sample.
It is generally believed that when the coal dust explosion index is greater than 15%, coal dust will present an explosion risk (Cao et al. Citation2017). The coal dust samples were scanned with an electron microscope and analyzed by the industry, and the results are shown in and . Three magnification factors were selected, which were 2000, 5000 and 10,000 times.
Table 2. Industrial analysis results of the coal block samples.
As shown in , the particle size distribution of the coking coal sample could be clearly observed, and the particles were all irregular in shape, inhomogeneous in size, and irregular in distribution. At 10,000 times magnification, we found that the surface of the coal sample was relatively flat and the layers were uneven. In addition, the sheet structure was clear and the pore structure was not damaged; thus, it could be used as the experimental sample.
The particle size distribution of coal dust used in the experiment is shown in . As shown in , more than 90% of the coal dust particle sizes met the experimental requirements in the three coal dust samples. Therefore, the coal dust samples used in this experiment met the explosion conditions.
3. Analysis of the experimental gas-coal dust pipe network explosion results
3.1. Effect of mass of coal dust on the hybrid gas-coal dust explosion
3.1.1. Effect on shock wave pressure
According to the data presented in , the pressure peaks of the explosions varied with different mass when coal dust with different particle sizes was ignited and exploded.
As presented in , the pressure peaks increased and then decreased with increasing mass of coal dust. When the mass of the coal dust in the pipe was low, the concentration of the coal dust cloud that formed due to deposition from the explosion shock wave was low, resulting in a surplus of oxygen in the pipe, which was in an oxygen-rich state, causing the coal dust cloud to completely undergo combustion and explode (Mohammed et al. Citation2017b). As the mass of coal dust increased, the concentration of the coal dust cloud increased, and the reaction with oxygen intensified; therefore, this released more heat, which caused the pressure peak to increase. When the mass reached 25 g, the coal dust cloud in the pipe completely reacted with oxygen, and at this point, most of the heat was released and the explosion pressure was the highest, as the mass of coal dust continued to increase. Because the oxygen content in the pipe network remained constant, the pipe network was oxygen-poor, due to the continuous increase in coal dust concentration. Therefore, the energy released by the reaction did not continue to increase. The unburned coal dust would then absorb the heat generated by the explosion, thereby suppressing the shock wave, and resulting in a continuous decline in peak pressure (Zhang et al., Citation2021).
3.1.2. Effect on flame front velocity
As shown in and , as the distance from the explosion source gradually increased, the flame front velocity of the explosion flame front gradually decreased. The deposited coal dust was raised by the shock wave of the gas explosion, forming a coal dust cloud in the pipe. This subsequently ignited after absorbing a significant amount of heat, resulting in another explosion. Therefore, the flame front velocity was the highest closest to the explosion source, and the mass of coal dust in the pipe and the flame front velocity were both different. When the mass of coal dust in the pipe was 25 g, the flame front velocity reached its maximum value (Mohammed et al. Citation2017a). In addition, the coal dust completely reacted with the oxygen in the pipe. When the mass of the coal dust continued to increase, due to a certain amount of oxygen contained in the pipe, some of the coal dust did not participate in the reaction and some of the heat was absorbed, causing the peak flame front velocity in the pipe to decrease (Mohammed et al. Citation2017b). When the mass of coal dust reached 35 g, the flame front velocity significantly decreased, indicating that when the mass of coal dust exceeded the maximum limit value, the coal dust had a certain inhibitory effect on the explosion.
3.1.3. Effect on the flame front temperature
shows the temperature peak of the flame front generated by the explosion, as a function of the three different mass of coal dust. As shown in , at different mass of coal dust, the temperature variations at each measurement point were identical, and the maximum temperature was measured at M1. When the mass of coal dust was 15 g, the temperature peak of the flame was between the temperature peak of the flame when the concentration of coal dust was 25 g and the temperature peak of the flame when the concentration was 35 g. With increasing mass of coal dust, there was sufficient oxygen content in the pipe for the coal dust to participate in the explosion reaction; thus, the reaction temperature continued to increase (Kundu et al. Citation2017).
When the mass of coal dust was 25 g, the coal dust reacted completely, the maximum amount of heat was released, and the temperature peak of the flame front in the pipe reached its highest point. When the mass of coal dust increased to 35 g, there was an insufficient amount of oxygen in the pipe to react with all of the coal dust. As a result, the unreacted coal dust continued to absorb some of the heat, and the temperature peak of the flame front began to decrease when the temperature peak of the flame front in the pipe dropped to its minimum value, which was 17.1% lower than the flame front temperature when the mass of the coal dust was 100 g/m3. This indicated that when the mass of coal dust was 25 g, the explosion risk was the highest under the actual working conditions (Wang, Shi et al. Citation2019).
3.2. Effect of particle size of coal dust on hybrid gas-coal dust explosions
3.2.1. Effect on shock wave pressure
shows the changes in pressure peak as a function of particle size. As shown in , we found that as the particle size of coal dust increased, the pressure peak initially increased and then decreased. Considering the theory of coal dust explosions, when coal dust participates in a hybrid explosion, the smaller the particle size of coal dust, the lower the ignition energy, and the more likely a combustion explosion will occur (Si et al. Citation2018). However, in the hybrid gas-coal dust explosion experiment, we determined that the generated peak pressure was greater when the particle size of coal dust was 48–52 μm, compared to 22–26 μm. We found that when coal dust was deposited in the form of a coal dust cloud, large numbers of positive and negative charges accumulated on the surface of the coal seam, due to the irregular shape of the coal dust surface, resulting in aggregation of the coal seam particles (Kundu et al. Citation2017; Mohammed et al. Citation2017a). In addition, the moisture, electrical charges, and van der Waals forces on the coal dust surface interacted with one another. Therefore, the smaller the particle size of the coal dust, the larger the specific surface area, and the greater the surface energies between the coal dust. As a result, dissimilar coal dust was more likely to accumulate, and when the shock wave increased and deposited the coal dust, it was affected by factors such as the friction of the inner wall of the pipe. Thus, the coal dust propagated in the form of turbulence, and the deposition and propagation rates of the coal dust clouds at different locations differed, which affect the pressure value of the explosion (Gan et al. Citation2019).
3.2.2. Effect on flame front velocity
As shown in and , the flame front velocity of the hybrid explosion exhibited a gradual decrease as the propagation distance increased during the propagation of the flame front in the pipe. In addition, with increasing particle size of coal dust, the flame front velocity initially increased and then decreased. The flame front velocity in the pipe was greater when the mass of coal dust in the pipe was 25 g, compared to the other two mass of the coal dust. The fastest flame front velocity in the pipe was 501.53 m/s when the mass of coal dust was 25 g and the particle size of coal dust was 22–26 μm. As the particle size of coal dust increased, the flame front velocity also increased. Thus, when the particle size of coal dust increased to 48–52 μm, the peak flame front velocity reached 539.13 m/s. At this point, the coal dust completely reacted, and its explosion was 7.6% greater compared to coal dust with a particle size of 22–26 μm. When the particle size of the coal dust increased to 72–76 μm, the flame front with the fastest velocity began to slow. This was attributed to the smaller particle size of the coal dust, as its specific surface area was larger, allowing it to absorb heat faster and cause an explosive reaction. When the particle size of the coal dust exceeded the optimal reaction particle size, the specific surface area of the coal dust became smaller. In addition, the heat exchange rate between the interior and exterior of the coal dust decreased, resulting in a lower rate of combustion heat release. Therefore, the velocity of the flame front generated by the hybrid explosion in the pipe decreased (Cloney et al. Citation2018).
3.2.3. Effect on flame front temperature
shows the peak temperature of the flame front with different coal dust particle sizes. The temperature variations for each measurement point were the same for different coal dust particle sizes, and the maximum temperature in the pipe was measured at measurement point M1. When coal dust with three different particle sizes was hybrid and exploded, we found that the peak temperature in the pipe was the lowest when the particle size was 22–26 μm. As the size of the coal dust increased, the peak temperature in the pipe also increased. When the particle size of the coal dust was smaller, the coal dust surface attracted more positive and negative charges, which were affected by van der Waals forces. As the particle size of coal dust increased, the effects of these factors became weaker, which transferred energy to the exterior faster, causing a combustion explosion reaction, and as a result, the flame front temperature increased. When the particle size of coal dust exceeded the optimal size of 48–52 μm (i.e. the particle size of coal dust increased to 72–76 μm), the temperature of the explosion decreased. This occurred because with increasing size of the coal dust particles, the specific surface area of the coal dust decreased, and the efficiency of heat exchange with the exterior decreased. Therefore, the explosion effect became weaker, and flame front temperature decreased (Cloney et al. Citation2019).
4. Theoretical verification
Applying statistical analysis methods in the research to verify the experimental results can test the experimental data from the other side to ensure that the experimental data meet the accuracy requirements. Meanwhile, the statistical analysis method can effectively eliminate the inevitable measurement and statistical errors in the experimental process and ensure the scientificity of the experimental results.
Multiple quadratic regression equations have been adapted to fit the quantitative relationship between the factors and the response values, as expressed by the following model (Mishra and Azam Citation2018):
(2)
(2)
where
is the response function of
and ε is a random error value. If ε is independent of the other variables in the different experiments, then the mean will be 0, and the variance will be
When the test conditions were far from the optimal value of the surface, a first-order model can be used for approximating according to:
(3)
(3)
where
is the slope of the coded variable
When the test area is close to the optimal range of the value, a two-level model is used:
(4)
(4)
where
is a linear function of xi,
is the interaction function between xi and xj, and
is the quadratic function of xi.
The deviation was estimated from the observed values, or its repeated value relative to the mean, and the square of the deviation was calculated according to:
(5)
(5)
In the sum of squares of experimental results and deviations, we divided each constituent term by its corresponding degrees of freedom to obtain the sum of squares of the mean deviations (MS). The calculation method for the sum of squares is shown in and is presented as follows:
(6)
(6)
where SStot is the sum of the squares for the total variance, SSreg is the sum of squares for the fitting variance, and SSres is the sum of the squares for the residuals, according to:
(7)
(7)
where SSpe is the sum of the squares for the pure error, and SSlof is the sum of squares for the misfit errors.
Table 3. Calculated variance relationships in the multiple regression model.
After solving the mean square sum, the statistical significance for the established model was tested by the Fisher distribution (Li et al. Citation2016). The F value was calculated from Formula (8), and then compared with the corresponding standard value:
(8)
(8)
If the calculated value was greater than the value, it indicated that the model was significant, and the constructed model best fit the experimental data. The corresponding mass and particle size of coal dust of A and B were selected as independent variables to analyze the effect of each factor on the explosion effect. As shown in , p represented the model regression coefficients, n was the total number of samples, and m was the number of levels of independent variables.
An equation for the quadratic multiple regression model between the response factor pressure P (KPa) and independent variable factors A and B was also obtained through regression analysis:
(9)
(9)
According to the calculations in , the probability of model ‘Prob > F’ was less than 0.0001, indicating that the model selected in this experiment was extremely significant. The missing item was 0.0531, and the result was greater than 0.05, indicating that the experimental analysis was reasonable and reliable using this method. Furthermore, the fitting degree for the model could be tested by the correlation coefficient. The complex correlation coefficient for this model was R2 = 95.19%, indicating that the model exhibited a good fit. Therefore, the effect of mass on pressure was greater than the effect of particle size of coal dust.
The quadratic multiple regression model equation between the response factor flame front velocity V and the independent variable factors A and B were obtained:
(10)
(10)
The probability of the model ‘Prob > F’ was less than 0.0001, indicating that the model used in this study was extremely significant, and the lack of fit 0.426 > 0.05 indicated that the method was reasonable and reliable. The correlation coefficient was used to test the degree of fit, and the multiple correlation coefficient was R2 = 92.9%, indicating that the model fit well. Thus, the effect of particle size of coal dust on velocity was greater than the mass of coal dust.
A quadratic multiple regression model equation between the response factor flame front temperature T and the independent variable factors A and B, was also obtained:
(11)
(11)
According to the calculation, the probability of model ‘Prob > F’ was 0.0009, indicating that the model selected in this experiment was significant, and the missing item followed 0.983 > 0.05, indicating that the experimental results obtained using method were reasonable and reliable, and the complex correlation coefficient was R2 = 93.09%, indicating the model exhibited a good degree of fit. Therefore, the effect of mass of coal dust on temperature value was stronger than the particle size of the coal dust.
In conclusion, the effect of mass of coal dust on the pressure value of the shock wave generated by the explosion in the pipe network was greater than the particle size. For the flame front velocity, the effect of particle size of coal dust was greater than the mass of coal dust. In addition, the effect of mass of coal dust on the flame front temperature was stronger than the particle size of coal dust.
5. Conclusions
In this work, we studied the effect of particle size and mass of coking coal dust on gas-coal dust explosions in pipe networks and obtained the following conclusions.
The peak values for the gas-coal dust explosion pressure, flame front velocity, and flame front temperature all initially increased and then decreased with increasing mass of coal dust. When the particle size of coal dust was the same, the explosion effect of coal dust with mass of 25g is the strongest, followed by 15g and 35g.
With increasing particle size of coal dust, the pressure peak value, flame front velocity value, and the flame front temperature value produced by the hybrid explosion also initially increased and then decreased. When the mass was the same, the coal dust particle size corresponding to the strongest explosion effect of pressure peak and flame front temperature is 48–52 μm, followed by 72–76 μm and 22–26 μm, and the coal dust particle size corresponding to the strongest explosion effect of the flame front velocity is 48–52 μm, followed by 22–26 μm and 72–76 μm.
For the shock wave pressure value, the effect of mass of coal dust was greater than the particle size. For the flame front velocity, the effect of particle size of coal dust was greater than the mass of coal dust. Lastly, the effect of the mass of coal dust on the flame front temperature was stronger than the particle size of coal dust. In addition, there was no obvious correlation between the mass of coal dust and particle size of coal dust.
The results in this study provide a generalized theoretical basis for the effects of coal dust on hybrid gas-coal dust explosions. And the experimental system should be further enriched and improved to be closer to the actual working conditions, so as to obtain more informative conclusions in the next research.
Disclosure statement
No potential conflict of interest was reported by the authors
Data availability statement
The data and materials that support the results or analyses presented in our study are freely available.
Additional information
Funding
References
- Cao W, Qin Q, Cao W, Lan Y, Chen T, Xu S, Cao X. 2017. Experimental and numerical studies on the explosion severities of coal dust/air mixtures in a 20-L spherical vessel. Powder Technol. 310(01):17–23.
- Cloney CT, Ripley RC, Pegg MJ, Khan F, Amyotte PR. 2018. Lower flammability limits of hybrid mixtures containing 10 micron coal dust particles and methane gas. Process Saf Environ Prot. 120:215–226.
- Cloney CT, Ripley RC, Pegg MJ, Khan FI, Amyotte PR. 2019. Role of particle diameter in the lower flammability limits of hybrid mixtures containing coal dust and methane gas. J Loss Prev Process Ind. 61:206–212.
- Gan B, Gao W, Zhang X, et al. 2019. Flame temperature characteristics of PMMA dust clouds with different particle sizes. Explos Shock Waves. 39(01):140–147.
- Gieras M, Klemens R, Rarata G. 2015. Determination of explosion parameters of methane-air mixtures in the chamber of 40dm3, at normal and elevated temperature. J Loss Prev Process Ind. 15(03):263–270.
- Guo C, Shao H, Jiang S, Wang Y, Wang K, Wu Z. 2020. Effect of low-concentration coal dust on gas explosion propagation law. Powder Technol. 367(01):243–252.
- Jing G, Guo S, Wu Y, Wang Y. 2020. Study on the influence of coal dust concentration on flame propagation characteristics of gas explosion in semi-closed tube. Energy Sour Part A. 1–15.
- Jing G, Guo S, Wu Y. 2021. Investigation on the characteristics of single-phase gas explosion and gas-coal dust coupling explosion in bifurcated tubes. Therm Sci. 25(5 Part A):3595–3605.
- Jing G, Liu C, Duan X. 2019. Experimental study on coupled gas and coal dust explosion in semi-closed pipeline. J China Coal Soci. 44(S1):157–163.
- Kundu SK, Zanganeh J, Eschebach D, Badat Y, Moghtaderi B. 2018. Confined explosion of methane-air mixtures under turbulence. Fuel. 220(01):471–480.
- Kundu SK, Zanganeh J, Eschebach D, Mahinpey N, Moghtaderi B. 2017. Explosion characteristics of methane–air mixtures in a spherical vessel connected with a duct. Process Saf Environ Prot. 3(01):85–93.
- Li D, Feng G, Guo Y, et al. 2016. Analysis on the strength increase law of filling material based on response surface method. J China Coal Soci. 41(02):392–398.
- Li H, Deng J, Chen X, Shu C-M, Kuo C-H, Hu X. 2020. Influence of ignition delay on explosion severities of the methane–coal particle hybrid mixture at elevated injection pressures. Powder Technol. 367(01):860–876.
- Lin S, Liu Z, Wang Z, Qian J, Gu Z. 2022. Flame characteristics in a coal dust explosion induced by a methane explosion in a horizontal pipeline. Combust Sci Technol. 194(3):622–635.
- Mishra D, Azam S. 2018. Experimental investigation on effects of particle size, dust concentration and dust-dispersion-air pressure on minimum ignition temperature and combustion process of coal dust clouds in a G-G furnace. Fuel. 227(01):424–433.
- Mohammed J, Jafar Z, Behdad M. 2017a. The flame deflagration of hybrid methane coal dusts in a large-scale detonation tube (LSDT). Fuel. 194(01):491–502.
- Mohammed J, Jafar Z, Behdad M. 2017b. The influences of the initial ignition energy on methane explosion in a flame deflagration tube. Energy Fuels. 31(6):6422–6434.
- Niu Y, Zhang L, Shi B, Yang Q, Zhong Z. 2021. Methane–coal dust mixed explosion in transversal pipe networks. Combust Sci Technol. 193(10):1734–1746.
- Niu Y, Zhang L, Shi B. 2020. Experimental study on the explosion-propagation law of coal dust with different moisture contents induced by methane explosion. Powder Technol. 361:507–511.
- Pinaev AV, Vasil’ev AA, Pinaev PA. 2015. Suppression of gas detonation by a dust cloud at reduced mixture pressures. Shock Waves. 25(3):267–275.
- Qi Y, Gan X, Li Z, Li L, Wang Y, Ji W. 2021. Variation and prediction methods of the explosion characteristic parameters of coal dust/gas mixtures. Energies. 14(2):264–213.
- Sanchirico R, Di Sarli V, Di Benedetto A. 2018. Volatile point of dust mixtures and hybrid mixtures. J Loss Prev Process Ind. 56:370–377. ():
- Sanchirico R, Di Sarli V, Di Benedetto A. 2020. Effect of initial pressure on the lower explosion limit of nicotinic acid/acetone mixture. J Loss Prev Process Ind. 64:104075.
- Sanchirico R, Russo P, Di Sarli V, Di Benedetto A. 2014. Explosibility and flammability characteristics of nicotinic acid-lycopodium/air mixtures. Chem Eng Trans. 36:265–270.
- Sanchirico R, Russo P, Saliva A, Doussot A, Di Sarli V, Di Benedetto A. 2015. Explosion of lycopodium-nicotinic acid-methane complex hybrid mixtures. J Loss Prev Process Ind. 36:505–508.
- Si R, Li R, Su D. 2018. Experimental study on the influence of coal dust cloud mass concentration on gas explosion pressure. J Saf Environ. 18(05):1796–1798.
- Tan B, Liu H, Xu B, Wang T. 2020. Comparative study of the explosion pressure characteristics of micro- and nano-sized coal dust mixtures in a pipe. Int J Coal Sci Technol. 7:68–78.
- Wang B, Gou R, Kan R. 2019. Influence of particle size of coal dust on gas and coal dust explosion. J North Univ China (Nat Sci Ed). 40(01):79–83+89.
- Wang S, Shi Z, Peng X, Zhang Y, Cao W, Chen W, Li J. 2019. Effect of the ignition delay time on explosion severity parameters of coal dust/air mixtures. Powder Technol. 342:509–516.
- Wang Z. 2017. Study on the influence of low concentration gas on the lower limit of coal dust explosion. Saf Coal Mines. 48(02):26–27+32.
- Zhang L, Yang Q, Shi B, Niu Y, Zhong Z. 2021. Influences of a pipeline’s bending angle on the propagation law of coal dust explosion induced by gas explosion. Combust Sci Technol. 193(5):798–811.
- Zhou Y, Gan B, Jiang H, Huang L, Gao W. 2022. Investigations on the flame propagation characteristics in methane and coal dust hybrid explosions. Explos Shock Waves. 42:1. http://kns.cnki.net/kcms/detail/51.1148.O3.20210721.1634.012.html.