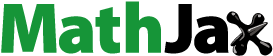
Abstract
In biodiesel production by trans-esterification, one of the essential compound is glycerin. Global glycerin production is increasing significantly, projecting a global value reduction for glycerol. Consequently the scientific community had been encouraged to investigate converting glycerol into more valuable products. In this research, the primary sources and processes of biodiesel production are surveyed. Where the processes that involve glycerin are reviewed and the diesel engine performance and emissions under variant states are discussed. According to the results of this study, it is reported that the choice of an optimal diesel/biodiesel significantly depends on the materials, additives and the engine condition. Glycerol etherification, carboxylation, and glycerol carbonate, however, had been identified as the widely manufactured and used additives. It is further observed that the use of these such additives has reduced several emissions, which is an important factor. In addition, it is suggested that using glycerin additives improves the properties of biodiesel. Acetone, on the other hand is introduced as one of the most important additives in the combination of diesel and biodiesel fuel due to the reduction of maximum emission. The presence of hydroxyl groups can reduce NOx. Finally, the diethyl ether additive can be mentioned which increases the thermal efficiency and increases the brake-specific fuel consumption (BSFC).
1. Introduction
Today, the need for new energy sources is one of the major problems for all countries in the world. This is a problem not only for oil-importing countries but also for the major oil producers. The unavailability of fossil fuels, termination and environmental problems and price fluctuations of these resources are the most important contemporary human challenge. Greenhouse gas emissions from fossil fuels, including coal, gasoline, and oil, are alarming, while many governments are developing fossil energy use (Karmaker et al., Citation2019). Given the current environmental challenges and concerns, it makes more sense to find renewable energy sources (Akbarian & Najafi, Citation2019; Karimi et al., Citation2020; Karimmaslak et al., Citation2021; Najafi et al., Citation2021; Shoar et al., Citation2021). Renewable energy sources should be able to reduce the negative environmental impacts of fossil fuels. They are economically competitive with fossil fuels and do not reduce the process of food production (Hill et al., Citation2006; Shoar et al., Citation2019). EU's policy on renewable energy use by 2030 is based on a soft governance approach (Akbari et al., Citation2020; Veum & Bauknecht, Citation2019). Due to the current market situation and increasing demand for green energy, the production of bioethanol and biodiesel will increase by 2030 (Bórawski et al., Citation2019). Predictions for the biofuel market for a ten-year period (2018–2027) show that global biodiesel production will be increasing from 36 billion liters in 2017–39 billion liters in 2027. Besides, global ethanol production will be increased from 120 billion liters in 2017 to 131 billion liters in 2027. Economic forecasts also show that prices for these biofuels will fall by 8 and 14 percent, respectively, over the next decade (Judge, Citation1988; Organisation for Economic Co-operation and Development (OECD), & Food and Agriculture Organization of the United Nations (FAO), Citation2018).
Biodiesel is mainly used to generate heat and power in diesel engines (Klein et al., Citation2018). The biodiesel building is similar to that of diesel fuel (Xu et al., Citation2016). The cetane number and similar thermal value provide the capability to replacing diesel with biodiesel (Noor et al., Citation2018). Biodiesel can easily be blended with both diesel and alcohol blends (Yilmaz & Atmanli, Citation2017). Research showed that biodiesel cetane number was higher than that of diesel, but its thermal value was lower than that of diesel (Najafi et al., Citation2018). The biodiesel cetane number from oilseeds is lower than the biodiesel cetane number from animal oils (Ambata et al., Citation2018). Besides, the attendance of oxygen in the chemical structure of biodiesel results in cleaner combustion than that of diesel fuel. By biodiesel fuel combustion, emissions of PM, poly aromatic hydrocarbons and SO2 decrease. Biodiesel has a high flash point. Biodiesel does not have sulfur (Akbarian & Najafi, Citation2019; Hosseinzadeh-Bandbafha et al., Citation2018; Noor et al., Citation2018). Biodiesel can be mixed with diesel fuel in any proportion. It is currently common to use 5% biodiesel (B5) and diesel fuel mixes, and most countries are planning to use B20 fuel (Lewis et al., Citation2009). Researches showed that biodiesel–diesel fuel mixture up to 20% can be used in the conventional diesel engine. This 20% compounding rate was recommended in order to keep engine performance at a high level and also to reduce environmental pollution (Attia et al., Citation2018).
Biodiesel is mono-alkyl fatty acid esters (FAAE), produced from triglycerides found in vegetable oils or animal fats. Various methods have been developed for biodiesel production, which was reviewed in Ambata et al. (Citation2018), Mittelbach (Citation2009), and Tabatabaei et al. (Citation2019). Currently, biodiesel production by alkaline trans-esterification is very common because it costs less and has a higher conversion efficiency. Figure shows the trans-esterification reaction from triglycerides in the presence of oil (Go et al., Citation2016; Haghighat Shoar & Najafi, Citation2021). However, acid catalysts for the trans-esterification process are not widely used in the industry (Boon-Anuwat et al., Citation2015). According to the theory, 1 mol of triglyceride and 3 moles of alcohol (such as methanol or ethanol) react together with a catalyst (such as NaOH) to produce 3-mole of ester (biodiesel) and 1 mol of glycerol.
In research by Ghazanfari et al. (Citation2017), biodiesel was obtained by the trans-esterification method from oil (palm) and ethanol in the presence of NaOH catalysts. According to this method, the oil was warmed to 70°C and mixed at 600 rpm. In other reactor, ethanol, with 1/3 of the primary weight of the oil (with molar ratio of alcohol to oil of 6:1), was warmed to 70°C in the presence of a 0.1 wt% NaOH catalyst. Then alcohol and catalyst were added to oil and the solution was stirred at 600 rpm for 30 min and 70°C. After 8 h, the solution temperature was reduced to ambient temperature (25°C). Then the acidity of the solution was measured and by adding 46% hydrochloric acid, it was regulated to about 7. The operation of rinsing by using water at 50°C was performed by gravitation for 12 h (Ghazanfari et al., Citation2017). Figure shows the steps of biodiesel production by trans-esterification.
Figure 2. Processes of biodiesel production under optimal conditions by alkaline trans-esterification method.
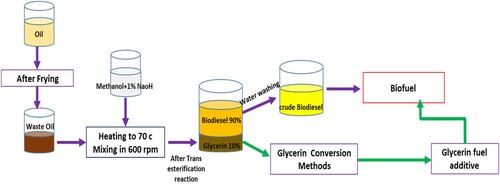
The conversion efficiency obtained in the trans-esterification reaction depends on the type and percentage of catalyst purity, alcohol to oil ratio, reaction temperature and time, water mass, and amount of free fatty acids (Pitt et al., Citation2019). In a study by Ahmad et al. (Citation2019), optimization of effective factors in the biodiesel production process from flaxseed oil was performed by a trans-esterification method using response surface methodology. They studied factors such as ratio of methanol to oil volume, catalyst weight percentage (KOH), reaction temperature and time. According to the results, the highest amount of biodiesel production was about 99.5% at optimum conditions with reaction temperature of 59°C, catalyst content of 0.51% primary oil, 33 min reaction time and molar ratio of 5.9:1 from methanol to cotton oil (Ahmad et al., Citation2019). Successful commercialization and marketability of biodiesel require stringent quality assurance standards. Evaluation of the quality of biodiesel is achieved by determining its chemical composition and physical properties. Properties and limits specified in the biodiesel standard should protect the efficiency and durability of automobile engines or combustion equipment (Carrero & Pérez, Citation2012). Biodiesel can only be used when it meets the required standards. These standards (Table ) include a density at 15°C (according to NPEN 14214 standard: 2009), which is adapted from (Knothe, Citation2006), the amount of iodine (according to EN14111 standard) and some others (Caetano et al., Citation2012).
Table 1. Biodiesel standard according to ASTM D6751a.
Biodiesel is produced from renewable energy sources, including vegetable oils or animal fats. Production of biodiesel from food sources can imperil food security, therefore, global efforts to produce biodiesel from non-food sources have increased. And biomass, which contains raw materials, is considered as an energy source. Plant oils and animal adiposes are green energy sources. Table , which is adapted from (Atabani et al., Citation2013), shows oils available from raw materials as well as their percentages of oil.
Table 2. Available oil per hectare of sources.
Sources of biodiesel production can be divided into three generations (Figure ). In the first generation, biodiesel was produced from oil sources such as sunflower, soybean, date, coconut, castor, rapeseed, and sesame. By increasing the production of biodiesel from edible oils, there have been concerns about the utilization of arable land for the agricultural generation to produce biodiesel, which could lead to a shortage of food sources. In the second generation of biodiesel production sources, the tendency to use non-food sources has increased. As such, it was not competitive with food production (Yang et al., Citation2014).
Biodiesel sources in the third generation (Mofijur et al., Citation2019) do not directly compete with food and also do not lead to land-use change and environmental damage. These sources can make cheap biodiesel fuel available. For example, through the third generation, Isochrysis aff. galbana microalgae can be considered as more viable source for biodiesel production, partly due to the relative ease in producing a high oil yield (Atmanli, Citation2020). Therefore, third generation resources are a good alternative for the first and second generations (Singh et al., Citation2011). In the biodiesel production process by trans-esterification, glycerol is produced as a by-product (Anger et al., Citation2011). By increasing the biodiesel utilization in the world, the glycerol production amount is increasing. Excess glycerol has created a new challenge. Although there are a wide range of potential applications for crude glycerol, glycerol produced in the trans-esterification process has a low purity, which limits its conversion to other materials (Monteiro et al., Citation2018). Studies showed that biodiesel production was drastically increasing (Nomanbhay et al., Citation2018), and consequently, glycerin production was also growing. It was expected that this trend would continue until 2030. Figure is adapted and reproduced from (Nomanbhay et al., Citation2018). This figure shows the global glycerol production trend by 2030. This amount of glycerin is anticipated to be about 48500 million cubic meters.
Due to the increasing production of glycerin and its environmental problems, it needs to be managed and transformed into more valuable and environmentally friendly products. Therefore, in this research, the conversion of glycerin to other materials is investigated. The production of glycerin occurs in both edible and non-edible oils and its amount is approximately the same as 10% by volume of the transesterification process material produced. Glycerin is produced during the transesterification reaction, which is one of the most efficient and common methods for biodiesel production, and therefore glycerin is produced during different steps of this process. Therefore, various edible and non-edible oils do not play a significant role in the production or non-production of glycerin. However, the use of edible waste oils (second-generation) and non-edible oils (third-generation), which have no competition with human food is recommended. These sources are much more economical and feasible. In this research, the study is conducted with emphasis on non-edible oils, although as mentioned above, glycerin production is due to various stages of the transesterification method and its amount for all various sources is about 10% by volume. Different ways of producing glycerol products are investigated at first. Then the materials from these methods and their applications are analyzed. Finally, the possibility of using glycerin-derived products as an additive for diesel fuel and their impacts on performance and emission of the engine are investigated on a diesel engine.
2. Glycerin
Glycerol, being a chemical product commercially known as glycerin, is colorless, odorless, and viscous at room temperature (Christoph et al., Citation2000). It is classified as three-component alcohols with formula C3H5(OH)3 according to IUPAC and is known as 1, 2, 3-propantryriol. Glycerol is completely soluble in water, alcohol and in many common solvents such as ether and dioxane, due to its three hydrophilic hydroxyl groups, but it is insoluble in hydrocarbons. This is true for glycerin with 95% purity. Table shows some of the glycerol physical properties at 293 K (Pitt et al., Citation2019) that make it difficult to use for new products. Usually, glycerol obtained from the trans-esterification process has a purity of 90-92%, adapted from (Christoph et al., Citation2000).
Table 3. Some physical properties of glycerol at 293 K.
2.1. Glycerol reforming processes (GRP)
Glycerol is a fundamental chemical for biological refineries. Glycerol produced during the biodiesel production process is the primary feedstock for bio-factory (Yazdani & Gonzalez, Citation2007). Glycerol is a crude substance for the production of intermediates or chemical materials at various industrialization and application sectors (Monteiro et al., Citation2018). In general, glycerol can be used for the following usages:
Production of chemical products;
Manufacture of polymer compounds;
Generation of biofuels;
Refinement and direct utilization from glycerol.
Therefore, the extension of novel technologies for the utilization of glycerol is essential (Monteiro et al., Citation2018). Production of chemical materials, foods, polymers, fuel additives, hydrogen, and energy industries such as fuel cells, gasification industries, and anaerobic digestion are important destinations for glycerin conversion from biodiesel production.
Glycerol as an attractive substance (Karam et al., Citation2008) is used for the synthesis of many products such as surfactants (Pirog et al., Citation2013) and solvents (Favier et al., Citation2018). Besides, glycerol as a promising crude substance for microbial surfactants, can create modern antimicrobial materials for use in food, pharmaceutical, health, agricultural and practical applications (Pirog et al., Citation2013). Due to the high demand for renewable energy sources, glycerol has a tremendous potential to become a valuable material, which can be used as a fuel additive to petroleum derivatives, have a good perspective in the oil industry. Converting glycerol to oxygenated fuels by a variety of methods such as etherification and esterification have attracted attention (Rahmat et al., Citation2010). For example, glycerol triacetate (GT) compound was used as a fuel additive by glycerol esterification on the CI engine (Akbarian & Najafi, Citation2019). General methods for converting glycerin to other substances are shown in Figure . In the following, methods for converting glycerin to more valuable materials are discussed.
2.1.1. Glycerol aqueous phase modification process (GAPR)
The glycerol aqueous phase modification process (GAPR) is a potential pathway for the manufacture of fluid and H2 fuels. GAPR is usually accomplished in continuous current with a moderate temperature (200–260°C) and high pressure (20–50 bar). The conversion to aqueous phase occurs without any pre-evaporation steps. The GAPR reaction is according to EquationEq. (1(1)
(1) ) (Roslan et al., Citation2019):
(1)
(1)
Fluid alkanes can be directly manufactured from glycerol during a continuous process (Figure ). The process implicates the catalytic transformation from glycerol into H2 and CO synthesis gas mixtures, which are combined by FT synthesis process (Fischer-Tropsch). Syngas (synthesis gas) can be manufactured from concentrated glycerol at 548 K, pressures of 1–17 bar and 10% weight of Pt-Re catalyst (1:1). The major intermediates when converting glycerol to syngas include acetone and ethanol (Simonetti et al., Citation2007). As an application of synthesis gas from H2 and CO produced by the APR method, the production of saturated and unsaturated liquid fuels can be mentioned (Domínguez-Barroso et al., Citation2019). Using Pt-Ni/Al2O3 catalyst at 200°C, 80.3% of glycerol can be converted to H2.
Figure 6. Formation of alkanes and liquid fuels from glycerol by combining two processes of GAPR and Fischer-Tropsch.
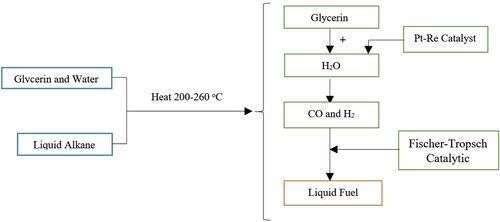
The best way to increase the economic values of biodiesel is to convert raw glycerol into valuable products such as H2 and syngas. H2 production from glycerol is accomplished by various processes such as aqueous phase modification, pyrolysis, steam modification, partial oxidation, and dry modification reactions. In large-scale industrial applications, Ni-based catalysts are used as the most common catalyst, because this type of catalyst is easily accessible, cheap and has high catalytic activity (Roslan et al., Citation2019).
The GAPR process is an endothermic process. As such, this method requires high energy consumption; but the advantages of this process are its high speed and selectivity. Due to the harsh conditions and high cost of this method, there has been little research performed on this method, yet this method can convert glycerol into liquid fuels (alkanes).
2.1.2. Glycerol reduction process (GRP)
Glycerol reduction process (GRP) with hydrogen produces ethylene and propylene glycol (Figure ). Glycerol is hydrogenated by metal catalysts and hydrogen and it is converted to products such as propylene glycol ethylene glycol and 1, 3 – propylene glycol. The major product of the glycerol reduction process is propylene glycol (propanediol).
Figure 7. Glycerol reduction process (GRP) with hydrogen to produce propanediol and ethylene glycol.
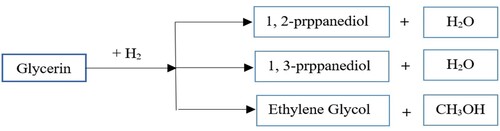
Hydrogenolysis of glycerol to propane-diol is accomplished by using Ni, Pd, and Cu chromate catalysts. Propanediol conversion is reduced due to excessive hydrogenolysis of propylene glycol at 473 K and 13.79 bar. Besides, with decreasing water content, the efficiency of propanediol increases. Cu chromite catalyst (CuO.Cr2O3) at 473 K is used to generate propanediol from glycerol. The reaction is executed by forming an intermediate, which is acetol (hydroxy-acetone). Figure is adapted and reproduced from (Dasari et al., Citation2005). Studies of different catalysts at 473 K and 13.79 bar pressure indicated that the highest conversion rate of glycerol to propylene glycol was obtained by chromite copper catalyst.
Figure 8. Mechanism for generation of 1- 2-propanediol from glycerol and formation of acetol intermediates during the glycerol reduction reactions.

Besides, the highest glycerol conversion is achievable by using CuNi/Al2O3 and CuNi/ZSM-5 catalysts at 80 and 85%, respectively. With these catalysts, about 25% of the production is propylene glycol. By hydrogen addition, the glycerol conversion achieves above 90% in all catalysts. Single mono-metal catalysts, compared with bimetallic samples from copper, produces higher propylene glycol. Cu/Al2O3 showed the highest performance to convert to propylene glycol (with 70% efficiency) (Freitas et al., Citation2018). In this method, selectively the intermediate hydroxyl category converts glycerol to the tosyloxy group, afterward separates the changed group by using catalyst hydrogenolysis. By this novel approach, the transformation of glycerol to 1, 3-propanediol was performed in 3 stages: (1) acetylation, (2) tosyloxylation and (3) de-tosyloxylation. Steps for the establishment of 1, 3-Propylene glycol are shown in Figure , which is adapted and reproduced from (Wang et al., Citation2003).
Nanoparticles synthesis (AuNPs), specifically with greenways, due to its bio-adaptability and various usages in different threads, has received a lot of attention. The establishment of permanent AuNPs with a controlled scale mostly needs the utilization of surfactants. These stabilizing factors may damage catalytic actuality and also have noxious effect on the bio-adaptability of AuNPs and surfactants. Therefore, in the study (Parveen et al., Citation2019), the effects of glycerol and water ratio, pH, temperature, ionic strength on stability and particle size distribution were investigated. Such AuNPs obtained in this way by the reduction method were environmentally friendly and have useful applications in catalytic and medical fields (Parveen et al., Citation2019).
Glycerol reduction is another effective way to produce different products from glycerol under mild conditions. In this method, glycerol is hydrogenated using metal catalysts. This method does not require high-temperature conditions in the glycerol aqueous phase modification process, so it is more economical. Synthesis parameters indicate that the ability to reduce and stabilize glycerol is associated with pH and percentage of glycerol in the reaction medium, respectively. The main products produced by this method include 1, 2-propanediol (propylene glycol) and 1, 3-propane (diethyl and ethylene glycol). A major product of the glycerol reduction process is propylene glycol, which is not harmful to the environment.
2.1.3. Glycerol dehydration process (GDP)
From the Glycerol Dehydration reaction, two important acrolein chemicals and 3-hydroxy-propionaldehyde (3-HPA) can be prepared directly. In the primary stage, the glycerol dehydration process results in the establishment of enols that are in balance with hydroxy-acetone and 3-hydroxy-propionaldehyde. Then in the second step, it is formed by the dehydration reaction of acrolein or by the reaction of retro-aldol in the presence of O2 and formaldehyde. Figure is adapted and reproduced from (Katryniok et al., Citation2009). Acetaldehyde may be quickly converted to acetic acid.
Figure 10. Formation of acrolein and 3-hydroxy propion aldehyde (3-HPA) via glycerol dehydrogenation reaction.
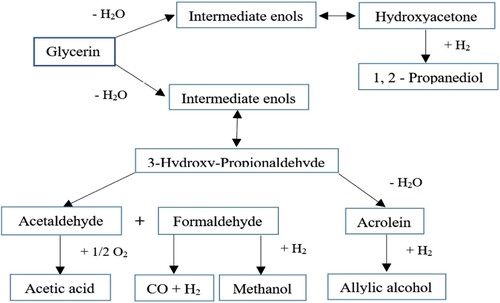
Different studies on the method of dehydrating glycerol to3-hydroxy propionaldehyde were performed (Table ). In the study of Lago et al. (Citation2018), modified H-ZSM-5 zeolite catalysts for the dehydration of glycerol to acrolein in the gaseous phase were investigated. Alkaline pretreatment with sodium carbonate aqueous solutions at various concentrations was also carried out with ion exchange from ammonium nitrate solution. Their results showed that at selected concentrations, temperature and time of pretreatment to achieve selective removal of Si from the zeolite structure and keeping Al content, middle porosity was more appropriate. Alkaline pretreatment with Na2CO3 resulted in higher performance compared to that of NaOH pretreatment. Therefore, this led to lower acrolein selectivity and higher selectivity for acetone formation (Lago et al., Citation2018). The glycerol dehydration process to acrolein and acrylic acid is shown in Figure .
Table 4. Studies on dehydration of glycerol to 3-hydroxy propionaldehyde.
In the study of Vieira et al. (Citation2015), the effect of crystal size, acidity, and synthesized products on the efficiency of AL and Ga -MFI zeolite catalysts in glycerol dehydrogenation were studied. The outcome illustrated that the efficiency of these catalysts was very good in glycerol dehydrogenation reaction. Besides, small zeolite particles, especially gallium zeolite catalysts, increased the duration of catalyst effectiveness. The main product of this synthesis was acrolein. Therefore, the acidity and size of the zeolite crystals affected the inactivation and activation of the catalyst in glycerol dehydration.
Different studies on dehydrating glycerol to acrolein were performed (Table ) (Dasari et al., Citation2005; Domínguez-Barroso et al., Citation2019; Freitas et al., Citation2018; Katryniok et al., Citation2009; Parveen et al., Citation2019; Simonetti et al., Citation2007; Wang et al., Citation2003). Acrolein is a chemical material and is used as an industrial and pesticide chemical. So dealing with it requires safety tips (Auerbach et al., Citation2008). The conversion process of glycerol dehydration to acrolein is accompanied by adverse reactions and leading to the establishment of byproducts. This causes the formation of coke on the catalyst and changes its color from white to black. Besides, the catalyst increases weight and becomes inactive, and its efficiency and selectivity for acrolein production are reduced. 90% of glycerol conversion, with 80% selectivity of acrolein, is achievable in supercritical conditions at 34.5 MPa, 673 K and in the vicinity of H2SO4 catalyst. In order to improve the efficiency of this process, the authors propose to increase the concentration of glycerol and H2SO4 and work at higher pressures (Watanabe et al., Citation2007). After the acrolein product, the product of 3-hydroxy propion aldehyde (3-HPA) is another glycerine-derived substance during the dehydration procedure. 3-HPA is an important industrial intermediate that can be converted into a number of large-scale conventional chemicals. Figure is adapted and reproduced from (Zheng et al., Citation2008). These include acrolein, acrylic acid, 3-hydroxy propionic acid (3- HPA), malonic acid, acrylamide and 1, 3-propanediol.
Figure 11. Use of enzymes in the production of 3-HPA and application of this intermediate in the preparation of other chemicals.
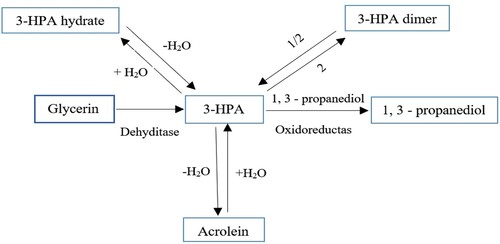
Table 5. Studies on dehydrating glycerol to acrolein.
3HPA is important for several chemicals and polymer materials and is also momentous for various chemical materials and polymer. Poly 3HP is a polyester that is tolerable to degradability. Figure is adapted and reproduced from (Zaushitsyna et al., Citation2017). Different studies on dehydrating glycerol to 3-hydroxy propionaldehyde were performed (Auerbach et al., Citation2008; Sardari et al., Citation2013; Sardari et al., Citation2014; Zaushitsyna et al., Citation2017).
Figure 12. Metabolic pathway for biological transfer of glycerol to 3HP and 1, 3-PDO with 3HPA as intermediates with Lactobacillus reuteri cells along with various enzymes, mediators and effectors factors.
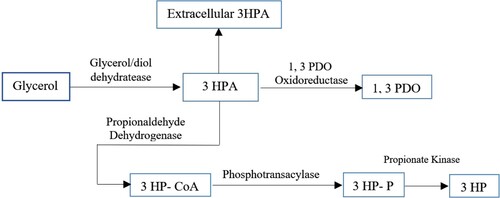
Numerous attempts have been made to develop glycerol conversion processes into precious chemical materials, which suggests that this is a major source for some future glycerol applications. These include the generation of 1,2-propylene glycol, 1,3-propylene glycol, and acrolein. According to these results, alkaline pretreatment is a suitable solution to increase acrolein production. The use of catalysts also improves the production of acrolein and in the meantime, the SiW20-Al / Zr10 catalyst performs well. Another important product from the glycerol dehydration method is 3-hydroxy propion aldehyde, which is an important industrial intermediate, and it turns into some of the most common chemicals on a large scale. However, given the usual use of glycerol, the actual market seems to be unable to consume all produced glycerol. Therefore, in the future, a purification step is needed to achieve the degree of purity on an industrial scale.
2.1.4. Oxidative dehydration of glycerol to acrylic acid (ODG)
Acrylic acid is one of common products made of glycerin. The dehydration reaction is coupled with aerobic oxidation to transform acrolein to acrylic acid directly. In this process, the oxidative exothermic reaction is accompanied by the dehydrating endothermic reaction. Figure is adapted and reproduced from (Li & Zhang, Citation2016). An investigation by dos Santos et al. (Citation2019) performed the oxidative dehydration of glycerol for the generation of stable acrylic acid using H, Fe-MCM-22 catalysts, in which H, Fe-MCM-22 catalysts were reported to be highly active in the dehydration oxidation of glycerol and its conversion to acrylic acid. Fe is a marvelous metal, mostly due to its Fe3+ or Fe2+ regeneration cycle, which has made it affordable and low costly response, also it is low toxic than V, W or Mo (dos Santos et al., Citation2019).
Balancing tissue properties and regeneration of H, Fe-MCM-22 catalysts leads to a better dehydration function of glycerol. This is especially true for low Fe amount catalysts. The performance of H-Fe-MCM-22 catalysts is related to other catalysts caused by regenerated molecules or blended oxides. Even in more difficult moods, it also acts as an enhancer of the molar ratio of oxygen to glycerol. Low iron catalysts increase the selectivity of acrylic acid. Vanadium-based catalysts also have good potential and are used for glycerol conversion and acrylic acid production without significant reduction. Vanadium is a non-toxic and widely available metal and it has the potential to achieve sustainable manufacture from acrylic acid. But results showed that He-MCM-22 was a promising catalyst for sustainable manufacture from acrylic acid instead of V23 catalysts (dos Santos et al., Citation2019).
In general, the ODG to acrylic acid is a thermally equilibrated process because it has both exothermic and endothermic phases. Acrylic acid is a widely used substance derived from glycerin and the toxicity of this substance is low. In the production of this material, H, Fe-MCM-22 has been reported as the best catalyst because of its high activity. Compared to other glycerol conversion methods, less research has been performed on this method.
2.1.5. Glycerol etherification (GE)
Glycerol ethers are manufactured from esterification of glycerol via iso-butene in the presence of homogeneous acidic catalysts (Vlad et al., Citation2011). Figure is adapted and reproduced from (Zheng et al., Citation2008). By reacting glycerol with isobutene in etherification, the production of mono-ether, di-ether and tri-ether can be attained. Different syntheses have been undertaken to convert di-ethers and tri-ethers from glycerin to higher ethers. ‘Superior ethers’ may be consumed as an octane booster for car fuel (Behr & Obendorf, Citation2002).
Figure 14. Provision of glycerol ethers from the reaction between glycerol and isobutene with different molar ratios.
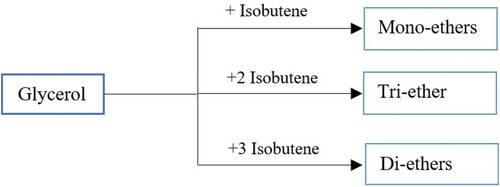
Oxygenated compounds can be considered as fuel additives with the function of octane resonator. For example, methyl tri-butyl ether has explosive properties and is added to the fuel as octane enhancers. Glycerol tri-butyl ethers (GTBEs), as additives for diesel fuel and biodiesel, increase the fuel octane number and they are soluble in nonpolar fuels. Alcohols and ethers offer different and specific benefits in providing clean fuel. Methyl tri-butyl ether (MTBE) has been the preferable product, but a positive future outlook is predictable for less volatile ethyl tri-butyl ether (ETBE) and methyl tri-ethyl ether (TAME) (Ancillotti & Fattore, Citation1998; Noureddini, Citation2001).
Different researches on etherification of glycerol are reviewed (Table ) (Ancillotti & Fattore, Citation1998; Behr & Obendorf, Citation2002; Bookong et al., Citation2015; Bozkurt, Baglar, et al., Citation2019; Bozkurt, Yılmaz, et al. Citation2019; Cannilla et al., Citation2015; Decolatti et al., Citation2014; dos Santos et al., Citation2019; Estevez et al., Citation2016; Ishak et al., Citation2016; Kim et al., Citation2007; Klepacova et al., Citation2007; Li & Zhang, Citation2016; Neves et al., Citation2018; Noureddini, Citation2001; Okoye et al., Citation2017; Vlad et al., Citation2011; Yun et al., Citation2016). Glycerol acetyls and glycerol ethers are known as fuel additives (Bozkurt, Yılmaz, et al. Citation2019; Ishak et al., Citation2016; Kim et al., Citation2007). One promising way to transform glycerol into high-value chemicals is to yield acetone by acetylation of glycerol. The major outcomes of glycerol acetylation are mon-acetin, di-acetin, and tri-acetin. These actions have great commercial importance. They are mostly consumed as a fuel additive in transport (Okoye et al., Citation2017; Zheng et al., Citation2008). The production of glycerol ethers can be one of the promising approaches because its synthesis helps as a desirable solution in technical, economic, and strategic fields. Some wonderful alternative production from glycerol are mono, di, and tri -acetyl-glycerols, which are mostly consumed in food, cosmetic, pharmaceutical and plastic industries (Rahmat et al., Citation2010).
Table 6. Different studies on the etherification of glycerol.
As a result, it is highly desirable to add low-cost glycerol to valuable chemicals or substances. Glycerol etherification with acetic acid is used to produce glycerol acetate as a bio-additive from biodiesel, which provides a promising approach to glycerol use. This pathway leads to the establishment of glyceryl-mono-acetate (MAG), glyceryl-di-acetate (DAG) and glyceryl-tri-acetate (TAG), which are widely used in degradable polyesters as well as cosmetics (Rahmat et al., Citation2010).
Many of the recent methods that use glycerol as a raw material are in the expanding phase yet, and some have been commercialized. Accordingly, the straight transformation of glycerol to important chemical materials have engrossed many considerations. Glycerol ethers are produced by using different catalysts during the etherification process; Based on the comparison of results in the above table, when BEA di-silicate zeolite catalysts react with glycerol, they produce high amounts of di and tri-butyl-glycerol. Therefore, these ethers may be utilized as oxygen fuels to improve diesel fuel.
2.1.6. Polymerization to poly-glycerol
Poly-glycerol is a branched structure, it is liquid and has high viscosity. It is completely solvable in liquid and polar solvents, for example, ethanol. Besides, it is non-volatile at normal temperatures. Glycidol is a derivative of glycerol and is used in the controlled synthesis of poly-glycerol. For example, one type of rapidly emerging polymers is PGs. PEG is a promising alternative for medical applications (Ampatzidis et al., Citation2014; Gheybi et al., Citation2018). Poly-glycerols (sometimes called ‘poly-glycidols’) represent classes of extremely bio-matchable and multi-hydroxyl polymers that can be propounded as polyethylene glycol (PEG). is adapted and reproduced from (Thomas et al., Citation2014). Also, is adapted and reproduced from (Jamróz-Piegza et al., Citation2006). Different architectures of monomers lead to the formation of poly-glycerols. Glycidol polymerization results in over-excited state poly-glycerols.
A novel type of exothermic polymers based on modified polymers poly-glycidol (1, 2, 3-expoxypropanol) has been proposed. During heating, the water reactivity and solubility of the polymer (glycidol-ethyl glycidyl carbamate) are obtained by modifying the hydrophilicity of the hydroxyl groups from the poly-glycidol chain with ethyl isocyanate.
Linear poly-glycidols with high molar masses are provided using activated monomeric anionic polymerization, ethoxy ethyl-glycidyl ether, and tert-butyl-glycidyl ether, with a composed system of tetra-octyl ammonium bromide as initiator and tri iso-butyl-ammonium as an activator of monomer. The polymerization reaction is shown in Figure , which is adapted and reproduced from (Gervais et al., Citation2010).
Pharmaceutical polymeric compounds derived from branched poly-glycerol sulfate and mono-methyl auristatin E were evaluated as anticancer drugs. Intermixed polymers (PDCs) offer promising ways to treat cancer, according to (Rades et al., Citation2019).
Sangkhum et al. (Citation2019) investigated the oxidation of Ca–Mg–Al compound for selective glycerol etherification to short-chain poly-glycerols. The oxidation of Ca–Mg–Al triple compound by various loading rates of Ca was successfully provided by saturating raw materials from calcium citrate solution on Mg–Al formed from LDH oxide. The calcination was performed at 700°C. Results by using the poly-glycerol polymerization method were as follows. Ca–Mg–Al MMO with high-dispersion of Ca2 + ions introduced a new semi-porous structure. Glycerol conversion and DG correlation performance were well correlated with the amount of MMO catalysts. In 7.5% Ca–Mg–Al MMO, the greatest conversion rate of glycerol (40.4%) and DG selectivity (78.3%) were reported at relatively bottom temperature (220°C) (Sangkhum et al., Citation2019).
In another study by Zhang et al. (Citation2010), high-energy PEI polymers led poly-glycerol to the delivery of genes. To improve the efficiency of gene transfection and prevent cancer cells, branched polymers, namely PG6-PEI25k and PG6-PEI800, are designed as novel gene pathways.
Currently, a number of poly-glycerols are commercially available in a variety of applications, including cosmetics and pharmaceuticals. Biocompatibility is a prominent feature of these materials in determining their use.
2.1.7. Glycerol esterification
Glycerol esterification has been one of the practical methods of converting glycerol into valuable substances. The esterification reaction is carried out by carboxylic acids, carboxylation and adding nitrate to glycerol. By glycerol esterification via acetic acid and catalysts, glycerol is converted to glycerol-monoacetate, glyceryl -diacetate, and glyceryl-tri- acetate. Glycerol conversion can be caused even under the absence of the catalyst in this reaction. Therefore, glycerol esterification is a self-catalyzed reaction, in which the acidic protons present in acetic acid can catalyze this reaction itself (Gao et al., Citation2015).
2.1.8. Carboxylation reaction for glycerol carbonate preparation
In general, glycerol carbonate is synthesized by the reaction between glycerol and fusogen. However, due to the great noxiously of fusogen, trans-esterification-based alternatives to di-alkyl or alkylene carbonates have been investigated. Industrial synthesis of glycerol carbonate requires several stages. Ethylene oxide reacts with carbon dioxide, which results in the production of annular ethylene carbonate. Glycerol is also reacted to produce glycerol carbonate and ethylene glycol. This function includes the utilization of homogeneous basic catalysts, for example, sodium bicarbonate or sodium hydroxide (Figure ). It has problems such as neutralization and also causes problems in the recovery of the product with low-pressure distillation method (Alvarez et al., Citation2012).
Trans-esterification of glycerol by annular carbonates or alkyl carbonates is thermodynamically favorable for the production of glycerol carbonate from glycerol. Increasing the temperature may enhance the chemical balance of the reaction of glycerol with dimethyl carbonate (Li & Wang, Citation2011).
Moreover, glycerol carbonate can be produced by the following methods (Figures ) (Li & Wang, Citation2011).
The production of glycerol carbonate by using aluminum waste as a low-cost catalyst resulted in the highest conversion of glycerol at 500°C (Das & Mohanty, Citation2019). Glycerol carbonate is polar, colorless, non-toxic and has high boiling temperature. Another method for the production of carbonate derivatives of glycerol results from the reaction between urea and glycerol. In this process, glycerol carbonate is separated from glycerol by 90% yield (with100% purity) and the reaction provides more conversion and more energy savings, 29.1%, and 37.1% respectively (Lertlukkanasuk et al., Citation2013).
Alvarez et al. (Citation2012) investigated the synthesis of glycerol carbonate by trans-esterification of glycerol in a continuous system using hydrotalcites as a catalyst. Glycerol esterification method, as an efficient method to obtain the hydrotalcite used in α-Al2O3 or γ-Al2O3, was employed. They are active in converting glycerol to glycerol carbonate and glycerol di-carbonate.
In addition, it was demonstrated that activated catalysts led to greater production of glycerol dicarbonate manufactured in glycerol carbonate. An enhancement in Mg amount in the catalyst resulted in better glycerol conversion and better glycerol dicarbonate yield, although the HTr4-Alpha catalyst was less stable than the HTr2-Alpha catalyst. This was maybe due to the presence of excess MgO (H) in the catalyst. Therefore, it was deduced that hydrotalcite combinations were promising for the continuous trans-esterification reaction (Alvarez et al., Citation2012).
Zheng et al. (Citation2015) investigated the trans-esterification of glycerol with calcined Ca–Al hydrocalumite dimethyl carbonate. Ca–Al hydrodalumite (Ca/Al = 2–6) was synthesized by high crystallization using a conventional Coprecipitation technique in N2 space. According to results, calcined Ca–Al hydrocalumite was an efficient catalyst for glycerol trans-esterification with dimethyl glycerol carbonate and had high selectivity of glycerol carbonate compared with usual conditions. The highest conversion rates of glycerol and GC selectivity were 93% and 97%, respectively.
Different studies on the carboxylation reaction for glycerol carbonate were performed (Alvarez et al., Citation2012; Alvarez et al., Citation2012; Das & Mohanty, Citation2019; dos Santos et al., Citation2019; Elhaj et al., Citation2019; Gao et al., Citation2015; Goncalves et al., Citation2015; Gonzalez-Arellano et al., Citation2015; Lertlukkanasuk et al., Citation2013; Li & Wang, Citation2011; Sangkhum et al., Citation2019; Wang et al., Citation2017; Zhang et al., Citation2010; Zheng et al., Citation2015) (Table ). The carboxylation reaction results in the production of glycerol carbonate, which is used as a solvent for plastics and resins, for example, cellulose acetate, nitro-cellulose, and poly-acrylonitrile. Besides, this compound has the adhering property to metal surfaces and resistant to oxidation, hydrolysis, and pressure, and has a lubricating effect. According to the results of the above table, various studies have been carried out to produce glycerol carbonate. Among them, Wang et al. (Citation2017) reported the highest amount of glycerol carbonate production. The Na2SiO3 solid base catalyst at 200°C was a noteworthy example for industrial applications in GC synthesis that illustrated glycerol conversion of 97.7%. This comparison is expressed based on the highest amount of glycerol carbonate production efficiency.
Table 7. Studies on carboxylation reaction for glycerol carbonate preparation.
2.1.9. Reaction of adding nitrate to glycerol
Glycerol can be treated by using nitrating material to form di-nitro-glycerol solution. This solution is converted to glycidyl nitrate by an annular agent from di-nitro-glycerol, which is also polymerized to poly (glycidyl nitrate). Poly (glycidyl nitrate) is known as a high-energy polymer appropriate for utilization in propellants, explosive materials, gas generators and pyrotechnics (Zheng et al., Citation2008). Besides, the glycerol nitrate reaction can produce glycerol carbonate. In this method, glycerol reacts with urea to produce glycerol carbonate (Figure ).
In Ashok et al. (Citation2013), under anaerobic conditions, 3-HP production of glycerol by KpC (Klebsiella pneumonia ΔglpKΔdhaT) resulted in an increase of NADH cell levels and decrease of glycerol consumption. Adding nitrate enables KpC to successfully regenerate NAD+, but the active presence of the enzymes was effective in reducing the carbon flow pathway to produce 3-HP and 1, 3-PDO. A heavy compound of KpCΔglpKΔdhaT, which contained both GlpK and DhaT, ran a large amount of glycerol toward the generation of 3-HP in the presence of nitrate under anaerobic conditions.
Glycerol can be polymerized into poly-glycidyl nitrate using nitrating factors. This polymer has the potential to be used in fire-cracking materials and propulsions. Researches showed that successful production of 3-HP from glycerol required maintaining an appropriate inhibitory balance and optimal enzyme activity related to glycerol metabolism. However, not many researches have been reported on glycerol nitration and therefore more studies need to be done.
2.1.10. Selective oxidation of glycerol
The catalytic conversion of glycerol into high-value products has attracted scientists’ attention. Among various methods, the selective oxidation of glycerol via oxygen molecule to di-hydroxy-acetone, glyceric acid, glyceryl aldehydes, and tartaric acid are challenging in research and industrial applications. Extensive catalysts for the selective oxidation of hydroxyl groups in glycerol have been reported, for example, single metals Au, Pt, and Pd NPs and bimetallic Au–Pt, Au–Pd, Pt–Bi, Pt–Sb and Cu–Pt (Yang et al., Citation2019). Glycerol oxidation consists of four basic steps: Di-hydrogenation of OH- group, Di-hydrogenation of CH group, aldehyde oxidation and C-C bond cleavage. Studies showed that the increased catalytic activity of glycerol oxidation to carboxylic acids (mainly glycyrrhizic acid and Tartronic acid) was possible by polarizing the Pt surface and forming Pt–OH. From a thermodynamic point of view, high-energy molecule oxygen reacted exothermically with organic compounds. Most organic compounds were stable in the vicinity of oxygen due to their high activation energy. Hydroxylated molecules and oxygen were activated on the surface of the solid catalyst and the hydrogen removal reaction was carried out and converted to the carbonyl group. Figure is adapted and reproduced from (Yan et al., Citation2019).
Hydrotalcite catalyst supported by platinum catalyst (Pt/HT) was determined as an extremely active heterogeneous catalyst for the oxidation of glycerol in net water under atmospheric oxygen pressure and at a high glycerol-metal molar ratio. Moreover, the high selectivity of glyceric acid (78%) was attained at 25°C and 1 atm. The Pt/HT catalyst also selectively oxidized the hydroxyl groups 1,2-propylene glycol to obtain carboxylic acid from glycerol (Tsuji et al., Citation2011). Selective oxidation of glycerol requires a temperature of 60-80°C. Generally, platinum and palladium are highly active catalysts for oxidation of glycerol. Di-hydroxy-acetone is obtained by aerobic oxidation of glycerol in the vicinity of Pt-Bi-C and in high acidic ambiance. More research is needed to attain comprehensive results.
2.2 Important compounds derived from glycerol
A list of important compounds that can be synthesized from glycerol is shown in Table .
Table 8. Important compounds derived from glycerol.
2.3 Effects of modified glycerin on engine performance and emissions
After having described methods of producing valuable substances from glycerol, the effects of the utilization of these materials as diesel fuel additives in diesel engines are investigated. The purpose of this research is to investigate the consequence of these additives on engine performance and emissions, which are identified by examining the results of reported studies. Clearly, an additive that can improve engine performance while decreasing emissions is paramount. In Table , the role of these additives on engine performance and emissions is investigated.
Table 9. Effects of additives from glycerin on engine performance and emission.
3. Discussion about effects of additives on the performance and emissions of diesel engines
The use of glycerin in the production of a valuable additive is very economical due to the use of 10% of the production of the transesterification process material besides the 90% biodiesel. But some parameters can influence the economic condition. Therefore, depending on the type of production equipment and available primary resources for biodiesel production, the economic parameter is slowly changing, but in general, the use of glycerin as waste material and its conversion into a suitable and valuable additive to reduce diesel engine pollution and improve engine performance is very important. It is observed that most research has been performed on acetone, isopropanol, propanol, diethyl ether and poly-oxy-methylene dimethyl ethers. In the following, the effects of these additives are discussed. Adding acetone to diesel and biodiesel fuel and using it in diesel engine reduces the emissions and most NOx reduction occurs. Therefore, adding this substance can solve one of the problems (i.e. the production of high NOx) caused by the use of biodiesel. The main reason for this decrease is due to the low heat value of acetone, which reduces heat and therefore reduces NOx production. On the other hand, the addition of this substance reduces the soot, which can be due to the presence of oxygen in the acetone combination. Therefore, oxidation can reduce soot. Besides, the reduction of CO, PAH (aromatic hydrocarbons) and PM occur. Adding acetone to diesel has a better effect on soot reduction compared to butanol and ethanol. It adds acetone effect on engine performance because it improves braking thermal efficiency. Moreover, adding acetone improves energy efficiency and productivity.
Acetone delays the combustion time and improves the required temperature for combustion, which is due to the endothermic properties of acetone. Therefore, the use of this additive can be effective in providing engine benefits and reducing emissions. Adding isopropanol to diesel and biodiesel fuel and using it in diesel engine reduces CO and THC. However, according to most of the reported research in Table , it increases NOx, which can be one of the major disadvantages of isopropanol. Although a study reported that changing the type of injecting and double injecting could reduce NOx production, NOX increase, especially at full load, is generally greater. The high thermal value of isopropanol, which releases high heat, is the main parameter in increasing NOx production. Another study also reported that using the EGR method could reduce NOx and soot simultaneously. By using isopropanol, most reduction is observed in UBHC and CO emission. Adding isopropanol to the diesel engine increases BSEC. This combination delays combustion and reduces the peak pressure. It also reduces BTE but increases the brake thermal efficiency. Injector penetration results in higher fuel injection than diesel fuel. Therefore, it can be concluded that the use of isopropanol in engines containing EGR due to NOx reduction can be recommended. But compared to acetone, it has a low performance in reducing emissions and engine performance.
Adding propanol to diesel fuel and biodiesel mixture reduces some of the diesel engine emissions. Most studies show that the addition of propanol reduces NOx and soot emissions. Adding this substance reduces the temperature of the exhaust gas (EGT). Lower temperature and lower heat value are the main reasons for the reduction of NOx emissions. However, adding propanol increases some of the emissions such as SOF, THC and CO. Therefore, higher monoxide production can be negative factors for propanol use. The addition of propanol also affects the engine performance. Its addition reduces the combustion time. At low injection pressure, the BSFC value also decreases. Important and effective factors in the addition of propanol are the decrease in viscosity and density. Besides, cloud point improves with the addition of this material. On the other hand, adding propanol reduces the noise of the diesel engine. Adding diethyl ether to biodiesel and diesel fuel reduces some of the emission parameters. In general, THC and CO engines emissions increase with blending this material in diesel fuel. These pollutants are especially increased in EGR engines, due to the reduced inlet oxygen to the combustion chamber. The rate of heat emission is reduced by diethyl ether. Therefore, NOx production is reduced due to the addition of this substance and this decrease has been reported at higher loads. The addition of diethyl ether to blend of diesel fuel and hydrogen increases NOx because hydrogen fuel has a high heat value, which increases temperature and NOx emission. Besides, the use of diethyl ether in fuel blend up to 10% improves the engine performance. The addition of diethyl ether has better engine performance in comparison to that of butanol. The addition of diethyl ether increases BSFC and thermal efficiency. Compared to diesel, it has a longer combustion delay. Cloud point temperature occurs at below 25°C. With the addition of diethyl ether, it has been reported an increase in BTE, which is due to the high thermal efficiency of this material. However, this action reduces BSEC. Adding poly-oxy- methylene dimethyl ethers reduces the emission of soot, CO, and HC. The effect of adding this substance to diesel fuel is much more severe in reducing HC, which is due to its high oxygen concentration. Yet, adding it does not have much effect on NOx. If EGR is used, NOx emissions are high due to the increase in inlet air temperature to the combustion chamber. Therefore, the disadvantages of using this additive are its non-efficiency in reducing NOX. Adding poly-oxy methylene dimethyl ethers improves engine efficiency. This additive improves the combustion process due to the high oxygen concentration in it, and also increases the brake thermal efficiency. Adding this material also increases the cetane number of fuels. Therefore, it is found that this additive performs very well on the diesel engine combustion process.
4. Conclusion
The global production of glycerol is increasing significantly and leading to its economic evaluation in the market. Since the generation of new glycerol is quicker than the market demand, the value of glycerol decreases significantly due to overproduction. The production capacity and demand for biodiesel fuel have been increasing in recent years and consequently, global production of glycerol is on the increase. It has little direct utilization and its fuel value is low. Glycerol is a suitable molecule for the synthesis of various products, for example, surfactants, emulsifiers, solvents, lubricants, cosmetics, etc. Besides, glycerol is non-toxic, edible, and biodegradable and has a very different structure that enables the synthesis of a wide array of valuable derivatives using different methods. Among various methods of producing valuable materials from glycerol, the choice of the best method depends on criteria such as the desired product, equipment required and other economic and environmental parameters. Therefore, depending on these parameters, the required method to produce the desired product is chosen. The methods of etherification, carboxylation, and glycerol carbonate preparation have been more widely used, respectively. This is due to being more industrial and producing different products. The use of derived additives from glycerin (with a variety of ways) shows that it plays a role in engine performance and emission parameters. For this reason, different studies on these materials should be carried out under different engine operating conditions. In most study cases, the use of these additives has reduced several emissions parameters, which proved their importance. The presence of hydroxyl groups can reduce NOx. Using glycerin additives to improve the properties of biodiesel can be important. Therefore, they must be added to the base fuel under different engine conditions and in different amounts. Among these additives, acetone is one of the most important additives in the blend of diesel and biodiesel fuel due to the maximum reduction of emissions. Diethyl ether additive is also a useful additive due to its increased thermal efficiency and BSFC. Hence, wide experimental investigations will be needed to obtain an appropriate additive.
Acknowledgement
Open Access Funding by the Publication Fund of the TU Dresden.
Disclosure statement
No potential conflict of interest was reported by the author(s).
References
- Ahmad, T., Danish, M., Kale, P., Geremew, B., Adeloju, S. B., Nizami, M., & Ayoub, M. (2019). Optimization of process variables for biodiesel production by transesterification of flaxseed oil and produced biodiesel characterizations. Renewable Energy, 139, 1272–1280. https://doi.org/https://doi.org/10.1016/j.renene.2019.03.036
- Akbari, R., Ajabshirchi, Y., & Haghighat Shoar, F. (2020). Environmental analysis and evaluation of energy consumption using hybrid system for industrial unit in Mianeh city. Modares Mechanical Engineering, 20(9), 2363–2375. https://doi.org/https://doi.org/10.1001/1.10275940.1399.20.9.8.5
- Akbarian, E., & Najafi, B. (2019). A novel fuel containing glycerol triacetate additive, biodiesel and diesel blends to improve dual-fuelled diesel engines performance and exhaust emissions. Fuel, 236, 666–676. https://doi.org/https://doi.org/10.1016/j.fuel.2018.08.142
- Algayyim, S. J. M., Wandel, A. P., Yusaf, T., Al-Lwayzy, S., & Hamawand, I. (2018). Impact of butanol-acetone mixture as a fuel additive on diesel engine performance and emissions. Fuel, 227, 118–126. https://doi.org/https://doi.org/10.1016/j.fuel.2018.04.091
- Algayyim, S. J. M., Wandel, A. P., Yusaf, T., & Hamawand, I. (2017). The impact of n-butanol and iso-butanol as components of butanol-acetone (BA) mixture-diesel blend on spray, combustion characteristics, engine performance and emission in direct injection diesel engine. Energy, 140, 1074–1086. https://doi.org/https://doi.org/10.1016/j.energy.2017.09.044
- Algoufi, Y. T., Kabir, G., & Hameed, B. H. (2016). Synthesis of glycerol carbonate from biodiesel by-product glycerol over calcined dolomite. Journal of the Taiwan Institute of Chemical Engineers, 1–9. https://doi.org/https://doi.org/10.1016/j.jtice.2016.10.039.
- Alptekin, E. (2017). Evaluation of ethanol and isopropanol as additives with diesel fuel in a CRDI diesel engine. Fuel, 161–172. https://doi.org/https://doi.org/10.1016/j.fuel.2017.05.076
- Alvarez, M. G., Plíšková, M., Segarra, A. M., Medina, F., & Figueras, F. (2012). Synthesis of glycerol carbonates by transesterification of glycerol in a continuous system using supported hydrotalcites as catalysts. Applied Catalysis B: Environmental, 113–114, 212–220. https://doi.org/https://doi.org/10.1016/j.apcatb.2011.11.040
- Ambata, I., Srivastava, V., & Sillanpää, M. (2018). Recent advancement in biodiesel production methodologies using various feedstock: A review. Renewable and Sustainable Energy Reviews, 90, 356–369. https://doi.org/https://doi.org/10.1016/j.rser.2018.03.069
- Ampatzidis, C. D., Varka, E. M., & Karapantsios, T. D. (2014). Interfacial activity of amino acid-based glycerol ether surfactants and their performance in stabilizing O/W cosmetic emulsions. Colloids and Surfaces A: Physicochemical and Engineering Aspects, 460, 176–183. https://doi.org/https://doi.org/10.1016/j.colsurfa.2014.02.033
- Ancillotti, F., & Fattore, V. (1998). Oxygenate fuels: Market expansion and catalytic aspect of synthesis. Fuel Processing Technology, 57(3), 163–194. https://doi.org/https://doi.org/10.1016/S0378-3820(98)00081-2
- Anger, S., Trimis, D., Stelzner, B., Makhynya, Y., & Peil, S. (2011). Development of a porous burner unit for glycerine utilization from biodiesel production by supercritical water reforming. International Journal of Hydrogen Energy, 36(13), 7877–7883. https://doi.org/https://doi.org/10.1016/j.ijhydene.2011.01.058
- Ashok, S., Raj, S. M., Ko, Y., Sankaranarayanan, M., Zhou, S., Kumar, V., & Park, S. (2013). Effect of puuC overexpression and nitrate addition on glycerol metabolism and anaerobic3-hydroxypropionic acid production in recombinant Klebsiella pneumoniae ΔglpKΔdhaT. Metabolic Engineering, 15, 10–24. https://doi.org/https://doi.org/10.1016/j.ymben.2012.09.004
- Atabani, A. E., Mahlia, T. M. I., Anjum Badruddin, I., Masjuki, H. H., Chong, W. T., & Lee, K. T. (2013). Investigation of physical and chemical properties of potential edible and non-edible feedstocks for biodiesel production, a comparative analysis. Renewable and Sustainable Energy Reviews, 21, 749–755. https://doi.org/https://doi.org/10.1016/j.rser.2013.01.027
- Atmanli, A. (2016). Comparative analyses of diesel–waste oil biodiesel and propanol, n-butanol or 1-pentanol blends in a diesel engine. Fuel, 209–215. https://doi.org/https://doi.org/10.1016/j.fuel.2016.02.076
- Atmanli, A. (2020). Experimental comparison of biodiesel production performance of two different microalgae. Fuel, 278, Article 118311. https://doi.org/https://doi.org/10.1016/j.fuel.2020.118311
- Attia, A. M., Nour, M., & Nada, S. A. (2018). Study of Egyptian castor biodiesel-diesel fuel properties and diesel engine performance for a wide range of blending ratios and operating conditions for the sake of the optimal blending ratio. Energy Conversion and Management, 174, 364–377. https://doi.org/https://doi.org/10.1016/j.enconman.2018.08.016
- Auerbach, S. S., Mahler, J., Travlos, G. S., & Irwin, R. D. (2008). A comparative 90-day toxicity study of allyl acetate, allyl alcohol and acrolein. Toxicology, 253(1–3), 79–88. https://doi.org/https://doi.org/10.1016/j.tox.2008.08.014
- Ayoub, M., Khayoon, M. S., & Abdullah, A. Z. (2012). Synthesis of oxygenated fuel additives via the solventless etherification of glycerol. Bioresource Technology, 112, 308–312. https://doi.org/https://doi.org/10.1016/j.biortech.2012.02.103
- Barro, C., Parravicini, M., Boulouchos, K., & Liati, A. (2018). Neat polyoxymethylene dimethyl ether in a diesel engine; part 2: Exhaust emission analysis. Fuel, 234, 1414–1421. https://doi.org/https://doi.org/10.1016/j.fuel.2018.07.108
- Beatrice, C., Di Blasio, G., Guido, C., Cannilla, C., Bonura, G., & Frusteri, F. (2014). Mixture of glycerol ethers as diesel bio-derivable oxy-fuel: Impact on combustion and emissions of an automotive engine combustion system. Applied Energy, 132, 236–247. https://doi.org/https://doi.org/10.1016/j.apenergy.2014.07.006
- Behr, A., & Obendorf, L. (2002). Development of a process for the acid-catalyzed etherification of glycerine and isobutene forming glycerine tertiary butyl ethers. Engineering in Life Sciences, 2(7), 185–189. https://doi.org/https://doi.org/10.1002/1618-2863(20020709)2:7<185::AID-ELSC185>3.0.CO;2-4
- Benajes, J., Novella, R., Pastor, J. M., Hernández-López, A., & Kokjohn, S. L. (2018). Computational optimization of the combustion system of a heavy duty direct injection diesel engine operating with dimethyl-ether. Fuel, 218, 127–139. https://doi.org/https://doi.org/10.1016/j.fuel.2018.01.020
- Bencheikh, K., Atabani, A. E., Shobana, S., Mohammed, M. N., Uğuz, G., Arpa, O., Kumar, G., Ayanoğlu, A., & Bokhari, A. (2019). Fuels properties, characterizations and engine and emission performance analyses of ternary waste cooking oil biodiesel–diesel–propanol blends. Sustainable Energy Technologies and Assessments, 35, 321–334. https://doi.org/https://doi.org/10.1016/j.seta.2019.08.007
- Bookong, P., Ruchirawat, S., & Boonyarattanakalin, S. (2015). Optimization of microwave-assisted. Etherification of glycerol to polyglycerols by sodium carbonate as catalyst. Chemical Engineering Journal. https://doi.org/https://doi.org/10.1016/j.cej.2015.04.033
- Boon-Anuwat, N. N., Kiatkittipong, W., Aiouache, F., & Assabumrungrat, S. (2015). Process design of continuous biodiesel production by reactive distillation: Comparison between homogeneous and heterogeneous catalysts. Chemical Engineering and Processing: Process Intensification, 92, 33–44. https://doi.org/https://doi.org/10.1016/j.cep.2015.03.025
- Bórawski, P., Bełdycka-Bórawska, A., Szymańska, E. J., Jankowski, K. J., Dubis, B., & Dunn, J. W. (2019). Development of renewable energy sources market and biofuels in the European Union. Journal of Cleaner Production, 228, 467–484. https://doi.org/https://doi.org/10.1016/j.jclepro.2019.04.242
- Bozkurt, O. D., Baglar, N., Celebi, S., & Uzun, A. (2019). Assessment of acid strength in sodium-exchanged resin catalysts: Consequences on glycerol etherification with isobutene in batch and flow reactors. Molecular Catalysis, 466, 1–12. https://doi.org/https://doi.org/10.1016/j.mcat.2018.12.027
- Bozkurt, O. D., Yılmaz, F., Bağlar, N., Çelebi, S., & Uzun, A. (2019). Compatibility of di-and tri-tert-butyl glycerol ethers with gasoline. Fuel, 255, Article 115767. https://doi.org/https://doi.org/10.1016/j.fuel.2019.115767
- Caetano, N. S., Silva, V. F., & Mata, T. M. (2012). Valorization of coffee grounds for biodiesel production. Chemical Engineering Transactions, 26.
- Cannilla, C., Bonura, G., Frusteri, L., & Frusteri, F. (2015). Batch reactor coupled with water permselective membrane: Study of glycerol etherification reaction with butanol. Chemical Engineering Journal, 282, 187–193. https://doi.org/https://doi.org/10.1016/j.cej.2015.03.013
- Carrero, A., & Pérez, Á. (2012). Advances in biodiesel quality control, characterisation and standards development. In Advances in biodiesel production (pp. 91–130). Woodhead Publishing, 2012.
- Changa, Y.-C., Lee, W.-J., Lin, S.-L., & Wang, L.-C. (2013). Green energy: Water-containing acetone–butanol–ethanol diesel blends fueled in diesel engines. Applied Energy, 109, 182–191. https://doi.org/https://doi.org/10.1016/j.apenergy.2013.03.086
- Chang, Y.-C., Lee, W.-J., Wu, T. S., Wu, C.-Y., & Chen, S.-J. (2013). Use of water containing acetone–butanol–ethanol for NOx-PM (nitrogen oxide-particulate matter) trade-off in the diesel engine fueled with biodiesel. Energy, 64, 678–687. https://doi.org/https://doi.org/10.1016/j.energy.2013.10.077
- Christoph, R., Schmidt, B., Ssteinberner, U., Dilla, W., & Karinen, R. (2000). Glycerol, Ullmann's encyclopedia of industrial chemistry. Wiley and Sons.
- Das, B., & Mohanty, K. (2019). A green and facile production of catalysts from waste red mud for the one-pot synthesis of glycerol carbonate from glycerol. Journal of Environmental Chemical Engineering, 7(1), Article 102888. https://doi.org/https://doi.org/10.1016/j.jece.2019.102888
- Dasari, M., Kiatsimkul, P.-P., Sutterlin, W. R., & Suppes, G. J. (2005). Low pressure hydrogenolysis of glycerol to propylene glycol. Applied Catalysis A: General, 281(1–2), 225–231. https://doi.org/https://doi.org/10.1016/j.apcata.2004.11.033
- Decolatti, H. P., Dalla Costa, B. O., & Querini, C. A. (2014). Dehydration of glycerol to acrolein using H-ZSM5 zeolite modified by alkali treatment with NaOH. Microporous and Mesoporous Materials. https://doi.org/https://doi.org/10.1016/j.micromeso.2014.11.014
- Dhanasekaran, R., Ganesan, S., Rajesh Kumar, B., & Saravanan, S. (2018). Utilization of waste cooking oil in a light-duty DI diesel engine for cleaner emissions using bio-derived propanol. Fuel, 832–837. https://doi.org/https://doi.org/10.1016/j.fuel.2018.08.093
- Domínguez-Barroso, V., Herrera, C., Larrubia, M. Á., & Alemany, L. J. (2019). Coupling of glycerol-APR and in situ hydrodeoxygenation of fatty acid to produce hydrocarbons. Fuel Processing Technology, 190, 21–28. https://doi.org/https://doi.org/10.1016/j.fuproc.2019.03.011
- dos Santos, M. B., Andrade, H. M. C., & Mascarenhas, A. J. S. (2019). Oxidative dehydration of glycerol over alternative H,Fe-MCM-22 catalysts: Sustainable production of acrylic acid. Microporous and Mesoporous Materials. https://doi.org/https://doi.org/10.1016/j.micromeso.2019.01.016
- Dumitrescu, C. E., Mueller, C. J., & Kurtz, E. (2015). Investigation of a tripropylene-glycol monomethyl ether and diesel blend for soot-free combustion in an optical direct-injection diesel engine. Applied Thermal Engineering, 101, 639–646. https://doi.org/https://doi.org/10.1016/j.applthermaleng.2015.12.068
- Elhaj, E., Wang, H., & Gu, Y. (2019). Functionalized quaternary ammonium salt ionic liquids (FQAILs) as an economic and efficient catalyst for synthesis of glycerol carbonate from glycerol and dimethyl carbonate. Molecular Catalysis, 468, 19–28. https://doi.org/https://doi.org/10.1016/j.mcat.2019.02.005
- Estevez, R., López, M. I., Jiménez-Sanchidrián, C., Luna, D., Romero-Salguero, F. J., & Bautista, F. M. (2016). Etherification of glycerol with tert-butyl alcohol over sulfonated hybrid silicas. Applied Catalysis A: General. https://doi.org/https://doi.org/10.1016/j.apcata.2016.08.019
- Favier, I., Pla, D., & Gómez, M. (2018). Metal-based nanoparticles dispersed in glycerol: An efficient approach for catalysis. Catalysis Today, 310, 98–106. https://doi.org/https://doi.org/10.1016/j.cattod.2017.06.026
- Freitas, I. C., Manfro, R. L., & Souza, M. M. (2018). Hydrogenolysis of glycerol to propylene glycol in continuous system without hydrogen addition over Cu-Ni catalysts. Applied Catalysis B: Environmental. https://doi.org/https://doi.org/10.1016/j.apcatb.2017.08.030
- Frusteri, F., Arena, F., Bonura, G., Cannilla, C., Spadaro, L., & Di Blasi, O. (2009). Catalytic etherification of glycerol by tert-butyl alcohol to produce oxygenated additives for diesel fuel. Applied Catalysis A: General, 367(1–2), 77–83. https://doi.org/https://doi.org/10.1016/j.apcata.2009.07.037
- Fu, J., Shu, J., Zhao, Z., Liu, J., & Zhou, F. (2017). Comparative analysis of soot formation processes of diesel and ABE (acetone-butanol-ethanol) based on CFD coupling with phenomenological soot model. Fuel, 203, 380–392. https://doi.org/https://doi.org/10.1016/j.fuel.2017.04.108
- Gao, X., Zhu, S., & Li, Y. (2015). Graphene oxide as a facile solid acid catalyst for the production of bioadditives from glycerol esterification. Catalysis Communications, 62, 48–51. https://doi.org/https://doi.org/10.1016/j.catcom.2015.01.007
- García-Sancho, C., Cecilia, J. A., Mérida-Robles, J. M., González, J. S., Moreno-Tost, R., Infantes-Molina, A., & Maireles-Torres, P. (2017). Effect of the treatment with H3PO4 on the catalytic activity of Nb2O5 supported on Zrdoped mesoporous silica catalyst. Case study: Glycerol dehydration. Applied Catalysis B, Environmental. https://doi.org/https://doi.org/10.1016/j.apcatb
- Garcia, A., Monsalve-Serrano, J., Villalta, D., Zubel, M., & Pischinger, S. (2018). Potential of 1-octanol and di-n-butyl ether (DNBE) to improve the performance and reduce the emissions of a direct injected compression ignition diesel engine. Energy Conversion and Management, 177, 563–571. https://doi.org/https://doi.org/10.1016/j.enconman.2018.10.009
- Gervais, M., Brocas, A.-L., Cendejas, G., Deffieux, A., & Carlotti, S. (2010). Synthesis of linear high molar mass glycidol-based polymers by monomer-activated anionic polymerization. Macromolecules, 43(4), 1778–1784. https://doi.org/https://doi.org/10.1021/ma902286a
- Ghazanfari, J., Najafi, B., Faizollahzadeh Ardabili, S., Shamshirband, S., & Jin, Z. (2017). Limiting factors for the use of palm oil biodiesel in a diesel engine in the context of the ASTM standard. Cogent Engineering, 4(1), Article 1411221. https://doi.org/https://doi.org/10.1080/23311916.2017.1411221
- Gheybi, H., Sattari, S., Bodaghi, A., Soleimani, K., Dadkhah, A., & Adeli, M. (2018). Polyglycerols. In Engineering of biomaterials for drug delivery systems (pp. 103–171). Woodhead Publishing.
- Go, A. W., Sutanto, S., Ong, L. K., Tran-Nguyen, P. L., Ismadji, S., & Ju, Y.-H. (2016). Developments in in-situ (trans) esterification for biodiesel production: A critical review. Renewable and Sustainable Energy Reviews, 60, 284–305. https://doi.org/https://doi.org/10.1016/j.rser.2016.01.070
- Gómez-Cuenca, F., Gómez-Marín, M., & Folgueras-Díaz, M. (2011). Effects of ethylene glycol ethers on diesel fuel properties and emissions in a diesel engine. Energy Conversion and Management, 3027–3033. https://doi.org/https://doi.org/10.1016/j.enconman.2011.04.017
- Gómez-Cuenca, F., Gómez-Marín, M., & Folgueras-Díaz, M. B. (2013). The influence of propylene glycol ethers on base diesel properties and emissions from a diesel engine. Energy Conversion and Management, 741–747. https://doi.org/https://doi.org/10.1016/j.enconman.2013.07.012
- Goncalves, M., Castro, C. S., Oliveira, L. C., & Carvalho, W. A. (2015). Green acid catalyst obtained from industrial wastes for glycerol etherification. Fuel Processing Technology, 138, 695–703. https://doi.org/https://doi.org/10.1016/j.fuproc.2015.07.010
- Gonzalez-Arellano, C., Grau-Atienza, A., Serrano, E., Romero, A. A., Garcia-Martinez, J., & Luque, R. (2015). The role of mesoporosity and Si/Al ratio in the catalytic etherification of glycerol with benzyl alcohol using ZSM-5 zeolites. Journal of Molecular Catalysis A: Chemical, 406, 40–45. https://doi.org/https://doi.org/10.1016/j.molcata.2015.05.011
- Haghighat Shoar, F., & Najafi, B. (2021). Investigating energy efficiency, economic performance, and emission of the diesel engine using natural gas with a combination of biodiesel B5 and B20 in diesel fuel. Modares Mechanical Engineering, 21(3), 143–161. https://doi.org/https://doi.org/10.1001/1.10275940.1399.21.3.18.6
- Han, K., Pang, B., Ma, X., Chen, H., Song, G., & Ni, Z. (2017). An experimental study of the burning characteristics of acetone–butanol–ethanol and diesel blend droplets. Energy, 139, 853–861. https://doi.org/https://doi.org/10.1016/j.energy.2017.08.037
- Hill, J., Nelson, E., Tilman, D., Polasky, S., & Tiffany, D. (2006). Environmental, economic, and energetic costs and benefits of biodiesel and ethanol biofuels. Proceedings of the National Academy of Sciences, 103(30), 11206–11210. https://doi.org/https://doi.org/10.1073/pnas.0604600103
- Hongwei, S. W., Yang, H., Hu, J., Shen, D., Zhang, H., & Xiao, R. (2017). The miscibility of hydrogenated bio-oil with diesel and its applicability test in diesel engine: A surrogate (ethylene glycol) study. Fuel Processing Technology, 161, 162–168. https://doi.org/https://doi.org/10.1016/j.fuproc.2017.03.022
- Hosseinzadeh-Bandbafha, H., Tabatabaei, M., Aghbashlo, M., Khanali, M., & Demirbas, A. (2018). A comprehensive review on the environmental impacts of diesel/biodiesel additives. Energy Conversion and Management, 174, 579–614. https://doi.org/https://doi.org/10.1016/j.enconman.2018.08.050
- Hu, K., Wang, H., Liu, Y., & Yang, C. (2015). KNO3/CaO as cost-effective heterogeneous catalyst for the synthesis 3 of glycerol carbonate from glycerol and dimethyl carbonate. Journal of Industrial and Engineering Chemistry, 28, 334–343. https://doi.org/https://doi.org/10.1016/j.jiec.2015.03.012
- Ibrahim, A. (2016). Investigating the effect of using diethyl ether as a fuel additive on diesel engine performance and combustion. Applied Thermal Engineering, 853–862. https://doi.org/https://doi.org/10.1016/j.applthermaleng.2016.07.061
- Ibrahim, A. (2018). An experimental study on using diethyl ether in a diesel engine operated with diesel-biodiesel fuel blend. Engineering Science and Technology, an International Journal, 1024–1033. https://doi.org/https://doi.org/10.1016/j.jestch.2018.07.004
- Imtenan, S., Masjuki, H. H., Varman, M., Rizwanul Fattah, I. M., Sajjad, H., & Arbab, M. I. (2015). Effect of n-butanol and diethyl ether as oxygenated additives on combustion–emission-performance characteristics of a multiple cylinder diesel engine fuelled with diesel–Jatropha biodiesel blend. Energy Conversion and Management, 94, 84–94. https://doi.org/https://doi.org/10.1016/j.enconman.2015.01.047
- Ishak, Z. I., Sairi, N. A., Alias, Y., Aroua, M. K. T., & Yusoff, R. (2016). Production of glycerol carbonate from glycerol with aid of ionic liquid as catalyst. Chemical Engineering Journal. https://doi.org/https://doi.org/10.1016/j.cej.2016.03.104
- Izquierdo, J. F., Iniesta, E., Outón, P. R., & Izquierdo, M. (2017). Experimental study of glycerol etherification with C5 olefins to produce biodiesel additives. Fuel Processing Technology, 160, 1–7. https://doi.org/https://doi.org/10.1016/j.fuproc.2017.02.011
- Izquierdo, J. F., Montiel, M., Palés, I., Outón, P. R., Galán, M., Jutglar, L., Villarrubia, M., Izquierdo, M., Hermo, M. P., & Ariza, X. (2012). Fuel additives from glycerol etherification with light olefins: State of the art. Renewable and Sustainable Energy Reviews, 16(9), 6717–6724. https://doi.org/https://doi.org/10.1016/j.rser.2012.08.005
- Jamróz-Piegza, M., Utrata-Wesołek, A., Trzebicka, B., & Dworak, A. (2006). Hydrophobic modification of high molar mass polyglycidol to thermosensitive polymers. European Polymer Journal, 42(10), 2497–2506. https://doi.org/https://doi.org/10.1016/j.eurpolymj.2006.04.017
- Jaworski, M. A., Rodríguez Vega, S., Siri, G. J., Casella, M. L., Romero Salvador, A., & Santos López, A. (2015). Glycerol etherification with benzyl alcohol over Sulfated Zirconia catalysts. Applied Catalysis A: General, 505, 36–43. https://doi.org/https://doi.org/10.1016/j.apcata.2015.04.027
- Jeevanantham, A. K., Nanthagopal, K., Ashok, B., Al-Muhtaseb, A. H., Thiyagarajan, S., Geo, V. E., Ong, H. C., & Samuel, K. J. (2019). Impact of addition of two ether additives with high speed diesel- Calophyllum inophyllum biodiesel blends on NOx reduction in CI engine. Energy, 185, 39–54. https://doi.org/https://doi.org/10.1016/j.energy.2019.07.013
- Judge, K. (1988). Organisation for Economic Co-operation and Development (OECD), financing and delivering health care: A comparative analysis of OECD countries, social policy studies no. 4, OECD, Paris, 1987. Journal of Social Policy, 17(4), 547–548. https://doi.org/https://doi.org/10.1017/S0047279400017050
- Kakoee, A., & Gharehghani, A. (2019). Comparative study of hydrogen addition effects on the natural-gas/diesel and natural-gas/dimethyl-ether reactivity controlled compression ignition mode of operation. Energy Conversion and Management, 196, 92–104. https://doi.org/https://doi.org/10.1016/j.enconman.2019.05.113
- Karam, A., Villandier, N., Delample, M., Koerkamp, C. K., Douliez, J.-P., Granet, R., Krausz, P., Barrault, J., & Jérôme, F. (2008). Rational design of sugar-based-surfactant combined catalysts for promoting glycerol as a solvent. Chemistry – A European Journal, 14(33), 10196–10200. https://doi.org/https://doi.org/10.1002/chem.200801495
- Karimi, P., Najafi, B., Ardabili, S. F., Mesri-Gundoshmian, T., Ariyanfar, L., & Haghighatshoar, F. (2020). Ethyl ester production from Iranian bitter almond (BAO) oil to improve the performance and emissions of OM457 diesel engine. Renewable Energy Focus, 33, 16–22. https://doi.org/https://doi.org/10.1016/j.ref.2020.02.001
- Karimmaslak, H., Najafi, B., Band, S. S., Ardabili, S., Haghighat-Shoar, F., & Mosavi, A. (2021). Optimization of performance and emission of compression ignition engine fueled with propylene glycol and biodiesel–diesel blends using artificial intelligence method of ANN-GA-RSM. Engineering Applications of Computational Fluid Mechanics, 15(1), 413–425. https://doi.org/https://doi.org/10.1080/19942060.2021.1880970
- Karmaker, A. K., Rahman, M. M., Hossain, M. A., & Ahmed, M. R. (2019). Exploration and corrective measures of greenhouse gas emission from fossil fuel power stations for Bangladesh. Journal of Cleaner Production, 244, 118645. https://doi.org/https://doi.org/10.1016/j.jclepro.2019.118645
- Katryniok, B., Paul, S., Capron, M., & Dumeignil, F. (2009). Towards the sustainable production of acrolein by glycerol dehydration. ChemSusChem: Chemistry & Sustainability Energy & Materials, 2(8), 719–730. https://doi.org/https://doi.org/10.1002/cssc.200900134
- Kiatkittipong, W., Intaracharoen, P., Laosiripojana, N., Chaisuk, C., Praserthdam, P., & Assabumrungrat, S. (2011). Glycerol ethers synthesis from glycerol etherification with tert-butyl alcohol in reactive distillation. Computers and Chemical Engineering, 35(10), 2034–2043. https://doi.org/https://doi.org/10.1016/j.compchemeng.2011.01.016
- Kim, S. C., Kim, Y. H., Lee, H., Yoon, D. Y., & Song, B. K. (2007). Lipase-catalyzed synthesis of glycerol carbonate from renewable glycerol and dimethyl carbonate through transesterification. Journal of Molecular Catalysis B: Enzymatic, 49(1–4), 75–78. https://doi.org/https://doi.org/10.1016/j.molcatb.2007.08.007
- Klein, B. C., Bonomi, A., & Maciel Filho, R. (2018). Integration of microalgae production with industrial biofuel facilities: A critical review. Renewable and Sustainable Energy Reviews, 82, 1376–1392. https://doi.org/https://doi.org/10.1016/j.rser.2017.04.063
- Klepacova, K., Mravec, D., Kaszonyi, A., & Bajus, M. (2007). Etherification of glycerol and ethylene glycol by isobutylene. Applied Catalysis A: General, 328(1), 1–13. https://doi.org/https://doi.org/10.1016/j.apcata.2007.03.031
- Knothe, G. (2006). Analyzing biodiesel: Standards and other methods. Journal of the American Oil Chemists’ Society, 83(10), 823–833. https://doi.org/https://doi.org/10.1007/s11746-006-5033-y
- Krishnamoorthi, M., & Malayalamurthi, R. (2017a). Availability analysis, performance, combustion and emission behavior of bael oil - diesel - diethyl ether blends in a variable compression ratio diesel engine. Renewable Energy, 119, 235–252. https://doi.org/https://doi.org/10.1016/j.renene.2017.12.015
- Krishnamoorthi, M., & Malayalamurthi, R. (2017b). Experimental investigation on performance, emission behavior and exergy analysis of a variable compression ratio engine fueled with diesel-aegle marmelos oil-diethyl ether blends. Energy, 128, 312–328. https://doi.org/https://doi.org/10.1016/j.energy.2017.04.038
- Krishnamoorthi, M., Malayalamurthi, R., & Sakthivel, R. (2019). Optimization of compression ignition engine fueled with diesel – chaulmoogra oil – diethyl ether blend with engine parameters and exhaust gas recirculation. Renewable Energy, 579–602. https://doi.org/https://doi.org/10.1016/j.renene.2018.11.062
- Lago, C. D., Decolatti, H. P., Tonutti, L. G., Dalla Costa, B. O., & Querini, C. A. (2018). Gas phase glycerol dehydration over H-ZSM-5 zeolite modified by alkaline treatment with Na2CO3. Journal of Catalysis, 366, 16–27. https://doi.org/https://doi.org/10.1016/j.jcat.2018.07.036
- Lee, T. H., Li, G., & Lee, T. (2019). Effects of isopropanol-butanol-ethanol and diesel fuel blends on combustion characteristics in a constant volume chamber. Fuel, 254, 115613. https://doi.org/https://doi.org/10.1016/j.fuel.2019.06.021
- Lemos, C. O. T., Rade, L. L., Barrozo, M. A. d. S., Cardozo-Filho, L., & Hori, C. E. (2018). Study of glycerol etherification with ethanol in fixed bed reactor under high pressure. Fuel Processing Technology, 178, 1–6. https://doi.org/https://doi.org/10.1016/j.fuproc.2018.05.015
- Lertlukkanasuk, N., Phiyanalinmat, S., Kiatkittipong, W., Arpornwichanop, A., Aiouache, F., & Assabumrungrat, S. (2013). Reactive distillation for synthesis of glycerol carbonate via glycerolysis of urea. Chemical Engineering and Processing: Process Intensification, 70, 103–109. https://doi.org/https://doi.org/10.1016/j.cep.2013.05.001
- Lewis, P., Frey, H. C., & Rasdorf, W. (2009). Development and use of emissions inventories for construction vehicles. Transportation Research Record, 2123(1), 46–53. https://doi.org/https://doi.org/10.3141/2123-06
- Li, G., Lee, T. H., Liu, Z., Lee, C. F., & Zhang, C. (2019). Effects of injection strategies on combustion and emission characteristics of a common-rail diesel engine fueled with isopropanol-butanol-ethanol and diesel blends. Renewable Energy, 130, 677–686. https://doi.org/https://doi.org/10.1016/j.renene.2018.06.099
- Li, G., Liu, Z., Lee, T. H., Lee, C. F., & Zhang, C. (2018). Effects of dilute gas on combustion and emission characteristics of a common-rail diesel engine fueled with isopropanol-butanol-ethanol and diesel blends. Energy Conversion and Management, 373–381. https://doi.org/https://doi.org/10.1016/j.enconman.2018.03.073
- Li, J., & Wang, T. (2011). Chemical equilibrium of glycerol carbonate synthesis from glycerol. The Journal of Chemical Thermodynamics, 43(5), 731–736. https://doi.org/https://doi.org/10.1016/j.jct.2010.12.013
- Li, X., & Zhang, Y. (2016). Xidative dehydration of glycerol to acrylic acid over vanadium-substituted cesium salts of keggin-type heteropolyacids. ACS Catalysis, 6(5), 2785–2791. https://doi.org/https://doi.org/10.1021/acscatal.6b00213
- Liu, J., Daoutidis, P., & Yang, B. (2016). Process design and optimization for etherification of glycerol with isobutene. Chemical Engineering Science, 144, 326–335. https://doi.org/https://doi.org/10.1016/j.ces.2016.01.055
- Liu, J., Sun, P., Huang, H., Meng, J., & Yao, X. (2017). Experimental investigation on performance, combustion and emission characteristics of a common-rail diesel engine fueled with polyoxymethylene dimethyl ethers-diesel blends. Applied Energy, 202, 527–536. https://doi.org/https://doi.org/10.1016/j.apenergy.2017.05.166
- Liu, H., Wang, Z., Wang, J., He, X., Zheng, Y., Tang, Q., & Wang, J. (2015). Performance, combustion and emission characteristics of a diesel engine fueled with polyoxymethylene dimethyl ethers (PODE3-4)/diesel blends. Energy, 88, 793–800. https://doi.org/https://doi.org/10.1016/j.energy.2015.05.088
- Liu, H., Wang, Z., Zhang, J., Wang, J., & Shuai, S. (2017). Study on combustion and emission characteristics of polyoxymethylene dimethyl ethers/diesel blends in light-duty and heavy-duty diesel engines. Applied Energy, 185, 1393–1402. https://doi.org/https://doi.org/10.1016/j.apenergy.2015.10.183
- Luo, J., Zhang, Y., Zhang, Q., Liu, J., & Wang, J. (2017). Evaluation of sooting tendency of acetone–butanol–ethanol (ABE) fuels blended with diesel fuel. Fuel, 209, 394–401. https://doi.org/https://doi.org/10.1016/j.fuel.2017.08.019
- Miranda, C., Urresta, J., Cruchade, H., Tran, A., Benghalem, M., Astafan, A., Gaudin, P., Daou, T. J., Ramírez, A., Pouilloux, Y., Sachse, A., & Pinard, L. (2018). Exploring the impact of zeolite porous voids in liquid phase reactions: The case of glycerol etherification by tert-butyl alcohol. Journal of Catalysis, 365, 249–260. https://doi.org/https://doi.org/10.1016/j.jcat.2018.07.009
- Mittelbach, M. (2009). Process technologies for biodiesel production. In W. Soetart & E. J. Vandamme (Eds.), Biofuels (pp. 77–93). John Wiley & Sons.
- Mofijur, M., Rasul, M. G., Hassan, N. M. S., & Nabi, M. N. (2019). Recent development in the production of third generation biodiesel from microalgae. Energy Procedia, 156, 53–58. https://doi.org/https://doi.org/10.1016/j.egypro.2018.11.088
- Monteiro, M. R., Kugelmeier, C. L., Pinheiro, R. S., Batalha, M. O., & da Silva César, A. (2018). Glycerol from biodiesel production: Technological paths for sustainability. Renewable and Sustainable Energy Reviews, 88, 109–122. https://doi.org/https://doi.org/10.1016/j.rser.2018.02.019
- Najafi, B., Faizollahzadeh Ardabili, S., Shamshirband, S., Chau, K.-W., & Rabczuk, T. (2018). Application of ANNs, ANFIS and RSM to estimating and optimizing the parameters that affect the yield and cost of biodiesel production. Engineering Applications of Computational Fluid Mechanics, 12(1), 611–624. https://doi.org/https://doi.org/10.1080/19942060.2018.1502688
- Najafi, B., Haghighatshoar, F., Ardabili, S., Band, S., Chau, K. W., & Mosavi, A. (2021). Effects of low-level hydroxy as a gaseous additive on performance and emission characteristics of a dual fuel diesel engine fueled by diesel/biodiesel blends. Engineering Applications of Computational Fluid Mechanics, 15(1), 236–250. https://doi.org/https://doi.org/10.1080/19942060.2021.1871960
- Narkhede, N., & Patel, A. (2016). Sustainable valorisation of glycerol via acetalization as well as carboxylation reactions over silicotungstates anchored to zeolite hrmbeta. Applied Catalysis A: General. https://doi.org/https://doi.org/10.1016/j.apcata.2016.02.010
- Neves, T. M., Fernandes, J. O., Lião, L. M., da Silva, E. D., da Rosa, C. A., & Mortola, V. B. (2018). Glycerol dehydration over micro- and mesoporous ZSM-5 synthesized from a one-step method. Microporous and Mesoporous Materials, 275, 244–252. https://doi.org/https://doi.org/10.1016/j.micromeso.2018.09.006
- Nomanbhay, S., Hussein, R., & Ong, M. Y. (2018). Sustainability of biodiesel production in Malaysia by production of bio-oil from crude glycerol using microwave pyrolysis: A review. Green Chemistry Letters and Reviews, 11(2), 135–157. https://doi.org/https://doi.org/10.1080/17518253.2018.1444795
- Noor, C. M., Noor, M. M., & Mamat, R. (2018). Biodiesel as alternative fuel for marine diesel engine applications: A review. Renewable and Sustainable Energy Reviews, 94, 127–142. https://doi.org/https://doi.org/10.1016/j.rser.2018.05.031
- Noureddini, H. (2001). Process for producing biodiesel fuel with reduced viscosity and a cloud point below 32°F (US Pat. 6174501).
- Okoye, P. U., Abdullah, A. Z., & Hameed, B. H. (2017). A review on recent developments and progress in the kinetics and deactivation of catalytic acetylation of glycerol – a byproduct of biodiesel. Renewable and Sustainable Energy Reviews, 74, 387–401. https://doi.org/https://doi.org/10.1016/j.rser.2017.02.017
- Okoye, P. U., & Hameed, B. H. (2016). Review on recent progress in catalytic carboxylation and acetylation of glycerol as a byproduct of biodiesel production. Renewable and Sustainable Energy Reviews, 53, 558–574. https://doi.org/https://doi.org/10.1016/j.rser.2015.08.064
- Organisation for Economic Co-operation and Development (OECD), & Food and Agriculture Organization of the United Nations (FAO). (2018). Chapter 8. Fish and seafood. In OECD/FAO agricultural outlook 2018–2027 (pp. 175–190).
- Pan, C., Tan, G.-Y. A., Ge, L., Chen, C.-L., & Wang, J.-Y. (2016). Microbial removal of carboxylic acids from 1,3-propanediol inglycerol anaerobic digestion effluent by PHAs-producing consortium. Biochemical Engineering Journal, 112, 269–276. https://doi.org/https://doi.org/10.1016/j.bej.2016.04.031
- Parveen, R., Ullah, S., Sgarbi, R., & Tremiliosi-Filho, G. (2019). One-pot ligand-free synthesis of gold nanoparticles: The role of glycerol as reducingcum-stabilizing agent. Colloids and Surfaces A: Physicochemical and Engineering Aspects, 565, 162–171. https://doi.org/https://doi.org/10.1016/j.colsurfa.2019.01.005
- Pinzi, S., Redel-Macías, M. D., Leiva-Candia, D. E., Soriano, J. A., & Dorado, M. P. (2017). Influence of ethanol/diesel fuel and propanol/diesel fuel blends over exhaust and noise emissions. Energy Procedia, 142, 849–854. https://doi.org/https://doi.org/10.1016/j.egypro.2017.12.136
- Pirog, T., Sofilkanych, A., Konon, A., Shevchuk, T., & Ivanov, S. (2013). Intensification of surfactants’ synthesis by rhodococcus erythropolis IMV Ac-5017, acinetobacter calcoaceticus IMV B-7241 and nocardia vaccinii K-8 on fried oil and glycerol containing medium. Food and Bioproducts Processing, 91(2), 149–157. https://doi.org/https://doi.org/10.1016/j.fbp.2013.01.001
- Pitt, F. D., Domingos, A. M., & Barros, A. C. (2019). Purification of residual glycerol recovered from biodiesel production. South African Journal of Chemical Engineering, 29, 42–51. https://doi.org/https://doi.org/10.1016/j.sajce.2019.06.001
- Qing, Y., Lu, H., Liu, Y., Liu, C., Liang, B., & Jiang, W. (2017). Production of glycerol carbonate using crude glycerol from biodiesel production with DBU as a catalyst. Chinese Journal of Chemical Engineering, 26, 1912–1919. https://doi.org/https://doi.org/10.1016/j.cjche.2018.01.010
- Rades, N., Achazi, K., & Qiu, M. (2019). Reductively cleavable polymer-drug conjugates based on dendritic polyglycerol sulfate and monomethyl auristatin E as anticancer drugs. Journal of Controlled Release. https://doi.org/https://doi.org/10.1016/j.jconrel.2019.01.035
- Rahmat, N., Abdullah, A. Z., & Mohamed, A. R. (2010). Recent progress on innovative and potential technologies for glycerol transformation into fuel additives: A critical review. Renewable and Sustainable Energy Reviews, 14(3), 987–1000. https://doi.org/https://doi.org/10.1016/j.rser.2009.11.010
- Raj, S. M., Rathnasingh, C., Jo, J. E., & Park, S. (2008). Production of 3-hydroxypropionic acid from glycerol by a novel recombinant Escherichia coli BL21 strain. Process Biochemistry, 43(12), 1440–1446. https://doi.org/https://doi.org/10.1016/j.procbio.2008.04.027
- Roslan, N. A., Abidin, S. Z., Ideris, A., & Vo, D. V. N. (2019). A review on glycerol reforming processes over Ni-based catalyst for hydrogen and syngas productions. International Journal of Hydrogen Energy, 45(36), 18466–18489. https://doi.org/https://doi.org/10.1016/j.ijhydene.2019.08.211
- Roy, M. M., Calder, J., Wang, W., Mangad, A., & Diniz, F. C. M. (2016). Cold start idle emissions from a modern tier-4 turbo-charged diesel engine fueled with diesel-biodiesel, diesel-biodiesel-ethanol, and diesel-biodiesel-diethyl ether blends. Applied Energy, 180, 52–65. https://doi.org/https://doi.org/10.1016/j.apenergy.2016.07.090
- Sangkhum, P., Yanamphorn, J., Wangriya, A., & Ngamcharussrivichai, C. (2019). Ca–Mg–Al ternary mixed oxides derived from layered double hydroxide for selective etherification of glycerol to short-chain polyglycerols. Applied Clay Science, 173, 79–87. https://doi.org/https://doi.org/10.1016/j.clay.2019.03.006
- Sardari, R. R. R., Dishisha, T., Pyo, S.-H., & Hatti-Kaul, R. (2013). Biotransformation of glycerol to 3-hydroxypropionaldehyde: Improved production by in situ complexation with bisulfite in a fed-batch mode and separation on anion exchanger. Journal of Biotechnology, 168(4), 534–542. https://doi.org/https://doi.org/10.1016/j.jbiotec.2013.09.009
- Sardari, R. R. R., Dishisha, T., Pyo, S.-H., & Hatti-Kaul, R. (2014). Semicarbazide-functionalized resin as a new scavenger for in siturecovery of 3-hydroxypropionaldehyde during biotransformation of glycerol by Lactobacillus reuteri. Journal of Biotechnology, 192, 223–230. https://doi.org/https://doi.org/10.1016/j.jbiotec.2014.10.013
- Saxena, S. K., Al-Muhtaseb, A. H., & Viswanadham, N. (2015). Enhanced production of high octane oxygenates from glycerol etherification using the desilicated BEA zeolite. Fuel, 159, 837–844. https://doi.org/https://doi.org/10.1016/j.fuel.2015.07.028
- Sen, M. (2019). The effect of the injection pressure on single cylinder diesel engine fueled with propanol–diesel blend. Fuel, 254, Article 115617. https://doi.org/https://doi.org/10.1016/j.fuel.2019.115617
- Shaafi, T., & Velraj, R. (2015). Influence of alumina nanoparticles, ethanol and isopropanol blend as additive with diesel–soybean biodiesel blend fuel: Combustion, engine performance and emissions. Renewable Energy, 80, 655–663. https://doi.org/https://doi.org/10.1016/j.renene.2015.02.042
- Shoar, F. H., Abdi, R., Najafi, B., & Ardabili, S. F. (2019). The effect of thermochemical pre-treatment on biogas production efficiency from kitchen waste using a novel lab scale digester. Renewable Energy Focus, 28, 140–152. https://doi.org/https://doi.org/10.1016/j.ref.2018.12.001
- Shoar, F. H., Najafi, B., & Mosavi, A. (2021). Effects of triethylene glycol mono methyl ether (TGME) as a novel oxygenated additive on emission and performance of a dual-fuel diesel engine fueled with natural gas-diesel/biodiesel. Energy Reports, 7, 1172–1189. https://doi.org/https://doi.org/10.1016/j.egyr.2021.01.088
- Simonetti, D. A., Rass-Hansen, J., Kunkes, E. L., Soares, R. R., & Dumesic, J. A. (2007). Coupling of glycerol processing with Fischer-Tropsch synthesis for production of liquid fuels. Green Chemistry, 9(10), 1073–1083. https://doi.org/https://doi.org/10.1039/b704476c
- Singh, A., Olsen, S. I., & Nigam, P. S. (2011). A viable technology to generate third-generation biofuel. Journal of Chemical Technology & Biotechnology, 86(11), 1349–1353. https://doi.org/https://doi.org/10.1002/jctb.2666
- Srinivas, M., Raveendra, G., Parameswaram, G., Prasad, P. S. S., & Lingaiah, N. (2015). Cesium exchanged tungstophosphoric acid supported on tin oxide: An efficient solid acid catalyst for etherification of glycerol with tertbutanol to synthesize biofuel additives. Journal of Molecular Catalysis A: Chemical, 413, 7–14. https://doi.org/https://doi.org/10.1016/j.molcata.2015.10.005
- Tabatabaei, M., Aghbashlo, M., Dehhaghi, M., Panahi, H. K. S., Mollahosseini, A., Hosseini, M., & Soufiyan, M. M. (2019). Reactor technologies for biodiesel production and processing: A review. Progress in Energy and Combustion Science, 74, 239–303. https://doi.org/https://doi.org/10.1016/j.pecs.2019.06.001
- Talebian-Kiakalaieh, A., & Saidina Amin, N. R. (2017). Coke-tolerant SiW20-Al/Zr10 catalyst for glycerol dehydration to acrolein. Chinese Journal of Catalysis, 38(10), 1697–1710. https://doi.org/https://doi.org/10.1016/S1872-2067(17)62891-2
- Tang, Y., Xue, Y., Li, Z., Yan, T., Zhou, R., & Zhang, Z. (2019). Heterogeneous synthesis of glycerol carbonate from glycerol and dimethyl carbonate catalyzed by LiCl/CaO. Journal of Saudi Chemical Society, 23(4), 494–502. https://doi.org/https://doi.org/10.1016/j.jscs.2018.11.003
- Teng, W. K., Ngoh, G. C., Yusoff, R., & Aroua, M. K. (2014). A review on the performance of glycerol carbonate production via catalytic transesterification: Effects of influencing parameters. Energy Conversion and Management, 88, 484–497. https://doi.org/https://doi.org/10.1016/j.enconman.2014.08.036
- Thomas, A., Muller, S. S., & Frey, H. (2014). Beyond poly (ethylene glycol): Linear polyglycerol as a multifunctional polyether for biomedical and pharmaceutical applications. Biomacromolecules, 15(6), 1935–1954. https://doi.org/https://doi.org/10.1021/bm5002608
- Tsai, J.-H., Chen, S. J., Huang, K. L., Lin, W. Y., Lee, W. J., Lin, C. C., & Kuo, W. C. (2013). Emissions from a generator fueled by blends of diesel, biodiesel, acetone, and isopropyl alcohol: Analyses of emitted PM, particulate carbon, and PAHs. Science of The Total Environment, 466, 195–202. https://doi.org/https://doi.org/10.1016/j.scitotenv.2013.07.025
- Tsuji, A., Rao, K. T. V., Nishimura, S., Takagaki, A., & Ebitani, K. (2011). Selective oxidation of glycerol by using a hydrotalcite-supported platinum catalyst under atmospheric oxygen pressure in water. ChemSusChem, 4(4), 542–548. https://doi.org/https://doi.org/10.1002/cssc.201000359
- Veiga, P. M., Gomes, A. C. L., Veloso, C. O., & Henriques, C. A. (2017). Acid zeolites for glycerol etherification with ethyl alcohol: Catalytic activity and catalyst properties. Applied Catalysis A: General, 548, 2–15. https://doi.org/https://doi.org/10.1016/j.apcata.2017.06.042
- Veum, K., & Bauknecht, D. (2019). How to reach the EU renewables target by 2030. An analysis of the governance framework. Energy Policy, 127, 299–307. https://doi.org/https://doi.org/10.1016/j.enpol.2018.12.013
- Vieira, L. H., Carvalho, K. T., Urquieta-González, E. A., Pulcinelli, S. H., Santilli, C. V., & Martins, L. (2015). Effects of crystal size, acidity, and synthesis procedure on the catalyticperformance of gallium and aluminum MFI zeolites in glyceroldehydration. Journal of Molecular Catalysis A: Chemical, 422, 148–157. https://doi.org/https://doi.org/10.1016/j.molcata.2015.12.019
- Vlad, E., Bildea, C. S., Zaharia, E., & Bozga, G. (2011). Conceptual design of glycerol etherification processes. Computer Aided Chemical Engineering, 29, 331–335. https://doi.org/https://doi.org/10.1016/B978-0-444-53711-9.50067-5
- Wang, S., Hao, P., Li, S., Zhang, A., Guan, Y., & Zhang, L. (2017). Synthesis of glycerol carbonate from glycerol and dimethyl carbonate catalyzed by calcined silicates. Applied Catalysis A: General. https://doi.org/https://doi.org/10.1016/j.apcata.2017.05.021
- Wang, K., Hawley, M. C., & DeAthos, S. J. (2003). Conversion of glycerol to 1,3-propanediol via selective dehydroxylation. Industrial & Engineering Chemistry Research, 42(13), 2913–2920. https://doi.org/https://doi.org/10.1021/ie020754h
- Watanabe, M., Iida, T., Aizawa, Y., Aida, T. M., & Inomata, H. (2007). Acrolein synthesis from glycerol in Hot compressed water. Bioresource Technology, 98(6), 1285–1290. https://doi.org/https://doi.org/10.1016/j.biortech.2006.05.007
- Wu, H., Nithyanandan, K., Zhou, N., Lee, T. H., Chia-fon, F. L., & Zhang, C. (2014). Impacts of acetone on the spray combustion of acetone–butanol–ethanol (ABE)-diesel blends under low ambient temperature. Fuel, 142, 109–116. https://doi.org/https://doi.org/10.1016/j.fuel.2014.10.009
- Wu, H., Lee, T. H., Lee, C.-f., Liu, F., & Sun, B. (2016). Optical soot measurement of bio-butanol upstream product, ABE (acetone–butanol–ethanol), under diesel-like conditions. Fuel, 181, 300–309. https://doi.org/https://doi.org/10.1016/j.fuel.2016.04.092
- Xie, Q., Li, S., Gong, R., Zheng, G., Wang, Y., Xu, P., & Ji, J. (2018). Microwave-assisted catalytic dehydration of glycerol for sustainable production of acrolein over a microwave absorbing catalyst. Applied Catalysis B: Environmental, 243, 455–462. https://doi.org/https://doi.org/10.1016/j.apcatb.2018.10.058
- Xu, Y., Keresztes, I., Condo, A. M., Phillips, D., Pepiot, P., & Avedisian, C. T. (2016). Droplet combustion characteristics of algae-derived renewable diesel, conventional# 2 diesel, and their mixtures. Fuel, 167, 295–305. https://doi.org/https://doi.org/10.1016/j.fuel.2015.11.036
- Yan, H., Yao, S., Liang, W., Feng, X., Jin, X., Liu, Y., Chen, X., & Yang, C. (2019). Selective oxidation of glycerol to carboxylic acids on Pt (111) in base-free medium: A periodic density functional theory investigation. Applied Surface Science, 497, Article 143661. https://doi.org/https://doi.org/10.1016/j.apsusc.2019.143661
- Yang, J., Jiang, Y., Karavalakis, G., Johnson, K. C., Kumar, S., Cocker, D. R., & Durbin, T. D. (2016). Impacts of dimethyl carbonate blends on gaseous and particulate emissions from a heavy-duty diesel engine. Fuel, 184, 681–688. https://doi.org/https://doi.org/10.1016/j.fuel.2016.07.053
- Yang, L., Li, X., Chen, P., & Hou, Z. (2019). Selective oxidation of glycerol in a base-free aqueous solution: A short review. Chinese Journal of Catalysis, 40(7), 1020–1034. https://doi.org/https://doi.org/10.1016/S1872-2067(19)63301-2
- Yang, L., Takase, M., Zhang, M., Zhao, T., & Wu, X. (2014). Potential non-edible oil feedstock for biodiesel production in Africa: A survey. Renewable and Sustainable Energy Reviews, 38, 461–477. https://doi.org/https://doi.org/10.1016/j.rser.2014.06.002
- Yazdani, S. S., & Gonzalez, R. (2007). Anaerobic fermentation of glycerol: A path to economic viability for the biofuels industry. Current Opinion in Biotechnology, 18(3), 213–219. https://doi.org/https://doi.org/10.1016/j.copbio.2007.05.002
- Yilmaz, N., & Atmanli, A. (2017). Experimental assessment of a diesel engine fueled with diesel-biodiesel-1-pentanol blends. Fuel, 191, 190–197. https://doi.org/https://doi.org/10.1016/j.fuel.2016.11.065
- Yun, D., Yun, Y. S., Kim, T. Y., Park, H., Lee, J. M., Han, J. W., & Yi, J. (2016). Mechanistic study of glycerol dehydration on Brønsted acidic amorphous aluminosilicate. Journal of Catalysis, 341, 33–43. https://doi.org/https://doi.org/10.1016/j.jcat.2016.06.010
- Zaushitsyna, O., Dishisha, T., Hatti-Kaul, R., & Mattiasson, B. (2017). Crosslinked, cryostructured Lactobacillus reuteri monoliths for production of 3-hydroxypropionaldehyde, 3-hydroxypropionic acid and 1, 3-propanediol from glycerol. Journal of Biotechnology, 241, 22–32. https://doi.org/https://doi.org/10.1016/j.jbiotec.2016.11.005
- Zhang, L., Hu, C.-H., Cheng, S.-X., & Zhuo, R.-X. (2010). PEI grafted hyperbranched polymers with polyglycerol as a core for gene delivery. Colloids and Surfaces B: Biointerfaces, 76(2), 427–433. https://doi.org/https://doi.org/10.1016/j.colsurfb.2009.12.001
- Zhang, F., Ren, X., Huang, H., Huang, J., Sudhakar, M., & Liu, L. (2018). High-performance phosphate supported on HZSM-5 catalyst for dehydration of glycerol to acrolein. Chinese Journal of Chemical Engineering, 26(5), 1031–1040. https://doi.org/https://doi.org/10.1016/j.cjche.2018.01.005
- Zheng, Y., Chen, X., & Shen, Y. (2008). Commodity chemicals derived from glycerol, an important biorefinery feedstock. Chemical Reviews, 108(12), 5253–5277. https://doi.org/https://doi.org/10.1021/cr068216s
- Zheng, L., Xia, S., Lu, X., & Hou, Z. (2015). Transesterification of glycerol with dimethyl carbonate over calcined Ca-Al hydrocalumite. Chinese Journal of Catalysis, 36(10), 1759–1765. https://doi.org/https://doi.org/10.1016/S1872-2067(15)60915-9
- Zhou, N., Huo, M., Wu, H., Nithyanandan, K., Chia-fon, F. L., & Wang, Q. (2013). Low temperature spray combustion of acetone–butanol–ethanol (ABE) and diesel blends. Applied Energy, 117, 104–115. https://doi.org/https://doi.org/10.1016/j.apenergy.2013.11.035