Abstract
This paper investigates the trade-off between low percolation threshold and large positive temperature coefficient (PTC) intensity in conductive polymer composites (CPCs). Conductive particles with low aspect ratios and large dimensions have been demonstrated to induce large PTC intensity in CPCs. Conversely high aspect ratio conductive (nano)particles like carbon nanotubes (CNTs) are desirable because of their extremely low percolation threshold (typically well below 1 wt.%), providing benefits in terms of reduced density, brittleness, costs and improved processability. Herein we report on combinations of different conductive fillers to explore the possibility to obtain both low percolation threshold and high PTC intensity. For the first time we use model systems in which at least one of the two conductive fillers is of relatively homogenous size and shape to facilitate unraveling some of the complicated inter-relationships between (mixed) conductive fillers and the PTC effect.
Graphical abstract
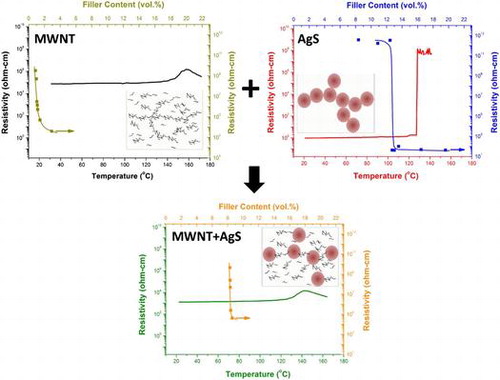
Introduction
Conductive polymer composites (CPCs) are promising materials for a series of challenging new applications like wearable electronics, smart textile and soft robotics, owing to their demonstrated capability to sense and response to a number of stimuli such as strain,Citation1 liquid and gasses,Citation2,3 damageCitation4–6 and degradation.Citation7
One of the first phenomena observed in CPCs, which have found commercial exploitation since the 1980s,Citation8 was the pyroresistive effect, commonly referred to as positive temperature coefficient (PTC) effect. PTC is defined as the increase in electrical resistivity over a relatively narrow temperature range,Citation9–14 usually in correspondence of a phase transition of the host polymer matrix (melting temperature or glass transition temperature). As the temperature increases and exceeds a certain range, the continuous network formed by the conductive filler is disrupted causing the composite to become electrically insulating. This temperature activated switching phenomenon has made CPCs very attractive in applications like self-regulated heaters and over-current protectors.Citation15–18
A pyroresistive material would ideally possess a host of characteristics including: a very large PTC intensity (defined as the log of the ratio of the maximum resistivity and the room temperature resistivity), defined transition over a certain temperature range combined with a constant resistivity before and after transition (hence no negative temperature coefficient (NTC) effect), tuneable switching temperature, stability over a large number of heating/cooling cycles and insensitivity to other external stimuli (e.g. environmental conditions, strain, etc.), combined with additional application-specific characteristics like flexibility, etc.
A lot of approaches have been explored to achieve some of the above including polymer blends,Citation11,19–23 segregated phases and networks,Citation24–30 fillers of non-uniform size and shape, aggregates, mixed fillers,Citation10,31–33 chemical and physical crosslinking,Citation34,35 etc.
The PTC intensity, for instance, has been suggested to depend on a large number of factors including polymer type,Citation36 filler shape and sizeCitation9,37 and filler distribution in the matrix.Citation38 Recently our group has demonstrated for the first time in a controlled model system that the PTC intensity increases with increasing filler size and decreasing filler content, both for spherical and flake-like conductive fillers.Citation39
The consequence of this is that, in order to have a large PTC intensity (i.e. greater than 3–4 orders of magnitude change in resistivity), large filler particles are required. Unfortunately large filler particles of low aspect ratio are characterized by high percolation thresholds,Citation40–43 leading to increased density, cost, brittleness and processing difficulties.
On the other hand, high aspect ratio nanostructured conductive particles (e.g. CNTs) are desirable since they can create a percolated conductive network at very low filler content, typically well below 1 wt.%.Citation38 The drawback is that CNTs-based CPCs exhibit low PTC intensities (less than 1–2 orders of magnitude change in resistivity) which undermines their use as pyroresistive materials.Citation44
The aim of this paper is to use combinations of different conductive fillers to explore the possibility to achieve both low percolation thresholds and high PTC intensities. A similar hypothesis has been previously suggested, but mainly using carbon black as the primary conductive filler.Citation10,33,35,45,46
Lee et al.Citation33 reported that the addition of small amounts of multi-walled carbon nanotubes (MWNTs) (<0.25 wt.% for a composite containing 20 wt.% of CB) was able to increase the PTC intensity of HDPE/CB composites of up to two orders of magnitude. Higher MWNTs loadings (>1 wt.%) instead had an overall neutral or detrimental effect on the PTC intensity. The authors related this increase in PTC intensity to an increase in degree of crystallinity of HDPE, but the latter effect was far too small (only 2% increase) to be the dominating mechanism. Moreover, some inconsistencies were noticed in their single filler composite systems, which pose doubts on the reliability of the performed PTC intensity measurements. For instance, the composite HDPE + 25 wt.% CB shows a PTC intensity more than twice that of HDPE + 20 wt.% CB, while a decrease in PTC intensity with increased filler content is generally observed.Citation9,39,44
Dang et al.Citation10 also observed a slight increase in PTC intensity of HDPE/CB composites by replacing the total amount of conductive filler (constant at 8 vol.%) with small amounts of carbon fibers (CF). In their work 2 vol.% of CF combined with 6 vol.% of CB resulted in a slight increase in PTC intensity (~30%) compared to a composite with CB only. More CF (>2.5 vol.%), instead, neutralized any beneficial effect.
More recently, Zha et al.Citation47 found that the addition of 0.5 vol.% of CNTs and 4 vol.% of CB to a blend of 80/20 of UHMWPE/PVDF could decrease the initial resistivity by two orders of magnitude and slightly increase the PTC intensity by 30%, when compared to the same polymer blend containing no CNTs and 4.5 vol.% CB. The addition of more CNTs (for instance 1 vol.% CNTs and 4 vol.% CB) had again a detrimental effect on the PTC intensity. Unfortunately polymer blends are too complicated systems to study, if the causal effects of (mixed) fillers are to be understood. In fact, differences in both electrical resistivity and pyroresistive behavior could be due to a number of factors unrelated to the actual conductive fillers used, like a change in blend morphology with temperature for instance.Citation48
Overall, the results found so far in the scientific literature are rather inconsistent, limiting our understanding of the effect of mixed fillers on PTC intensity. Therefore, here for the first time we propose to study model systems in which at least one of the two conductive fillers is of relatively homogenous size and shape, to facilitate unraveling some of the complicated relationships between (mixed) conductive filler and PTC effect.
In line with our previous paper,Citation35 silver-coated glass particles (spheres and flakes) are used as model conductive fillers due to the ease in controlling size and shape. In particular two mixed filler systems are studied. In one system both fillers are model conductive flakes of different lateral dimensions (5 and 100 μm). In the other system CNTs are used as minority filler, in combination with model conductive spherical filler (50 μm). The selection of CNTs, though slightly departing from the model system approach, serves as a limit case of a conductive filler of very high aspect ratio and hence low percolation threshold.
Experimental
High density polyethylene (HDPE) (MF1: 1.8 g min−1 2.16 kg load, density: 952 kg/m3) was received from Ineos Polyolefins under the trade name Rigidex HD5218EA. Silver-coated glass flakes (AgF) of different sizes were procured from Glassflake Ltd. (AgFL, supplier D50 = 100 μm) or kindly donated by Nippon Glass Flakes Europe (AgFS, supplier D50 = 8 μm). Silver-coated spherical glass spheres (AgSM) of 50 μm diameter were supplied by Potters Industries Ltd. The CNTs used are MWNTs supplied by Nanocyl, Belgium (Product No. NC7000).
The composites were prepared via melt compounding using a DSM X’plore 15 mini twin-screw extruder at 170 °C and 50 rpm for 15 min. The extruded strands were pelletized and compression molded into rectangular shaped samples (25 mm × 4 mm × 2 mm) using a Collin P300E hot press at 200 °C and 60 bars for 5 min. Brass electrodes were attached to the ends of the sample after silver paste was applied to reduce contact resistance between the electrode and the sample.
The microstructure of the samples was studied by FEI Inspect-F scanning electron microscope (SEM) after gold sputtering the cryogenically fractured surface of the samples.
PTC effect of the samples was examined by measuring the electrical resistance while the sample was subjected to a certain temperature profile, when placed onto a mini hot-stage, in analogy with previous publications.Citation1,39 Electrical resistance was measured by a simple two-point measurement using a combination of a picoammeter (Keithley 6485) and a DC voltage source (Agilent 6614C). A minimum of three samples are tested and the average PTC intensities are reported.
Results and discussion
Morphology
Figure shows the SEM images of HDPE filled with the different silver-coated glass particles and/or MWNTs. Silver-coated glass particles (AgFL, AgFS, AgSM) all show poor interfacial interaction with HDPE (Fig. (a–c), (e)), with clear signs of interfacial debonding. The effect of melt processing on the damage of the particles (particularly AgFL) as well as the silver coating has previously been reported.Citation35 No preferential orientation of the platelets was observed. Figure d shows a relatively good dispersion of MWNTs in HDPE matrix, with isolated MWNTs among micron-size agglomerates (shown in white circles). The mixed filler polymer composite in Fig. (e) (HDPE/AgFL + AgFS) presents two populations of glass flakes in HDPE, though a bimodal distribution is not obvious. The presence of AgSM in the composite HDPE/AgSM + MWNTs (Fig. (f)) does not affect the dispersion of MWNTs (and vice versa) as sometimes reported in literature in the case of mixed (nano)fillers.Citation49,50
Single filler HDPE pyroresistive composites
Figure shows the percolation curves of the four conductive fillers individually dispersed in HDPE. As expected the percolation threshold decreases with increased particle aspect ratio and reduced particle size.Citation39,41,43 MWNTs – possessing the smallest size and highest aspect ratio – present the lowest percolation threshold, with a value below 1 vol.% in filler content. AgSM shows instead the largest percolation threshold, at about 13 vol.%. The difference in particle size between AgFL (100 μm) and AgFS (8 μm) explains the decrease in percolation threshold, respectively, from just below 9 vol.% to about 4.5 vol.%.
Figure 2 Percolation curves of four fillers (MWNTs, AgSM, AgFS and AgFL) in HDPE. Percolation thresholds decrease with particle aspect ratio and particle sizeCitation35
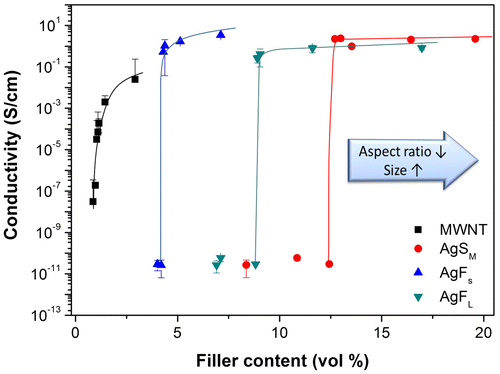
Figure shows typical resistivity-temperature curves for the four single filler composites. In agreement with previous reports,Citation35 the PTC intensity increases with increasing particles size and decreasing aspect ratio. HDPE/MWNTs present the lowest PTC intensity and the least sharp transition as well as an evident NTC effect (usually explained by particle re-agglomeration). The transition temperature for all composites is approximately in correspondence with the melting temperature of the polymer matrix, with the exception of HDPE/MWNTs. This might be a consequence of a more robust conductive and rheological network established by MWNTs.
Mixed filler HDPE pyroresistive composites
After having studied the pyroresistive behavior of the single filler composites in the previous section, two different filler combinations have been selected and investigated: AgSM + MWNTs and AgFL + AgFS.
AgSM and MWNTs were chosen because of their most extreme difference in terms of aspect ratio, percolation threshold and PTC intensity. Several series of composites were prepared at fixed AgSM contents, starting from just below the percolation threshold. A minority phase of MWNTs was added to establish a continuous (hybrid) conductive network (Fig. a).
Figure 4 Mixed filler composites HDPE/AgSM + MWNTs: a percolation curves and b PTC intensities as a function of MWNTs loading for several fixed AgSM loadings
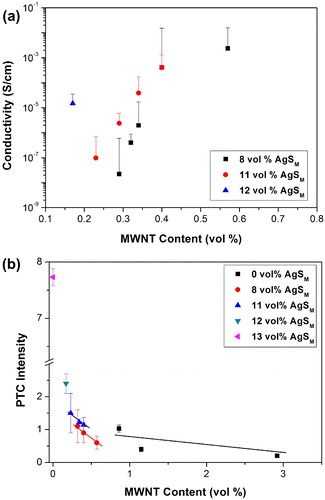
For a fixed AgSM content, increasing the MWNTs vol.% resulted, as expected, in a decrease in PTC intensity (Fig. b). Overall the different series of mixed filler composites showed values of PTC intensity between the values of single filler composites but very much skewed toward the lower end of the range, i.e. closer to values for the HDPE/MWNTs system. Adding even a minute amount of MWNTs (e.g. 0.17 vol.%) to a concentration of AgSM just below its percolation threshold (12 vol.%) resulted in a dramatic decrease in PTC intensity, from almost 8 to 2.5 orders of magnitudes (Fig. b). In other words, the pyroresistive behavior seems to be dominated by the conductive phase with the lowest PTC intensity (and percolation threshold), even at very low loadings.
To confirm and generalize the results obtained on HDPE/AgSM + MWNTs, a second group of mixed fillers composites were prepared by combining AgFL and AgFS. This constitutes a model system in which both fillers are of relatively homogeneous size and shape. The fillers have got the same shape (flake-like) and nature (conductivity, coefficient of thermal expansion, etc.) but different sizes (aspect ratio).
Also in this case the majority filler phase constituted of the filler with the highest PTC intensity (AgFL). For a fixed AgFL content, starting from just below its percolation threshold, a small amount of AgFS was added to establish a continuous (hybrid) conductive network (Fig. a).
Figure 5 Mixed filler composites HDPE/AgFL + AgFS: a percolation curves and b PTC intensities as a function of AgFS loading for several fixed AgFL loadings
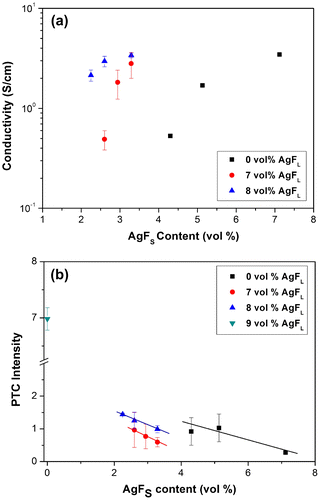
As for the HDPE/AgSM + MWNTs, also in the case of HDPE/AgFL + AgFS the PTC intensity was dominated by the conductive phase with the lowest PTC intensity (and percolation threshold) – AgFS – even at low loadings. Adding about 2 vol.% of AgFS to 8 vol.% of AgFL resulted in a dramatic decrease in PTC intensity, from about 7 to 1.5 orders of magnitudes, when compared to the single filler system based on HDPE + 9 vol.% AgFL (Fig. b).
This is a very interesting result because, to the best of our knowledge, it is the first demonstration of how, in essence, the distribution of conductive filler sizes affects the PTC intensity. Adding small amounts of AgFS to a majority of AgFL effectively means modifying the distribution of AgFL particle sizes by adding a ‘tail’ to the small particle size region. This modification of size distribution is sufficient to compromise the PTC intensity which becomes dominated by the small tail of the distribution curve.
Hence, the important underlying message here is that the PTC intensity is not only influenced by the conductive particle size, as previously demonstrated,Citation39 but also by its distribution.
At the same time these results pose doubts on the simplistic – but generally accepted – view that a thermal expansion coefficient (CTE) mismatch between polymer and filler is the main governing mechanism for the pyroresistive effect. In the present study, AgFS and AgFL have the same CTE but they, as well as their combinations, induce very different pyroresistivity behaviors. We believe that a better understanding could come from a quantitative study of ‘robustness’ of the conductive network and how this is affected by a number of disruptive mechanisms generated upon temperature increase, one of which could certainly being thermal expansion.
It is possible to imagine two extreme conductive network morphologies in a mixed filler composite, as opposed to a single filler composite (Fig. a). The first case assumes two independent and interpenetrating conductive networks. The second case assumes the two fillers constituting a hybrid conductive network in which one filler occupies the interstitial sites of the second filler’s network (Fig. b).
Figure 6 Schematic of conductive pathways in a single filler composites or b mixed filler composites with a hybrid conductive network
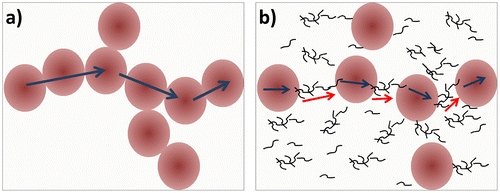
Both our mixed filler composites are believed to exhibit predominantly a hybrid network morphology (Fig. b) also because the two filler contents are very different from each other (Fig. e, f). It is believed that understanding and modeling the specific network morphology assumed by the fillers could well explain the dramatic decrease in PTC intensity in both our mixed filler conductive composites.
Conclusions
Two series of mixed filler conductive composites were studied, to explore the possibility to obtain both a low percolation threshold and a large PTC intensity. In both series, two fillers were combined; the principal filler exhibiting a large PTC intensity, and the secondary filler exhibiting a low percolation threshold. At least one of the two conductive fillers (the principal filler) was selected to be of relatively homogenous size and shape (i.e. silver-coated glass spheres or flakes) to help unravel the relationship between (mixed) conductive fillers and PTC effect.
For the first time, it was demonstrated in a universal manner that the PTC intensity of mixed filler composites is dominated by the filler with the lowest PTC intensity, even at very low loadings. Interestingly, it was also demonstrated for the first time that the PTC intensity is not only influenced by the conductive particle size but also by its size distribution.
Disclosure statement
No potential conflict of interest was reported by the authors.
Funding
This work was supported by Engineering and Physical Sciences Research Council [grant number EP/P505674/1].
Acknowledgments
Financial support from LMK Thermosafe Ltd. and EPSRC (DTA; grant reference number: EP/P505674/1) is kindly acknowledged. Nippon Glass Flakes (NGF Europe) is thanked for donating 5 um Ag-coated glass flakes. EB would like to express gratitude to Prof. Paul van der Schoot from TU/e, Dr Ettore Barbieri from QMUL and Dr Claudio Grimaldi from EPFL for fruitful discussions.
References
- E. Bilotti, R. Zhang, H. Deng, M. Baxendale and T. Peijs: ‘Fabrication and property prediction of conductive and strain sensing TPU/CNT nanocomposite fibres’. J. Mater. Chem., 2010, 20, (42), 9449–9455.10.1039/c0jm01827a
- T. Villmow, S. Pegel, P. Pötschke and G. Heinrich: ‘Polymer/carbon nanotube composites for liquid sensing: model for electrical response characteristics’. Polymer, 2011, 52, (10), 2276–2285.10.1016/j.polymer.2011.03.029
- B. Kumar, M. Castro and J.-F. Feller: ‘Quantum resistive vapour sensors made of polymer coated carbon nanotubes random networks for biomarkers detection’. Chem. Sens., 2013, 3, (20), 1–7.
- H. Zhang, Y. Liu, M. Kuwata, E. Bilotti and T. Peijs: ‘Improved fracture toughness and integrated damage sensing capability by spray coated CNTs on carbon fibre prepreg’. Compos. Part A: Appl. Sci. Manuf., 2015, 70, 102–110.10.1016/j.compositesa.2014.11.029
- E. T. Thostenson and T.-W. Chou: ‘Carbon nanotube networks: sensing of distributed strain and damage for life prediction and self healing’. Adv. Mater., 2006, 18 (21), 2837–2841.
- H. Zhang, E. Bilotti and T. Peijs: ‘The use of carbon nanotubes for damage sensing and structural health monitoring in laminated composites: a review’. Nanocomposites, 2015, 1, (4), 167–184.
- F. Mai, Y. Habibi, J. M. Raquez, P. Dubois, J. F. Feller, T. Peijs and E. Bilotti: ‘Poly(lactic acid)/carbon nanotube nanocomposites with integrated degradation sensing’. Polymer, 2013, 54, (25), 6818–6823.10.1016/j.polymer.2013.10.035
- K. Ohe and Y. Naito: ‘A new resistor having an anomalously large positive temperature coefficient’. Jpn. J. Appl. Phys., 1971, 10, (1), 99–108.10.1143/JJAP.10.99
- S. J. Luo and C. P. Wong: ‘Study on effect of carbon black on behavior of conductive polymer composites with positive temperature coefficient’. IEEE Trans. Compon. Packag. Technol., 2000, 23, (1), 151–156.10.1109/6144.833054
- Z.-M. Dang, W.-K. Li and H.-P. Xu: ‘Origin of remarkable positive temperature coefficient effect in the modified carbon black and carbon fiber cofillled polymer composites’. J. Appl. Phys., 2009, 106, (2), 024913.10.1063/1.3182818
- J. Feng and C. M. Chan: ‘Double positive temperature coefficient effects of carbon black-filled polymer blends containing two semicrystalline polymers’. Polymer, 2000, 41, (12), 4559–4565.10.1016/S0032-3861(99)00690-4
- A. Kono, K. Shimizu, H. Nakano, Y. Goto, Y. Kobayashi, T. Ougizawa and H. Horibe: ‘Positive-temperature-coefficient effect of electrical resistivity below melting point of poly(vinylidene fluoride) (PVDF) in Ni particle-dispersed PVDF composites’. Polymer, 2012, 53, (8), 1760–1764.10.1016/j.polymer.2012.02.048
- J. Meyer: ‘Stability of polymer composites as positive-temperature-coefficient resistors’. Polym. Eng. Sci., 1974, 14, (10), 706–716.
- F. Bueche: ‘A new class of switching materials’. J. Appl. Phys., 1973, 44, (1), 532–533.10.1063/1.1661934
- A. Rybak, G. Boiteux, F. Melis and G. Seytre: ‘Conductive polymer composites based on metallic nanofiller as smart materials for current limiting devices’. Compos. Sci. Technol., 2010, 70, (2), 410–416.10.1016/j.compscitech.2009.11.019
- R. stru¨mpler, J. Glatz-Reichenbach, Feature article conducting polymer composites, J. Electroceram., 1999, 3, (4), 329–346.10.1023/A:1009909812823
- C. P. Wong, S. Luo: ‘Conductive polymer composites with large positive temperature coefficients, encyclopedia of smart materials’, 2002, Wiley Online Library.
- S. Isaji, Y. Bin and M. Matsuo: ‘Electrical conductivity and self-temperature-control heating properties of carbon nanotubes filled polyethylene films’. Polymer, 2009, 50, (4), 1046–1053.10.1016/j.polymer.2008.12.033
- C. Lu, X. N. Hu, Y. X. He, X. Huang, J. C. Liu and Y. Q. Zhang: ‘Triple percolation behavior and positive temperature coefficient effect of conductive polymer composites with especial interface morphology’. Polym. Bull., 2012, 68, (7), 2071–2087.10.1007/s00289-012-0723-0
- C. Lu, R. Wang, X.-N. Hu, Q.-Q. Cao, X.-H. Huang, Y.-X. He and Y.-Q. Zhang: ‘Influence of morphology on PTC effect for poly (ethylene-co-butyl acrylate)/nylon6 blends with multiwall carbon nanotubes dispersed at interface and in matrix’. Polym. Bull., 2014, 71, (3), 545–561.10.1007/s00289-013-1076-z
- S. A. H. Pour, B. Pourabbas and M. S. Hosseini: ‘Electrical and rheological properties of PMMA/LDPE blends filled with carbon black’. Mater. Chem. Phys., 2014, 143, (2), 830–837.10.1016/j.matchemphys.2013.10.021
- F. Gubbels, R. Jerome, P. Teyssie, E. Vanlathem, R. Deltour, A. Calderone, V. Parente and J. L. Bredas: ‘Selective localization of carbon black in immiscible polymer blends: a useful tool to design electrical conductive composites’. Macromolecules, 1994, 27, (7), 1972–1974.10.1021/ma00085a049
- G. Droval, J. F. Feller, P. Salagnac and P. Glouannec: ‘Conductive polymer composites with double percolated architecture of carbon nanoparticles and ceramic microparticles for high heat dissipation and sharp PTC switching’. Smart Mater. Struct., 2008, 17, (2), 025011.
- Y. Bao, L. Xu, H. Pang, D. X. Yan, C. Chen, W. Q. Zhang, J. H. Tang and Z. M. Li: ‘Preparation and properties of carbon black/polymer composites with segregated and double-percolated network structures’. J. Mater. Sci., 2013, 48, (14), 4892–4898.10.1007/s10853-013-7269-x
- S. Isaji, Y. Bin and M. Matsuo: ‘Electrical and self-heating properties of UHMWPE-EMMA-NiCF composite films’. J. Polym. Sci. Part B: Polym. Phys., 2009, 47, (13), 1253–1266.10.1002/polb.v47:13
- K. Nagata, M. Inaba, N. Toge, K. Takahashi and Y. Aoki: ‘Localization of carbon black particles in polypropylene/polyethylene polymer blend and its electrical resistivity’. Kobunshi Ronbunshu, 2002, 59, (11), 694–701.10.1295/koron.59.694
- H. Pang, Q. Y. Chen, Y. Bao, D. X. Yan, Y. C. Zhang, J. B. Chen and Z. M. Li: ‘Temperature resistivity behaviour in carbon nanotube/ultrahigh molecular weight polyethylene composites with segregated and double percolated structure’. Plast. Rubber Compos., 2013, 42, (2), 59–65.10.1179/1743289812Y.0000000031
- H. Pang, L. Xu, D.-X. Yan and Z.-M. Li: ‘Conductive polymer composites with segregated structures’. Prog. Polym. Sci., 2014, 39, (11), 1908–1933.10.1016/j.progpolymsci.2014.07.007
- Y. Wei, Z. Li, X. Liu, K. Dai, G. Zheng, C. Liu, J. Chen and C. Shen: ‘Temperature-resistivity characteristics of a segregated conductive CB/PP/UHMWPE composite’. Colloid Polym. Sci., 2014, 292, (11), 2891–2898.10.1007/s00396-014-3334-5
- M. Wen, X. Sun, L. Su, J. Shen, J. Li, S. Guo: ‘The electrical conductivity of carbon nanotube/carbon black/polypropylene composites prepared through multistage stretching extrusion’. Polymer, 2012, 53, 1602–1610.
- Y. Fang, J. Zhao, J. W. Zha, D. R. Wang and Z. M. Dang: ‘Improved stability of volume resistivity in carbon black/ethylene-vinyl acetate copolymer composites by employing multi-walled carbon nanotubes as second filler’. Polymer, 2012, 53, (21), 4871–4878.10.1016/j.polymer.2012.08.035
- P. Kar, S. Maiti, N. K. Shrivastava, S. Dhibar and B. B. Khatua: ‘Positive temperature coefficient to resistively characteristics of polystyrene/nickel powder/multiwall carbon nanotubes composites’. Polym. Compos., 2012, 33, (11), 1977–1986.10.1002/pc.v33.11
- J. H. Lee, S. K. Kim and N. H. Kim: ‘Effects of the addition of multi-walled carbon nanotubes on the positive temperature coefficient characteristics of carbon-black-filled high-density polyethylene nanocomposites’. Scr. Mater., 2006, 55, (12), 1119–1122.10.1016/j.scriptamat.2006.08.051
- M.-K. Seo, K.-Y. Rhee and S.-J. Park: ‘Influence of electro-beam irradiation on PTC/NTC behaviors of carbon blacks/HDPE conducting polymer composites’. Curr. Appl. Phys., 2011, 11, (3), 428–433.10.1016/j.cap.2010.08.013
- K.-Y. Tsao, C.-S. Tsai and C.-Y. Huang: ‘Effect of argon plasma treatment on the PTC and NTC behaviors of HDPE/carbon black/aluminum hydroxide nanocomposites for over-voltage resistance positive temperature coefficient (PTC)’. Surf. Coat. Technol., 2010, 205, Supplement 1(0), S279–S285.
- Y. Luo, G. Wang, B. Zhang and Z. Zhang: ‘The influence of crystalline and aggregate structure on PTC characteristic of conductive polyethylene/carbon black composite’. Eur. Polym. J., 1998, 34, (8), 1221–1227.10.1016/S0014-3057(98)00099-8
- S. J. Luo, C. P. Wong: ‘Conductive polymer composites with positive temperature coefficient’. Proceedings of IEEE, International Symposium on Advanced Packaging Materials: Processes, Properties and Interfaces, 1999, 311–316.
- W. Bauhofer and J. Z. Kovacs: ‘A review and analysis of electrical percolation in carbon nanotube polymer composites’. Compos. Sci. Technol., 2009, 69, (10), 1486–1498.10.1016/j.compscitech.2008.06.018
- E. Asare, J. Evans, M. Newton, T. Peijs and E. Bilotti: ‘Effect of particle size and shape on positive temperature coefficient (PTC) of conductive polymer composites (CPC) — a model study’. Mater. Des., 2016, 97, 459–463.
- L. Karásek, B. Meissner, S. Asai and M. Sumita: ‘Percolation concept: polymer-filler gel formation, electrical conductivity and dynamic electrical properties of carbon-black-filled rubbers’. Polym. J., 1996, 28, (2), 121–126.10.1295/polymj.28.121
- X. Jing, W. Zhao and L. Lan: ‘The effect of particle size on electric conducting percolation threshold in polymer/conducting particle composites’. J. Mater. Sci. Lett., 2000, 19, (5), 377–379.10.1023/A:1006774318019
- P. Banerjee and B. M. Mandal: ‘Blends of HCl-doped polyaniline nanoparticles and poly(vinyl chloride) with extremely low percolation threshold - a morphology study’. Synth. Met., 1995, 74, (3), 257–261.10.1016/0379-6779(95)03370-Y
- T. Ota, M. Fukushima, Y. Ishigure, H. Unuma, M. Takahashi, Y. Hikichi and H. Suzuki: ‘Control of percolation curve by filler particle shape in Cu-SBR composites’. J. Mater. Sci. Lett., 1997, 16, (14), 1182–1183.
- M. O. Lisunova, Y. P. Mamunya, N. I. Lebovka and A. V. Melezhyk: ‘Percolation behaviour of ultrahigh molecular weight polyethylene/multi-walled carbon nanotubes composites’. Eur. Polym. J., 2007, 43, (3), 949–958.10.1016/j.eurpolymj.2006.12.015
- Q. Li, Siddaramaiah, N. H. Kim, G. H. Yoo, J. H. Lee: ‘Positive temperature coefficient characteristic and structure of graphite nanofibers reinforced high density polyethylene/carbon black nanocomposites’. Compos. Part B: Eng., 2009, 40, (3), 218–224.10.1016/j.compositesb.2008.11.002
- R. Socher, B. Krause, S. Hermasch, R. Wursche and P. Pötschke: ‘Electrical and thermal properties of polyamide 12 composites with hybrid fillers systems of multiwalled carbon nanotubes and carbon black’. Compos. Sci. Technol., 2011, 71, (8), 1053–1059.10.1016/j.compscitech.2011.03.004
- J. W. Zha, W. K. Li, R. J. Liao, J. B. Bai and Z. M. Dang: ‘High performance hybrid carbon fillers/binary-polymer nanocomposites with remarkably enhanced positive temperature coefficient effect of resistance’. J. Mater. Chem. A, 2013, 1, (3), 843–851.10.1039/C2TA00429A
- A. Nuzzo, E. Bilotti, T. Peijs, D. Acierno and G. Filippone: ‘Nanoparticle-induced co-continuity in immiscible polymer blends – A comparative study on bio-based PLA-PA11 blends filled with organoclay, sepiolite, and carbon nanotubes’. Polymer (Guilford), 2014, 55, (19), 4908–4919.10.1016/j.polymer.2014.07.036
- J. Sumfleth, X. C. Adroher and K. Schulte: ‘Synergistic effects in network formation and electrical properties of hybrid epoxy nanocomposites containing multi-wall carbon nanotubes and carbon black’. J. Mater. Sci., 2009, 44, (12), 3241–3247.10.1007/s10853-009-3434-7
- E. Bilotti, H. Zhang, H. Deng, R. Zhang, Q. Fu and T. Peijs: ‘Controlling the dynamic percolation of carbon nanotube based conductive polymer composites by addition of secondary nanofillers: The effect on electrical conductivity and tuneable sensing behaviour’. Compos. Sci. Technol., 2013, 74, 85–90.10.1016/j.compscitech.2012.10.008