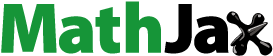
Abstract
High safety and rate capability of lithium-ion batteries (LIBs) remain challenging. In this study, sandwich-structured poly(vinylidene fluoride)/poly(vinylidene fluoride-co-hexafluoropropylene)/poly(vinylidene fluoride) (PVDF/PVDF-HFP/PVDF) membranes with thermal shut-down function were successfully prepared through electrospinning. The effects of different weight ratios of PVDF and PVDF-HFP in a composite membrane on the physical and electrochemical properties of the membrane were explored. It was found that the composite membrane with 36 wt% PVDF-HFP (P/H2/P) showed excellent electrolyte absorption (367%) and ionic conductivity (2.5 × 10−3 S/cm). Half-cell with P/H2/P as separator exhibited higher discharge capacity and better cycle performance than commercial PP membrane. More importantly, thermally stable high melting-temperature PVDF was chosen as outer layer, while low melting-temperature PVDF-HFP was used as inner layer. Self-shutdown function of this separator was achieved when heated at 140 °C, providing a safety measure for LIBs. These results indicate that PVDF/PVDF-HFP/PVDF composite membrane is a promising separator candidate in high performance LIBs applications.
Graphical Abstract
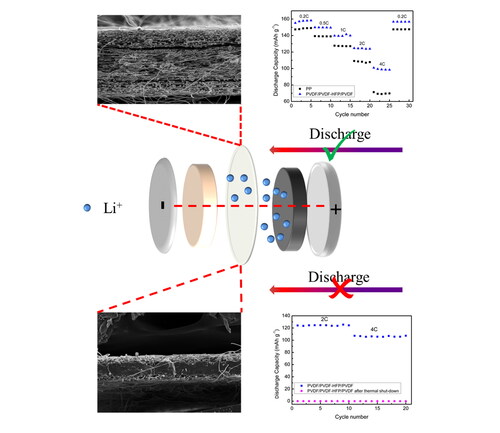
1. Introduction
Due to their obvious advantages of high energy density, long cycle life and environmental friendliness, lithium-ion batteries (LIBs) have been widely used in smart electronic devices, electric vehicles (EVs) and energy storage system [Citation1, Citation2]. However, current safety issue and poor rate capability severely impede their further applications and development of new generation high performance LIBs [Citation3, Citation4]. In recent years, the safety of LIBs has been improved by adding electrolyte additives [Citation5, Citation6], composite electrodes [Citation7] and modified separators [Citation8-10], etc. As an inert component, separators do not participate in electrochemical processes but determine the electrochemical performance and safety of LIBs, providing an effective and less sacrificial way to improve the safety of LIBs [Citation11]. Commercial polyolefin membranes including polyethylene (PE), polypropylene (PP) and PP/PE/PP have been widely used as LIBs separators due to their excellent mechanical properties and low cost. However, their relatively low porosity, insufficient electrolyte wettability severely affect the rate capability of LIBs [Citation12]. Besides, low thermal stability may cause internal short circuit at elevated temperatures and lead to uncontrollable thermal runaway, limiting their applications in next generation of batteries [Citation13]. Although there have been studies on modifying commercial membranes, such as coating inorganic particles to polyethylene terephthalate (PET) nonwoven fabrics [Citation14], electrospun PVDF on PP nonwoven fabrics [Citation15], etc. Yet the coated membranes suffer from pore blockage and performance deterioration [Citation16]. On the other hand, poor compatibility between different polymer materials in the composite membrane may result in inferior interfacial bonding and premature interlayer failure. Therefore, a method to fabricate a durable membrane with shut-down function, high porosity and excellent ionic conductivity is still a challenge.
Electrospinning has been widely used to prepare various functional fiber membranes with high porosity, large specific surface area and interconnected porous structure [Citation17, Citation18]. Electrospun membranes have been made from a variety of polymers including polyacrylonitrile (PAN) [Citation19, Citation20], polyimide (PI) [Citation21, Citation22], thermoplastic polyurethane (TPU) [Citation23, Citation24], polyvinylidene fluoride (PVDF) [Citation25, Citation26], polyvinylidene fluoride-hexafluoropropylene (PVDF-HFP) [Citation27, Citation28], etc. In particular, PVDF and PVDF-HFP have attracted significant attentions because of their excellent mechanical properties and thermal stability, chemical inertness in electrolyte and good electrolyte affinity [Citation29, Citation30]. Kim et al. confirmed that the cross-linked PVDF-HFP membrane provided highly efficient ionic conducting pathways, resulting in higher discharge capacity of assembled LIBs compared with PP membranes [Citation31]. Khalifa et al. demonstrated a nonwoven PVDF/halloysite nanotube (HNT) nanocomposite membrane with high ionic conductivity and low thermal shrinkage [Citation32]. Although single-layer polymer fiber membranes with nanoparticles embedded can gain higher thermal stability, it is not able to achieve thermal shut-down at heat accumulation situation, therefore, three-layer membranes based on electrospun fibers have been further developed to improve safety and electrochemical performance of LIBs. Wu et al. reported a novel sandwich structured PI/PVDF/PI composite membrane. High melting-temperature PI component improved thermal stability while low melting-temperature PVDF component melt to shut down ion pathways at elevated temperatures [Citation33]. Pan et al. fabricated ultrathin SiO2-anchored layered PVDF/PE/PVDF porous fiber membranes. The membranes exhibited highly porous structure with high electrolyte uptake capability, and unique layered structure was beneficial to arrest heat accumulations by cutting off Li+ diffusion channels [Citation34]. However, most polymer pairs are thermodynamically immiscible, which results in poor interfacial adhesion and therefore inferior mechanical and electrochemical properties [Citation35].
In this study, we chose PVDF homopolymer and PVDF-HFP copolymer to prepare all-fluoropolymer composite membrane, aiming to achieve better interlayer adhesion and lower lithium ion transfer resistance. Moreover, the outer PVDF microfibers layer with better thermal stability was selected as a support to avoid short circuit and the intermediate PVDF-HFP microfibers layer with a low melting temperature was selected to realize thermal shut-down at high-temperature situation in order to improve battery safety. By controlling a total spinning time of 18 h, membranes with different time ratios were obtained (), i.e. PVDF: PVDF-HFP: PVDF = 1:1:1, 1:2:1, 1:3:1, denoted as P/H1/P, P/H2/P, P/H3/P, respectively. The influences of different weight ratios of two polymers in composite membranes on ionic conductivity, electrolyte uptake, thermal stability, mechanical properties and electrochemical properties of assembled half-cells were investigated. Thermal shut-down function was also examined by a simulated high-temperature situation.
2 Experimental section
2.1. Materials
PVDF (Solef 6010) and PVDF-HFP (Solef 21510) were purchased from Solvay, Germany; dimethylformamide (DMF, analytical grade), acetone (analytical grade) were purchased from Sinopharm Chemical Reagent Co. Ltd. (Shanghai, China). The liquid electrolyte solution of 1 M lithium hexafluorophosphate (LiPF6) in the ethylene carbonate (EC):dimethyl carbonate (DMC)=1:1(v:v) was obtained from Duoduo Reagent Network (Suzhou, China). Commercial membrane (Celgard 2500) was used as reference for comparison purpose. PVDF binder (Arkema 500) was purchased from Arkema, France and super P was purchased from Tianchenghe Technology Co. Ltd. (Shenzhen, China) used as conductive additive.
2.2. Membranes fabrication
The PVDF/PVDF-HFP/PVDF microfibrous membranes were prepared by electrospinning method, as shown in . Before preparing the spinning solution, PVDF and PVDF-HFP powders were dried at 60 °C for 12 h. Then PVDF and PVDF-HFP powders were dissolved in a mixed solvent of DMF:acetone = 7:3 (v:v) respectively, and mechanically stirred at 50 °C for 3 h to obtain 14 wt% PVDF solution and 20 wt% PVDF-HFP solution.
The as-prepared solution was then electrospun into fibers at a tip-to-collector distance of 19 cm, a voltage of 18 kV, a flow rate of 0.02 ml min−1 and the speed of collector was 150 rpm. By controlling a total spinning time of 18 h to obtain membranes with different time ratios, i.e. PVDF:PVDF-HFP:PVDF = 1:1:1, 1:2:1, 1:3:1, denoted as P/H1/P, P/H2/P, P/H3/P, respectively. The as-prepared membranes were dried in a vacuum oven at 80 °C for 12 h to remove the solvent. Finally, the membranes were hot pressed at 120 °C under a pressure of 4 MPa for 1 h to consolidate into PVDF/PVDF-HFP/PVDF composite membranes.
2.3. Characterizations
The microscopic morphology of the membranes were observed by a scanning electron microscope (SEM JSM-6390LV, Japan), and the accelerating voltage was 15 kV.
The porosity of membranes was measured as follows. The samples with a diameter of 18 mm were cut from membranes by a membrane-punching machine. They were washed and dried at 50 °C for 6 h. The porosity was then calculated by using EquationEq. (1)(1)
(1) [Citation36].
(1)
(1)
where, P is the porosity of the sample; ρ0 is the density of PVDF and PVDF-HFP (1.78 g cm−3) and ρ is the density of the sample.
In order to evaluate the electrolyte affinity of microporous membranes, the electrolyte uptake ratio (EU) of membranes was calculated by EquationEq. (2)(2)
(2) . The membranes were soaked in the electrolyte (1 M LiPF6 in EC:DEC) for 2 h.
(2)
(2)
where, W0 and W are the mass of membrane before and after absorbing the electrolyte, respectively.
Tensile tests were carried out using a tensile tester (UTM4104X, SUNS, Shenzhen, China) at a testing speed of 20 μm s−1. The gauge length of samples was 20 mm and the width was 8 mm.
The thermal behavior of the membranes was characterized by a differential scanning calorimeter (DSC 250, TA Instruments, US). The membranes were heated from 25 °C to 200 °C at a rate of 10 °C min−1 under nitrogen atmosphere. The crystallinity of membranes was calculated from DSC data by using EquationEq. (3)(3)
(3) .
(3)
(3)
where ΔHm is the enthalpy of melting peak in the DSC curve; ΔH100 is the apparent enthalpy of fusion per gram of totally crystalline PVDF/PVDF-HFP (ΔH100=104.7 J g−1) [Citation37].
The samples with a diameter of 18 mm were cut from membranes by a membrane-punching machine and treated at 130 °C for 0.5 h to compare thermal stability of these membranes. Thermal shrinkage ratio (TS) was calculated by EquationEq. (4)(4)
(4) .
(4)
(4)
where S0 and S1 represent the surface area of membranes before and after thermal treatment, respectively.
Cells with a configuration of stainless steel (SS)/membrane/SS were assembled, electrochemical impedance spectroscopy (EIS) was used to measure bulk resistance (Rb) of the membranes at frequencies between 1 Hz and 500 KHz at an amplitude of 5 mV. Then the ion conductivity was calculate by EquationEq. (5)(5)
(5) [Citation38].
(5)
(5)
where, σ is ionic conductivity; L is the thickness of the membrane; Rb is the bulk resistance and A is the effective area of the membrane.
The cathode materials were prepared by blending LiFePO4 powders (80 wt%), super P (10 wt%) and PVDF binder (10 wt%). A coin-type cell (CR 2032) with a configuration of Li/membrane/LiFePO4 was used to investigate the rate capability, cycling performance and EIS. Galvanostatic charge/discharge C-rate capabilities were examined at voltage range of 2.5–4.2 V in a Neware Battery Test System (BTS-4000, China) at 0.2, 0.5, 1, 2, and 4 C, a 1 C-rate meaning that the selected discharge current discharged the battery in 1 h. The cycling performance was investigated at 1 C for 100 cycles.
In order to simulate its thermal shut-down behavior at high temperature, the P/H2/P was sandwiched between two steel plates and treated at 140 °C for 30 min (denoted as SD-P/H2/P). The half-cell assembled with SD-P/H2/P was charged and discharged at 2 C and 4 C.
3 Results and discussion
The microscopic morphology of P/H2/P composite membrane was observed by SEM and shown in . P/H2/P had interconnected fibrous structures leading to high porosity, which can facilitate the absorption and retention of electrolyte and lithium ion transportation. After a time-controlled electrospinning process, the P/H2/P membrane had a 72 μm-thick layer made of PVDF-HFP microfibers at the center and two 40 μm-thick layers made of PVDF microfibers at the top and bottom. After hot pressing at 120 °C, PVDF-HFP microfibers were partially melted () and consolidated well with the PVDF microfiber layer (). It is noticed from magnified image in that the partially melted and consolidated PVDF-HFP formed numerous microfibrils in the interfacial regions between PVDF and PVDF-HFP layers resulting in better interfacial bonds between these two layers. Furthermore, it is observed from that a crack was formed during the freeze-fracture preparation of these samples. It shows that the crack occurred in the outer PVDF layer instead of in the interlayer regions between PVDF and PVDF-HFP layers. This intralayer crack indicates that a good interfacial bonding between PVDF and PVDF-HFP layers were obtained. The cohesive and physically connected interfacial regions of these all-PVDF composite membranes can promote an integrity of composite membranes and therefore their mechanical properties.
Figure 2. SEM images of P/H2/P membrane (a) top view; (b) cross-sectional image;(c) magnified image of circled region in (b); (d) Stress-strain curves of PVDF, PVDF-HFP, nHP-P/H2/P and PVDF/PVDF-HFP/PVDF composite membranes.
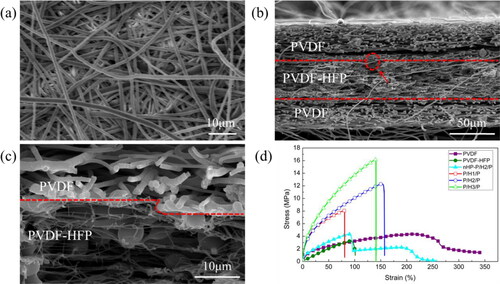
Excellent tensile properties of separators are necessary to improve the safety and prelong service life of LIBs, but the tensile strength and modulus of electrospun membrane are generally low because its non-woven features [Citation21]. shows the stress-strain curves of different samples. The maximum tensile strengths of single-layered PVDF-HFP and PVDF membranes were only 3.3 MPa and 4.4 MPa, respectively. Besides, PVDF-HFP membrane was brittle and less tough than PVDF membrane. The tensile properties of sandwich-structured membrane without hot pressing (denoted as nHP-P/H2/P in ) were also investigated. This nHP-P/H2/P membrane exhibited a similar brittleness as PVDF-HFP membrane. However, the sandwich-structured membranes after hot pressing showed much higher tensile strengths (∼ 400% maximum increment) and tensile moduli (∼1400% maximum increment) than single-layered and non hot-pressed membranes. During hot press process, PVDF-HFP microfibers with a low melting point (Tm) (∼130 °C) partially melted and consolidated with PVDF microfibers to obtain cohesive interfacial adhesions, which led to a significant increase in tensile strength. Inspiringly, the superior interfacial adhesion between microfibers in the interfacial regions similar as adhesion between fibers and matrix in all-polymer composites is a key factor for the improvement in tensile properties [Citation39–47]. Meanwhile, as the content of PVDF-HFP in the composite membrane increased, the tensile strength of membrane was improved successively because more interfacial regions with cohesive adhesions were created.
Thermal behavior of PVDF/PVDF-HFP/PVDF composite membrane was characterized by DSC and shown in . It is observed that the composite membrane showed endothermic peaks at around 135 °C and 172 °C corresponding to the melting temperatures of PVDF-HFP and PVDF components, respectively. By calculating from DSC curves [Citation48], the actual weight ratios of three layers in these composite membranes were 1:0.6:1, 1:1.1:1 and 1:2.1:1 for P/H1/P, P/H2/P and P/H3/P respectively. The crystallinity of PVDF-HFP and PVDF components was calculated by EquationEq. (3)(3)
(3) and shown in . As the PVDF-HFP content increased from 23 wt% (P/H1/P) to 51 wt% (P/H3/P), the crystallinity of PVDF-HFP component only increased from 4.1% to 5.5%, revealing the crystallization of PVDF-HFP copolymer chains with strong steric hindrance is kinetically unfavorable. Meanwhile, when the content of PVDF component in these composite membranes decreased from 77 wt% to 49 wt%, the crystallinity of PVDF component decreased sharply by 58.8%. The total crystallinity of composite membranes was reduced to below 20% for P/H2/P and P/H3/P. Because electrolyte uptake and retention occur through a swelling process in the amorphous regions in separators [Citation49], lower crystallinity is therefore beneficial to improve electrolyte affinity and ionic conductivity.
Figure 3. (a) DSC curves of the composite membranes; (b) crystallinity of PVDF and PVDF-HFP components in composite membrane; (c) porosity and electrolyte uptake ratio of different membranes; (d) photograph of different membranes after heat treatment at 25 °C and 130 °C for 0.5 h.
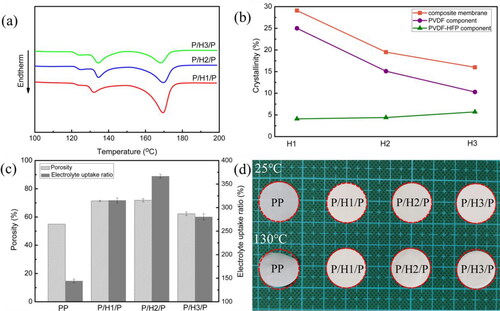
Additionally, porosity and electrolyte uptake ratio are two evidently important indicators for evaluating the performance of membranes. shows that the composite membranes exhibited significantly higher porosity and electrolyte uptake ratio than PP membrane, attributing to three-dimensional fibrerous network structure of electrospun microfibre membranes and lower crystallinity. Especially, due to effective combination of PVDF and PVDF-HFP layers through hot press, P/H2/P membrane had high porosity (69%) and electrolyte uptake ratio (367%), which is beneficial to improve ionic conductivity and subsequent cell performance.
Severe thermal shrinkage of the membrane may cause a short circuit within the battery and increase the risks of spontaneous combustion and explosion during heat accumulation, therefore good thermal stability of the membrane is crucial to the safety performance of LIBs. shows the photographs of the membranes before and after heat treatment at 25 °C and 130 °C for 0.5 h. Thermal shrinkage ratios of PP, P/H1/P, P/H2/P, and P/H3/P membranes were calculated to be 11.9%, 1.1%, 2.1%, and 10.1%, respectively. The thermal shrinkage ratio of membranes increased as PVDF-HFP component increased due to relatively lower thermal stability of PVDF-HFP than PVDF. The thermal shrinkage ratio of PP was the highest among these membranes, obvious shrinkage and shape change from round to rolled-up in the machine direction (uniaxial stretching direction) were observed for PP. Meanwhile, P/Hx/P showed uniform shrinkage in all directions, which is advantageous for effectively improving the safety of LIBs at high temperatures.
shows the Nyquist plots of SS/membrane/SS cells. In high-frequency region, the intercept of Nyquist plot on the real axis represents the bulk resistance (Rb) of membrane. The ionic conductivity value were hence calculated and presented in Table S1. Due to their high porosity and electrolyte uptake ratio, the composite membranes demonstrated lower Rb and much higher ionic conductivity than PP membrane (0.8 × 10−3 S cm−1). Obviously, the Rb of P/H2/P membrane was lower than P/H1/P and P/H3/P membranes, therefore, it showed the highest ionic conductivity (2.5 × 10−3 S cm−1) among these composite membranes, indicating rapid migration of lithium ions during charge-discharge process.
Figure 4. (a) Nyquist plots of SS/membrane/SS; (b) interfacial impedance of Li/membrane/LiFePO4 with different membranes; (c) the initial charge–discharge profiles of cells with different membranes at 0.2 C; (d) the rate performance of cells with different membranes; (e) the initial charge–discharge profiles of cells with different membranes at 2 C; (f) cycling performance of cells with different membranes at 1 C.
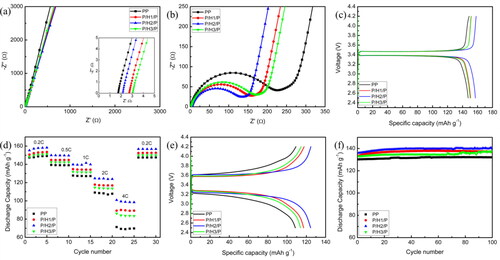
The compatibility of liquid electrolyte-soaked porous membrane with commercial electrode materials was characterized by EIS of Li/membrane/LiFePO4 half cells. All the Nyquist plots in show a semicircle in high- and medium-frequency region indicating the charge-transfer resistance (Rct) in interfacial regions, as well as straight line in low-frequency region indicating the diffusion of lithium ions in cathode materials [Citation50]. The Rct values of composite membranes were significantly lower than that of PP membrane (Table S1), particularly, P/H2/P membrane displayed the lowest charge-transfer resistance, due to its high porosity, better wettability to electrolyte and low crystallinity. The low resistance of P/H2/P composite membrane would improve the compatibility between electrode and electrolyte-soaked P/H2/P membrane, revealing that the transportation of lithium ions between electrode and electrolyte interfaces is more efficient.
The electrochemical performances of Li/membrane/LiFePO4 half-cells are shown in . The type and structure of membranes influences lithium ions transport through electrolyte-soaked membranes. The initial discharge capacities of half-cells with composite membranes at 0.2 C were higher than cell with PP (147.0 mAhg−1) as shown in . This is correlated with the fact that these electrospun microfibrous membranes had higher porosity and electrolyte retention, leading to lower interfacial resistances. Moreover, P/H2/P membrane showed higher initial discharge capacity (157.1 mAhg−1) than P/H1/P membrane (152.2 mAhg−1) and P/H3/P membrane (150.0 mAhg−1), due to its higher ionic conductivity than other two composite membranes. shows the rate capability of the cells assembled with various membranes. At the same C-rate, cells with PVDF/PVDF-HFP/PVDF composite membranes exhibited higher capacities than cell with PP due to their lower interfacial resistances. Meaningfully, the capacity-decay values of P/H1/P, P/H2/P and P/H3/P were 41.4%, 36.1% and 42.0% respectively, lower than PP (53.0%) when the charge-discharge rate increased from 0.2 C to 4 C, indicating that composite membranes can help to reduce the ohmic polarization of the cell. P/H2/P membrane had higher porosity and liquid electrolyte absorption, consequently, it had superior ionic conductivity which can facilitate rapid lithium ions transportation between electrodes and improve the high-rate performance of battery. Therefore, cell assembled with P/H2/P had the highest discharge capacity especially at higher rates ().
shows the cycling performance of the cells with different membranes at 1 C. The cells with PVDF/PVDF-HFP/PVDF membranes had no apparent capacity loss after 100 cycles, indicating that composite membranes had excellent cycle stability.
The shut-down behavior of composite membrane was further investigated. P/H2/P was sandwiched between two steel plates and treated at 140 °C for 30 min (denoted as SD-P/H2/P). The microscopic morphology of SD-P/H2/P composite membrane was shown in . It is noticed from that pore blockage clearly occurred. Because 140 °C does not reach the melting temperature of PVDF layer, it is supposed that the melted PVDF-HFP microfibers penetrated into PVDF outer layers and consolidated to cause pore blockage. indicate that melted and consolidated PVDF-HFP wrapped the fibers of PVDF layers to form a dense membrane. It is expected that the as-formed dense membrane would be able to effectively block ion transfer channels and therefore shut down electrochemical reactions between electrodes to prevent further heat accumulations.
Figure 5. SEM images of SD-P/H2/P membrane (a) top view; (b) cross-sectional view; (c) magnified image of circled cross-sectional region; (d) Cycle performance of cells with P/H2/P and SD-P/H2/P membrane.
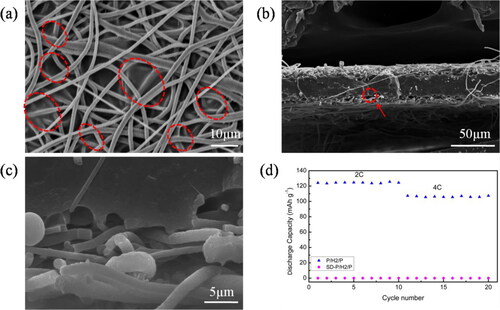
The charge-discharge tests of Li/membrane/LiFePO4 half-cell with SD-P/H2/P membrane were performed at 2 C and 4 C, the results are shown in . The discharge capacity of this cell was almost zero at both 2 C and 4 C, indicating that the dense middle layer of SD-P/H2/P membrane blocked the transport channels of lithium ions [Citation51], demonstrating that P/H2/P composite membrane can perform thermal shut-down function at high-temperature situation [Citation33]. Currently, polypropylene (PP) and polyethylene (PE) monolayer membranes are mostly used in LIBs industry, but they suffer from low thermal stability and high safety risks [Citation10]. Although commercial PP/PE/PP membranes (e.g. Celgard 2320) can provide thermal shut-down function at 135 °C (Tm of PE), its thermal shrinkage ratio is as high as 20% at 130 °C [Citation51] due to its low thermal stability and poor interfacial compatibility between different polymer layers. The current PVDF/PVDF-HFP/PVDF composite membrane can therefore provide a promising alternative separator solution for high safety LIBs.
4 Conclusions
In summary, a sandwich-structured all-fluoropolymer composite membrane was prepared by time-controlled electrospinning and hot pressing process. The all-fluoropolymer composite membrane exhibited excellent tensile properties due to its cohensive interfacial adhesion between microfibers in interfacial regions. The effects of different weight ratios of two polymers in composite membrane on physical and electrochemical properties of the membrane were explored. P/H2/P composite membrane showed superior electrolyte absorption ratio (367%), ionic conductivity (2.5 × 10−3 S/cm) and lower interfacial resistance (119.3 Ω). Hence, cell with P/H2/P composite membrane demonstrated high discharge capacity (157.1 mAhg−1) at 0.2 C and low capacity-decay of 36% from 0.2 C to 4 C. More importantly, P/H2/P can perform thermal shut-down function at high-temperature situation to prevent heat accumulation and decrease the risks of thermal runaway. Therefore, the all-fluoropolymer composite membrane is a promising separator candidate to improve safety and electrochemical properties of LIBs.
CRediT Authorship contributions statement
Rongyan Wen: implementing experiments, acquiring and processing data, writing & editing draft. Zhihao Gao: implementing parts of experiments, processing data, editing draft. Lin Luo: implementing parts of experiments, validation. Xiaochen Cui: validation, editing draft. Jie Tang: reviewing & editing draft, supervising. Zongmin Zheng: reviewing & editing draft. Jianmin Zhang: proposing concept and method, reviewing & editing draft, supervising, project and ministration, funding acquisition.
Supplemental Material
Download MS Word (111.5 KB)Disclosure statement
No potential conflict of interest was reported by the authors.
Additional information
Funding
Notes on contributors
Rongyan Wen
Rongyan Wen received her BEng degree in 2019 and she is now a postgraduate student working on electrospun polymeric functional membranes for LIBs.
Zhihao Gao
Zhihao Gao received his BEng degree in 2019 and he is now a postgraduate student working on functional composite membranes for LIBs.
Lin Luo
Lin Luo received his BEng degree in 2020 and he is now a postgraduate student working on functional composite membranes for LIBs.
Xiaochen Cui
Xiaochen Cui received his BEng degree in 2020 and he is now a postgraduate student working on carbon-based materials for energy storage applications.
Jie Tang
Prof. Jie Tang is a managing researcher in advanced low-dimentional nanomaterials group in National Institute for Materials Science, Tsukuba, Japan. Her research interest is in the design, fabrication, characterization and applications of one- or two-dimensional nanostructured materials.
Zongmin Zheng
Dr. Zongmin Zheng received her PhD degree in Chemistry from Xiamen University and joined in Qingdao University in 2017. Her research focuses on materials for energy storage applications.
Jianmin Zhang
Dr. Jianmin Zhang is now an Associated Professor in Qingdao University. She received her PhD degree in Materials Science from Queen Mary University of London in 2009. Then she worked for AVIC and Simens in Beijing. In 2015 she joined in Qingdao University. Her research interests include polymeric functional membranes, carbon-based materials for energy storage applications.
References
- Tang JJ, Hou L, Hu TJ, et al. Influence of oxygen content on the electrochemical behavior of SiOx@C anodes for Li-ion battery. Compos. Commun. 2021;23:100544.
- Zhou CY, Zong W, Zhou GY, et al. Radical-functionalized polymer nanofiber composite separator for ultra-stable dendritic-free lithium metal batteries. Compos. Commun. 2021;25:100696.
- Chombo PV, Laoonual Y. A review of safety strategies of a Li-ion battery. J. Power Sources. 2020;478:228649.
- Yang Z, Zhang XJ, Li Z, et al. Interlinked carbon nanocages-coated separator as an efficient trap for soluble polysulfides in a lithium–sulfur battery. Energ Fuel. 2021;35(23):19843–19848.
- Kim K, Ma H, Park S, et al. Electrolyte-Additive-Driven interfacial engineering for High-Capacity electrodes in Lithium-Ion batteries: Promise and challenges. ACS Energy Lett. 2020;5(5):1537–1553.
- Zhou ZH, Sun T, Cui J, et al. A homogenous solid polymer electrolyte prepared by facile spray drying method is used for room-temperature solid lithium metal batteries. Nano Res. 2021.
- Liang CL, Liu Y, Bao RY, et al. Sodium ascorbate assisted uniform distribution of Fe3O4 nanoparticles on rGO surface: improved cycling and rate performance of rGO/Fe3O4 anode material for lithium ion batteries. Nanocomposites. 2015;1(3):170–175.
- Xie Y, Chen XY, Han K, et al. Natural halloysite nanotubes-coated polypropylene membrane as dual-function separator for highly safe Li-ion batteries with improved cycling and thermal stability. Electrochim. Acta. 2021;379:138182.,
- Song Y-Z, Zhang Y, Yuan J-J, et al. Fast assemble of polyphenol derived coatings on polypropylene separator for high performance lithium-ion batteries. J. Electroanal. C. 2018;808:252–258.
- Gao ZH, Wen RY, Deng H, et al. Composite membrane of poly(vinylidene fluoride) AND 2D Ni(OH)2 nanosheets for high-performance lithium-ion battery. ACS Appl Polym Mater. 2022;4:960–970.
- Yuan M, Liu K. Rational design on separators and liquid electrolytes for safer lithium-ion batteries. J. Energy Chem. 2020;43:58–70.
- Wang LL, Liu F, Shao WL, et al. Graphite oxide dopping polyimide nanofiber membrane via electrospinning for high performance lithium-ion batteries. Compos. Commun. 2019;16:150–157.
- Liu J, Liu YB, Yang WX, et al. Lithium ion battery separator with high performance and high safety enabled by tri-layered SiO2@PI/m-PE/SiO2@PI nanofiber composite membrane. J. Power Sources. 2018;396:265–275.
- Kyeremateng NA, Gukte D, Ferch M, et al. Preparation of a self‐supported SiO2 membrane as a separator for Lithium-Ion batteries. Batteries Supercaps. 2020;3(5):456–462.
- Yanilmaz M, Chen C, Zhang XW. Fabrication and characterization of SiO2/PVDF composite nanofiber-coated PP nonwoven separators for lithium-ion batteries. J Polym Sci Part B: Polym Phys. 2013;51(23):1719–1726.
- Qi XT, Zhang Z, Tu CB, et al. Covalent grafting interface engineering to prepare highly efficient and stable polypropylene/mesoporous SiO2 separator for Li-ion batteries. Appl. Surf. Sci. 2021;541:148405.,
- Rogalski JJ, Bastiaansen CWM, Peijs T. Rotary jet spinning review – a potential high yield future for polymer nanofibers. Nanocomposites. 2017;3(4):97–121.
- Zhang X, Shi XT, Gautrot JE, et al. Nanoengineered electrospun fibers and their biomedical applications: A review. Nanocomposites. 2021;7(1):1–34.
- Yusuf A, Avvaru VS, Dirican M, et al. Low heat yielding electrospun phosphenanthrene oxide loaded polyacrylonitrile composite separators for safer high energy density lithium-ion batteries. Appl. Mater. Today. 2020;20:100675.,
- Chen CC, Zhang WD, Zhu H, et al. Fabrication of metal-organic framework-based nanofibrous separator via one-pot electrospinning strategy. Nano Res. 2021;14(5):1465–1470.
- Cai M, Yuan D, Zhang X, et al. Lithium ion battery separator with improved performance via side-by-side bicomponent electrospinning of PVDF-HFP/PI followed by 3D thermal crosslinking. J. Power Sources. 2020;461:228123.,
- Li ML, Sheng L, Xu R, et al. Enhanced the mechanical strength of polyimide (PI) nanofiber separator via PAALi binder for lithium ion battery. Compos. Commun. 2021;24:100607.,
- Stojanovska E, Kurtulus M, Abdelgawad A, et al. Developing lignin-based bio-nanofibers by centrifugal spinning technique. Int J Biol Macromol. 2018;113:98–105.
- Cai M, Zhu JM, Yang CC, et al. A parallel bicomponent TPU/PI membrane with mechanical strength enhanced isotropic interfaces used as polymer electrolyte for lithium-ion battery. Polymers. 2019;11(1):185.,
- Wang LY, Deng NP, Ju JG, et al. A novel core-shell structured poly-m-phenyleneisophthalamide@polyvinylidene fluoride nanofiber membrane for lithium ion batteries with high-safety and stable electrochemical performance. Electrochim. Acta. 2019;300:263–273.
- Zhou Y-T, Yang J, Liang H-Q, et al. Sandwich-structured composite separators with an anisotropic pore architecture for highly safe Li-ion batteries. Compos. Commun. 2018;8:46–51.
- Liang T, Liang W-H, Cao J-H, et al. Enhanced performance of high energy density lithium metal battery with PVDF-HFP/LAGP composite separator. ACS Appl Energy Mater. 2021;4(3):2578–2585.
- Shi C, Dai JH, Huang SH, et al. A simple method to prepare a polydopamine modified core-shell structure composite separator for application in high-safety lithium-ion batteries. J. Membr. Sci. 2016;518:168–177.
- Men SL, Gao ZH, Wen RY, et al. Effects of annealing time on physical and mechanical properties of PVDF microporous membranes by a melt extrusion-stretching process. Polym Adv Technol. 2021;32(6):2397–2408.
- Pornsawan KO, Narong C, Prasit T, et al. Largely enhanced dielectric properties of TiO2- nanorods/poly(vinylidene fluoride) nanocomposites driven by enhanced interfacial areas. Nanocomposites. 2021;7(1):123–131.
- Kim I, Kim BS, Nam S, et al. Cross-Linked poly(vinylidene fluoride-co-hexafluoropropene) (PVDF-co-HFP) gel polymer electrolyte for flexible Li-Ion battery integrated with organic light emitting diode (OLED). Mater. 2018;11(4):543.,
- Khalifa M, Janakiraman S, Ghosh S, et al. PVDF/halloysite nanocomposite-based non-wovens as gel polymer electrolyte for high safety lithium ion battery. Polym Compos. 2019;40(6):2320–2334.
- Wu DZ, Shi C, Huang SH, et al. Electrospun nanofibers for sandwiched polyimide/poly (vinylidene fluoride)/polyimide separators with the thermal shutdown function. Electrochim. Acta. 2015;176:727–734.
- Pan J-L, Zhang Z, Zhang H, et al. Ultrathin and strong electrospun porous fiber separator. ACS Appl Energy Mater. 2018;1(9):4794–4803.
- Jiang GJ, Wu H, Guo SY. Reinforcement of adhesion and development of morphology at polymer-polymer interface via reactive compatibilization: a review. Polym Eng Sci. 2010;50(12):2273–2286.
- Xia Y, Li JJ, Wang HJ, et al. Synthesis and electrochemical performance of poly(vinylidene fluoride)/SiO2 hybrid membrane for lithium-ion batteries. J Solid State Electrochem. 2018;23(2):519–527.
- Cao JH, Zhu BK, Xu YY. Structure and ionic conductivity of porous polymer electrolytes based on PVDF-HFP copolymer membranes. J. Membr. Sci. 2006;281(1–2):446–453.
- Zhang F, Ma XL, Cao CB, et al. Poly(vinylidene fluoride)/SiO2 composite membranes prepared by electrospinning and their excellent properties for nonwoven separators for lithium-ion batteries. J. Power Sources. 2014;251:423–431.
- Zhang JM, Cortés-Ballesteros B, Peijs T. All-aramid composites by partial fiber dissolution in mixed solvents. Polym Compos. 2018;39(9):3013–3021.
- Alcock B, Cabrera NO, Barkoula NM, et al. The mechanical properties of unidirectional all-polypropylene composites. Compos. Part A. 2006;37(5):716–726.
- Zhang JM, Mousavi Z, Soykeabkaew N, et al. Effects of surface-dissolution process multivariables on the morphology, mechanical properties, and crystallization of all-aramid composites. Polym Compos. 2018;39(9):3307–3316.
- Nattakan S, Takashi N, Peijs T. All-cellulose composites of regenerated cellulose fibres by surface selective dissolution. Compos. Part A. 2009;40:321–328.
- Cabrera N, Alcock B, Loos J, et al. Processing of all-polypropylene composites for ultimate recyclability. P I Mech Eng L. 2004;218(L2):145–155.
- Alcock B, Cabrera NO, Barkoula NM, et al. Interfacial properties of highly oriented coextruded polypropylene tapes for the creation of recyclable all-polypropylene composites. J Appl Polym Sci. 2007;104(1):118–129.
- Somord K, Suwantong O, Tawichai N, et al. Self-reinforced poly(lactic acid) nanocomposites of high toughness. Polymer. 2016;103:347–352.
- Somord K, Somord K, Suwantong O, et al. Self-reinforced poly(lactic acid) nanocomposites with integrated bacterial cellulose and its surface modification. Nanocomposites. 2018;4(3):102–111.
- Alcock B, Peijs T. Technology and development of self-reinforced polymer composites. Adv Polym Sci. 2011;251:1–76.
- Zhang JM, Peijs T. Self-reinforced poly(ethylene terephthalate) composites by hot consolidation of Bi-component PET yarns. Compos. Part A. 2010;41(8):964–972.
- Barbosa JC, Dias JP, Lanceros-Mendez S, et al. Recent advances in poly(vinylidene fluoride) and its copolymers for Lithium-Ion battery separators. Membranes. 2018;8(3):45.,
- Gören A, Mendes J, Rodrigues H, et al. High performance screen-printed electrodes prepared by a green solvent approach for lithium-ion batteries. J. Power Sources. 2016;334:65–77.
- Shi C, Zhang P, Huang SH, et al. Functional separator consisted of polyimide nonwoven fabrics and polyethylene coating layer for lithium-ion batteries. J Power Sources. 2015;298:158–165.